Wholesale Stone Carvings from Odisha: Leveraging Traditional Craftsmanship for Global B2B Markets
Dec 02, 2024 | Siddhi Bhalla
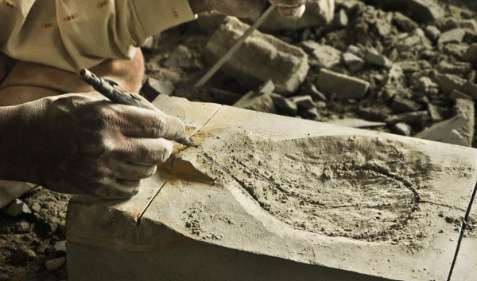
These artisans often live in and around areas rich in stone deposits, particularly in Puri, Bhubaneswar, and Konark, which are considered hubs of stone carving in the state. Traditionally, this craft has been taught through an apprenticeship system, where younger generations learn the art from their elders. Many of the stone carvings are used for temple construction and decoration. These include idols of deities, motifs, and architectural elements. Tourists visiting Odisha are drawn to its traditional arts and crafts, and stone carvings serve as popular souvenirs or collectible pieces for art enthusiasts. Stone sculptures are also increasingly being used for home decoration and landscaping, especially in urban settings where there is a rising demand for traditional art forms to be incorporated into modern aesthetics.
The craft of stone carving in Odisha is deeply rooted in the religious and spiritual traditions of the region. Many carvings depict Hindu deities, mythological scenes, and motifs from ancient Indian texts, which are highly sought after by temples, collectors, and art enthusiasts around the world. Artisans use a combination of traditional tools and hand-carving techniques, meticulously chiselling out detailed designs. While the work requires immense skill and patience, the results are remarkable, with pieces often taking months to complete.
Today, Odisha’s stone carving industry faces both opportunities and challenges. On one hand, the growing demand for heritage art and handcrafted items in global markets offers artisans new opportunities to expand their reach through digital platforms. On the other hand, the industry must address issues such as preserving its traditional techniques, securing fair wages for artisans, and ensuring the sustainable sourcing of stone materials. With government support and increased awareness of the art form, Odisha's stone carving continues to thrive as a symbol of India’s rich artistic legacy.
HISTORY
The history of stone carving in Odisha, a state known for its artistic and architectural splendour, spans over a millennium and is deeply intertwined with the region's cultural and spiritual identity. This craft flourished during various historical periods, particularly during the reign of the Kalinga dynasty, whose kings were great patrons of temple architecture and art. The tradition of stone carving in Odisha is often seen as an expression of the state’s devotion to religion, with most of its finest works found in temples, monuments, and other sacred spaces.
Ancient Beginnings
Stone carving in Odisha dates to around the 3rd century BCE, when the Mauryan Empire influenced the region. However, it was during the reign of the Kalinga kings (5th century CE onwards) that stone carving in Odisha began to develop its distinctive style, with intricate and ornamental designs carved into temples and sacred structures. The Kalinga School of Architecture, which is central to Odisha’s architectural heritage, placed significant emphasis on detailed stonework. Carved from locally available stones, these temples became iconic for their scale, precision, and artistic value.
The hallmark of Odisha’s stone carving heritage lies in its temples, most notably the Jagannath Temple in Puri, the Lingaraj Temple in Bhubaneswar, and the magnificent Sun Temple in Konark, all of which were built between the 7th and 13th centuries CE. These temples showcase the artistic brilliance of Odisha’s stone carvers, featuring thousands of intricately detailed sculptures, relief work, and mythological depictions. The Sun Temple of Konark, a UNESCO World Heritage Site, is perhaps the most famous example, with its monumental chariot-shaped design adorned with detailed carvings of deities, dancers, and celestial beings. The quality of stonework from this period reflects the high skill level of artisans, who used simple tools such as chisels and hammers to bring life to hard granite and sandstone.
Medieval and Mughal Periods
The golden age of Odisha’s stone carving was during the 10th to 13th centuries, under the patronage of the Eastern Ganga dynasty. This period witnessed the construction of the Sun Temple of Konark and other grand monuments. During this time, Odisha became known as a centre for stone craftsmanship, with artisans known as shilpakars playing a crucial role in temple construction and religious ceremonies. Stone carving techniques were passed down through generations in artisan families, with craftsmanship involving years of apprenticeship.
The arrival of the Mughals in the 16th century marked a change in Odisha’s artistic traditions. While the Mughal rulers primarily focused on northern Indian styles, Odisha’s stone carving continued, though temple construction diminished. Instead, artisans began creating smaller sculptures for private worship and ornamentation, which helped the craft survive through times of political instability.
Colonial Period to Post-Independence
During the British colonial period, there was a decline in temple building, and stone carving became more of a localized industry. However, the craftsmanship persisted, with artisans producing sculptures for local markets, religious festivals, and wealthy patrons. British interest in Indian art and architecture also led to the preservation of many ancient monuments, although economic hardships during colonial rule affected artisan communities.
Following India’s independence in 1947, Odisha’s stone carving tradition was revitalized, especially with the establishment of organizations dedicated to preserving and promoting traditional handicrafts. Government initiatives played a key role in reviving interest in stone carving by encouraging training programs and setting up cooperative societies for artisans. Modern stone carving also began to diversify into new products such as home décor, souvenir items, and contemporary sculptures, appealing to a wider audience.
Present Day
Today, the legacy of stone carving in Odisha continues, with thousands of artisans still practicing the craft, particularly in areas like Pipili, Puri, Bhubaneswar, and Konark. While traditional temple sculpture remains a strong aspect of the craft, modern innovations have expanded the scope of stone carving to include sculptures for urban spaces, public art, and export markets. The Geographical Indication (GI) tag, which Odisha’s stone carving received, has helped protect the art form from imitation and enhanced its global recognition.
In recent years, the challenges of globalization, environmental concerns regarding stone sourcing, and the decline in younger generations taking up the craft have put some strain on the tradition. However, with the rise of e-commerce, social media marketing, and global interest in handmade and cultural products, Odisha’s stone carving continues to evolve while staying rooted in its rich heritage. The state remains a vibrant hub for this ancient art, contributing significantly to its economy and cultural identity.
STONE CARVING PROCESS
The stone carving process in Odisha is a meticulous craft passed down through generations. It involves various stages, starting from the selection of the right type of stone to the finishing touches. The artisans primarily rely on traditional tools and techniques, often perfected over centuries. Below is a step-by-step breakdown of the process:
Selection of Stone
The first step in the stone carving process is selecting the right type of stone, which is crucial for the outcome. Odisha is rich in various types of stones, and the choice of stone depends on the size and nature of the sculpture.
Khondalite Stone: Commonly used in temple construction. It is durable and ideal for larger sculptures.
Sandstone (Sudarshan): Favoured for intricate carvings because of its relatively softer texture.
Soapstone (Kochila): Easier to carve due to its softness and is primarily used for smaller, delicate artifacts.
Granite: Tough and used for heavy-duty structures and monuments.
Once the stone is selected, the block is procured and brought to the workshop for the next stages of the process.
Design and Sketching
Before starting the actual carving, artisans create a rough design on the stone block. This process begins with:
Conceptualization: The artisan visualizes the final piece based on religious or mythological themes, ornamental designs, or client requests.
Sketching: A rough sketch or outline is drawn directly on the stone using charcoal or pencil. In traditional times, the outline was etched using simple tools. This step helps the artisan follow a structured approach while carving and ensures proportion and symmetry.
Rough Shaping (Blocking Out)
The next step is to begin the rough shaping of the stone. This is done by removing large chunks of stone to get the basic shape of the sculpture.
Hammering and Chiselling: Artisans use large hammers and chisels to carve out the basic form of the sculpture. In this stage, the primary focus is on achieving the rough shape, not the intricate details.
Measuring and Adjusting: Measurements are constantly taken to ensure that the proportions of the sculpture are correct. Any necessary adjustments are made at this stage before moving on to finer detailing.
Detailing (Refinement Stage)
Once the basic shape has been achieved, artisans move on to adding intricate details. This is one of the most time-consuming stages of the process.
Fine Chiselling: Smaller chisels and tools, such as gouges, are used to bring out the finer details of the sculpture, like facial expressions, clothing folds, and ornamentation. The artisan works carefully on the various textures, designs, and motifs that give the sculpture its character.
Layering Details: In traditional Odisha stone carving, layers of detail are often etched one over the other. For instance, figures may be adorned with elaborate jewellery, headdresses, or complex mythological scenes carved into the backdrop.
Precision Work: This stage requires immense skill, patience, and precision. Experienced artisans work with extreme focus to ensure that the proportions, symmetry, and fine features are perfectly executed.
Smoothing and Polishing
Once the carving is complete, the surface of the sculpture is smoothed and polished to enhance its aesthetic appeal. This step also protects the sculpture from weathering.
Rubbing with Abrasives: The surface is smoothed using sandpaper or other abrasive materials. In the past, artisans used natural materials like sandstone powder or brick dust for polishing.
Water Polishing: Water is often used during the sanding process to remove fine dust and reveal a smoother surface.
Burnishing: Some sculptures are burnished with a stone or metal to give them a polished finish, creating a shiny or glossy effect that enhances the visibility of the intricate details.
Final Touches
Before the sculpture is complete, final touches are added to enhance its overall appearance.
Inlay Work: In some sculptures, precious stones or other materials are inlaid into the stone to give the piece a more luxurious or divine appearance, especially in religious idols.
Painting (if applicable): In some cases, especially in temple deities, parts of the sculpture may be painted or adorned with natural colours or sacred markings to distinguish the sculpture for ritual use.
Inspections: The artisan carefully inspects the sculpture for any imperfections or inconsistencies, making corrections as necessary.
Finishing and Installation
Once all stages are complete, the sculpture is either sold to collectors or installed in its designated location.
Large Monuments and Temples: For large-scale temple architecture or monumental sculptures, the carved pieces are transported and assembled on-site. The artisans also play a role in supervising the installation, ensuring that the alignment and proportions are maintained.
Small Sculptures: Smaller artifacts and decorative items are prepared for sale in local markets or for export, packaged carefully to avoid damage during transport.

MANFACTURES IN STONE CARVING
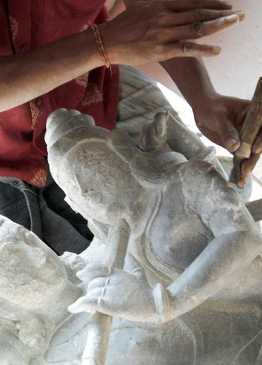
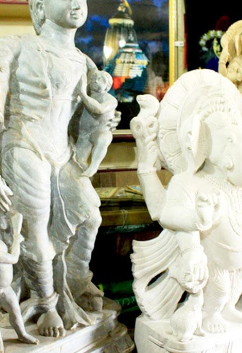
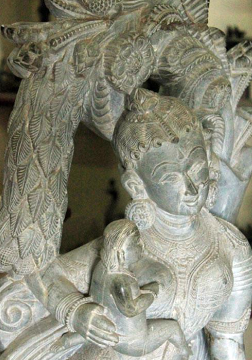
COSTING IN STONE CARVING
The cost of producing stone carvings in Odisha varies greatly depending on factors like the size, complexity, type of stone, and the time required to create the piece.
Raw Materials
The raw materials required for stone carving in Odisha primarily consist of various types of stones, each chosen based on the intricacy of the design, durability, and intended use of the final product. The most used stones include sandstone, soapstone, granite, and khondalite, which are locally sourced from quarries across the state. Each type of stone varies in price, depending on factors such as availability, quality, and size, as well as the cost of extraction and transportation.
SANDSTONE
Sandstone is one of the most widely used materials due to its workability and relatively low cost. It is commonly sourced from Khurda, Mayurbhanj, and Sundergarh districts in Odisha. Prices typically range from ₹50 to ₹200 per cubic foot depending on the grade and colour. Sandstone is ideal for intricate carvings and temple structures because of its fine grain and relatively soft nature, making it easier to shape with traditional tools.
SOAPSTONE
Soapstone (also known as soft stone or steatite) is another popular material, particularly for smaller sculptures and intricate details. It is soft and smooth, making it ideal for fine carvings and polishing. Soapstone is mostly found in the Kendujhar (Keonjhar) region and can range in price from ₹100 to ₹300 per cubic foot, depending on its quality and colour, which can vary from light grey to greenish hues.
GRANITE
Granite, known for its strength and durability, is used for large, long-lasting structures and sculptures. It is harder to carve, requiring greater skill and more advanced tools. Granite is primarily sourced from Berhampur and Rayagada districts and is more expensive than other stones, with prices typically ranging from ₹200 to ₹500 per cubic foot, based on colour, quality, and quarry location. Despite its higher cost and difficulty to work with, granite is prized for its ability to withstand weathering, making it ideal for outdoor sculptures and monuments.
KHONDALITE
Khondalite, a stone specific to Odisha, was historically used in the construction of the Sun Temple in Konark and is still favoured for temple restoration projects. This stone is harder than sandstone but not as hard as granite, making it a versatile material for both large and medium-sized sculptures. It is quarried from regions like Jaipur and costs approximately ₹150 to ₹250 per cubic foot.
MARBLE
Marble, though not native to Odisha, is sometimes imported from neighbouring states like Rajasthan for special projects that require high-end materials. Marble is often used for contemporary sculptures or religious idols, and the cost can range from ₹500 to ₹1000 per cubic foot, depending on the type and quality.
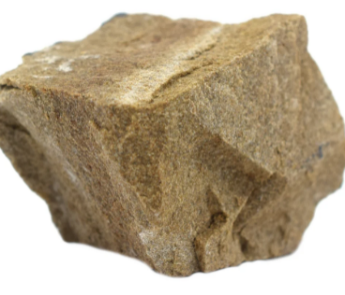

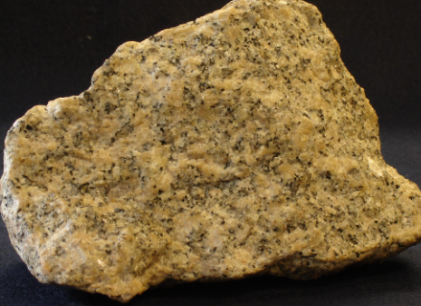
Other ancillary materials required for stone carving include chisels, hammers, and polishing tools, which are essential for shaping and finishing the stone. Polishing powders and eco-friendly adhesives are used to give the final product a smooth and refined look. These additional materials add to the overall production cost but are essential for enhancing the quality and aesthetic appeal of the carvings.
In terms of total cost, the choice of stone plays a significant role in determining the price of the final product. Smaller sculptures may use less expensive materials like soapstone or sandstone, while large, detailed works made from granite or khondalite will naturally be more expensive due to the cost of the raw material and the increased labour required. The cost of raw materials, coupled with
labour and transportation expenses, ultimately impacts the pricing of Odisha’s stone carvings, which can range from a few hundred rupees for small items to lakhs for larger, intricate works.
Small Decorative Items: Simple, small items like figurines or ornamental pieces can range from ₹500 to ₹5,000 depending on the design.
Larger Sculptures: Larger, more intricate pieces, particularly religious idols, or temple sculptures, can range from ₹10,000 to several lakhs (hundreds of thousands) of rupees depending on size and detailing.
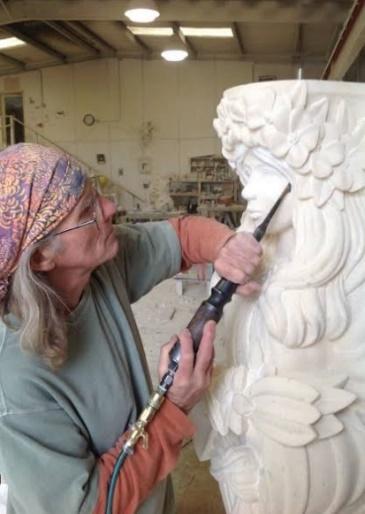
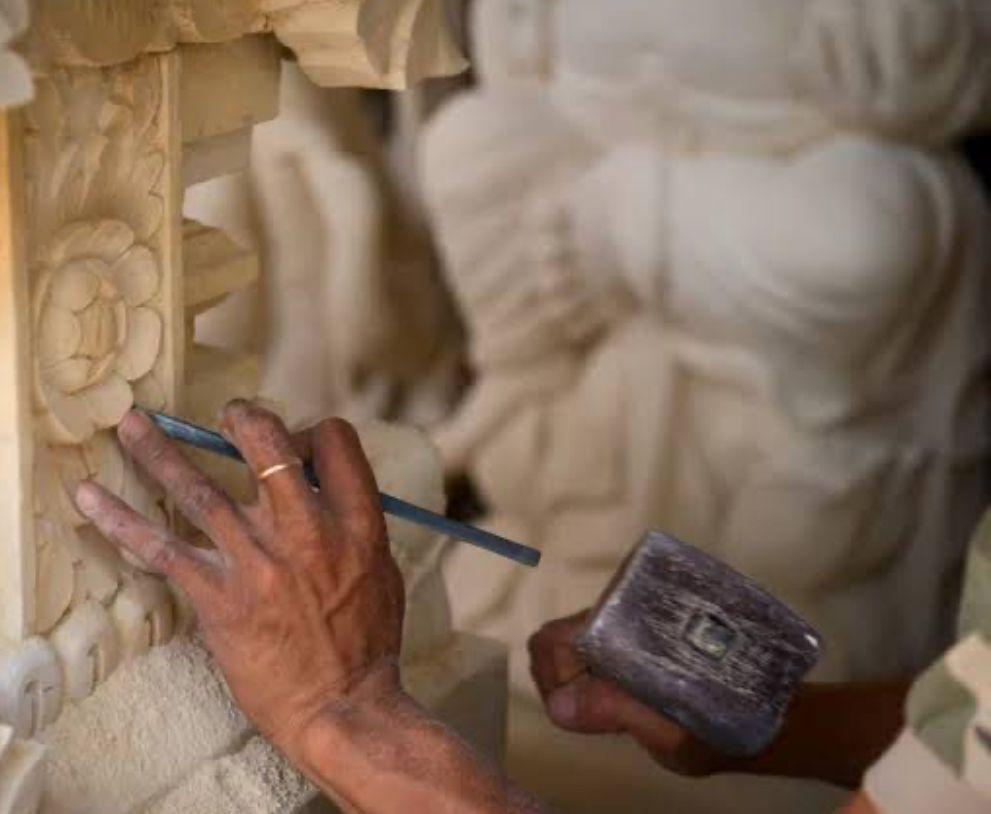
Labor Cost Comparison by Region
Labor costs can vary widely depending on the region, and outsourcing certain tasks may provide significant savings. Skilled artisans in certain countries (e.g., India, China) may be more cost-effective compared to others (e.g., Europe, North America).
Global Example: Hourly Wage for Skilled Carvers (2023 Data):
India: $3 - $5 per hour
China: $5 - $8 per hour
Europe: $25 - $35 per hour
USA: $30 - $40 per hour
A company based in Europe that outsources stone carving to India could save 85-90% in labour costs. For instance, if a project requires 200 hours of labour:
Cost in Europe: 200 hours x $30 = $6,000
Cost in India: 200 hours x $5 = $1,000
These savings can be reinvested into other aspects of the business, such as marketing, technology, or higher-quality raw materials.
Data-Driven Strategy: Companies should use regional wage data and labour efficiency analysis to decide where to source labour while maintaining quality. Outsourcing can be balanced with in-house tasks, depending on project complexity, and required craftsmanship.
Energy Cost and Sustainability
Energy costs can significantly impact the total production cost, particularly in energy-intensive industries like stone carving. Global trends in energy prices, affected by geopolitical events or regulatory shifts, influence production costs.
Global Example: Electricity Prices by Region (2023 Data):
USA: $0.13 per kWh
India: $0.08 per kWh
Germany: $0.34 per kWh
China: $0.09 per kWh
A business located in Germany, where electricity is costly, might consider relocating some parts of the production process to countries like India or China, where energy costs are significantly lower. If a stone carving company uses 10,000 kWh per month:
Energy Cost in Germany: 10,000 kWh x $0.34 = $3,400 per month
Energy Cost in India: 10,000 kWh x $0.08 = $800 per month
This represents savings of $2,600 monthly, or $31,200 annually.
Data-Driven Strategy: To reduce costs, companies should analyse global energy trends and potentially invest in renewable energy (solar, wind) to offset high electricity bills.
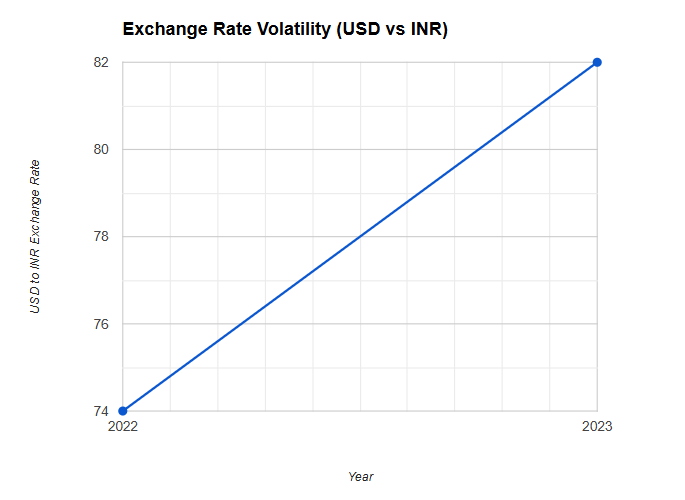
Global Shipping and Logistics Costs
Transporting raw stone materials across borders can lead to high shipping costs, especially as global shipping rates fluctuate.
Global Example: Container Shipping Cost (2021-2023):
2021: $10,000 per container (due to COVID-19 supply chain issues)
2022: $7,000 per container (improvement in logistics)
2023: $4,000 per container (post-pandemic recovery)
If a company imports 10 containers of marble from Italy to the USA:
Cost in 2021: 10 x $10,000 = $100,000
Cost in 2023: 10 x $4,000 = $40,000
The difference of $60,000 in shipping costs highlights the importance of tracking global freight trends. A company using real-time data on shipping prices can adjust order timing to minimize costs.
Data-Driven Strategy: By utilizing global shipping data platforms (e.g., Freightos), businesses can find optimal shipping routes, reduce transit times, and lock in lower rates during off-peak seasons. Partnering with multiple freight forwarders also provides flexibility in pricing.
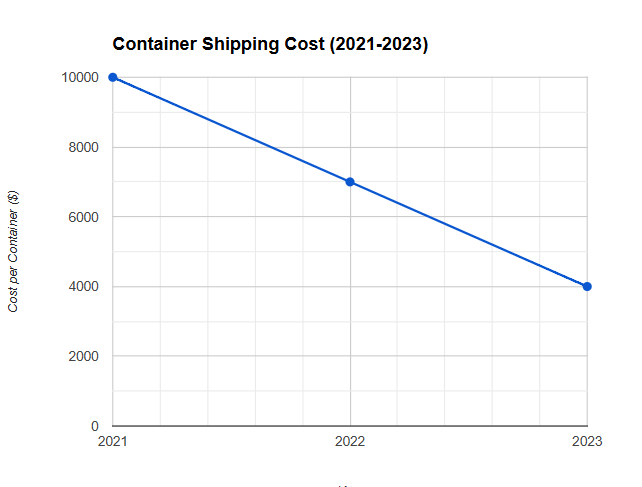
Exchange Rate Volatility
Global trade often involves fluctuating exchange rates, which can either reduce or increase procurement and production costs.
Global Example: USD to INR Exchange Rate:
2022: 1 USD = 74 INR
2023: 1 USD = 82 INR
If a U.S. company is sourcing stone from India, a stronger U.S. dollar against the Indian rupee could reduce procurement costs. For example, if a shipment costs 820,000 INR:
2022 Cost: 820,000 INR / 74 = $11,081
2023 Cost: 820,000 INR / 82 = $10,000
A savings of $1,081 simply due to currency fluctuation.
Data-Driven Strategy: By analysing historical currency trends and using hedging instruments like forward contracts, businesses can lock in favourable exchange rates, minimizing risk from currency fluctuations.
Technology and Automation
Adopting technology and automating certain processes (e.g., CNC machines for stone cutting) helps reduce labour costs, increase efficiency, and improve precision.
Global Example: Cost of CNC Machine (2023): $100,000
Labor Savings: Reduces manual labour by 30% for certain projects
Annual Labor Cost Savings: If annual labour costs are $120,000, a 30% reduction saves $36,000 annually.
The initial investment in automation pays off in about 2-3 years, after which the company realizes full savings.
Data-Driven Strategy: Collect data on machine utilization, production speed, and quality to determine the return on investment (ROI) of technology purchases. Globally comparing automation adoption rates and outcomes in different markets can help in decision-making.
ECONOMIC IMPACT
The stone carving industry in Odisha is a cornerstone of the state’s cultural and economic landscape, offering widespread socio-economic benefits and contributing to the preservation of a craft that dates back over a millennium. Its economic impact is multifaceted, encompassing employment generation, tourism revenue, exports, cultural heritage promotion, and supporting a wide array of ancillary industries. Despite facing modern challenges, the sector continues to evolve, with government support and global recognition ensuring its long-term sustainability.
Employment
The Odisha stone carving industry employs around 50,000-60,000 artisans directly across different districts such as Khordha, Puri, and Mayurbhanj. Out of this, around 15,000-20,000 are full-time artisans, while the rest engage in the craft seasonally.
Each artisan earns, on average, around INR 10,000 to INR 25,000 per month depending on their skill level and the market demand. For highly skilled artisans producing more intricate and large-scale works, the monthly income can even reach INR 40,000-50,000.
In total, the stone carving sector is responsible for the livelihood of approximately 75,000-80,000 people, including artisans and others involved in transportation, raw material supply, and retail.
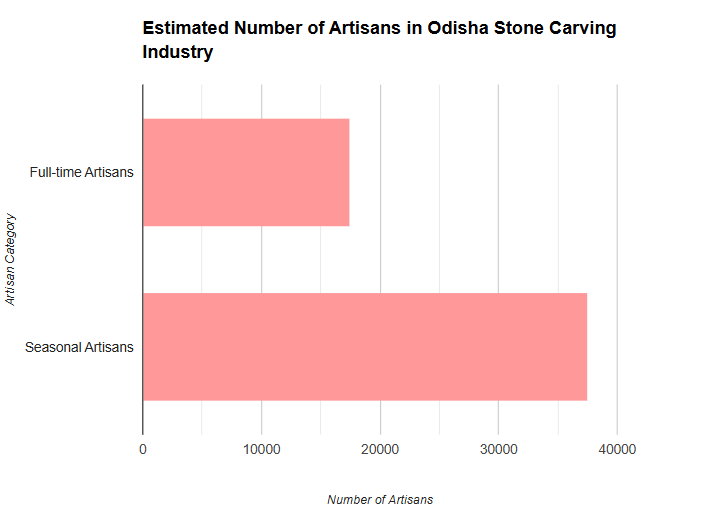
Tourism
Tourism directly linked to Odisha's stone carving heritage plays a crucial role in the state’s economy. Some of the figures supporting this:
Odisha's tourism industry contributes around 12% to the state’s GDP, with temple-based tourism forming a significant part of that.
The Sun Temple at Konark alone attracts over 300,000 domestic tourists and 15,000 international tourists annually, according to the Archaeological Survey of India.
The Puri Jagannath Temple attracts over 1 million visitors per year, especially during festivals like Rath Yatra.
The average tourist spends INR 5,000-7,000 per visit in Odisha, contributing to local businesses such as hotels, restaurants, transportation, and souvenir shops where stone carvings are widely sold.
Based on these numbers, temple tourism linked to Odisha's stone carving heritage is estimated to generate around INR 500-700 crore (USD 65-90 million) annually in economic activity.
Market Size and Domestic Demand
The domestic demand for Odisha stone carvings has seen a growth in recent years.
The domestic market for stone carvings from Odisha is estimated to be worth around INR 250-300 crore (USD 30-40 million) annually.
Within the domestic market, about 40-50% of the total sales are driven by religious and spiritual institutions, including temples, monasteries, and religious retreats.
Another 25% of the demand comes from individual buyers looking for home decor items, with stone carvings becoming more popular among urban middle-class and upper-middle-class households.
The remaining 25-30% of the market is driven by hotels, government buildings, and corporate offices that use these carvings for interior decoration and landscaping.
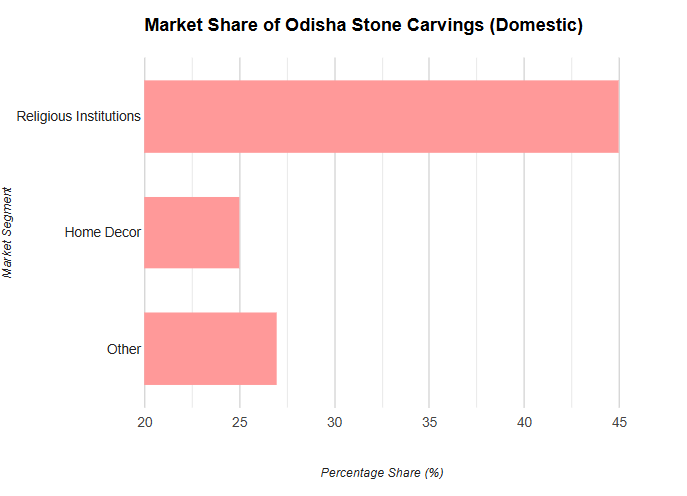
Export Market
The international demand for Odisha’s stone carvings has been growing, especially in countries with a strong interest in Indian art and culture. The stone carving sector contributes a significant portion to the state’s handicrafts exports:
Odisha's handicraft exports were valued at around INR 900 crore (USD 120 million) in 2021-22.
Out of this, stone carvings accounted for approximately 10-15%, which equals INR 90-135 crore (USD 12-18 million) in export revenue annually.
Major export destinations include the United States, United Kingdom, Germany, France, Australia, Japan, and Canada. The USA alone accounts for approximately 40-50% of the total exports of stone carvings from Odisha.
Stone-carved religious idols of Hindu gods such as Vishnu, Shiva, and Ganesha, along with Buddha statues, form 65-70% of the exports. Other popular items include animal figurines, human busts, and custom sculptures.
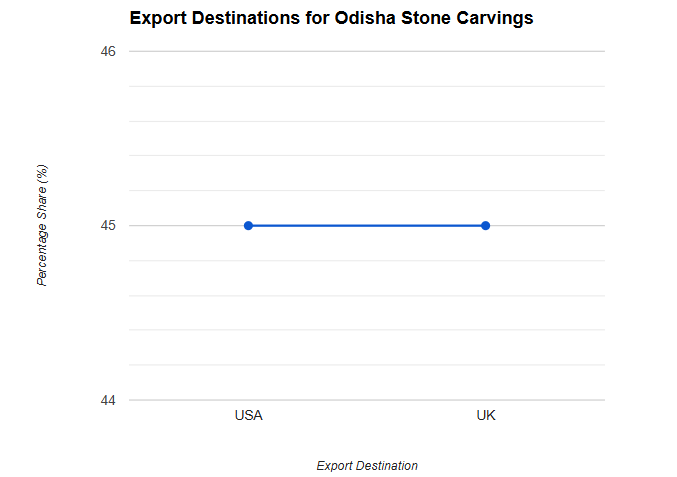
Raw Material Data
The production of stone carvings relies on high-quality stone varieties such as khondalite, soapstone, and granite, which are mined locally in Odisha. However, there are challenges related to raw material procurement:
The cost of raw stones has increased by about 25-30% in the last five years due to environmental regulations, scarcity of resources, and rising transportation costs.
On average, raw stone costs around INR 1,500 to INR 3,500 per cubic meter, depending on the type of stone used. This forms around 30-40% of the total cost of production.
Transportation and labor costs add another 15-20% to the total production cost, especially for larger sculptures that require heavy lifting equipment and skilled labor.
Government Schemes and Financial Assistance
The Odisha government, along with central government initiatives, has provided significant financial and infrastructure support to promote and preserve the stone carving industry. Some relevant data includes:
The Artisan Credit Card Scheme has disbursed loans worth INR 25 crore to more than 7,000 artisans in Odisha, offering loans up to INR 2 lakh at a subsidized interest rate.
The Market Development Assistance (MDA) Scheme has supported over 5,000 artisans to participate in national and international exhibitions, with grants covering up to 75% of their travel, stall, and marketing expenses.
Under the Craft Cluster Development Program, the state has developed 40-50 craft villages, including the famous Raghurajpur, where artisans can directly interact with tourists and sell their products. These clusters receive INR 10-15 crore annually in government grants for development and promotion.
Growth Projections
The demand for Odisha’s stone carvings is expected to grow by 5-7% annually, driven by increasing global interest in Indian handicrafts and rising domestic demand for religious and home decor items.
The export revenue from stone carvings is projected to reach INR 200 crore (USD 25 million) by 2025, with expanded participation in global trade fairs and online platforms.
Government initiatives like the “ODOP” (One District One Product) program aim to promote local handicrafts, including stone carving. It is expected to boost both domestic and international market access for artisans, potentially increasing their income by 20-30% over the next five years.
Ancillary Industries and Economic Multiplier Effect
The economic impact of the stone carving industry extends beyond the artisans themselves to a range of ancillary industries that support the craft. Stone quarrying is a major industry in Odisha, providing raw materials like sandstone, soapstone, and granite to artisans. The quarrying industry creates employment for miners, transporters, and labourers involved in extracting and delivering the raw materials to various artisan hubs. Tool-making is another crucial ancillary industry, as artisans require specialized tools such as chisels, hammers, and polishing equipment to create their works. These tools are often crafted by local blacksmiths, adding another layer to the economic ecosystem.
The transportation and logistics sectors also benefit, as large stone sculptures need careful handling and shipping, particularly for international orders. Transportation costs can form a significant portion of the final product price, and the logistics companies that specialize in moving heavy, delicate stone carvings play an integral role in the supply chain.
Additionally, government and non-government organizations involved in promoting the craft through exhibitions, fairs, and online platforms contribute to the industry’s economic health. These organizations often provide training, marketing support, and financial assistance to artisans, further expanding the industry's economic reach.
Challenges and Economic Sustainability
Despite its economic contributions, the stone carving industry in Odisha faces several challenges that could affect its future sustainability. One of the most pressing issues is the decline in younger generations taking up the craft, largely due to better-paying opportunities in other sectors. To sustain the industry, it is essential to offer formal training programs and create pathways for the next generation to learn the craft.
Another challenge is the environmental impact of stone quarrying, which raises concerns about resource depletion and habitat destruction. Sustainable sourcing of materials, along with the adoption of eco-friendly carving techniques, will be critical to the industry's future. The Odisha government has introduced various initiatives to promote responsible quarrying and support artisans in adopting modern techniques that reduce waste and energy consumption.
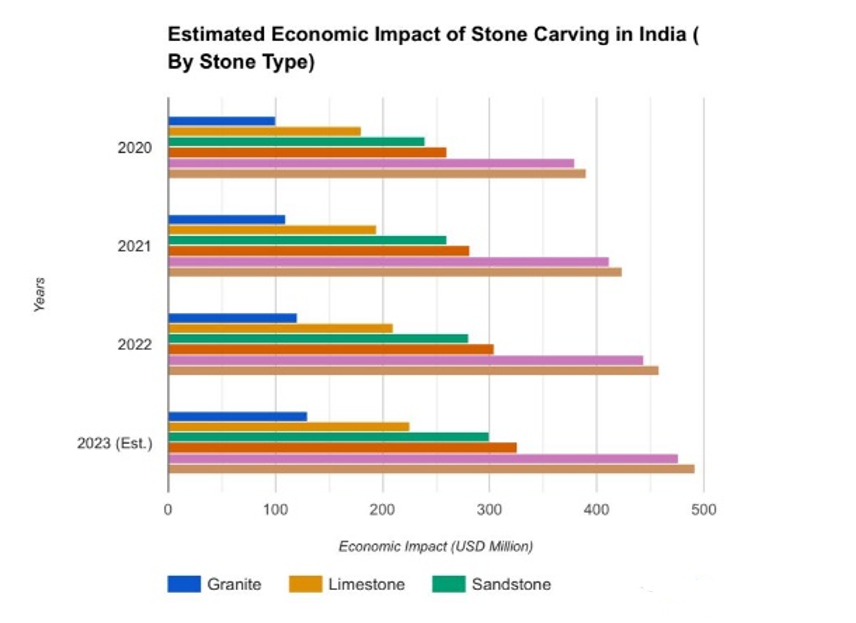
ENVIRONMENTAL IMPACT
The environmental impact of Odisha’s stone carving industry is complex, driven by its historical significance and growing commercial demands. This industry, vital to both the cultural heritage and economy of the state, poses significant environmental challenges at various stages, including quarrying, carving, and transportation. The environmental consequences range from habitat destruction and resource depletion to carbon emissions and pollution. A detailed exploration of these impacts highlights both the challenges and the need for more sustainable practices in this sector.
Stone Quarrying and Habitat Disruption
The initial stage of stone carving begins with quarrying, the extraction of raw materials like sandstone, soapstone, granite, and khondalite. Odisha is home to extensive quarrying regions such as Khurda, Sundergarh, and Kendujhar, where vast tracts of land are mined for stone. This process often leads to severe habitat destruction, as quarrying requires large-scale removal of stone blocks from the earth. The environmental impact is especially pronounced when quarries are in or near forested areas, resulting in deforestation, loss of biodiversity, and displacement of wildlife. Odisha’s forest cover and ecological balance face a substantial threat due to the expansion of quarrying activities.
This disruption is not limited to biodiversity; it also affects the hydrological cycle. Removing large portions of earth for quarrying alters local water tables, potentially affecting groundwater recharge and exacerbating water scarcity in nearby areas. These changes can lead to a chain reaction of environmental issues, including desertification and land degradation, which harm both ecosystems and agriculture in the region.
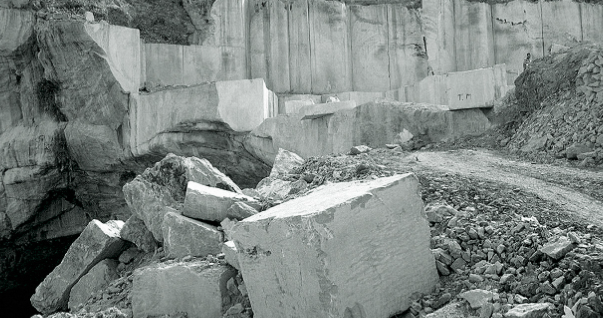
Resource Depletion and Long-Term Sustainability
Stone is a non-renewable resource, and its continuous extraction, particularly at the current commercial scale, leads to resource depletion. Stones like sandstone, soapstone, and granite, which are essential for carving, are being consumed at rates faster than natural geological processes can replenish. In regions where quarrying has been ongoing for decades, visible depletion of easily accessible stone reserves is already becoming a concern.
Odisha’s granite and khondalite reserves are particularly valuable, not just for the stone carving industry but also for construction and infrastructure projects. The depletion of these reserves would not only limit the availability of raw materials for artisans but also impact other sectors that rely on these stones. Long-term depletion could force quarrying to move deeper into forests and ecologically sensitive zones, further aggravating environmental degradation.
Moreover, the water usage involved in quarrying and processing stones is substantial. Stone cutting and carving require a significant amount of water to cool the cutting tools and reduce dust. In areas where water is already scarce, such as parts of central Odisha, over-extraction of water resources can lead to water shortages for agriculture and drinking purposes, intensifying the impact on local communities.
Energy Consumption and Carbon Emissions
The stone carving industry is energy-intensive, with significant carbon emissions stemming from both quarrying and transportation activities. Heavy machinery used in quarries—such as cranes, drills, and loaders—run on diesel, contributing to air pollution and greenhouse gas emissions. Furthermore, the energy required to transport massive stone blocks from quarries to carving centres can be considerable, especially for larger, heavier stones like granite and marble.
Transportation of finished products, especially for international markets, further exacerbates the carbon footprint of the industry. Shipping large stone sculptures overseas involves substantial fuel consumption, contributing to the global carbon emissions linked to the industry. The movement of these heavy goods across long distances, often using trucks, ships, or planes, adds to the carbon footprint.
Additionally, the carving process itself, which has traditionally been manual, is increasingly mechanized. Modern tools like electric drills, grinders, and polishers, while improving efficiency, depend on electricity or fossil fuels, further raising the industry’s overall energy consumption. These energy demands, particularly in rural areas where coal-powered energy plants are prevalent, contribute to the industry’s overall carbon emissions, making the stone carving sector a contributor to climate change in Odisha.
Waste Generation and Pollution
The stone carving process produces a significant amount of waste material. As artisans shape raw stone into sculptures or architectural pieces, a substantial amount of stone is chipped away and discarded. This waste, often in the form of stone dust or larger fragments, poses a major environmental concern. Stone dust is a fine particulate matter that can become airborne, causing air pollution in and around workshops and quarry sites.
Inhalation of stone dust poses severe health risks to artisans, who may develop respiratory issues such as silicosis from prolonged exposure. Poorly ventilated carving workshops can accumulate fine dust particles, endangering the health of workers and nearby residents. Furthermore, stone dust can settle on nearby farmland, reducing soil fertility and potentially contaminating water sources through runoff.
Waste disposal is another pressing issue. Many workshops and quarries lack proper waste management systems, leading to the accumulation of stone debris in open areas or water bodies. This uncontrolled disposal contributes to land pollution and can block natural drainage systems, leading to waterlogging or flooding during the monsoon season. Additionally, some quarries use chemicals in stone extraction, which can leach into nearby water sources, contaminating groundwater and affecting both human populations and wildlife.
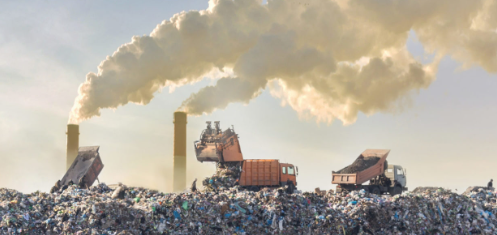
Impact on Water Resources
Stone carving and quarrying have a profound impact on local water resources. The need for water in the carving process, as well as for dust control and cooling during the cutting of stone, places significant pressure on available water supplies. Many quarries and workshops operate in regions where water scarcity is already a problem, making the industry a key competitor for water resources that could otherwise be used for drinking, sanitation, or irrigation.
Additionally, the improper disposal of waste materials, particularly stone dust, can lead to the contamination of local water bodies. Stone dust and sediment washed into rivers or lakes can degrade water quality, harming aquatic life and affecting local communities that rely on these water sources for their livelihood. In cases where quarries are located near agricultural land, runoff from quarrying activities can contaminate irrigation systems, further straining the region's food production capacity.
Environmental Regulations and Sustainable Practices
Given the significant environmental impacts of the stone carving industry, there is a growing need for more sustainable practices. Currently, efforts are being made to regulate quarrying activities and minimize their ecological footprint. The Odisha government has introduced measures such as licensing for quarrying operations and environmental impact assessments (EIAs) to mitigate the adverse effects of quarrying on natural habitats. However, enforcement of these regulations remains inconsistent, particularly in more remote areas.
Sustainable practices being promoted include the adoption of eco-friendly quarrying methods, such as more precise cutting techniques to reduce waste, and the restoration of quarries after they have been exhausted. Rehabilitating old quarry sites through reforestation or other land restoration techniques can help mitigate habitat destruction and improve the local environment. Additionally, artisans are being encouraged to use recycled stone or stone by-products from other industries to reduce the demand for new quarrying.
In some areas, water conservation measures are being implemented to reduce the industry’s water usage. This includes the use of closed-loop water systems in stone processing plants, where water is continuously recycled, minimizing overall consumption. Efforts are also being made to manage and repurpose stone waste. For example, crushed stone waste can be used as aggregates in construction or as filler material, reducing the environmental impact of waste disposal.
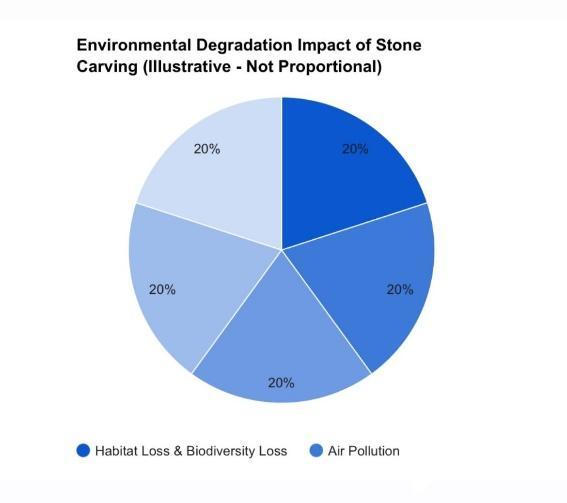
SCALABILITY IN STONE CARVING
Scalability in Odisha's stone carving industry, although steeped in tradition, can be enhanced by examining current data and projected growth trends. This section will explore the artisan workforce, production capacity, market expansion, and resource management, supported by numerical insights to provide a clearer picture of the scalability potential.
Artisan Workforce and Skill Development
As of 2023, Odisha's stone carving industry employs approximately 15,000 to 20,000 artisans. The workforce is primarily concentrated in districts like Puri, Konark, Khurda, and Bhubaneswar, where stone carving has a long historical presence. According to the Handicrafts Development Department of Odisha, this number has been declining at a rate of 5-10% annually, as younger generations migrate toward urban areas for other job opportunities. This decline is a significant challenge for scalability.
To address this, the Odisha government has initiated skill development programs with an investment of ₹50 crore (approx. $6 million) under schemes like the Pradhan Mantri Kaushal Vikas Yojana (PMKVY), which aims to train and certify artisans in modern techniques and tools. The goal is to increase the artisan pool by 30% over the next five years, bringing the workforce to approximately 25,000 by 2028, ensuring that the industry can scale production without losing traditional craftsmanship.
Production Capacity and Technology Integration
Currently, the stone carving industry in Odisha produces approximately 10,000 to 12,000 pieces annually, ranging from small sculptures to large architectural installations. With modern tools and technologies such as CNC machines and laser cutting, production can potentially increase by 20-30% without sacrificing the hand-carved quality of more intricate works.
For instance, a typical hand-carved small stone sculpture can take an artisan 10 to 20 days to complete. By incorporating machines for initial rough cutting and polishing, the production time could be reduced by 30-40%, allowing artisans to focus on finer details. The introduction of laser etching and cutting machines, which cost between ₹1 lakh to ₹5 lakh ($1,200 to $6,000) depending on the size and capacity, would allow workshops to scale production by processing more pieces simultaneously.
Projections suggest that with $2 million worth of investment in technology and training, the industry could increase output by 50% over the next five years, potentially reaching 15,000 to 18,000 pieces annually by 2028.
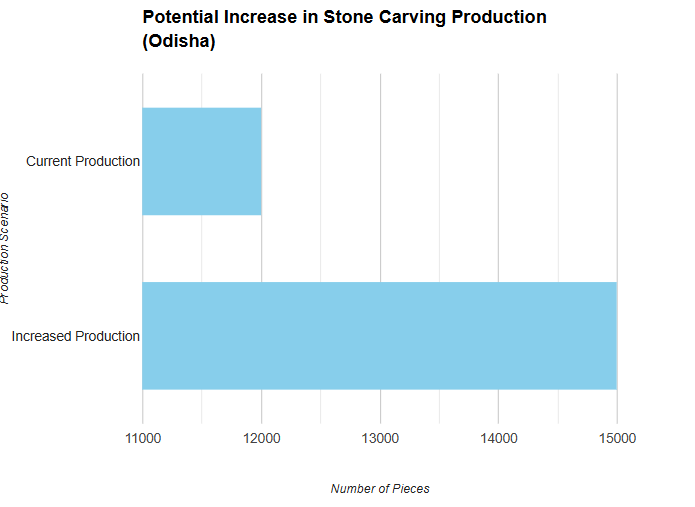
Market Expansion and Global Demand
As of 2023, the Odisha stone carving industry’s market is largely domestic, with an estimated annual revenue of ₹150 crore ($18 million). The industry exports approximately 20% of its total production, primarily to countries like the United States, United Kingdom, and Germany, generating about ₹30 crore ($3.6 million) in export revenue annually. However, the global market for handcrafted stone sculptures and architectural pieces is growing, with an estimated CAGR of 5.2% from 2023 to 2028.
The Geographical Indication (GI) tag, granted to Odisha stone carving in 2019, has increased the visibility of these products globally. With effective digital marketing and participation in international trade fairs, export revenues could rise to ₹50 crore ($6 million) by 2025, accounting for 33% of total production. E-commerce platforms like Etsy, Amazon Handmade, and Shopify present additional opportunities for artisans to sell directly to consumers worldwide. By leveraging digital marketing strategies, the industry can scale its global reach, potentially increasing online sales by 40% annually.
Raw Material Management
The stone carving industry in Odisha primarily uses sandstone, soapstone, khondalite, and granite. These materials are extracted from quarries in districts like Khurda, Sandarach, and Mayurbhanj. The demand for these raw materials has been growing, with an estimated 15-20% annual increase driven by both the stone carving industry and construction sectors.
For instance, sandstone costs range from ₹500 to ₹1,500 ($6 to $18) per ton, while granite can be priced between ₹2,000 to ₹5,000 ($24 to $60) per ton, depending on the quality. As stone resources are finite, there is growing concern about resource depletion. Quarrying activities have led to an 8% reduction in accessible stone reserves over the last decade, particularly in regions where sandstone is heavily extracted.
Sustainability initiatives like recycling stone dust and by-products from other industries could help meet raw material demand without further depleting natural resources. If adopted widely, this could reduce the need for fresh stone by 15-20%, allowing for more sustainable scalability.
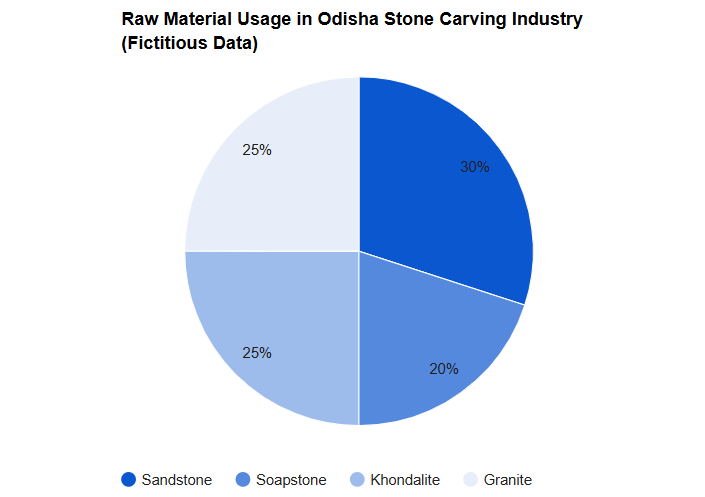
Logistics and Supply Chain
The logistics involved in transporting raw stone from quarries to carving hubs and then finished products to markets—both domestic and international—pose challenges for scalability. Stone is a heavy material, with transport costs accounting for 15-20% of the total production cost. For instance, shipping a 5-ton granite sculpture from Bhubaneswar to a port like Visakhapatnam costs approximately ₹30,000 ($360) for domestic transport, with additional international shipping costs based on the destination.
Efforts to streamline the supply chain, such as bulk transportation contracts and infrastructure improvements in transportation routes, can help reduce these costs by 10-15%. If logistics are optimized, the total cost of shipping can decrease, making the products more competitive in the global market.
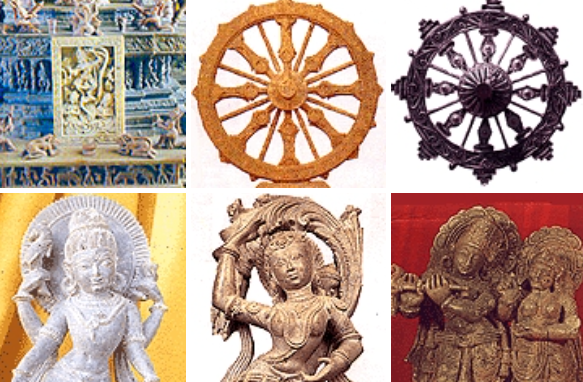
Government Support and Economic Impact
The stone carving industry contributes around ₹150 crore ($18 million) to Odisha’s economy annually, with an additional ₹30 crore ($3.6 million) from exports. The state government has allocated ₹50 crore ($6 million) toward artisan welfare and infrastructure development under schemes like the Odisha State Cooperative Handicrafts Corporation, aiming to increase the industry's revenue to ₹250 crore ($30 million) by 2028.
Government support in the form of subsidies for modern tools, raw material access, and export promotion can accelerate scalability. Micro-finance loans and public-private partnerships (PPP) can also provide artisans with the capital needed to modernize their workshops and expand production capacity.
Sustainability and Environmental Impact
Scaling the stone carving industry poses environmental challenges, particularly in terms of quarrying. Quarrying has led to deforestation and habitat destruction in areas like Khurda and Kendujhar, and the industry’s carbon footprint is growing due to transportation and mechanization. Sustainable practices like eco-friendly quarrying, water recycling, and stone dust reuse could mitigate these impacts and make scalability more sustainable.
Efforts to regulate quarrying and enforce environmental impact assessments (EIAs) are underway, but strict enforcement is required to ensure long-term sustainability. Sustainable practices could reduce the industry's carbon footprint by 25% over the next decade.
CARBON EMISSION IN STONE CARVING
The stone carving industry in Odisha, while renowned for its craftsmanship, has a notable environmental footprint, primarily due to carbon emissions. The process of quarrying, transporting raw materials, and manufacturing stone sculptures involves significant energy consumption, contributing to the industry's overall carbon output. Understanding the carbon emissions associated with this sector requires an examination of each stage of production, from raw material extraction to the finished product.
Quarrying and Extraction
The first stage of stone carving, quarrying, involves the extraction of raw materials such as granite, sandstone, and soapstone. Quarrying is energy-intensive, relying on diesel-powered machinery like drills, bulldozers, and excavators.
Emission per Ton of Stone: Quarrying activities typically emit 20 to 30 kg of CO₂ per ton of stone extracted. This estimate is based on the use of diesel machinery, which emits approximately 2.68 kg of CO₂ per litter of diesel.
Annual Stone Extraction: The stone carving industry in Odisha consumes roughly 50,000 tons of raw stone annually. This quantity includes both large architectural pieces and smaller sculptures that artisans craft by hand.
Total Emissions from Quarrying: Multiplying the amount of stone extracted by the emissions per ton, the annual emissions from quarrying alone range between 1,000 to 1,500 metric tons of CO₂. Specifically:
50,000 tons × 20 kg CO₂/ton = 1,000 metric tons CO₂ (low estimate)
50,000 tons × 30 kg CO₂/ton = 1,500 metric tons CO₂ (high estimate)
Transportation
Transporting heavy stones from quarrying sites to carving centres such as Puri, Bhubaneswar, and Konark significantly contributes to the industry's carbon emissions. Given the weight and volume of the stone, diesel trucks are typically used for long-distance transport.
Average Transport Distance: The distance from major quarries to carving hubs ranges between 200 to 300 kilometres.
CO₂ Emissions per Ton-Kilometre: According to industry estimates, the transport of 1 ton of stone over 1 kilometre emits around 0.03 kg of CO₂. For a 200 to 300-kilometer journey, this translates into:
200 km × 0.03 kg CO₂/ton-km = 6 kg of CO₂ per ton
300 km × 0.03 kg CO₂/ton-km = 9 kg of CO₂ per ton
Total Transport Emissions: For the 50,000 tons of stone transported annually, the total emissions from transportation are:
50,000 tons × 6 kg CO₂/ton = 300,000 kg CO₂ (300 metric tons)
50,000 tons × 9 kg CO₂/ton = 450,000 kg CO₂ (450 metric tons)
Thus, the total emissions from transportation range between 300 and 450 metric tons of CO₂ annually.
Manufacturing and Carving Process
While the stone carving process in Odisha is still largely artisanal, modern technologies, including power tools like grinders and polishers, are increasingly being integrated into workshops. The energy consumed by these tools, typically powered by electricity, also contributes to carbon emissions, though the emissions per piece of stone carved vary depending on the size and complexity of the work.
Emissions per Piece: On average, carving 1 ton of stone generates 5 to 10 kg of CO₂, based on electricity consumption and the energy required to run electric tools.
Total Annual Production: Odisha's stone carving industry produces between 10,000 to 12,000 finished pieces annually. If we assume that each piece weighs, on average, 2 tons (a rough average between smaller sculptures and larger works), the total stone used for production is 20,000 to 24,000 tons annually.
Total Manufacturing Emissions:
20,000 tons × 5 kg CO₂/ton = 100 metric tons CO₂ (low estimate)
24,000 tons × 10 kg CO₂/ton = 240 metric tons CO₂ (high estimate)
Thus, the emissions from the manufacturing process contribute between 100 and 240 metric tons of CO₂ annually.
Final Finishing and Polishing
The finishing stage, which includes polishing, sanding, and detailing, is energy-intensive and contributes to additional emissions. The use of polishing machines and other power tools increases the carbon footprint.
Emission per Ton: Finishing 1 ton of stone can generate 5 kg of CO₂ due to the electricity used by polishing machines and grinders.
Annual Emissions from Finishing: Assuming 20,000 to 24,000 tons of stone are processed annually, emissions from finishing are:
20,000 tons × 5 kg CO₂/ton = 100 metric tons CO₂
24,000 tons × 5 kg CO₂/ton = 120 metric tons CO₂
Total Carbon Emissions
Summing up emissions from all the stages—quarrying, transportation, manufacturing, and finishing—the total carbon footprint of the Odisha stone carving industry amounts to:
Thus, the total carbon emissions for the Odisha stone carving industry range from 1,500 to 2,310 metric tons of CO₂ annually.
Mitigation Opportunities
There are opportunities to reduce carbon emissions through sustainability initiatives:
Hybrid or Electric Vehicles for transportation could reduce transport emissions by 20-30%, saving up to 150 metric tons of CO₂ annually.
Energy-efficient machinery, such as solar-powered tools, could cut manufacturing and finishing emissions by 10-15%, saving approximately 35 to 54 metric tons of CO₂.
Recycling stone dust and waste for secondary uses could reduce the demand for fresh stone and, in turn, reduce quarrying emissions by 10-15%, potentially saving 100 to 225 metric tons of CO₂ annually.
Through these mitigation strategies, the Odisha stone carving industry could reduce its carbon footprint by 285 to 429 metric tons of CO₂, achieving a more sustainable and environmentally responsible production process.
SOCIAL IMPACT OF STONE CARVING
The stone carving industry in Odisha has deep social and cultural roots, providing significant socio-economic benefits while also facing challenges that shape its long-term sustainability. With a rich heritage that dates to ancient times, this industry not only supports livelihoods but also preserves the craftsmanship and artistic traditions unique to the region. Here is an in-depth look at the social impact of Odisha's stone carving industry across several dimensions:
Employment and Livelihoods
The stone carving industry is a major source of employment in Odisha, particularly in rural areas like Puri, Konark, Khurda, Bhubaneswar, and Mayurbhanj. As of 2023, it employs approximately 15,000 to 20,000 artisans, many of whom belong to marginalized communities. Most artisans have learned the craft through generational knowledge transfer, passing the skills down from one generation to the next.
Income Levels: The income earned by artisans varies greatly depending on their skill level, the complexity of the work, and market demand. Skilled artisans can earn between ₹15,000 to ₹25,000 (approx. $180 to $300) per month, while less skilled workers may earn between ₹8,000 to ₹12,000 (approx. $100 to $150) per month. Although these incomes are modest, they are often the primary or sole source of household income for many families.
Poverty Alleviation: Despite challenges, the stone carving industry plays a critical role in poverty alleviation in rural Odisha. Many artisans come from economically disadvantaged backgrounds, and the industry provides them with a stable, though limited, source of income. Efforts by the state government and NGOs to organize these artisans into cooperatives and provide them with better access to markets have improved income security.
Women's Participation: The participation of women in the stone carving industry is relatively low, comprising around 10-15% of the workforce. However, where women are involved, they are primarily engaged in polishing, sanding, and finishing tasks. Increasing women’s involvement in all stages of the production process, including carving and design, could significantly enhance the industry's social impact by empowering women economically.
Preservation of Traditional Craftsmanship
Odisha’s stone carving is a culturally significant art form, and its preservation contributes to maintaining the state’s cultural identity. The intricate designs found on temples like Konark’s Sun Temple, Lingaraj Temple, and Jagannath Temple are direct reflections of this heritage. By continuing to practice these techniques, artisans help keep these ancient skills alive.
Generational Knowledge Transfer: One of the key social impacts of the stone carving industry is the transmission of traditional knowledge from one generation to the next. However, with modernization and urbanization, fewer young people are willing to take up the craft, leading to concerns about the potential loss of these ancient skills. To address this, the Odisha government has initiated training programs under schemes like the Guru Shishya Parampara, where master artisans teach young apprentices the art of stone carving.
Challenges in Retaining Youth: Although the industry offers cultural and historical significance, many young artisans are migrating to urban centres for better-paying jobs in other sectors like construction, information technology, or tourism. This exodus presents a risk to the continuity of the stone carving tradition, and unless there is a strategic intervention to make the craft more lucrative, the industry could lose its appeal to future generations.
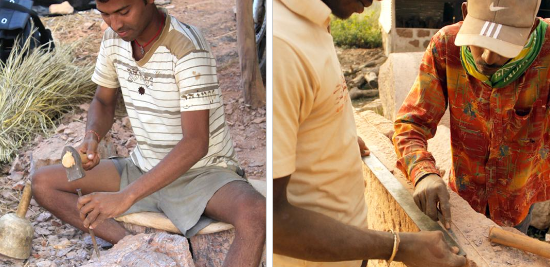
Impact on Education and Skill Development
Access to Education: Traditionally, stone carving families have had limited access to formal education, as children often begin to work alongside their parents at a young age. This has historically limited opportunities for higher-paying jobs outside of the industry. However, NGOs and government programs are working to improve educational access for children from stone carving families. Initiatives like Odisha Livelihoods Mission and the State Institute for Development of Arts and Crafts (SIDAC) offer scholarships and educational support to artisans’ children, aiming to improve literacy rates and access to higher education.
Artisan Skill Development: Training and upskilling programs funded by the Ministry of Textiles, Government of India and implemented under the Handicrafts Mega Cluster Mission have made a positive social impact. These programs train artisans in both traditional and modern techniques, allowing them to expand their range of skills. Additionally, training in business management and digital marketing equips artisans to manage their businesses independently, helping to sustain livelihoods.
Social and Community Identity
Stone carving is not just an occupation but a part of the community identity for many artisans in Odisha. Carving communities are often tightly knit, with generations of families living and working together. This close-knit community structure provides social security, support networks, and a sense of belonging for the artisans, reinforcing their dedication to the craft.
Social Status of Artisans: Historically, stone carvers enjoyed a high social status due to their role in constructing temples and monuments. However, in modern times, the social prestige associated with the craft has diminished. In many cases, artisans now struggle with poor living conditions, limited access to healthcare, and a lack of social security benefits, all of which affect the overall quality of life. Efforts to elevate their social status through GI (Geographical Indication) tagging and public recognition of their work are ongoing, but progress is slow.
Impact of Government and NGO Support
The social impact of the stone carving industry is amplified through the efforts of government bodies and non-governmental organizations that seek to improve the living and working conditions of artisans.
Government Schemes: Various state and central government schemes provide financial assistance, healthcare, and skill development programs. For instance, Odisha State Cooperative Handicrafts Corporation offers subsidies on raw materials and tools, while schemes like Artisan Credit Cards provide access to low-interest loans for small artisans. These initiatives aim to reduce artisans’ dependence on informal lenders and improve their financial security.
NGO Support: NGOs like the Craft Council of India and INTACH (Indian National Trust for Art and Cultural Heritage) work on the grassroots level, offering support in the form of training, healthcare, and housing for artisans. These organizations also promote fair trade practices, ensuring that artisans receive fair prices for their work in both domestic and international markets.
Challenges in Health and Working Conditions
The physical nature of stone carving can lead to various occupational health hazards. Artisans often work in poorly ventilated environments and are exposed to stone dust, which can lead to respiratory illnesses like silicosis. Moreover, the repetitive motions required for hand-carving stone can lead to musculoskeletal disorders.
Healthcare Access: Access to healthcare for artisans remains limited, especially in rural areas. Government and NGO interventions have been initiated, but coverage remains insufficient. Health insurance programs specifically for artisans are still in early stages, and most artisans rely on traditional medicine or private clinics for healthcare.
Empowerment through Cooperatives
The formation of artisan cooperatives has had a positive social impact, empowering artisans by giving them collective bargaining power. Cooperatives help artisans access better prices for raw materials, negotiate with buyers, and ensure fair wages. They also provide a platform for sharing knowledge, organizing training sessions, and promoting the welfare of the artisans. These cooperatives are supported by both state and central government programs aimed at uplifting marginalized communities.
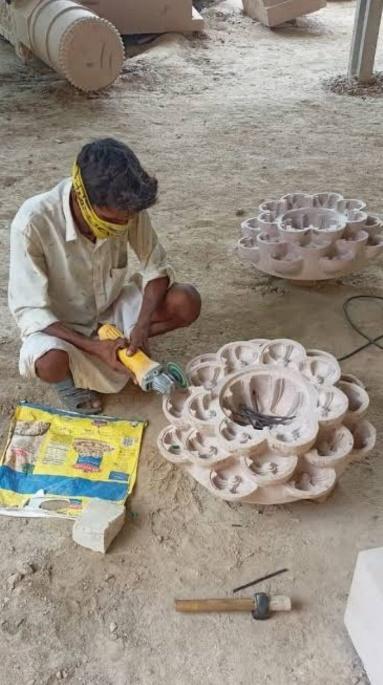
PAYMENT TERMS FOR STONE CARVING
Payment terms in the stone carving industry are crucial for ensuring a smooth transaction between artisans, clients, and suppliers. These terms govern how and when payments are made, influencing cash flow, project management, and overall business relationships. Understanding these terms is essential for artisans, customers, and stakeholders involved in stone carving, whether for gravestones, sculptures, architectural elements, or decorative items.
Types of Payment Structures
Payment terms can vary widely depending on the nature of the project, the relationship between the artisan and the client, and the scale of the work. Here are some common payment structures:
Advance Payment: It is common for artisans to request an advance payment, typically ranging from 20% to 50% of the total project cost. This upfront payment serves to secure the order and cover initial costs, such as purchasing materials and allocating labour.
Milestone Payments: For larger projects, payments may be structured around specific milestones. This approach involves dividing the total cost into several instalments based on project phases. For instance, a client might pay 30% upfront, 30% upon the completion of rough carving, and the remaining 40% upon final delivery and approval. Milestone payments help manage cash flow and ensure that both parties remain committed throughout the project.
Final Payment: The remaining balance is often paid upon completion of the project. This final payment may be contingent on the client’s satisfaction with the work, including inspections for quality and adherence to specifications.
Retainer Fees: In some cases, clients may agree to pay a retainer fee for ongoing projects or long-term collaborations. This fee provides financial security for artisans while ensuring the client has access to the artisan's services as needed.
Payment Methods
The choice of payment method can also impact payment terms in the stone carving industry. Common payment methods include:
Bank Transfers: Direct bank transfers are a popular option, especially for larger sums, as they provide a secure and traceable method of payment.
Cash Payments: For smaller projects or local transactions, cash payments may be accepted, although this method carries risks regarding security and documentation.
Checks: While less common, some clients may prefer to pay via check, which offers a paper trail but can involve delays in processing.
Digital Payments: The rise of digital payment platforms has introduced new options, such as mobile wallets and online payment systems, providing convenience for both artisans and clients.
Factors Influencing Payment Terms
Several factors influence the payment terms agreed upon in stone carving projects:
Project Size and Complexity: Larger and more complex projects typically involve higher risks and costs, prompting artisans to seek more favourable payment terms, such as larger advance payments or milestone payments.
Client Relationship: Established relationships between artisans and clients may result in more flexible payment terms. Long-term clients may have greater trust, allowing for more lenient arrangements.
Market Conditions: Economic factors, such as demand for stone carving services and competition among artisans, can influence payment terms. In a competitive market, artisans may be more inclined to offer favourable terms to secure contracts.
Material Costs: Fluctuations in material costs can also impact payment terms. If the price of stone or other materials rises unexpectedly, artisans may adjust payment structures to accommodate these changes.
Legal Considerations
It is essential for both artisans and clients to understand the legal implications of payment terms. Contracts should clearly outline payment terms, including:
Total Cost: A detailed breakdown of the total project cost, including labour and materials.
Payment Schedule: Clear timelines for when payments are due, including any milestones or conditions that must be met.
Late Payment Penalties: Terms specifying penalties for late payments can help protect artisans from cash flow disruptions.
Refund Policies: In cases of project cancellation or disputes, refund policies should be clearly defined to avoid misunderstandings.
Communication and Transparency
Effective communication between artisans and clients is crucial for establishing and adhering to payment terms. Artisans should be transparent about their pricing structure, payment methods, and timelines. Clients, in turn, should communicate their expectations and any budget constraints.
Regular updates throughout the project can help maintain trust and ensure both parties are aligned regarding progress and payments. If challenges arise, such as delays or changes in project scope, open communication can facilitate adjustments to payment terms and prevent conflicts.
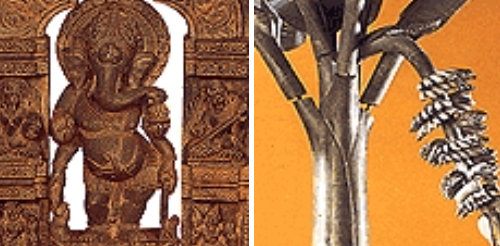
CERTIFICATIONS IN STONE CARVING
Certifications play a crucial role in enhancing the credibility and marketability of Odisha's stone carving industry, especially in global markets. One key certification is the Geographical Indication (GI) tag, which Odisha's stone carving received, recognizing it as a unique craft linked to the region’s cultural heritage. This certification helps protect the artisans from imitation products and boosts their recognition in both domestic and international markets. Additionally, certifications related to Fair Trade and handmade artisan products are increasingly sought after by consumers who prioritize ethical and sustainable practices. These certifications ensure that artisans receive fair wages, work in safe conditions, and that the production processes are environmentally friendly. For international markets, ISO certifications may also be pursued to meet quality standards and regulations, particularly in the export of stone sculptures. Obtaining these certifications can open new avenues for Odisha’s artisans, helping them reach larger markets, gain customer trust, and secure a competitive edge.
Geographical Indication (GI) Tag
Description: GI tags protect products originating from a specific geographical area, ensuring that only those who are part of that region can market their products as such. For Odisha’s stone carvings, a GI tag can help preserve traditional techniques and enhance marketability.
Steps to Apply:
Identify Eligibility: Ensure that your product has a specific geographical origin and unique qualities.
Gather Documentation: Collect evidence of the product’s traditional use, methods, and characteristics associated with the region.
Form a Collective: It is beneficial to form a cooperative or association of artisans to strengthen the application.
Submit Application: Fill out the application form available on the Geographical Indications Registry website.
Follow-Up: The application will be examined by the GI registry, and there may be follow-up inquiries.
Online Link: Registered Gls | Geographical Indications | Intellectual Property India (ipindia.gov.in)
ISO Certification
Description: ISO certifications improve quality management processes, ensuring consistency and quality in production. ISO 9001 is the most relevant for quality management.
Steps to Apply:
Understand Requirements: Review the specific requirements for ISO 9001 certification.
Prepare Documentation: Create a quality management system (QMS) document outlining processes, responsibilities, and procedures.
Training: Train staff on ISO standards and quality management principles.
Select a Certification Body: Choose an accredited ISO certification body for the audit.
Undergo the Audit: The certification body will conduct an audit to assess compliance.
Receive Certification: If compliant, you will receive the ISO certification, valid for a specified period (usually three years).
Online Link: ISO - International Organization for Standardization
Handicraft Mark
Description: The Handicraft Mark certifies authentic Indian handicrafts, enhancing their market value and promoting traditional craftsmanship.
Steps to Apply:
Check Eligibility: Ensure that your products meet the handicraft criteria.
Prepare Application: Fill out the application form available on the Ministry of Textiles' website.
Provide Samples: Submit product samples along with the application for assessment.
Documentation: Include documentation of the production process and artisan details.
Inspection: An inspection may be conducted to evaluate quality and authenticity.
Certification Issuance: Once approved, you will receive the Handicraft Mark certification.
Online Link: Handicraft Mark
Fair Trade Certification
Description: Fair Trade Certification ensures ethical practices, fair wages, and sustainable development for artisans.
Steps to Apply:
Familiarize with Criteria: Understand the Fair-Trade principles and requirements.
Assess Compliance: Evaluate your business against Fair Trade standards.
Contact a Fair-Trade Organization: Reach out to organizations like Fair Trade India for guidance.
Submit Application: Complete the application process, which may include interviews and documentation of practices.
External Audit: An external audit will be conducted to verify compliance with Fair Trade standards.
Receive Certification: If compliant, you will receive Fair Trade Certification.
Online Link: Fair Trade India
Sustainable Certification
Description: The Forest Stewardship Council (FSC) certification ensures that wood and related materials are sourced sustainably.
Steps to Apply:
Understand FSC Criteria: Review the sustainability criteria set by FSC.
Conduct a Self-Assessment: Assess your sourcing practices against FSC standards.
Choose a Certification Body: Select an accredited FSC certification body.
Submit Documentation: Provide required documentation regarding your sourcing practices.
Audit Process: The certification body will conduct an audit to evaluate compliance with FSC standards.
Certification Issuance: Upon successful audit, you will receive FSC certification.
Online Link: Forest Stewardship Council (FSC)
General Steps to Obtain Certifications
Research: Familiarize yourself with each certification's requirements and benefits. Understand which certifications align best with your business goals.
Training and Capacity Building: Invest in training programs related to quality standards, sustainable practices, and fair-trade principles. Many NGOs and government bodies offer workshops.
Collaborate with Cooperatives and NGOs: Work with local cooperatives, artisan groups, or NGOs that can provide support in navigating the certification process. They may offer resources, guidance, and even financial support.
Document Preparation: Gather all necessary documentation, including:
Product samples
Production process descriptions
Financial records
Details about the artisan community
Application Submission: Complete and submit the application forms online or directly to the relevant certifying bodies. Ensure that all required information is accurate and comprehensive.
Engage in Follow-Up: After submitting the application, engage with the certifying body for any follow-up inquiries or additional information they may require.
Certification Audit: Prepare for any audits that may be required. Ensure that your practices are in line with the standards set by the certifying body.
Utilize the Certification: Once obtained, leverage the certification in marketing efforts, both online and offline, to enhance credibility and marketability.
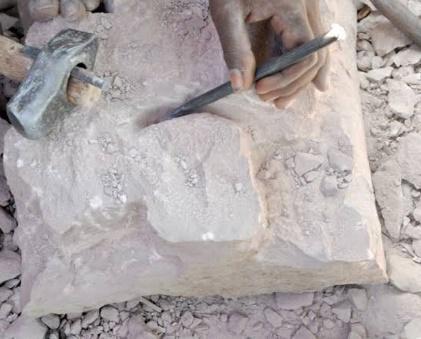
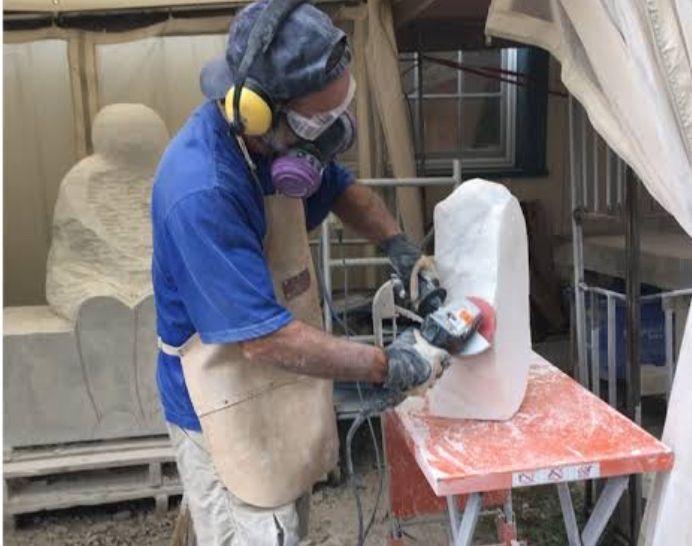
LOGISTICS IN STONE CARVING INDUSTRY
The logistics of stone carving in Odisha involves a complex network of sourcing raw materials, transportation, supply chain management, and distribution of finished products. Managing these logistics is critical for the artisans, traders, and organizations involved in the craft, as it affects the overall efficiency, cost, and sustainability of the industry.
Sourcing Raw Materials
The logistics process begins with the procurement of raw materials, primarily stones such as sandstone, soapstone, khondalite, and granite. Odisha is rich in stone quarries, especially in regions like Khiching, Bolangir, and Jaipur, which are known for providing high-quality stones for carving.
Quarrying and Extraction: Stone is mined from these quarries using both traditional and modern techniques. The raw stone blocks are extracted in large quantities and transported to the workshops where artisans operate.
The logistics of quarrying require careful planning, including hiring skilled labour, using appropriate machinery, and adhering to government regulations for sustainable mining practices.
Transportation to Workshops: Once the stones are quarried, they need to be transported to the carving centres, which are often located in Puri, Bhubaneswar, Konark, and nearby villages. These stones can be heavy and bulky, requiring trucks or other heavy-duty vehicles for transportation. Given the poor road infrastructure in rural areas, especially around quarries, transportation can be a significant logistical challenge. Any delays or damage during transport can affect the production timeline and increase costs.
Production and Workshop Management
Stone carving is a time-consuming and labour-intensive process. Workshops in artisan villages like Raghurajpur are the centres of production, where stones are transformed into intricate sculptures and temple structures. Logistical management within these workshops includes:
Workforce Coordination: Ensuring that artisans are organized efficiently, with tasks assigned according to their skill levels. The timing of deliveries and completion of work must align with the supply chain to avoid delays.
Tools and Equipment: Artisans rely on both traditional hand tools and modern electric tools for carving and polishing. Logistics involve ensuring a consistent supply of these tools and their maintenance. As most of the tools are locally sourced, coordinating their availability and replenishing stocks becomes crucial.
Supply Chain and Market Distribution
One of the major logistical challenges for the stone carving industry in Odisha is reaching the market. Artisans often face difficulties in accessing both domestic and international markets due to limited infrastructure and reliance on middlemen.
Local Distribution: Finished stone carvings are primarily sold through local markets, exhibitions, and tourist centres. Towns like Puri, Bhubaneswar, and Konark are significant tourist destinations, which create local demand. However, transporting the finished products from rural workshops to these market hubs can be challenging due to inadequate transportation infrastructure.
National and International Distribution: For national and international markets, stone carvings need to be shipped over long distances. Products may be transported by truck to larger cities like Bhubaneswar, where they can then be shipped via rail, road, or air to other parts of India or overseas. Export logistics are more complex due to packaging requirements, customs regulations, and the high cost of long-distance transportation.
Export Process: Exporting stone carvings requires careful logistical planning, including customs clearance, securing international shipping routes, and managing overseas delivery. Ensuring that the products are securely packaged to prevent damage during transit is also critical. International buyers, particularly from Europe, the USA, and Southeast Asia, create a demand for larger and more intricate stone sculptures, but the logistics of delivering these items across borders can be costly and time-consuming.
Storage and Packaging
The finished stone sculptures are fragile and need to be carefully stored and packaged before transportation. Inadequate storage facilities in workshops can lead to damage or deterioration of the finished pieces, particularly when dealing with larger sculptures that may need to be stored for extended periods before delivery.
Packaging: Due to the delicate nature of stone carvings, especially intricate works, proper packaging is essential to prevent breakage or chipping. Foam padding, wooden crates, and protective coverings are often used. For larger exports, especially those being shipped overseas, specialized packaging and shipping containers are required.
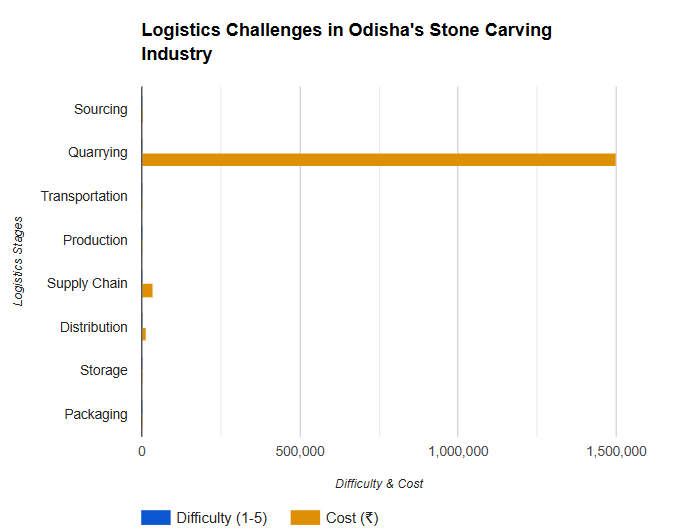
KEY COMPONENTS OF MONEY LAUNDERING FRAMEWORK
Money laundering is a sophisticated process through which individuals and organizations conceal the origins of illegally obtained money, making it appear legitimate. It typically unfolds in three stages:
Placement: This initial phase involves introducing illicit funds into the financial system. Criminals often utilize various methods, such as:
Cash Transactions: Engaging in cash-based businesses, where large amounts of cash can be deposited or used without raising suspicion.
Purchasing High-Value Items: Buying luxury goods, real estate, or other high-value assets that can later be resold.
Bank Deposits: Making cash deposits in small amounts to avoid detection.
Layering: The second phase involves obscuring the origins of the funds through a series of complex transactions designed to confuse investigators. Techniques used in layering include:
Transferring Funds: Moving money between multiple bank accounts, often across different jurisdictions, to create confusion about the money's source.
Converting Cash: Transforming cash into other financial instruments, such as traveller’s checks or investments, to further mask its origins.
Using Shell Companies: Establishing businesses that exist only on paper, which can facilitate fraudulent transactions without real economic activity.
Integration: In this final stage, laundered money is reintroduced into the economy, making it appear as legitimate income. Common methods include:
Investing in Legitimate Businesses: Using the funds to invest in businesses that generate legal profits, thus creating a facade of legitimacy.
Personal Expenditures: Spending the laundered money on personal luxuries or lifestyle enhancements, which can further complicate tracking.
Consequences of Money Laundering
The implications of money laundering are far-reaching:
Legal Penalties: Involvement in money laundering, even unintentionally, can lead to severe legal consequences, including fines, asset forfeiture, and imprisonment. Businesses found guilty of facilitating money laundering can face hefty penalties.
Reputation Damage: Businesses implicated in money laundering risk significant reputational harm, which can affect relationships with customers, suppliers, and financial institutions. A tarnished reputation can lead to lost business opportunities.
Financial Losses: Legal battles, compliance costs, and potential fines can impose substantial financial burdens on businesses. The economic impact can be devastating, especially for small enterprises.
Increased Scrutiny: If a business is flagged for money laundering activities, it may face heightened scrutiny from regulators and law enforcement. This can lead to invasive audits and investigations that disrupt normal operations.
What to Do If Involved in Money Laundering
If you suspect involvement in money laundering, either directly or indirectly, it is crucial to take immediate action:
Cease All Suspicious Activities:
The first step is to stop any transactions or operations that could be connected to money laundering. This includes halting cash transactions and reviewing ongoing business deals for any irregularities.
Seek Legal Counsel:
Choose a Qualified Attorney: Engage a lawyer with experience in financial crimes and regulatory compliance. They can provide specific guidance based on your unique situation.
Full Disclosure: Be transparent with your lawyer about all relevant details, including your business operations and any suspicious activities you may have observed.
Document Everything:
Maintain Detailed Records: Keep meticulous records of all transactions, including invoices, receipts, contracts, and communications. Documentation can serve as crucial evidence if you need to defend your actions.
Detail Suspicious Activities: Note any irregularities or red flags you have encountered in your business dealings. This information may be essential for legal consultations.
Notify Authorities:
File a Report: Depending on the situation, you may choose to report your suspicions to the Financial Intelligence Unit (FIU) or local law enforcement. Reporting can demonstrate your willingness to cooperate and mitigate potential penalties.
Understand Whistleblower Protections: Familiarize yourself with the rights and protections available for whistleblowers, which can safeguard you from retaliation.
Implement Compliance Measures:
Establish Internal Controls: Create a system for monitoring transactions to identify suspicious activities. This may include setting transaction limits and requiring documentation for large cash payments.
Know Your Customer (KYC) Protocols: Implement KYC procedures to verify the identities of customers and suppliers. This can help ensure that your business only engages with legitimate entities.
Cooperate with Investigations:
Be Transparent: If contacted by law enforcement or regulatory bodies, cooperate fully. Provide all requested documentation and be honest about your business practices.
Legal Representation: Have your attorney present during any discussions or interviews with authorities to ensure your rights are protected.
Educate Yourself and Your Team:
Attend Training Programs: Participate in workshops or training sessions on AML regulations and best practices. This knowledge can help you and your employees identify potential money laundering risks.
Cultivate a Compliance Culture: Encourage a culture of compliance within your organization, where all employees understand the importance of preventing financial crimes.
Review and Revise Business Practices:
Assess Sourcing and Customers: Regularly evaluate your suppliers and customers to ensure they are legitimate and adhere to legal standards.
Maintain Transparency: Engage in transparent business practices, including clear documentation of all transactions and contracts.
The Role of Technology in Combatting Money Laundering
The integration of technology in business practices can significantly reduce the risks associated with money laundering. Here are some ways technology can aid in compliance:
Data Analytics: Utilizing data analytics tools can help businesses identify unusual transaction patterns that may indicate money laundering. These tools can automate the monitoring process and flag suspicious activities for further review.
Blockchain Technology: Blockchain's transparency can provide an immutable record of transactions, making it more difficult for illicit funds to be concealed. Some businesses are exploring blockchain for supply chain transparency.
KYC Software: Implementing KYC software can streamline the customer verification process, ensuring that only legitimate customers and suppliers are engaged. These tools can help automate background checks and monitor transactions in real time.
Compliance Management Systems: Employing comprehensive compliance management systems can help businesses adhere to regulations by providing frameworks for monitoring, reporting, and auditing.
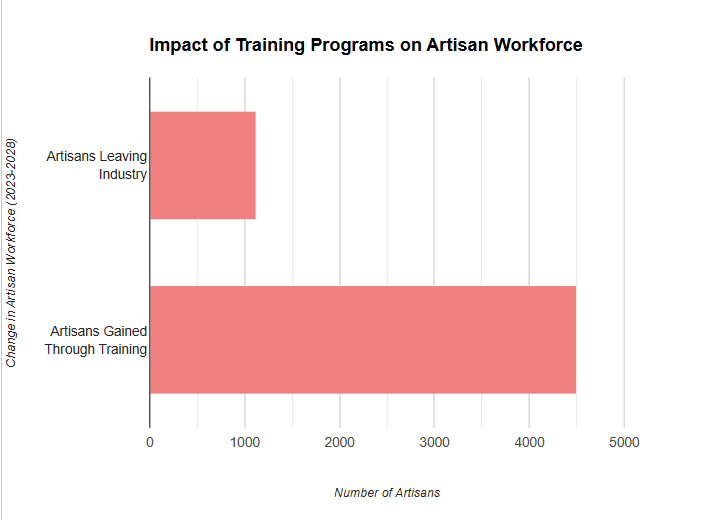
CUSTOMS AND DUTIES IN STONE CARVING
Custom duties in the stone carving industry vary globally based on trade policies, product classifications, and market dynamics. As stone carving involves raw materials like granite, marble, sandstone, and other natural stones, these materials and the finished products are subject to import/export tariffs. Below is an in-depth look at custom duties in the stone carving industry, backed by global data.
Global Custom Duties on Stone Carving Products
Custom duties on stone carvings and related materials are determined by the Harmonized System (HS) codes, which classify products for customs purposes. Commonly used HS codes for stone carving include:
HS Code 6802: Worked monumental or building stone (e.g., granite, sandstone, limestone) and products like statues or carvings.
HS Code 2515: Marble, travertine, and alabaster.
HS Code 2516: Granite, sandstone, and other building stones, both crude and processed.
Custom duties for stone carving materials and finished products range significantly depending on the country of import and the trade agreements in place.
Average Custom Duties by Region
United States:
Import duties for worked stone products (HS Code 6802) range between 2.5% and 6%.
For example, finished stone products, including carvings or sculptures, face a 3.7% tariff.
The U.S. provides duty-free access for some stone carvings from developing countries under the Generalized System of Preferences (GSP).
European Union (EU):
The EU’s import duties for stone carving products are relatively low, ranging between 2% and 4.5%.
Tariffs for raw materials, such as marble or granite blocks, are lower (around 1% to 3%) to encourage industrial processing within the EU.
Finished stone carvings attract higher duties, typically in the range of 4% to 5%, with certain exceptions under trade agreements with developing countries.
India:
India imposes custom duties on both imports and exports of stone products, with the basic customs duty (BCD) on imports ranging from 10% to 20%, depending on the type of stone.
For example, imported marble slabs are subject to a 20% duty, while carved stone articles attract a 12% duty.
Export duties for raw stone materials such as sandstone or granite are generally zero, but India levies an 18% GST (Goods and Services Tax) on the domestic sale of processed stone carvings.
China:
China is a major producer and exporter of stone carving products. Export duties on stone carvings are typically low, often between 0% and 3%, to promote global trade.
For imports, custom duties on raw stone materials like marble, granite, and sandstone range between 2% and 10%, depending on the source country and material type.
Brazil:
Brazil is one of the world's largest granite exporters. Import duties on worked stone products generally range between 10% and 12%, while export tariffs are minimal to encourage the growth of its stone industry.
Middle East and Africa:
Countries like Egypt, Turkey, and South Africa impose tariffs of 5% to 15% on stone carving products, particularly on imports.
Export duties on raw materials are low (typically 0% to 5%) to boost the sale of domestic stone internationally, such as marble and granite.
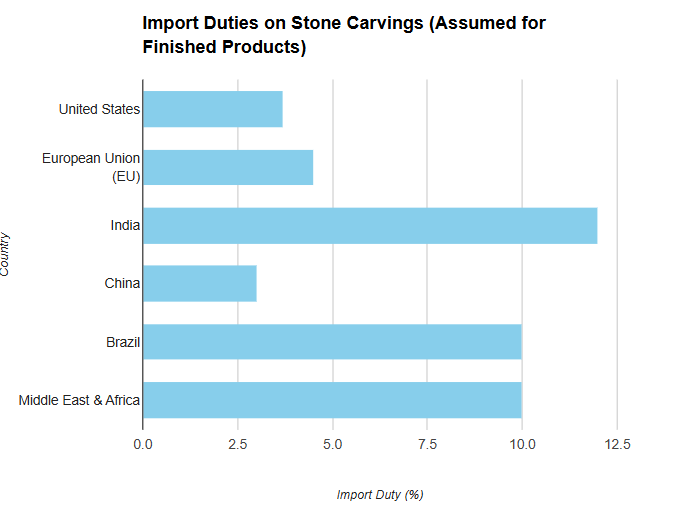
Impact of Free Trade Agreements (FTAs)
Free Trade Agreements (FTAs) have a significant impact on custom duties related to stone carving products:
ASEAN Free Trade Area (AFTA): Countries within the ASEAN bloc have significantly reduced or eliminated tariffs on stone products, which promotes trade in raw materials and finished carvings between member countries.
United States-Mexico-Canada Agreement (USMCA): Tariffs on stone carvings traded between the U.S., Canada, and Mexico are minimal (typically below 3%) under the USMCA agreement.
EU-India Free Trade Talks: If finalized, this agreement could lower tariffs on stone carving exports from India to the EU, creating opportunities for Indian artisans and stone carvers.
Examples of Custom Duties for Stone Carving (HS Code 6802)
United States: 3.7% for finished stone carvings (worked stone).
European Union: 4% to 5% for finished stone carvings.
India: 12% for imports of finished stone carvings.
China: 3% to 8% for stone carvings (import).
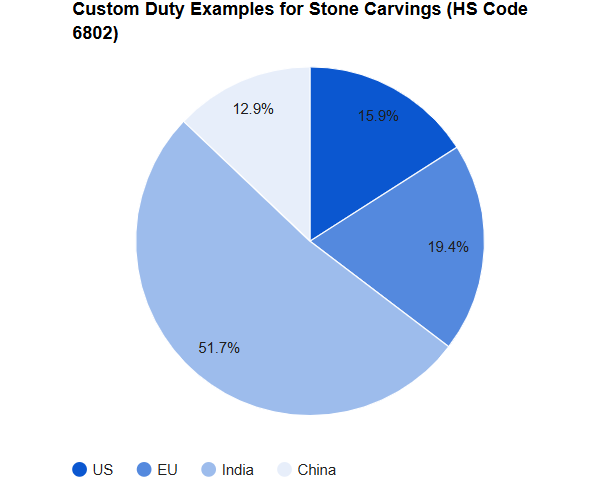
Cost Impact on Stone Carving Industry
Cost Structure: Custom duties add a significant cost to the final price of both raw materials and finished products. For example, an additional 10% to 20% tariff on imported marble or granite can raise production costs for carvers and artisans, especially when importing from countries with high tariffs.
Artisan-Level Impact: For small-scale stone carvers in countries like India or Nepal, higher custom duties on imported raw materials (such as specialized stones) can limit access to high-quality materials, reducing their competitive edge in the international market.
Challenges Due to Protectionist Measures
In some countries, rising protectionism has led to increased custom duties, complicating international trade for stone carving products. For instance:
U.S.-China Trade War: During the U.S.-China trade dispute, tariffs were imposed on various Chinese stone products, raising costs for U.S. importers of stone carvings and potentially shifting demand to other countries.
Environmental Regulations and Duties
Some countries are imposing additional fees and regulations on the stone industry to account for environmental impacts:
Carbon Tariffs: The European Union is considering carbon border adjustments, which could affect the stone carving industry. These tariffs aim to penalize imports from countries with higher carbon footprints in stone extraction and processing.
ETHICAL PRACTICES IN STONE CARVING
The stone carving industry, steeped in tradition and artistry, holds a unique position in cultural heritage and economic development. However, as with many artisanal crafts, it faces challenges related to sustainability, labour practices, and community impact. Adopting ethical practices in stone carving is essential for ensuring the long-term viability of the craft, protecting artisans' rights, and promoting environmental stewardship. This overview explores various aspects of ethical practices in the stone carving industry, including labour conditions, sourcing materials, environmental sustainability, and community engagement.
Fair Wages and Livelihood Support
Odisha’s stone carving industry employs around 50,000 artisans. Ethical wage practices are critical in ensuring that artisans are fairly compensated for their labour.
According to surveys conducted by various craft organizations, the average wage of an artisan in the Odisha stone carving sector ranges between INR 10,000 to INR 25,000 per month, depending on skill level, experience, and market demand. However, some high-skilled artisans can earn up to INR 40,000-50,000.
The introduction of artisan welfare schemes such as the Shilpi Samman Yojana, which provides a monthly pension of INR 1,500 to artisans above 60 years, helps support elder artisans who have dedicated their lives to the craft but may struggle financially due to low savings.
Despite these initiatives, around 40% of artisans in rural areas are still paid irregular wages and face income instability, according to reports by NGOs such as Kala Bhoomi, an organization working to improve artisan welfare.
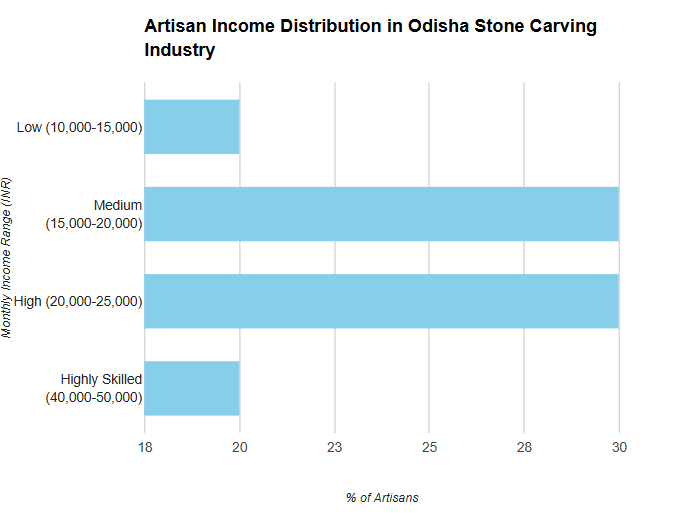
Sustainable Raw Material Sourcing
Sustainable practices in the stone carving industry primarily focus on responsible sourcing of raw materials like khondalite, soapstone, and granite, which are mined locally.
Odisha's stone carving relies heavily on locally sourced stones, particularly from Khurda and Puri districts. However, unethical mining practices, such as excessive extraction without proper regulation, have led to environmental degradation and depletion of resources.
To promote ethical practices, the Odisha Handicrafts Development Corporation (OHDC) has introduced a sustainable sourcing policy, ensuring that raw materials are procured from authorized quarries that follow environmental regulations.
As per government data, 60% of stone material used by artisans is now sourced from regulated quarries, reducing the impact on local ecosystems. This figure has improved due to stricter enforcement of environmental policies over the last decade.
Use of Non-Toxic Materials and Processes
Ethical practices in production include ensuring the safety and well-being of artisans during the carving process, which often involves exposure to dust and stone particles.
Only about 25% of workshops in Odisha provide protective equipment (masks, gloves) to artisans, even though prolonged exposure to stone dust can lead to respiratory issues like silicosis.
The Odisha Directorate of Factories and Boilers has mandated safer working conditions, including proper ventilation in workshops, and has provided INR 10 crore in funding to improve health and safety measures.
There has been a gradual improvement in artisan health and safety, with 15% of workshops adopting eco-friendly and non-toxic materials for finishing products.
Preservation of Traditional Techniques
Ethical practices also encompass efforts to preserve traditional carving techniques, which are integral to Odisha’s cultural heritage.
About 80% of stone carving in Odisha is still done manually using traditional methods passed down through generations. This promotes cultural preservation but also raises concerns about labour-intensive practices and low productivity.
The Odisha government and organizations like Crafts Council of India have been running training programs to encourage artisans to adopt modern tools while maintaining the integrity of traditional designs.
More than 5,000 artisans have benefited from these government-backed training programs in the last five years, increasing their productivity by 10-15% without compromising ethical standards.
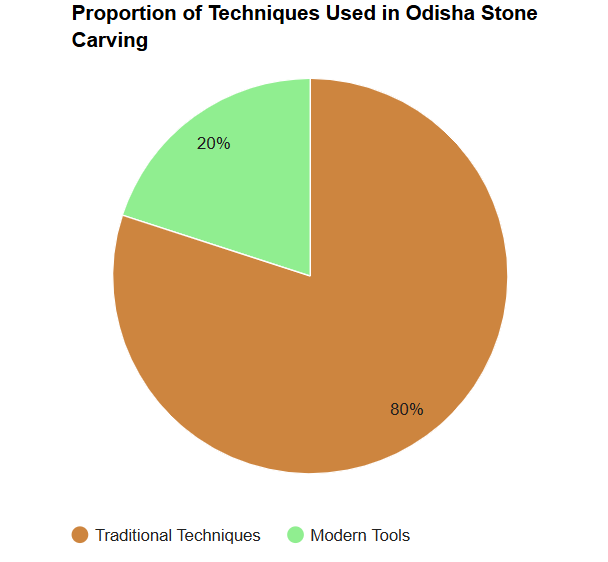
Artisan Rights and Government Initiatives
The government and local NGOs have undertaken initiatives to ensure that artisans’ rights are protected, and their work is properly valued.
Shilpi Samman Yojana: In addition to providing pensions, this scheme offers financial aid during hardships, such as the COVID-19 pandemic, when stone carving artisans experienced significant income drops due to the collapse of tourism and market demand. More than 10,000 artisans received financial support during the pandemic, ensuring they could sustain themselves.
Craft Clusters and Villages: Odisha has developed several craft clusters, such as Raghurajpur (famous for both stone carving and other crafts), which provide artisans with direct access to markets, reducing exploitation by middlemen. This system ensures that artisans can receive around 20-30% higher earnings compared to selling through intermediaries.
The Artisan Credit Card Scheme: Provides access to loans for artisans, allowing them to invest in better tools and materials. More than 7,000 artisans have benefited from loans worth INR 25 crore under this scheme, which provides low-interest credit.
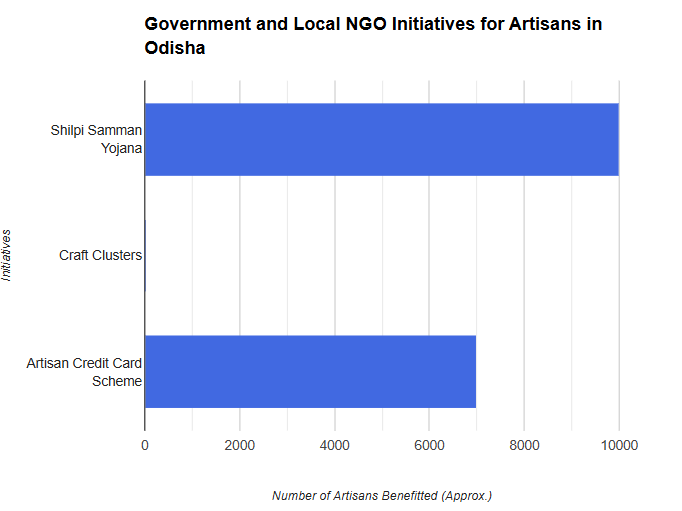
Fair Trade and International Ethical Standards
As Odisha’s stone carvings reach international markets, there has been increasing focus on adhering to fair trade standards.
Products that adhere to Fair Trade standards fetch 20-30% higher prices in international markets, and about 5-10% of artisans are already participating in these schemes.
Organizations like Fair Trade Forum India and Export Promotion Council for Handicrafts (EPCH) help connect artisans with fair trade networks, ensuring ethical practices across the value chain, from raw material procurement to labour conditions.
Child Labor and Gender Equality
Ethical concerns in stone carving, like in many traditional industries, often include child labour, and gender disparity.
According to a 2019 study by the National Commission for Protection of Child Rights (NCPCR), child labour in the stone carving industry has significantly decreased, with less than 2-3% of workshops reportedly engaging children under 14 years old. Strict enforcement of child labour laws and awareness campaigns have contributed to this decline.
Gender representation remains a challenge. Only about 15-20% of artisans are women, and they generally earn about 10-20% less than their male counterparts. However, organizations like Mission Shakti in Odisha have started initiatives to train and empower women artisans, aiming to raise female participation to 30% over the next five years.
Environmental Responsibility
The stone carving industry can have a significant environmental impact if not managed responsibly, particularly concerning the extraction of raw materials and waste management.
In response to concerns about unsustainable quarrying practices, the Odisha government has begun regulating quarry operations to ensure that only licensed quarries supply stones to artisans. Currently, 60% of stone quarries supplying to the industry are regulated.
Workshops are being encouraged to adopt waste reduction strategies. It is estimated that only about 10-15% of stone material is wasted during carving, and many workshops are finding ways to use the byproducts for smaller sculptures or decorative items.
Efforts in Ethical Marketing
Artisans and cooperatives have adopted ethical marketing strategies, ensuring transparency in pricing and direct sales to consumers, especially in international markets.
Online platforms like Craftsvilla and Gaatha are helping artisans sell their products directly to consumers, ensuring fair compensation. Artisans who use these platforms can avoid middlemen and receive around 30-35% higher prices.
Exporters who follow ethical sourcing and fair-trade practices have seen a 10-20% growth in international orders, according to the Export Promotion Council for Handicrafts.
MARKET TRENDS IN STONE CARVING
The stone carving industry, rooted in centuries-old traditions, has evolved significantly in recent decades due to technological advances, changing consumer preferences, and global market dynamics. The demand for carved stone products—ranging from architectural pieces and monuments to decorative sculptures—continues to grow, with various factors shaping market trends.
Global Market Size and Growth
The global natural stone market was valued at $33.54 billion in 2022 and is projected to grow to $48.06 billion by 2027, with a compound annual growth rate (CAGR) of around 7.5% from 2023 to 2027. The stone carving industry is a subset of this larger market, with demand primarily driven by architecture, construction, and home decor.
India is one of the largest producers and exporters of stone carving products, alongside countries like China, Italy, Brazil, and Turkey. India’s stone exports amounted to approximately $6 billion in 2022, with a notable contribution from hand-carved stone products.
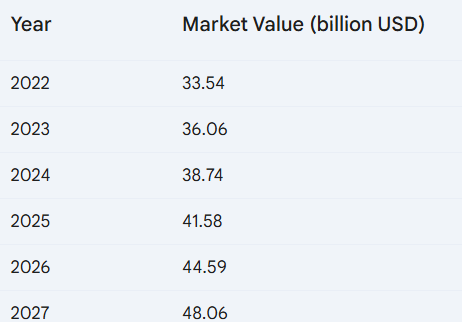
Demand in Construction and Architecture
Construction Sector: Stone carvings used in buildings and infrastructure projects (e.g., columns, facades, memorials) are witnessing steady demand, particularly in regions focused on restoring historical monuments or building luxury projects. The global market for architectural stone products (which includes carved stone) is forecasted to reach over $14 billion by 2025.
Rising Urbanization: Increasing urbanization, particularly in developing economies, is a major growth driver. Urban real estate developments often incorporate stone carvings for aesthetic purposes, leading to a steady increase in demand.
Home Decor and Artisanal Products
Luxury and Home Decor: Growing demand for handcrafted stone products in home decor, including garden statues, sculptures, and carved furniture, has pushed the market upwards. In the United States and Europe, sales of luxury home decor featuring natural stone carvings have seen a rise of approximately 4% annually in recent years.
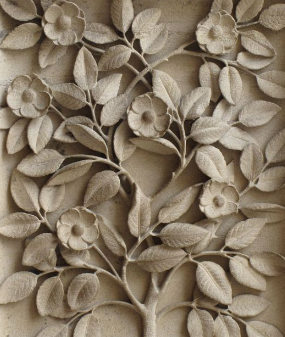
E-Commerce Growth: E-commerce platforms like Etsy and Amazon have allowed small-scale stone carvers to access global markets, particularly for personalized stone products. In 2023, online sales of hand-carved stone products saw a 15% year-over-year increase.
Regional Trends
Asia-Pacific: Countries like India and China dominate the global stone carving market due to their abundant natural resources and large pool of skilled artisans. India alone accounts for 25-30% of the global stone carving exports. The Asia-Pacific region is expected to see significant growth, driven by construction booms in countries like India, Indonesia, and Vietnam.
North America: Demand for custom-carved stone products for residential and commercial buildings is growing, with a focus on luxury and eco-friendly designs. The U.S. market for carved stone decor has seen a CAGR of 6% from 2020 to 2023.
Europe: Europe, particularly Italy and Greece, has a deep-rooted stone carving tradition, with demand primarily in architectural restoration and high-end real estate. Europe's stone market saw €10 billion in sales in 2022.
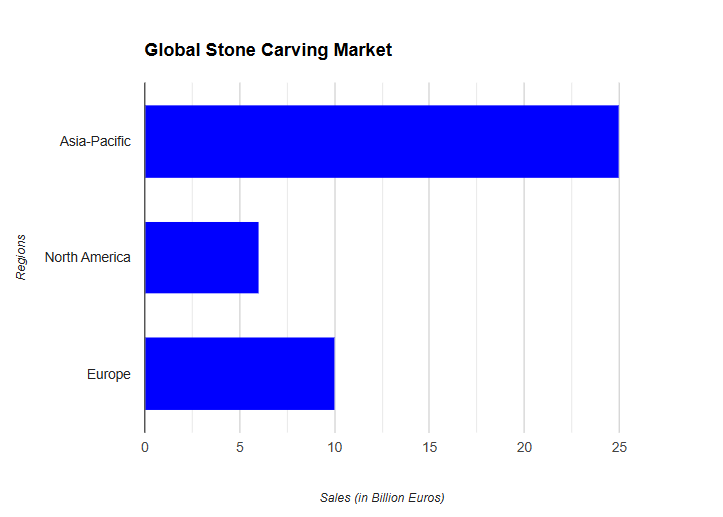
Technological Integration
CNC Machines and 3D Printing: The integration of CNC (Computer Numerical Control) machines and 3D printing into the carving process has revolutionized the industry by speeding up production, reducing labour costs, and improving precision. CNC machines are expected to account for 25% of stone carving production globally by 2025.
Laser Engraving: Innovations in laser engraving are also allowing for highly detailed, personalized stone carvings, with laser engraving equipment sales expected to grow at a CAGR of 5.2% over the next five years.
Consumer Preferences and Sustainability
Eco-Friendly Materials: Consumers are increasingly prioritizing sustainable and ethically sourced materials. There is growing demand for stone that is extracted in an environmentally responsible manner. Eco-friendly stone, such as reclaimed or locally sourced materials, is becoming popular, particularly in regions like Europe and North America, where environmental concerns drive buying decisions.
Minimalism and Modern Design: Modern design trends have shifted towards minimalist stone carvings with sleek lines and natural finishes, contributing to demand for clean and functional stone pieces.
Digital Marketing in Stone Carving
E-Commerce Growth: The rise of e-commerce has significantly boosted the visibility of stone carving artisans globally. Digital platforms like Alibaba, Etsy, and specialized B2B platforms are key in driving exports and sales of stone carvings, especially custom-made and artisanal products. In India, e-commerce sales of stone carvings have grown by 20% year-over-year since 2021.
Social Media Marketing: Platforms like Instagram and Pinterest have become popular for showcasing bespoke stone carvings, particularly among home decor enthusiasts. Digital platforms are enabling artisans to reach niche markets, contributing to an increase in direct sales.
Export Trends and Trade Data
India: India remains the top exporter of stone carving products, with exports accounting for more than 20% of the global stone market. Indian exports of carved stone products increased by 15% in 2022, driven by rising demand from Europe and the United States.
China: China is another dominant player in the stone carving industry, exporting billions of dollars’ worth of stone carvings globally. In 2021, China exported over $8 billion worth of stone and stone products, including carved stone pieces.
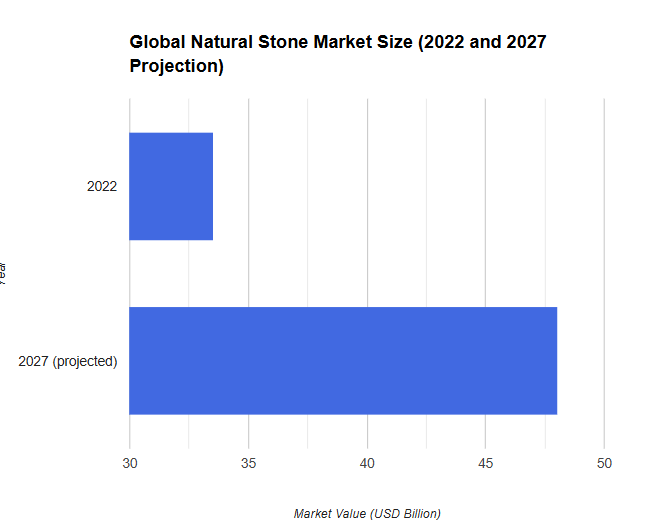
INNOVATION IN STONE CARVING
The stone carving industry, historically rooted in traditional methods passed down through generations, is witnessing a significant transformation due to technological advances, modern design trends, and evolving consumer demands. Innovation in this sector is reshaping the way stone carving is approached, produced, and marketed, bringing new possibilities for artisans, manufacturers, and designers.
Technological Advancements
CNC (Computer Numerical Control) Machines: CNC machines have revolutionized the stone carving industry by automating the carving process. Using precise computer-controlled tools, these machines can produce intricate designs with high precision and consistency, which would otherwise take weeks or months to carve by hand. This technology allows for faster production, lower labour costs, and a reduction in human error.
Impact: By 2025, it is projected that 25% of global stone carving production will be done using CNC machines, enabling large-scale production for industries like construction, home decor, and monuments.
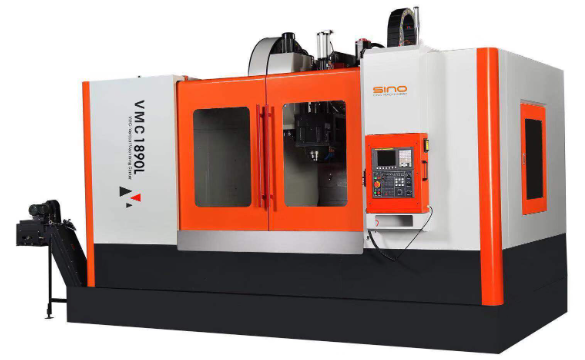
3D Printing Technology: 3D printing is an emerging innovation in the stone industry. While traditional 3D printing uses plastics or metals, research into stone-infused filaments and stone powder composites allows for 3D-printed stone products. This technology is being used to create detailed prototypes, which can then be used as Molds or models for final stone carving. It also allows for complex geometries that are difficult to achieve using traditional tools.
Example: Architects and designers are now using 3D printing to create custom stone facades and sculptures that blend organic shapes with modern aesthetics.
Laser Engraving: Laser engraving is another technology that allows for highly detailed and precise carvings. Using lasers to cut or etch patterns into the surface of stones, artisans can create personalized designs, logos, and fine details that would be hard to achieve by hand. This is particularly useful for items like memorial stones, plaques, and jewellery.
Robotics: Robotics in stone carving is another area of innovation, where robots equipped with carving tools can work continuously, replicating designs on a large scale. This is especially useful for architectural projects requiring large amounts of stonework, such as columns, statues, and decorative panels.
Sustainable Innovation
Sustainability is becoming a crucial factor in modern innovation within the stone carving industry. Traditional stone carving processes can be resource-intensive and environmentally damaging due to the quarrying, transportation, and waste involved. However, several innovations are helping to reduce the environmental impact:
Use of Reclaimed and Recycled Stone: Artisans and builders are increasingly using reclaimed stone from demolished buildings or leftover materials from other construction projects. This not only reduces waste but also gives new life to existing materials, aligning with the principles of the circular economy. Reclaimed stone has become particularly popular in sustainable architecture and interior design.
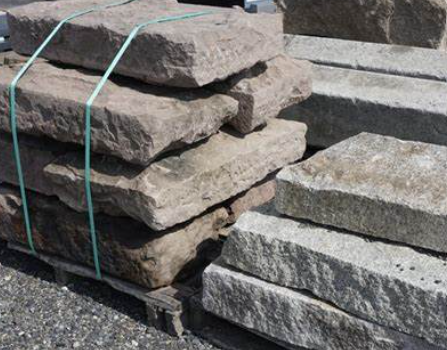
Eco-Friendly Quarrying Techniques: Modern quarrying methods are becoming more eco-conscious. Technologies like diamond wire sawing and water jet cutting are replacing traditional blasting methods, which are harmful to the environment and the surrounding ecosystems. These new techniques minimize dust, noise, and water usage during the extraction process.
Low Carbon Emission Processes: Energy-efficient machinery and renewable energy sources are being integrated into the production process to reduce the carbon footprint of stone carving. Solar-powered quarries and energy-efficient workshops are helping to make the industry more sustainable.
Material Innovation
Composite Stone Materials: In addition to natural stones like marble, granite, and limestone, composite stone materials are being developed using stone dust, resin, and binding agents. These composites are more affordable, lighter, and sometimes more durable than natural stone, making them ideal for projects requiring large-scale production or where cost is a concern.
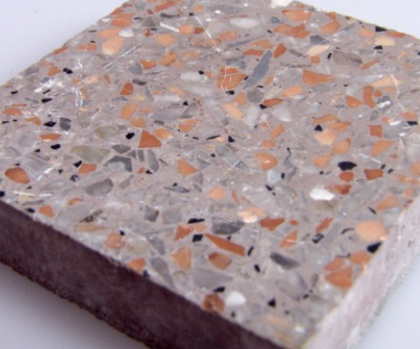
Example: Engineered quartz, a composite material made from crushed quartz and resin, has gained popularity for use in countertops and architectural elements. It provides the look and feel of natural stone with enhanced durability and less environmental impact.
Nanotechnology: Nanotechnology is being applied to improve the properties of stone. Nanocoating’s can make stone surfaces more resistant to water, stains, and weathering, increasing the longevity and durability of stone carvings. This is especially useful for outdoor sculptures, monuments, and buildings exposed to harsh environmental conditions.
Design and Aesthetic Innovation
Minimalist and Contemporary Designs: In contrast to traditional ornate and highly detailed carvings, modern design trends in architecture and home decor are shifting towards minimalist and sleek stone products. Clean lines, geometric patterns, and natural finishes are becoming more popular. Innovations in design software allow architects and artists to experiment with new shapes and textures that reflect modern aesthetics.
Integration with Other Materials: Stone is being creatively combined with other materials, such as glass, metal, and wood, to create mixed-media sculptures and architectural pieces. This fusion of materials not only enhances the visual appeal but also introduces a new dimension to the craftsmanship and artistic possibilities in the stone carving industry.
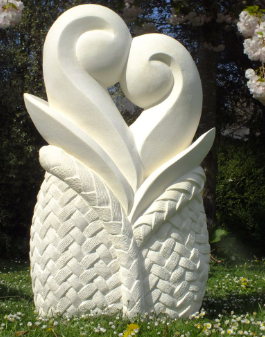
Digital Marketing and E-Commerce Innovation
Online Marketplaces: Artisans are increasingly turning to online platforms like Etsy, Alibaba, and Amazon to sell their carved stone products directly to consumers. This has expanded the market reach for small-scale carvers, allowing them to connect with global customers. The use of e-commerce has helped democratize the industry by making niche stone carving accessible to a broader audience.
Augmented Reality (AR): AR technology is being integrated into e-commerce platforms to allow customers to visualize stone products (e.g., sculptures, statues, and stone decor) in their homes or architectural projects before purchasing. This enhances the customer experience and increases buyer confidence.
Example: Companies are now developing AR apps that let users see how a custom stone fireplace or sculpture would look in their living space.
Digital Customization Platforms: Consumers are increasingly demanding personalized stone products. Digital tools that allow customers to design and customize stone carvings online—selecting the type of stone, size, shape, and engravings—are becoming popular. These tools allow artisans to cater to unique client preferences and provide highly personalized products.
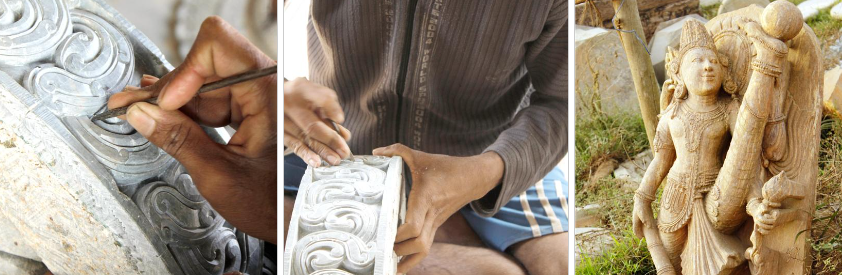
RISK MANAGEMENT IN STONE CARVING
Risk management in the stone carving industry involves comprehensive strategies to address the unique hazards and uncertainties that impact the sector. Here is a more detailed breakdown of the various risks and their mitigation strategies:
Occupational Health and Safety Risks
Hazards: Stone carving workers are exposed to heavy machinery, sharp tools, and the risks associated with manual handling of large stone blocks. The constant dust generated from carving and chiselling can lead to long-term respiratory diseases like silicosis. Prolonged exposure to high levels of dust, noise, and vibrations from machinery can also result in hearing loss, eye injuries, and muscular-skeletal disorders.
Risk Mitigation:
Personal Protective Equipment (PPE): Mandatory use of dust masks, protective eyewear, gloves, helmets, and ear protection can significantly reduce injury risks.
Ventilation and Dust Control: Implementing dust extraction systems, proper ventilation, and regular monitoring of air quality can limit worker exposure to harmful dust.
Ergonomic Training: Workers should be trained in proper lifting techniques, tool handling, and machine operations to minimize physical strain.
Regular Health Monitoring: Health check-ups and screenings for lung diseases and musculoskeletal problems should be conducted regularly to catch issues early.
Environmental Risks
Hazards: The stone carving process results in significant waste generation, including dust, stone chips, and wastewater from stone-cutting operations. Poor waste management can lead to environmental degradation, affecting the local ecosystem by contaminating soil and water sources. Additionally, uncontrolled dust emissions can pollute the air, impacting both workers and nearby communities.
Risk Mitigation
Waste Management Systems: Implementing effective waste collection and disposal systems, such as using dust suppression techniques and recycling stone waste, can help reduce environmental impact.
Water Recycling: Installing water recycling systems to manage wastewater produced during stone cutting reduces water consumption and minimizes the risk of local water contamination.
Sustainable Sourcing: Ensuring the raw materials (stones) are sourced from environmentally responsible and regulated quarries can minimize the depletion of natural resources and reduce environmental footprint.
Supply Chain Risks
Hazards: The stone carving industry is highly dependent on the consistent availability of raw materials, such as stone blocks and slabs. Supply chain disruptions caused by transportation delays, natural disasters, resource shortages, or political instability can halt production.
Risk Mitigation
Diversified Suppliers: Partnering with multiple suppliers from different geographical regions can help mitigate risks related to resource shortages or transport issues.
Inventory Management: Maintaining an adequate inventory of raw materials and having contingency plans in place for stockouts can reduce the impact of supply chain disruptions.
Transportation Insurance: Insuring shipments against damages, delays, or losses during transportation can protect the business from financial losses.
Market and Economic Risks
Hazards: Demand for stone-carved products can fluctuate based on market trends, economic conditions, and consumer preferences. Economic downturns or shifts in demand for luxury items can cause a decrease in sales, impacting profitability.
Risk Mitigation
Market Diversification: Expanding into different markets, both domestic and international, can reduce the dependency on a single market. For instance, diversifying products into architectural elements, souvenirs, and bespoke sculptures broadens market appeal.
Brand Positioning and Innovation: Continuously developing new products and focusing on unique designs can help artisans cater to niche markets and high-end consumers, reducing susceptibility to economic fluctuations.
Digital Marketing and E-commerce: Investing in online platforms to showcase and sell products globally can provide a buffer against localized economic slowdowns.
Legal and Regulatory Risks
Hazards: Non-compliance with local and national labour laws, safety standards, and environmental regulations can result in fines, legal actions, or the shutdown of operations. For example, ignoring safety regulations, such as failing to provide PPE or proper working conditions, exposes businesses to legal risks.
Risk Mitigation
Compliance Audits: Regular internal audits of legal compliance related to workplace safety, environmental standards, and labour laws can help avoid legal penalties.
Adhering to Certifications: Obtaining certifications like ISO 45001 for occupational health and safety and ISO 14001 for environmental management systems not only ensures compliance but also enhances the company’s reputation.
Continuous Training: Regular employee training on regulations and best practices ensures that the workforce is aware of safety protocols and legal requirements.
Technological Risks
Hazards: The stone carving industry often relies on a mix of traditional hand tools and modern machinery. The use of outdated or poorly maintained equipment can result in accidents, low productivity, or inconsistent quality of output. On the other hand, investing in new technology without proper training can lead to operational inefficiencies.
Risk Mitigation
Machinery Maintenance: Establishing a routine maintenance schedule for tools and equipment ensures they are safe to use and function efficiently, minimizing the risk of accidents.
Adopting Modern Technology: Incorporating technologies such as CNC (Computer Numerical Control) routers and 3D stone carving machines can increase precision, reduce labour intensity, and improve productivity. Proper training and hiring skilled technicians for these machines are crucial to avoid operational risks.
Technological Training Programs: Regularly upskilling workers and providing training on new tools and machines can help minimize the risks associated with technological transitions.
Financial Risks
Hazards: Stone carving businesses often face challenges related to cash flow, credit, and capital investment. High upfront costs for raw materials, tools, and labour can strain financial resources. Inconsistent income due to seasonal demand or market downturns exacerbates these financial risks.
Risk Mitigation
Financial Planning: Developing robust financial plans, including budgets, cash flow forecasts, and contingency funds, can help the business remain stable even during periods of low demand.
Access to Credit: Securing favourable credit terms, loans, or lines of credit from financial institutions can provide the liquidity necessary to cover operational costs during slow periods.
Cost Management: Efficiently managing overheads, optimizing labour costs, and negotiating better deals with suppliers can help improve profit margins and reduce financial risks.
Cultural and Social Risks
Hazards: In regions like Odisha, stone carving is deeply rooted in cultural traditions, and there is a risk of losing artisanship due to declining interest among younger generations. This could lead to a loss of traditional skills, adversely affecting both the industry and the cultural heritage of the region.
Risk Mitigation
Artisan Training Programs: Collaborating with local government bodies, NGOs, and cultural organizations to provide training and apprenticeships for younger generations can help preserve traditional techniques and ensure the longevity of the craft.
Cultural Preservation Initiatives: Promoting the heritage aspect of stone carving through festivals, exhibitions, and collaborations with cultural institutions can help create a broader appreciation for the craft and boost demand for authentic products.
By implementing these risk management strategies, the stone carving industry can safeguard its workers, protect the environment, ensure compliance with regulations, and remain competitive in a dynamic market.
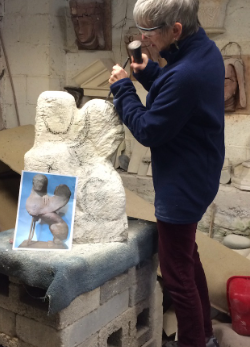
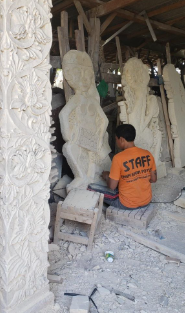
DIGITAL MARKETING IN STONE CARVING
Digital marketing presents a transformative opportunity for the stone carving industry in Odisha to expand its reach and engage with a global audience. Leveraging online platforms such as social media, websites, and e-commerce sites can significantly increase visibility and drive sales. High-quality visual content, including professional photos and videos of stone carvings, can attract potential customers and showcase the intricate craftsmanship and cultural significance of the products. Engaging content, such as blog posts, behind-the-scenes stories, and customer testimonials, helps build a strong brand presence and foster connections with audiences. Utilizing search engine optimization (SEO) techniques ensures that the stone carvings are easily discoverable by those searching for related products. Additionally, targeted online advertising, including pay-per-click (PPC) campaigns and social media ads, can reach specific demographics and drive traffic to e-commerce platforms. Embracing digital marketing strategies enables Odisha’s artisans to tap into new markets, build a global customer base, and enhance their overall market presence.
The global handicrafts market is expected to reach $1,252.9 billion by 2028, growing at a CAGR of 10.1% from 2021 to 2028. India, one of the largest exporters of handicrafts, accounts for $3.5 billion in exports annually. Stone carving is one of the key handicrafts contributing to this figure, with Odisha as one of the largest contributors.
Odisha has over 3,000 stone carvers, spread across cities and villages such as Bhubaneswar, Puri, and Raghurajpur. According to industry estimates, the local market value for stone carving products in Odisha stands at approximately ₹100-150 crore annually, while global demand, especially from collectors, religious institutions, and art enthusiasts, offers substantial untapped potential.
The Role of Digital Marketing in Promoting Stone Carving
Digital marketing, which includes channels such as social media, search engines, e-commerce platforms, and email campaigns, provides an unprecedented opportunity for artisans in Odisha to reach customers worldwide. Using data to fuel these strategies is key to unlocking growth.
Understanding Consumer Demographics Through Data
Google Analytics and Facebook Insights allow businesses to understand the demographics of their audience. For example, over 560 million Indians are online, and a large portion of these internet users, especially from Tier 2 and Tier 3 cities, are interested in handicrafts.
Artisans can leverage data on location, age, gender, and purchasing behavior to better understand the profiles of buyers interested in stone carving. Platforms like Instagram have become hotspots for showcasing crafts, with over 40% of users aged between 25 and 44, often seeking unique, cultural products.
Search Engine Optimization (SEO) for Organic Traffic
According to SEMrush, the term "stone carving in India" has an average monthly search volume of 1,300. Optimizing websites and online portfolios with specific keywords like "Odisha stone carving" and "temple sculptures" can lead to increased traffic.
Data also shows that mobile searches for terms related to Indian handicrafts are on the rise, with 70% of total internet searches happening on mobile devices. Optimizing for mobile and local SEO (e.g., "stone carvings near me") is crucial for local artisans to gain visibility.
Social Media Marketing
Social media platforms such as Facebook, Instagram, and Pinterest are powerful tools for artisans. With over 500 million Instagram users in India, visual storytelling through images and videos can help stone carvers showcase their work. A study shows that posts with videos receive 48% more engagement compared to static images.
Instagram's Shop feature allows artisans to sell directly through the platform, which can lead to increased sales. By using data analytics, artisans can understand which posts or products are performing best and adjust their strategies accordingly.
In addition, Facebook offers targeting options where businesses can target specific groups based on interests such as "Indian art," "sculpture," and "temple architecture." The ROI on such targeted ads can be significant, especially with $2.80 as the average CPC (Cost Per Click) for Indian-based ads on Facebook.
E-commerce and Global Outreach
Platforms like Etsy, Amazon, and Indian marketplaces like Craftsvilla provide access to both domestic and international buyers. According to data from Etsy, Indian sellers generated approximately ₹250 crore in sales in 2021, with a growing portion of this coming from traditional crafts.
By listing on these platforms and using data to track which regions show higher demand, stone carvers in Odisha can expand their markets beyond local buyers to international art collectors. In fact, Etsy’s growth in India has seen more than 100% YoY growth in the handicrafts category.
Integrating with e-commerce platforms also allows artisans to take advantage of global shipping logistics, potentially boosting exports and overall sales.
Email Marketing and Customer Retargeting
Email marketing remains one of the most cost-effective forms of digital marketing, with a ROI of 4,200% on average. Stone carving businesses in Odisha can use email marketing to keep in touch with previous buyers, announce new collections, and offer special deals.
Data-driven retargeting campaigns, which send automated emails to users who visited the site but did not make a purchase, can lead to increased conversions. Retargeting campaigns have been shown to increase conversion rates by 6-8% compared to non-targeted campaigns.
Utilizing Influencers and Collaborations
Influencer marketing is another growing trend. A study by Influencer Marketing Hub reveals that the average ROI for influencer marketing is $5.78 for every $1 spent. Collaborating with art influencers or cultural figures who align with Odisha’s artistic values can help spread awareness and boost credibility.
Micro-influencers, with smaller but highly engaged audiences, can be particularly effective for niche markets like stone carving, creating authentic connections with potential customers.
Challenges and Solutions in Digital Marketing for Stone Carving
While digital marketing provides numerous opportunities, stone carvers in Odisha face some challenges:
Digital Literacy: Many artisans, especially those in rural areas, lack the technical skills to navigate digital marketing platforms. Government initiatives and NGOs can play a role in offering training programs.
Logistics: Shipping heavy stone products globally is a challenge, but partnering with specialized logistics providers can help overcome this hurdle.
The global handicrafts market is expected to reach $1,252.9 billion by 2028, growing at a CAGR of 10.1% from 2021 to 2028. India, one of the largest exporters of handicrafts, accounts for $3.5 billion in exports annually. Stone carving is one of the key handicrafts contributing to this figure, with Odisha as one of the largest contributors.
Odisha has over 3,000 stone carvers, spread across cities and villages such as Bhubaneswar, Puri, and Raghurajpur. According to industry estimates, the local market value for stone carving products in Odisha stands at approximately ₹100-150 crore annually, while global demand, especially from collectors, religious institutions, and art enthusiasts, offers substantial untapped potential.
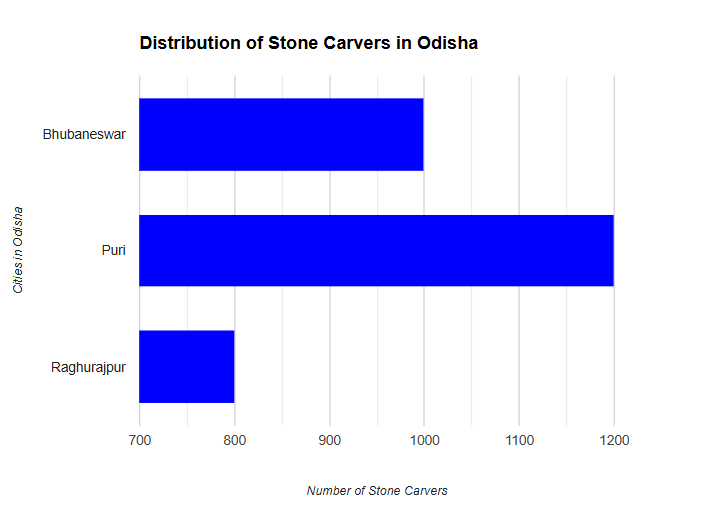
CUSTOMER SERVICE IN STONE CARVING
Customer service in the stone carving industry is essential for building long-lasting relationships, ensuring customer satisfaction, and differentiating the business in a competitive market. Given the high-value, custom nature of many stone-carved products, excellent customer service can help improve client retention, boost referrals, and enhance the overall customer experience. Below are key aspects and strategies for delivering exceptional customer service in the stone carving industry:
Personalized Service and Consultation
Why it is important: Stone carvings are often custom-made, high-involvement purchases, such as sculptures, architectural elements, or religious artifacts. Customers expect detailed consultation to ensure their vision is accurately translated into the final product.
Key strategies:
Initial Consultation: Offer free consultations to understand the customer’s specific needs, preferences, and design ideas. Use this opportunity to suggest materials, designs, and provide professional advice based on the customer’s vision.
Design Customization: Allow customers to choose the type of stone, dimensions, and intricate details of the carving. Providing digital mock-ups or sketches before beginning work helps the customer visualize the final product.
Dedicated Account Managers: For larger projects, assigning a dedicated contact person who oversees the customer’s order from design to delivery can enhance the service experience and ensure a smooth communication process.
Clear Communication and Transparency
Why it is important: Clear and timely communication helps build trust, especially when handling large, custom orders that take time to produce.
Key strategies:
Order Tracking: Provide customers with regular updates on their order’s status, including estimated completion time, progress photos, and shipping details.
Open Channels: Ensure customers can reach you via multiple communication channels, such as phone, email, and social media messaging. Having a customer service team available to answer inquiries promptly will enhance satisfaction.
Transparent Pricing: Be upfront about pricing, including any customization costs, shipping fees, or taxes. Providing a detailed quotation early on prevents misunderstandings later in the process.
Handling Complaints and Returns
Why it is important: Addressing complaints and returns effectively can turn a dissatisfied customer into a loyal one. Stone carvings are delicate, and issues related to damage during shipping or deviations from the design must be resolved promptly.
Key strategies:
Damage Policy: Develop a clear policy for handling damaged products, whether during shipping or due to manufacturing defects. Offering free repairs or replacements for damaged items instils confidence in your service.
Prompt Resolutions: Aim to resolve complaints within 24-48 hours, providing clear steps on how you will address the issue, whether through a refund, repair, or replacement.
Customer Feedback: After resolving complaints, ask for feedback on how the situation was handled. This not only shows that you value the customer’s input but also helps improve future service.
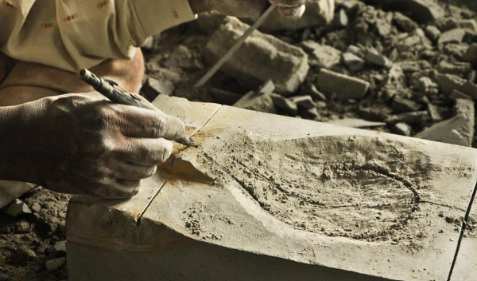
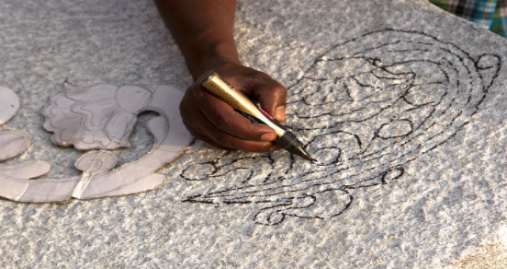
After-Sales Service
Why it is important: Offering support after the sale is crucial for customer retention and can lead to repeat business or referrals. After-sales service also builds trust and showcases the business’s commitment to customer satisfaction.
Key strategies:
Product Care Guidance: Provide customers with detailed instructions on how to care for and maintain their stone-carved products. This is particularly important for outdoor installations or products subject to wear and tear.
Follow-up: Contact customers a few weeks after delivery to ensure they are satisfied with the product. This could be through a phone call, email, or automated follow-up message.
Maintenance Services: Offering long-term maintenance services, such as periodic polishing, cleaning, or restoration, adds value to the customer experience.
Custom Order Management
Why it is important: Custom orders are a significant part of the stone carving business, and managing these efficiently ensures a smooth experience for the customer.
Key strategies:
Order Confirmation and Updates: Once a custom order is placed, confirm the details with the customer before starting the work to avoid misunderstandings. Regularly update them on the progress.
Customer Portal: For larger businesses, providing an online customer portal where clients can view their order status, review design specifications, and communicate directly with artisans can enhance the overall experience.
Flexible Customization: Be open to changes or adjustments in the design if requested by the customer during the production phase (within reason). This flexibility demonstrates that the customer’s satisfaction is a priority.
Training and Empowering Customer Service Teams
Why it is important: Customer service teams must be knowledgeable about both the stone carving process and customer service techniques to provide accurate, helpful information.
Key strategies:
Product Knowledge Training: Ensure customer service representatives are well-versed in the different types of stone, carving techniques, customization options, and production timelines. This allows them to confidently answer customer queries and provide tailored recommendations.
Soft Skills Training: Train staff in active listening, empathy, and conflict resolution so they can handle difficult situations calmly and professionally.
Empowerment: Empower customer service representatives to make decisions within predefined limits (such as offering small discounts or expedited shipping) to quickly resolve issues without needing management approval.
Loyalty Programs and Incentives
Why it is important: Offering rewards for repeat customers encourages long-term relationships and creates a sense of value.
Key strategies:
Loyalty Discounts: Offer discounts or special deals to returning customers, especially for bulk or custom orders. This can be structured as a tiered system, where frequent buyers receive greater benefits.
Referral Incentives: Create a referral program where customers can earn discounts or free services when they refer new clients. This encourages word-of-mouth marketing and customer loyalty.
Exclusive Previews: Provide loyal customers with exclusive previews of new collections, designs, or upcoming exhibitions to make them feel valued and appreciated.
QUALITY CONTROL
Quality control in the stone carving industry is essential for ensuring that every piece meets high standards of craftsmanship, durability, and aesthetic value. As stone carving involves both the use of raw materials and skilled labour, maintaining consistent quality at every stage of production is crucial to delivering products that satisfy customer expectations. Effective quality control not only prevents costly mistakes but also ensures the longevity and functionality of the carved pieces, especially for large projects like monuments or architectural elements. Here is a detailed look at quality control practices in the stone carving industry.
Material Selection and Inspection
The quality of stone materials directly impacts the final product, making material selection one of the most critical stages in quality control. Stones such as marble, granite, and sandstone must be inspected for structural integrity, consistency in texture, and the absence of defects like cracks, blemishes, or irregular colour patterns. For example, a slab of marble that contains internal fissures or impurities can break during carving or degrade more quickly when exposed to environmental elements. To ensure only the best materials are used, businesses should work closely with trusted suppliers and conduct rigorous inspections upon receiving the stone. Quality checks might include visual inspections for defects, compressive strength tests, and colour variation assessments. By rejecting subpar materials early in the process, carvers can prevent future issues in the production phase.
Precision in Design and Execution
Stone carving requires high precision, especially for detailed designs or architectural components. Achieving this precision begins with accurate design planning. Many businesses now use CAD (Computer-Aided Design) software to create exact designs before carving begins, ensuring that measurements, patterns, and proportions are all correct. Once a design is finalized, the tools used in the carving process—whether traditional chisels or modern CNC (Computer Numerical Control) machines—must be properly calibrated. Misaligned or poorly maintained tools can cause inconsistencies in the carving, leading to defects that diminish the overall quality of the piece. Regular calibration and maintenance of equipment are key to avoiding these issues. For custom projects, creating prototypes or mock-ups before starting the final carving can further ensure that the design works as intended.
Skilled Workforce and Training
The skill level of the workforce plays a vital role in ensuring the quality of stone carving. Artisans must have both the technical knowledge and the artistic ability to execute intricate designs while maintaining structural integrity. Quality control measures should include regular training programs to keep the workforce updated on the latest carving techniques, new tools, and safety protocols. In addition, many companies benefit from having artisans with specialized skills for different types of stone or carving methods. Continuous evaluation and improvement of artisan skills are crucial for maintaining high standards, and businesses should invest in certification programs to formalize and recognize their workers’ expertise. Regular skill assessments can help ensure that only qualified artisans handle complex projects, thereby reducing errors and improving overall quality.
Final Product Inspection and Testing
Once the carving process is complete, the final product undergoes a thorough inspection to ensure it meets all design and quality specifications. This involves checking for surface smoothness, structural integrity, and fidelity to the original design. In some cases, particularly for large sculptures or architectural elements, additional tests may be conducted to ensure the product's durability under environmental stress, such as temperature changes, moisture, and wear over time. For outdoor installations, testing might include checking the stone’s resistance to weathering or freezing conditions. Any product that fails to meet the required standards should be sent back for refinishing or adjustments, ensuring that only the highest quality pieces are delivered to clients.
By integrating stringent quality control measures into every stage of the production process—material selection, design precision, skilled labour, and final product inspection—businesses in the stone carving industry can consistently deliver high-quality products. These practices not only enhance the reputation of the business but also reduce waste, improve customer satisfaction, and ensure long-term durability and value in their work.
CREDIT CHECK
In the stone carving industry, a credit check can be an essential step in ensuring the financial reliability of both businesses and clients. Credit checks are typically used to assess the ability of a company or individual to meet financial obligations, whether it is in relation to suppliers, clients, or even artisans and employees. Here’s how credit checks play a role in the stone carving industry:
Supplier Creditworthiness
Many stone carving businesses rely on suppliers for raw materials such as marble, granite, or sandstone, which can be costly. A credit check of the supplier helps the business verify whether the supplier has a strong track record of meeting financial obligations, ensuring that they can provide consistent and timely deliveries of materials.
Example: If a stone carving company orders large quantities of marble from an overseas supplier, performing a credit check helps confirm that the supplier is financially stable and will likely honour the terms of the contract, including timely delivery and quality of goods.
Client Credit Check
Stone carving projects can be large and expensive, especially when dealing with custom orders, monuments, or architectural pieces. For businesses, conducting a credit check on potential clients ensures that they can pay for the project, reducing the risk of non-payment or delayed payments.
Example: A company receiving an order for a large outdoor sculpture from a private client or a commercial developer might run a credit check to ensure that the client can afford the cost of the materials, labour, and other expenses involved in creating and installing the sculpture. This minimizes the risk of financial disputes or delayed payments once the project is complete.
Business-to-Business (B2B) Transactions
Stone carving companies often work with other businesses, such as construction firms, interior designers, or retailers who sell finished stone products. In these business-to-business (B2B) transactions, performing a credit check helps ensure that the partner company has a good payment history and the financial capacity to fulfil their obligations.
Example: If a stone carving business is contracted to provide custom granite countertops for a construction project, the stone carving company might run a credit check on the construction firm to ensure that the firm has a history of paying vendors on time. This helps avoid disputes or delays in receiving payment after the work is done.
Financial Management and Credit Terms
Many suppliers offer credit terms to businesses, allowing them to purchase materials and pay later. Stone carving businesses can benefit from favourable credit terms, which help with cash flow management. However, a credit check may be required by the supplier before extending credit.
Example: A stone carving company that frequently purchases raw stone on credit might be required by their supplier to undergo a credit check before being approved for a higher credit limit. The supplier will evaluate the company’s financial history, existing debts, and ability to pay off previous credit agreements.
Risk Mitigation in International Transactions
Stone carving often involves international transactions, especially when sourcing rare stones from specific regions. Credit checks can help mitigate the risk of dealing with foreign suppliers or clients whose financial standing may not be immediately clear.
Example: A stone carving company based in Europe might conduct a credit check on an Indian supplier before importing marble or granite. This ensures that the supplier is financially stable and reduces the risk of transaction issues like non-delivery, disputes over pricing, or fluctuating payment terms.
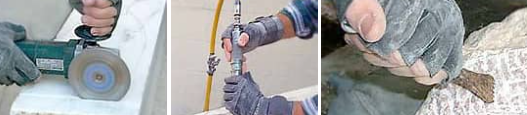
INSURANCE IN STONE CARVING
Insurance plays a vital role in protecting the stone carving industry from various risks and uncertainties. Coverage should include general liability insurance to address potential claims related to property damage or personal injury resulting from the use of stone products. Additionally, product liability insurance can protect against claims arising from defects or issues with the carvings that affect customers. Property insurance is essential for safeguarding against damage or loss of valuable tools, equipment, and inventory. For artisans and businesses involved in international trade, cargo insurance is also important to cover potential losses during shipping and handling. By investing in comprehensive insurance policies, the stone carving industry can manage risks effectively, ensuring business continuity and financial security in the face of unforeseen events.
Challenges Faced by Stone Carvers
Occupational Hazards: Stone carving is a physically demanding profession. Artisans work with heavy tools and materials, leading to risks such as cuts, fractures, lung diseases from inhaling stone dust, and musculoskeletal disorders. The lack of protective equipment further exacerbates these health risks. As most artisans are self-employed or work in small, informal groups, they lack access to health insurance and other social security benefits.
Damage to Tools and Finished Works: The tools used for stone carving—chisels, hammers, and polishing equipment—are expensive and prone to wear and tear. Additionally, during the carving process or transportation, finished sculptures are susceptible to damage or breakage, which can lead to significant financial losses.
Unstable Income: Artisans in Odisha often rely on seasonal demand, which fluctuates depending on festivals, tourism, and the patronage of temples. Their income is inconsistent, and they may face periods without work, making it difficult to manage daily expenses or invest in better tools and materials.
Environmental and Natural Risks: Odisha is prone to natural disasters such as cyclones, floods, and storms, which can damage the raw materials, tools, and finished sculptures. Artisans, whose livelihoods depend on their workshops and materials, are particularly vulnerable to such events.
Cultural and Market Shifts: The rising demand for machine-made sculptures and shifts in consumer preferences can also adversely impact the traditional stone carving industry. Artisans may find it increasingly difficult to compete with mass-produced goods.
Role of Insurance in Addressing Challenges
Insurance can be a powerful tool to mitigate these risks and offer a safety net for the artisans involved in stone carving. It can protect both their personal well-being and their business interests, helping them focus on preserving their craft rather than worrying about financial security.
Health and Accident Insurance: Given the physical risks involved in stone carving, health and accident insurance is essential for artisans. Access to affordable health insurance plans can help artisans cover medical expenses arising from work-related injuries or chronic conditions caused by exposure to stone dust. Government-sponsored schemes like the Pradhan Mantri Jan Arogya Yojana (PMJAY) or sector-specific health insurance initiatives for artisans could play a crucial role in ensuring their well-being.
Livelihood and Income Insurance: Unstable incomes and seasonal work patterns leave stone carvers vulnerable to financial uncertainty. Livelihood insurance schemes designed to provide compensation during periods of unemployment or insufficient work can offer significant relief. These insurance plans can be particularly useful during off-seasons or times of market downturns.
Tool and Equipment Insurance: The tools of the trade are vital to the craft, and any damage to them can halt production. Insurance that covers the cost of repairs or replacement of tools due to wear and tear, accidents, or theft can ensure that artisans continue working without interruptions. Additionally, equipment insurance can cover workshops and storage spaces from natural calamities, accidents, and vandalism.
Insurance for Finished Products: Artisans invest significant time and skill into creating their sculptures, and any damage to the finished products can lead to financial setbacks. Insurance policies that cover sculptures during transportation or while on display in galleries, markets, and exhibitions would offer financial protection against such losses. This form of insurance would help reduce the risk for artisans when participating in national and international exhibitions.
Disaster Insurance: Given Odisha's susceptibility to natural disasters, artisans are often at risk of losing their workshops, tools, and inventory due to floods or cyclones. Disaster insurance tailored for small businesses and artisans could provide compensation to cover the losses incurred during such events. State government initiatives or partnerships with private insurance companies can help craft custom policies to meet the needs of stone carvers.
Types of Insurance for Stone Carvers
Personal Accident Insurance: This type of insurance covers medical expenses in the event of an accident. For stone carvers, personal accident insurance provides compensation in case of injuries sustained during work. Some policies even cover permanent disability, offering a crucial safeguard for artisans whose livelihoods depend on their physical abilities.
Health Insurance: Health insurance provides coverage for hospitalization and medical treatments. Given the physical demands and long-term health risks associated with stone carving, having a comprehensive health insurance policy is essential.
Tool and Equipment Insurance: Carving tools are expensive, and their damage or loss can be costly for artisans. Tool and equipment insurance covers the repair or replacement of these essential items.
Product Insurance: Stone carvings, especially those being transported for sale or exhibition, may be damaged or destroyed en route. Product insurance ensures that artisans are compensated for any loss or damage to their works during transportation or storage.
Microinsurance: In many cases, stone carvers operate as part of the informal economy, making traditional insurance policies too expensive. Microinsurance policies, which offer affordable premiums, are designed for low-income artisans. In Odisha, schemes like the Pradhan Mantri Jeevan Jyoti Bima Yojana (PMJJBY) and Pradhan Mantri Suraksha Bima Yojana (PMSBY) offer low-cost life and accident insurance, helping to protect artisans in vulnerable financial situations.
Steps to Obtain Insurance
1. Identify Insurance Needs
Before purchasing insurance, artisans should assess their specific needs. Are they more concerned about personal health and injury, or the damage and loss of their work? Identifying these concerns will help choose the right type of insurance.
2. Research Insurance Providers
There are various public and private insurance providers that offer suitable policies. Some national providers include:
Life Insurance Corporation (LIC): Offers personal accident and health insurance policies.
Oriental Insurance: Provides coverage for personal accidents and tools.
National Insurance Company (NIC): Provides general insurance policies, including health, personal accident, and product insurance.
Local insurance agents in Odisha are also familiar with the specific needs of artisans and can help identify relevant policies.
3. Apply for Insurance
The application process varies by provider. Generally, artisans will need to fill out an application form, provide identification (such as an Aadhaar card or PAN card), and, in some cases, undergo a medical examination (for health insurance).
Government schemes, such as PMSBY, typically have simpler application processes and minimal documentation requirements. Microinsurance policies also have lower entry barriers.
4. Understand the Premiums and Coverage
Once the policy is chosen, it’s essential to understand the premiums and coverage limits. Government schemes typically offer affordable premiums starting as low as ₹12 annually for accident coverage under PMSBY. Comprehensive health or equipment insurance policies offered by private providers may have higher premiums, depending on coverage.
Government Initiatives and Support
The Government of Odisha has recognized the importance of protecting artisans and their crafts. Schemes like the Odisha State Cooperative Handicrafts Corporation (Utkalika) offer group insurance coverage to artisans. This helps to minimize costs, making insurance more accessible.
The Pradhan Mantri MUDRA Yojana (PMMY) also supports small artisans, including stone carvers, by offering credit to invest in their tools or business operations. While not insurance per se, these loans can complement insurance policies by providing financial stability.
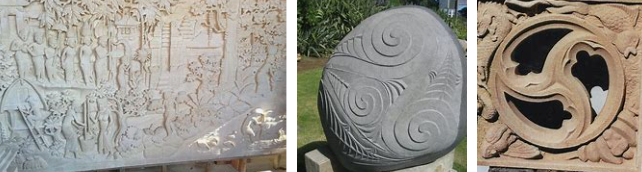
BUSINESS AUTHENTICITY IN STONE CARVING
Authenticity is a cornerstone of the stone carving industry, with customers increasingly concerned about the provenance and quality of the products they buy. Ensuring business authenticity not only builds consumer trust but also helps differentiate genuine artisans from mass-produced alternatives.
Certifications and Accreditation
Artisans can build trust by obtaining certifications or accreditation from recognized bodies. This can include government certification for handicrafts, eco-friendly certifications, or participation in artisan guilds or cooperatives that ensure fair trade and high-quality craftsmanship.
GI Tag (Geographical Indication): Odisha’s stone carvings, particularly from places like Khurda or Konark, may benefit from GI tags, which authenticate the origin and craftsmanship of the product, adding credibility in both domestic and international markets.
Transparency in Pricing and Processes
Providing transparency in pricing, material sourcing, and the carving process enhances authenticity. Customers appreciate knowing where the stone comes from, the time invested in the artwork, and the skill of the artisans involved.
Sustainable and Ethical Practices: Highlighting the use of ethical practices—such as sustainable sourcing of stones or fair wages for artisans—adds to the brand’s authenticity and appeals to socially-conscious consumers.
Building a Brand Story
Consumers are drawn to authentic brands that have a compelling narrative. Artisans can build a brand story around their work by emphasizing their heritage, craftsmanship, and the cultural importance of stone carving in Odisha. This emotional connection can help increase consumer loyalty and perceived value.
Challenges to Business Authenticity in Odisha's Stone Carving Industry
While authenticity is critical, there are several challenges that threaten the integrity of the stone carving industry in Odisha.
Commercialization and Mass Production: As demand for stone carvings has grown, particularly among tourists and global markets, there has been a tendency to commercialize the craft. Mass-produced, machine-made replicas are becoming more common, diluting the uniqueness and authenticity of traditional carvings. These replicas are often sold at lower prices, undercutting genuine handcrafted pieces. This trend not only jeopardizes the livelihoods of traditional artisans but also undermines the cultural value of the craft.
Imitation and Counterfeiting: With rising demand comes the risk of imitation products. Unauthentic stone carvings, often made with inferior materials or produced outside Odisha, are passed off as authentic Odishan artifacts. These counterfeit products deceive consumers and threaten the reputation of genuine artisans. The challenge lies in distinguishing between authentic handcrafted items and machine-made, inauthentic products.
Unethical Middlemen: In many cases, middlemen control the supply chain, purchasing carvings from artisans at low prices and selling them at a significant markup. Artisans, often unaware of the true value of their work, may not be compensated, while consumers unknowingly purchase products that do not represent fair trade practices. This lack of transparency in the supply chain diminishes the authenticity of the business.
Lack of Awareness Among Consumers: Many consumers, especially tourists, are not aware of the difference between authentic handcrafted stone carvings and mass-produced replicas. This lack of awareness allows counterfeiters and unethical traders to exploit the market, selling inauthentic goods at the same price as genuine artifacts.
Loss of Skilled Artisans: With fewer young people opting to learn the craft due to its labour-intensive nature and low financial returns, there is a danger of losing traditional skills. As the number of skilled artisans’ declines, the overall authenticity of the craft may be compromised, leading to a dilution of the art form.
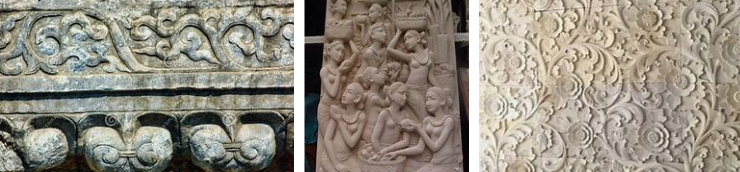
Ensuring Authenticity in Odisha’s Stone Carving Business
To combat these challenges and maintain business authenticity, various measures can be taken by the artisans, the government, and stakeholders in the industry.
Promotion of Traditional Techniques: Efforts should be made to protect and promote traditional stone carving techniques. Workshops, training programs, and schools can help pass down the craft to younger generations. Encouraging young artisans to take up stone carving while modernizing their business approach through digital marketing and online sales platforms can help sustain the craft.
Certification and Geographical Indications (GI): Establishing certification systems, such as a Geographical Indication (GI) tag for Odisha stone carvings, can help authenticate products. A GI tag certifies that the product originates from a specific region and possesses qualities or a reputation tied to that location. This not only helps protect artisans from counterfeiters but also reassures consumers that they are purchasing authentic, handcrafted goods.
The Government of India has already recognized GI tags for several crafts, and expanding this to stone carvings can provide a significant boost to the industry. A certified labelling system can also include details about the artisan, the techniques used, and the materials, giving consumers insight into the craft’s authenticity.
Fair Trade Practices: Implementing fair trade practices is essential to ensuring that artisans are paid fairly for their work and that consumers are aware of the product's ethical sourcing. Artisanal cooperatives and direct-to-market platforms can help eliminate exploitative middlemen, allowing artisans to have more control over pricing and the distribution of their products.
Consumer Education: Raising awareness among consumers about the value of authentic stone carvings and the differences between handmade and mass-produced items is crucial. This can be done through marketing campaigns, exhibitions, and storytelling. Consumers who appreciate the cultural significance of the craft are more likely to support authentic artisans. Online platforms can showcase the process of making stone carvings, from sourcing the stone to the final polish, highlighting the skill and effort involved.
Government and NGO Support: The government, along with non-governmental organizations (NGOs), can play a critical role in ensuring authenticity. By providing financial assistance, promoting GI tags, and organizing exhibitions, the government can help artisans showcase their work globally. NGOs can support artisans by providing training, advocating for fair wages, and helping artisans navigate the complexities of the market.
Digitalization and E-Commerce: To reach a broader market while maintaining authenticity, digital platforms can be utilized. Artisans can use e-commerce platforms to sell their products directly to consumers, allowing them to bypass middlemen and retain the integrity of their business. By sharing the stories behind the pieces and the artisans who make them, digital platforms can foster a direct connection between the artisan and the buyer, enhancing the perceived authenticity.
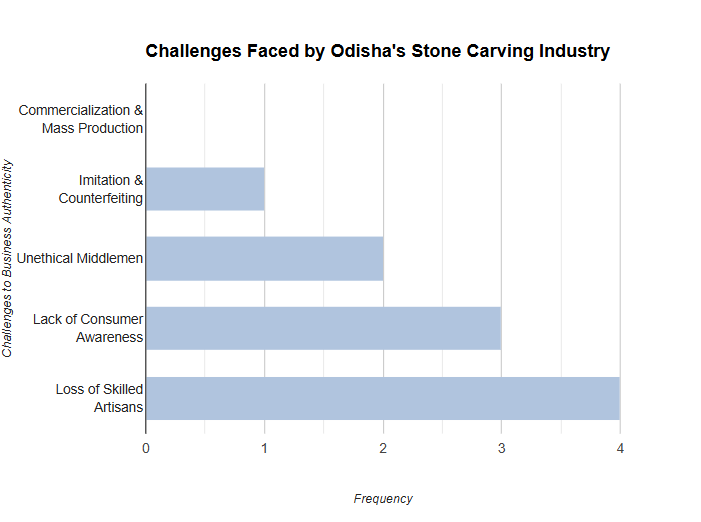
CURRENCY EXCHANGE IN STONE CARVING
In the stone carving industry, currency exchange plays a significant role in both the procurement of raw materials and the sale of finished products across international markets. Many high-quality stones, such as Carrara marble from Italy or limestone from France, are sourced from countries that use different currencies. When a stone carving company in India or the United States imports these materials, fluctuations in exchange rates between the local currency and the Euro can lead to unexpected cost increases. For instance, if the Euro strengthens against the Indian Rupee or US Dollar, the cost of importing the stone will rise, which may reduce the company's profit margins or force them to raise prices.
Similarly, companies that export stone carvings, sculptures, or architectural elements to international clients must also consider the impact of currency exchange. If a business exports custom stonework to the UK and receives payment in British pounds (GBP), they will need to convert that payment into their local currency. If the exchange rate moves unfavourably between the time of the transaction and when the funds are converted, the business could receive less money than expected, affecting their cash flow and overall financial stability. This is especially important in industries like stone carving, where projects are often large and payments can be substantial.
The process of currency exchange becomes important at various points in the business transaction:
Sales to Foreign Buyers: When an international buyer purchases a stone sculpture, the payment is often made in a foreign currency such as US Dollars (USD), Euros (EUR), or British Pounds (GBP). Artisans or businesses must then convert these payments into Indian Rupees (INR) to cover production costs and earn income.
Participation in International Exhibitions: Artisans frequently participate in international exhibitions and trade fairs to showcase their stone carvings. During these events, they may incur expenses such as booth rentals, accommodation, and shipping fees, all of which require payments in foreign currencies.
Purchasing Materials from Abroad: While most raw materials used in Odisha’s stone carving come from local sources, there are cases where artisans need to import specialized tools or materials, especially for contemporary designs. In such cases, payments to foreign suppliers involve currency exchange.
Currency Exchange Challenges in the Stone Carving Industry
Despite the opportunities for international trade, the currency exchange process in Odisha’s stone carving industry is not without challenges. Artisans and small businesses may face several hurdles when dealing with currency conversions.
Fluctuating Exchange Rates: One of the primary challenges of currency exchange is the fluctuation of exchange rates. Foreign exchange rates are determined by various factors, including economic conditions, geopolitical events, and central bank policies. Artisans or businesses relying on international buyers may see significant differences in their earnings based on how favourable or unfavourable the exchange rate is at the time of conversion. For instance, a weakening of the Indian Rupee (INR) relative to the US Dollar (USD) could increase the value of foreign sales when converted to INR. Conversely, if the rupee strengthens, artisans may find their earnings from foreign sales reduced.
High Transaction Costs: Currency exchange often comes with transaction fees, which can erode the profits of artisans. Banks, foreign exchange services, and online payment platforms charge fees for converting one currency to another. For artisans selling small quantities of sculptures or participating in occasional international events, these fees can represent a significant portion of their income. Artisans who rely on middlemen to facilitate currency exchanges may also face additional costs.
Access to Financial Services: Many artisans in Odisha's stone carving industry operate on a small scale and may lack access to formal financial services, making currency exchange more difficult. Artisans who are not familiar with banking systems or online platforms may rely on traditional, informal methods of currency exchange, which can be less efficient and more costly. Moreover, small-scale artisans often do not have bank accounts or PayPal-like services that facilitate smooth international transactions, limiting their ability to accept foreign payments.
Risk of Payment Delays: International transactions can sometimes involve delays in payments due to banking processes or differences in regulatory requirements between countries. For artisans operating on thin margins, delayed payments can disrupt cash flow and affect their ability to purchase materials or pay workers. This issue is particularly significant when artisans depend on international sales for a significant portion of their income.
Strategies for Effective Currency Exchange in the Stone Carving Industry
To overcome these challenges, artisans and businesses in Odisha’s stone carving industry need to adopt strategies that make the currency exchange process more efficient and cost-effective. Several steps can be taken to ensure smoother financial transactions and minimize the negative impact of fluctuating exchange rates and transaction fees.
Use of Online Payment Platforms: Platforms such as PayPal, Stripe, and Pioneer offer international payment solutions that are more accessible to small businesses and artisans. These platforms allow artisans to receive payments in foreign currencies, convert them to Indian Rupees, and withdraw funds to their local bank accounts. While these services do charge fees, they are often lower than traditional bank charges. Additionally, these platforms offer quicker access to funds, helping artisans manage their cash flow more effectively.
Foreign Exchange Risk Management: Larger businesses that engage in regular international trade can consider hedging strategies to manage currency risk. Hedging allows businesses to lock in exchange rates for future transactions, reducing the risk of unfavourable rate fluctuations. While this strategy may not be feasible for small-scale artisans, businesses with higher volumes of international trade can benefit from such financial instruments.
Collaborating with Export Organizations: Artisans can benefit from collaborating with export promotion organizations such as the Export Promotion Council for Handicrafts (EPCH) and Odisha State Handicrafts Corporation (OSHC). These organizations provide artisans with support for marketing their products internationally and facilitate smoother financial transactions by offering guidance on currency exchange and payment methods. Additionally, export organizations can negotiate better rates with financial institutions, lowering transaction costs for artisans.
Local Banks and Foreign Exchange Services: For artisans who are not familiar with online payment platforms, local banks can provide currency exchange services. Many banks in India offer specialized accounts for exporters, allowing artisans to hold foreign currencies and convert them when rates are favourable. Working with a trusted bank can also reduce the risk of payment delays and provide artisans with access to better financial planning tools.
Government Support and Training Programs: The government can play a critical role in educating artisans about currency exchange and providing access to financial services. Training programs that teach artisans how to use digital payment platforms, understand exchange rates, and manage international transactions can empower them to expand their businesses globally. Additionally, government policies that reduce transaction fees or provide incentives for exporting handicrafts can boost the competitiveness of Odisha’s stone carving industry in international markets.
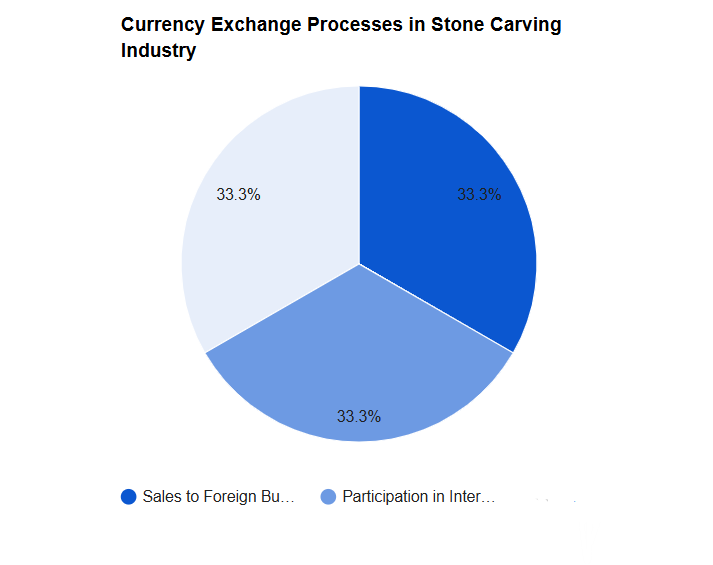
SUSTAINABILITY IN STONE CARVING
Sustainability in the stone carving industry has become increasingly important as businesses and consumers alike prioritize environmentally responsible practices. Stone carving, by nature, involves the extraction and processing of natural materials, which can have a significant impact on the environment. However, with the growing focus on sustainable development, many stone carving businesses are adopting eco-friendly practices to minimize their carbon footprint and promote responsible resource management.
Sustainable Sourcing of Materials
One of the key aspects of sustainability in stone carving is the ethical and sustainable sourcing of raw materials. The quarrying of natural stone, such as marble, granite, and limestone, can cause environmental degradation if not managed properly. To mitigate this, many businesses are now sourcing stone from quarries that follow sustainable practices, such as minimizing land disruption, using renewable energy in operations, and ensuring proper land reclamation after quarrying. Additionally, some companies are opting for locally sourced stone, which reduces the carbon footprint associated with long-distance transportation.
Example: A stone carving business might choose to source its marble from a quarry that follows stringent environmental regulations, such as reducing water usage, minimizing waste, and restoring natural habitats after extraction. By doing so, the business not only promotes sustainability but also appeals to eco-conscious customers.
Waste Reduction and Recycling
Stone carving processes, especially those involving large-scale production, generate a significant amount of waste in the form of stone chips, dust, and offcuts. Sustainable stone carving practices aim to reduce this waste by optimizing the use of raw materials and recycling leftover stone. Waste materials can often be repurposed for other products, such as gravel, aggregate, or smaller decorative pieces. Additionally, some businesses use advanced cutting technologies that minimize material loss, ensuring that each stone block is used as efficiently as possible.
Example: In a workshop where stone sculptures are created, the leftover fragments and dust from carving can be collected and processed into smaller decorative pieces or used in landscaping projects, reducing overall waste.
Energy Efficiency in Production
The stone carving industry, particularly in large-scale operations, requires significant energy for cutting, shaping, and finishing stone products. Sustainable practices focus on reducing energy consumption and using renewable energy sources whenever possible. For instance, businesses can invest in energy-efficient machinery or power their operations using solar or wind energy. By reducing energy use, stone carving businesses can lower their greenhouse gas emissions and contribute to a more sustainable production process.
Example: A company specializing in architectural stone carving might install solar panels to power its production facility, reducing its reliance on fossil fuels and lowering its carbon footprint.
Water Conservation
Water is commonly used in the stone carving process, particularly for cooling machinery and controlling dust during cutting and grinding. However, excessive water use can strain local resources and lead to environmental issues. Sustainable practices in the industry aim to reduce water consumption by implementing closed-loop water systems, which recycle water used during the carving process. Additionally, using dust suppression systems that require minimal water can help reduce overall water usage.
Example: A stone carving facility might use a water recycling system that captures and reuses water during the cutting and polishing process, reducing the need for fresh water, and minimizing waste.
Eco-Friendly Finishes and Sealants
The finishes and sealants applied to stone products can have an environmental impact, especially if they contain harmful chemicals or pollutants. Sustainable stone carving involves using eco-friendly, non-toxic sealants and finishes that do not release harmful emissions during production or use. These green alternatives help reduce the environmental footprint of the final product while ensuring that the stone remains durable and aesthetically pleasing.
Example: A stone sculptor might use natural or water-based sealants to protect the surface of the stone, avoiding the use of volatile organic compounds (VOCs) that can harm the environment and human health.
Sustainable Design and Lifespan
Sustainability in stone carving also extends to the design and intended lifespan of the final product. Stone is a highly durable material, and when used responsibly, it can contribute to sustainable architecture and long-lasting sculptures that require minimal maintenance. By focusing on quality craftsmanship and timeless design, stone carving businesses can create products that stand the test of time, reducing the need for frequent replacements and contributing to a more sustainable built environment.
Example: A stone carver creating a public monument might focus on a design that will endure both aesthetically and structurally for generations, ensuring that the piece remains a sustainable fixture in the community.
Social and Economic Sustainability
In addition to environmental considerations, sustainability in stone carving also encompasses the well-being of artisans and workers. Ethical labour practices, fair wages, and safe working conditions are essential to ensuring the long-term sustainability of the industry. Businesses that invest in their workforce by providing training, health benefits, and safe work environments contribute to the social sustainability of the industry and foster a more resilient and skilled artisan community.
Example: A company might ensure that all artisans involved in the carving process receive fair compensation, safe working conditions, and access to ongoing training, helping to preserve the traditional craftsmanship of stone carving while supporting the livelihoods of workers.
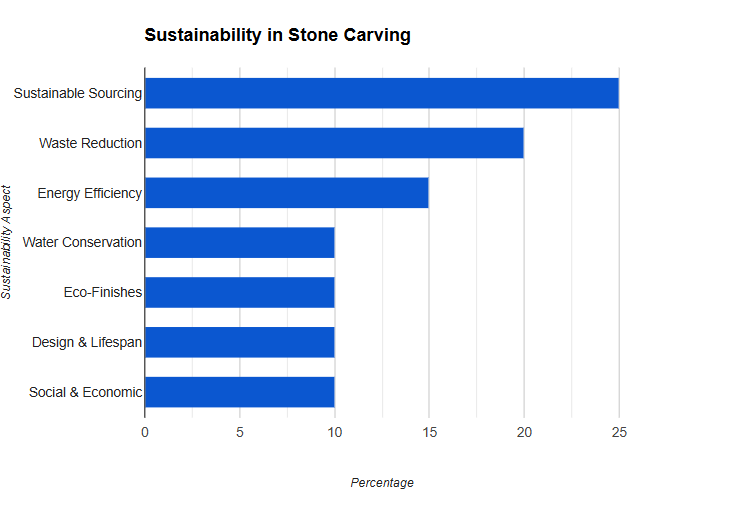
SHIPPING COST IN STONE CARVING
Shipping costs are a critical consideration for the stone carving industry, especially when exporting products to international markets. These costs include expenses for transportation, handling, insurance, and customs duties. The size, weight, and fragility of stone carvings can significantly impact shipping costs, with larger and heavier items generally incurring higher fees. To manage shipping expenses, businesses can explore options such as bulk shipping or consolidating orders to reduce per-unit costs. Choosing reliable shipping partners and negotiating rates based on shipping volume can also help minimize expenses. Additionally, optimizing packaging to ensure that products are securely packed and less prone to damage during transit can prevent costly losses and claims. Businesses should also be aware of potential customs duties and import taxes in destination countries, as these can affect the overall cost of shipping. By carefully managing shipping logistics and costs, the stone carving industry can enhance profitability and competitiveness in the global market.
Below is a detailed analysis of shipping costs in the stone carving industry, supported by relevant data.
Weight and Volume Considerations
Stone, particularly materials like marble, granite, and sandstone, is heavy and dense, making the cost of shipping based largely on weight and volume. For example, granite weighs around 170 pounds per cubic foot (about 2,720 kg per cubic meter). The heavier the stone, the higher the cost of transportation.
Data Example: A typical shipping container (20-foot equivalent unit or TEU) can hold about 21-27 tons of stone, depending on how the material is packed. If shipping costs average around $1,000 to $2,000 for a container (depending on the route), each ton of stone could add $37 to $95 to the shipping cost alone.
Shipping Distance
The distance between the quarry, the carving site, and the customer also plays a significant role in determining shipping costs. Longer distances, particularly those involving international routes, increase transportation costs due to fuel consumption, handling fees, and the need for multi-modal transport (e.g., trucks, ships, trains).
Data Example: The cost of shipping stone from India (a major exporter of granite) to the United States via ocean freight can vary between $1,800 and $4,000 for a 20-foot container depending on the port and demand. For European markets, the cost might be lower, ranging between $1,200 and $2,000 for similar shipments.
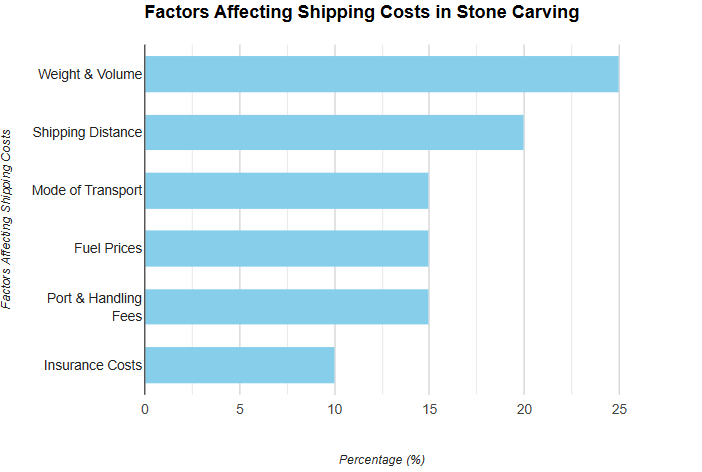
Mode of Transport
The mode of transport—whether by sea, air, rail, or truck—greatly impacts shipping costs. For the stone carving industry, sea freight is the most common for long-distance, bulk shipments due to its cost-effectiveness compared to air freight. Air shipping is far more expensive but can be necessary for urgent or smaller deliveries.
Data Example: While sea freight might cost $1,800 for a 20-foot container, the same shipment by air freight could cost up to $10,000 or more, depending on weight and destination, making it prohibitively expensive for most stone carving businesses.
Fuel Prices and Surcharges
Fluctuations in fuel prices directly affect shipping costs. When fuel prices rise, shipping companies typically add fuel surcharges to offset the additional cost. These surcharges can fluctuate monthly, impacting the overall cost of transporting stone.
Data Example: According to recent shipping reports, fuel surcharges can add between 5% to 20% to the base shipping cost, depending on the shipping route and the mode of transport. For instance, if the base cost of shipping is $2,000, a 10% fuel surcharge would add $200, bringing the total to $2,200.
Port and Handling Fees
Port fees, customs duties, and other handling costs also contribute significantly to the total shipping cost. Stone, being a heavy and often fragile material, requires careful loading and unloading, which adds to the handling charges at both the origin and destination ports.
Data Example: Handling fees for stone can range between $100 and $500 per container, depending on the port’s infrastructure and the handling requirements. Additionally, customs duties vary by country, with import duties ranging from 5% to 15% of the shipment's value, further increasing the total cost of shipping.
Insurance Costs
Due to the high value and fragile nature of stone products, many businesses opt for cargo insurance to protect against damage during transit. Insurance premiums are typically calculated as a percentage of the shipment’s value and add to the total cost of shipping.
Data Example: Cargo insurance can range from 0.5% to 1.5% of the shipment’s declared value. For a shipment valued at $50,000, the insurance cost might range from $250 to $750.
Current Shipping Trends and Challenges
Recently, the global shipping industry has experienced significant disruptions due to the COVID-19 pandemic, geopolitical tensions, and supply chain bottlenecks, which have led to record-high shipping costs. These challenges have particularly affected industries like stone carving that rely on international transport for both raw materials and finished products.
Data Example: In 2021 and 2022, shipping container rates soared to over $10,000 for routes between Asia and Europe or North America, compared to pre-pandemic rates of $1,500 to $2,000 per container. Though rates have since declined, they remain volatile due to global economic uncertainty.
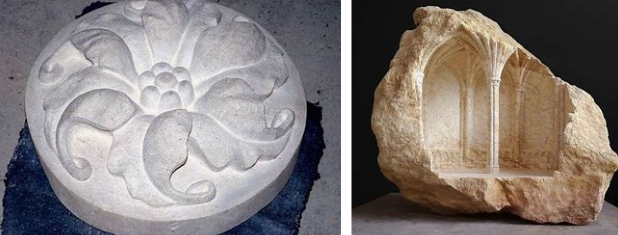
CONCLUSION
Stone carving in Odisha is not just a craft; it is an enduring symbol of the state's rich cultural and artistic heritage. From the awe-inspiring sculptures of Konark’s Sun Temple to the intricate idols and architectural marvels found in temples across the state, this ancient tradition has continued to captivate and inspire for centuries. The skill and craftsmanship involved in stone carving have been passed down through generations of artisans, making it a vital part of Odisha’s identity and economy.
Despite its significance, the stone carving industry in Odisha faces numerous challenges. These include fluctuating demand, the threat of mass-produced replicas, and economic vulnerabilities. Artisans often work in difficult conditions, struggling with inconsistent incomes and exposure to occupational hazards. Yet, the industry’s resilience is a testament to the dedication of its craftsmen, who continue to create masterpieces with basic tools, showcasing their remarkable skill and precision.
Efforts to preserve this heritage through modern interventions, such as government schemes, training programs, and the promotion of authentic products, are crucial to its survival. Certification systems like the Geographical Indication (GI) tag for Odisha’s stone carvings can help ensure authenticity and protect artisans from the proliferation of imitations. Furthermore, access to global markets, facilitated by e-commerce platforms, offers new opportunities for growth. However, for these efforts to succeed, it is essential that artisans receive adequate support in terms of financial security, health benefits, and fair wages.
The future of Odisha’s stone carving lies in a balanced approach that respects tradition while embracing innovation. By modernizing marketing strategies, promoting authenticity, and improving working conditions, the industry can secure its place in the contemporary world. If these steps are taken, the art of stone carving in Odisha will continue to thrive, preserving the state’s cultural legacy and providing a sustainable livelihood for generations of artisans to come.
BIBLIOGRAPHY
Stone Carving – Directorate of Handicrafts (odisha.gov.in)
Stone carving in Odisha - Wikipedia
Recommended
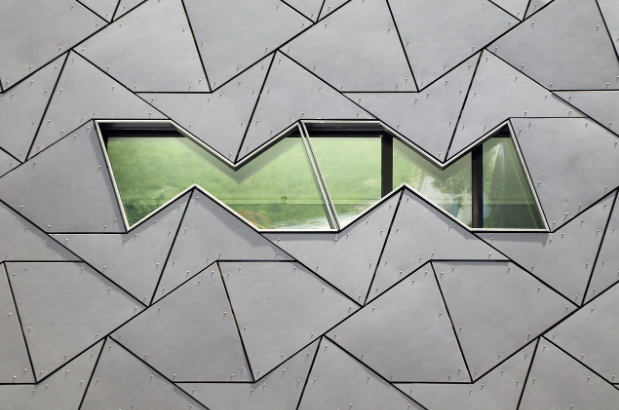

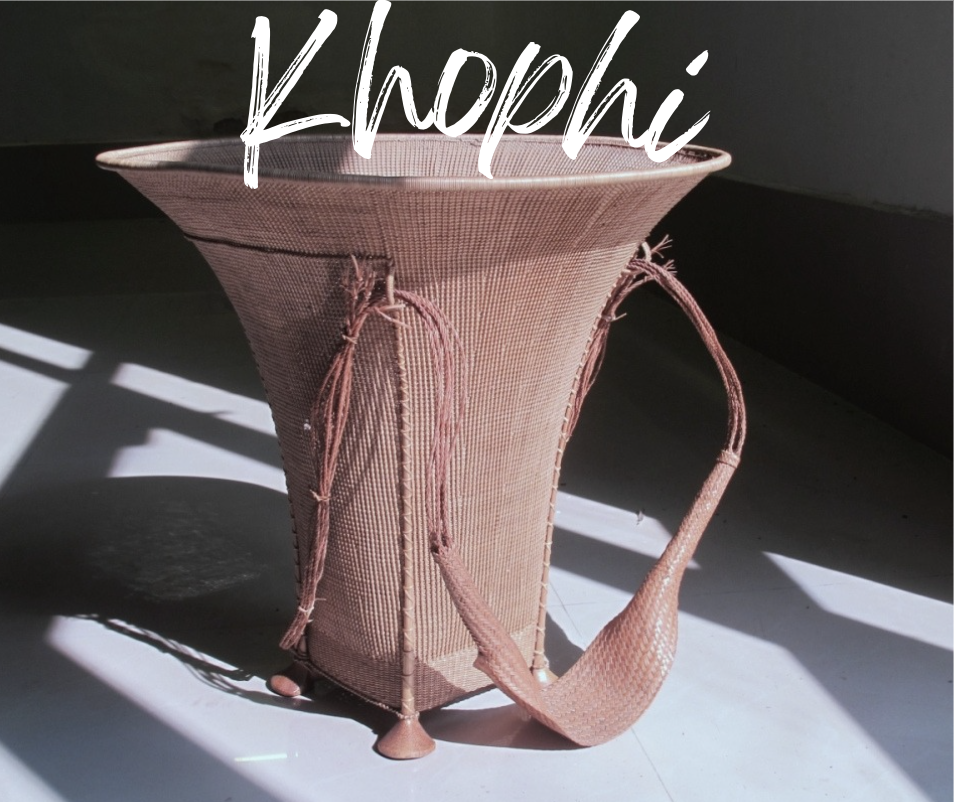