6 Fundamental Warehouse Operations: A Guide To Optimizing Your Warehouse
Sep 05, 2023 | Salauddin Shaik
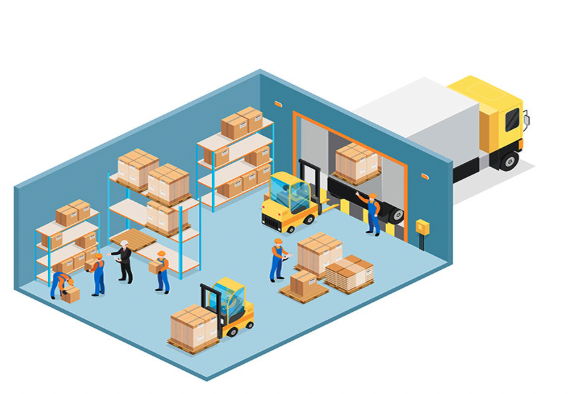
Because a warehouse needs to be a functioning structure for a variety of users, designing one might be challenging. A well-designed warehouse enables employees and the organization as a whole to operate securely, efficiently, and productively, whether it's administrators in the office areas or the people on the ground loading, unloading, picking, and dispatching.
Introduction
Warehouse management is a crucial part of a company's operations. It involves the storage and movement of goods, and it can be difficult to get right.
The good news is that there are plenty of strategies for improving your warehouse management. Here are some of the most important ones:
1) Cross-docking - This is a technique that allows you to increase efficiency by reducing the amount of time it takes to receive and unload shipments. It involves storing goods in the same location so they can be transferred directly from one truck to another.
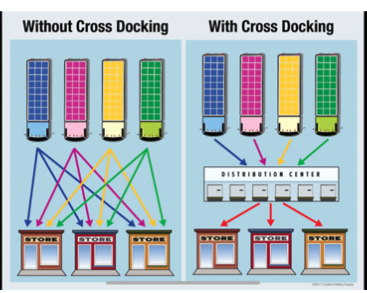
2) Compliance - Compliance refers to following regulations set out by health and safety agencies, such as those related to hazardous materials. It's important because these regulations protect workers and make sure their working environment is safe.
3) Collaboration - This means working with other companies or organizations in order to achieve common goals or solve problems together. For example, two companies might collaborate on a project if they both have different strengths but still need each other's expertise in order to succeed at completing it successfully on time!
In this article you will learn and understand how a warehouse is managed.
Rural Handmade is a website dedicated to helping businesses find the perfect warehouse for their needs. We've got listings from all over the country, and we'll help you find what you're looking for.
We know how important it is to have the right space for your business, so we make it our mission to make sure you get exactly what you need.
Check out our website before diving right into the procedure.
We know how important it is to have the right space for your business, so we make it our mission to make sure you get exactly what you need.
Check out our website before diving right into the procedure.
How does the Warehouse Operate and Steps to Optimize them:
Inventory in the warehouse typically runs in cycles. The inbound procedure takes place at night, while the outbound procedure gets going in the early hours of the morning.
Before we jump into the processes, there are some safety and important things to understand.
Safety Precautions:
To improve safety and efficiency in your warehouse, you must make sure that everyone who works there is following company guidelines and procedures. There are many different rules and regulations that you must follow to ensure the safety of all workers and customers. You need to ensure that all employees are wearing proper safety gear, including hardhats with reflective bands, steel-toe boots and gloves.
You also need to make sure that all equipment is safe for use and working correctly. You should have a clear understanding of how each piece of equipment should be used so that it can be properly maintained by trained staff members who know how to fix any problems or malfunctions before they become dangerous or costly problems.
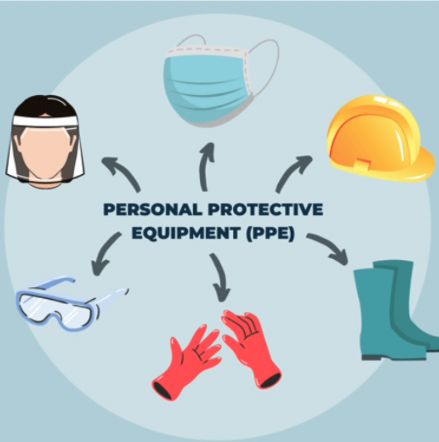
We have a wide variety of safety equipment for your warehouse and workplace.
From hard hats and earplugs to forklifts and fire extinguishers, we have what you need to keep your employees safe.
Important Points:
You will need to have a good understanding of how each process works before you can learn how to do them correctly. For example, if you don't understand how the warehouse operations system works in your company's case, then you won't know where shipments go once they arrive at your warehouse and how they are supposed to be processed. So it's important that you understand every part of a process before learning how to perform it step-by-step!
Digital Platform:
As a warehouse employee, you are responsible for knowing your company's warehouse software. This software is designed to keep track of all the products that come into and leave your facility, as well as how they are stored, shipped, and billed. It is important that you know how to use this software because it will help you do your job more efficiently and correctly.
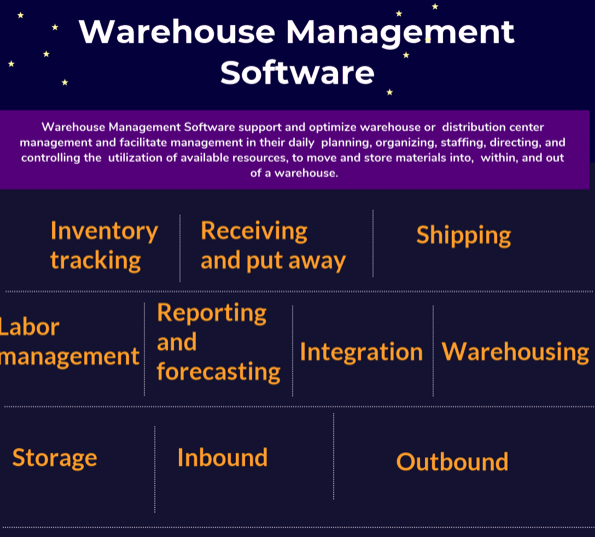
Warehouse inventory management software is an essential tool for any company that deals with the storage and distribution of products. While it may seem like a simple concept, when you consider the complexities involved in running a warehouse, it's easy to see why so many companies struggle with this process.
Warehouse inventory management software can help companies streamline their logistics processes by automating or semi-automating their inventory management activities. This includes tasks like receiving new goods, sorting them by type and location, storing them appropriately, and distributing them to customers as needed. It also includes tasks like managing customer orders and ensuring they are fulfilled correctly.
The benefits of using warehouse inventory management software include:
- Increased efficiency: Warehouse managers can use this software to reduce labor costs by eliminating much of the manual work associated with managing an efficient warehouse operation.
- Improved accuracy: The software provides valuable insights into what needs attention within your facility, so you can act on those insights quickly before problems arise.
- Enhanced security: The software helps protect against theft and employee fraud by providing real-time access controls over who can do what within your facility's networked computers.
The first step in using inventory management software is to set up your accounts. This can be done through entering the name of the product, its description and then entering the correct cost per unit or total cost of each item. You will also need to create a warehouse where items can be stored.
Once you have entered all of your information into the system, it will begin calculating how much inventory you have left and how much you need to order from suppliers in order for them to arrive at your warehouse before they run out completely. In addition, it can tell you when new shipments are due so that you can prepare for them on time without having something happen like running out of stock unexpectedly due to poor planning skills or ignoring issues until they become too big (which often happens).
For example, Amazon uses a dolphin app for warehouse operations.
The app allows employees to use a mobile device to scan items as they fill orders, which helps them ensure that the right items are going into boxes.
The app also allows employees to take photos of damaged or defective goods, which helps Amazon keep track of what is being sold.
Amazon Dolphin Software, Inc., is a leading provider of warehouse management software solutions for businesses in the retail and distribution industries. Dolphin's software helps companies save time, money, and effort by automating their processes.
Dolphin's solutions automate and optimize how your company processes orders, tracks inventory, manages product shipments and returns, calculates shipping costs, and much more.
Dolphin's products are designed to work seamlessly with your current ERP system or inventory management system so that you can integrate them into one easy-to-use platform.
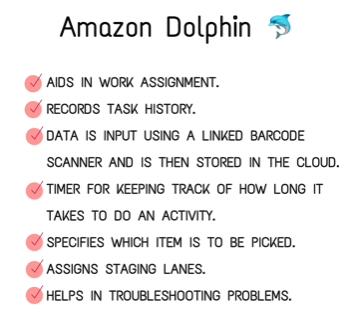
Each employee receives a different login ID.
How do you set up an Inventory Management Software for your Business?
There are many inventory management software options out there, but it's best to get the one that works best for your business.
You can get inventory management software from third party companies as well as from your own internal IT team. If you want to go with a third party product, make sure it has all of the features you need in an inventory management system. You should also consider how much training will be required for your employees before they start using the system and whether or not they will be able to learn it on their own or if they will need outside help from an experienced expert who knows how to use this kind of software.
If you decide that it would be better for your company if you got an internal IT team member to create an inventory management system instead, then make sure that person has enough time available so that they can work on creating such a program right away instead of having them wait until later when they have more free time available before starting on such a project again!
If you are looking for a third party company to provide you with inventory management software, there are many options available. You can find companies that specialize in providing this type of software, or you can look for other types of companies that offer it as part of their service. Click here to know more about top warehouse softwares.
6 Fundamental Warehouse operations and how to optimize them.
Receiving:
At the pier where they are received, products are either manually put together onto pallets or forked off of trailers. The goods are subsequently brought in using crates and conveyor belts. When any objects are lost or misplaced, troubleshooting is necessary. A quality control is carried out on the received items to look for any damage or anomalies before moving on to the next step.
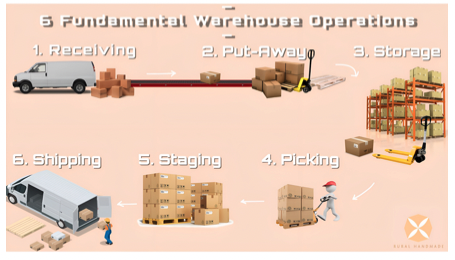
The freight is divided into that arriving directly from a vendor, such as an Amazon Fulfillment by Amazon seller, and that coming from another Amazon facility (FBA). Small businesses can expand their customer bases by using FBA, where Amazon chooses, packs, ships, and offers customer care while small businesses keep their goods at fulfillment centers. Small businesses and independent sellers account for 50% of all items sold on Amazon.com.
You might be wondering about where to get the equipments.
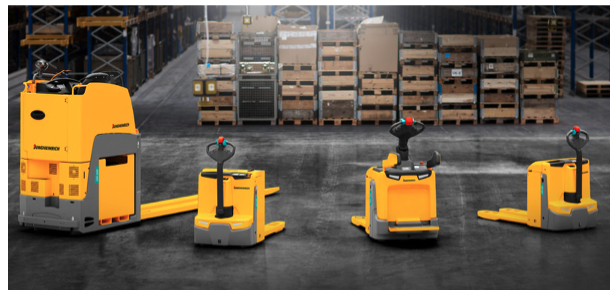
We've got you covered!
At Rural Handmade, We have everything you need for your warehouse. From office equipment to inventory control, we have what you need to keep your business running smoothly. We can't wait for you to see our selection!
We have the best quality products, the most affordable prices, and the best customer service in the industry. Our company is committed to providing customers with high-quality goods and services at a reasonable price.
We have a large list of warehouses with all kinds of equipment, from small to large.
Put-Away:
The put-away procedure is a series of steps that a worker follows to put an item away in the warehouse. This step-by-step guide will help you put away your items quickly and easily!
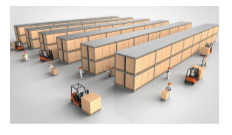
1. Start by picking up an item that you need to put away.
2. Follow the path to the correct bin or shelf (if you're using a warehouse with aisles).
3. Put the item down in the correct spot.
4. If you're at an aisle, move down to the next row and repeat step 1 until you have finished putting away all of your items.
Sounds like you need to shop more, aye?
We got you! Shelves? Pallets? Bins? You name it.
Rural Handmade is always the way to go.
Storage/Stowing:
Stowing is the process of organizing and storing materials in a warehouse. It is often done by the warehouse manager, but it may also be handled by employees at other levels within the organization. Storing materials in a warehouse involves stowing them according to their location and function within the company.
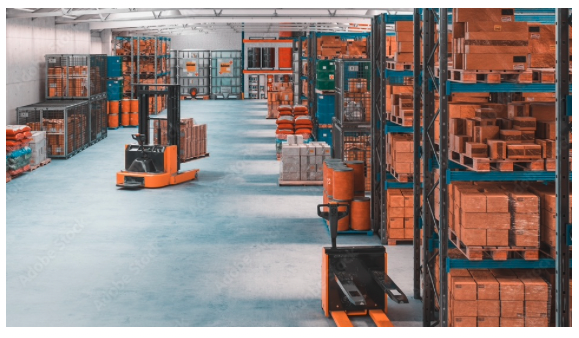
The act of stowing involves placing new merchandise in a proper storage space for later retrieval.
The primary responsibility of a stow associate in an Amazon facility is to accept incoming merchandise, organize it into storage spaces like pods or racks (in VNA facilities), and then scan it to input it into the inventory system.
At Amazon fulfillment centers, everything is arranged haphazardly rather than being organized like it would be in a physical store, with gadgets on one aisle and books on another.
According to the location or delivery path, the items are stored in the aisles' cargo bags.
If you want to make sure that your order fulfillment goes smoothly, keeping track of your inventory is essential. To keep track of all your products, proper inventory management necessitates a solid SKU¹ architecture.
You may rearrange parts, cycle count goods, and complete a variety of other jobs in the warehouse more quickly and accurately by using barcode scanners² rather than by hand. This is a significant benefit because it enables your warehouse staff to accomplish more in the same amount of time while also continuously updating your inventory data. Advanced inventory monitoring solutions can actually be downloaded as applications on any smartphone or tablet, converting your already-owned mobile devices into barcode scanners without the need to purchase specific hardware.
Depending on the type of facility they work in, stowers carry out their duties in various ways. For example, in PIT centers and non-robotic facilities, they use order pickers to stow items in racks³, while in facilities run by Amazon Robotics (AR), they stow items in pods that are delivered by robots.
¹ SKU, which stands for Stock Keeping Unit, is a special number used to keep track of inventories internally. SKUs are alphanumeric and should list the most crucial details about a product, such as the cost, style, color, brand, etc. Ideally, SKU information should be arranged from most important to least important, or from the information you need most to the least.
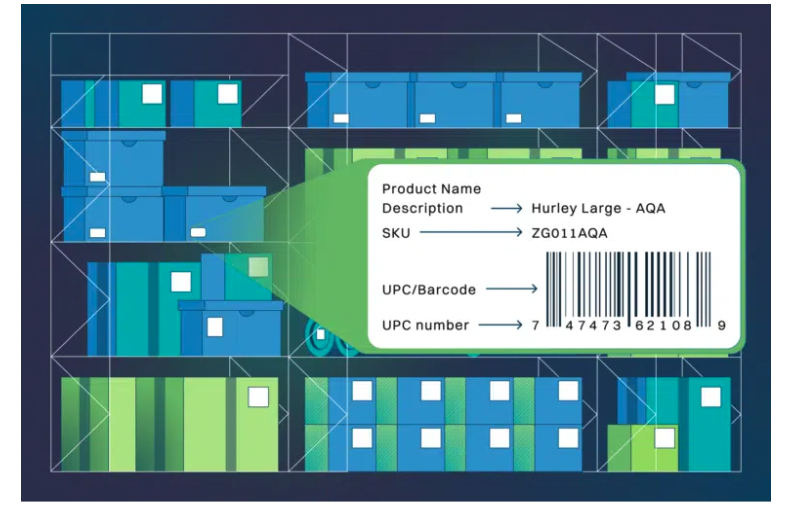
² The MDU, or multiple dwelling unit, is used, and it includes a built-in barcode scanner. It is connected to the company’s software used for managing warehouse inventory.
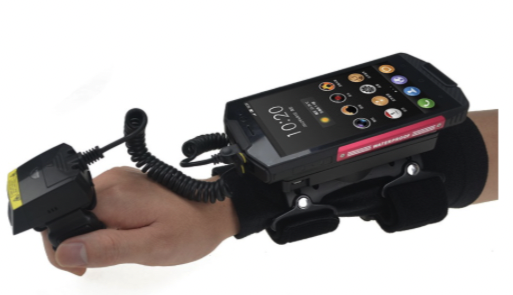
Click here to learn more about Handheld Scanners.
³ A storage solution known as a warehouse racking system is made to stack materials in multiple-level, horizontal rows. These solutions can assist you in sorting goods to simplify operations while managing and making better use of your warehouse space.
At Rural Handmade, we know that you're looking for a great place to store your products.
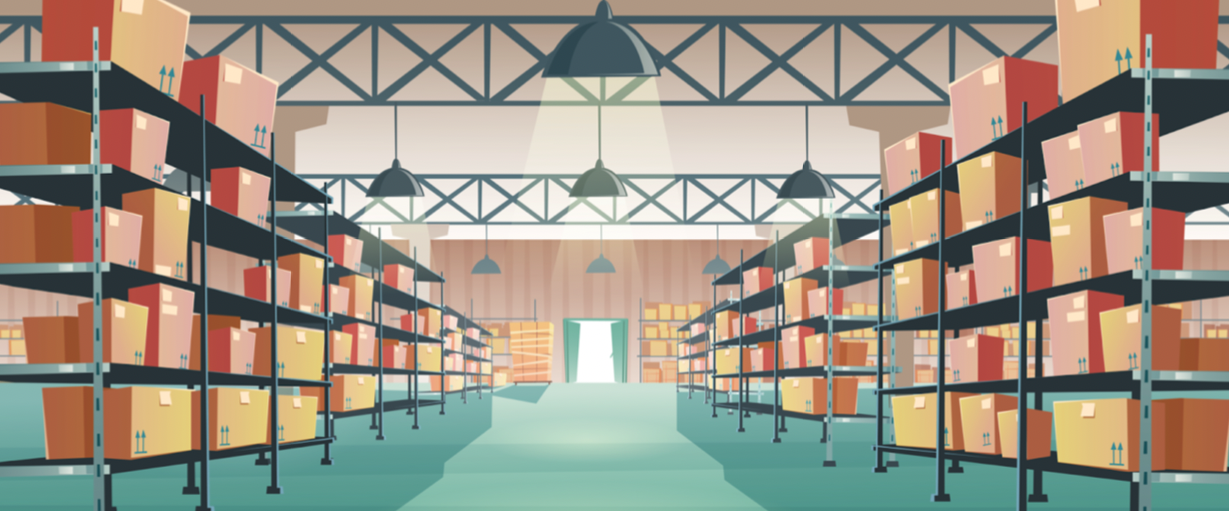
That's why we've got racks, barcode scanners, and more. We can help you get your business up and running in no time!
Picking:
Picking is the process of retrieving appropriate items from storage and placing them in Carts. The person responsible for picking is known as a picker.
The Warehouse Management software instructs the picker to select specific items and bags from the racks that must be delivered along a particular route or to a particular address. It is accomplished with the use of a barcode scanner used to read the merchandise's codes.
The picking process must be completed within a certain amount of time so that it does not interfere with other operations at the warehouse.
Warehouse inventory management software helps you manage your picking process by providing you with real-time access to your entire warehouse, including all of its parts and pieces. You'll be able to track each item as it progresses through its journey from storage location to final destination so that nothing gets lost along the way.
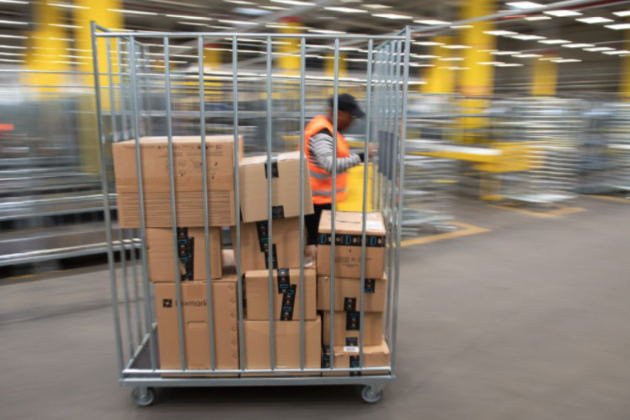
Once all the items have been sent to their appropriate locations, they can be picked again by other workers.
We have a warehouse full of warehouse carts!
Rural Handmade is proud to offer warehouse carts in a variety of sizes and styles. Whether you're looking for a basic utility cart, or something more… tailored? We've got it all!
We also supply warehouse carts from anywhere—whether you're just looking to stock up on your favorite model, or you need to replace one that's been lost or stolen, we have what you need.
Staging:
Staging is a critical aspect of warehouse management. The most basic form of staging involves creating a place for items to sit before they are shipped out. This can be as simple as putting boxes in a random order on the floor, or as complex as organizing them into categories by product line, then subcategorizing by size and color.
The staging lanes at Amazon are determined by the Dolphin app, and carts with selected items must stage in these lanes in order to be picked for delivery.
The staging lane is a buffer between the main flow of traffic and the sorting area where goods are grouped by destination. This allows for faster processing times by removing the need for multiple handlers to handle each item individually.

Staging is a process in which products are moved from one area to another. It is important that this process is done correctly, as it can affect the amount of space needed and the efficiency of your warehouse.
For example, when staging inventory before it is shipped out, you do not want to put all of your inventory on one side of the warehouse. This would mean that there would be no room for new shipments to come in or for any other activity to take place.
Instead, you should set up a staging area near your shipping dock so that items can be moved immediately after they are received and then taken to their final destinations once they have been processed.
This Process involves the following steps:
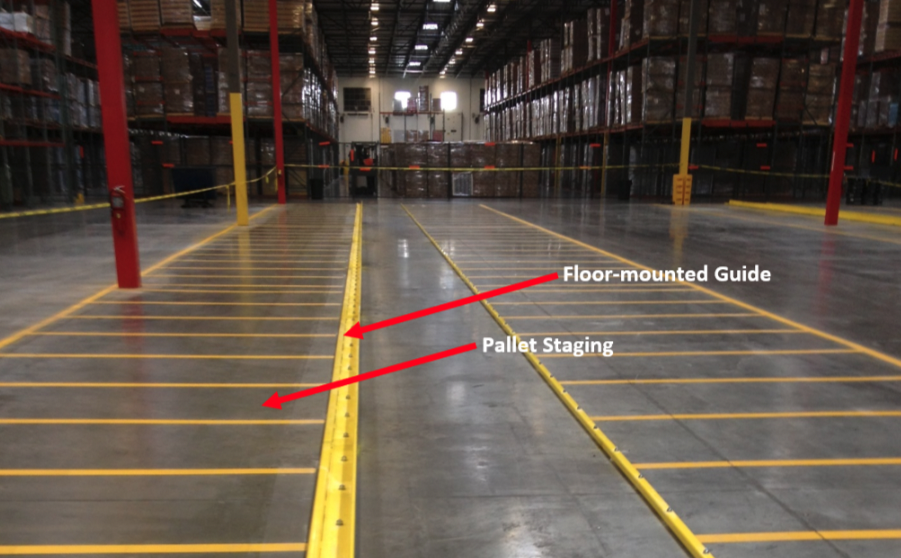
1. Set up the staging area for specific items, which will be picked by workers to fill orders
2. Pickers put items into bins designated for each order or customer, and then load those bins onto a conveyor belt that transports them to an outbound shipping area
3. The outbound shipping area prints labels with shipping information, attaches them to each bin, and sends them off through another conveyor belt to be loaded onto trucks for delivery
You want to make sure that the products are clearly marked and simple to find when it comes time to transport them. It's crucial to identify each cart specifically for this purpose. Each cart can have its own distinctive label, such as "Cart-2A," which will also be determined by the dolphin app. Additionally, the staging lane and route numbers must be labeled.
Shipping:
The merchandise in the staged carts is then put into trailers or delivery trucks for distribution to customers.
This is the process of getting products from the warehouse to the delivery vehicle. This can be done in two ways: by pallet or by truck. Pallet loading is a simple, low-cost process that can be used for small loads and is generally reserved for products that are not highly sensitive to damage during shipping. Large objects such as furniture or electronics require more expensive pallet handling equipment.
The goal of loading is to get the product to the desired location, where it can be delivered. Loading can take place anywhere in the warehouse, although it is often done near the warehouse entrance or exit.
It's important to get your shipping process right from the start so you can avoid wasting time and money later. Here are some tips:
1) Make sure your shipping process is automated as much as possible. This will save everyone involved in the process a lot of time and allow them to focus on other tasks. You can also use automation to cut down on human error and make sure that everything gets done correctly each time without fail.
2) Use technology such as RFID tags or barcodes to track shipments through their entire journey so you know exactly where they are at all times throughout the warehouse management process (including when they're being loaded onto trucks, how long they've been sitting in transit, etc.). This helps you monitor overall efficiency levels within your organization's efforts toward achieving goals like this one!
3) Have clear guidelines for employees about what types of materials should be used for each type of shipment: For example, if something needs special handling due to its weight or fragility.
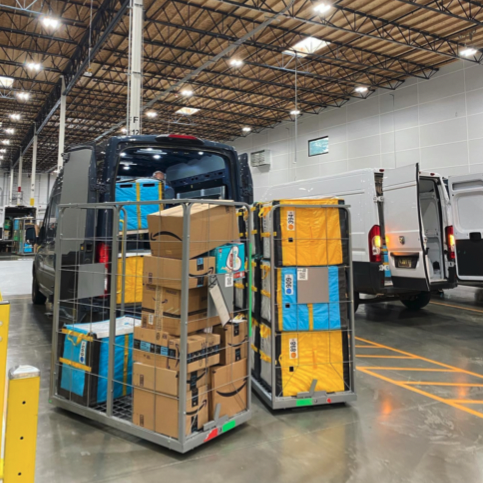
You've got a great idea for a new business. You've got the drive to make it happen, and you've done your homework—you know exactly what you need to get started.
But when it comes to actually opening up shop and setting up your own warehouse, where do you start? What's involved? What will you need? And how much will it cost?
At Ruralhandmade.com, we can help! We provide any support needed in opening a warehouse. Whether you need help with design or construction, we're here for you. Just give us a call to get started today!
Additional Resources
https://control.com/technical-articles/introduction-to-warehouse-management-systems-wms/
https://control.com/technical-articles/introduction-to-warehouse-management-systems-wms/
https://time.com/5836036/amazon-delivery-coronavirus/
https://www.nbcnews.com/business/business-news/behind-curtains-amazon-shadow-industry-black-hat-consultants-alter-listings-n1240982
https://articles.cyzerg.com/warehouse-processes-how-to-optimize-them
Recommended

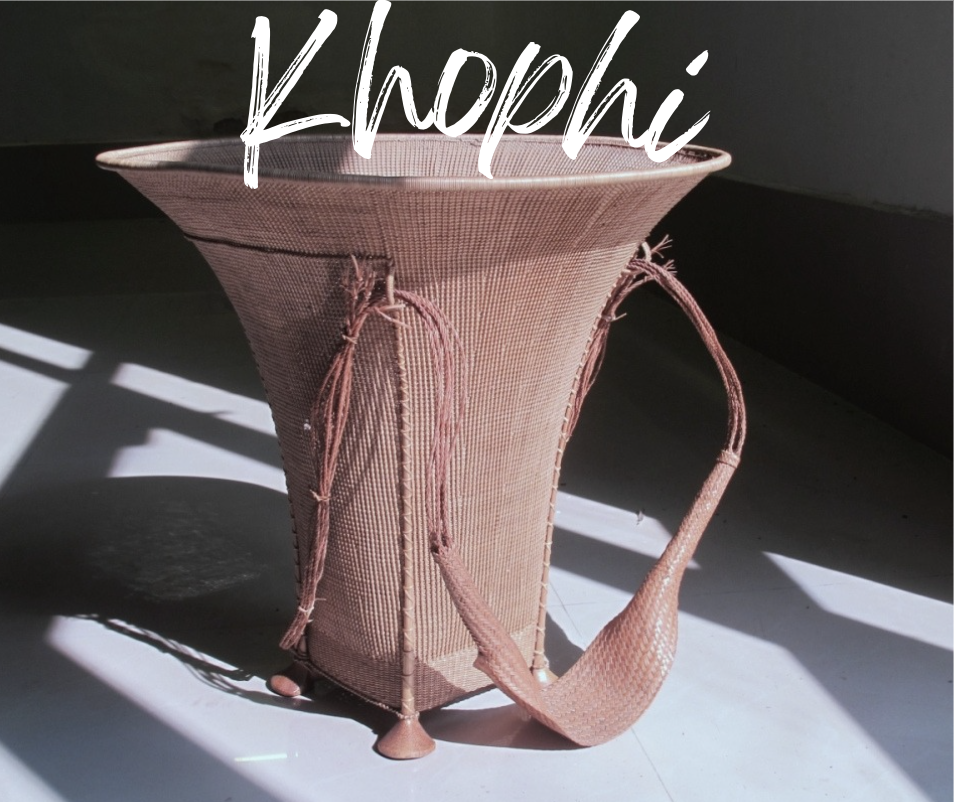
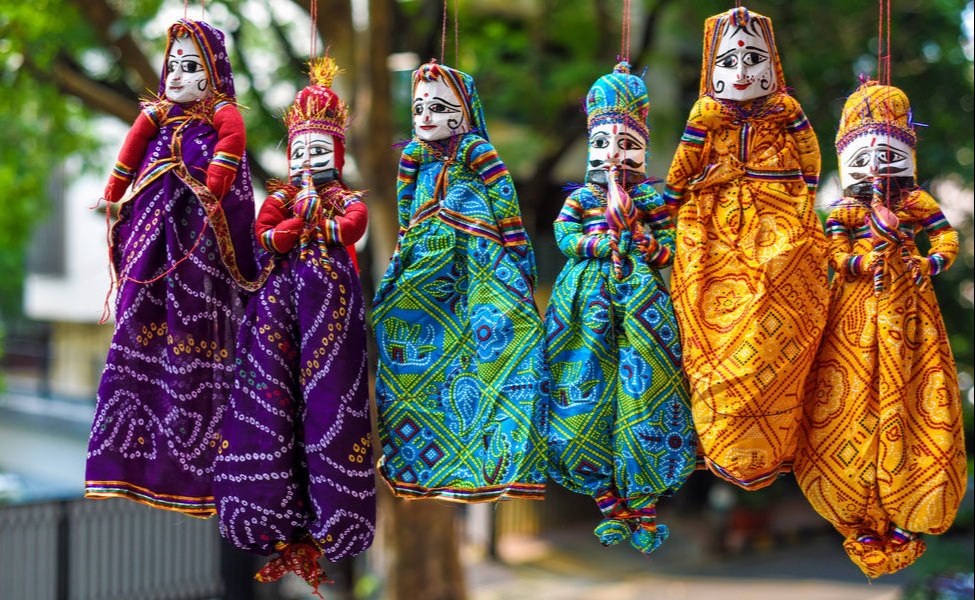
Wholesale / B2b Kathputli Puppets From Ahemdabad
Dec 16, 2024