The Ultimate Guide For International Buyers Navigating Manufacturing, Quality, And Logistics. CHAPTER 4
Feb 24, 2024 | Tanya Sachdeva
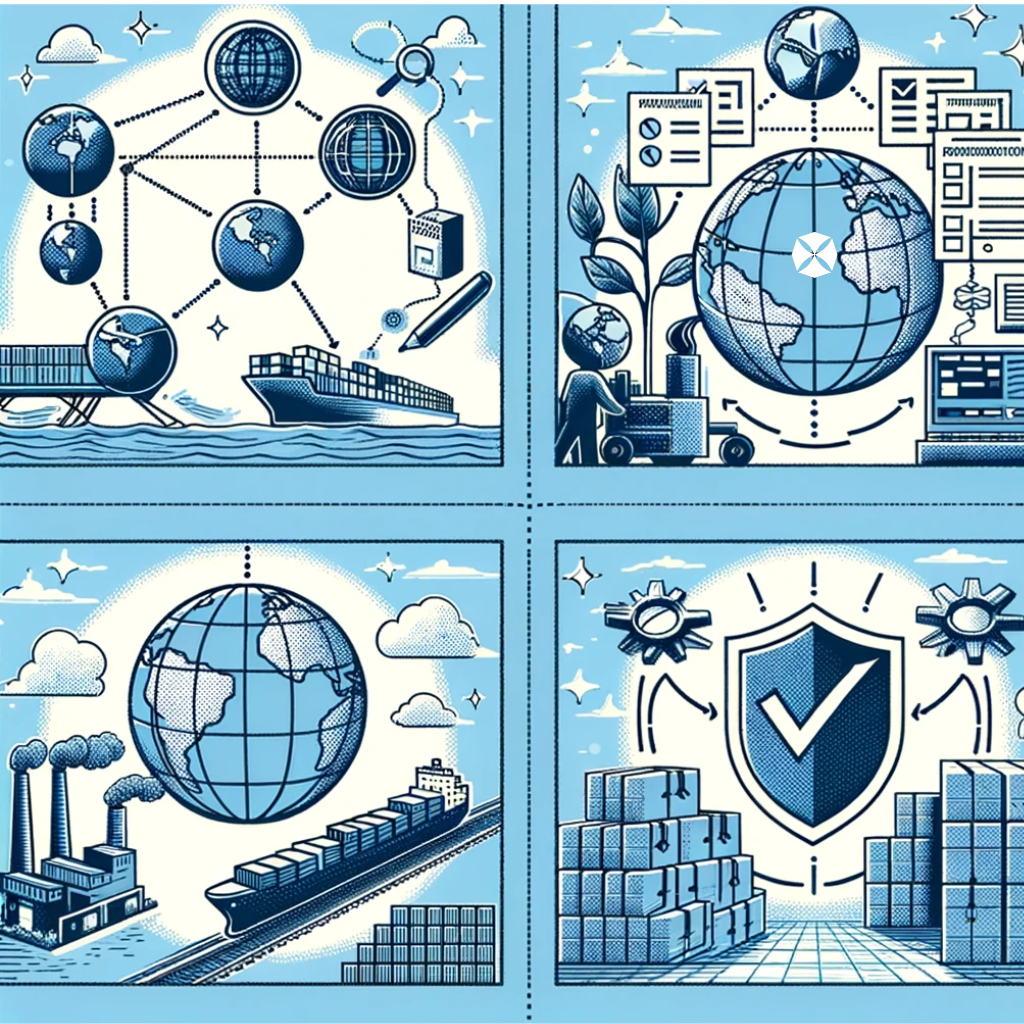
Process Mapping: A Comprehensive Guide to International Procurement and Production
In today's global market, a standardized process for international procurement and production is essential to streamline operations and reduce risks. This blog post will provide a detailed overview of process mapping, a step-by-step guide to the entire procurement and manufacturing process, from product development to delivery.
Step 1: Define the Process
Begin by outlining the entire procurement and production process, including all stages, milestones, and deliverables. This will serve as the foundation for your process map.
Step 2: Break Down the Process
Divide the process into smaller, manageable tasks. This will help you identify potential bottlenecks and inefficiencies.
Step 3: Create a Visual Map
Step 4: Identify Key Stakeholders
List all the stakeholders involved in the process, including suppliers, manufacturers, quality control teams, and logistics providers.
Step 5: Establish Responsibilities
Step 6: Develop a Timeline
Create a timeline for each stage of the process, including milestones and deadlines. This will help you and your team stay on track and ensure that deliverables are met on time.
Step 7: Implement Quality Control Measures
Integrate quality control measures at each stage of the process to ensure that products meet the required standards.
Step 8: Establish Communication Protocols
Create a communication plan that outlines how information will be shared among stakeholders. This will help prevent misunderstandings and ensure that everyone is on the same page.
Step 9: Monitor and Evaluate
Regularly monitor the process to identify areas for improvement and ensure that quality standards are being met. Use data and feedback from stakeholders to make informed decisions about process improvements.
Step 10: Continuous Improvement
Implement a continuous improvement process to ensure that the procurement and production process remains efficient and effective. This will help you stay competitive in the global market and reduce risks associated with international procurement and production.
What are some tools or software that can be used for process mapping in international procurement and production?
There are several tools and software that can be used for process mapping in international procurement and production. Some of these tools include:
Flowchart or diagramming software: These tools allow you to create visual representations of the process, including flowcharts, swimlane diagrams, and value stream maps
Procurement process mapping software: These tools are specifically designed for mapping the procurement process, including identifying the starting point, outlining all relevant steps involved in procuring goods or services, specifying product requirements, obtaining quotes from vendors, negotiating prices and terms, placing orders with suppliers, receiving deliveries, processing invoices, and payments
Microsoft Office Suite: Microsoft Word, PowerPoint, and Excel can be used to create process maps and flowcharts.
What are the features of smartsheet's process mapping tool?
Drag-and-drop interface
Integrated BPM tool
Publishing and sharing capabilities
Venn diagram maker
Intuitive design
Integration with MS Office products
Linking between charts and other documents
Reporting capabilities
Review scheduling capacity
Web-based
Unified platforms
Collaboration
Business rules management
Process simulation
High-Level Process Map (process map showing four to eight key steps)
SIPOC (Suppliers, Inputs, Processes, Outputs, Customers) map
Assign ownership to each process and task
Aid with compliance requirements
Support business process analysis
Show where you're going (help users understand the goal or destination before starting a process)
Customizable templates for various processes, such as IT, sales, and product management
CHECKLISTS AND TEMPLATES
Checklists and Templates for RFQs
An RFQ (Request for Quotation) is a document that is used to request pricing information from suppliers for a specific product or service. To ensure that the RFQ process is efficient and effective, it is important to use a checklist or template that includes the following information:
Specify the product or service you're requesting the quote for: Clearly define the product or service that you are requesting a quote for. This will help suppliers provide accurate pricing information.
State the product quantity or length of service needed: Indicate the quantity of the product or the length of service that you require. This will help suppliers provide accurate pricing information.
Determine the pricing method: Decide on the pricing method that you want to use, such as unit price or hourly rate. This will help suppliers provide accurate pricing information.
Request a product or service price breakdown: Ask suppliers to provide a breakdown of the pricing for the product or service. This will help you understand the cost of each component and make informed decisions.
Note when you need the product or service delivered: Indicate the date when you need the product or service delivered. This will help suppliers provide accurate pricing information and ensure that the product or service is delivered on time.
Describe the evaluation method/criteria and process: Clearly define the evaluation method and criteria that you will use to select a supplier. This will help suppliers understand what is expected of them and ensure that the evaluation process is fair and transparent.
Include payment terms and contract terms and conditions: Specify the payment terms and conditions that you require, as well as any contract terms and conditions that are relevant. This will help suppliers understand what is expected of them and ensure that the contract is fair and transparent.
Create a section for Frequently Asked Questions (FAQ): Include a section for frequently asked questions to help suppliers understand the RFQ process and provide accurate pricing information.
Provide instructions on how to complete the RFQ: Clearly define the instructions for completing the RFQ. This will help suppliers understand what is expected of them and ensure that the RFQ process is efficient and effective.
Highlight the due date for submitting price quotations: Indicate the due date for submitting price quotations. This will help suppliers understand the timeline for the RFQ process and ensure that the pricing information is submitted on time.
Checklists and Templates for Contracts
A contract is a legally binding agreement between two or more parties that outlines the terms and conditions of a business relationship. To ensure that the contract is fair and transparent, it is important to use a checklist or template that includes the following information:
Clearly define the scope of work: Define the scope of work that is covered by the contract. This will help all parties understand what is expected of them and ensure that the contract is fair and transparent.
Specify the deliverables and timelines: Indicate the deliverables that are required and the timelines for delivery. This will help all parties understand what is expected of them and ensure that the contract is fair and transparent.
Outline the payment terms and conditions: Specify the payment terms and conditions that are required. This will help all parties understand what is expected of them and ensure that the contract is fair and transparent.
Include quality control measures and standards: Define the quality control measures and standards that are required. This will help all parties understand what is expected of them and ensure that the contract is fair and transparent.
Address intellectual property rights and confidentiality: Address any intellectual property rights and confidentiality issues that are relevant. This will help all parties understand what is expected of them and ensure that the contract is fair and transparent.
Define the termination and dispute resolution processes: Define the termination and dispute resolution processes that are required. This will help all parties understand what is expected of them and ensure that the contract is fair and transparent.
Include a force majeure clause: Include a force majeure clause that outlines what will happen if unforeseen circumstances occur. This will help all parties understand what is expected of them and ensure that the contract is fair and transparent.
Ensure that all parties sign the contract: Ensure that all parties sign the contract to indicate their agreement to the terms and conditions. This will help ensure that the contract is legally binding and enforceable.
Checklists and Templates for Quality Control
Quality control is the process of ensuring that products or services meet the required standards. To ensure that quality control is efficient and effective, it is important to use a checklist or template that includes the following information:
Develop a quality control plan: Develop a plan that outlines the quality control measures that are required. This will help ensure that all stakeholders understand what is expected of them and ensure that the quality control process is efficient and effective.
Establish quality control measures and standards: Establish the quality control measures and standards that are required. This will help ensure that all stakeholders understand what is expected of them and ensure that the quality control process is efficient and effective.
Train employees on quality control procedures: Train employees on the quality control procedures that are required. This will help ensure that all stakeholders understand what is expected of them and ensure that the quality control process is efficient and effective.
Conduct regular quality control audits: Conduct regular quality control audits to ensure that the required standards are being met. This will help identify any areas for improvement and ensure that the quality control process is efficient and effective.
Address non-conformances and corrective actions: Address any non-conformances that are identified and take corrective actions as required. This will help ensure that the quality control process is efficient and effective and that the required standards are being met.
Checklists and Templates for Shipping Documentation
Shipping documentation is the paperwork that is required for the shipment of goods. To ensure that shipping documentation is efficient and effective, it is important to use a checklist or template that includes the following information:
Provide accurate and complete product details: Provide accurate and complete details of the product that is being shipped. This will help ensure that the product is shipped to the correct destination and that the required customs clearance is obtained.
Include the origin and destination addresses: Include the origin and destination addresses for the shipment. This will help ensure that the product is shipped to the correct destination and that the required customs clearance is obtained.
Specify the shipping terms and conditions: Specify the shipping terms and conditions that are required. This will help ensure that all stakeholders understand what is expected of them and ensure that the shipping process is efficient and effective.
Determine the mode of transportation: Determine the mode of transportation that is required. This will help ensure that the product is shipped in the most efficient and effective manner.
Calculate the cargo ready date: Calculate the cargo ready date to ensure that the product is shipped on time.
Obtain the HTS or HS code for customs clearance: Obtain the HTS or HS code for customs clearance to ensure that the product is shipped in compliance with customs regulations.
Provide packaging details: Provide packaging details, such as carton dimensions, units per carton, and total units. This will help ensure that the product is shipped in the most efficient and effective manner.
Include special handling or stowing requirements: Include any special handling instructions.
Risk management in cross-border transactions is a critical aspect of international procurement and production. Identifying common risks and implementing strategies to mitigate them is essential for ensuring the success and sustainability of global business operations.
Common Risks in Cross-Border Transactions
Currency Risk: Fluctuations in exchange rates can significantly impact the cost of goods and services, potentially affecting the profitability of a transaction.
Political Risk: Political instability, changes in regulations, and trade disputes can disrupt supply chains and impact the overall success of a transaction.
Quality Risk: Variations in product quality and compliance standards across different jurisdictions can pose a significant risk to the success of a transaction.
Logistics Risk: Challenges related to shipping, customs, and transportation can lead to delays and disruptions, impacting the timely delivery of goods.
Legal Risk: Differences in laws and regulations across borders can lead to legal disputes and non-compliance issues, posing a risk to the transaction.
Strategies to Mitigate Risks
Currency Risk Mitigation: Implementing hedging strategies, such as forward contracts and options, to mitigate the impact of exchange rate fluctuations on transactions.
Political Risk Mitigation: Diversifying business partners and markets, monitoring political developments, and developing contingency plans to address potential political risks.
Quality Risk Mitigation: Implementing robust quality control measures, conducting thorough due diligence on suppliers, and establishing clear quality standards in contracts.
Logistics Risk Mitigation: Developing comprehensive logistics plans, maintaining open communication with logistics partners, and having contingency measures in place for potential disruptions.
Legal Risk Mitigation: Engaging legal experts, conducting thorough legal due diligence, and ensuring that contracts are clear, compliant, and reflective of the parties' obligations.
By proactively identifying and addressing these common risks, international buyers can enhance the resilience of their procurement and production processes, reduce the potential for disruptions, and ensure the successful execution of cross-border transactions. The insights and strategies provided by industry experts and regulatory authorities offer valuable guidance for businesses seeking to navigate the complexities of global trade and mitigate the associated risks effectively.
CONCLUSION
In conclusion, it's clear that the establishment of a streamlined, predictable framework is not just advantageous but essential for international buyers navigating the complexities of global manufacturing. By adhering to a standardized process, buyers can significantly mitigate risks, enhance efficiency, and foster stronger, more transparent relationships with manufacturing partners. This chapter has outlined key strategies and best practices to implement such a process, from the initial design phase through to final production, ensuring quality and consistency are maintained at every step.
Incorporating these guidelines into your operations will not only optimize your manufacturing outcomes but also position your business for sustainable growth and competitiveness in the international market. Remember, the strength of your manufacturing process lies in its adaptability to changing market demands and regulatory environments, all while maintaining the highest standards of quality and efficiency.
As we move forward to the next chapter on Packaging, it's important to carry forward the principles of standardisation and quality control to ensure that the final product not only meets but exceeds market expectations, arriving in the hands of consumers in perfect condition. The journey from concept to consumer is intricate and challenging, yet with the right processes in place, it can be navigated successfully to achieve exceptional results.
Read the Complete Topic
Chapter 1 - CROSS BORDER PRODUCT DEVELOPMENT
Chapter 2 - QUALITY MANAGEMENT SYSTEM (QMS)
Chapter 3 - COST OF SHIPPING
Chapter 5 - PACKAGING
Recommended

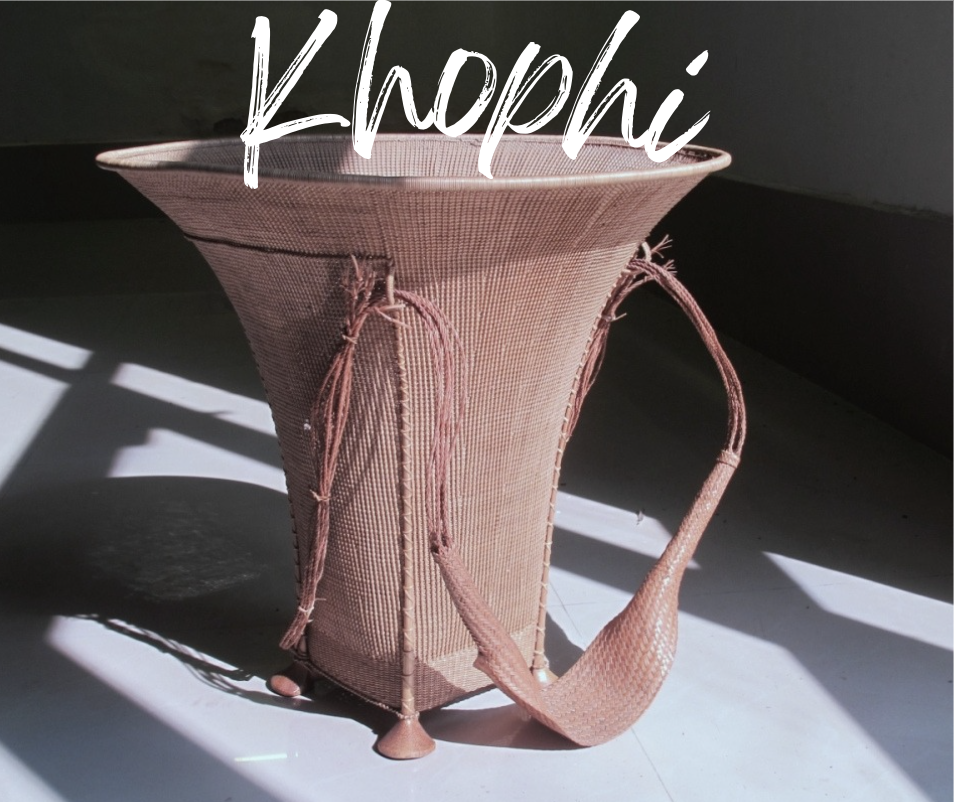
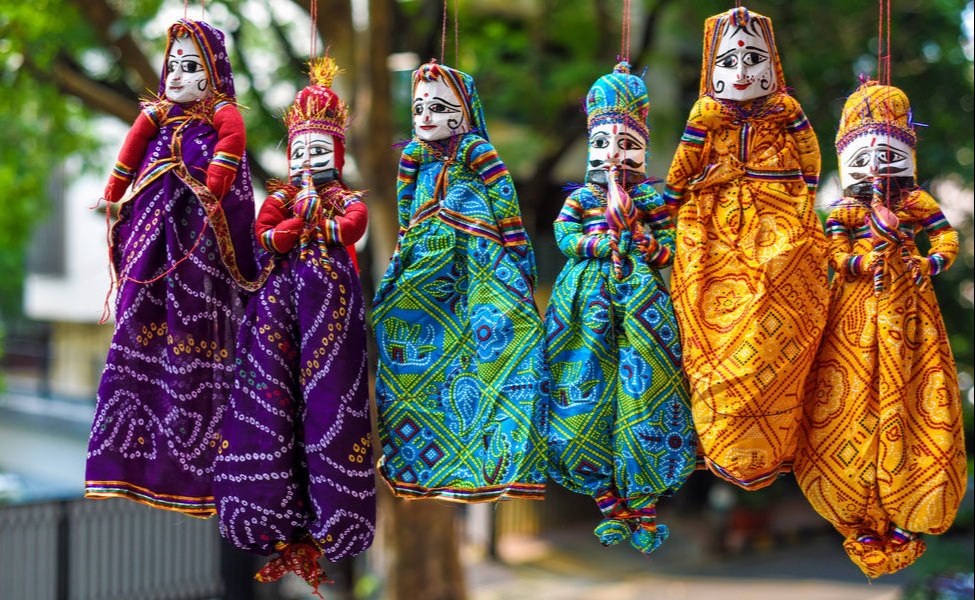
Wholesale / B2b Kathputli Puppets From Ahemdabad
Dec 16, 2024