The Blueprint For Production Excellence: A Step-by-step Guide To Optimizing Your Operations
Feb 01, 2024 | Tanya Sachdeva
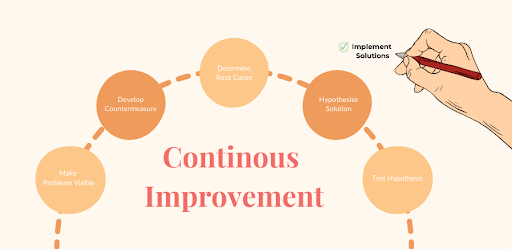
Production excellence in the Indian manufacturing landscape, especially in domains like fashion accessories, apparel, and interior products, is a multifaceted concept. It encapsulates not just the efficiency of production processes but also the adherence to quality standards, innovation in design, and the ability to meet global demands in a timely manner. For companies like Aarav, this meant not only mastering traditional craftsmanship but also embracing modern technology and practices to ensure consistency, scalability, and sustainability.
Production excellence, a term broadly used across various industries, signifies a commitment to manufacturing superiority. Its definition varies from one sector to another, but the underlying principles of operational efficiency, waste reduction, continuous improvement, and quality remain consistent.
OPERATIONAL EFFICIENCY
Operational efficiency is about maximising output while minimising input. It's not just about speed; it's about smart work. In the Indian context, numerous companies have exemplified this. For instance, in the textile and apparel industry, Aditya Birla Fashion and Retail Limited (ABFRL) restructured its supply chain management.
They integrated real-time data analytics for inventory tracking, optimised their logistics for faster delivery, and automated parts of their production line. This not only improved their production rate but also enhanced the quality of the output.
In the automotive sector, an Indian auto-components manufacturer revolutionised its assembly line by integrating robotics and automation. This not only increased the production speed but also brought down the error rate significantly, leading to a higher yield of quality products.
WASTE REDUCTION
Waste reduction is an integral part of production excellence, focusing on minimising unnecessary resource usage and inefficiencies. Indian companies have increasingly adopted Lean and Six Sigma methodologies for this purpose. For example, a food processing company in India implemented Lean techniques to optimise their production process.
They identified and eliminated steps that added no value to the final product, thus reducing waste and increasing efficiency. Similarly, an electronics manufacturer in India employed Six Sigma techniques to improve process quality. By rigorously analysing production data, they identified and addressed sources of defects, significantly reducing variability in their manufacturing process and enhancing the overall quality of their products.
CONTINUOUS IMPROVEMENT (KAIZEN)
Continuous improvement, often referred to as Kaizen, is a philosophy of ongoing, incremental improvement in the manufacturing process. In India, this approach has been embraced in various industries. A prominent IT firm used Kaizen to refine its software development lifecycle. By regularly soliciting and implementing feedback from employees at all levels, the company fostered a culture of continuous learning and improvement, leading to increased efficiency and better client satisfaction.
ROLE OF QUALITY
Quality is the thread that weaves these pillars together. It is about consistently meeting and exceeding customer expectations. For Indian companies, quality has become a key differentiator in the global market. A case in point is a luxury interior design company from India that has gained international acclaim. Their attention to detail, commitment to using high-quality materials, and adherence to global standards have made them a preferred choice in the competitive luxury market.
THE CHECKLIST: ENSURING QUALITY AT EVERY STAGE
1. Design: Emphasis on Design for Manufacturing (DFM) and Prototyping
In the design phase, Design for Manufacturing (DFM) and prototyping are critical. For instance, Tata Motors, a leading Indian automotive company, effectively utilizes DFM. By designing components for ease of manufacturing, they reduce costs and improve efficiency. In prototyping, Godrej, known for its diverse product range including appliances and furniture, leverages rapid prototyping techniques. This approach allows for quick iterations and refinements, ensuring the final design is both manufacturable and meets quality standards.
Design for Manufacturing (DFM), Design for Assembly (DFA), and Design for Failure (DFF) are three methodologies that ensure quality and efficiency at different stages of product development.
Design for Manufacturing(DFM) focuses on simplifying the manufacturing process of a product. By considering manufacturing constraints during the design phase, DFM aims to reduce production costs and complexity. It involves selecting the most cost-effective materials and processes to achieve the desired product quality and functionality.
The intent is to design products that are easy to manufacture without requiring expensive, complex, or highly specialized equipment.
Design for Assembly (DFA) is a process that emphasizes the ease of product assembly. The goal is to reduce the product’s assembly time and costs by minimizing the number of assembly operations and by designing parts that are easy to handle, fit, and fasten. Simplified assembly processes lead to faster production times, lower labor costs, and improved product reliability. DFA also helps in reducing the likelihood of assembly errors that can affect product quality.
Design for Failure (DFF), sometimes known as Design for Reliability, is focused on anticipating potential modes of failure within a product and designing to avoid these failures. It involves understanding how products might fail under different conditions and then incorporating solutions to prevent such failures or to minimize their impact. This could include adding redundancy, improving component quality, or enhancing product design to withstand stress and usage over time.
These concepts are integral parts of a holistic approach to product quality and efficiency. By considering manufacturing, assembly, and failure during the design stage, companies can ensure that their products are not only high in quality but also economical to produce, easy to assemble, and reliable over their lifespan, thereby satisfying customer needs and reducing costs.
2. Material Sourcing: Vendor Quality Assessment and Raw Material Inspection. In material sourcing, selecting the right vendors and inspecting materials is crucial. Reliance Industries, a conglomerate with a significant presence in textiles, implements rigorous vendor selection processes. They assess the quality systems of suppliers to ensure only high-quality raw materials enter their supply chain. In raw material inspection, Asian Paints, a leader in the paint industry, exemplifies best practices by conducting thorough checks on all incoming materials to maintain product consistency and quality.
3. Manufacturing: Process Standardization and Real-Time Monitoring
During manufacturing, standardisation and monitoring are key. Bajaj Auto, a major player in the automotive sector, has standardised its manufacturing processes to ensure consistency across its product lines. They also employ real-time monitoring to quickly identify and rectify any deviations from standard procedures, ensuring product quality.
4. Inspection: Comprehensive Testing Methods and Feedback Mechanisms
Inspection is a critical step to catch and address issues. Dr. Reddy's Laboratories, a prominent pharmaceutical company, employs a stringent inspection regimen. They use a combination of automated and manual testing to ensure their products meet global health and safety standards. Feedback mechanisms are in place to incorporate learnings from the inspection process, facilitating continuous improvement.
5. Packaging: Focus on Innovative and Safe Packaging Designs
Finally, packaging plays a crucial role in product integrity. Havells, an electrical equipment company, focuses on packaging designs that ensure product safety during transportation and are environmentally sustainable. Their innovative packaging solutions protect delicate components while minimizing waste.
IMPLEMENTING THE CHECKLIST
Training and Skill Development
Training is the cornerstone of effective implementation. For instance, Infosys, a global leader in technology services, places immense emphasis on employee training. They have established extensive training programs to ensure their staff is well-versed in the latest technologies and methodologies. This focus on skill development not only boosts productivity but also ensures adherence to quality standards. Similarly, Mahindra & Mahindra, in the automotive sector, conducts regular training sessions for its workforce. These sessions cover everything from basic skills to advanced manufacturing techniques, ensuring that all employees are equipped to maintain high-quality standards in their work.
Communication and Collaboration
Effective communication across all levels of the organisation is crucial for the successful implementation of quality checklists. Tata Steel, known for its global presence in the steel industry, has implemented a robust internal communication strategy. This strategy ensures that every employee, from the shop floor to the executive level, understands the quality standards and their role in maintaining them.
In addition, Larsen & Toubro, a major player in construction and engineering, fosters a culture of collaboration and open communication. Regular meetings and feedback sessions help identify areas for improvement, ensuring that quality standards are consistently met.
Accountability and Monitoring
Accountability is essential for ensuring that quality standards are not just implemented but sustained over time. Reliance Industries, in their petrochemical division, has established clear accountability mechanisms. Regular audits and performance reviews help maintain a high standard of quality in their manufacturing processes.
Addressing Challenges and Solutions
Indian industries face unique challenges, such as diverse market demands and supply chain complexities. For example, Hero MotoCorp, the world's largest manufacturer of two-wheelers, faces challenges in managing a vast supply chain. They address this through rigorous supplier audits and adopting a centralized supply chain management system to ensure quality consistency.
Benefits of Production Excellence
Production excellence yields tangible benefits for businesses, contributing significantly to their success and sustainability. These benefits can be quantified through customer satisfaction and loyalty, cost reduction and waste minimization, enhanced efficiency and productivity, and improved brand reputation and market competitiveness.
(I)Customer Satisfaction and Loyalty
Customer satisfaction is a critical benchmark of success, often leading to loyalty and repeat business. A study by Bain & Company found that increasing customer retention rates by 5% increases profits by 25% to 95%. An Indian success story in this regard is Maruti Suzuki. Known for their quality cars and customer service, they have one of the highest customer retention rates in the Indian automotive sector. Their focus on quality and customer satisfaction has resulted in a loyal customer base, with a significant portion of their sales coming from repeat customers.
(II)Cost Reduction and Waste Minimization
Efficient production processes significantly reduce costs and minimise waste. As per a report by McKinsey & Company, companies that excel in production efficiency can reduce their manufacturing costs by 10-30%. An example of this is found in the operations of ITC Limited, a conglomerate with a substantial presence in the FMCG sector. By implementing Lean manufacturing techniques, ITC has reduced waste in its supply chain, leading to cost savings and enhanced profit margins.
(III)Efficiency and Productivity
Efficiency and productivity are direct outcomes of production excellence. According to the World Economic Forum, companies that integrate advanced production technologies see up to 7% higher productivity compared to others. Tata Steel showcases this benefit. By adopting advanced manufacturing technologies and automation, they have improved their operational efficiency, resulting in a 5% increase in productivity over the past few years.
(IV)Brand Reputation and Market Competitiveness
A strong brand reputation and competitive market standing are critical for business success. As per a survey by Deloitte, 85% of business leaders believe that advanced manufacturing technologies are essential for market competitiveness. Reliance Jio, a relatively new entrant in the telecommunications market, has rapidly gained a competitive edge through its focus on quality and innovation. Their commitment to providing high-quality services at affordable prices has not only enhanced their brand reputation but also disrupted the market, making them a formidable competitor.
In conclusion, the pursuit of production excellence offers manifold benefits. It not only ensures customer satisfaction and loyalty but also drives cost
efficiency, enhances productivity, and bolsters brand reputation and market competitiveness. These benefits are not just theoretical but are evidenced by the success stories of leading Indian companies across various sectors.
CONTINUOUS IMPROVEMENT IN INDIAN INDUSTRY PRACTICES
Continuous improvement, a key element of production excellence, is about constantly seeking ways to make processes more efficient, cost-effective, and quality-oriented. In the Indian industrial landscape, this concept has been embraced with vigor, adapting global methodologies to local contexts. This comprehensive approach involves a range of tools and methods, underpinned by a culture that values regular process reviews and updates.
UNDERSTANDING CONTINOUS IMPROVEMENT
Continuous improvement, or Kaizen, is grounded in the philosophy that small, ongoing positive changes can reap significant improvements. It’s a long-term approach that systematically seeks to achieve incremental changes in order to improve efficiency and quality. In the Indian context, continuous improvement has been pivotal in transitioning industries from traditional labor-intensive methods to more technology-driven, efficient processes. This shift has been significant in industries such as automotive, pharmaceuticals, IT, and manufacturing.
Tools and Methods for Continuous Improvement
1. Lean Manufacturing: Originating from the Toyota Production System, Lean Manufacturing is about eliminating waste within manufacturing systems. Indian companies, like Ashok Leyland in the automotive sector, have adopted lean principles to reduce waste and improve process efficiency.
2. Six Sigma: A set of techniques aimed at improving the quality of process outputs by identifying and removing causes of defects, Six Sigma has found favor in India, particularly in companies like Wipro and Tata Motors. These companies use Six Sigma to reduce variability in their processes and improve product quality.
3. Total Quality Management (TQM): TQM is a management approach centered on quality, based on the participation of all members of an organization. Indian conglomerates like the Aditya Birla Group have incorporated TQM practices to enhance their operational excellence.
4. 5S System: This is a workplace organization method that uses a list of five Japanese words: seiri, seiton, seiso, seiketsu, and shitsuke. Translated into English as Sort, Set in order, Shine, Standardize, and Sustain. Companies like Hindustan Unilever have implemented 5S to organize and manage the workspace efficiently.
Implementing Continuous Improvement
Implementation of continuous improvement in Indian industries involves several key steps:
Employee Training and Involvement: Training employees in continuous improvement methodologies is crucial. Infosys, for instance, has a dedicated training program that equips its employees with the necessary skills and knowledge for process improvement.
Setting Benchmarks and Metrics: Companies need to establish clear benchmarks and metrics to measure the effectiveness of their continuous improvement efforts. Reliance Industries, for instance, uses specific key performance indicators (KPIs) to measure the impact of their continuous improvement initiatives.
Regular Process Reviews and Updates: To ensure continuous improvement, regular reviews of processes are essential. Tata Steel conducts periodic audits and reviews of its operational processes to identify areas for improvement.
Embracing Technological Advancements: Utilizing the latest technology is key to continuous improvement. Mahindra & Mahindra, in the automotive sector, uses advanced data analytics and automation technologies to continuously improve their manufacturing processes.
Challenges and Solutions
Implementing continuous improvement in the Indian context comes with its own set of challenges. One major challenge is the resistance to change, particularly in traditional industries. To address this, companies need to create a culture that embraces change and innovation. For example, Hero MotoCorp has established a culture that encourages innovation and continuous learning, helping to overcome resistance to change.
Another challenge is the skill gap. With rapidly evolving technologies and methodologies, keeping the workforce updated is crucial. Companies like Larsen & Toubro have addressed this by investing heavily in training and development programs.
Industry Insights
Continuous improvement is not just a strategy but a mindset. Indian companies are increasingly recognizing that to remain competitive, both on a national and global scale, they must continually improve. By implementing tools like Lean, Six Sigma, and TQM, and by fostering a culture of innovation and adaptability, these companies are setting new benchmarks in operational excellence.
For instance, in the IT sector, Infosys has been a pioneer in adopting continuous improvement methodologies. They have integrated agile methodologies into their software development processes, ensuring rapid and continuous improvement in their project deliveries. This approach has not only increased efficiency but also significantly enhanced client satisfaction.
In the pharmaceutical industry, companies like Sun Pharma have implemented continuous improvement in their manufacturing processes to adhere to stringent global quality standards. By doing so, they have been able to reduce production costs, minimize waste, and ensure the delivery of high-quality products.
The journey through the intricacies of production excellence in the Indian B2B sector underscores its undeniable importance.
From the meticulous design and material sourcing stages, through the rigorous processes of manufacturing and inspection, to the final touches in packaging, every step is vital. The commitment to continuous improvement and adherence to a structured quality checklist not only enhances operational efficiency but also elevates the overall value of products and services in the global marketplace.
As we conclude, it’s imperative to remember that production excellence is not a static achievement but a continuous journey. It demands ongoing commitment, adaptation to new technologies, and relentless pursuit of improvement. For Indian companies aspiring to scale new heights, the path is clear: embrace the principles of production excellence, invest in continuous improvement, and remain steadfast in the quest for quality.
The call to action for readers, especially those in the Indian B2B sector, is to take these insights and translate them into action. Assess your current production practices, identify areas for improvement, and relentlessly pursue excellence. In doing so, you'll not only contribute to the growth of your organisation but also to the larger narrative of India's burgeoning role in the global economy.
Recommended
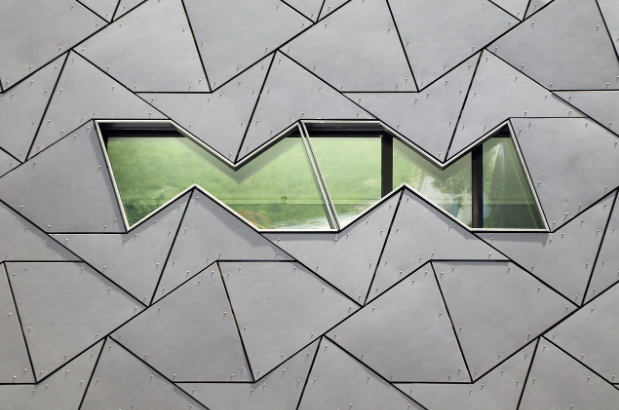

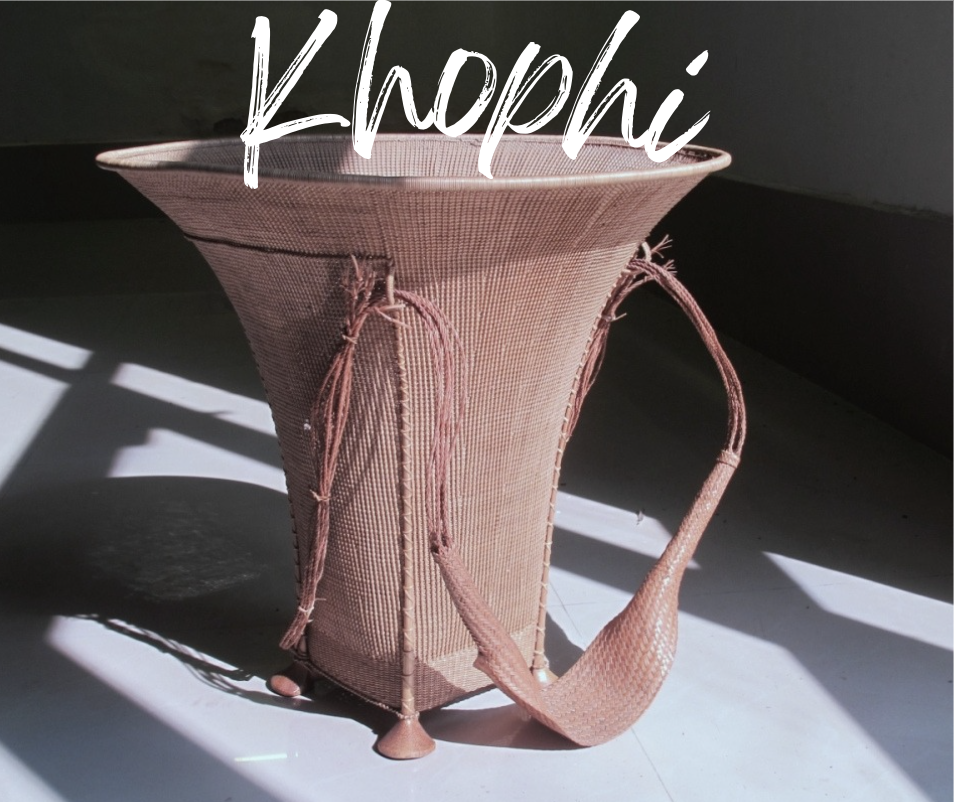