Ultimate Guide To Plastic Inlay On Wood
Aug 31, 2024 | Shagun Sneha
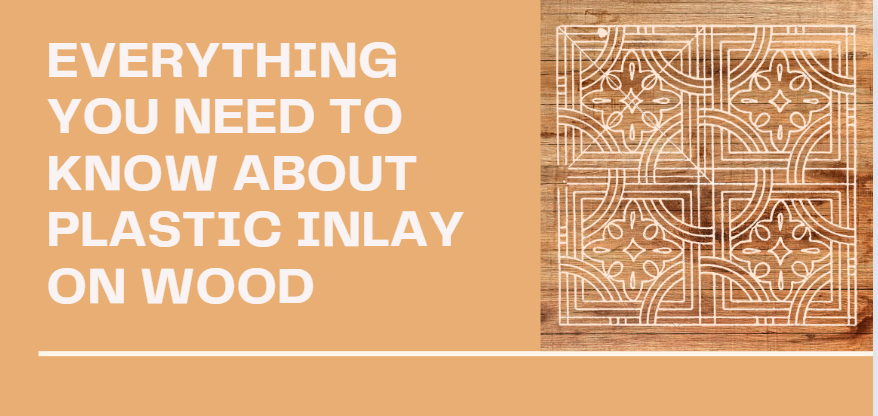
HISTORY
In the Punjab region, the art of wood inlay work began flourishing approximately 200-250 years ago. Initially, artists applied their skills and techniques to Indian musical instruments such as piano keys, veena, swarmandal, taanpura, and sitar. Over time, these artisans expanded their craft to include furniture items like inlaid tables, chairs, wooden almirahs, jewelry boxes, chest boxes, trays, and other daily use items, often decorated with ivory. The use of high-quality woods such as shisham (Sissoo), rosewood, teak (sagwan), and ebony were prevalent, providing a sturdy base for the complex ivory inlay designs.
Around 1950, the unique craftsmanship of wooden products from Hoshiarpur gained popularity both in India and abroad, leading to the establishment of export houses in the region. However, the growing scarcity of ivory and a government-imposed ban on its use and sale in 1975 led artisans to explore alternative materials. They began using gold, silver, aluminium, brass, camel bone, conch shells, pearl, and high-quality acrylic plastic for inlay work.
By the late 1980s, approximately 1700 families in Hoshiarpur were engaged in this profession, earning their livelihood through this craft and becoming skilled in inlay work. Unfortunately, exploitation by the prominent business houses and the scarcity of raw materials led many families to abandon the trade. Despite these challenges, the art form has survived, albeit in a diminished state, thanks to government support and efforts to preserve it.
Today, only a few individuals continue to learn this unique art, often driven by passion or academic interest. Notably, the work of artist Atta Singh has been showcased in a UK museum, highlighting the global appreciation for this art form. The Honourable Prime Minister of India, Shri Narendra Modi, also celebrated this heritage by presenting a chest decorated with shisham wood inlay work to the Honourable President of the USA, Donald Trump, inspiring the artisans of Hoshiarpur with pride and motivation.
THE MAKING PROCESS OF PLASTIC INLAY ON WOOD
What tools and raw materials are required?
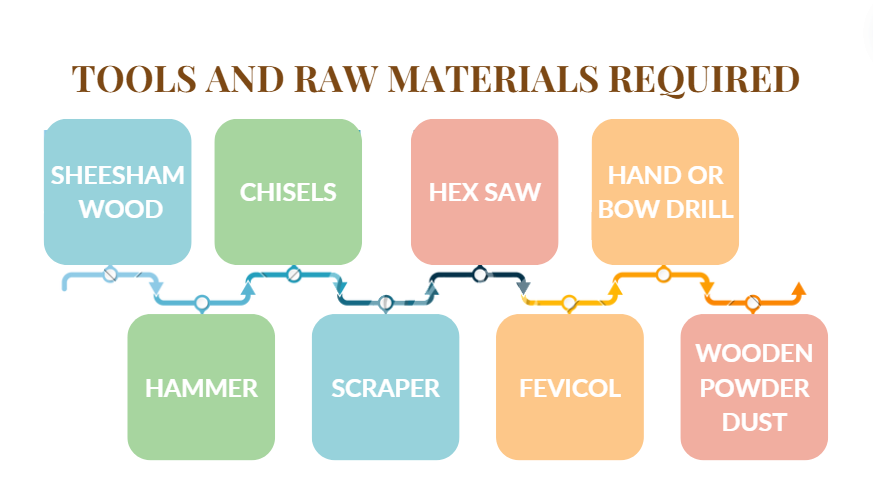
· Sheesham Wood: This wood is favored for its properties, such as closely packed grains, natural oil content, heaviness, moderately coarse nature, and uniform texture.
· Chisels: Various shaped chisels are used to carve intricate designs into wooden blocks.
· Hex Saw: This tool is used for cutting wood into the desired shapes.
· Hand or Bow Drill: A drill used to make holes in specific areas of the wood as needed.
· Hammer: Hammers, often with square or circular heads, are used to carefully strike chisels for carving designs into the wood. They are also used for embedding plastic or metal wire into the wood.
· Scraper: This tool smooths and levels the wood surface during the manufacturing and finishing process.
· Fevicol: A glue that is mixed with wooden powder dust to create a putty, which is used to fill gaps.
· Wooden Powder Dust: Combined with fevicol, this mixture is used to fill gaps between the inlaid materials and the wood.
The Process
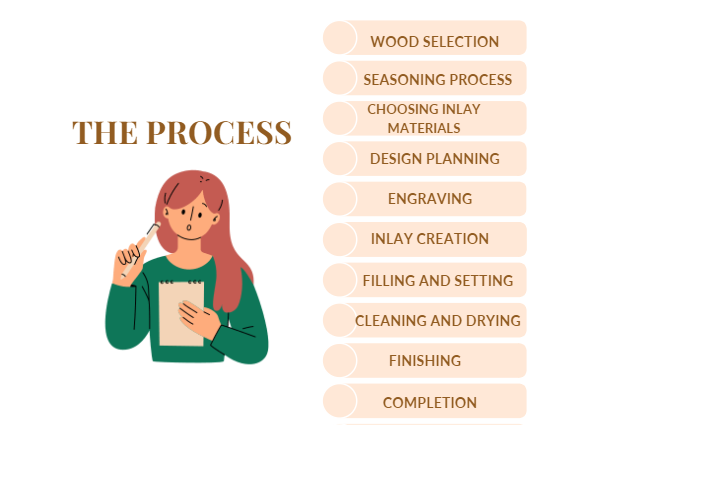
Wood Selection: The initial step in inlay work involves choosing the right type of wood, such as Sheesham (Sissoo) wood, teak, rosewood, serean resin, abnoy, and babool. Traditional inlay work in Hoshiarpur (Punjab) uses Sheesham wood from trees that are at least 50-60 years old, with a diameter of 7ft to 10ft.
Seasoning Process:
The selected Sheesham wood stem is submerged in water for five to six months to season it naturally. This process softens the outer and raw wood layers, which are then separated from the harder inner layers.
The seasoned wood is then dried naturally for another six months. Once dried, the wood is cut to the required size using an electric wood cutting machine, producing both round and flat pieces. These pieces are left to dry further for six months to ensure all moisture is removed.
Choosing Inlay Materials:
Traditionally, ivory was used for inlay work, but due to the 1975 ban on ivory, alternative materials such as camel bone, shallow shell, oyster shell, gold, copper, aluminum, marble, and acrylic plastic sheets are now used.
Design Planning:
The design process begins with hand-drawing skills, images, and common design elements to create the proposed artwork. The design is lightly scribed and engraved on the wood surface using patterns and stencils (pharmas).
Engraving:
Specialized tools like chisels and hammers are used to outline the design, carving grooves into the wood for the inlay material. This step requires precision to ensure the correct depth and shape for the inlay.
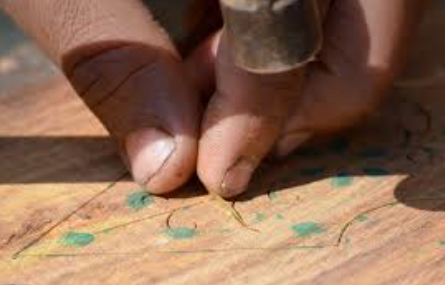
Inlay Creation:
8-10 motifs made of acrylic plastic in various sizes and designs are created using hand tools like files and thin saws. These motifs are then inlaid into the carved grooves on the wood.
Filling and Setting:
The engraved areas are filled with a mixture of the best quality acrylic plastic and wood sand, using glue and pasting material. This crucial step ensures a seamless and flawless appearance. The glue and paste are allowed to set properly, ensuring the joints are strong.
Cleaning and Drying:
Excess material is carefully removed using a sharp-edged blade. The inlaid piece is then left to dry completely before the final finishing steps.
Finishing:
Various spray lacquers and finishing techniques are applied to seal and protect the work from environmental factors. Finally, the piece is buffed with a cotton cloth to achieve a smooth and polished finish.
Completion:
The result is a fine, antique piece of handmade artwork, showcasing the intricate and skilled craftsmanship of the artisans.
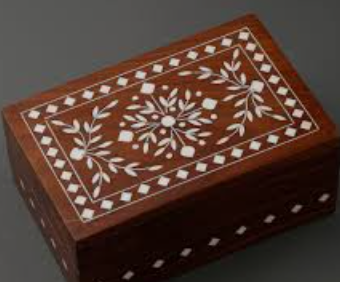
What are the market trends of plastic inlay on wood?
Market trends in the process of making plastic inlay on wood are increasingly shaped by stakeholder collaboration, supplier partnerships, and co-creation, leading to innovative and sustainable products that meet the demands of contemporary consumers.
Stakeholder collaboration is becoming a cornerstone of the plastic inlay on wood industry, where different entities, including designers, manufacturers, and end-users, work together to create products that are both aesthetically pleasing and functional. This collaboration allows for a more integrated approach to design and production, where feedback from all stakeholders is considered. For example, designers can work closely with manufacturers to ensure that the plastic inlay seamlessly integrates with the wood, enhancing the overall product quality. This collaborative approach not only improves the final product but also accelerates the development process, ensuring that new designs and innovations reach the market more quickly.
Supplier partnerships are also crucial in driving market trends within this industry. Strong relationships between wood suppliers, plastic manufacturers, and production facilities enable better coordination and alignment of goals. By working together, suppliers can ensure that the materials used in the inlay process are of the highest quality and are sourced responsibly. Moreover, these partnerships often lead to innovations in material combinations, such as using recycled plastics or sustainably sourced wood, which appeal to environmentally conscious consumers. Effective supplier partnerships also help in optimizing costs and streamlining the supply chain, making the production process more efficient and reducing time-to-market for new products.
Co-creation is another significant trend influencing the process of making plastic inlay on wood. This involves the active participation of customers in the design process, allowing them to contribute ideas and preferences that shape the final product. Co-creation is particularly popular in markets that demand highly customized products, such as luxury furniture or bespoke interior design elements. By involving customers in the design process, companies can create unique, personalized products that cater directly to individual tastes and needs. This approach not only enhances customer satisfaction but also builds stronger brand loyalty, as consumers feel a deeper connection to products they helped create.
Process:
Consumer Preferences: Conduct surveys and focus groups to understand the preferences of potential customers. Focus on styles, color schemes, and design patterns that are currently trending.
Competitive Analysis: Analyze competitors' offerings to identify gaps in the market. This includes studying their design aesthetics, pricing strategies, and marketing tactics.
Technological Advancements: Stay updated on the latest technological innovations in plastic inlay and woodworking. This could include new materials, tools, or methods that enhance the inlay process.
Trend Analysis:
Data Collection: Gather data from industry reports, online forums, social media, and trade shows. Pay attention to emerging trends such as sustainable materials, minimalistic designs, and customizable options.
Forecasting: Use statistical tools and models to predict future trends. This might involve analyzing historical data to identify patterns and make informed predictions about what will be popular in the coming years.
Product Development:
Design Adaptation: Modify product designs to align with current trends. For instance, if there is a growing demand for eco-friendly products, consider using recycled plastic or sustainably sourced wood.
Limited Editions: Introduce limited edition collections based on seasonal or temporary trends. This creates urgency and exclusivity, attracting trend-conscious consumers.
Collaborations: Partner with designers, artists, or influencers who are popular within the target market to co-create designs that resonate with current trends.
Marketing Strategies:
Social Media Campaigns: Leverage platforms like Instagram, Pinterest, and TikTok to showcase trendy designs. Use hashtags and collaborate with influencers to reach a wider audience.
Content Marketing: Create blog posts, videos, and tutorials that highlight how your plastic inlay products fit within current home decor trends. This positions your brand as a thought leader in the market.
Online Marketplaces: List products on popular e-commerce platforms, ensuring that the product descriptions emphasize their alignment with current trends.
Sales Monitoring:
Data Analysis: Continuously monitor sales data to identify which designs are performing well. Use this data to refine your product offerings and marketing strategies.
Customer Feedback: Collect feedback from customers to understand their satisfaction levels and to gauge how well the products meet current trends.
Resources:
Tools for Market Research:
Survey tools (e.g., SurveyMonkey, Google Forms)
Social media analytics tools (e.g., Hootsuite, Sprout Social)
Competitive analysis tools (e.g., SEMrush, SimilarWeb)
Statistical software for trend forecasting (e.g., SPSS, R)
Materials and Techniques:
Trendy plastic materials (e.g., eco-friendly plastics, colored resins)
Sustainable wood sources
Design software (e.g., Adobe Illustrator, AutoCAD)
Collaboration with industry experts
Marketing Tools:
Social media platforms (e.g., Instagram, Pinterest, TikTok)
Content management systems (e.g., WordPress, Squarespace)
E-commerce platforms (e.g., Etsy, Amazon Handmade)
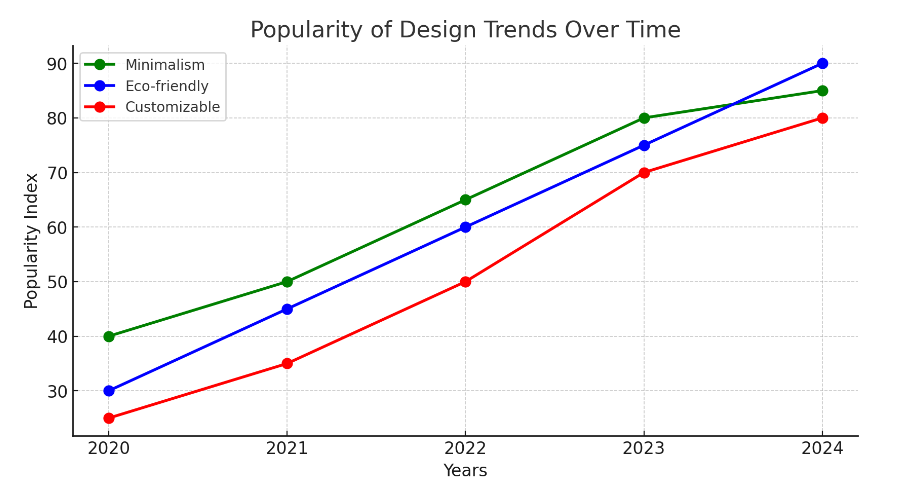
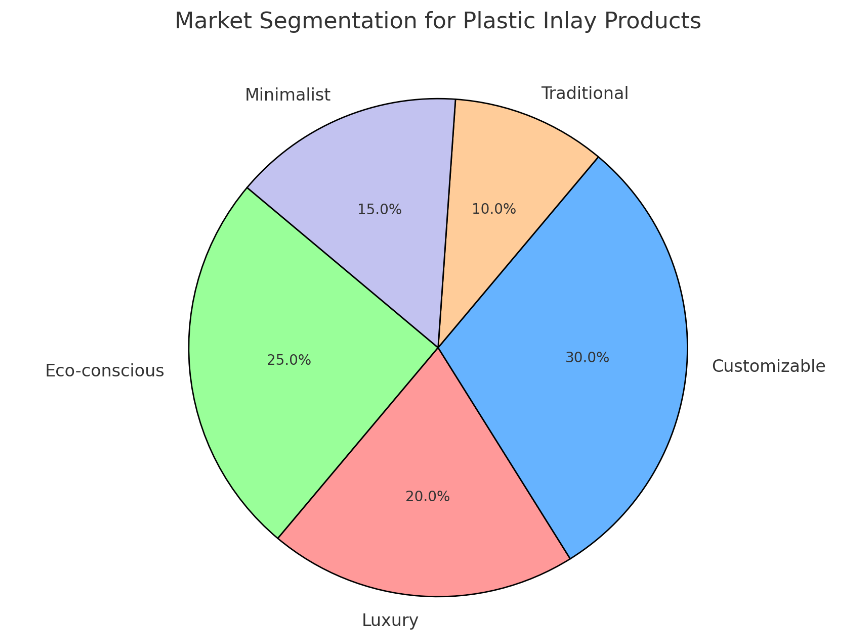
What is the costing of plastic inlay on wood?
Costing in the process of making plastic inlay on wood is a critical factor that influences the final pricing of the product, particularly when balancing the intricacies of cost management, handmade product pricing, and strategies for reducing production costs.
Cost management is essential in this process, as it involves controlling and optimizing various expenses to ensure profitability without compromising quality. The process of plastic inlay on wood is often labor-intensive, requiring skilled craftsmanship to achieve precise and intricate designs. Managing costs effectively means carefully monitoring the expenses associated with materials, labor, and overhead. This can include negotiating better rates with suppliers, investing in efficient tools and technologies that reduce waste, and streamlining production processes to minimize time and resource consumption. By implementing strong cost management practices, businesses can maintain competitive pricing while ensuring that the quality of the product remains high.
Handmade product pricing poses its own challenges and opportunities in the context of plastic inlay on wood. Handmade products generally command higher prices due to the skill, time, and effort involved in their creation. Pricing must reflect the craftsmanship and uniqueness of each piece while remaining attractive to consumers. In this niche market, customers are often willing to pay a premium for products that showcase high-quality materials and intricate designs. However, the pricing must also consider market demand and competition, ensuring that it is neither too high to deter potential buyers nor too low to undervalue the artisans' work. Transparent pricing strategies that communicate the value and effort behind handmade products can help justify higher price points to discerning customers.
Reducing production costs is another key aspect of costing in the plastic inlay on wood process. Achieving cost reductions without sacrificing quality is crucial for maintaining profitability. Strategies to reduce costs may include sourcing materials in bulk, which can lower the cost per unit; investing in technology that increases production efficiency, such as laser cutting for more precise inlays; and exploring alternative materials that are less expensive but still offer the desired aesthetic and durability. Additionally, optimizing the production workflow to reduce time and labor costs can contribute significantly to lowering overall expenses. However, it is important to strike a balance between cost reduction and maintaining the integrity and quality that handmade products are known for.
Process:
Material Costs:
Wood Selection: Calculate the cost of wood based on type (e.g., hardwood vs. softwood), quality, and source. Premium woods like oak or walnut will have higher costs compared to more common types.
Plastic Materials: Determine the cost of plastic materials, which can vary depending on type (e.g., acrylic, PVC, resin), thickness, and finish. Recycled or specialty plastics might cost more.
Design and Labor Costs:
Design Development: Include the cost of design creation, which may involve CAD software licensing, designer fees, and prototyping. Custom designs typically increase the overall cost.
Labor: Account for the labor involved in the inlay process, including routing, cutting, placement, and finishing. Skilled labor is more expensive but crucial for high-quality inlay work.
Tooling and Equipment Costs:
Tools and Machinery: Consider the depreciation cost of tools like routers, saws, and sanding equipment. Regular maintenance and potential replacements should also be factored in.
Software Costs: Include the cost of software used for design and precision cutting, such as AutoCAD or Adobe Illustrator. These tools often require ongoing subscriptions or licenses.
Overhead Costs:
Utilities and Rent: Factor in the cost of electricity, water, and rent for the workspace. These are indirect costs but contribute to the overall expense of production.
Administrative Costs: Include expenses related to management, marketing, and sales operations. This also covers costs like employee benefits and insurance.
Shipping and Handling Costs:
Packaging: Calculate the cost of materials used for packaging to protect the product during shipping. This might include custom boxes, padding, and protective wraps.
Shipping Fees: Depending on the destination, shipping costs can vary significantly. Factor in the cost of shipping both locally and internationally.
Profit Margins:
Markup: After calculating all the above costs, determine a suitable profit margin. The markup should reflect the market's willingness to pay, competitive pricing, and the uniqueness of the product.
Resources:
Materials:
High-quality wood (cost varies by type)
Plastic materials (acrylic, PVC, resin)
Packaging materials
Tools and Software:
Woodworking tools (routers, saws, sanders)
Design software (AutoCAD, Adobe Illustrator)
Shipping logistics services
Labor:
Skilled craftsmen for inlay work
Designers for custom patterns
Overhead:
Utilities (electricity, water)
Rent for workspace
Administrative expenses
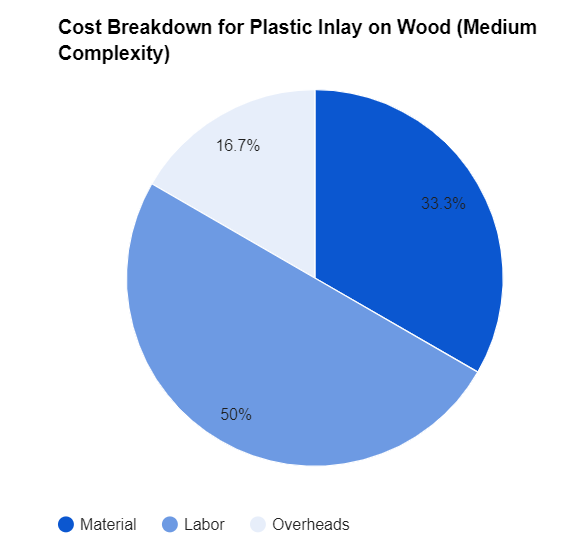
What are the logistics of plastic inlay on wood?
Logistics in the manufacturing of plastic inlay on wood involves optimizing supply chain efficiency, managing logistics effectively, and maintaining strict inventory control. Supply chain efficiency is critical for ensuring that raw materials, such as plastics and wood, are sourced, transported, and delivered in a timely manner, minimizing delays and costs. Effective logistics management encompasses coordination between suppliers, manufacturers, and distributors to streamline operations and reduce bottlenecks. Inventory control is also essential to manage stock levels of both raw materials and finished products, preventing overstocking or stockouts that could disrupt production. By implementing advanced logistics strategies and technologies, manufacturers can enhance overall operational efficiency and reduce associated costs.
Key Logistics Considerations
Raw Material Procurement:
Plastic Selection: Choose the appropriate type of plastic based on properties like durability, flexibility, and aesthetic appeal. Consider factors like cost, availability, and environmental impact.
Wood Selection: Select wood species that are suitable for inlay work. Factors to consider include hardness, grain pattern, and availability.
Supplier Relationships: Establish strong relationships with reliable suppliers of both plastic and wood to ensure consistent quality and timely delivery.
Manufacturing Processes:
Inlay Techniques: Determine the most suitable inlay techniques based on the complexity of the design and desired outcome (e.g., dovetail, miter, or routed inlay).
Equipment and Machinery: Ensure that the necessary equipment and machinery are available, including saws, routers, joinery tools, and finishing equipment.
Quality Control: Implement quality control measures to monitor the accuracy of cuts, alignment of inlays, and overall product quality.
Transportation:
Mode of Transportation: Choose the most efficient and cost-effective mode of transportation (e.g., truck, rail, or air) based on the distance, urgency, and nature of the goods.
Packaging: Ensure proper packaging to protect the finished products during transit and prevent damage.
Shipping Documentation: Prepare necessary shipping documents, such as invoices, packing lists, and customs declarations.
Warehousing:
Storage Facilities: Establish suitable storage facilities to protect the finished products from damage and deterioration.
Inventory Management: Implement inventory management systems to track stock levels, monitor product turnover, and prevent stockouts.
Security: Ensure adequate security measures to protect the warehouse and its contents from theft or unauthorized access.
Distribution:
Channels: Identify appropriate distribution channels, such as wholesalers, retailers, or direct-to-consumer sales.
Order Fulfillment: Efficiently process and fulfill orders to meet customer expectations and minimize delivery times.
Customer Service: Provide excellent customer service to build customer loyalty and address any issues related to shipping, returns, or product quality.
Logistics Resources
Transportation Companies: Research and select reliable transportation companies that specialize in handling delicate or fragile goods.
Warehousing Facilities: Explore options for warehousing facilities that meet your specific storage needs and location requirements.
Inventory Management Software: Consider using inventory management software to streamline your operations and track stock levels.
Supply Chain Management Consultants: Consult with supply chain management experts to optimize your logistics processes and reduce costs.
What are the customs and duties of plastic inlay on wood?
Customs and duties play a crucial role in the import and export of plastic inlay materials. Customs duties refer to the taxes imposed by governments on imported goods, affecting the cost of raw materials and finished products. Import tariffs are specific taxes levied on goods crossing international borders, which can impact the pricing and competitiveness of the products in the market. Trade agreements between countries can influence these tariffs, potentially reducing or eliminating them for certain goods. Understanding and navigating these customs regulations is essential for manufacturers to ensure compliance, manage costs effectively, and maintain smooth international trade operations.
Recommendations:
Research customs and duties regulations well in advance of importing or exporting plastic inlay on wood products.
Consult with a customs broker to ensure proper classification and valuation of your goods.
Factor in potential customs and duties costs when calculating your overall landed cost.
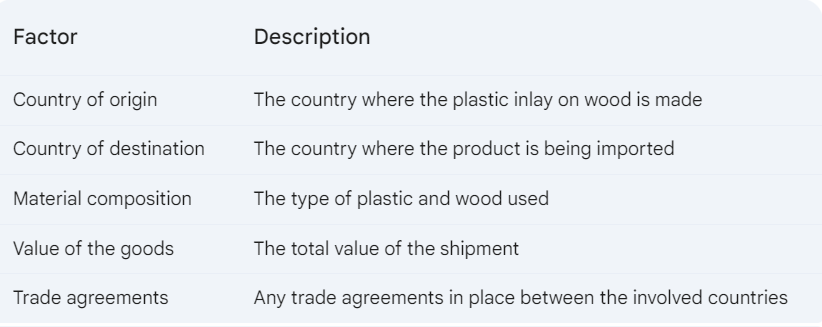
Anti-Money Laundering of plastic inlay on wood
Anti-money laundering (AML) measures are vital for ensuring the financial integrity of the plastic inlay on wood industry. AML compliance involves adhering to financial regulations designed to prevent money laundering and the financing of illegal activities. This includes implementing robust internal controls, conducting due diligence on financial transactions, and monitoring for suspicious activities. By adhering to AML standards, manufacturers can mitigate risks related to financial crimes, enhance their business credibility, and foster trust with financial institutions and partners.
Key Components of AML Programs
Customer Due Diligence (CDD):
Identification: Verify the identity of customers and their beneficial owners.
Source of Funds: Gather information on the source of funds and the nature of the business relationship.
Enhanced Due Diligence (EDD): Conduct additional checks for high-risk customers or transactions.
Transaction Monitoring:
Suspicious Activity Reports (SARs): File SARs with the relevant authorities when suspicious activities are identified.
Unusual Activity Reports (UARs): Report unusual or suspicious activities internally.
Real-Time Monitoring: Use technology to monitor transactions for red flags.
Employee Training:
Awareness: Educate employees about money laundering risks and signs of suspicious activity.
Policies and Procedures: Train staff on AML policies, procedures, and reporting requirements.
Risk Assessment:
Identify Risks: Conduct regular assessments to identify potential money laundering risks.
Mitigate Risks: Develop strategies to mitigate identified risks.
Independent Testing:
Evaluate Effectiveness: Periodically test the AML program's effectiveness.
Identify Deficiencies: Identify areas for improvement and address any weaknesses.
Why is AML Important?
Protect Financial Integrity: AML helps maintain the integrity of financial systems and prevent criminal activities from infiltrating them.
Combat Terrorism Financing: AML measures contribute to combating terrorist financing by disrupting the flow of funds that support terrorist activities.
Enhance Reputation: Compliance with AML regulations can enhance the reputation and credibility of financial institutions.
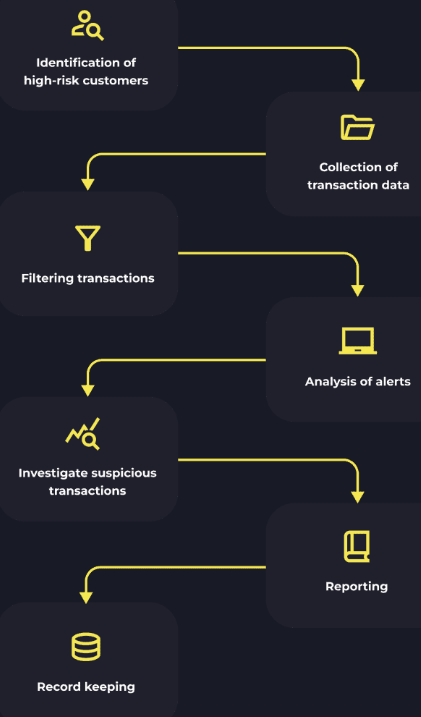
What are the ethical practices of plastic inlay on wood?
Ethical practices in the plastic inlay on wood industry focus on ensuring ethical manufacturing processes, fair labor practices, and sustainable operations. Ethical manufacturing involves upholding high standards for worker conditions, including fair wages and safe working environments. Fair labor practices ensure that workers are treated with respect and dignity, avoiding exploitative practices. Sustainable practices involve adopting environmentally friendly methods and materials, such as using recyclable plastics and responsibly sourced wood. By prioritizing these ethical standards, manufacturers can build a positive reputation, comply with regulations, and contribute to a more responsible industry.
Environmental Sustainability
Sustainable Materials: Prioritize the use of sustainable materials, including recycled plastics and sustainably sourced wood.
Reduced Waste: Minimize waste generation during the manufacturing process by optimizing production techniques and utilizing waste reduction strategies.
Energy Efficiency: Implement energy-efficient practices in production facilities to reduce environmental impact.
Fair Labor Practices
Ethical Sourcing: Ensure that all materials, including plastic and wood, are sourced ethically and from suppliers that adhere to fair labor standards.
Fair Wages and Benefits: Provide fair wages and benefits to all employees, in accordance with local labor laws and industry standards.
Safe Working Conditions: Maintain safe and healthy working conditions for all employees, free from hazards and discrimination.
Consumer Safety
Non-Toxic Materials: Use non-toxic materials that do not pose any health risks to consumers.
Product Safety: Ensure that products meet all safety standards and regulations, including those related to chemical content and flammability.
Clear Labeling: Provide clear and accurate labeling on products, including information about materials used, care instructions, and any potential hazards.
Corporate Social Responsibility
Community Engagement: Contribute to the local community through charitable initiatives, volunteer work, or support for community projects.
Transparency: Be transparent about business practices, environmental impact, and social responsibility initiatives.
Ethical Business Conduct: Adhere to ethical business practices, including fair competition, honest advertising, and avoidance of bribery or corruption.
Ethical Considerations Specific to Plastic Inlay on Wood
Animal Welfare: If using animal-derived materials (e.g., leather or bone) for inlays, ensure that they are sourced ethically and do not contribute to animal cruelty.
Cultural Sensitivity: Respect the cultural significance of wood species and avoid using materials that are protected or endangered.
Product Longevity: Design products that are durable and long-lasting to reduce waste and promote sustainability.
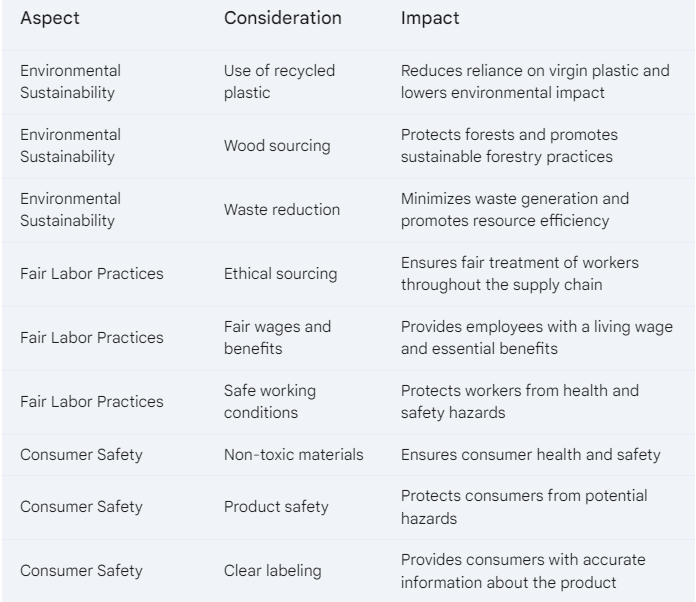
What are the innovative aspects of plastic inlay on wood?
Innovation in the manufacturing of plastic inlay on wood is driven by advancements in technology and research and development (R&D). Manufacturing innovation includes the adoption of new technologies and techniques that improve production efficiency, product quality, and design capabilities. Technology adoption may involve integrating automated systems, advanced machinery, or new materials that enhance the manufacturing process. R&D efforts focus on developing innovative solutions and products that meet evolving market demands and consumer preferences. By fostering a culture of innovation, manufacturers can stay competitive, differentiate their products, and address emerging industry trends.
Material Innovation
Biodegradable Plastics: Using biodegradable plastics that decompose naturally can reduce the environmental impact of the products.
Recycled Plastics: Incorporating recycled plastics into the inlay process can help divert waste from landfills.
Composite Materials: Combining wood and plastic with other materials, such as natural fibers or resins, can create new properties and enhance performance.
Design Innovation
3D Printing: Utilizing 3D printing technology to create intricate and customized inlay designs that would be difficult or impossible with traditional methods.
Digital Fabrication: Employing digital fabrication techniques, such as laser cutting or CNC machining, to achieve precise and repeatable inlays.
Interactive Inlays: Incorporating interactive elements, such as LEDs or sensors, into the inlays to create dynamic and engaging pieces.
Production Innovation
Automation: Implementing automated processes to improve efficiency, reduce labor costs, and increase production capacity.
Lean Manufacturing: Adopting lean manufacturing principles to eliminate waste, improve quality, and reduce lead times.
Circular Economy: Designing products with a circular economy mindset, where materials can be reused or recycled at the end of their lifecycle.
Application Innovation
Functional Inlays: Developing inlays that serve specific functions, such as providing insulation, soundproofing, or structural support.
Personalized Inlays: Creating custom inlays that cater to individual preferences and needs.
Sustainable Furniture: Incorporating plastic inlay techniques into sustainable furniture designs that prioritize environmental friendliness and ethical sourcing.
Potential Innovations:
Self-Healing Inlays: Developing inlays that can repair minor scratches or cracks on their own.
Smart Inlays: Integrating sensors and technology into inlays to monitor environmental conditions or provide interactive features.
Biomimicry Inlays: Inspired by natural patterns and structures, creating inlays that mimic the properties and aesthetics of living organisms.
Risk Management of plastic inlay on wood
Risk management is essential for addressing potential challenges in the plastic inlay on wood manufacturing process. Effective risk management involves identifying, assessing, and mitigating risks related to production, supply chain disruptions, and financial uncertainties. Contingency planning is crucial for preparing responses to unforeseen events, such as equipment failures or supply shortages. By implementing robust risk management strategies, manufacturers can minimize the impact of adverse events, maintain operational stability, and ensure the continuity of their business.
Key Risk Areas
Supply Chain Risks:
Raw Material Availability: Risks associated with fluctuations in the availability or pricing of plastic and wood materials.
Supplier Disruptions: Risks due to supplier failures, financial instability, or natural disasters.
Quality Control: Risks related to the quality and consistency of materials, leading to defects or production delays.
Manufacturing Risks:
Equipment Failures: Risks arising from equipment breakdowns or malfunctions, resulting in production downtime and increased costs.
Process Inefficiencies: Risks associated with inefficient manufacturing processes, leading to waste, delays, and reduced productivity.
Workplace Accidents: Risks related to workplace safety hazards, which can result in injuries, legal liabilities, and negative publicity.
Market Risks:
Economic Downturns: Risks associated with economic recessions or downturns, leading to reduced demand for products and financial losses.
Competitive Pressure: Risks from intense competition, which can erode market share, lower prices, and reduce profitability.
Changing Consumer Preferences: Risks due to shifts in consumer tastes and preferences, leading to declining demand for certain products.
Regulatory Risks:
Environmental Regulations: Risks related to compliance with environmental regulations, including those governing waste disposal, emissions, and resource conservation.
Labor Laws: Risks associated with compliance with labor laws, including minimum wage, working hours, and health and safety standards.
Trade Restrictions: Risks due to changes in trade policies, tariffs, or quotas, which can impact the cost and availability of materials or finished products.
Risk Management Strategies
Risk Identification:
Brainstorming: Identify potential risks through brainstorming sessions, discussions, and analysis of past experiences.
Risk Assessment Tools: Utilize risk assessment tools and frameworks to identify and prioritize risks based on their likelihood and impact.
Risk Assessment:
Probability: Assess the likelihood of each risk occurring.
Impact: Evaluate the potential consequences of each risk, including financial, operational, and reputational impacts.
Risk Mitigation:
Risk Avoidance: Eliminate or avoid high-risk activities.
Risk Reduction: Implement measures to reduce the likelihood or impact of risks.
Risk Transfer: Transfer risks to third parties through insurance or contracts.
Risk Acceptance: Accept risks that are deemed acceptable based on their likelihood and impact.
Risk Monitoring and Review:
Continuous Monitoring: Monitor risks on an ongoing basis to identify changes or emerging threats.
Regular Reviews: Conduct periodic reviews of the risk management plan to ensure its effectiveness and make necessary adjustments.
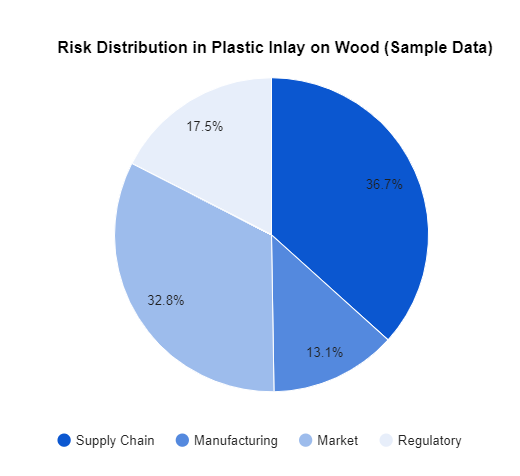
What are the digital marketing measures of plastic inlay on wood?
Digital marketing strategies are increasingly important for manufacturers of plastic inlay on wood to reach and engage with their target audience. Digital marketing encompasses various tactics, including social media marketing, content marketing, and search engine optimization (SEO). Social media platforms offer opportunities to connect with customers, showcase products, and build brand awareness. Content marketing involves creating valuable and relevant content to attract and retain customers, while SEO ensures that the company’s online presence ranks well in search engine results. A well-rounded digital marketing strategy can enhance brand visibility, drive traffic, and generate leads.
Key Digital Marketing Channels
Search Engine Optimization (SEO):
Optimize your website to rank higher in search engine results for relevant keywords.
Use relevant keywords in your website content, meta tags, and headings.
Build high-quality backlinks from other reputable websites.
Pay-Per-Click (PPC) Advertising:
Create and manage paid ads on search engines like Google Ads and social media platforms.
Target specific keywords and demographics to reach your ideal customers.
Track and analyze campaign performance to optimize your budget.
Social Media Marketing:
Create engaging content and build a community on platforms like Instagram, Facebook, and Pinterest.
Use visuals and videos to showcase your products and craftsmanship.
Interact with your followers and respond to comments and messages.
Content Marketing:
Create high-quality content, such as blog posts, articles, and videos, that educates and informs your target audience.
Share your content on social media and through email marketing.
Optimize your content for search engines to improve visibility.
Email Marketing:
Build an email list of interested customers and send targeted email campaigns.
Promote new products, offer discounts, and provide valuable content.
Track open rates, click-through rates, and conversions to measure campaign effectiveness.
Specific Strategies for Plastic Inlay on Wood
Showcase Craftsmanship: Highlight the unique craftsmanship and artistry behind your products through high-quality images and videos.
Target Home Decor Enthusiasts: Focus on reaching home decor enthusiasts, interior designers, and architects who appreciate handcrafted items.
Leverage Visual Platforms: Utilize platforms like Instagram and Pinterest to showcase visually appealing images of your products.
Partner with Influencers: Collaborate with home decor influencers to reach a wider audience and generate credibility.
Offer Online Workshops or Tutorials: Educate your audience through online workshops or tutorials on plastic inlay techniques or home decor tips.
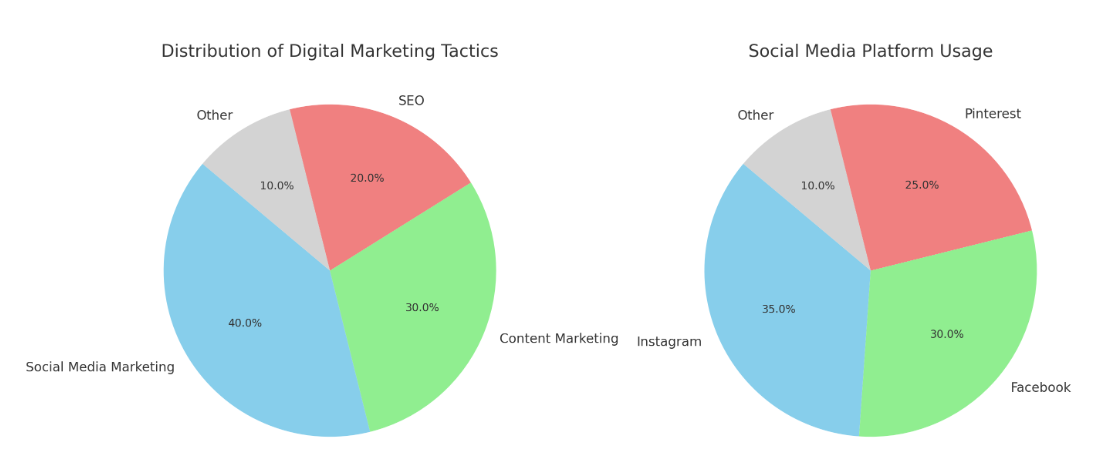
What are the customer service aspects of plastic inlay on wood?
Customer service in the plastic inlay on wood industry focuses on improving service quality, responding to customer feedback, and implementing effective support systems. Enhancing customer service involves providing timely and efficient support to address inquiries, complaints, and product issues. Gathering and analyzing customer feedback helps identify areas for improvement and tailor services to meet customer needs. Implementing robust support systems, such as customer service platforms and help desks, ensures that customers receive the assistance they need promptly. By prioritizing customer service, manufacturers can build strong relationships, enhance customer satisfaction, and foster loyalty.
Customer Service Aspects
Pre-Purchase Support:
Product Information: Provide detailed information about products, including materials, dimensions, and care instructions.
Customization Options: Offer customization options to meet specific customer preferences.
Personalized Recommendations: Suggest suitable products based on customer needs and tastes.
Order Processing:
Efficient Order Handling: Process orders promptly and accurately to minimize wait times.
Clear Communication: Keep customers informed about order status and estimated delivery times.
Secure Payment Processing: Ensure a secure and convenient payment experience.
Post-Purchase Support:
Installation Assistance: Provide guidance on installation or offer professional installation services.
Troubleshooting Support: Assist customers with troubleshooting issues and resolving problems.
Returns and Exchanges: Handle returns and exchanges efficiently and fairly.
Customer Feedback:
Feedback Collection: Actively seek customer feedback through surveys, reviews, or social media.
Analysis and Improvement: Analyze feedback to identify areas for improvement and implement necessary changes.
Customer Service Channels
Website: Provide a comprehensive FAQ section, contact information, and online chat support.
Email: Respond to customer inquiries promptly and professionally.
Phone: Offer a dedicated customer service phone line with knowledgeable and helpful representatives.
Social Media: Monitor social media platforms for customer questions or complaints and respond in a timely manner.
Measuring Customer Satisfaction
Customer Satisfaction Surveys: Conduct surveys to measure customer satisfaction and identify areas for improvement.
Net Promoter Score (NPS): Calculate the NPS to gauge customer loyalty and willingness to recommend your products.
Customer Reviews and Feedback: Monitor online reviews and social media comments to understand customer sentiment.
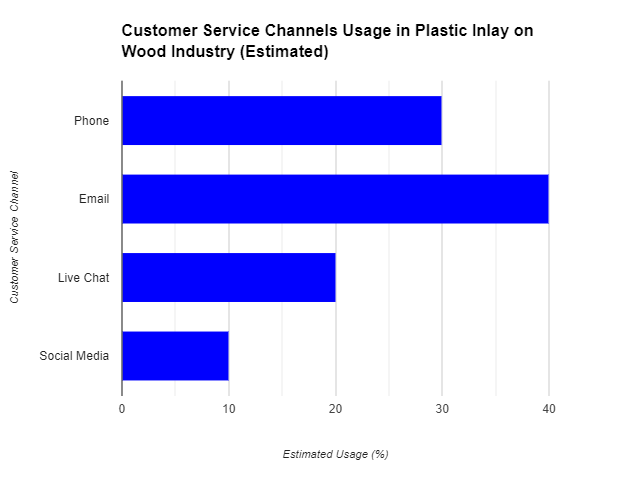
How to do quality control of plastic inlay on wood?
Quality control is critical in ensuring the consistency and reliability of plastic inlay on wood products. Quality control processes involve rigorous product inspections at various stages of manufacturing to detect and address defects or deviations from standards. Continuous improvement initiatives focus on refining production techniques, enhancing material quality, and implementing best practices. By maintaining strict quality control measures, manufacturers can deliver high-quality products, meet customer expectations, and minimize returns or rework.
Quality Control Areas
Raw Material Inspection:
Quality Assurance: Verify the quality of plastic and wood materials against predetermined standards.
Compliance: Ensure compliance with relevant industry regulations and certifications.
Inlay Process Monitoring:
Precision: Monitor the accuracy of cuts, alignment of inlays, and adherence to design specifications.
Consistency: Ensure consistent quality throughout the manufacturing process.
Product Inspection:
Visual Inspection: Inspect finished products for defects such as cracks, scratches, or uneven surfaces.
Functional Testing: Test the functionality of products, including their strength, durability, and resistance to wear and tear.
Dimensional Accuracy:
Measurements: Verify the accuracy of dimensions and tolerances using appropriate measuring tools.
Consistency: Ensure consistency in measurements to maintain product quality.
Finishing Inspection:
Surface Finish: Inspect the surface finish for smoothness, evenness, and adherence to desired specifications.
Color and Texture: Verify the accuracy of colors and textures to match design requirements.
Packaging Inspection:
Packaging Integrity: Ensure that products are packaged securely and adequately protected from damage.
Labeling Accuracy: Verify the accuracy of product labels and ensure compliance with labeling regulations.
QC Methods and Tools
Visual Inspection: Using the human eye to identify defects or inconsistencies.
Dimensional Inspection: Using measuring tools such as calipers, micrometers, or gauges to verify dimensions.
Functional Testing: Simulating real-world conditions to assess product performance.
Statistical Process Control (SPC): Using statistical techniques to monitor and control processes and identify variations.
Inspection Software: Utilizing software tools to automate inspection processes and improve efficiency.
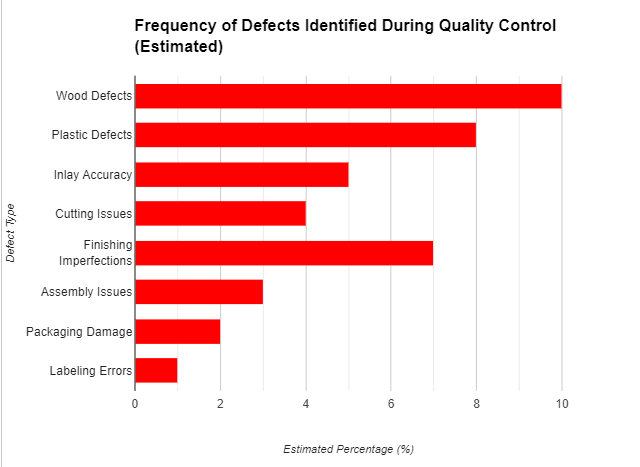
How to do cost management of plastic inlay on wood?
Cost management in the plastic inlay on wood industry involves budgeting, financial planning, and controlling production costs. Effective cost management includes developing detailed budgets that account for all aspects of manufacturing, from raw materials to labor and overheads. Financial planning involves forecasting future expenses and revenues to ensure profitability and financial stability. By implementing cost control measures, such as optimizing resource use and reducing waste, manufacturers can manage expenses effectively and enhance their overall financial performance.
Cost Areas
Raw Material Costs:
Material Selection: Choose cost-effective materials without compromising quality.
Supplier Negotiations: Negotiate favorable pricing terms with suppliers.
Bulk Purchasing: Consider bulk purchasing to leverage volume discounts.
Labor Costs:
Efficiency Improvements: Implement measures to improve labor efficiency and reduce waste.
Skill Development: Invest in employee training and development to enhance productivity.
Wage Optimization: Ensure that wages are competitive and aligned with market standards.
Manufacturing Costs:
Equipment Maintenance: Regularly maintain equipment to minimize downtime and repair costs.
Energy Efficiency: Implement energy-saving measures to reduce utility expenses.
Waste Reduction: Minimize waste generation through efficient production processes.
Overhead Costs:
Rent and Utilities: Negotiate favorable lease terms and manage utility expenses.
Insurance: Obtain appropriate insurance coverage to protect against risks.
Administrative Costs: Streamline administrative processes to reduce overhead expenses.
Marketing and Sales Costs:
Effective Marketing: Allocate marketing resources effectively to generate leads and drive sales.
Sales Force Management: Optimize sales team structure and compensation to maximize productivity.
Digital Marketing: Leverage cost-effective digital marketing channels to reach your target audience.
Cost Management Strategies
Cost-Benefit Analysis: Evaluate the costs and benefits of different options before making decisions.
Budgeting: Create detailed budgets to track expenses and identify areas for cost reduction.
Standard Costing: Establish standard costs for materials, labor, and overhead to measure performance and identify variances.
Variance Analysis: Analyze variances between actual and standard costs to identify cost drivers and take corrective actions.
Benchmarking: Compare your costs to industry benchmarks to identify areas for improvement.
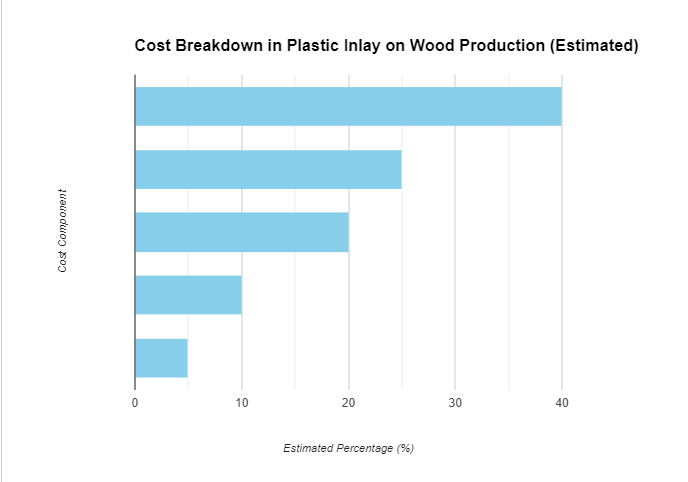
Business Authenticity of plastic inlay on wood
Business authenticity is crucial for building trust and credibility in the plastic inlay on wood industry. Authenticity involves maintaining transparency in business practices, ensuring honesty in marketing and communications, and delivering on promises. Trust in business is fostered by consistently providing high-quality products, adhering to ethical standards, and maintaining reliable customer service. Reputation management involves actively managing public perception and addressing any issues that may impact the company's image. By prioritizing business authenticity, manufacturers can strengthen their brand reputation and build lasting relationships with customers and partners.
Elements of Business Authenticity
Transparent Communication:
Open and Honest: Communicate openly and honestly about your business, products, and processes.
Transparency in Pricing: Clearly communicate pricing and avoid hidden fees.
Customer Support: Provide timely and helpful customer support.
Ethical Practices:
Fair Labor Practices: Adhere to fair labor standards and ensure ethical treatment of employees.
Sustainable Sourcing: Source materials responsibly and minimize environmental impact.
Ethical Business Conduct: Avoid unethical practices such as bribery, corruption, or deceptive marketing.
Consistent Branding:
Strong Brand Identity: Develop a strong and consistent brand identity that reflects your values and mission.
Brand Messaging: Communicate your brand message effectively through all channels.
Visual Consistency: Maintain consistency in your branding elements, such as logo, colors, and typography.
Customer Focus:
Customer-Centric Approach: Put customers at the center of your business decisions.
Personalized Service: Offer personalized service and tailor your offerings to meet customer needs.
Customer Feedback: Actively seek and respond to customer feedback.
Community Engagement:
Social Responsibility: Contribute to the community through charitable initiatives or volunteer work.
Ethical Partnerships: Partner with other businesses that share your values and ethical standards.
Benefits of Business Authenticity
Increased Trust: Build trust with customers, leading to repeat business and positive word-of-mouth.
Stronger Brand Loyalty: Foster customer loyalty and reduce churn.
Improved Reputation: Enhance your reputation as a trustworthy and ethical company.
Attracting Talent: Attract and retain talented employees who align with your values.
Sustainable Growth: Drive sustainable growth through long-term customer relationships and positive brand image.
What are the credit checks of plastic inlay on wood?
Credit checks are an essential aspect of financial risk assessment for manufacturers of plastic inlay on wood. Conducting credit checks involves evaluating the creditworthiness of potential customers, suppliers, and partners to assess their ability to fulfill financial obligations. This process helps identify potential risks, such as delayed payments or default, and informs decision-making related to extending credit or entering into contracts. By performing thorough credit assessments, manufacturers can mitigate financial risks, protect their cash flow, and ensure stable business relationships.
Uses of Credit Checks
Customer Creditworthiness: Assessing a customer's creditworthiness before extending credit or offering payment terms.
Supplier Reliability: Evaluating a supplier's financial stability and ability to fulfill orders.
Partner Assessments: Determining the financial health and creditworthiness of potential business partners.
Debt Collection: Identifying potential risks associated with extending credit and informing debt collection strategies.
Factors Considered in Credit Checks
Payment History: On-time or late payments on previous loans and credit cards.
Credit Utilization: The amount of credit used compared to available credit limits.
Length of Credit History: The duration of credit accounts and the time since the last account was opened.
Credit Inquiries: The number of recent credit inquiries, which can indicate shopping around for credit.
Public Records: Any negative public records, such as bankruptcies or judgments.
Importance of Credit Checks
Risk Mitigation: Helps businesses mitigate the risk of financial losses due to unpaid debts.
Improved Decision-Making: Provides valuable information for making informed decisions regarding credit extensions and business relationships.
Enhanced Cash Flow: Reduces the risk of bad debts and improves cash flow management.
Compliance: Ensures compliance with relevant regulations and industry standards.
What is the importance of insurance of plastic inlay on wood?
Insurance in the manufacturing of plastic inlay on wood provides essential risk coverage and protection against potential losses. Manufacturing insurance typically includes policies such as property insurance, liability insurance, and worker’s compensation. These policies protect against risks such as property damage, product liability claims, and employee injuries. Insurance processing involves handling claims efficiently and ensuring that coverage aligns with the specific needs of the business. By securing appropriate insurance coverage, manufacturers can safeguard their assets, manage risks effectively, and ensure business continuity.
Insurance
Property Insurance:
Building Insurance: Covers damage to your manufacturing facility, including the building structure, fixtures, and equipment.
Contents Insurance: Protects your inventory, machinery, tools, and other assets within the building.
General Liability Insurance:
Product Liability: Covers claims arising from defective products or injuries caused by your products.
Property Damage: Protects you against claims of property damage caused by your business operations.
Bodily Injury: Covers claims for bodily injury caused by your business operations.
Business Interruption Insurance:
Loss of Income: Provides coverage for lost income due to business interruptions caused by insured perils (e.g., fire, flood, natural disasters).
Additional Expenses: Covers extra expenses incurred during business interruptions, such as rental of temporary facilities.
Workers' Compensation Insurance:
Employee Injuries: Covers medical expenses, lost wages, and rehabilitation costs for employees injured on the job.
Legal Defense: Provides legal defense in case of workers' compensation claims.
Professional Liability Insurance:
Design Errors: Covers claims arising from design errors or omissions in your products.
Negligence: Protects you against claims of negligence or professional misconduct.
Factors to Consider
Risk Assessment: Evaluate the potential risks facing your business and tailor your insurance coverage accordingly.
Coverage Limits: Determine appropriate coverage limits based on the value of your assets and potential liabilities.
Deductibles: Choose deductibles that balance affordability with adequate coverage.
Insurance Providers: Compare insurance providers based on coverage, premiums, and customer service.
Currency Exchange of plastic inlay on wood
Currency exchange management is important for manufacturers engaged in international trade of plastic inlay on wood. Currency exchange involves converting and managing foreign currencies used in transactions with international customers and suppliers. Forex management includes monitoring exchange rates and implementing strategies to mitigate the impact of currency fluctuations on costs and revenues. Hedging strategies, such as forward contracts or options, can help lock in exchange rates and protect against adverse movements. Effective currency exchange management ensures financial stability and helps maintain profitability in a global market.
Factors Affecting Currency Exchange Rates
Economic Indicators: Interest rates, inflation, and GDP growth rates in different countries can influence exchange rates.
Political Stability: Political instability or uncertainty can affect currency values.
Trade Balance: The balance of trade between countries can impact exchange rates.
Market Speculation: Speculation by investors and traders can drive short-term fluctuations in exchange rates.
Currency Exchange Risks
Exchange Rate Volatility: Fluctuations in exchange rates can impact profitability, especially for businesses with significant foreign currency exposure.
Transaction Costs: Currency exchange transactions often involve fees or commissions.
Settlement Risks: Delays or failures in currency settlements can lead to financial losses.
Risk Management Strategies
Hedging: Using financial instruments like futures or options to protect against adverse exchange rate movements.
Currency Forward Contracts: Agreeing to buy or sell a specific amount of currency at a predetermined rate on a future date.
Diversification: Spreading currency risk across multiple currencies to reduce exposure.
Currency Forecasting: Using forecasting tools to anticipate potential exchange rate movements.
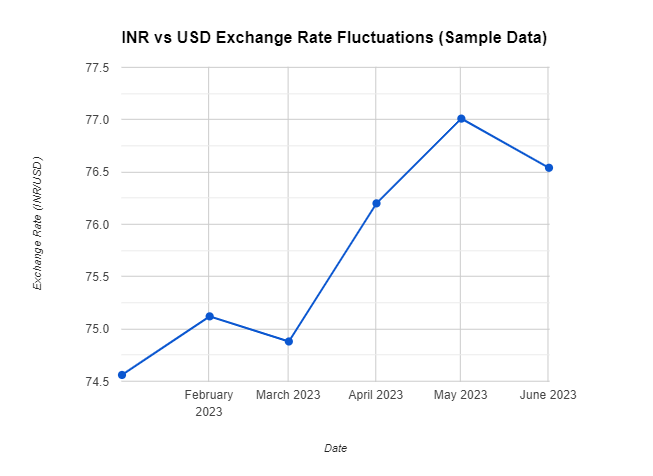
What are the sustainability measures of plastic inlay on wood?
Sustainability in the manufacturing of plastic inlay on wood focuses on adopting eco-friendly practices and promoting green manufacturing. Sustainability involves minimizing the environmental impact of production processes by using recyclable or biodegradable materials, reducing waste, and implementing energy-efficient technologies. Eco-friendly practices include sourcing raw materials responsibly and reducing carbon emissions throughout the supply chain. Green manufacturing emphasizes the development of sustainable products and processes that contribute to environmental conservation. By prioritizing sustainability, manufacturers can enhance their environmental stewardship, meet regulatory requirements, and appeal to environmentally conscious consumers.
Sustainability in the plastic inlay on wood industry involves minimizing environmental impact, promoting ethical practices, and ensuring long-term viability. Here are key areas to focus on:
1. Sustainable Materials:
Recycled Plastics: Use recycled plastics to reduce reliance on virgin materials and divert waste from landfills.
FSC-Certified Wood: Source wood from sustainably managed forests certified by the Forest Stewardship Council (FSC).
Biodegradable Materials: Explore biodegradable options for both plastic and adhesives to reduce environmental impact.
2. Efficient Production Processes:
Waste Reduction: Minimize waste generation through efficient production techniques and proper material handling.
Energy Efficiency: Implement energy-saving measures in manufacturing facilities, such as using LED lighting and efficient equipment.
Water Conservation: Conserve water resources by optimizing water usage in production processes.
3. Ethical Sourcing:
Fair Trade Practices: Ensure fair wages and working conditions for all employees and suppliers involved in the production process.
Ethical Materials: Avoid using materials that contribute to deforestation, animal cruelty, or human rights violations.
4. Product Longevity:
Durability: Design products to be durable and long-lasting, reducing the need for frequent replacements.
Repairability: Make products easily repairable to extend their lifespan and reduce waste.
5. End-of-Life Management:
Recycling: Develop recycling programs for both plastic and wood components to minimize waste.
Composting: If using biodegradable materials, promote composting as a sustainable disposal method.
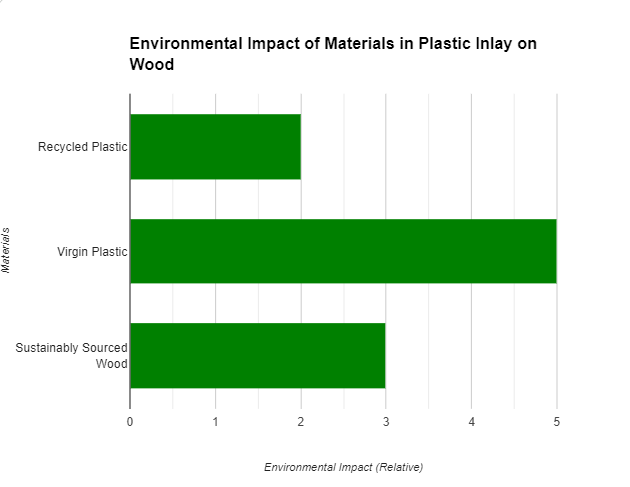
How to do shipping and handling of plastic inlay on wood?
Shipping and handling efficiency is crucial for the distribution of plastic inlay on wood products. Shipping optimization involves selecting cost-effective and reliable transportation methods, managing shipping logistics, and minimizing delivery times. Handling efficiency focuses on proper packaging, safe loading and unloading practices, and minimizing damage during transit. Packaging solutions, such as protective materials and efficient designs, ensure that products arrive in good condition and reduce the risk of returns. By optimizing shipping and handling processes, manufacturers can improve customer satisfaction, reduce costs, and enhance overall operational efficiency.
Key Factors to Consider
Packaging:
Protection: Ensure proper packaging to protect products during transit and prevent damage.
Weight and Dimensions: Consider the weight and dimensions of packages to determine shipping costs.
Sustainability: Use eco-friendly packaging materials to reduce environmental impact.
Shipping Methods:
Carrier Selection: Choose a reliable shipping carrier based on factors like speed, cost, and services offered.
Shipping Options: Select the appropriate shipping option, such as standard, expedited, or overnight delivery, based on customer needs and time constraints.
Insurance: Consider purchasing shipping insurance to protect against losses or damages during transit.
Shipping Costs:
Weight and Dimensions: Shipping costs are typically based on the weight and dimensions of packages.
Distance: The distance between the shipping origin and destination will also affect shipping costs.
Shipping Method: Different shipping methods have varying costs, with expedited shipping generally being more expensive.
Handling Fees:
Packaging and Handling: Carriers may charge additional fees for packaging, handling, and special services.
Customs Clearance: If shipping internationally, customs clearance fees may apply.
Customer Experience:
Tracking: Provide customers with tracking information to allow them to monitor the progress of their shipment.
Delivery Notifications: Notify customers of expected delivery dates and times.
Returns and Exchanges: Have clear policies for returns and exchanges, including handling fees if applicable.
How to maintain the quality of plastic inlay on wood?
Quality in the production of plastic inlay on wood is characterized by high standards of craftsmanship and rigorous quality control processes. Handmade products are often valued for their attention to detail and artisanal skill, which contribute to their overall quality. Quality control measures ensure that each product meets specific standards, preventing defects and ensuring durability. Premium home products are crafted with a focus on both aesthetics and functionality, providing consumers with high-quality, bespoke items that enhance their living spaces. The emphasis on craftsmanship reflects a commitment to excellence and the creation of superior, one-of-a-kind products.
Process:
Material Selection:
Wood: Choose high-quality wood with a smooth, uniform grain. Hardwood is typically preferred for inlay work due to its durability.
Plastic: Select plastic materials that are compatible with the wood and suitable for inlay, such as acrylic, PVC, or resin. The plastic should be of high quality, free from impurities, and capable of withstanding cutting and finishing processes.
Design and Pattern Creation:
CAD Design: Use computer-aided design (CAD) software to create precise patterns and designs. Ensure that the design is proportionate to the wood surface and fits the aesthetic requirements.
Stencil Creation: Create a stencil or template to ensure accurate placement of the inlay design on the wood.
Surface Preparation:
Sanding: Thoroughly sand the wood surface to ensure smoothness and remove any imperfections.
Marking: Use the stencil to mark the inlay pattern on the wood. Precision is crucial to avoid gaps between the wood and plastic.
Inlay Process:
Routing: Carefully route the wood surface along the marked lines to create a recess where the plastic will be inlaid. The depth of the recess should be consistent and appropriate for the thickness of the plastic.
Plastic Cutting: Cut the plastic material to match the routed recess. Precision in cutting is essential to ensure a snug fit.
Placement and Adhesion: Place the plastic into the recess, ensuring a tight fit. Use a high-quality adhesive suitable for both wood and plastic to bond them together.
Finishing:
Sanding: Sand the entire surface, including the inlaid plastic, to ensure a smooth, flush finish.
Polishing: Polish the surface to enhance the wood's natural grain and the plastic's sheen. This step helps in achieving a high-quality, professional finish.
Sealing: Apply a protective sealant to safeguard the inlay work from moisture, wear, and other environmental factors.
Resources:
Materials:
High-quality hardwood (e.g., oak, maple)
Plastic inlay materials (acrylic, PVC, resin)
Adhesive (wood-plastic compatible)
Sandpaper (various grits)
Wood sealant
Tools:
CAD software for design
Router for wood cutting
Precision cutting tools for plastic
Stencils or templates
Polishing tools
Process:
Material Selection:
Wood: Choose high-quality wood with a smooth, uniform grain. Hardwood is typically preferred for inlay work due to its durability.
Plastic: Select plastic materials that are compatible with the wood and suitable for inlay, such as acrylic, PVC, or resin. The plastic should be of high quality, free from impurities, and capable of withstanding cutting and finishing processes.
Design and Pattern Creation:
CAD Design: Use computer-aided design (CAD) software to create precise patterns and designs. Ensure that the design is proportionate to the wood surface and fits the aesthetic requirements.
Stencil Creation: Create a stencil or template to ensure accurate placement of the inlay design on the wood.
Surface Preparation:
Sanding: Thoroughly sand the wood surface to ensure smoothness and remove any imperfections.
Marking: Use the stencil to mark the inlay pattern on the wood. Precision is crucial to avoid gaps between the wood and plastic.
Inlay Process:
Routing: Carefully route the wood surface along the marked lines to create a recess where the plastic will be inlaid. The depth of the recess should be consistent and appropriate for the thickness of the plastic.
Plastic Cutting: Cut the plastic material to match the routed recess. Precision in cutting is essential to ensure a snug fit.
Placement and Adhesion: Place the plastic into the recess, ensuring a tight fit. Use a high-quality adhesive suitable for both wood and plastic to bond them together.
Finishing:
Sanding: Sand the entire surface, including the inlaid plastic, to ensure a smooth, flush finish.
Polishing: Polish the surface to enhance the wood's natural grain and the plastic's sheen. This step helps in achieving a high-quality, professional finish.
Sealing: Apply a protective sealant to safeguard the inlay work from moisture, wear, and other environmental factors.
Resources:
Materials:
High-quality hardwood (e.g., oak, maple)
Plastic inlay materials (acrylic, PVC, resin)
Adhesive (wood-plastic compatible)
Sandpaper (various grits)
Wood sealant
Tools:
CAD software for design
Router for wood cutting
Precision cutting tools for plastic
Stencils or templates
Polishing tools
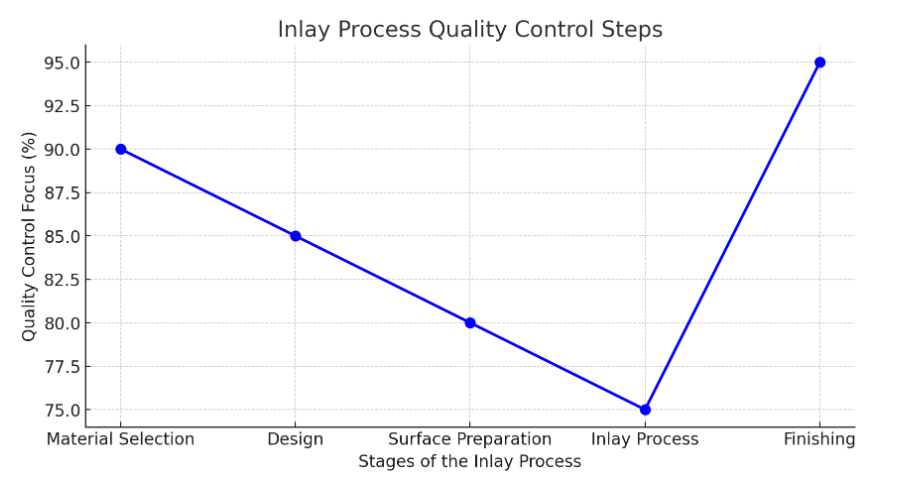
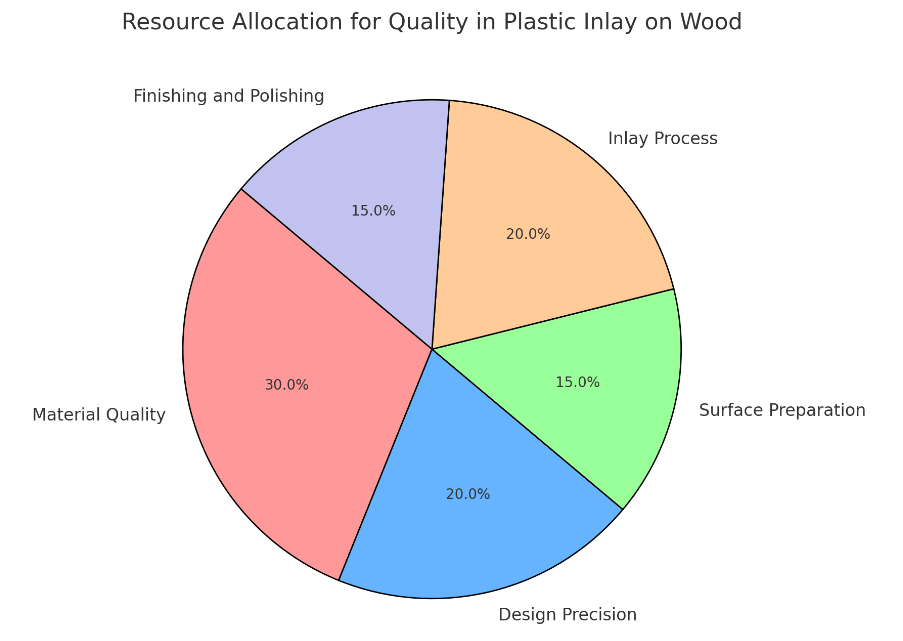
Uniqueness of plastic inlay on wood
Uniqueness in plastic inlay on wood products is achieved through the creation of distinctive, handmade crafts that stand out from mass-produced items. Unique handmade crafts often feature exclusive designs and custom home décor elements that cater to individual tastes and preferences. The ability to offer limited editions and personalized customization allows consumers to acquire bespoke home goods that reflect their personal style. By focusing on exclusive designs and high-quality raw materials, manufacturers can create products that are not only functional but also unique and memorable, distinguishing themselves in the marketplace.
Elements of Uniqueness
Innovative Designs:
Original Concepts: Develop original and creative designs that are not easily replicated.
Artistic Expression: Incorporate artistic elements and personal style to make products stand out.
Functional Integration: Combine aesthetics with functionality to create unique and practical pieces.
Exceptional Craftsmanship:
Skill and Precision: Demonstrate exceptional skill and precision in inlay techniques.
Attention to Detail: Pay meticulous attention to detail to create high-quality products.
Traditional Techniques: Use traditional or heritage techniques to add a unique touch.
Unique Materials:
Rare or Exotic Materials: Incorporate rare or exotic materials to create one-of-a-kind pieces.
Sustainable Materials: Utilize sustainable materials to differentiate your products from those made with conventional materials.
Recycled Materials: Use recycled materials to create eco-friendly and unique products.
Customization Options:
Personalized Designs: Offer customization options to allow customers to create personalized and unique pieces.
Tailored to Preferences: Adapt designs to meet specific customer preferences and tastes.
Storytelling:
Brand Narrative: Develop a compelling brand narrative that connects with customers on an emotional level.
Product Stories: Tell the story behind each product to make it more meaningful and memorable.
Benefits of Uniqueness
Increased Value: Unique products can command higher prices due to their distinctive qualities.
Customer Loyalty: Build strong customer loyalty by offering products that are not readily available elsewhere.
Competitive Advantage: Gain a competitive edge over competitors who offer generic or mass-produced products.
Brand Recognition: Establish a strong brand identity through unique and memorable products.
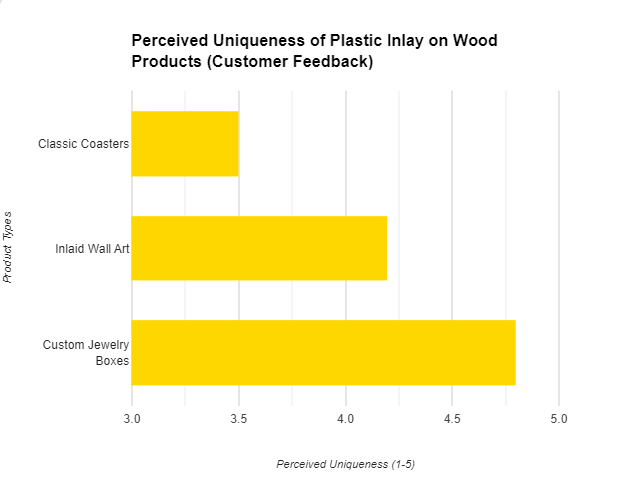
Importance of raw materials in plastic inlay on wood?
Raw material selection is crucial for producing high-quality plastic inlay on wood products. Sustainable raw materials, such as eco-friendly plastics and responsibly sourced wood, are essential for creating ethical and environmentally conscious home products. Ethical sourcing practices ensure that materials are obtained in a manner that respects both environmental and social standards. By prioritizing sustainability in raw material selection, manufacturers can reduce their environmental footprint and support the development of green home décor solutions. This commitment to ethical and sustainable materials aligns with broader trends toward environmental responsibility in manufacturing.
Factors to Consider
Compatibility: Ensure compatibility between the plastic and wood materials to prevent warping, cracking, or delamination.
Durability: Choose materials that are durable and resistant to wear and tear.
Aesthetics: Select materials that complement the desired aesthetic and design of the product.
Sustainability: Consider using sustainable and eco-friendly materials whenever possible.
What are the production steps of plastic inlay on wood?
Production efficiency and craftsmanship are key factors in the manufacture of plastic inlay on wood products. Efficient production processes ensure that products are made in a timely manner without sacrificing quality. Handmade production processes highlight the artisanal skills involved, emphasizing attention to detail and traditional techniques. Craft production technology can enhance efficiency while maintaining the unique characteristics of handmade items. Balancing efficiency with craftsmanship allows manufacturers to scale their operations while preserving the distinctiveness of their products.
Key Production Steps
Design and Planning:
Concept Development: Create the design for the plastic inlay, considering factors like aesthetics, functionality, and materials.
Material Selection: Choose suitable plastic and wood materials based on their properties and compatibility.
Wood Preparation:
Cutting and Shaping: Cut and shape the wood pieces according to the desired design.
Sanding and Finishing: Smooth the wood surfaces and apply any necessary finishes, such as stains or varnishes.
Plastic Preparation:
Cutting and Shaping: Cut and shape the plastic pieces to fit the desired inlay design.
Finishing: Apply any necessary finishes to the plastic, such as polishing or coloring.
Inlay Process:
Preparation: Create grooves or cavities in the wood to accommodate the plastic inlay.
Adhesive Application: Apply a suitable adhesive to the wood and plastic surfaces.
Inlay Placement: Carefully place the plastic inlay into the prepared grooves or cavities.
Securing: Secure the inlay using clamps or other methods to ensure proper adhesion.
Finishing:
Sanding and Smoothing: Sand and smooth the surface of the inlay to ensure a seamless transition between the plastic and wood.
Finishing Touches: Apply any additional finishes, such as polishing or waxing, to enhance the appearance and durability of the product.
Quality Control:
Inspection: Inspect the finished product for defects, such as misalignment, uneven surfaces, or poor adhesion.
Testing: Conduct functional testing to ensure the product meets quality standards.
Production Techniques
Hand Inlay: Traditional method involving manual carving and shaping of the wood and plastic pieces.
Machine Inlay: Using specialized machinery to automate certain aspects of the inlay process, such as cutting and shaping.
Laser Cutting: Precisely cutting and shaping both wood and plastic using laser technology.
CNC Machining: Using computer-controlled machines to create intricate and complex inlay designs.
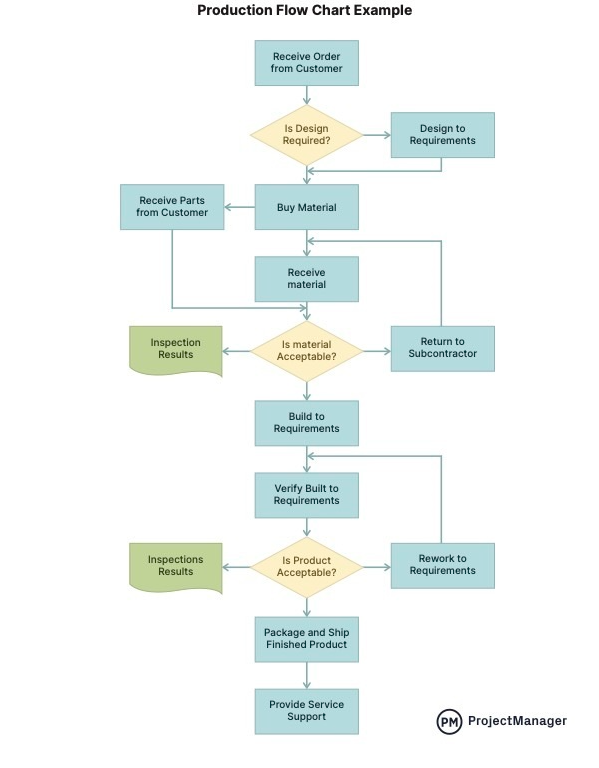
What is the scope of scalability of plastic inlay on wood?
Scalability in the context of handmade plastic inlay on wood products involves expanding production capabilities while maintaining quality. Scaling a handmade business requires careful planning to increase production volume without compromising the craftsmanship and attention to detail that define the products. This includes optimizing production processes, investing in technology, and managing resources effectively. Maintaining quality during scaling is crucial to ensuring that the increased output meets the same high standards as smaller batches. By addressing scalability challenges, manufacturers can grow their business sustainably and reach a larger market.
Factors Affecting Scalability
Production Capacity:
Equipment and Machinery: Having the necessary equipment and machinery to handle increased production volumes.
Labor Resources: Access to a skilled workforce to meet production demands.
Manufacturing Space: Adequate manufacturing space to accommodate expansion.
Supply Chain Scalability:
Raw Material Availability: Ensuring a reliable supply of high-quality raw materials.
Supplier Capacity: Having suppliers capable of meeting increased demand.
Transportation and Logistics: Efficient transportation and logistics systems to handle larger volumes of products.
Financial Resources:
Investment: Access to capital for investments in equipment, facilities, and working capital.
Financial Planning: Effective financial planning and management to support growth.
Market Demand:
Market Analysis: Understanding market trends and potential for growth.
Customer Acquisition: Effective marketing and sales strategies to attract new customers.
Business Model:
Flexibility: A flexible business model that can adapt to changing market conditions.
Scalable Processes: Efficient and scalable processes that can be replicated and expanded.
Scalability Strategies
Modular Design: Design products and processes that can be easily scaled up or down.
Outsourcing: Utilize outsourcing for non-core activities to increase capacity and flexibility.
Technology Adoption: Implement technology solutions to improve efficiency and streamline operations.
Strategic Partnerships: Collaborate with strategic partners to expand market reach and access resources.
Financial Planning: Develop a solid financial plan to support growth and manage risks.
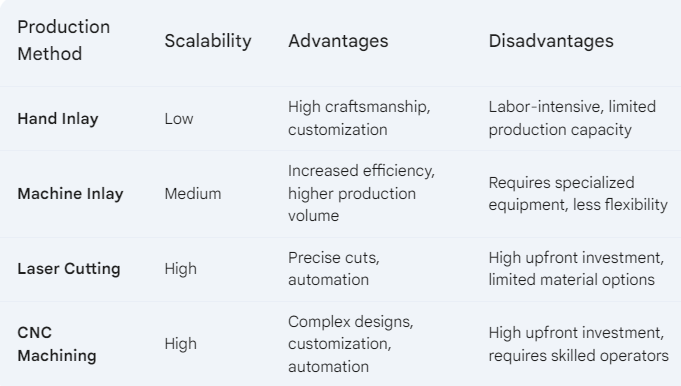
How to do carbon emission management of plastic inlay on wood?
Carbon emission management is an important consideration in the production of plastic inlay on wood products. Handmade production processes, while often more environmentally friendly than industrial methods, still contribute to carbon emissions. Reducing carbon emissions involves adopting practices such as using energy-efficient technologies, optimizing production processes, and sourcing low-carbon materials. Carbon reduction strategies can also include offsetting emissions through environmental initiatives or certifications. By addressing carbon emissions, manufacturers can enhance their sustainability efforts and appeal to environmentally conscious consumers.
Sources of Carbon Emissions
Raw Material Sourcing:
Deforestation: Logging for wood can contribute to deforestation, releasing stored carbon into the atmosphere.
Plastic Production: The production of plastic materials, derived from fossil fuels, emits carbon dioxide.
Manufacturing Processes:
Energy Consumption: The use of energy for manufacturing, such as electricity and heat, can generate carbon emissions.
Chemical Use: The use of chemicals in the production process can contribute to emissions.
Transportation:
Material Transportation: The transportation of raw materials, finished products, and waste generates emissions.
Shipping and Logistics: The shipping and logistics industry contributes to emissions through the use of fossil fuel-powered vehicles.
End-of-Life Disposal:
Landfills: Landfilling of plastic and wood waste can release methane, a potent greenhouse gas.
Incineration: Incinerating waste can emit carbon dioxide and other pollutants.
Strategies for Reducing Carbon Emissions
Sustainable Materials: Use recycled plastics and sustainably sourced wood to reduce the environmental impact of raw material sourcing.
Energy Efficiency: Implement energy-efficient practices in manufacturing facilities to reduce carbon emissions.
Waste Reduction: Minimize waste generation through efficient production processes and recycling programs.
Transportation Optimization: Optimize transportation routes and consolidate shipments to reduce emissions.
Product Design: Design products for durability and repairability to extend their lifespan and reduce waste.
Carbon Offset: Consider purchasing carbon offsets to neutralize your business's carbon emissions.
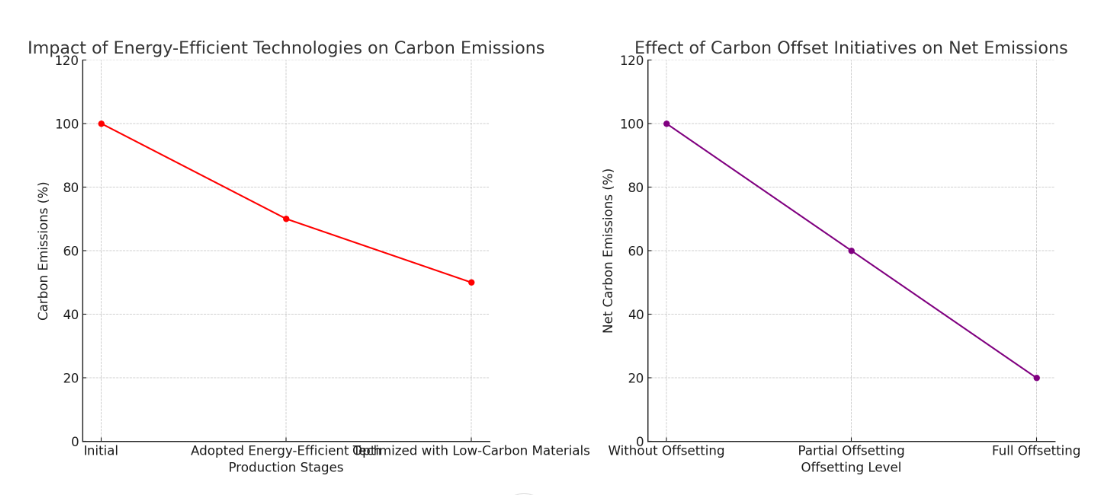
What is the scope of customization of plastic inlay on wood?
Customization in the plastic inlay on wood industry allows for the creation of personalized home décor items that cater to individual preferences. Personalized handmade products offer unique design options and bespoke features that reflect the customer's style and needs. Customization involves working closely with clients to design and produce exclusive home goods that align with their vision. This level of personalization adds value to the products and enhances customer satisfaction by providing tailored solutions that stand out in the market.
Customization Options
Design Customization:
Personalized Patterns: Allow customers to choose from a variety of patterns or design their own.
Custom Colors: Offer a wide range of color options for both the plastic and wood components.
Personalized Messages: Incorporate personalized messages or logos into the inlay.
Material Customization:
Material Selection: Provide customers with a choice of materials, including different types of wood and plastic.
Sustainable Options: Offer sustainable materials like recycled plastics and FSC-certified wood.
Size and Dimensions:
Custom Sizes: Allow customers to specify the desired size and dimensions of the inlay.
Shape Customization: Offer a variety of shapes, such as rectangular, square, or custom-shaped.
Finishing Options:
Finishes: Provide options for different finishes, such as staining, varnishing, or polishing.
Distressing: Offer distressed or aged finishes for a vintage look.
Functional Customization:
Interactive Elements: Incorporate interactive elements like LED lights or hidden compartments.
Storage Solutions: Design inlays with built-in storage or organizational features.
Benefits of Customization
Increased Customer Satisfaction: Meet the unique needs and preferences of individual customers.
Higher Sales: Attract customers who are willing to pay a premium for customized products.
Brand Differentiation: Set your business apart from competitors by offering personalized options.
Customer Loyalty: Build strong customer relationships through personalized experiences.
What is the environmental impact of plastic inlay on wood?
Environmental impact considerations in the production of plastic inlay on wood products involve assessing and mitigating the effects of manufacturing activities on the environment. This includes evaluating the use of materials, energy consumption, and waste generation. By adopting eco-friendly practices and sustainable materials, manufacturers can reduce their environmental footprint and contribute to environmental conservation. The environmental benefits of these practices include reduced pollution, lower resource consumption, and support for biodiversity. Addressing environmental impact is essential for aligning with consumer expectations and regulatory requirements.
Raw Material Sourcing:
Deforestation: The sourcing of wood from unsustainable logging practices can contribute to deforestation.
Plastic Production: The production of plastics, derived from fossil fuels, emits greenhouse gases.
Manufacturing Processes:
Energy Consumption: The use of energy for manufacturing, including electricity and heat, can generate carbon emissions.
Chemical Use: The use of chemicals in the production process can have environmental impacts.
Transportation:
Carbon Emissions: The transportation of materials and finished products contributes to greenhouse gas emissions.
End-of-Life Disposal:
Landfills: Landfilling of plastic and wood waste can release methane, a potent greenhouse gas.
Incineration: Incinerating waste can emit air pollutants.
Strategies for Reducing Environmental Impact
Sustainable Materials: Use recycled plastics and sustainably sourced wood to minimize environmental impact.
Efficient Production: Implement energy-efficient practices and reduce waste generation.
Transportation Optimization: Optimize transportation routes and consolidate shipments to reduce emissions.
Recycling and Composting: Encourage recycling of plastic and wood components and promote composting for biodegradable materials.
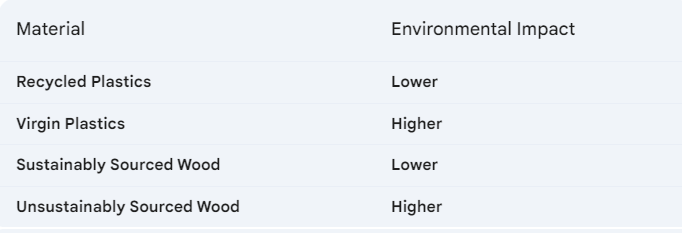
What is the social impact of plastic inlay on wood?
Social impact in the plastic inlay on wood industry focuses on the effects of manufacturing practices on communities and workers. Positive social impacts include providing fair wages, safe working conditions, and opportunities for local employment. Social effects also encompass community engagement and support for local artisans and craftspeople. By fostering a positive social impact, manufacturers can contribute to the well-being of their workforce and communities, enhancing their reputation and building stronger relationships with stakeholders.
Social Impact Areas
Job Creation:
Direct Employment: The plastic inlay on wood industry creates jobs in various roles, including artisans, craftsmen, designers, and production workers.
Indirect Employment: The industry can support indirect jobs in related sectors, such as raw material suppliers, transportation, and retail.
Economic Development:
Local Economies: Contributes to the growth and development of local economies, especially in regions with a strong craft or artisanal tradition.
Export Opportunities: Can create opportunities for exporting products to international markets, boosting economic growth.
Ethical Considerations:
Fair Labor Practices: Ensures fair wages, working conditions, and employee rights.
Community Engagement: Contributes to community development through charitable initiatives or partnerships.
Cultural Preservation:
Traditional Crafts: Preserves traditional crafts and skills associated with plastic inlay on wood.
Cultural Heritage: Contributes to the preservation of cultural heritage and identity.
What is the economic impact of plastic inlay on wood?
Economic impact in the plastic inlay on wood industry involves understanding the effects of production and market dynamics on the economy. This includes analyzing demand and supply trends, which influence pricing and market growth. The economic impact also extends to employability, as manufacturing activities create jobs and support local economies. By contributing to economic development and job creation, manufacturers can play a significant role in fostering economic stability and growth in their regions.
Economic Impacts
Job Creation:
Direct Employment: The industry creates jobs for artisans, craftsmen, designers, and production workers.
Indirect Employment: Supports indirect jobs in related sectors, such as raw material suppliers, transportation, and retail.
Revenue Generation:
Sales and Exports: Generates revenue through the sale of plastic inlay on wood products, both domestically and internationally.
Economic Multiplier Effect: Contributes to the economic multiplier effect, where a dollar spent in the industry can lead to additional economic activity.
Supply Chain Effects:
Local Suppliers: Supports local suppliers of raw materials, tools, and equipment.
Value-Added Products: Creates value-added products that can be sold at higher prices.
Tourism and Cultural Heritage:
Attracting Tourists: May attract tourists interested in the craftsmanship and cultural heritage associated with plastic inlay on wood.
Preserving Traditions: Contributes to the preservation of traditional skills and crafts.
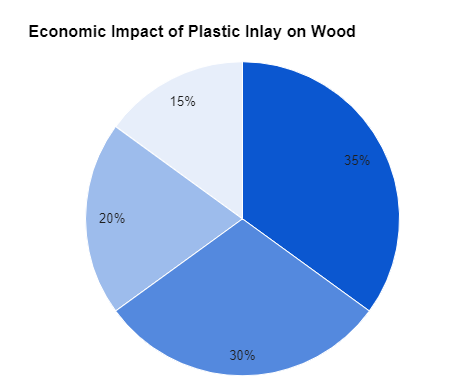
Design Thinking in plastic inlay on wood
Design thinking in the plastic inlay on wood industry emphasizes innovative approaches to creating handmade products that meet user needs and preferences. Design thinking involves understanding the user experience, generating creative solutions, and prototyping to refine product designs. Innovative handmade products result from applying design thinking principles to address functional and aesthetic challenges. By focusing on user-centered design, manufacturers can develop products that are not only visually appealing but also practical and tailored to consumer demands.
Applying Design Thinking to Plastic Inlay on Wood
Empathize:
Understand Customers: Gain a deep understanding of customer needs, preferences, and pain points.
Research Trends: Stay informed about industry trends, emerging technologies, and changing consumer tastes.
Define:
Identify Challenges: Clearly define the challenges or problems that customers face.
Set Goals: Establish specific goals and objectives for your design.
Ideate:
Generate Ideas: Brainstorm a wide range of creative solutions and possibilities.
Encourage Diversity: Foster a collaborative environment where diverse perspectives are valued.
Prototype:
Create Models: Develop prototypes or mock-ups of potential designs.
Test and Iterate: Test prototypes with customers and gather feedback to refine the design.
Test:
User Testing: Conduct user testing to evaluate the effectiveness and usability of the design.
Gather Feedback: Collect feedback from customers and stakeholders to identify areas for improvement.
Benefits of Design Thinking
Innovative Solutions: Develop unique and creative solutions that address customer needs.
Improved Customer Satisfaction: Create products that resonate with customers and meet their expectations.
Reduced Risk: Minimize the risk of product failure by involving customers in the design process.
Increased Efficiency: Streamline the design and development process through rapid prototyping and iteration.
What is the turnaround time of plastic inlay on wood?
Turnaround time refers to the efficiency of production processes and the speed at which plastic inlay on wood products are manufactured and delivered. Reducing production time involves streamlining workflows, improving process efficiency, and leveraging technology to accelerate production. Efficient craft production ensures that products are completed and shipped promptly, meeting customer expectations for timely delivery. By optimizing turnaround time, manufacturers can enhance customer satisfaction, manage demand fluctuations, and improve overall operational efficiency.
Factors Affecting Turnaround Time
Order Complexity: The complexity of the design, size, and quantity of the order can significantly impact turnaround time.
Material Availability: The availability of the required plastic and wood materials can influence production timelines.
Production Capacity: The capacity of the manufacturing facility and the availability of skilled labor can affect turnaround time.
Customization: Customized orders may require additional time for design, prototyping, and production.
Shipping and Delivery: The chosen shipping method and distance to the customer can impact delivery times.
Strategies for Managing Turnaround Time
Efficient Production Processes: Streamline production processes to minimize bottlenecks and delays.
Inventory Management: Maintain adequate inventory levels of commonly used materials to avoid delays.
Capacity Planning: Ensure that the manufacturing facility has the capacity to handle incoming orders and avoid overloading.
Communication with Customers: Keep customers informed about expected turnaround times and any potential delays.
Prioritization: Prioritize orders based on urgency and customer needs.
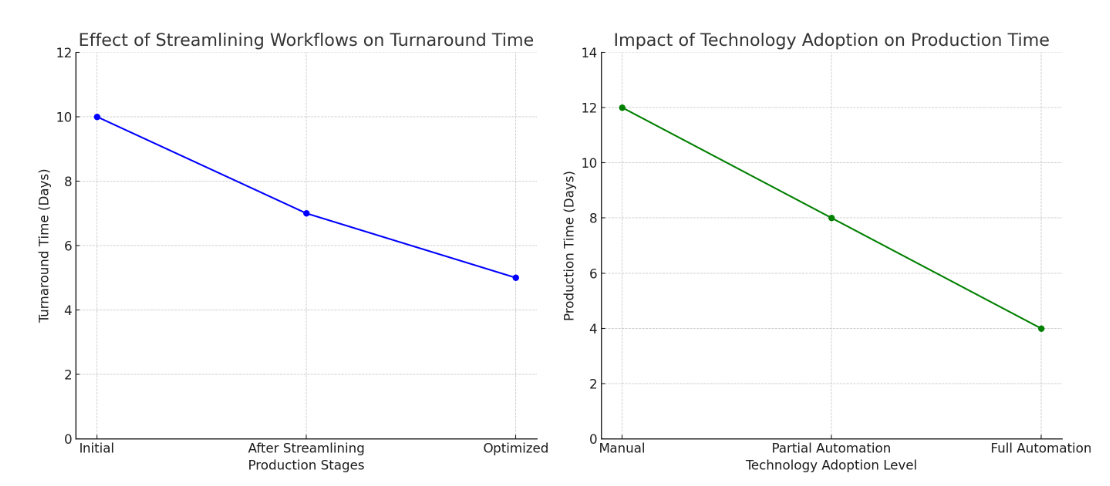
What are the payment terms of plastic inlay on wood?
Payment terms in the handmade plastic inlay on wood industry involve establishing clear financial agreements and service terms with customers and suppliers. Payment terms specify the conditions under which payments are made, including deadlines, payment methods, and any applicable discounts or penalties. Transparent payment terms help in managing cash flow, reducing financial risks, and ensuring smooth transactions. By defining and adhering to payment terms, manufacturers can maintain financial stability and build trust with their business partners.
Common Payment Terms
Net 30: The customer has 30 days from the invoice date to pay in full.
Net 60: The customer has 60 days from the invoice date to pay in full.
2/10, Net 30: The customer can receive a 2% discount if the payment is made within 10 days of the invoice date. The full amount is due within 30 days.
Credit Card: The customer can pay using a credit card, typically with a processing fee.
Wire Transfer: The customer can make a direct bank transfer to the seller's account.
Factors Affecting Payment Terms
Customer Creditworthiness: The creditworthiness of the customer will influence the payment terms offered.
Industry Standards: The payment terms commonly used in the plastic inlay on wood industry.
Business Relationship: The length and nature of the business relationship can impact payment terms.
Order Size: Larger orders may qualify for more favorable payment terms.
Credit Checks
To assess customer creditworthiness and mitigate the risk of bad debts, businesses in the plastic inlay on wood industry should conduct credit checks before extending credit.
What are the key certifications of plastic inlay on wood?
Certifications for plastic inlay on wood products ensure compliance with industry standards and regulations. Certified handmade products often undergo rigorous testing and evaluation to verify their quality, safety, and environmental impact. Regulatory compliance and certification processes involve meeting specific criteria set by industry bodies and obtaining relevant certifications that attest to the product's standards. Achieving certification enhances credibility, provides assurance to customers, and supports adherence to legal and industry requirements.
Key Certifications
Craftmanship and Artisanship:
Master Craftsman: Certifications recognizing exceptional skill and expertise in plastic inlay techniques.
Apprentice Certifications: Certifications for individuals in training to develop skills in plastic inlay craftsmanship.
Design and Aesthetics:
Design Certifications: Certifications in design principles, color theory, and aesthetic appreciation relevant to plastic inlay.
Interior Design Certifications: Certifications for those who specialize in designing interiors using plastic inlay techniques.
Business and Entrepreneurship:
Entrepreneurship Certifications: Certifications in business management, marketing, and entrepreneurship for those starting or running businesses in plastic inlay.
Financial Management Certifications: Certifications in financial planning and management relevant to the plastic inlay industry.
Sustainability and Ethics:
Sustainability Certifications: Certifications in sustainable practices, environmental impact assessment, and ethical sourcing.
Fair Trade Certifications: Certifications for businesses committed to fair trade principles and ethical sourcing.
Benefits of Certifications
Enhanced Credibility: Certifications can enhance your credibility as a skilled professional in the plastic inlay industry.
Improved Job Prospects: Certifications can increase your job opportunities and potential earning potential.
Professional Development: Certifications can help you stay up-to-date with industry trends and best practices.
Networking Opportunities: Certifications can connect you with other professionals in the field and provide networking opportunities.
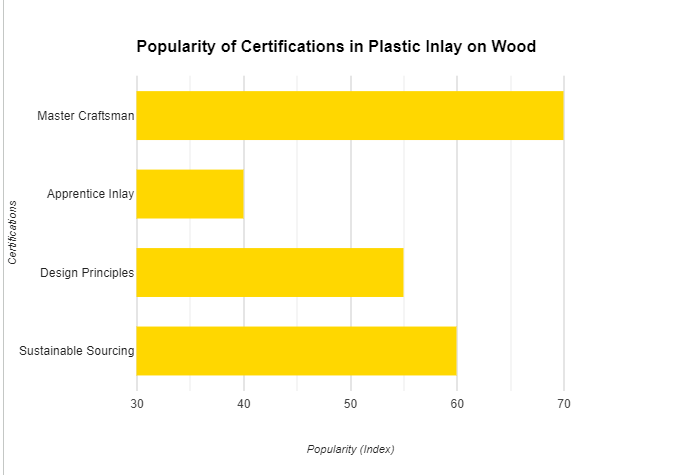
THE PRODUCTS IN THE MARKET
The traditional inlay woodwork of Punjab is a highly intricate craft that demands a high degree of precision, practice, and meticulous manual labor. The artisans have kept this art form alive through their dedication and quality of their work, despite facing various challenges and changes over time. This craft not only reflects the vibrant culture and spirit of Punjab but is also celebrated worldwide for its uniqueness and beauty.
Inlay work involves a technique where pieces of contrasting colors are inserted into hollow spaces to create beautiful designs. This meticulous process results in a striking contrast that enhances the visual appeal of the finished product.
The artisans of Hoshiarpur are renowned for creating a variety of inlaid wooden items, including:
Furniture: Inlaid table and chair sets
Decorative Items: Chest boxes, corner pieces, and decorative elephants
Games and Accessories: Chess boards, jewelry boxes, trays
Utility Items: Modern utility products like trays, pen stands, photograph frames, flower vases, charkhas (spinning wheels), and agarbati (incense) stands
These products are highly sought after not only for their functionality but also for their artistic value. The intricate designs and vibrant colors reflect the rich cultural heritage of Punjab, making these items popular both within India and internationally.
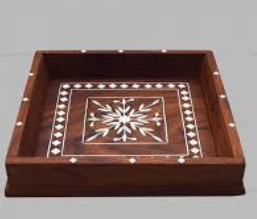
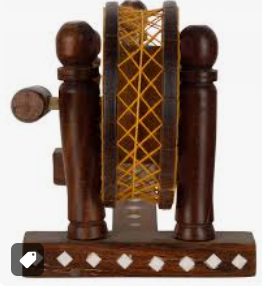
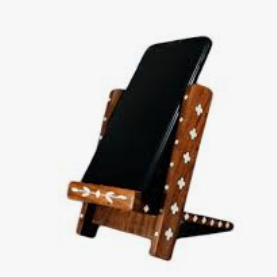
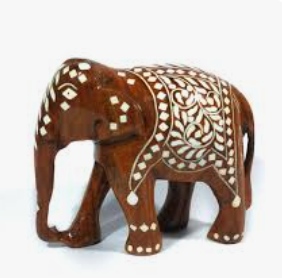
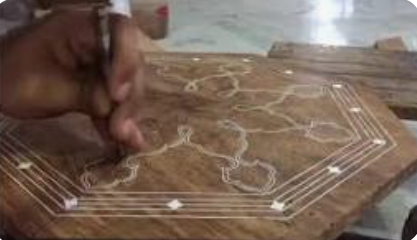
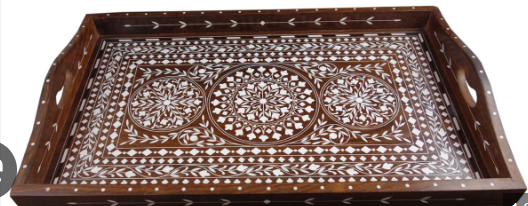
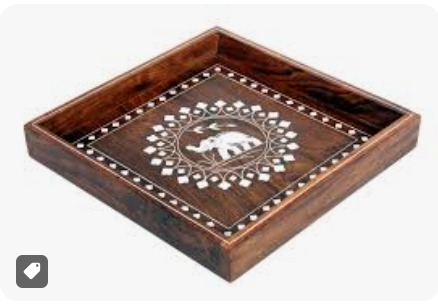
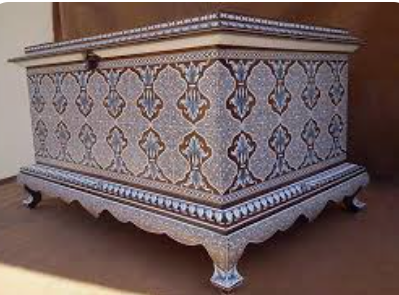
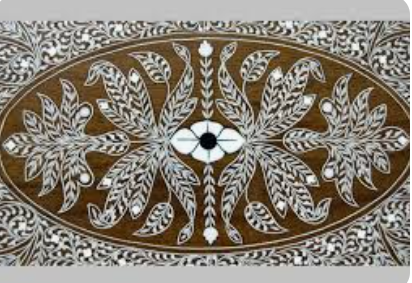
CHALLENGES AND THE FUTURE OF THE CRAFT
Despite its rich tradition and global acclaim, the craft of inlay woodwork in Hoshiarpur faces significant challenges. One of the major issues is the scarcity of Sheesham wood, which is a preferred material for its durability and fine grain. Additionally, the number of skilled artisans specializing in this craft is dwindling, partly due to the labor-intensive nature of the work and the lure of more modern and profitable occupations.
The declining number of artisans and the limited availability of traditional materials threaten the survival of this beautiful craft. While some efforts have been made to preserve and promote inlay woodwork, more support is needed to ensure its continuity. This includes providing artisans with better access to raw materials, encouraging younger generations to learn the craft, and promoting these products in broader markets.
The persistence and originality of the artisans have been crucial in keeping this traditional art form alive. It is essential to recognize and support these artisans to ensure that the craft does not fade into obscurity. By fostering a greater appreciation for the craft and its cultural significance, there is scope for a revival and sustained interest in inlay woodwork from Punjab. This would not only preserve an important aspect of the region's heritage but also continue to bring joy and admiration to people around the world who appreciate the beauty of such handcrafted art.
Manufacturers of Plastic Inlay on Wood:-
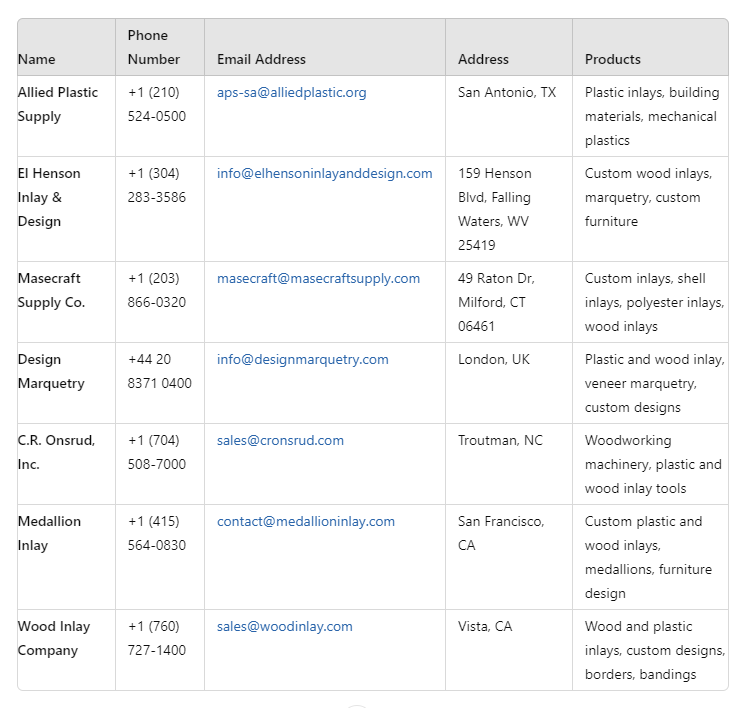
Details of the paper from which the information was taken:
Shri. Rupan Matharu and Sanmati Hosure - Plastic Inlay on Wood Punjab - IDC, IIT Bombay - D’Source - Paper Link
Recommended

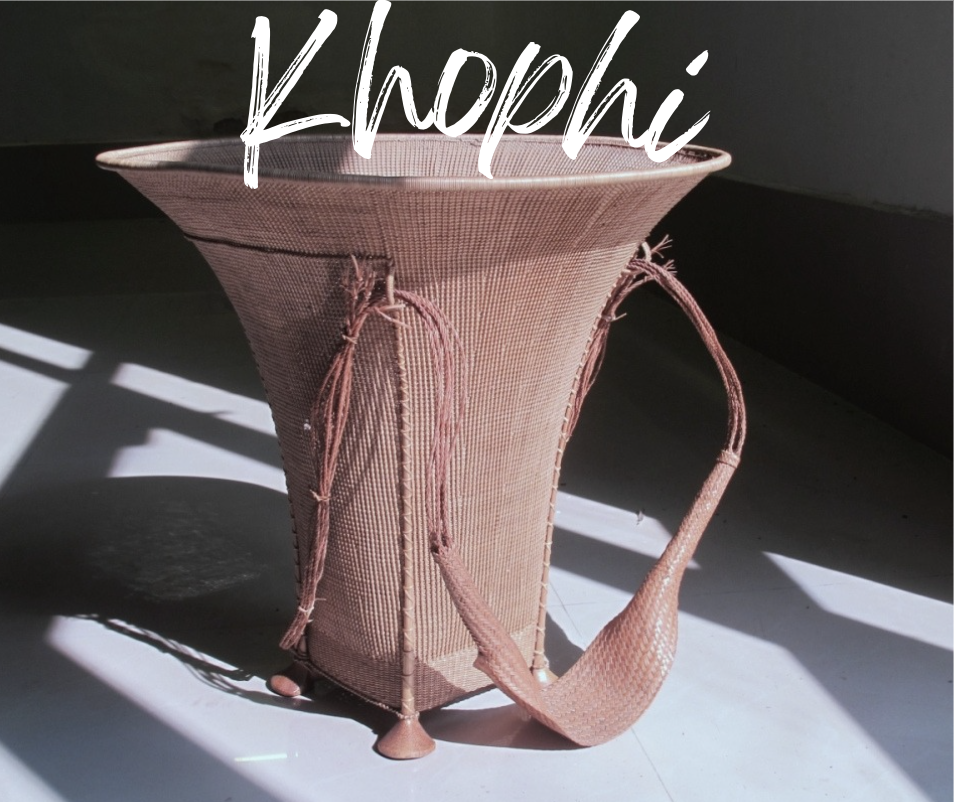
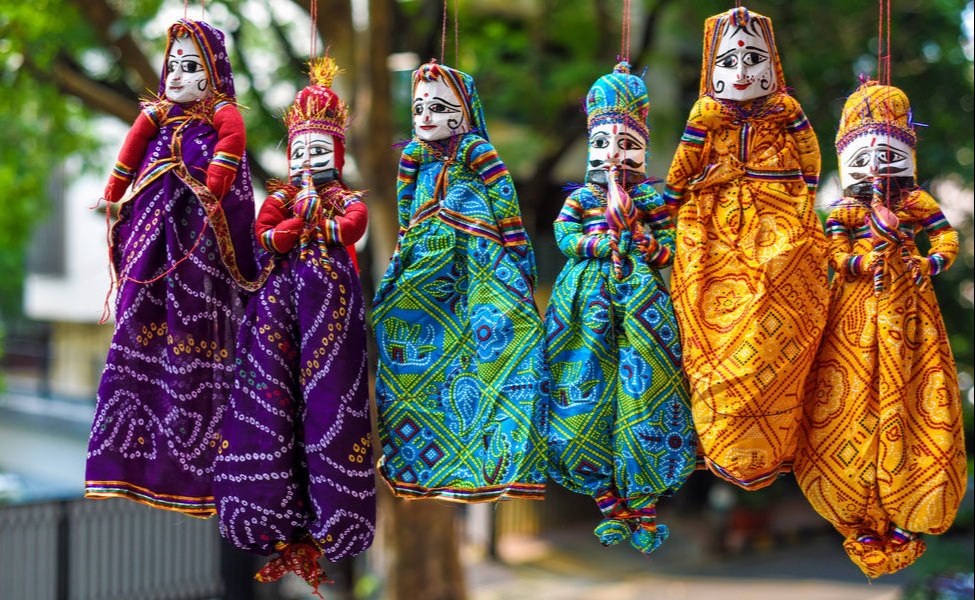
Wholesale / B2b Kathputli Puppets From Ahemdabad
Dec 16, 2024