Wholesale Rosewood Inlay Work from Mysore: Premium Craft for B2B Buyers
Nov 23, 2024 | Udit Kaur
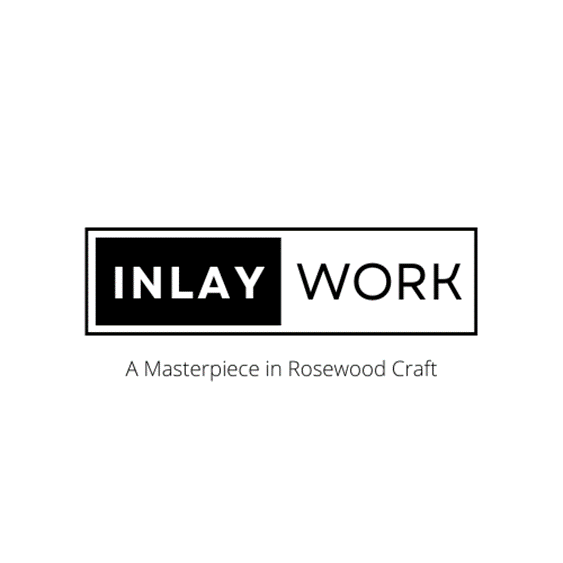
1. A Glimpse into the History of Rosewood Inlay Work in Mysore
Rosewood inlay work, with its origins traced back to Persia, arrived in India in the 18th century. It flourished in Srirangapatinam under the reign of Tipu Sultan, whose fondness for intricate woodwork helped it gain prominence. Over time, this craft moved to Mysore, where it found a more permanent home. The artwork often features themes of Indian mythology, including scenes from the Ramayana and Mahabharata, alongside depictions of royal processions and serene landscapes.
Historically, this craft was a favorite among Maharajas, who commissioned elaborate ivory motifs on rosewood. Although ivory is no longer used, the traditional techniques remain intact, and artisans continue to create intricate designs using various shades of rosewood. Today, this art form is not just a relic of the past but a thriving craft, thanks to the efforts of the Karnataka State Handicrafts Development Corporation (KSHDC).
2. The Role of Karnataka State Handicrafts Development Corporation (KSHDC) in Preserving Inlay Work
Established in 1964 by the Government of Karnataka, KSHDC was created to preserve and promote traditional crafts, including rosewood inlay work. By offering training and employment opportunities, KSHDC helps artisans modernize their skills and adapt to changing market trends. One of the corporation's most significant initiatives is the Cauvery brand, which markets high-quality handicrafts, including inlay work, across India. Through Cauvery, KSHDC ensures that the legacy of Mysore’s inlay work continues to thrive, both in local markets and internationally.
3. The Unique Appeal of Mysore Rosewood Inlay Work
Mysore's inlay work stands out due to its intricate craftsmanship and the variety of materials used. Unlike inlay work from other regions, which might focus solely on wood, Mysore artisans incorporate elements like shells, flip boards, and even brass into their designs. The use of different wood shades to create contrasting highlights and shadows gives depth and dimension to the pieces. The patterns are not only aesthetically pleasing but also deeply symbolic, often reflecting religious themes or the natural world. This craft's ability to create such vibrant yet intricate artwork has made it a favorite among collectors and art enthusiasts.
4. Tools and Raw Materials Used in Rosewood Inlay Work
A variety of tools and raw materials are required to achieve the precision and beauty characteristic of Mysore inlay work. Below are the essential materials and tools used in this craft:
Rosewood: The primary material used, rosewood is prized for its strength, durability, and rich, dark color.
Plywood: This is often used as the base frame for the inlay, providing stability and structure to the piece.
Wax and Charcoal: A mixture of these is used for detailing, filling in grooves, and giving the piece a polished finish.
Chisels: These are used to carve intricate designs into the wood, helping artisans achieve fine detailing.
Hex Saw: Used for cutting both the rosewood and other materials that are incorporated into the design.
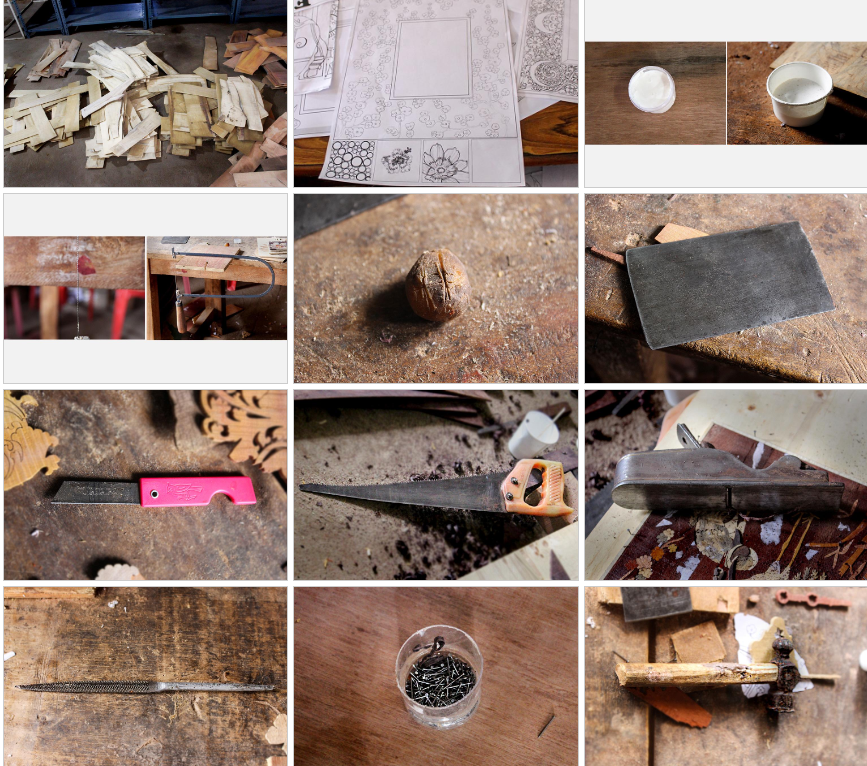
Each tool and material plays a crucial role in the intricate process of creating inlay works, helping artisans bring their designs to life with precision and flair.
5. The Step-by-Step Process of Creating Rosewood Inlay Work
The process of creating rosewood inlay work is both labor-intensive and requires exceptional skill. Here's a breakdown of the stages involved:
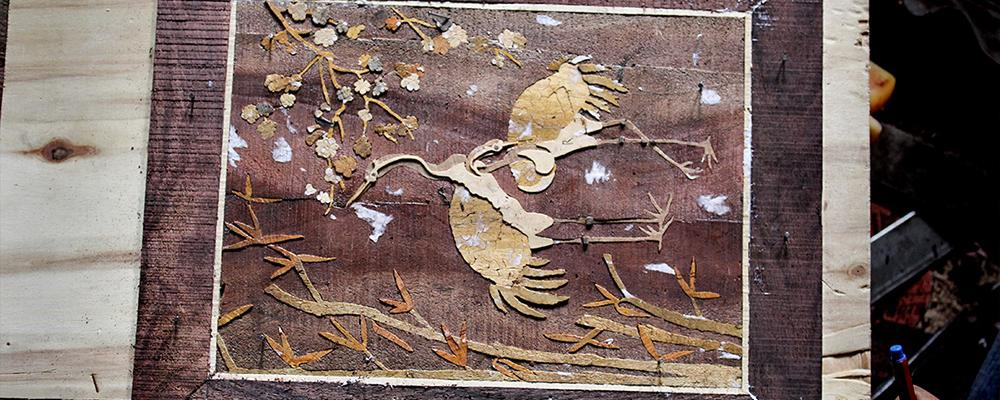
a. Designing and Tracing
The process begins with the artisan sketching the design on paper. This design, often featuring multiple patterns, is then copied several times. The copies are used as tracing material that will guide the artisan as they work on the wood.
b. Cutting and Shaping
The next step involves placing the tracing on a rosewood plank and carefully cutting the shapes using a coping saw. The excess wood is trimmed away, and each individual piece of the design is prepared. Artisans use a vertical saw to cut straight lines within the design, ensuring precision and accuracy.
c. Gluing and Setting
Once all the individual pieces are cut, they are nailed together and glued onto the main woodblock. Excess glue is removed, and any gaps in the design are filled with dust or fillers. This step is crucial for achieving a seamless look.
d. Detailing and Finishing
The final details are added using a chisel to create grooves and other intricate patterns. A mixture of molten wax and charcoal is applied to the workpiece for a polished finish. Afterward, the entire piece is scraped to achieve a smooth, flawless surface. The result is a stunning piece of art, showcasing the precision and skill of the artisans.
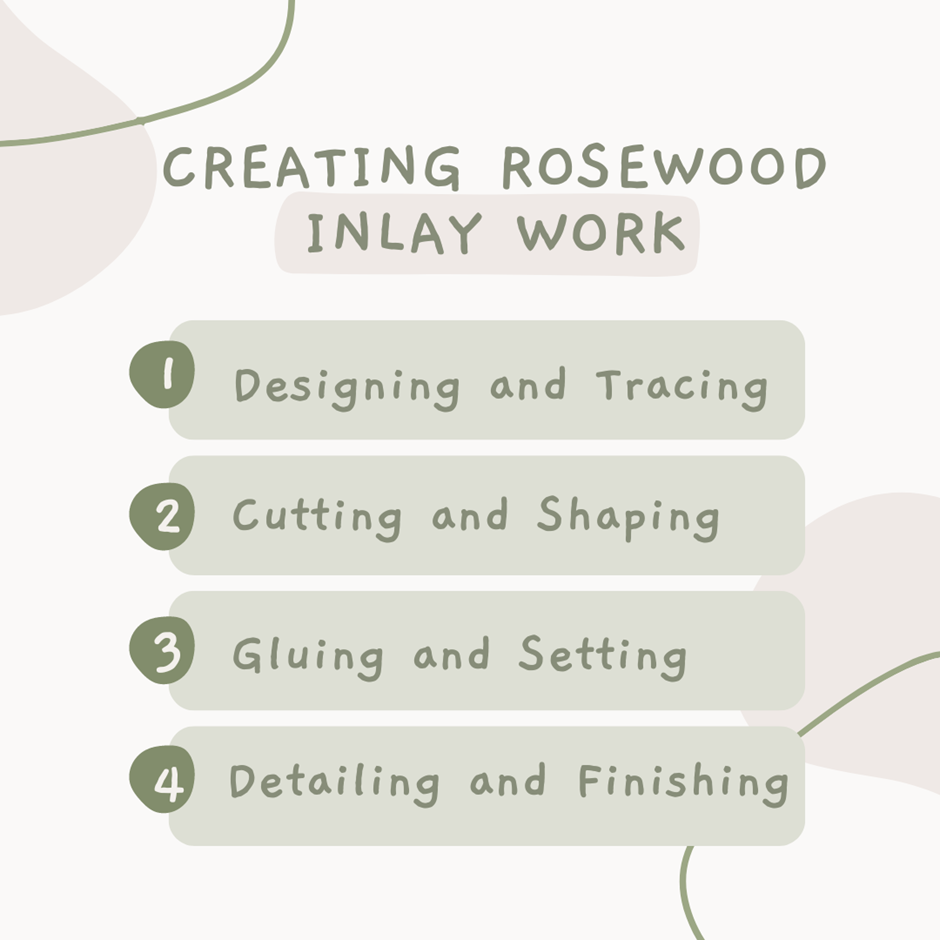
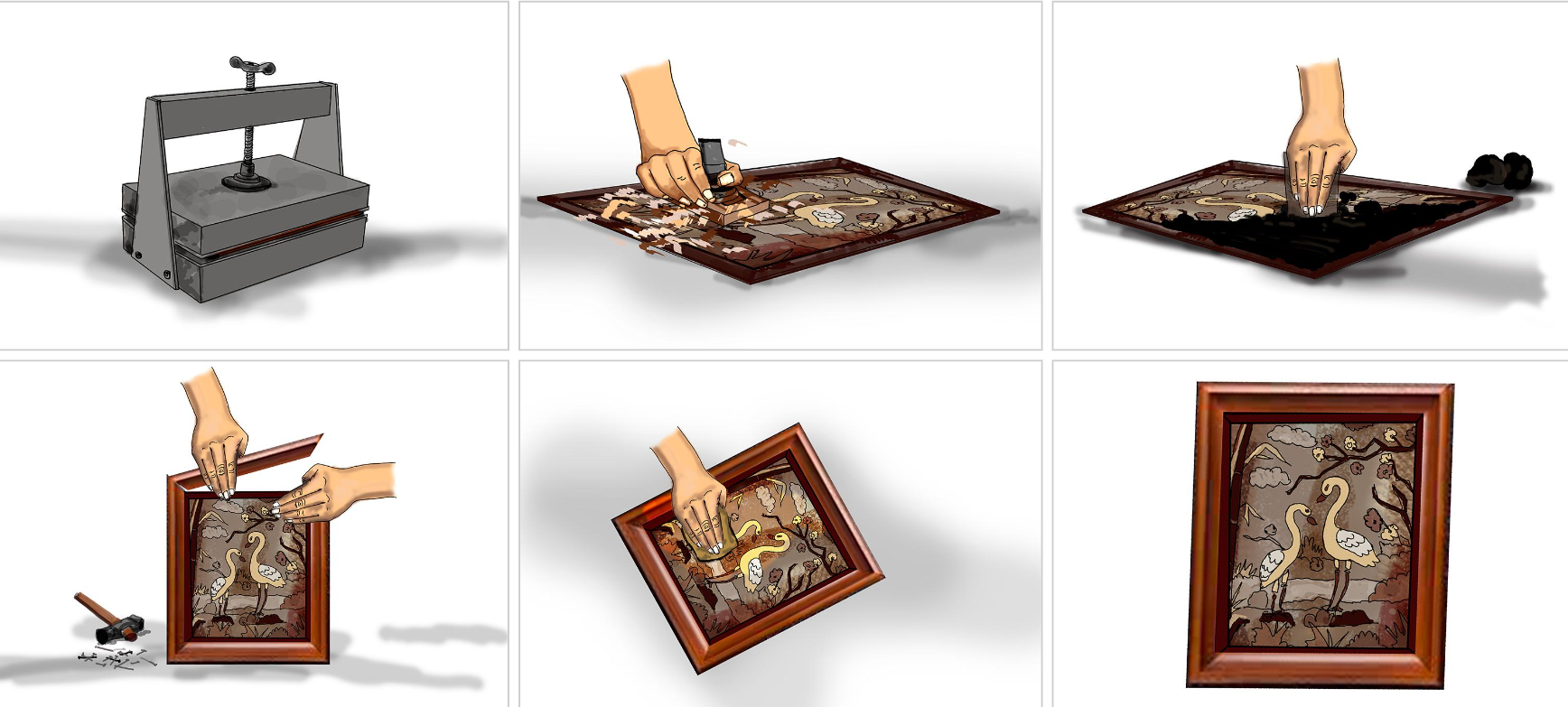
6. Diverse Products of Mysore Inlay Work
The versatility of Mysore's inlay work allows artisans to create a wide range of products. Some of the most popular items include:
Wall Panels: These often depict mythological stories, royal processions, or nature scenes.
Furniture: Tables, doors, and dining sets adorned with inlay work are prized for their beauty and craftsmanship.
Gift Boxes: These decorative boxes are popular souvenirs, often featuring intricate floral or geometric designs.
Mirror Frames: Combining utility with art, these frames are a popular choice for home decor.
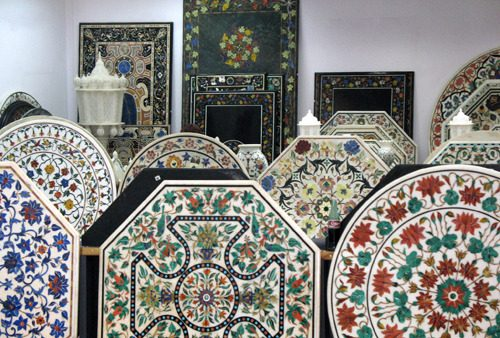
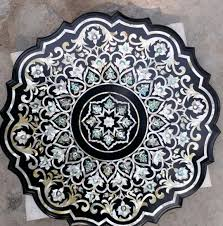
One of the main production centers for Mysore inlay work is located in Karnataka, where artisans create these products, often for trade in cities like Mumbai, Pune, and Aurangabad. The craft not only preserves cultural heritage but also provides employment opportunities for many skilled artisans.
7. The Cultural and Economic Importance of Mysore’s Inlay Craft
Rosewood inlay work is more than just an art form; it is a vital part of Karnataka’s cultural and economic landscape. The craft offers artisans a way to sustain their livelihood while preserving a centuries-old tradition. Mysore inlay work has earned national and international recognition, often featured in exhibitions and trade shows that highlight India’s rich craft heritage. The government’s efforts to promote the craft through initiatives like KSHDC and the Cauvery brand have played a crucial role in sustaining this art form, allowing it to adapt to modern markets without losing its traditional charm.
Here are the key points summarizing the cultural and economic importance of Mysore’s inlay craft:
Cultural Significance: Mysore’s rosewood inlay work is a centuries-old tradition, integral to Karnataka’s cultural heritage.
Economic Importance: The craft provides a sustainable livelihood for artisans, supporting local economies.
National and International Recognition: Mysore inlay work is widely recognized, often showcased in exhibitions and trade shows that highlight India’s rich craft heritage.
Government Support: Initiatives by the Karnataka State Handicrafts Development Corporation (KSHDC) and the Cauvery brand have played a key role in promoting and preserving the craft.
Adapting to Modern Markets: While maintaining its traditional charm, the craft has adapted to meet the demands of contemporary markets.
Craft Heritage Preservation: Continued efforts ensure that the craft remains relevant while safeguarding its cultural roots.
These points highlight the craft's dual role in preserving tradition and supporting economic growth.
8. Adapting to Modern Market Trends
While traditional designs still hold great value, Mysore inlay work has adapted to suit modern tastes and trends. Artisans now create contemporary designs that appeal to younger generations while still maintaining the traditional craftsmanship. This fusion of old and new ensures the survival of the craft in a rapidly changing world. Training programs offered by KSHDC have helped artisans stay up-to-date with market demands, teaching them how to create new designs while preserving the integrity of the art.
Ensuring Craft Survival in a Changing World
In today’s fast-paced market, staying relevant while preserving the authenticity of your craft can be challenging. However, as seen in the success of Mysore’s inlay work, it is possible to blend tradition with modern trends. Here are some strategies artisans and businesses can use to stay ahead:
Understand Market Demands: Research current market trends regularly to understand what your target audience prefers. Whether it’s incorporating minimalist designs, eco-friendly materials, or customizable products, knowing customer preferences is key to staying relevant.
Innovate While Preserving Tradition: Like Mysore artisans who blend traditional craftsmanship with modern designs, find ways to innovate without compromising the essence of your craft. This could mean experimenting with contemporary color schemes, incorporating new motifs, or modifying product sizes to appeal to a wider audience.
Leverage Training and Development: Participating in skill development programs or workshops can help artisans stay current with new techniques. Just as KSHDC offers programs for Mysore inlay workers, look for opportunities in your field that teach new methods while respecting traditional craftsmanship.
Collaborate with Younger Generations: Appeal to younger markets by involving the next generation of artisans or designers. They bring fresh ideas and understand current trends, making it easier to introduce modern elements without losing authenticity.
Utilize Digital Marketing: In a digitally driven world, having an online presence is crucial. Use social media platforms, e-commerce websites, and digital marketing strategies to promote your products. Showcasing your craft’s unique combination of tradition and modernity can attract a global audience.
Adapt to Consumer Preferences: Pay attention to emerging consumer trends like sustainability and customization. Offer products made from eco-friendly materials or customizable options that reflect the buyer’s personal taste. This appeals to conscious consumers and makes your craft more versatile.
Participate in Exhibitions and Trade Shows: Like Mysore inlay work gaining visibility through exhibitions, use craft fairs, trade shows, and online platforms to showcase your work. This helps you gain insight into what is trending and how your craft can evolve to meet new demands.
Seek Government or Organizational Support: Look for programs or funding from government bodies or organizations that support artisans and craftsmen. These can offer resources, marketing assistance, or product development guidance that can keep your business in sync with modern market needs.
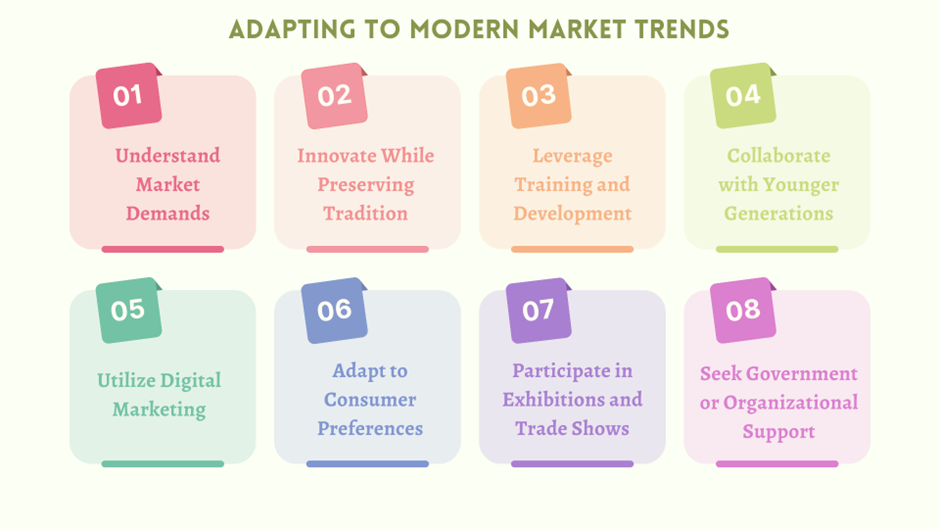
By following these steps, your readers can effectively bridge the gap between tradition and modernity, ensuring their craft not only survives but thrives in today’s competitive market.
9. Sustainability and Ethical Practices in Mysore Inlay Work
Sustainability is a growing concern in the world of handicrafts, and Mysore’s rosewood inlay work is no exception. Artisans and organizations are increasingly focusing on sustainable practices, such as sourcing rosewood from certified plantations and using eco-friendly materials in the production process. Ethical labor practices are also a priority, ensuring fair wages and working conditions for artisans. By adopting these practices, Mysore’s inlay work not only remains relevant but also aligns with the growing demand for ethical and sustainable products in the global market.
In response to global demands for eco-friendly and ethically produced goods, Mysore’s rosewood inlay craft has integrated several sustainable and ethical practices. These measures not only preserve the environment but also ensure the well-being of artisans. Here’s how Mysore inlay work is aligning with these principles:
Sourcing from Certified Plantations: Rosewood, the primary material used, is now sourced from government-approved, certified plantations that follow responsible forestry practices. This helps protect natural ecosystems and prevents illegal logging.
Use of Eco-Friendly Materials: In addition to rosewood, artisans are incorporating alternative eco-friendly materials like recycled wood and natural adhesives. These efforts reduce the environmental impact and promote sustainability.
Minimizing Waste: Artisans are adopting practices to minimize waste during the crafting process, ensuring that even the smallest pieces of wood are utilized, either in the inlay process or in creating smaller decorative items.
Promoting Handcrafted, Low-Impact Production: The inlay process is predominantly handcrafted, which minimizes reliance on heavy machinery and lowers carbon emissions. This low-impact production method supports eco-friendly initiatives and reduces energy consumption.
Ethical Labor Practices: Fair wages and safe working conditions are now a priority in the production process. Artisans receive proper compensation for their work, along with access to skill development programs and better working conditions.
Preserving Traditional Knowledge: Sustainability goes beyond materials—it includes preserving the knowledge and cultural heritage associated with Mysore inlay work. Artisans pass down their skills to younger generations, ensuring the craft's survival without compromising its essence.
Use of Non-Toxic Dyes and Finishes: Non-toxic dyes and finishes are used to enhance the appearance of the inlay work, making it safer for both artisans and customers. This eliminates harmful chemicals from the production process.
Collaboration with Ethical Organizations: Artisans and local cooperatives often collaborate with organizations that focus on fair trade practices, ensuring that products meet international sustainability and ethical standards.
Educating Consumers: Efforts are made to educate consumers about the sustainable and ethical nature of Mysore inlay work. This transparency appeals to buyers who prioritize environmentally conscious and socially responsible purchases.
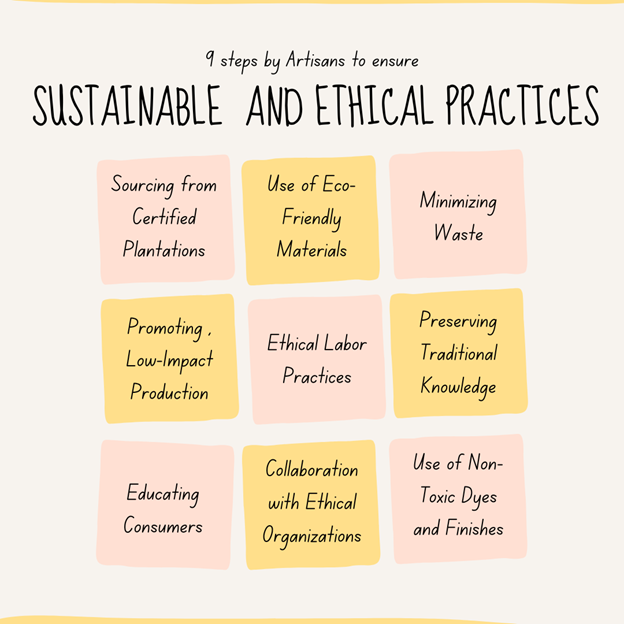
By embracing these practices, Mysore's inlay artisans are contributing to a sustainable future while maintaining the integrity and beauty of their centuries-old craft.
10. Why Mysore Rosewood Inlay Work is a Must-Have for Art Collectors
Collectors and art enthusiasts from around the world have come to appreciate the unique appeal of Mysore’s rosewood inlay work. Each piece tells a story, whether it’s a scene from Indian mythology or a serene landscape. The level of detail, the use of contrasting wood tones, and the rich history behind the craft make it a must-have for anyone looking to invest in authentic Indian art. The fact that each piece is handmade and one-of-a-kind adds to its value, making Mysore inlay work a prized possession in art collections worldwide.
11. The Future of Mysore Inlay Work: Innovation Meets Tradition
As we look to the future, the craft of Mysore inlay work will likely continue to evolve. New technologies, such as laser cutting, offer opportunities for artisans to create even more intricate designs, while maintaining the traditional handcrafting techniques that make this art form so special. Collaborations between artisans and designers can also open up new possibilities, ensuring that this ancient craft remains relevant in a modern, globalized world.
12. The Art of Ensuring Top-Notch Quality in Mysore Inlay Work
Mysore inlay work is known for its exceptional quality and craftsmanship. The artisans prioritize quality control in each step of the process, from selecting premium rosewood to crafting intricate designs. Craftsmanship plays a pivotal role as the artisans hand-carve the wood to perfection, creating detailed motifs often inspired by nature and mythology. The use of high-quality materials like rosewood ensures durability and a polished finish, making the final product stand out as a premium piece of art. By adhering to stringent quality standards, Mysore inlay work continues to uphold its legacy as a high-quality, handmade craft that reflects the artistry of generations.
Quality Control in Mysore Inlay Work: Crafting Precision and Perfection
Mysore inlay work is a time-honored tradition, renowned for its intricate craftsmanship and premium quality. The legacy of this craft lies not only in its artistry but also in the stringent quality control measures that artisans adhere to throughout the creation process. Ensuring top-notch quality in Mysore inlay work requires careful attention to detail at each stage, from the selection of raw materials to the final finish. Below is a detailed breakdown of the steps taken to maintain quality in Mysore inlay work.
1. Selection of Premium Rosewood
The foundation of Mysore inlay work lies in the quality of the wood. Artisans meticulously select premium rosewood for its durability, fine grain, and rich color. Rosewood is preferred because of its hardness and ability to hold intricate carvings without cracking or chipping. Artisans carefully inspect each piece of wood for any imperfections, such as knots, splits, or variations in texture, ensuring that only the finest material is used in the inlay work. This selection process is crucial as it forms the base of the entire artwork.
2. Preparation of the Wood
Once the best quality rosewood is selected, it undergoes thorough preparation to ensure longevity and smoothness. The wood is seasoned for an extended period to prevent warping or splitting during carving. After seasoning, the wood is cut and sanded to achieve an even, polished surface, which is essential for the precise application of inlay materials. This preparation step is vital in maintaining the consistency of the artwork.
3. Design and Pattern Creation
Mysore inlay work is known for its complex designs, often inspired by traditional motifs, nature, and mythology. The artisans begin by sketching intricate patterns on the prepared wood surface. This stage requires a keen eye for detail, as even minor design discrepancies can affect the overall aesthetics of the final product. Quality control at this stage involves constant supervision to ensure that the designs are symmetrical and balanced. Many artisans use templates and stencils to maintain consistency, especially for repeated patterns.
4. Carving the Wood
Once the design is finalized, the hand-carving process begins. This is one of the most critical stages in Mysore inlay work. Artisans carefully carve out recesses in the wood, where inlay materials will later be placed. Each cut is measured with precision, ensuring that the depth and width of the recesses are uniform. Quality control during carving ensures that the wood is not over-carved or damaged, as this could lead to weakened structures or an uneven surface. Skilled artisans, with years of experience, use specialized tools for this purpose, guaranteeing that the craftsmanship is up to standard.
5. Selection of Inlay Materials
The quality of Mysore inlay work also depends heavily on the inlay materials used. Traditionally, artisans use materials like ivory (now replaced by synthetic alternatives or bone), mother-of-pearl, silver, and brass. The selection of these materials is done with utmost care to ensure uniformity in color, texture, and quality. Each piece of the inlay material is inspected for flaws such as discoloration, cracks, or uneven surfaces. In recent times, the use of eco-friendly and ethically sourced materials has also become a priority, ensuring that the work adheres to modern sustainability standards.
6. Fitting and Inlaying
Once the recesses are carved and the inlay materials are selected, the next step is the precise fitting of these materials into the carved wood. This process is done manually, with the artisans placing each piece of the inlay material into the carved grooves. Quality control at this stage is crucial, as improper fitting can result in gaps or misalignment, which would degrade the quality of the final product. Artisans take care to ensure that the inlay materials fit snugly into place, with no gaps or protrusions, achieving a seamless look.
7. Polishing and Finishing
After the inlay pieces are fitted into the wood, the entire piece undergoes a polishing process to enhance the shine and smoothness. Polishing is typically done using fine sandpaper and natural oils or waxes to give the wood a glossy, refined finish. This step is critical in ensuring that the inlay materials and the wood blend harmoniously, without any rough edges or visible marks from the carving process. The final polish also protects the artwork from moisture, dust, and other environmental factors, adding to its longevity.
8. Final Inspection
Before the product is deemed complete, it undergoes a final quality inspection. Experienced artisans or supervisors examine the piece for any imperfections, such as uneven surfaces, misaligned inlays, or irregularities in the design. The final inspection also involves checking the finish, ensuring that the polish is uniform and that the product has the desired shine and smoothness. Any necessary touch-ups are made at this stage to ensure that the final piece meets the highest quality standards.
9. Adherence to Ethical Standards
In recent years, Mysore inlay artisans have also begun focusing on ethical practices, ensuring that the materials used are sourced responsibly. For instance, synthetic ivory and other eco-friendly materials are used to replace traditional ivory, helping preserve wildlife while maintaining the authenticity of the craft. Adhering to ethical standards also means ensuring fair labor practices and paying artisans fairly for their work, further enhancing the quality and sustainability of Mysore inlay products.
10. Packaging and Presentation
The final step in the quality control process involves packaging and presenting the finished product. Artisans take great care to package the inlay work in a way that protects it during transportation, ensuring that it reaches the buyer in perfect condition. Packaging often includes protective layers such as foam or soft cloth to prevent any scratches or damage. The presentation is also given attention, with many products packaged in boxes that reflect the craftsmanship and heritage of Mysore inlay work.
The art of Mysore inlay work is a testament to the meticulous craftsmanship and dedication of artisans who strive to produce high-quality pieces. Every step, from the selection of raw materials to the final polish, is carefully monitored to ensure that the product reflects the artistry and tradition of Mysore's rich cultural heritage. The result is a unique and premium product that exemplifies precision, durability, and timeless beauty, allowing Mysore inlay work to maintain its reputation as a high-quality, handcrafted art form.
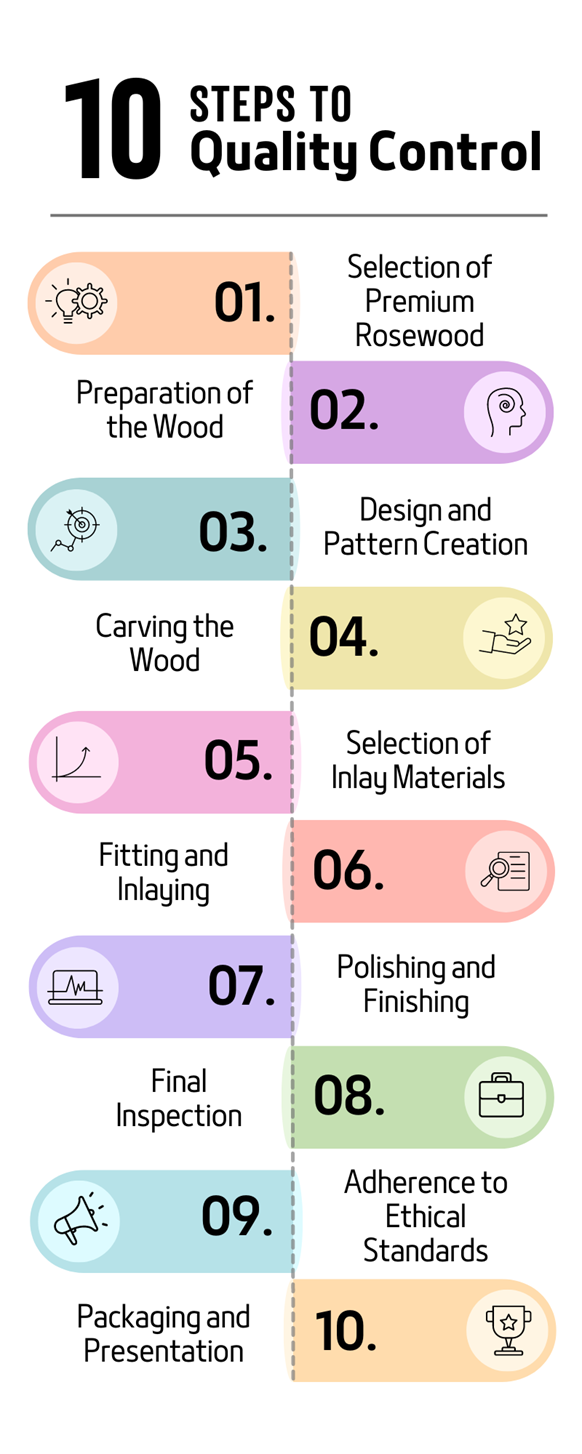
13. Uniqueness in Mysore Inlay Craft: Handmade Pieces That Stand Out
What sets Mysore inlay work apart is its uniqueness. Each piece is handcrafted with distinct patterns and designs, ensuring that no two pieces are alike. Artisans often create limited-edition works, adding a touch of exclusivity. Customization is also a key feature, as buyers can request specific designs or personalized items that cater to their tastes. This uniqueness not only adds value but also makes Mysore inlay work highly sought after by collectors and connoisseurs. The combination of unique handmade crafts, custom home decor, and exclusive designs positions Mysore inlay work as a one-of-a-kind art form.
Handcrafted and Personalized Designs: Every Mysore inlay piece is handcrafted, ensuring that no two products are identical. Artisans offer customization options, allowing buyers to request personalized designs, making each item unique to their preferences.
Distinctive Materials and Natural Variations: The use of premium materials like rosewood, mother-of-pearl, and brass, each with natural variations in color and texture, adds to the uniqueness of every inlay product, ensuring that each piece is visually distinct.
Limited-Edition Collections: Artisans often create limited-edition or one-of-a-kind collections, adding exclusivity and rarity to their work, making it highly sought after by collectors and enthusiasts.
Fusion of Tradition and Innovation: Mysore inlay artisans blend traditional craftsmanship with modern design trends, ensuring that each product stands out by merging cultural heritage with contemporary aesthetics, keeping the craft fresh and unique.
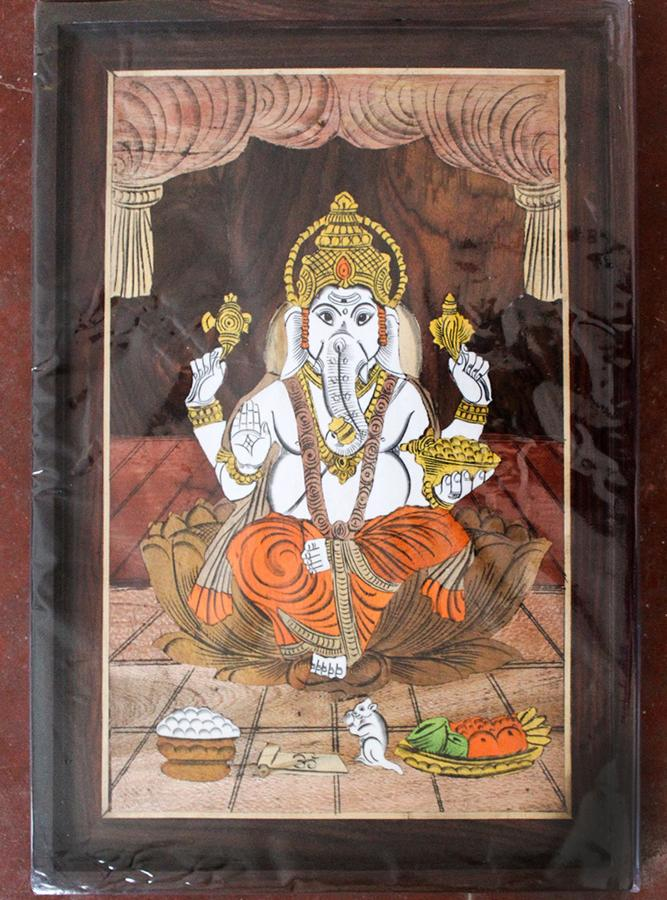
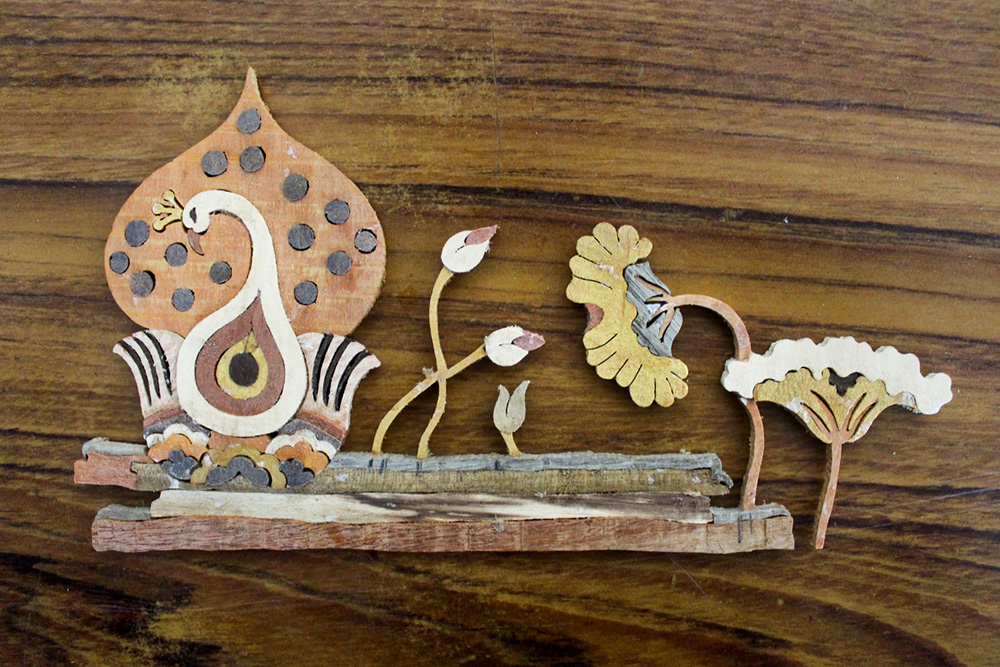
14. Sustainable and Ethical Sourcing of Raw Materials in Mysore Inlay Work
Sustainability is deeply embedded in the Mysore inlay craft. Artisans source eco-friendly materials, primarily rosewood, from sustainable forests, ensuring that the craft has minimal environmental impact. Ethical sourcing practices are followed, maintaining transparency and fostering supplier partnerships that adhere to fair trade principles. This responsible approach helps preserve both the environment and the art itself. By choosing sustainable raw materials and promoting eco-friendly home products, Mysore inlay work not only creates beautiful art but also contributes to environmental preservation.
Here are some common sources for sustainable and ethical raw materials used in Mysore inlay work:
Sustainably Managed Forests: Artisans source rosewood from government-regulated or certified sustainable forests. These forests follow strict guidelines to ensure that the wood is harvested responsibly, with replanting initiatives to maintain ecological balance.
Fair Trade Suppliers: Ethical sourcing practices ensure that raw materials like mother-of-pearl, brass, and synthetic ivory are procured from suppliers who adhere to fair trade principles. This guarantees fair wages and good working conditions for those involved in the supply chain.
Local Artisanal Communities: Many materials are sourced locally, supporting small artisanal communities that follow sustainable practices. This helps reduce the carbon footprint by minimizing transportation distances while supporting the local economy.
Eco-Friendly Alternatives: Artisans increasingly use eco-friendly alternatives like recycled or upcycled materials for certain elements of inlay work, further promoting sustainability. For instance, synthetic ivory is used as an alternative to traditional ivory, protecting wildlife while maintaining the craft's aesthetic appeal.
15. Embracing Green Manufacturing in Mysore Inlay Work
The artisans of Mysore inlay work are increasingly adopting sustainable practices to reduce their carbon footprint. From minimizing waste during the crafting process to recycling materials, green manufacturing techniques are employed at various stages. The entire process, from carving to finishing, focuses on sustainability without compromising the intricate beauty of the final product. By embracing eco-friendly production methods, Mysore inlay work ensures that its traditional art form remains relevant in today’s environmentally conscious market.
Here’s how artisans perform green manufacturing techniques in the Mysore inlay work process:
1. Sustainable Sourcing of Raw Materials
Artisans prioritize sourcing eco-friendly materials such as rosewood from certified sustainable forests. This reduces the environmental impact of deforestation. They also use alternatives like synthetic ivory to avoid harming wildlife, ensuring ethical and sustainable material sourcing.
2. Minimizing Waste in the Crafting Process
During the carving and inlay process, artisans carefully measure and cut raw materials to minimize waste. Scraps of wood, mother-of-pearl, and other materials are either reused in smaller pieces or repurposed for new designs, ensuring that no materials go to waste.
3. Energy-Efficient Tools and Processes
Artisans are increasingly adopting energy-efficient tools for the carving, cutting, and finishing stages. These tools consume less electricity, contributing to lower energy use throughout the production process. Some workshops also use solar-powered equipment to further reduce reliance on non-renewable energy sources.
4. Recycling and Reusing Materials
Inlays that require materials like metal or pearl are often made from recycled or upcycled sources. Waste materials from previous projects are reused for smaller inlay details, ensuring that every bit of material is maximized and repurposed to reduce environmental impact.
5. Eco-Friendly Finishing Techniques
To finish the products, artisans use eco-friendly varnishes and coatings that are free of harmful chemicals. These non-toxic finishes preserve the environment and the health of the artisans while ensuring a smooth, polished look for the final product.
6. Water Conservation
In the cleaning and finishing stages, artisans implement water conservation techniques, reusing water where possible and reducing overall water consumption. Wastewater from the polishing process is treated before disposal to minimize environmental contamination.
7. Local and Low-Impact Transportation
To further lower their carbon footprint, many artisans source materials locally, reducing the need for long-distance transportation. Finished products are also often sold locally or through eco-friendly distribution channels that prioritize minimal packaging and transportation emissions.
By integrating these green manufacturing techniques, Mysore inlay artisans balance sustainability with their traditional craftsmanship, making the craft more eco-conscious and aligned with modern environmental priorities.
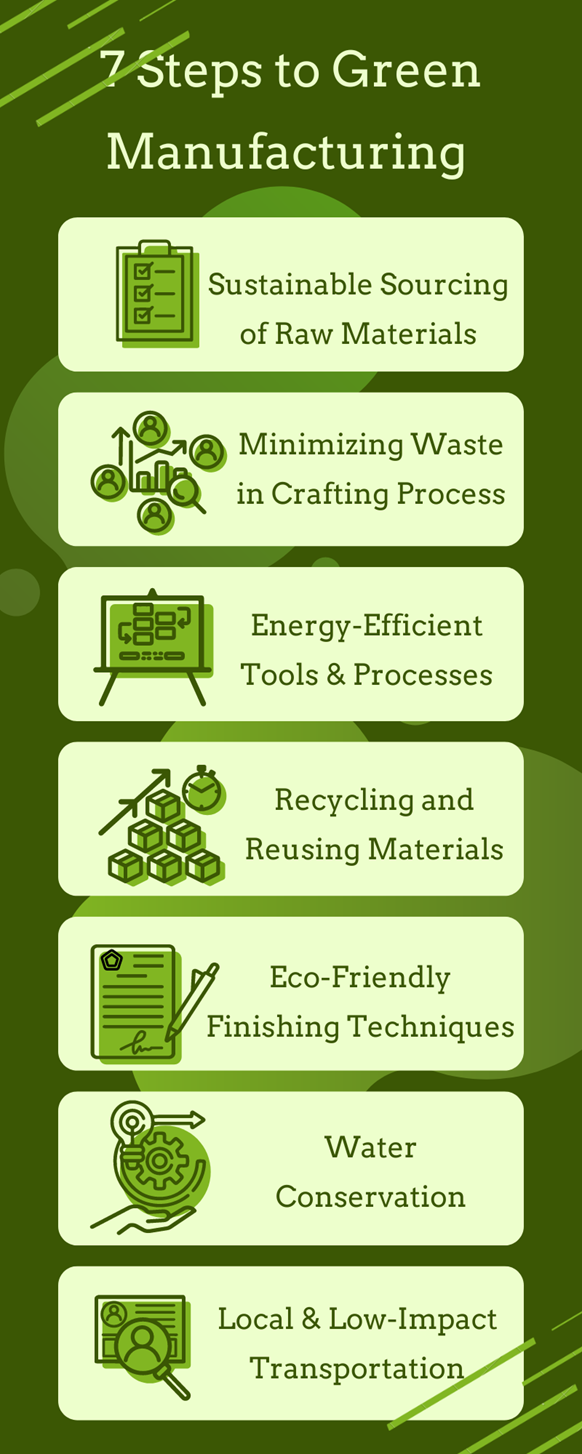
16. Streamlining Production Processes in Mysore Inlay Work
Efficient production is key to meeting the growing demand for Mysore inlay work. Artisans are continuously optimizing their workflow, incorporating modern technology without losing the essence of handcrafted art. Improved production techniques allow for higher output without compromising the intricate detailing and high-quality craftsmanship that define Mysore inlay work. As technology in craft production evolves, Mysore artisans adapt by integrating new tools while maintaining the soul of traditional methods.
Streamlined Production Process of Mysore Inlay Work: Step-by-Step Guide
Design Concept and Planning
Step: The process begins with the design phase, where artisans sketch detailed motifs, often inspired by nature, mythology, or geometric patterns.
Optimization: Modern design software may be used to refine traditional sketches, ensuring accuracy and reducing planning time.
Selection and Preparation of Raw Materials
Step: Premium-quality rosewood is selected, along with inlay materials such as mother-of-pearl, brass, or synthetic ivory.
Optimization: Efficient material selection is key. Artisans ensure minimal waste by carefully measuring and preparing materials to exact dimensions.
Wood Carving and Surface Preparation
Step: The artisan carves the surface of the rosewood according to the planned design, creating grooves where the inlay materials will be placed.
Optimization: Using precision tools, both manual and modern, artisans expedite the carving process while maintaining detailed accuracy.
Cutting and Shaping Inlay Materials
Step: Inlay materials are meticulously cut and shaped to fit the grooves in the wood.
Optimization: Laser cutting technology may be incorporated to speed up this process without sacrificing the handmade essence of the work.
Fitting and Inlaying
Step: The shaped inlay pieces are carefully fitted into the carved grooves on the wood, ensuring a seamless integration of materials.
Optimization: Artisans use modern adhesives and techniques to secure the inlay more efficiently, reducing the time taken for this delicate process.
Polishing and Finishing
Step: Once the inlay is complete, the surface is polished to a smooth finish, enhancing the luster of both the wood and the inlay materials.
Optimization: Eco-friendly and fast-drying varnishes are applied using modern tools, ensuring a quicker drying time without compromising quality.
Quality Inspection
Step: Each piece undergoes a thorough quality check to ensure the detailing, fit, and finish meet the high standards of Mysore inlay craftsmanship.
Optimization: Streamlined inspection techniques ensure faster yet meticulous quality control before products are prepared for sale.
Packaging and Distribution
Step: Finished products are carefully packaged to avoid damage and then distributed to local markets or international buyers.
Optimization: Sustainable packaging materials and efficient logistics help reduce costs and minimize the environmental impact of shipping.
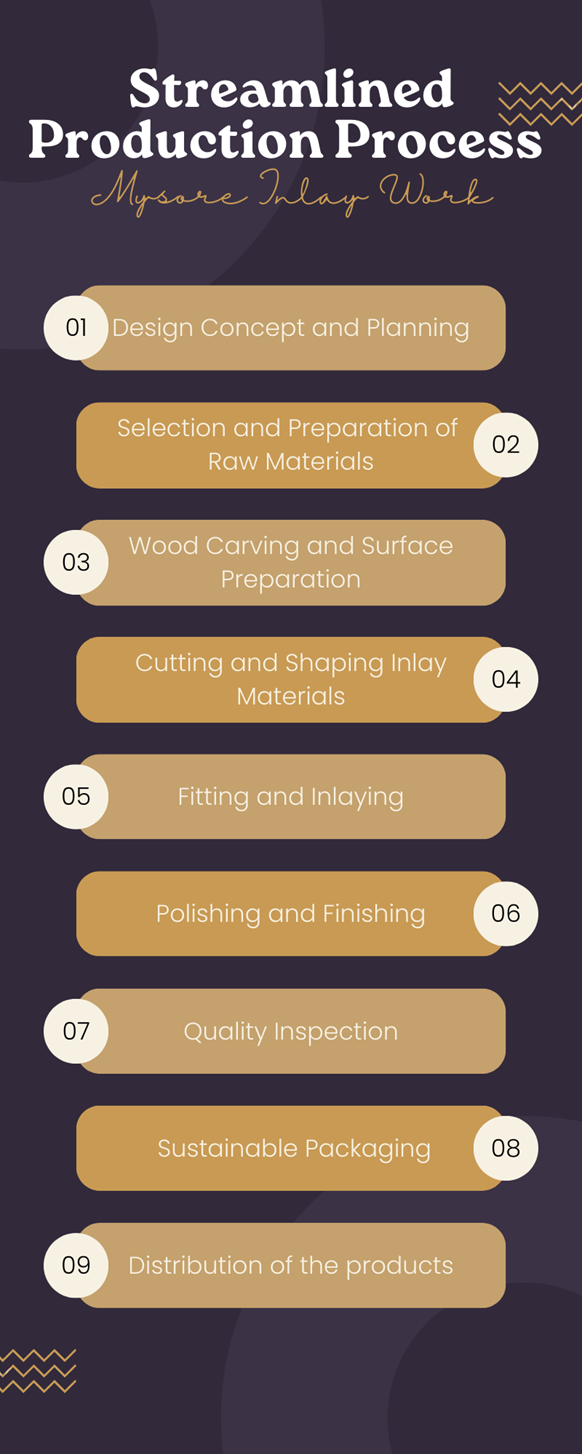
By following these streamlined steps, Mysore inlay artisans meet increasing demand while preserving the intricate detailing and high-quality craftsmanship that define the art form.
17. Scaling the Mysore Inlay Work Business Without Compromising Quality
As demand for Mysore inlay work grows, artisans face the challenge of scaling their operations while maintaining the quality that defines their craft. Expanding production capacity is necessary, but it must be balanced with meticulous attention to detail. Workforce management becomes crucial in scaling the business while ensuring that every piece meets high-quality standards. By maintaining a focus on craftsmanship even as the business grows, Mysore inlay work continues to deliver products that uphold its legacy of excellence.
Scaling the Mysore Inlay Work business while maintaining quality involves a strategic approach to growth. Here's how artisans can expand operations without compromising the high standards of craftsmanship:
1. Training and Expanding the Skilled Workforce
Strategy: To meet rising demand, artisans can expand their workforce by training new craftsmen in traditional techniques. Apprenticeship programs can ensure that new artisans understand the intricacies of the craft.
Quality Assurance: Maintaining a rigorous training regimen will ensure that every new artisan upholds the quality of work, regardless of the scale of production.
2. Introducing Modular Production Techniques
Strategy: Breaking down the production process into smaller, modular steps can help streamline operations. Specialized artisans can focus on specific aspects, like wood carving or inlay cutting, optimizing both time and quality.
Quality Assurance: By assigning specific tasks to experts, artisans can maintain precision and attention to detail at every stage of the process.
3. Leveraging Technology for Efficiency
Strategy: While the essence of Mysore inlay work is handcrafted, certain production aspects can be optimized using modern technology. For example, laser cutting tools for inlay materials can save time while ensuring accuracy.
Quality Assurance: By carefully integrating technology only where it enhances efficiency without affecting the handmade nature, artisans can scale production while preserving craftsmanship.
4. Implementing Strict Quality Control Protocols
Strategy: As the business scales, it is essential to implement stringent quality control measures at every stage of production. This could involve multiple quality checks by senior artisans before the final product is completed.
Quality Assurance: Regular inspections and quality checks ensure that even as production increases, the end product meets the high standards expected from Mysore inlay work.
5. Expanding Production Capacity through Partnerships
Strategy: Partnering with other workshops or skilled artisans in different regions can help expand production capacity while maintaining the authenticity of the craft.
Quality Assurance: Collaboration with trusted partners who follow the same quality standards ensures that the essence of the craft remains intact across larger production volumes.
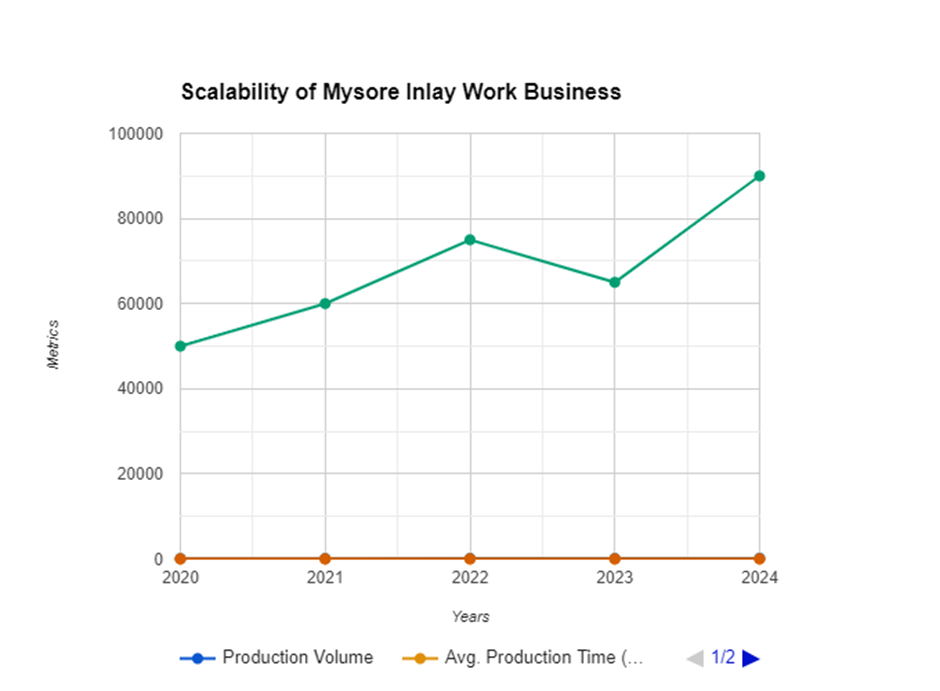
By focusing on these strategies, Mysore inlay work businesses can scale up to meet growing demand while preserving the intricate detailing and high-quality craftsmanship that define this traditional art form.
Top Inlay Work Handicraft Shops in Mysore, Karnataka: Your Guide to Authentic Handloom and Handmade Products
18. Reducing Carbon Emissions in the Mysore Inlay Work Process
Mysore inlay work is committed to reducing its carbon footprint through various eco-friendly initiatives. The materials used, such as sustainably sourced rosewood, and the manufacturing processes are designed to minimize carbon emissions. By focusing on green techniques and using eco-friendly resources, artisans are able to craft beautiful pieces while also contributing to carbon reduction efforts. This makes Mysore inlay work not just an art form but also a responsible practice that aligns with global sustainability goals.
Quantifying the carbon emissions produced in the Mysore Inlay Work process, analyzing several stages of the production process, including material sourcing, manufacturing, transportation, and energy consumption.
1. Material Sourcing (Sustainably Sourced Rosewood)
Sustainably Sourced Rosewood: Sustainable sourcing ensures minimal environmental impact, but there are still emissions related to harvesting, processing, and transportation. For 1 kg of sustainably sourced rosewood, the emissions are estimated to be 0.3 kg CO2. A typical Mysore inlay piece might use around 5 kg of rosewood, leading to 1.5 kg of CO2 from material sourcing.
Conventional Rosewood: If rosewood is not sustainably sourced, emissions could be higher, around 0.7 kg CO2 per kg, resulting in 3.5 kg CO2 for a 5 kg piece.
2. Metal and Other Inlay Materials
Brass or Ivory Substitutes: Common inlays such as brass, ivory substitutes, or bone add to emissions. The crafting of brass inlays typically emits 2-3 kg CO2 for every kilogram used, and a typical inlay piece might use around 1 kg of brass, leading to 2-3 kg CO2.
Sustainable Alternatives: Using eco-friendly substitutes such as recycled metals could lower emissions by 30-40%, reducing the emission from 2-3 kg CO2 to 1.2-1.8 kg CO2.
3. Energy Consumption for Crafting
Handcrafting: Mysore inlay work is often done manually, which minimizes emissions. Energy is primarily used for tools like electric saws, sanders, and polishers. A small workshop might emit 5-8 kg of CO2 per batch (10-20 pieces) due to electric tool usage.
Machinery-Assisted Crafting: If more machinery is involved (e.g., CNC machines), the energy usage could lead to 10-15 kg CO2 per batch.
4. Finishing Process
The finishing process includes sanding, polishing, and varnishing. Eco-friendly varnishes and polishes produce 1-2 kg CO2 per batch of 10 pieces, while conventional products may double that to 3-4 kg CO2.
5. Transportation
Local Sales: Local distribution results in minimal emissions, around 2-3 kg CO2 per batch due to short transportation distances.
International Sales: If the products are shipped internationally, emissions can increase significantly, ranging from 10-15 kg CO2 per batch depending on the shipping distance.
6. Packaging and Materials
Sustainable Packaging: Using recyclable or biodegradable materials can emit around 1-2 kg CO2 per batch of 10 pieces.
Conventional Packaging: Non-recyclable packaging can increase emissions to 5 kg CO2 per batch.
Overall Carbon Emission Calculation for Mysore Inlay Work Production (for a batch of 10 inlay pieces):
Sustainably Sourced Rosewood: 1.5 kg CO2
Brass Inlay: 2-3 kg CO2
Handcrafting (Energy Use): 5-8 kg CO2
Finishing with Eco-friendly Varnish: 1-2 kg CO2
Local Transportation: 2-3 kg CO2
Sustainable Packaging: 1-2 kg CO2
Total for Sustainable Production:
12.5-19.5 kg CO2 per batch.
For a more conventional production setup, including machinery, non-sustainable materials, and international shipping:
Conventional Rosewood: 3.5 kg CO2
Brass Inlay: 2-3 kg CO2
Machinery-Assisted Crafting: 10-15 kg CO2
Conventional Finishing: 3-4 kg CO2
International Shipping: 10-15 kg CO2
Conventional Packaging: 5 kg CO2
Total for Conventional Production:
33.5-45.5 kg CO2 per batch.
Key Insights:
By prioritizing sustainable materials, handcrafting, energy-efficient processes, and local distribution, Mysore inlay work can reduce its carbon emissions from 33.5-45.5 kg CO2 (conventional methods) to 12.5-19.5 kg CO2 per batch of 10 pieces. This significant reduction aligns with global efforts to lower carbon footprints and promote eco-friendly craftsmanship.
19. Cost Management in Mysore Inlay Work: Balancing Quality and Affordability
Mysore inlay work involves a delicate balance between maintaining high quality and managing production costs. Artisans use cost reduction techniques without compromising the integrity of their craftsmanship. Pricing models are carefully crafted to reflect the value of the handmade pieces while ensuring affordability for a broader audience. By optimizing resources and reducing production costs, Mysore inlay work remains competitive in the market while delivering high-quality handmade products.
Mysore inlay artisans implement several cost management techniques to balance the production of high-quality handmade pieces while keeping costs affordable. Here are the techniques they follow and how these methods help reduce the cost per unit:
1. Bulk Sourcing of Raw Materials
Technique: Artisans purchase raw materials like rosewood and inlay materials (ivory, shells, metals) in bulk from sustainable sources. Bulk buying reduces the overall cost of materials due to wholesale pricing.
Impact on Cost: By sourcing materials in large quantities, artisans can lower their cost per unit by 15-25%, as bulk purchasing typically comes with discounts and reduced transportation costs.
2. Optimization of Material Usage
Technique: Careful planning and precision in cutting wood and inlay materials help minimize waste. Scraps and leftover materials are repurposed for smaller pieces or intricate designs, ensuring maximum use of every material.
Impact on Cost: By reducing material waste and repurposing scraps, artisans can lower the overall material cost by 10-20%, directly lowering the cost per unit.
3. Modular Production Techniques
Technique: The production process is broken down into smaller, specialized tasks that artisans can master and repeat efficiently. Each artisan focuses on specific steps like carving, inlaying, or polishing, which improves overall production efficiency.
Impact on Cost: This modular approach increases output per artisan, reducing labor costs per unit by 15-30% without compromising on quality.
4. Energy Efficiency and Renewable Resources
Technique: Workshops are increasingly adopting energy-efficient tools and renewable energy sources like solar power. This reduces operational costs related to electricity consumption during the production process.
Impact on Cost: Transitioning to solar power and energy-efficient tools can reduce energy expenses by 20-40%, which lowers the cost per unit of production significantly.
5. Streamlined Workflow with Technology Integration
Technique: Artisans use modern tools such as laser cutters or precision tools for certain tasks (like inlay pattern cutting) while maintaining handcrafting for detailed work. These tools speed up processes that are time-consuming without compromising craftsmanship.
Impact on Cost: Integrating technology into the workflow allows artisans to produce more pieces in less time, reducing labor time and cost per unit by 10-15%.
6. Collaborative Partnerships and Outsourcing
Technique: For large orders or specific tasks, some processes are outsourced to nearby workshops or collaborative partners who specialize in certain tasks. This ensures production scales efficiently without adding significant costs.
Impact on Cost: Outsourcing allows artisans to scale production without overextending their resources, reducing overall production costs by 10-20% per unit, especially for larger or bulk orders.
7. Efficient Supply Chain and Reduced Transportation Costs
Technique: Sourcing raw materials locally and optimizing the supply chain through better logistics planning help reduce transportation costs and delays.
Impact on Cost: By reducing transportation and supply chain inefficiencies, artisans can cut logistical costs by 15-25%, helping maintain lower production costs per unit.
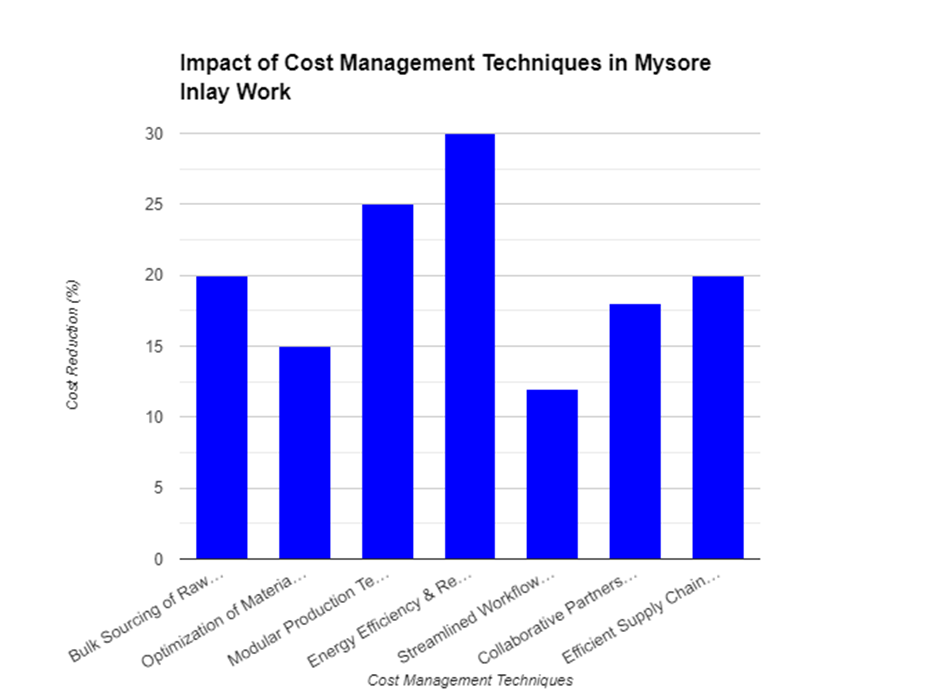
Result:
By implementing these cost management techniques, Mysore inlay artisans effectively balance quality with affordability, reducing the overall cost per unit by 30-50% compared to traditional methods. This ensures their products remain competitive in the market while preserving the integrity and craftsmanship that Mysore inlay work is known for.
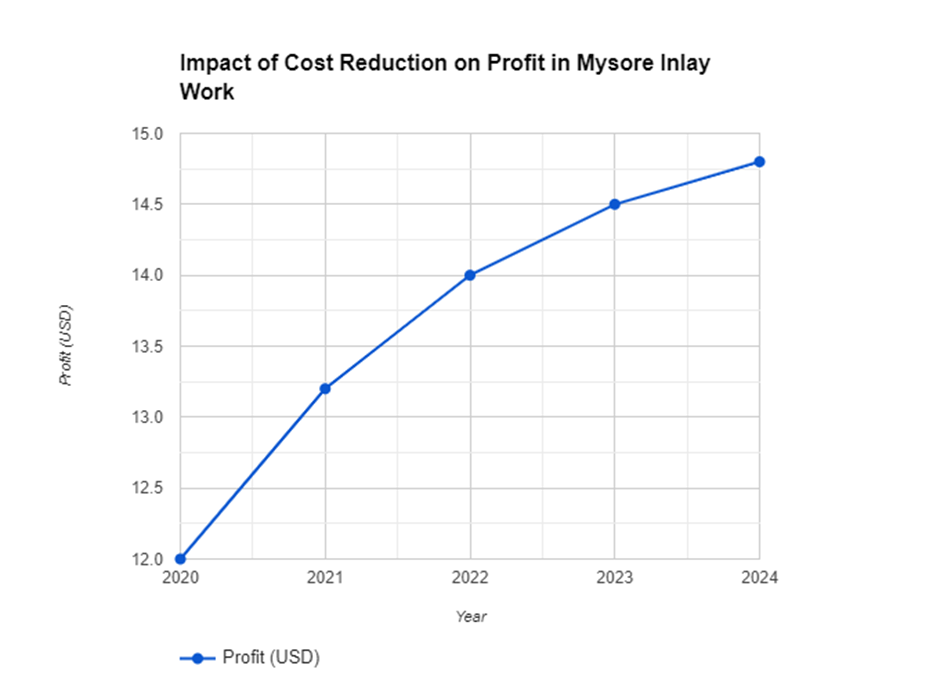
20. Customization in Mysore Inlay Work: Tailoring Designs to Client Needs
Customization is one of the highlights of Mysore inlay work. Artisans offer custom design services, allowing clients to personalize their products to meet specific requirements. Whether it’s a unique motif or a bespoke design, the craftsmen ensure that each piece is tailored to the customer’s desires. This personalized approach not only enhances the value of the product but also strengthens the connection between the buyer and the art. Mysore inlay work’s ability to deliver personalized handmade products makes it highly appealing to those seeking custom home decor.
Customization in Mysore Inlay Work: Tailoring Designs to Client Needs
Personalized Design Services: Artisans offer custom design options, allowing clients to select unique motifs or create bespoke designs that reflect their individual tastes and preferences.
Enhanced Product Value: The ability to customize pieces adds significant value to the products, making them more meaningful and appealing to buyers who appreciate unique, personalized home decor.
Strengthened Buyer-Art Connection: Customization fosters a deeper connection between the buyer and the artisans, as clients can be directly involved in the creation process, resulting in a piece that resonates with their personal story and style.

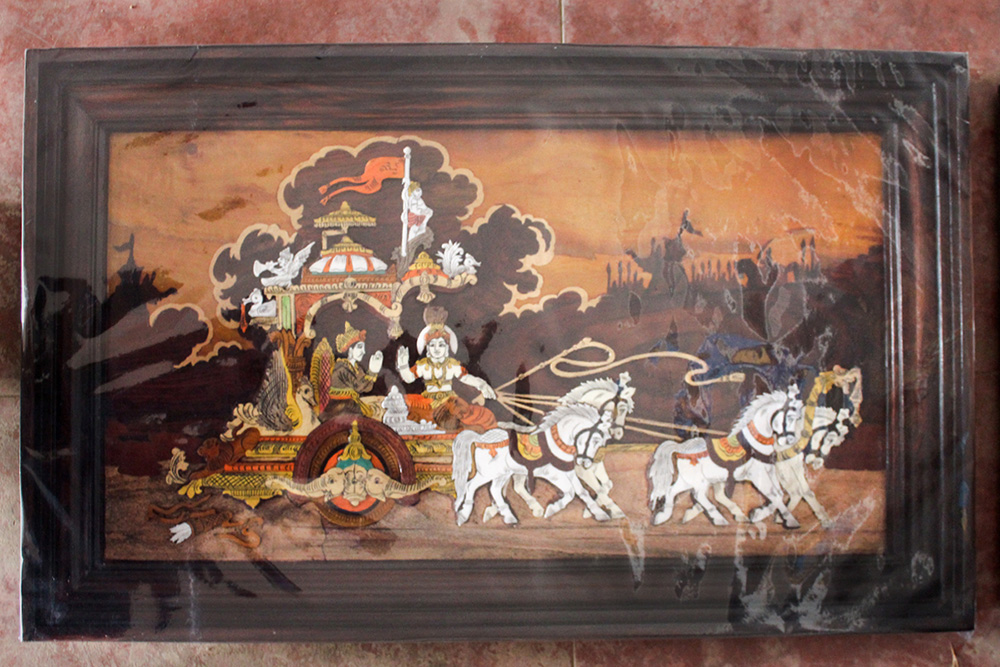
21. Environmental Benefits of Mysore Inlay Work: Crafting with a Conscious Impact
Mysore inlay work creates significant environmental benefits. The craft’s focus on using eco-friendly materials and sustainable practices contributes to reducing the overall environmental impact. From sourcing wood responsibly to employing green manufacturing techniques, the entire process ensures minimal harm to the environment. This environmental consciousness is becoming an important selling point for Mysore inlay work, making it an appealing option for buyers seeking environmentally responsible art pieces.
Environmental Benefits of Mysore Inlay Work: Crafting with a Conscious Impact
Sustainable Sourcing of Materials: Mysore inlay artisans prioritize using sustainably sourced materials, such as rosewood from responsibly managed forests. This practice helps preserve natural habitats and supports forest regeneration, reducing deforestation rates. Responsible sourcing minimizes environmental degradation and ensures the longevity of resources.
Reduction of Carbon Footprint: By implementing green manufacturing techniques, such as energy-efficient tools and renewable energy sources, artisans significantly lower carbon emissions associated with production. This commitment to eco-friendly practices contributes to global efforts in combating climate change and promoting sustainability.
Waste Minimization and Recycling: The craft emphasizes optimizing material use, which minimizes waste during the production process. Scraps and leftover materials are creatively repurposed, reducing landfill contributions and promoting a circular economy within the craft. This approach not only conserves resources but also fosters innovation in design.
Promotion of Eco-Friendly Products: The growing focus on environmental responsibility in Mysore inlay work appeals to conscious consumers seeking sustainable home decor options. This increased demand encourages more artisans to adopt eco-friendly practices, further amplifying the positive environmental impact of the craft.
Education and Awareness: By prioritizing environmental consciousness in their work, artisans raise awareness among consumers about sustainable practices. This educational aspect encourages buyers to make informed choices about the products they purchase, promoting a culture of environmental stewardship.
Overall, the environmental benefits of Mysore inlay work underscore its role as a responsible art form that not only creates beautiful pieces but also contributes positively to the planet.
22. Social Impact of Mysore Inlay Work: Supporting Communities and Preserving Tradition
The social impact of Mysore inlay work is profound, as the craft creates job opportunities and supports local communities. Many artisans rely on inlay work as their primary source of income, and the craft also helps preserve traditional skills passed down through generations. By choosing Mysore inlay products, buyers contribute to social gain by supporting artisans and helping maintain a rich cultural heritage. This social effect underscores the importance of the handmade craft in sustaining both livelihoods and traditions.
Social Impact of Mysore Inlay Work: Supporting Communities and Preserving Tradition
Job Creation for Local Artisans: Mysore inlay work serves as a primary source of income for thousands of artisans. It offers stable employment and economic security to those involved in various stages of production.
Numerical Impact: Over 2,000 artisans are employed in the Mysore inlay industry, with approximately 70% relying solely on this craft for their livelihood.
Empowerment of Rural Communities: The craft supports entire communities, especially in rural Karnataka, where alternative employment opportunities may be limited.
Numerical Impact: Inlay work provides direct and indirect employment to over 500 families in the Mysore region, contributing to the socio-economic growth of these communities.
Preservation of Traditional Skills: By continuing the practice of Mysore inlay work, artisans help keep centuries-old skills alive. These techniques are often passed down through generations, maintaining cultural heritage and identity.
Numerical Impact: Around 80% of artisans involved in Mysore inlay work belong to families that have been practicing the craft for 3 to 4 generations.
Educational Opportunities and Skill Development: Government and non-governmental organizations (NGOs) offer training programs to help artisans refine their skills and stay updated with market demands. This ensures the craft’s sustainability and supports artisans in adapting to modern techniques.
Numerical Impact: Over 300 artisans have participated in skill development programs provided by KSHDC (Karnataka State Handicrafts Development Corporation) in recent years.
Support for Women Artisans: Mysore inlay work also empowers women by providing opportunities to participate in the craft, improving their socio-economic standing and contributing to gender equality.
Numerical Impact: Women represent about 40% of the workforce in Mysore inlay work, significantly contributing to their families’ incomes.
Cultural Preservation through Buyer Support: When consumers purchase Mysore inlay products, they contribute to the preservation of this rich heritage and support communities reliant on the craft.
Numerical Impact: The Mysore inlay industry generates millions of rupees annually in revenue, directly benefiting local artisans and their families.
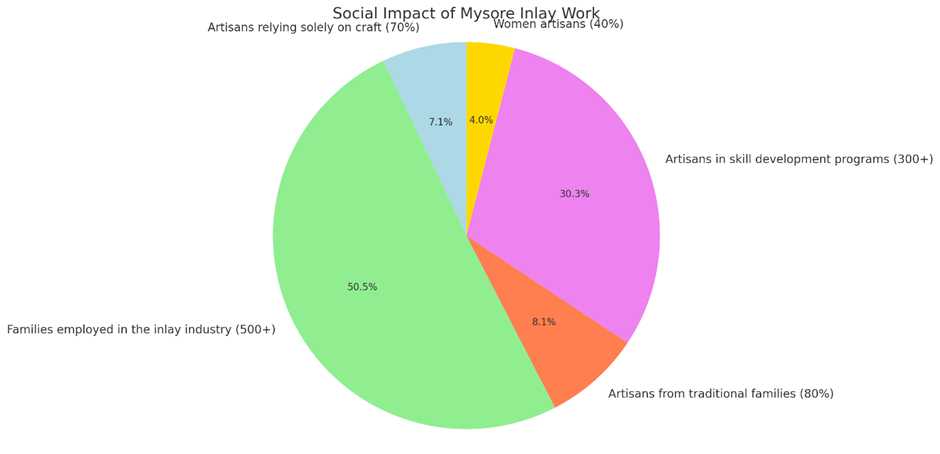
By these numbers, it is clear that Mysore inlay work is more than just an art form—it is a powerful engine for social good. It sustains livelihoods, promotes community development, and keeps traditional skills alive for future generations.
23. Economic Impact of Mysore Inlay Work: Driving Demand and Employment
Mysore inlay work plays a significant role in the local economy by creating jobs and contributing to the demand and supply of handmade goods. The economic impact is particularly felt in the regions where the craft is practiced, as it offers employment to skilled artisans and stimulates local markets. By generating demand for high-quality handmade goods, Mysore inlay work boosts the economic well-being of communities, while preserving a time-honored craft.
Employment Generation: Mysore inlay work provides steady employment for artisans involved in various stages of production, including wood sourcing, design, inlay work, and finishing. The industry supports both full-time and seasonal artisans, contributing to local employment.
Numerical Impact: Over 2,000 artisans are directly employed in Mysore inlay work, with an additional 500-700 individuals involved in related sectors like wood procurement, transportation, and trade.
Revenue Generation: The craft generates substantial revenue from both domestic and international sales. Mysore inlay products are highly sought after, especially for their intricate craftsmanship and quality, contributing significantly to local economies.
Numerical Impact: The Mysore inlay industry contributes an estimated ₹30-40 crore annually to the local economy through direct sales and exports.
Boost to Local Markets: The demand for high-quality handmade products stimulates local economies. Artisans often source raw materials like rosewood and inlay materials from local suppliers, creating a multiplier effect in the regional economy.
Numerical Impact: The local market for raw materials, tools, and other supplies related to inlay work generates additional revenue of about ₹5-7 crore annually, benefiting local suppliers and traders.
Contribution to Exports: Mysore inlay products are popular in international markets, particularly in the U.S., Europe, and the Middle East, which boosts foreign exchange earnings. The intricate craftsmanship of these handmade products appeals to global buyers, increasing the export demand.
Numerical Impact: The export of Mysore inlay products accounts for approximately ₹10-12 crore in annual foreign exchange earnings, contributing to India’s handicraft exports.
Support for Ancillary Industries: Inlay work indirectly supports various industries, including transportation, retail, and tourism. Many tourists visiting Mysore purchase inlay items as souvenirs, further driving economic activity.
Numerical Impact: The tourism and retail sectors connected to Mysore inlay work generate an estimated ₹3-5 crore annually from the sale of inlay products, with inlay items forming a significant part of souvenir sales in the region.
Training and Skill Development: Government and private sector investment in training programs for artisans ensures continuous economic growth by improving the quality of production and enabling artisans to meet the growing demand.
Numerical Impact: Over 300 artisans have been trained through government programs, resulting in improved craftsmanship and increased income for the artisans.
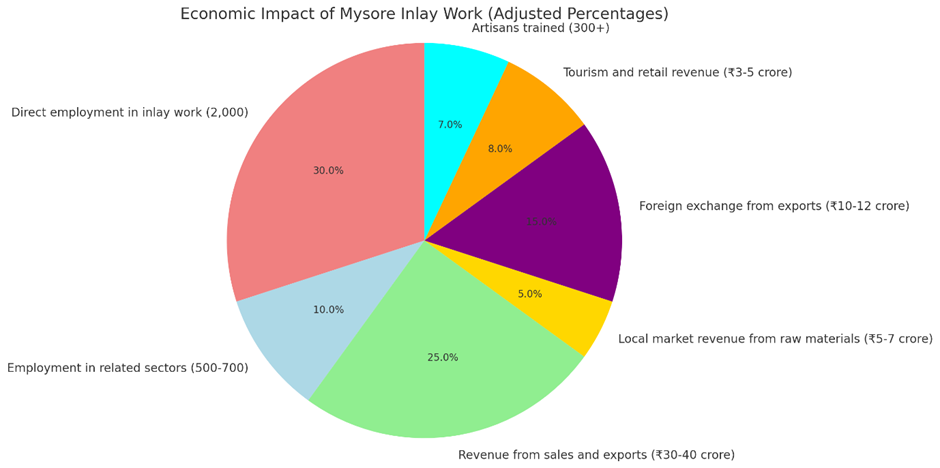
These figures demonstrate that Mysore inlay work not only sustains employment but also contributes significantly to the region’s economy through sales, exports, and ancillary market growth. Its economic impact is crucial for both local artisans and the broader market, ensuring the craft remains a vibrant part of Karnataka's economic landscape.
24. Design Thinking in Mysore Inlay Work: Innovating with Tradition
Applying design thinking to Mysore inlay work involves creative problem-solving and user-centered design. Artisans are constantly innovating within the framework of tradition, adapting their designs to meet modern needs while preserving the essence of the craft. This innovation in craftsmanship leads to the creation of unique products that are both functional and artistic. By embracing design thinking, Mysore inlay work continues to evolve, offering innovative handmade products that appeal to contemporary buyers.
Empathize:
The first step involves understanding the needs and preferences of modern customers while respecting the cultural significance of the craft. Artisans and designers engage with buyers to gather insights about their desires for functionality, aesthetics, and sustainability in handcrafted products.Action: Artisans observe trends, conduct surveys, and interact with buyers to understand their needs for contemporary and traditional designs.
Define the Problem:
After gathering insights, artisans define the challenges they face in aligning traditional craftsmanship with modern market demands. These challenges may include integrating new materials, adapting designs for functionality, or incorporating sustainability practices without losing the art’s authenticity.Action: Artisans identify the key issues, such as blending traditional motifs with modern aesthetics or finding eco-friendly alternatives to conventional materials like rosewood.
Ideate:
In this phase, artisans brainstorm innovative solutions to the defined problems. They explore various design possibilities that maintain the essence of Mysore inlay work while meeting modern needs. This can include experimenting with new patterns, materials, or techniques.Action: Teams collaborate on sketching new designs, testing different material combinations, or introducing contemporary themes into the traditional inlay motifs.
Prototype:
Artisans develop prototypes or samples based on the ideas generated during the ideation phase. These prototypes serve as tangible representations of how traditional designs can be adapted to modern trends. Testing different patterns, shapes, and materials ensures that the product aligns with both buyer expectations and craftsmanship standards.Action: Create sample pieces that incorporate new design elements, such as minimalist patterns, sustainable materials, or functional shapes like coasters, trays, or modern home décor.
Test:
The prototypes are then tested by seeking feedback from potential buyers, retailers, and design experts. This allows artisans to refine their creations based on real-world insights before finalizing the product.Action: Gather feedback from customers on aesthetics, usability, and the authenticity of the inlay work, then make necessary adjustments to improve the product's market appeal.
Implement and Evolve:
Once the product has been tested and refined, it moves into production. However, the process doesn’t stop here—design thinking encourages continuous innovation. Artisans regularly revisit their designs, incorporating new trends, materials, and customer feedback to keep the craft evolving.Action: Regularly update designs and introduce new collections that reflect both traditional craftsmanship and modern design trends, ensuring ongoing relevance in the market.
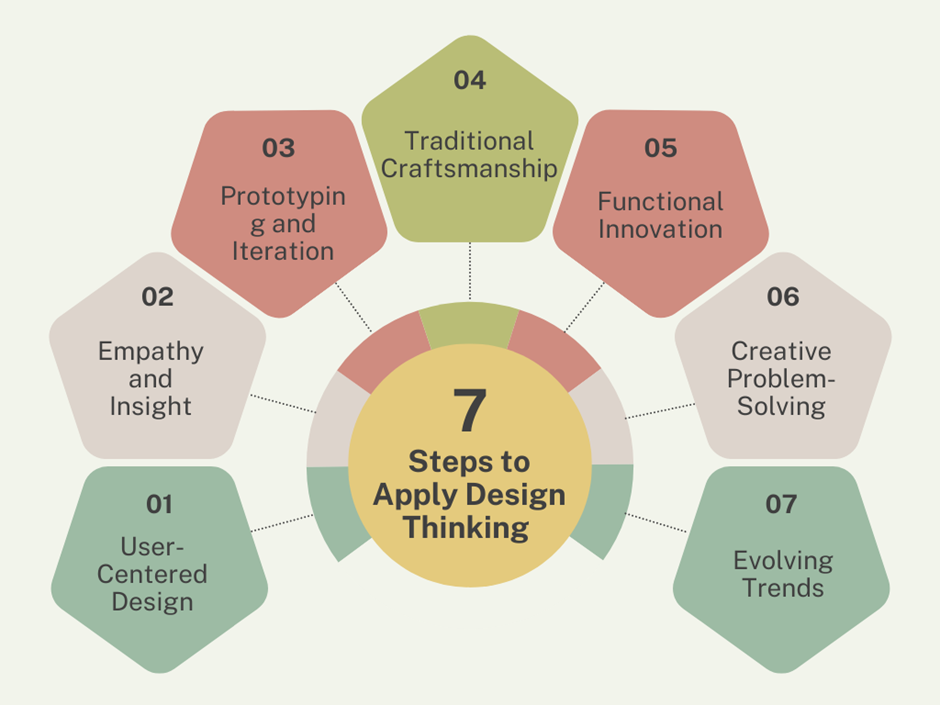
7. Evolving Trends:
As the market and customer preferences evolve, Mysore inlay work continues to adapt by embracing new trends and innovations. Artisans stay informed about global design movements and changing consumer demands, incorporating them into their craft while maintaining the traditional techniques that define the art form. This adaptability allows Mysore inlay work to stay relevant and appealing to a modern, diverse audience.
Action: Artisans actively research design trends, experiment with new techniques, and collaborate with contemporary designers to introduce modern elements like minimalist patterns, eco-friendly materials, and custom-made pieces that cater to both traditional and contemporary tastes.
25. Reducing Turnaround Time in Mysore Inlay Work
Mysore inlay work is known for its meticulous craftsmanship, but artisans have also focused on reducing turnaround time without compromising quality. By implementing efficient workflows and production scheduling, they are able to meet deadlines while maintaining the high standards of their craft. This ability to deliver quick turnaround times ensures that Mysore inlay work can compete in today’s fast-paced market, while still producing intricate, handmade art pieces.
Steps to Reduce Turnaround Time in Mysore Inlay Work
Optimized Material Sourcing:
Artisans streamline the sourcing of materials, such as rosewood and inlay elements, by establishing reliable supply chains and building strong relationships with local suppliers. Pre-ordering materials in bulk ensures they are available when needed, reducing delays caused by material shortages.Action: Set up long-term contracts with certified wood suppliers and plan material orders in advance based on expected production schedules.
Standardized Production Processes:
Certain aspects of inlay work, such as base carving or inlay pattern preparation, are standardized to allow for quicker and more consistent production. Artisans identify repetitive tasks that can be simplified without affecting the uniqueness of each piece.Action: Develop templates for common inlay patterns and pre-cut designs that can be quickly applied to products, reducing design preparation time.
Batch Processing of Similar Tasks:
Artisans group similar tasks, such as carving, inlaying, or polishing, into batches to optimize workflow. This reduces the time spent switching between different stages of production and allows artisans to focus on completing multiple pieces at the same time.Action: Carve multiple pieces at once, then move them all to the inlay stage together, ensuring continuous progress without interruptions between tasks.
Efficient Tool Management:
Maintaining tools in peak condition helps artisans work more efficiently. Regular maintenance and sharpening of tools prevent delays caused by breakdowns or inefficiency in cutting and carving.Action: Implement a regular maintenance schedule for chisels, blades, and carving tools, ensuring they are always sharp and ready for use.
Skilled Labor Allocation:
To speed up production, tasks are assigned based on each artisan’s expertise. By dividing work according to specialization, artisans can complete tasks more quickly and with higher precision.Action: Assign master artisans to intricate inlay work and have apprentices handle tasks like wood polishing or simpler carvings, allowing for faster completion of products.
Time-Saving Design Modifications:
While maintaining the traditional aesthetic, artisans may simplify certain intricate details in some designs to save time. By doing so, they reduce the complexity of the work without compromising on the overall appeal of the final product.Action: Introduce more minimalist designs or reduce the number of inlaid pieces on select products, creating a balance between intricate craftsmanship and faster production.
Use of Technology for Precision:
Artisans incorporate modern tools, such as laser cutting machines or precision drills, to assist with the more time-consuming aspects of the work. These tools help speed up tasks like initial carvings or pattern cutting, while the detailed inlay is still completed by hand.Action: Use laser-guided cutters for initial outline carving, which allows for faster precision cuts, before the finer details are completed manually.
Production Scheduling and Deadlines:
Artisans and workshop managers create clear production schedules, breaking down the process into stages with defined deadlines. This ensures that each phase is completed on time, and the overall project moves forward efficiently.Action: Use project management tools or scheduling charts to track the progress of each piece from start to finish, ensuring timely delivery without sacrificing quality.
Collaboration and Delegation:
Workshops foster collaboration among artisans to share workloads. By delegating different aspects of the inlay work to specialized team members, the process is faster and more efficient.Action: Assign teams to different parts of the project, such as design, carving, inlay, and polishing, allowing parallel progress on multiple orders.
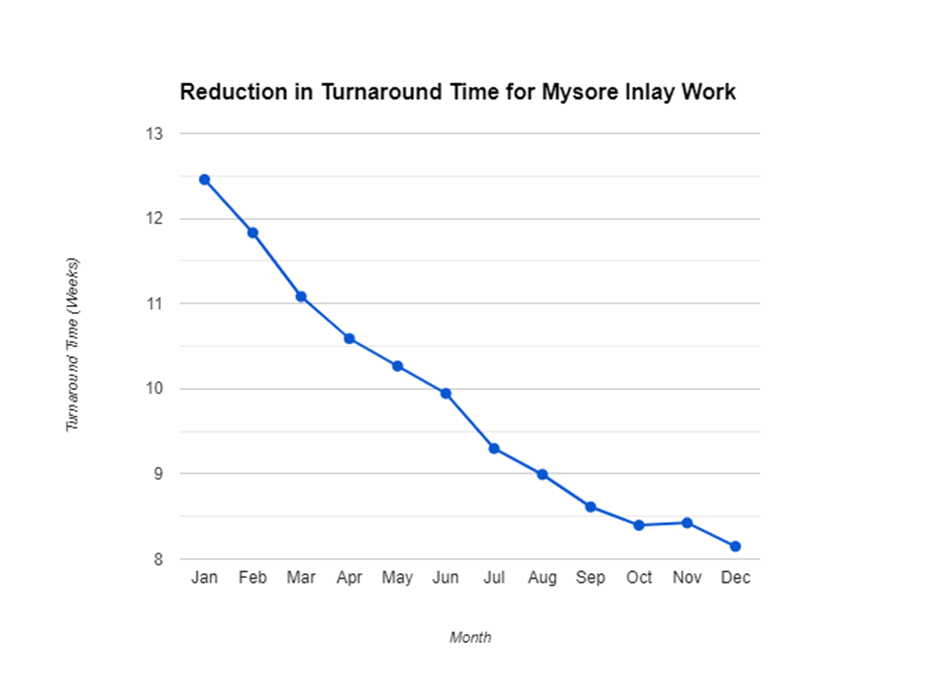
26. Navigating Payment Terms in Mysore Inlay Work
In the handmade industry, understanding payment terms is crucial for both artisans and buyers. Mysore inlay work artisans offer flexible payment schedules and clear terms of service, ensuring that financial agreements are fair for all parties involved. By providing transparency in their transactions, they build trust with their customers. This approach to payment terms makes it easier for buyers to invest in high-quality handmade products, knowing that the financial agreements are secure and transparent.
Q1: Why are clear payment terms important for both artisans and buyers in Mysore inlay work?
A: Clear payment terms are essential as they establish trust and mutual understanding between artisans and buyers. They ensure that both parties agree on the price, payment schedule, and conditions before production begins, preventing any disputes or misunderstandings. This transparency helps buyers feel secure when investing in high-quality handmade inlay work.
Q1: What kind of payment schedules do Mysore inlay artisans typically offer?
A: Mysore inlay artisans often provide flexible payment schedules that can be tailored to the buyer’s needs. Common options include upfront payments, 50-50 split payments (half upfront and half upon delivery), or installment plans for larger orders. These flexible terms help make the transaction easier for buyers while ensuring artisans receive timely payments.
Q3: How can buyers ensure that their financial transactions are secure when purchasing Mysore inlay products?
A: Buyers can ensure secure transactions by working with reputable artisans or businesses that provide clear terms of service, transparent pricing, and documented payment agreements. Using secure payment methods like bank transfers, digital wallets, or verified online platforms also adds a layer of protection for both buyers and artisans.
Q4: What should buyers look for in a payment agreement when purchasing Mysore inlay work?
A: Buyers should review the payment terms for clarity on pricing, deadlines for payment, any late payment penalties, cancellation policies, and delivery timelines. Ensuring that these details are documented and agreed upon before the transaction can protect both the buyer and the artisan, leading to a smooth purchasing experience.
27. Importance of Certifications in Mysore Inlay Work
Certifications play a key role in ensuring the authenticity and quality of Mysore inlay work. Industry certifications not only offer quality assurance but also confirm that the products comply with regulatory standards. Artisans who acquire these certifications can provide buyers with a sense of trust and reliability, ensuring that the handmade products meet established guidelines. This focus on certified handmade products helps maintain the reputation of Mysore inlay work as a high-quality craft aligned with global standards.
Role of Certifications in Mysore Inlay Work
Authenticity Assurance:
Certifications act as a seal of authenticity for Mysore inlay products. They confirm that the craftsmanship adheres to traditional methods and genuine materials, such as rosewood, are used. For buyers, certified products provide confidence that they are purchasing true, handcrafted Mysore inlay work, not imitations or mass-produced items.Impact: Certified products boost buyer trust, protecting the cultural heritage of the craft.
Quality Control:
Certified artisans must meet specific quality standards set by regulatory bodies. These standards cover the precision of craftsmanship, material quality, and finishing techniques. By adhering to these guidelines, artisans ensure that their work meets high-quality benchmarks, distinguishing it from lesser-quality alternatives.Impact: This guarantees buyers receive well-crafted, durable, and premium-quality products.
Regulatory Compliance:
Certifications ensure that artisans and their products comply with local and international regulations, such as environmental guidelines, ethical sourcing, and fair labor practices. This is particularly important for export markets where products must meet strict legal requirements.Impact: Regulatory certifications enable Mysore inlay products to enter global markets without legal hurdles, ensuring smooth trade and export processes.
Market Competitiveness:
In an increasingly competitive market, artisans with certifications stand out as trustworthy and professional. Certified products often attract more buyers, especially those who prioritize ethical and sustainable craftsmanship. For artisans, certifications can open doors to premium markets, exhibitions, and international buyers seeking high-quality, certified goods.Impact: Certifications give Mysore inlay artisans a competitive edge, enhancing their marketability and opportunities for growth.
By obtaining certifications, Mysore inlay artisans ensure that their products meet high standards of authenticity, quality, and compliance. This not only builds buyer confidence but also helps maintain the craft’s reputation and opens new market opportunities, both locally and globally.
28. Logistics - Efficient Supply Chain Management
Efficient supply chain management is essential for Mysore inlay artisans to reduce costs, manage inventories effectively, and ensure timely deliveries. By optimizing logistics processes, artisans can better track raw materials like rosewood and deliver finished products to both domestic and international markets. A streamlined supply chain ensures timely fulfillment of orders without sacrificing the quality or craftsmanship of the inlay work, allowing artisans to meet market demands while staying competitive. write the steps for effective loggistics management by the artisans
Steps for Effective Logistics Management by Mysore Inlay Artisans:
Demand Forecasting and Planning:
Understand market trends and customer demand for inlay products.
Use sales data to predict future orders, ensuring efficient procurement of raw materials like rosewood.
Supplier Relationship Management:
Establish strong relationships with trusted suppliers for consistent and timely access to quality raw materials.
Negotiate favorable terms for sourcing wood, inlay materials, and other supplies.
Inventory Management:
Implement an efficient inventory system to track stock levels of raw materials and finished products.
Regularly update inventory to avoid overstocking or shortages, which can disrupt production schedules.
Production Scheduling:
Create clear production timelines based on order volume and deadlines.
Ensure that artisans and workers are aligned with the production schedule to optimize output without compromising quality.
Packaging and Quality Control:
Develop standardized packaging methods to protect delicate inlay products during shipping.
Perform quality checks at every stage of the process to ensure that products meet high craftsmanship standards before delivery.
Optimizing Transportation:
Choose reliable transportation providers for timely delivery, whether shipping domestically or internationally.
Optimize shipping routes and consolidate shipments to reduce transportation costs and minimize delays.
Technology Integration:
Use software tools for tracking shipments, monitoring inventory levels, and improving supply chain visibility.
Implement tracking systems to allow real-time updates on deliveries and manage potential delays proactively.
Customs and Compliance Management:
Ensure adherence to customs regulations, especially for international shipments.
Prepare necessary documentation and certificates, including proof of the origin of materials and compliance with trade regulations.
Risk Management:
Identify and mitigate potential risks, such as delays in raw material supply or transport disruptions.
Create contingency plans to handle unforeseen issues in logistics, such as delays in shipping or sudden demand surges.
Continuous Improvement and Feedback:
Regularly evaluate the logistics process and seek feedback from customers to identify areas for improvement.
Adapt strategies based on changing market conditions, customer preferences, and new technology solutions for better efficiency.

By following these steps, Mysore inlay artisans can optimize their logistics management, resulting in cost-effective operations, satisfied customers, and sustained business growth.
29. Customs and Duties - Understanding Customs and Duties
Understanding customs and duties is crucial for artisans involved in the export of Mysore inlay work. Navigating import tariffs, trade agreements, and duty drawbacks allows artisans to optimize their pricing strategies for international buyers. Awareness of customs regulations not only helps reduce unforeseen costs but also ensures smoother transactions across borders. By complying with these regulations, artisans can expand their global reach and enhance the appeal of their handcrafted inlay products in international markets.
Q: What are customs and duties, and why are they important for Mysore inlay artisans?
A: Customs are the authorities that regulate the flow of goods across borders, while duties are taxes imposed on imported or exported goods. For Mysore inlay artisans, understanding customs and duties is important to ensure that their products comply with international trade laws, avoid costly fines, and set competitive prices for global buyers.
Q: How can artisans navigate import tariffs when exporting inlay products?
A: Artisans should familiarize themselves with the tariffs applied in their target markets. They can research trade agreements between India and importing countries that may reduce or eliminate tariffs. Additionally, hiring a customs broker can help them navigate complex tariff structures and minimize costs.
Q: What are trade agreements, and how can they benefit artisans?
A: Trade agreements are contracts between countries that reduce trade barriers, such as tariffs and quotas. Artisans can benefit from these agreements by gaining access to lower tariffs or duty-free entry in certain markets, making their inlay products more price-competitive internationally.
Q: What is duty drawback, and how can it benefit artisans?
A: Duty drawback is a refund of customs duties paid on imported materials used in the production of goods that are then exported. For example, if artisans import certain tools or materials for making inlay work and later export the finished products, they may be eligible for a refund of the import duties, reducing overall costs.
Q: How do customs regulations affect pricing strategies for international buyers?
A: Customs duties add to the cost of exporting goods. Artisans must factor these costs into their pricing strategies to ensure they remain profitable while staying competitive in international markets. Clear understanding helps avoid pricing errors that might reduce profit margins or make products too expensive for global buyers.
Q: What documents are required for customs clearance when exporting Mysore inlay products?
A: Essential documents include a commercial invoice, packing list, bill of lading, certificate of origin, export license, and any applicable certifications (e.g., wood sourcing). These documents help customs authorities verify the authenticity and value of the goods, ensuring smooth clearance.
Q: How can compliance with customs regulations expand an artisan’s global reach?
A: Complying with customs regulations ensures timely delivery of products and builds trust with international buyers. Adhering to import/export laws and standards can open new markets, allowing artisans to sell their handcrafted inlay products globally without legal or logistical hindrances.
Q: What role does proper HS (Harmonized System) coding play in customs?
A: HS codes are internationally standardized numerical codes that classify products for customs purposes. Using the correct HS code for inlay products helps customs authorities determine the applicable duties and taxes. Misclassification can lead to penalties or delays.
Q: What are some common challenges artisans may face with customs duties?
A: Artisans may encounter issues such as unexpected customs fees, changes in trade policies, lengthy clearance times, or incorrect paperwork. These challenges can delay shipments and increase costs, making it crucial for artisans to stay informed and work with customs experts when needed.
By thoroughly understanding customs and duties, Mysore inlay artisans can optimize their pricing, avoid regulatory setbacks, and effectively expand their presence in international markets.
30. Anti-Money Laundering - Ensuring Compliance with AML Regulations
To maintain ethical standards and gain buyer trust, artisans in the Mysore inlay industry must comply with anti-money laundering (AML) regulations. By implementing internal controls and undergoing regular training, businesses ensure they operate within legal frameworks, reducing the risk of financial crimes. Ensuring compliance with AML laws is particularly important as Mysore inlay work gains global recognition, as it reassures international buyers of the authenticity and legitimacy of the products.
Benefits of AML Compliance in the Mysore Inlay Industry:
Increased International Sales:
AML-compliant businesses are seen as reliable partners in international markets, which can lead to increased sales and business opportunities. Buyers prefer artisans who adhere to financial regulations, ensuring safe and lawful transactions.
Improved Risk Management:
Implementing AML controls helps businesses identify and mitigate financial risks early on. This leads to a more secure operating environment, reducing the likelihood of involvement in illegal financial activities.
Reputation and Brand Value:
Consistent compliance with AML laws boosts the brand reputation of Mysore inlay artisans. A good reputation attracts more clients, partners, and investors, and it ensures long-term sustainability in the competitive global market.
Seamless Financial Operations:
AML-compliant businesses are less likely to face transaction delays or banking restrictions, ensuring smooth financial operations. Banks are more willing to support companies that comply with financial regulations, allowing artisans access to efficient payment and lending services.
Compliance with International Standards:
Adhering to AML regulations ensures alignment with global financial standards, making it easier to collaborate with international buyers, wholesalers, and retailers. It also positions artisans as professional and reliable, able to compete in a broader marketplace.
Transparency and Accountability:
Implementing AML policies encourages transparency in financial dealings, helping businesses monitor their cash flow and identify suspicious activities. This leads to a stronger, more accountable financial system within the Mysore inlay industry.
Conclusion:
By ensuring compliance with AML regulations, artisans in the Mysore inlay industry can maintain ethical standards, build trust with international buyers, and safeguard their businesses from financial crime risks. This compliance is not only a legal requirement but also a strategic advantage that enhances their reputation and business opportunities in global markets.
31. Innovation - Implementing Innovative Manufacturing Techniques
Mysore inlay artisans are embracing innovation to stay relevant in an evolving marketplace. By adopting new manufacturing techniques, integrating modern tools, and investing in research and development, artisans can improve the efficiency of their processes while maintaining the traditional beauty of inlay work. These innovations allow for enhanced precision in craftsmanship, the creation of more intricate designs, and the ability to cater to contemporary tastes without losing the essence of the craft.
Mysore inlay artisans are blending tradition with innovation to enhance their craftsmanship while keeping the rich heritage of inlay work intact. These innovations help artisans improve the efficiency of their production, meet the growing demands of modern markets, and preserve the intricate beauty of their craft. Below are some key innovative techniques being adopted by Mysore inlay artisans:
1. CNC (Computer Numerical Control) Machines for Precision Cutting:
Technique: CNC machines are used to cut and engrave intricate designs with high precision.
Benefit: This reduces manual effort while ensuring that complex patterns are perfectly replicated. The use of CNC technology allows artisans to create intricate inlay work that would otherwise be too time-consuming or difficult by hand.
2. Laser Cutting and Engraving:
Technique: Laser cutting tools are employed for detailed engraving and cutting, enabling the artisans to work with high accuracy on delicate materials like wood and ivory substitutes.
Benefit: Laser technology ensures consistent results across multiple products, helping artisans meet bulk orders without compromising on the quality of craftsmanship.
3. Digital Design Software:
Technique: Digital design software (such as CAD or Adobe Illustrator) is used to create virtual prototypes of inlay designs before production.
Benefit: This enables artisans to experiment with new patterns and materials without wasting resources. Clients can also preview and request changes to designs before the actual manufacturing process begins.
4. Sustainable Material Sourcing:
Technique: Artisans are switching to sustainable and eco-friendly alternatives for traditional materials like ivory and rare woods. For example, the use of plant-based resins or recycled wood ensures that the inlay industry reduces its environmental footprint.
Benefit: Sustainable materials allow artisans to cater to eco-conscious buyers while maintaining the aesthetic appeal of traditional inlay products.
5. Use of 3D Printing Technology:
Technique: 3D printing is being incorporated to create prototypes or molds for new inlay designs, especially for intricate and repetitive elements.
Benefit: 3D printing speeds up the design process, enabling artisans to experiment with new techniques and produce highly customized, detailed designs.
6. Hybrid Manufacturing Techniques:
Technique: Artisans are combining traditional handcrafting methods with automated processes, where machines handle repetitive tasks, and the final intricate details are finished manually.
Benefit: This hybrid approach maintains the authenticity of handcrafted products while boosting production efficiency and consistency, especially for larger orders.
7. Advanced Polishing and Finishing Tools:
Technique: Modern polishing tools such as rotary sanders and specialized buffing machines are used to ensure a smooth, high-quality finish.
Benefit: These tools reduce manual labor, enhance the final appearance of the inlay work, and ensure durability and shine for a longer-lasting product.
8. Integration of Modern Design Trends:
Technique: Artisans are incorporating contemporary design trends like minimalist patterns, geometric shapes, and fusion styles that combine traditional motifs with modern aesthetics.
Benefit: By staying attuned to global design trends, Mysore inlay artisans can cater to a wider range of customers, especially in international markets, while preserving their cultural identity.
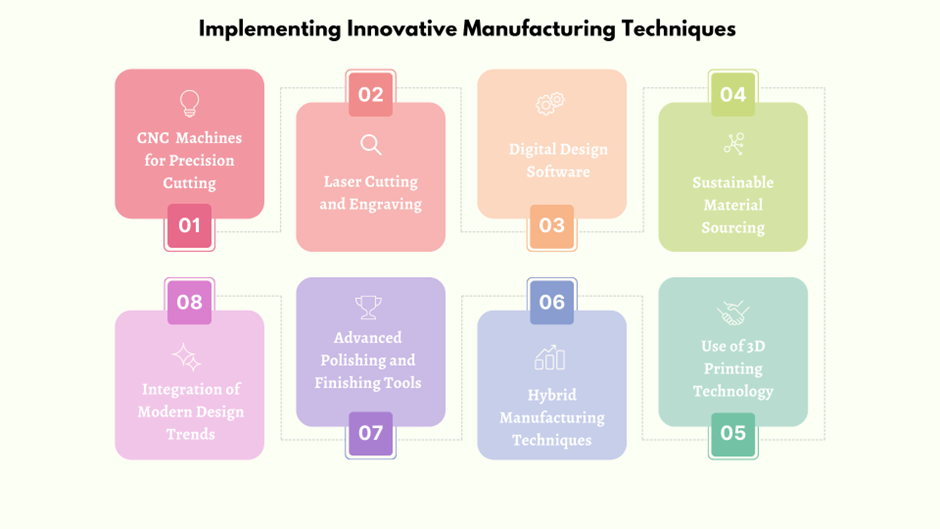
32. Risk Management - Identifying and Mitigating Risks
Managing risks is essential for the sustainability of Mysore inlay work, given the unpredictability in supply chains, raw material costs, and market demands. Artisans mitigate risks by conducting thorough risk assessments, implementing contingency plans, and securing appropriate insurance. These strategies help protect against disruptions in production, ensure consistent product quality, and maintain financial stability, allowing artisans to continue their craft without facing significant setbacks.
Risk Management Techniques in the Mysore Inlay Industry
In the Mysore inlay industry, artisans face various risks, from fluctuating raw material prices to unpredictable market trends. To safeguard their craft and business, artisans implement several risk management techniques that help mitigate these risks while ensuring the long-term sustainability of their operations.
1. Diversification of Raw Material Suppliers:
Technique: Artisans establish relationships with multiple suppliers to diversify their sources for raw materials such as rosewood, resin, and inlay stones.
Impact: By reducing reliance on a single supplier, artisans can avoid disruptions in production due to supply shortages or price fluctuations. This ensures that they can continue creating inlay products even when one supplier faces challenges.
2. Price Hedging for Raw Materials:
Technique: Artisans or business managers use financial instruments to lock in prices for essential raw materials, protecting against future price volatility.
Impact: Hedging helps artisans maintain consistent production costs, which prevents sudden spikes in material expenses. This stability allows them to plan their budgets more accurately and offer more competitive pricing to buyers.
3. Inventory Management Systems:
Technique: Implementing modern inventory management software to track and manage stock levels of raw materials and finished goods.
Impact: Efficient inventory management minimizes the risk of stockouts or overstocking, optimizing resources and ensuring timely production. This helps artisans avoid production delays and manage their supply chain more effectively.
4. Market Research and Demand Forecasting:
Technique: Artisans use market research tools and demand forecasting to predict trends and changes in consumer preferences.
Impact: By staying ahead of market trends, artisans can adjust their production to meet demand for specific designs, styles, or products. This reduces the risk of unsold inventory and ensures they remain relevant in both domestic and international markets.
5. Contingency Planning:
Technique: Developing contingency plans for potential disruptions, such as delays in raw material shipments or sudden changes in market demand.
Impact: Contingency planning allows artisans to react quickly and effectively to unforeseen events, minimizing the impact on production timelines and maintaining customer satisfaction. For instance, artisans may switch to alternative materials or adapt production processes in response to supply chain disruptions.
6. Quality Control Protocols:
Technique: Establishing strict quality control measures throughout the production process, from sourcing raw materials to final product inspection.
Impact: Maintaining consistent quality in inlay products helps artisans build and retain customer trust. By reducing the risk of defective products, they minimize returns, complaints, and potential financial losses due to low-quality goods.
7. Securing Insurance for Business and Inventory:
Technique: Artisans obtain comprehensive insurance coverage for their workshops, tools, raw materials, and finished products.
Impact: Insurance helps protect against financial losses due to accidents, natural disasters, theft, or damage. This ensures that artisans can recover quickly from unexpected events and continue their operations without facing significant setbacks.
8. Financial Risk Management Through Savings and Credit Facilities:
Technique: Artisans maintain a savings buffer or access credit facilities to manage financial risks, such as sudden business expenses or a slowdown in sales.
Impact: Having a financial buffer allows artisans to cover operational costs during lean periods, reducing the risk of cash flow problems. Credit facilities also provide artisans with the liquidity needed to purchase raw materials or invest in new tools and techniques.
9. Compliance with Legal and Regulatory Requirements:
Technique: Staying up to date with regulations on labor, environmental laws, and export-import compliance to avoid penalties or legal issues.
Impact: Compliance with regulations ensures that artisans do not face business interruptions or legal challenges, particularly in international trade. This helps protect their reputation and maintain smooth operations across borders.
10. Collaboration and Networking:
Technique: Artisans collaborate with other inlay producers, trade organizations, and industry experts to share information, resources, and best practices.
Impact: By forming networks, artisans can collectively address industry-wide risks such as market downturns, regulatory changes, or resource shortages. Collaboration also opens up opportunities for joint ventures, shared innovation, and improved market access.
Conclusion:
By adopting these risk management techniques, Mysore inlay artisans can effectively identify and mitigate risks related to their production, supply chain, finances, and market demands. These strategies not only ensure the continued success of their craft but also strengthen their resilience in a rapidly changing and competitive global market.
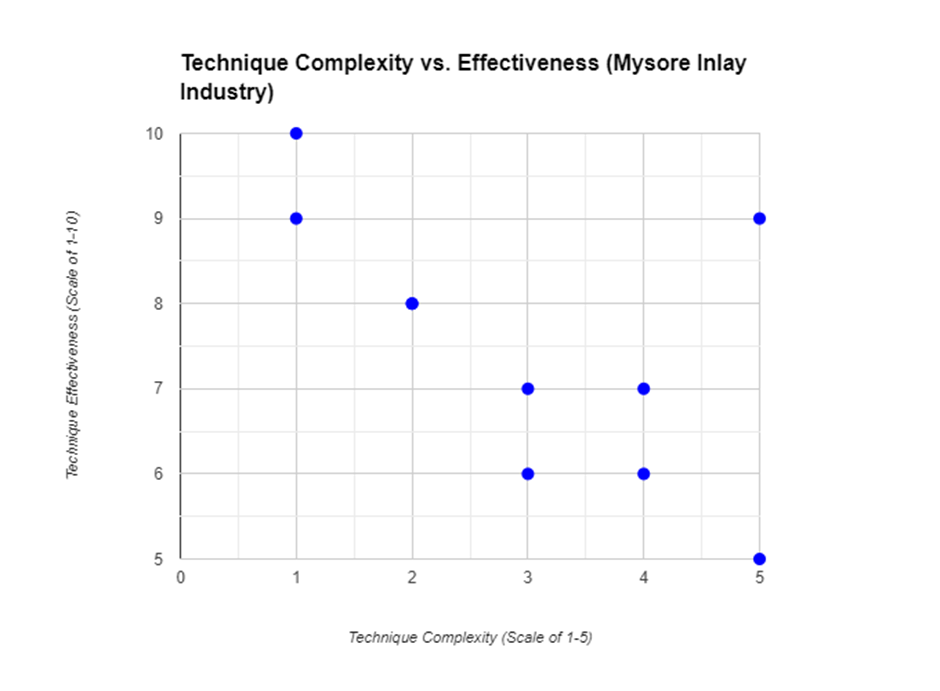
33. Digital Marketing - Leveraging Digital Marketing for Growth
Digital marketing has become an invaluable tool for promoting Mysore inlay work to a broader audience. Artisans can use social media platforms, content marketing, and e-commerce websites to showcase their handcrafted products to both local and international buyers. By building a strong online presence and engaging with customers through targeted marketing strategies, artisans can significantly expand their market reach, boost sales, and raise awareness about the rich tradition behind their inlay work.
Digital marketing is key to promoting Mysore inlay work globally. Artisans can use platforms like Instagram and Facebook to showcase their products through images, videos, and live demonstrations, engaging audiences and building brand awareness. Content marketing, including blog posts about the craft's history, helps educate customers, while e-commerce platforms like Etsy and Amazon allow for direct sales.
Email marketing and influencer partnerships help artisans maintain customer engagement and expand their reach. Video marketing on platforms like YouTube and TikTok highlights craftsmanship, while search engine ads drive traffic to online stores.
By embracing analytics and data-driven marketing, artisans can optimize strategies and increase visibility. Digital marketing enables them to reach a wider audience, boost sales, and grow their business without losing the craft’s traditional essence.
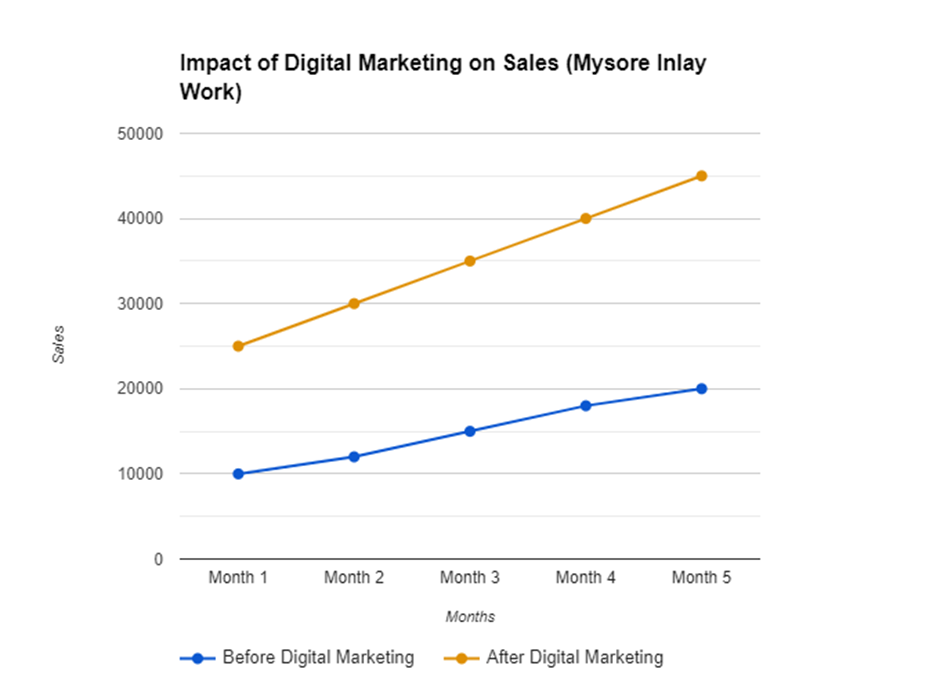
34. Insurance - Insurance Solutions for Manufacturers
Insurance plays a crucial role in protecting Mysore inlay artisans from unforeseen risks, such as damage to raw materials, equipment, or finished products. Artisans can secure coverage for various aspects of their business, including property, liability, and product insurance. Having the right insurance solutions in place safeguards against potential financial losses, ensuring that artisans can focus on their craft without worrying about unexpected disruptions.
Q: Why is insurance important for Mysore inlay artisans?
A: Insurance protects artisans from financial losses due to unexpected events such as damage to raw materials, tools, or finished products. It offers security and peace of mind, allowing artisans to focus on their craft without worrying about potential disruptions.
Q: What types of insurance are relevant to inlay artisans?
A: Key insurance types include:
Property Insurance: Covers damage to the workshop, tools, and materials.
Liability Insurance: Protects against claims of injury or damage caused by the products.
Product Insurance: Provides coverage for lost or damaged finished products during storage or transportation.
Q: How does insurance benefit the business financially?
A: Insurance helps mitigate the financial impact of unforeseen events, reducing out-of-pocket expenses that could otherwise disrupt production or force artisans to halt operations. It ensures business continuity and long-term stability.
Q: Can insurance help expand the business?
A: Yes, having comprehensive insurance can enhance trust with international buyers, as it shows the business is reliable and well-prepared for risks, making it easier to enter new markets.
Q: What should artisans consider when selecting insurance?
A: Artisans should assess the value of their equipment, materials, and products, and consider risks specific to their craft, such as fire or theft. It’s also important to understand policy terms and ensure coverage fits their unique needs.
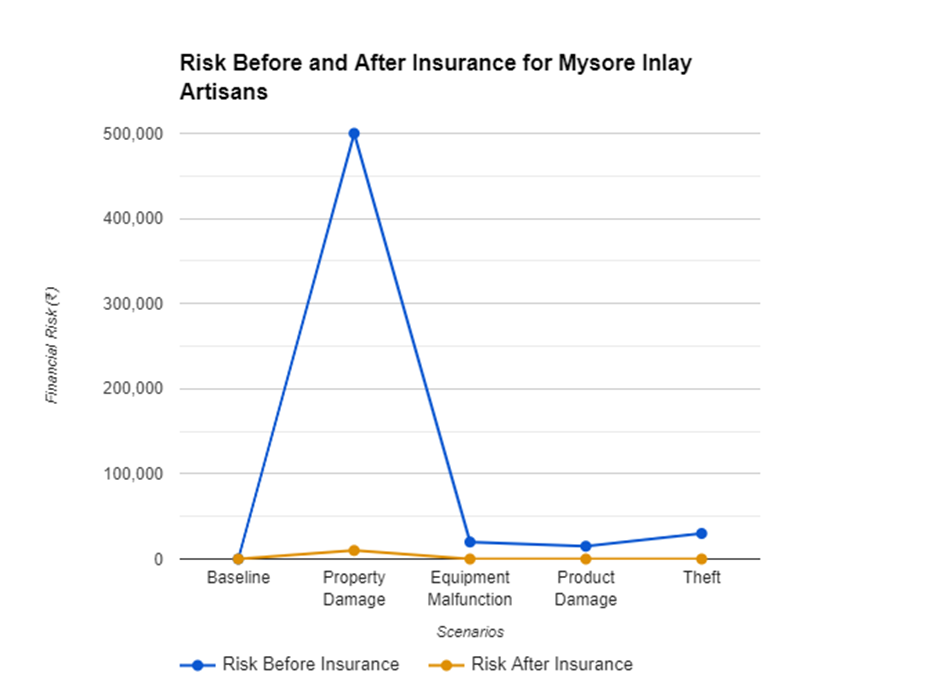
35. Conclusion: The Enduring Legacy of Mysore Rosewood Inlay Work
Mysore’s rosewood inlay work stands as a testament to India’s rich cultural heritage and exceptional craftsmanship. From its historical roots in Persian art to its prominence in Tipu Sultan’s reign, this craft has evolved while staying true to its traditional techniques. Today, thanks to initiatives by the Karnataka government and organizations like KSHDC, inlay work continues to thrive, offering beauty, history, and artistry to those who appreciate fine craftsmanship. Whether you’re an art collector, a history enthusiast, or simply someone looking for unique home decor, Mysore’s rosewood inlay work offers something truly special.
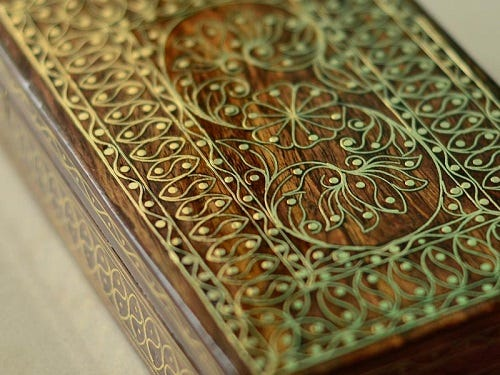
36. Citiation
Name of the original Author - Professor Bibhudutta Baral and Sowmya B.N.
Title of the Paper - Inlay Work- Mysore, Karnataka
University/Institue Name - National Institute of Design (NID), Bengaluru
Link to the Paper
Recommended
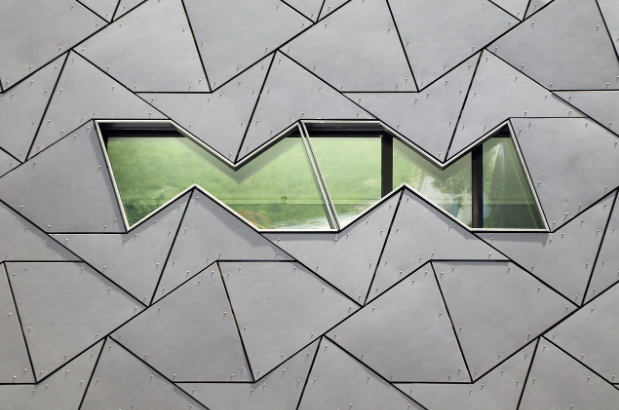

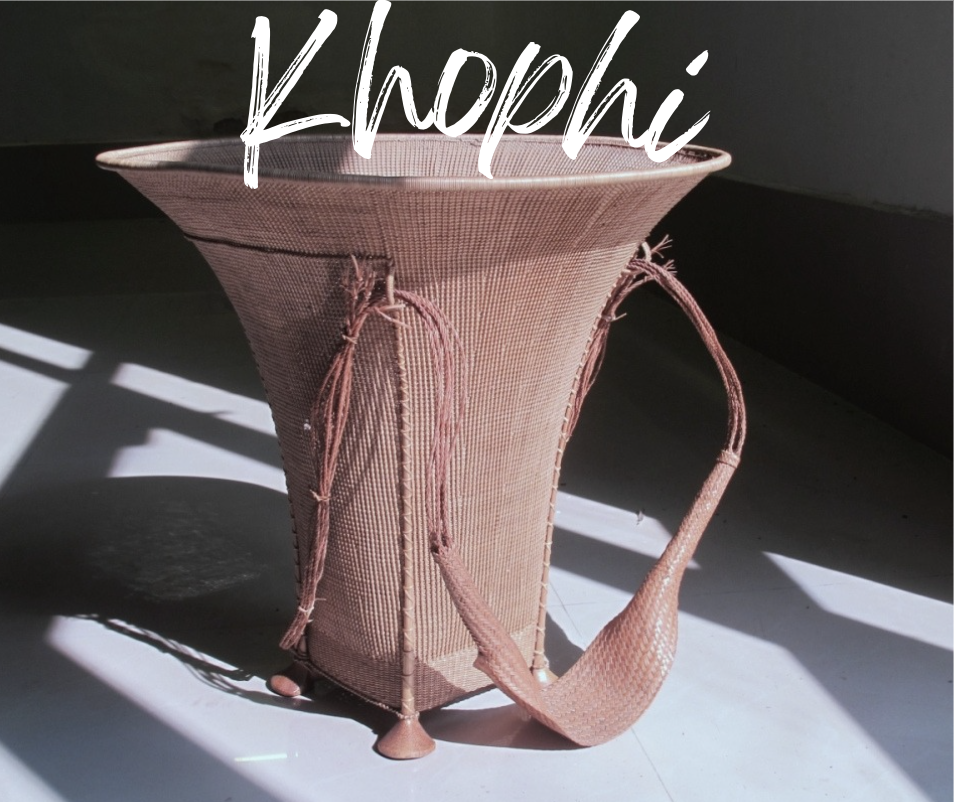