The Ultimate Guide For International Buyers Navigating Manufacturing, Quality, And Logistics. CHAPTER 2
Feb 24, 2024 | Tanya Sachdeva
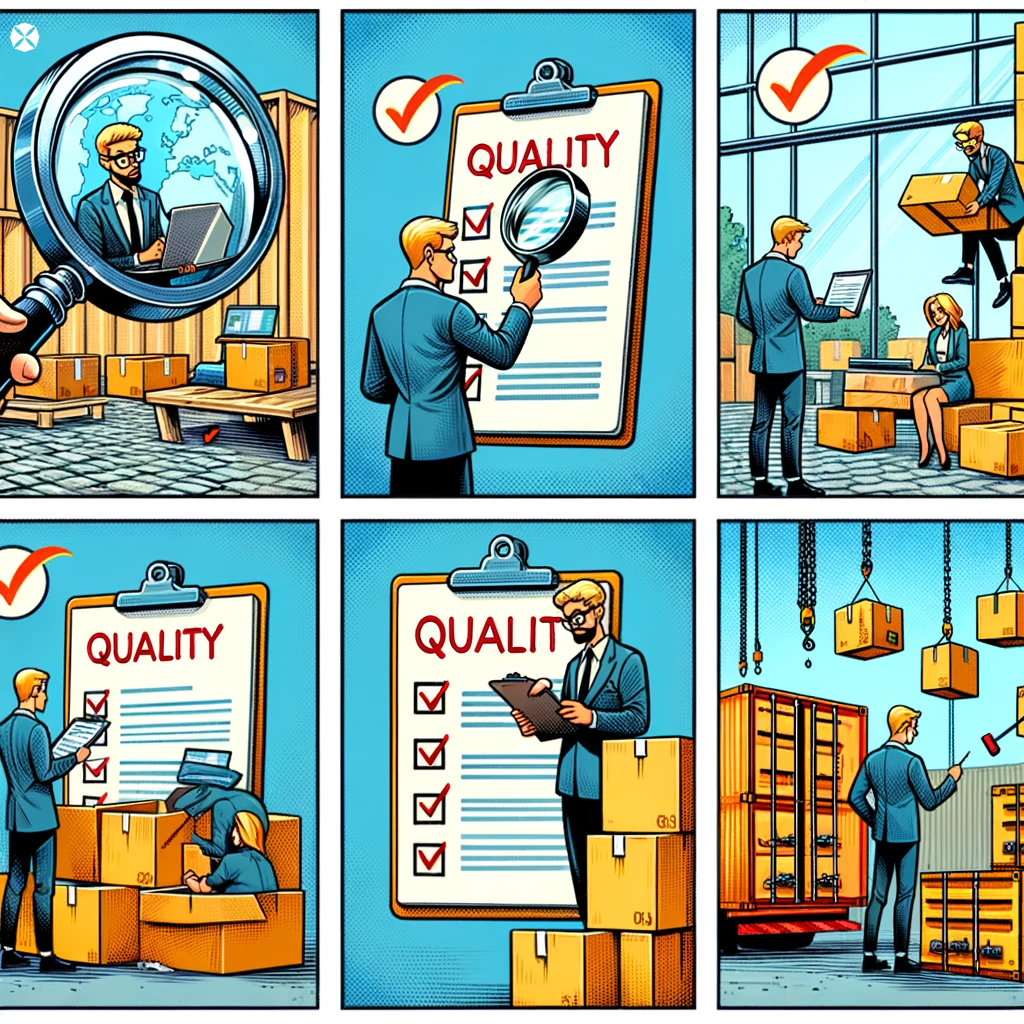
QUALITY MANAGEMENT SYSTEM (QMS)
A Quality Management System (QMS) is a structured framework that documents processes, procedures, and responsibilities for achieving quality policies and objectives. It is a comprehensive system designed to improve product and process quality, increase customer satisfaction, and ensure regulatory compliance. QMS is essential for handmade manufacturers, as it helps to maintain a competitive advantage in the global furnishings market by focusing on quality rather than just offering the lowest price.
The Importance of QMS
QMS is important for handmade manufacturers because it:
Ensures consistent quality and customer satisfaction
Reduces costs associated with rework and scrap
Improves efficiency and productivity
Enables continuous improvement
Ensures regulatory compliance
History and Development of QMS
QMS can be traced back to the late 13th century, with the American Society for Quality (ASQ) and the Process Excellence Institute (PEI) providing insights into its history and development. The original QMS concepts were developed by an American and implemented in Japan in the 1950s, with a focus on communicating how quality could be increased within an organisation.
QMS Challenges and Solutions
Handmade manufacturers may face challenges when implementing QMS, such as:
Alignment with organizational culture
Consistency across all operational levels
Technological adaptation
Resource management
Maintaining customer focus
To overcome these challenges, manufacturers should:
Secure support from top management
Engage employees in the process and product improvement efforts
Develop and implement a continuous improvement program
Utilize technology to improve quality control processes
Collaborate with suppliers and customers
QMS Resources
To learn more about QMS, manufacturers can refer to the following resources:
Quality Management System (QMS) by Quality-One
What is a Quality Management System (QMS)? by ASQ
Quality Management System Education and Resources
Quality Management System (QMS) by SimplerQMS
Quality Management System (QMS) Design & Implementation: A Comprehensive Guide
By understanding the importance of QMS and its history, handmade manufacturers can develop a robust QMS that will help them maintain a competitive advantage in the global furnishings market. In the next chapter, we will focus on the specific QMS requirements for handmade manufacturers.
Specific QMS Requirements for Handmade Manufacturers
Process Control and Risk Reduction: Implement processes that minimise risks and ensure consistent quality.
Documentation: Develop and maintain detailed quality control documentation, including inspection checklists, test procedures, and corrective action reports.
Process Improvement: Continuously improve processes to enhance quality and efficiency.
Supplier Management: Establish and maintain a supplier development program that includes regular audits, training, and collaboration to ensure quality standards are met.
Quality Control Technology: Utilize technology such as sensors, barcodes, and RFID tags to improve quality control processes and provide real-time data on product quality.
Collaboration: Encourage collaboration among all stakeholders, including suppliers, customers, and regulatory agencies, to ensure quality control processes are effective and efficient.
Employee Engagement: Engage employees in quality control processes and encourage them to take ownership of quality control initiatives.
Compliance: Adhere to all relevant regulatory requirements and industry standards, including those related to product safety, environmental protection, and social responsibility.
Certification: Seek certification, such as ISO 9001:2015, to demonstrate commitment to quality standards and to maintain a competitive advantage.
To implement these requirements, handmade manufacturers should:
Map out their manufacturing processes to identify inefficiencies, risks, and areas for improvement.
Utilize technology such as sensors, barcodes, and RFID tags to improve quality control processes and provide real-time data on product quality.
Encourage collaboration among all stakeholders, including suppliers, customers, and regulatory agencies, to ensure quality control processes are effective and efficient.
Engage employees in quality control processes and encourage them to take ownership of quality control initiatives.
Adhere to all relevant regulatory requirements and industry standards, including those related to product safety, environmental protection, and social responsibility.
Seek certification, such as ISO 9001:2015, to demonstrate commitment to quality standards and to maintain a competitive advantage.
QUALITY ASSURANCE
Quality assurance is a critical aspect of the Quality Management System (QMS) for handmade manufacturers. It involves implementing a comprehensive quality assurance program that includes first-article inspections, in-process checks, and final pre-shipment inspections. Utilizing qualified quality engineers and auditors to ensure that products meet or exceed customer expectations is also essential
Quality Assurance Program
A quality assurance program should include the following:
First-Article Inspections: Inspect the first article produced to ensure that it meets all customer requirements and specifications.
In-Process Checks: Conduct regular checks during the manufacturing process to ensure that products are being produced to the required quality standards.
Final Pre-Shipment Inspections: Inspect the final product before shipment to ensure that it meets all customer requirements and specifications.
Qualified Quality Engineers and Auditors: Utilize qualified quality engineers and auditors to ensure that products meet or exceed customer expectations.
Quality Assurance Challenges and Solutions
Handmade manufacturers may face challenges when implementing a quality assurance program, such as:
Resource Management: Ensuring that there are enough resources to implement the program.
Technological Adaptation: Adapting to new technologies that can improve quality assurance processes.
Maintaining Customer Focus: Ensuring that the program is focused on meeting customer needs.
To overcome these challenges, manufacturers should:
Secure Support from Top Management: Secure support from top management to ensure that there are enough resources to implement the program.
Utilize Technology: Utilize technology such as sensors, barcodes, and RFID tags to improve quality assurance processes.
Collaborate with Customers: Collaborate with customers to ensure that the program is focused on meeting their needs.
Quality Assurance Resources
To learn more about quality assurance, manufacturers can refer to the following resources:
Quality Assurance and Quality Control by the International Organization for Standardization (ISO)
Quality Assurance and Quality Control in Manufacturing by the American Society for Quality (ASQ)
Quality Assurance and Quality Control Services by Pro QC International
By implementing a comprehensive quality assurance program, handmade manufacturers can improve their quality control processes and maintain a competitive advantage in the global furnishings market. In the next chapter, we will focus on the specific quality control training requirements for handmade manufacturers.
QUALITY CONTROL TRAINING
Providing ongoing training to employees on quality control best practices is essential for handmade manufacturers to maintain a competitive advantage in the global furnishings market. This training should include the use of quality tools such as statistical process control (SPC), failure mode and effects analysis (FMEA), and design of experiments (DOE).
Quality Control Training Program
A quality control training program should include the following:
SPC Training: Statistical process control (SPC) is a method of quality control that uses statistical methods to monitor and control a process. SPC training should cover the basics of statistical process control, including control charts, process capability analysis, and statistical process control software.
FMEA Training: Failure mode and effects analysis (FMEA) is a method of quality control that identifies potential failures in a process or product and determines their effects. FMEA training should cover the basics of FMEA, including the FMEA process, FMEA software, and FMEA case studies.
DOE Training: Design of experiments (DOE) is a method of quality control that uses statistical methods to design experiments and analyze data. DOE training should cover the basics of DOE, including the DOE process, DOE software, and DOE case studies.
What are some examples of quality control training programs for employees?
Quality Awareness Training: This training covers the concepts, principles, and benefits of quality management and quality standards, such as ISO 9001.
Quality Tools and Techniques Training: A more advanced and specific training that teaches employees how to use various quality tools and techniques, such as the PDCA cycle, the 5 Whys, the fishbone diagram, or the Pareto chart.
Quality Audit Training: A specialised and formal training that prepares employees to conduct or participate in quality audits, either internal or external.
Leadership Development Program: A program that develops leaders who can manage teams and make strategic organisational choices.
Customer Service Training: Training that focuses on offering exceptional service, addressing complaints, and promoting client loyalty.
Compliance and Safety Training: Training that ensures employees understand and adhere to relevant regulations and safety standards.
These programs can be delivered through various formats, including online courses, in-person workshops, and on-the-job training, to ensure that employees receive the necessary knowledge and skills to perform their tasks effectively and contribute to the organisation's quality goals.
SUPPLIER DEVELOPMENT FOR HANDMADE MANUFACTURERS
Establishing a supplier development program is crucial for handmade manufacturers to ensure that suppliers meet quality standards. This program should include regular audits, training, and collaboration to help suppliers improve their quality management systems and processes.
Benefits of Supplier Development
Improved Supplier Performance: Working closely with suppliers can identify and address gaps in quality, delivery, cost, innovation, and sustainability, leading to improved supplier performance.
Long-Term Relationships: Cultivating long-term relationships with suppliers can empower them to grow and succeed, leading to better overall supplier relationships.
Cost Reduction: Supplier development can help suppliers remove cost and waste from their businesses, leading to cost reduction.
Innovation: Encouraging suppliers to collaborate to produce unique solutions can lead to more innovative thinking and increased competitiveness.
Regulatory Compliance: Ensures regulatory compliance by working with suppliers to adhere to relevant regulations and standards.
Supplier Development Program
A supplier development program should include the following:
Assessing Needs and Objectives: Assessing your own needs and objectives and aligning them with your business strategy and customer expectations.
Designing a Customized Plan: Designing a customized and collaborative plan for each supplier, based on their specific needs and objectives, and your mutual interests and benefits.
Reviewing and Improving: Reviewing and improving your supplier development program, and recognizing and rewarding your suppliers for their achievements.
Supplier Development Challenges and Solutions
Handmade manufacturers may face challenges when implementing a supplier development program, such as:
Resource Management: Ensuring that there are enough resources to implement the program.
Supplier Resistance: Overcoming supplier resistance to change and collaboration.
Communication: Ensuring effective communication between the manufacturer and the supplier.
To overcome these challenges, manufacturers should:
Secure Support from Top Management: Secure support from top management to ensure that there are enough resources to implement the program.
Incentivize Suppliers: Incentivize suppliers to participate in the program by offering rewards and recognition for their achievements.
Establish Clear Communication Channels: Establish clear communication channels between the manufacturer and the supplier to ensure effective communication.
Supplier Development Resources
To learn more about supplier development, manufacturers can refer to the following resources:
By establishing a supplier development program, handmade manufacturers can improve their supplier relationships, reduce costs, and increase innovation, leading to a competitive advantage in the global furnishings market.
CONCLUSION
In conclusion, handmade manufacturers in the global furnishings market must prioritize quality control to maintain a competitive advantage. A Quality Management System (QMS) is a structured framework that documents processes, procedures, and responsibilities for achieving quality policies and objectives. Implementing a comprehensive QMS can ensure consistent quality, reduce costs, improve efficiency and productivity, enable continuous improvement, and ensure regulatory compliance. Handmade manufacturers may face challenges when implementing QMS, such as alignment with organizational culture, consistency across all operational levels, technological adaptation, resource management, and maintaining customer focus. However, by securing support from top management, engaging employees in the process and product improvement efforts, developing and implementing a continuous improvement program, utilizing technology to improve quality control processes, and collaborating with suppliers and customers, these challenges can be overcome. Additionally, handmade manufacturers must establish a supplier development program that includes regular audits, training, and collaboration to help suppliers improve their quality management systems and processes.
By implementing a comprehensive quality assurance program that includes first-article inspections, in-process checks, and final pre-shipment inspections, and utilizing qualified quality engineers and auditors, handmade manufacturers can ensure that products meet or exceed customer expectations. Providing ongoing quality control training to employees is also essential to maintain a competitive advantage. By following these guidelines, handmade manufacturers can improve their quality control processes and maintain a competitive advantage in the global furnishings market.
Read the Complete Topic
Chapter 1 - CROSS BORDER PRODUCT DEVELOPMENT
Chapter 3 - CROSS BORDER SHIPPING
Chapter 4 - A STANDARDISED PROCESS FOR INTERNATIONAL PROCUREMENT AND PRODUCTION TO STREAMLINE OPERATIONS AND REDUCE RISKS.
Chapter 5 - PACKAGING
Recommended
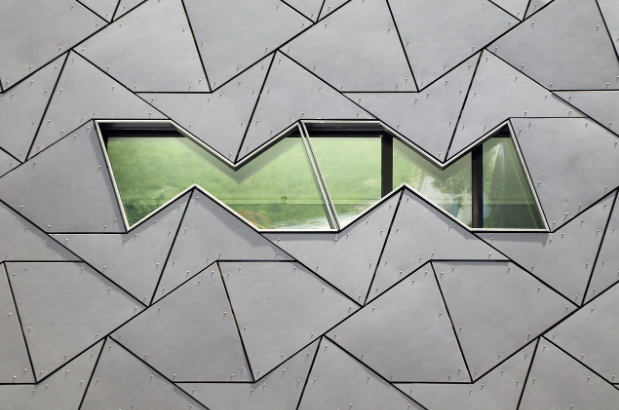

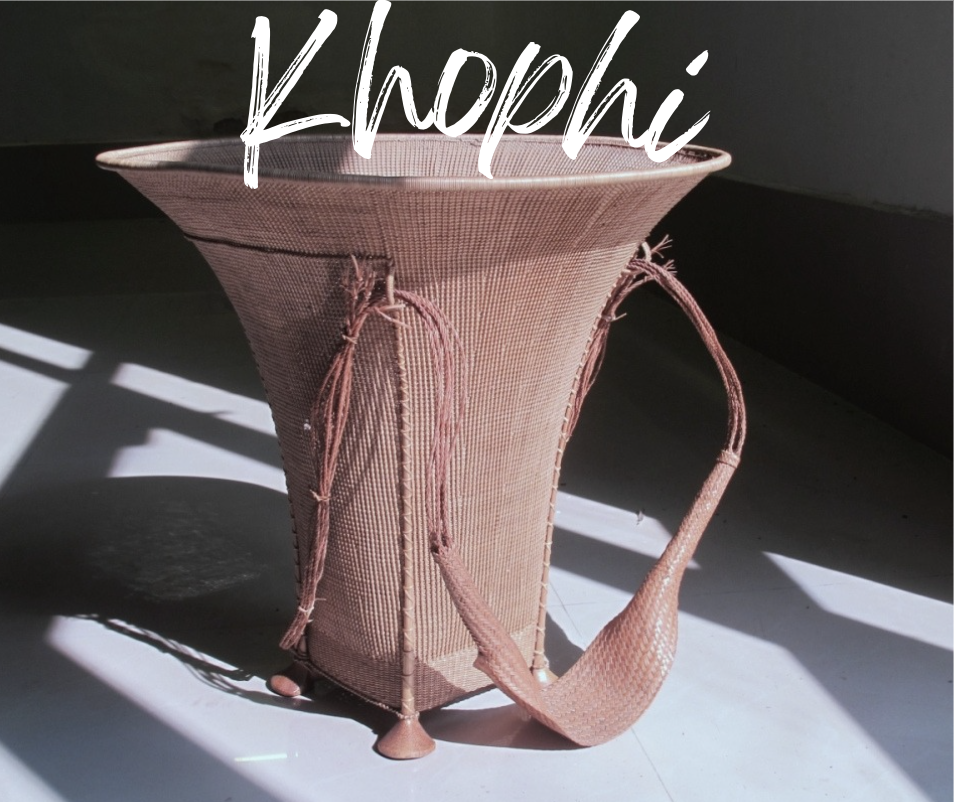