Understanding The Artistry Of Rugs: A Comprehensive Guide From Designing To Crafting
Oct 15, 2023 | Rushita Deshmukh
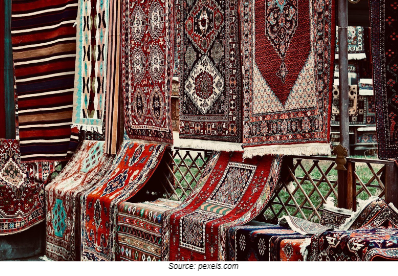
Table of Contents
What are Rugs? Different styles of Rugs
What is the process of making rugs? Steps to follow for manufacturing rugs Scope of Innovation in rug making Conclusion
What are Rugs?
Rugs are textile floor coverings typically made of thick woven material or pile, designed to be placed on the floor for functional and decorative purposes. They are often used to add warmth, comfort, and aesthetic appeal to a space. Rugs can be found in various shapes, sizes, colors, and patterns, and they are made from a wide range of materials, including natural fibers like wool, silk, cotton, and jute, as well as synthetic fibers such as nylon and polyester. They can be handwoven, tufted, knotted, or machine-made, each method contributing to the unique characteristics and quality of the rug.
Different styles of Rugs
There are several varieties of rugs, each having unique qualities depending on its technique and cultural roots. Let's look at some examples of the various rug types:
Persian Rugs: Iranian-made Persian rugs are renowned for their elaborate designs, vivid colors, and superior craftsmanship. They are often hand-knotted, which involves attaching the foundation of the rug with thousands of individual knots. Persian rugs are made in many parts of Iran, each with its own unique design and qualities. For instance, Kashan rugs frequently have exquisite medallion designs, whereas Tabriz rugs are renowned for their beautiful floral patterns.
Intricate details of persian rugs (Source: Amazon.in)
Moroccan Rugs: Moroccan rugs, commonly referred to as Berber rugs, are typically manufactured by Berber weavers. Through their designs, they frequently incorporate storytelling and symbolism. Aspects of Berber culture, beliefs, or way of life are represented through certain patterns and symbols that have cultural and historical value. Patterns can take the form of squares, triangles, zigzags, and diamond shapes. The designs are frequently asymmetrical, which adds to their distinctive and natural charm. These rugs have the unique ability to blend in with a wide range of interior design aesthetics, from bohemian and eclectic to modern and minimalist.
Texture of moroccan rugs (Source: etsy.com)
Kilim Rugs: They are flat-woven rugs, which means they lack a pile or other recognisable raised surface. They are made by closely tying together the warp and weft threads to get a flat, reversible rug that is uniformly thick. Kilim rugs are light and manageable because of their
flat-woven construction. Their unusual designs and hues provide both classic and modern rooms a dash of exoticism and personality.
Motifs of kilim rugs (Source: www.craftmaestros.com)
Shag Rugs: Shag rugs are distinguished by their long, dense pile. This gives the floor a velvety, fluffy texture that feels rich underfoot and lends a warm, welcoming quality to the space. They are perfect for relaxing or going barefoot because of the longer pile's cushioning effect.
Additionally, the deep pile has great sound-absorbing qualities that lessen echo and noise in a space. They are available in a huge selection of colors and patterns. Shag rugs frequently evoke a nostalgic charm since they are so closely related to the vintage style of the 1960s and 1970s.
Shag rugs (Source: rugs.com, loomkart.com)
What is the process of making rugs?
Source: www.choudharyexports.com
The process of making rugs is fascinating and demands skills, imagination, and attention to detail. Every step, from the choice of materials to the precise weaving or knotting techniques is important. The selection of fibers is usually the first step in the process, after which they are sourced and processed for use. The design is then conceptualized after considering elements like color, pattern, and cultural symbolism. The design is then brought to life by skilled artisans using a variety of methods like hand-knotting, hand-weaving, or machine-weaving. Consistent stress is maintained throughout the process, and a sturdy structure is made.
After the weaving or knotting is finished, the rug is given finishing touches to improve its appearance and texture, including trimming, washing, and drying. As a result, the rug is both a functional floor covering and a work of art that showcases the workmanship, culture, and ingenuity of its creators. Now let's look at the various techniques used for making rugs.
Hand Knotting: Hand knotting is the process of manually tying each knot onto the warp threads of a loom. The warp threads, which run vertically, form the rug's framework. The yarn is looped around pairs of neighboring warp threads using a specialized tool, such as a shuttle or a knotting comb.
Source: www.bashircarpets.com
The Persian (Senneh) knot and the Turkish (Ghiordes) knot are the two main knot types used in hand knotting. Due to the asymmetry of the Persian knot, the weaver must pass the yarn under one warp thread before crossing it over the adjacent warp thread. On the other hand, the Turkish knot is symmetrical and requires pulling the yarn back up between the two adjacent warp threads after passing it under both of them. The weaver tightly compacts each knot while they are being tied by using their fingers or a comb. The rug's longevity and thickness are determined by the knot density. The more knots there are per square inch, finer and more intricate the rug will be.
Hand Tufting: In this process, a pile is manually created using a tufting gun or other hand instrument. The foundation fabric or background material is stretched tightly on a frame or loom, which serves as the canvas on which the design or pattern is marked as a guide, before the hand tufting process can begin. The artist puts yarn loops into the fabric using a tufting gun or other hand tool. While the portable tool enables the artist to manually punch the yarn into the cloth, the tufting gun uses a needle to drive the yarn into the fabric.
Tufting done by tool and by hand (Source: www.desertcart.com.eg, www.plushrugs.com)
Once the backing cloth is attached to the yarn, it is secured using latex adhesive or another bonding agent. This holds the loops firmly in place and keeps them from coming undone.
Throughout the entire design area, the procedure is repeated. The loops are cut once tufting is finished to produce an even pile height and a smooth surface. The rug is then given a second layer of support and stability, such as a fabric or latex backing. A variety of design options, including complex patterns, textures, and various pile heights, are possible when tufting by hand. It enables for artistic expression and offers versatility in terms of color selection. The method is faster, it is also more time and money efficient than hand knotting.
Hooking: In this method, loops of yarn or fabric strips are pulled through a backing material to create rugs using a hooking tool. The foundation material is stretched tightly on a frame or hoop
at the beginning of the hooking process, similar to how tufting is done. The artist pulls loops of yarn or fabric strips through the foundation material using a hooking tool, which has a wooden or metal handle with a hooked end. A loop is made on the surface when the hook is introduced from the front of the fabric, catches a loop of yarn, and is then pulled back through to the front.
Source: somersetstitch.blogspot.com
The craftsman keeps going in this manner, completing each row as instructed by the pattern or design. To make an even pile, the loops are drawn through at regular intervals. Depending on the desired texture and design, the density and length of the loops can change. The strain of the yarn or fabric itself secures the loops as they are drawn through. The loops of hooked rugs produce a velvety and soft surface, giving them a distinct textured appearance.
Weaving: The process of weaving involves weaving together warp (longitudinal threads) and weft (horizontal threads) threads to form the rug's framework. Setting up a loom—a frame or apparatus that holds the warp threads stretched vertically on the loom under tension—is the first step in the weaving process. The weft threads are crossed and tucked beneath the warp threads to form the rug's framework. To generate a tightly woven fabric, this method is repeated row after row while alternating the over and under pattern.
A shuttle, a device that holds and moves the weft through the warp, is used in hand weaving to manually manipulate the weft threads. To produce an exact and consistent weave, the weaver meticulously manages the tension and placement of the weft threads. Rug styles and patterns can be made using a variety of weaving methods. The kilim, tapestry, soumak, and flat-weave are few of the popular weaving methods.
Source: klementinteriors.com
Needlepoint: In this method, a needle is used to sew yarn or thread through a canvas. The canvas used here is a fabric with holes that are properly spaced and resemble a grid. The artist threads the yarn through the holes in the canvas using a needlepoint needle, which has a big eye and a blunt tip. Many different techniques are used to create the stitches, such as tent stitch, basketweave stitch, or other decorative stitches. The most typical stitch used in needlepoint is the tent stitch. It involves making a slanted stitch that fills a single square on the canvas by diagonally pulling the needle up through one hole and down through the next hole.
Source: www.vermilionrugs.com
Another well-liked stitch that offers additional solidity and coverage is basketweave. It includes making a diagonal thread, locking it in place with a horizontal or vertical stitch to create the appearance of a woven fabric. After the canvas has been stitched all the way around, the edges
are completed with binding or fringe to protect the edges and give the canvas a polished appearance. Even though they can be used as floor coverings, needlepoint rugs are mostly valued for their decorative qualities.
Steps to follow for manufacturing rugs
Procuring quality materials
In order to make a rug, selecting the right materials is essential. It requires taking into account elements like the fiber type (wool, silk, cotton, synthetic), their quality, and their supply. Picking higher grade materials for rugs have a major role in the quality of the final products. Think about the fibers' durability, suppleness, and texture. Because of their lavish feel and durability, natural materials like wool and silk are often favored.
Source: www.nazmiyalantiquerugs.com
Dyeing the yarns
Source: www.niki-jones.co.uk
After the yarns are washed, they get ready for dyeing. It is crucial to comprehend how various dyeing methods, such as natural dyeing or synthetic dyeing, affect color fastness, vibrancy, and color variations. Getting the required designs and patterns on the rug requires accurate and uniform coloration throughout. Yarns can either be dyed using a natural dyeing method which involves the use of natural dyes derived from plants and minerals. This provides a subtle and earthy color to the yarns. Other than this, synthetic dyes are also widely used since these dyes offer a wide range of colors. Synthetic dyeing method also helps to maintain consistency and improves color fastness. Some other methods used are
Acid Dyeing (Water-soluble pigments called acid dyes are left in an acidic environment to bond with fibers)
Chrome Dyeing (Usually applied to wool, mordant acid dyes use a chromium compound as the mordant)
Space Dyeing (Yarn is divided into parts and then dyed to create visually appealing and dynamic color patterns)
Weaving technique based on the design and pattern
It takes skill and careful planning to produce distinctive and aesthetically pleasing designs. The general structure, scale, symmetry, motifs, and color schemes are all important design factors. The technical part entails converting the design into a blueprint or pattern chart that directs the rug-making procedure. You can use a variety of knotting or weaving techniques, including hand-knotting, hand-tufting, or hand-weaving, depending on the design you're aiming for. As we saw earlier, each method has unique technical nuances and effects on the finished result. To achieve the proper pile height,
texture, and structural integrity, it is crucial to comprehend the precise criteria, stress, and precision required for each approach.
Finishing the rug
Source: www.bashircarpets.com
The rug will look polished and professional thanks to proper finishing methods. Few processes that are used in finishing are as follows:
Trimming: Trimming is the delicate removal of extra yarn or thread to create a uniform pile height. It makes sure the rug's surface is level and smooth, which improves the appearance of the rug as a whole.
Binding: The procedure of binding involves covering the rug's edges with fabric or binding tape. This method offers the rug a tidy and polished appearance while preventing fraying and enhancing the edges' endurance.
Overcasting: Hand-knotted rugs' edges can be kept tight by overcasting. To create a strong and reinforced finish, more yarns are wrapped around the warp threads at the edges.
Blocking: The rug is shaped and stretched to its intended size by the blocking process. It guarantees that the rug sits flat and straight and that any shape abnormalities are fixed.
Quality Control
Throughout the rug-making process, quality control methods are put in place to make sure the finished product satisfies set requirements. This involves routine inspections for dimensions accuracy, craftsmanship, and color accuracy. To offer high-quality rugs and satisfy customers, consistent production practice and adherence to quality standards are essential. A crucial component of quality control is visual examination. Inspectors check the rug for any flaws, inconsistencies, or problems in the weaving, design, or finishing.
They look for any frayed threads, distorted patterns, or inconsistent color. The rug is cleared for sale or shipment once it has passed all quality control inspections.
Scope of Innovation in rug making
As per the above information, it is clear that rug making is a craft in itself and requires sufficient practice and skill. Hence, much like any other craft, rug manufacturers can enhance their products and stand out in the market by using innovative production, design, and sustainability methods.
Through the developments in digital technology and design tools, makers can now aim for more intricate and uniquely designed rugs. A greater use of computer-aided design (CAD) tools could speed up the prototyping process and can make way for client customisation.
Like many other businesses, the rug-making sector has been transitioning to more environmentally friendly and sustainable practices. Natural and plant-based dyeing innovations, as well as the utilization of recycled or organic materials, have gained traction.
Despite not being commonly used in traditional rug creation, 3D printing technology could be considered for the purpose of developing unique and avant-garde rug prototypes. This might open up the possibility of experimenting with novel textures, designs, and materials.
As e-commerce expands, rug manufacturers can engage in personalization-focused online platforms in order to provide clients the ability to customize their carpets in terms of size, color, and pattern, creating a distinctive shopping experience.
Conclusion
We have now seen how passion, custom, and creativity come together to create beautiful rugs that elegantly adorn our homes and places. It is fascinating to anticipate the development of new technologies and techniques that will impact the future of this time-honored art form as the rug-making industry continues to change.
Recommended
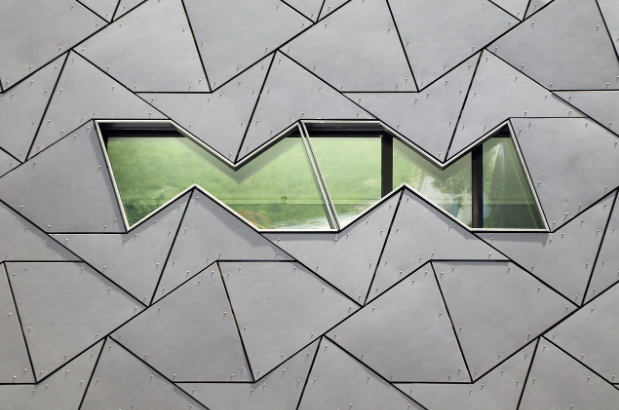

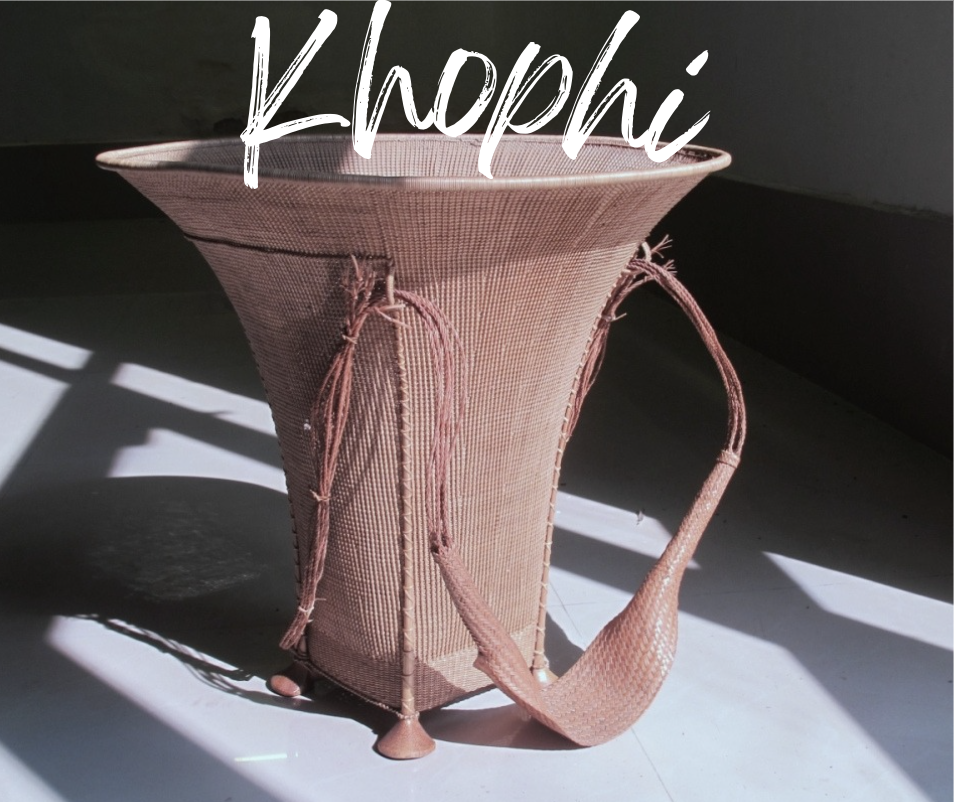