Rethinking The Workflow In Creative Manufacturing And Handmade Industry
Sep 29, 2023 | Raj Pushilal
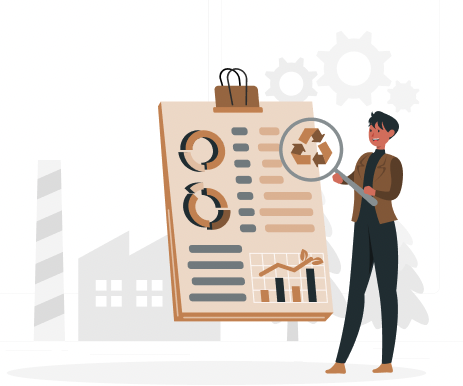
Leather Industry
The normal process of manufacturing and daily workflow in a Leather Industry
1. Raw Material Selection
2. Preparatory Stage
3. Tanning
4. Finishing
5. Product Manufacturing
6. Distribution and Retail
My Own Strategies to make it more efficient and reduce costs
1. Automation and Robotics:
• Implement automated machinery and robotics in various stages of the manufacturing process, such as cutting, stitching, and assembling.
• This can reduce labor costs, increase production speed, and improve accuracy in repetitive tasks.
• Advanced robotic systems can also handle complex processes like embossing or surface treatments.
2. Lean Manufacturing Principles:
• Apply lean manufacturing principles to identify and eliminate waste throughout the process.
• Streamline workflows, reduce excess inventory, optimize material handling, and minimize non-value-added activities.
• Use tools like value stream mapping to visualize and analyze the process, identifying areas for improvement.
3. Supply Chain Optimization:
• Improve coordination and communication with suppliers to ensure a steady supply of high-quality raw materials.
• Establish long-term relationships and negotiate favorable pricing and delivery terms.
• Implement just-in-time inventory practices to reduce storage costs and waste.
4. Energy Efficiency and Sustainability:
• Incorporate energy-efficient technologies and processes to reduce energy consumption and lower utility costs.
• Explore renewable energy sources and eco-friendly practices, such as utilizing solar power or adopting water recycling systems.
• Embrace sustainable tanning methods and chemicals, reducing environmental impact while meeting customer demands.
5. Digitalization and Data Analytics:
• Implement digital technologies like enterprise resource planning (ERP) systems and manufacturing execution systems (MES) to integrate and streamline operations.
• Utilize data analytics to gain insights into process performance, identify bottlenecks, and make data-driven decisions for optimization.
• Employ predictive maintenance techniques to minimize equipment downtime and improve productivity.
6. Cross-Training and Skill Development:
• Encourage cross-training of employees to enhance flexibility and versatility in the workforce.
• Ensure that employees have a diverse skill set, enabling them to handle multiple tasks and roles as needed.
• Invest in continuous training programs to improve employee skills and knowledge, promoting a culture of innovation and improvement.
7. Collaborative Partnerships:
• Foster collaborative partnerships with research institutions, industry experts, and technology providers.
• Engage in research and development activities to explore new materials, technologies, and process innovations.
• Participate in industry forums and conferences to stay updated on the latest trends and best practices.
Stone Craft Industry
Daily process of manufacturing and workflow in a Stone Craft Industry
1. Raw Material Selection
2. Extraction and Quarrying
3. Stone Cutting and Shaping
4. Surface Finishing
5. Fabrication and Assembly
6. Surface Treatment and Protection
7. Quality Control and Inspection
8. Packaging and Distribution:
My Own Strategies to make it more efficient and reduce costs
1. 3D Scanning and Digital Modeling:
• Utilize 3D scanning technology to capture accurate measurements and digital representations of stone blocks and designs.
• Create virtual models of products and simulate the manufacturing process to optimize material usage and reduce waste.
• Digital modeling allows for precise planning and visualization, minimizing errors and rework during fabrication.
2. Robotic Stone Cutting and Carving:
• Integrate robotic systems for stone cutting and carving processes, reducing manual labor and increasing precision.
• Robotic arms equipped with advanced cutting tools and sensors can perform intricate designs with high accuracy and efficiency.
• Automated systems can also handle repetitive tasks, improving production speed and consistency.
3. Waterjet Cutting and Abrasive Machining:
• Implement waterjet cutting technology, which utilizes high-pressure water mixed with abrasives to cut and shape stone.
• Waterjet cutting offers precise and intricate cuts, reducing material waste and enabling complex designs.
• This method reduces energy consumption compared to traditional cutting techniques and minimizes the need for subsequent shaping processes.
4. IoT-enabled Production Monitoring:
• Install sensors and IoT devices throughout the manufacturing facility to monitor and collect real-time data on production parameters.
• Use data analytics to optimize machine utilization, identify bottlenecks, and predict maintenance needs.
• Proactive monitoring and analysis help minimize downtime, enhance productivity, and reduce overall production costs.
5. Water Recycling and Filtration:
• Implement water recycling and filtration systems to reduce water consumption and minimize environmental impact.
• Recirculating water used in cutting, grinding, and polishing processes can significantly reduce water usage and wastewater generation.
• Advanced filtration systems can remove sediment and impurities from water, allowing its reuse in the manufacturing process.
6. Lean Production Principles:
• Apply lean production principles to streamline workflows, eliminate waste, and optimize resource allocation.
• Conduct value stream mapping to identify non-value-added activities and improve process efficiency.
• Embrace concepts like Just-in-Time manufacturing to reduce inventory holding costs and increase responsiveness to customer demands.
7. Energy-efficient Equipment and Lighting:
• Upgrade to energy-efficient machinery and lighting systems to reduce electricity consumption.
• Opt for modern equipment with improved energy efficiency ratings and utilize LED lighting for better energy management.
• Implement motion sensors or timers to automatically control equipment and lighting usage, reducing energy waste.
8. Collaborative Partnerships and Knowledge Sharing:
• Foster collaborations with technology providers, research institutions, and industry experts.
• Stay updated on the latest advancements in stone cutting, fabrication, and finishing techniques.
• Participate in knowledge-sharing initiatives and industry conferences to gain insights and implement best practices.
Recommended
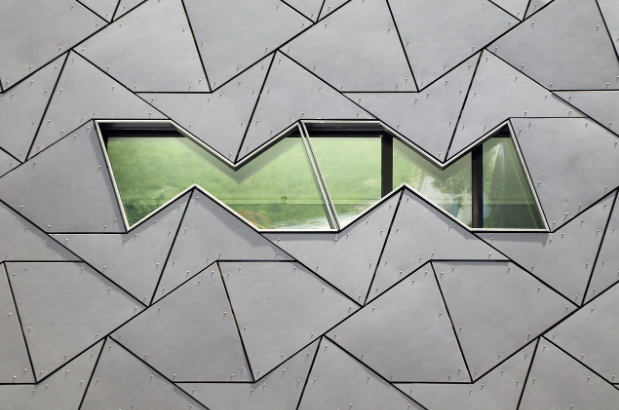

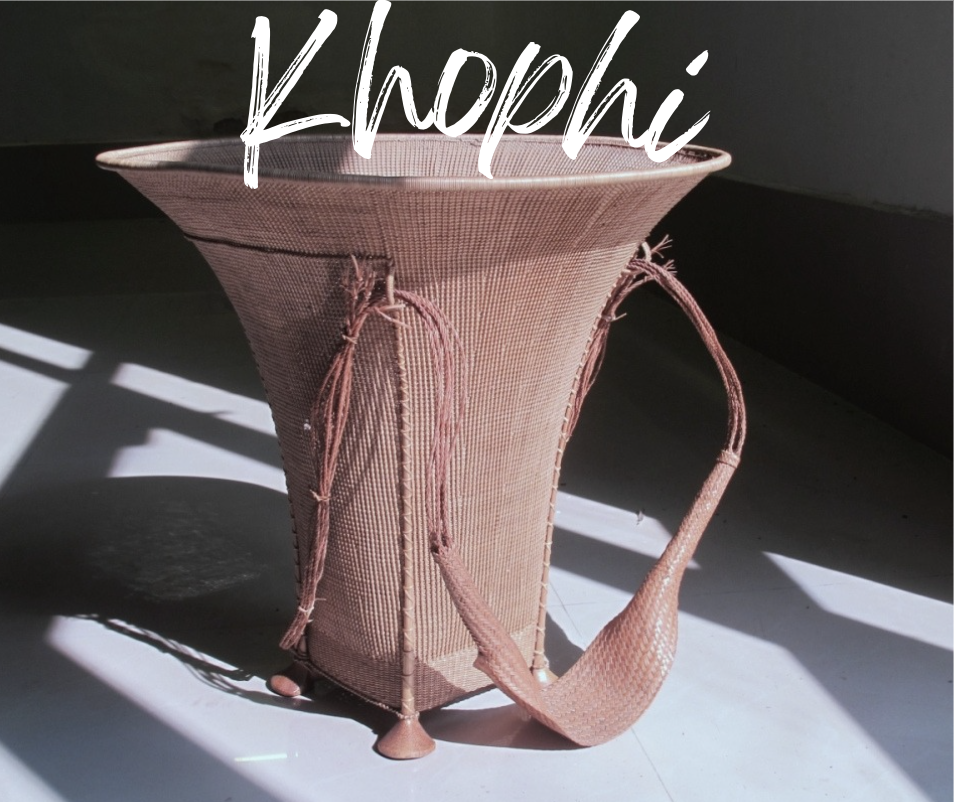