Investigation Of Quality Failures
Sep 17, 2023 | Medini Perera
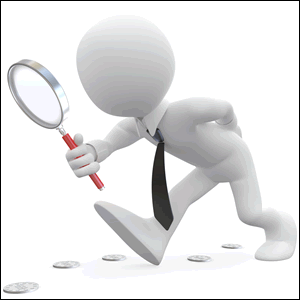
The period from when a product is initially discovered to its formal recall announcement is known as the "discovery-to-recall" period. Due to the fact that businesses must continually balance several conflicting objectives during the recall process, choosing when to recall is not an easy issue. General Motors was hit with a $35 million fine in 2014 for its tardiness in fixing the ignition switch issue that affected millions of cars.
We look at how five recall factors affect how quickly a recall occurs in the American auto sector. These characteristics include the origin of the initial defect report, the defect's nature, the total number of affected vehicle models, and the number of prior company recalls.
Our findings provide light on the timing of recall announcements by businesses following the initial disclosure of a flaw. According to a study, the six top manufacturers' average time from discovery to recall is 6.37 months, with a minimum of 1 month and a maximum of 39 months. The average recall length for Nis-san, who experienced the fewest automaker neurological issues of the six, is 6.27 months. To hasten recall investigations, we advise businesses to make improvements to communication, traceability, and supply-chain visibility.
Hypothesis
1. When the fault is initially disclosed externally (by NHTSA or customers) as opposed to internally (by the car company), the time from discovery to recall is greater.
2. When suppliers, rather than car firms, are to blame for product flaws, the discovery-to-recall process takes longer.
3. When the flaw is related to the design rather than the manufacturing, the discovery-to-recall period is longer.
4. The time from discovery to recall increases as more vehicle models are involved.
5. The time from discovery to recall gets shorter as the automaker experiences more recalls.
Results
We projected that when issues come from suppliers or are first reported outside, the automaker must work together with the outside parties to conduct joint investigations in order to identify the underlying causes and create appropriate fixes. This study specifically analyses circumstances in which information needed for problem-solving also lives outside of the organization by looking at the source of the initial defect report and the party liable for the defect.
We discover that supplier-caused recalls, as opposed to those caused by automakers, can be more expensive since they take longer to implement. Conducting a recall examination of supplier-caused issues gets more difficult with a complex supply chain structure. We emphasize the need to apply problem-solving theory to pinpoint the traits of quality issues and consider how these traits could shorten the time required for quality improvement projects.
Managerial Implications
Regarding the time between the initial notification of suspected flaws and the announcements of recalls, automakers should properly define expectations for stakeholders. It is possible to classify a lot of product recall situations as "poorly understood and participants may be in conflict" (Daft & Lengel, 1986). To track problems reported by outside sources, businesses should utilize standardized glossaries and templates.
To increase the likelihood of finding manufacturing flaws internally, businesses should strengthen their quality management and quality control procedures. Automobile manufacturers could search discussion boards, Facebook, and Twitter for potential quality issues using automated flaw results that it takes longer for suspected faults to be discovered and recalled when they are first reported externally rather than internally recommends that automakers should work with authorities to close the information gap.