Supply Chain As The Backbone Of Any Business
May 27, 2022 | Brinda Koundjim Mamiafo Youdjeu
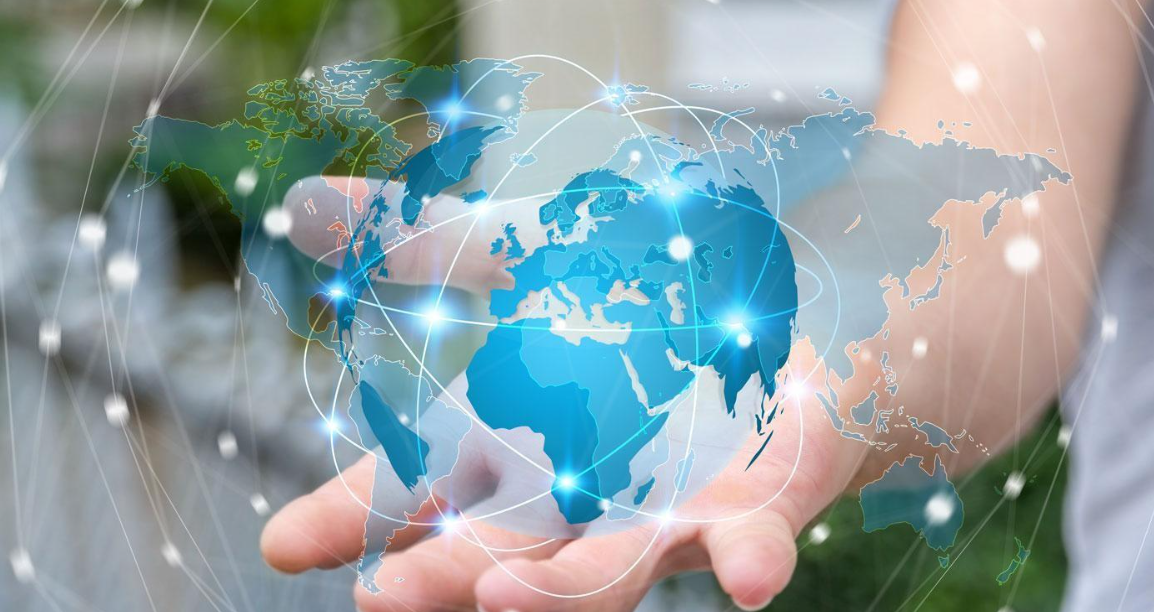
What are its objectives?
To coordinate operations (physical operations and information flow), while maximising benefits to customers (satisfaction and loyalty), and sales (profitability)
Business to Business SCM (Example RHM)
Business-to-business (B2B), is a form of transaction between businesses, such as one involving a manufacturer and wholesaler, or a wholesaler and a retailer B2B transactions tend to happen in the supply chain, where one company will purchase raw materials from another to be used in the production of other products or services which are sold, rented, or supplied to other businesses. Finished products can then be sold to individuals via business-to-consumer transactions.
Some key pillars of supply chain management
Sustainable Supply Chain
When we talk about supply chain the first thing that comes to our mind is logistics and logistics here refers to the transportation of goods.
Transportation has a significant impact on carbon footprint and the logistics chain therefore has an important role to play in controlling scope 3.
There are some factors to be taken into consideration for a successful sustainable supply chain such as:
Choice of raw materials
Type of conversation
Social, environmental and financial responsibility
Choice of raw materials
Since we talk about sustainability, the raw materials used in the production phase to the end phase should be well chosen for a successful sustainable supply chain.
Understanding the materials you are supplied with, how they are sourced, and the environmental impact they may have, is key to understanding how you can address these issues and ensure a transparent and ethical supply chain. Recyclability, material longevity, biodegradability and lower CO2 emissions are some important criterias when choosing your raw materials.
Type of conversation
As inflation and supply shortages are projected to continue, supply chain managers must adopt resource conservation strategies to prevent risks to their organisations.
they three conservation strategies:
1. Slow down primary consumption by employing circular economy model
A circular economy is an economic model designed to minimise resource input, as well as waste and emission production. It targets to rebuild all available types of capital, including financial, human, social, and natural. Essentially, a circular economy describes a regenerative economic system.
2. Treat waste like a value-based asset
Supply chain managers should be able to capitalise on the potential waste.With new law being surpassed round manufacturer duty and adjustments in waste regulation, waste may be more and more more visible as a liability – while it is able to additionally be a resource
3. Preserve natural capital
Every Organisation depends on natural Capital such as air, water and soil for their supply chain. A good preservation of these free natural resources will consequently lead to a good supply chain management
Social, environmental and financial responsibility
Social responsibility involves the moral, ethical, and philanthropic expectations that society has of a business.
This means making sure that every person in your sustainability chain, from company employees to those working for your suppliers, are treated fairly, in line with human rights laws and labour laws.
Workers should be provided with:
A work environment that is safe and free from safety risks and hazards
Free from discrimination of any kind
Compensated fairly
Treated with dignity and respect
Compensated fairly
Environmental responsibility
Ensure that current processes or interactions with the environment keep the environment as pristine as naturally possible. It's essential for businesses to understand all the ways in which they impact the environment.
Organizations need to take actions to reduce their environmental impact and to adhere to the relevant environmental obligations and laws.
Basic international laws like those of the UN’s Paris Agreement, for examples to which many countries around the world are signed up, and the Carbon Disclosure Project (CPD).
Financial responsibility
Financial responsibility is also key to your supply chain’s sustainability and fulfilling your obligations to partners, employees, and the communities in which your supply chain operates.
Financial responsibility in a sustainable supply chain includes compliance with financial laws and regulations, financial planning, risk management, and insurance coverage.
Some of the typical financial responsibilities of businesses across a supply chain are:
Paying employees and suppliers on time and in full
Paying national taxes in the countries you operate within
Paying into employee pensions and health insurance
Operating responsibly and within a company’s means
Regularly auditing and reviewing company finances
Having the necessary insurance coverage and reserve funds to keep your business afloat in unexpected events or emergency situations
People/Supplier Selection
It is one of the most important pillars for good supply chain management because they are the ones to make things happen.
It is very important to think about peoples competency which is required to deliver a supply chain strategy. They act as agents of delivery for products and they provide the tools, utilities and even training necessary for everyday operations.
Time and caution should be taken in selecting the suppliers that will be the best fit for a specific organization is part responsible for supply chain management.
Supplier profile should contain certifications like:
Sedex (As a multi-user system where buyers can view and manage data for multiple suppliers, and suppliers can share data for multiple buyers. it is fully secured, and the access is based on the user profile). The tool used by Sedex is named SMETA (Sedex Members Ethical Trade Audit). It incorporates 3 elements:
A best practice guidance on conducting ethical trade audits,
An audit report format and
A corrective action plan format.
Fairtrade: Fairtrade supports and challenges businesses and governments and connects farmers and workers with the people who buy their products. Fairtrade certification enables people to trade Fairtrade-certified products in bulk.
ISO 9000: Is a set of international standards on quality management and quality assurance developed to help companies effectively document the quality system elements needed to maintain an efficient quality system.ISO 9000 can help a company satisfy its customers, meet regulatory requirements, and achieve continual improvement. It should be considered to be a first step or the base level of a quality system.
Anti bribery
Transparency and trust are the building blocks of any organisation’s credibility. Nothing undermines effective institutions and equitable business more than bribery, which is why there’s ISO 37001.It’s the International Standard that allows organisations of all types to prevent, detect and address bribery by adopting an anti-bribery policy,
SDGs are a universal call to action to end poverty, protect the planet and ensure that all people enjoy peace and prosperity.
Integration
Integration starts at your strategic planning phase and is critical throughout your communications and information sharing and data analysis and storage.
A single-view, accurate, and reliable source of information on your supply chain activities and details reduces human error, delays, shortages, and over/under-stocking, and allows you to plan for and mitigate supply issues or interruptions.
Assess your technology needs, and ensure your choice gives you the right tools to integrate your full supply chain solution while being flexible enough to change and grow with your business.
Core processes
It is a set of repetitive tasks you want to accomplish with a certain input and an expected output. It is therefore very important to describe clearly and precisely what are the key processes you want to develop to do your supply chain strategy.
To aid in decision making, technology tools (and the way they are implemented) need to align with the organisation that is making the decisions and with that organisation's business processes.
Security
Supply chain security is the part of supply chain management that focuses on the risk management of external suppliers, vendors, logistics and transportation. Its goal is to identify, analyse and mitigate the risks inherent in working with other organisations as part of a supply chain.
Any disruptions and risk to the integrity of the products or services being delivered, the privacy of the data being exchanged, and the completeness of associated transactions can have damaging operational, financial and brand consequences.
Supply Chain Security Concerns:
Data protection: Data is at the heart of business transactions and must be secured and controlled at rest and in motion to prevent breach and tampering. Secure data exchange also involves trusting the other source, be it a third party or an e-commerce website. Having assurances that the party you are interacting with is who they say they are is vital.
Fraud prevention: In a single order-to-cash cycle, data changes hands numerous times, sometimes in paper format and sometimes electronic. Every point at which data is exchanged between parties or shifted within systems presents an opportunity for it to be tampered with—maliciously or inadvertently.
Essentials tools- these can be done through Blockchain platforms or any security platform like cyber security and Web 3.0 which protect critical systems and sensitive information from digital attacks
Logistics security. The assurance that the material, part, shipment etc. being provided remains secure from damage, theft, or contamination by weather and external forces.
Execution
Supply chain execution refers to the process of driving the flow of goods within the supply chain – starting from procurement all the way through final-mile delivery.
The end of any project is its execution by making full use of the planning, the resources, the process and the technology to deliver products, therefore activities included in supply chain execution are manufacturing, distribution, warehousing, fulfilment, and transportation.
Supply chain technology offers advanced solutions to efficiently execute your supply chain processes. This may include everything from production planning and procurement management to order fulfilment and returns management for Exemple:
Sources
sustainable supply chain - Bing images
Pillars of Supply Chain Management – Keller Technology Corporation
The 7 pillars of an efficient supply chain | Saint-Gobain
Supply Chain Strategy- 4 Key Pillars To Strengthen [Infographic] (scmdojo.com)
Business-to-Business (B2B) Definition & Example (investopedia.com)
How to build a sustainable supply chain | British Assessment Bureau (british-assessment.co.uk)
steps in choosing sustainable raw materials - Bing images
Recommended
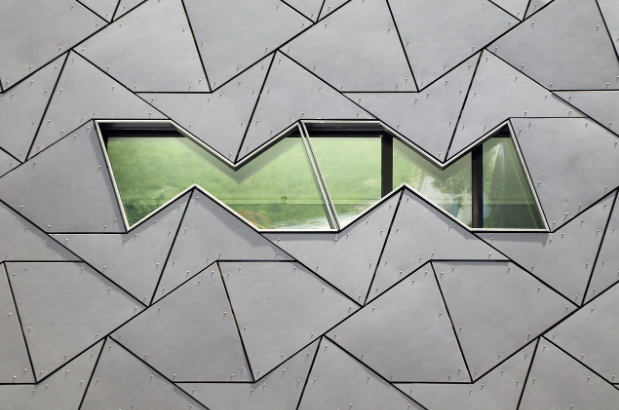

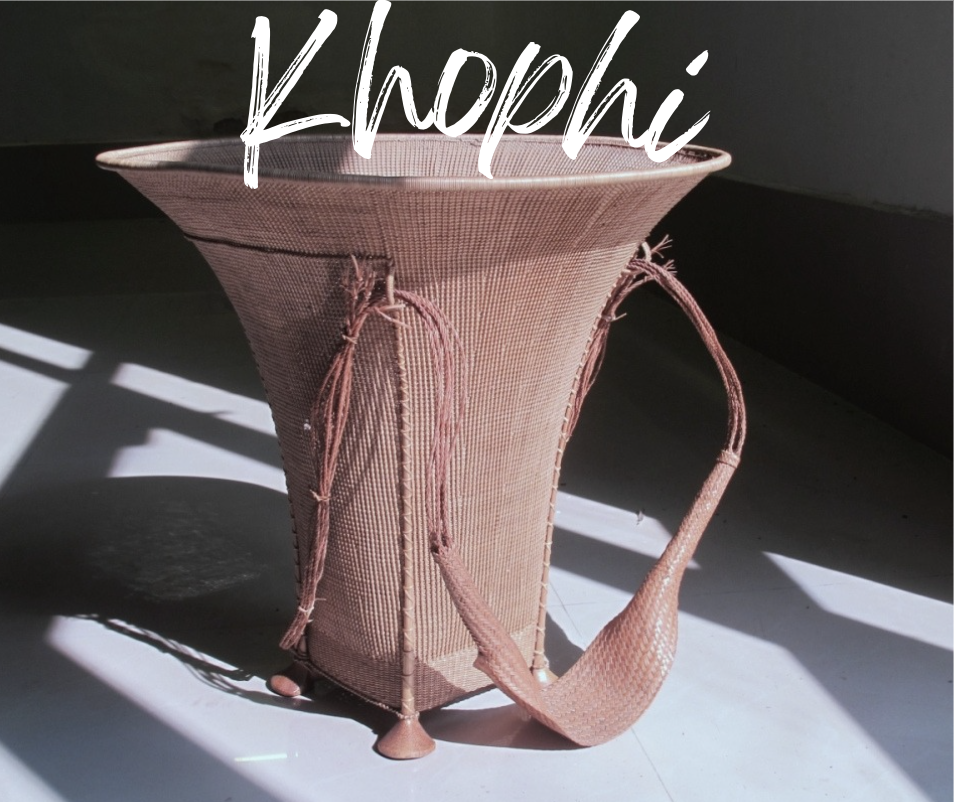