Guidelines On Furniture Manufacturing Sustainability In Southeast Asia
Jun 27, 2022 | Abdul Rahman
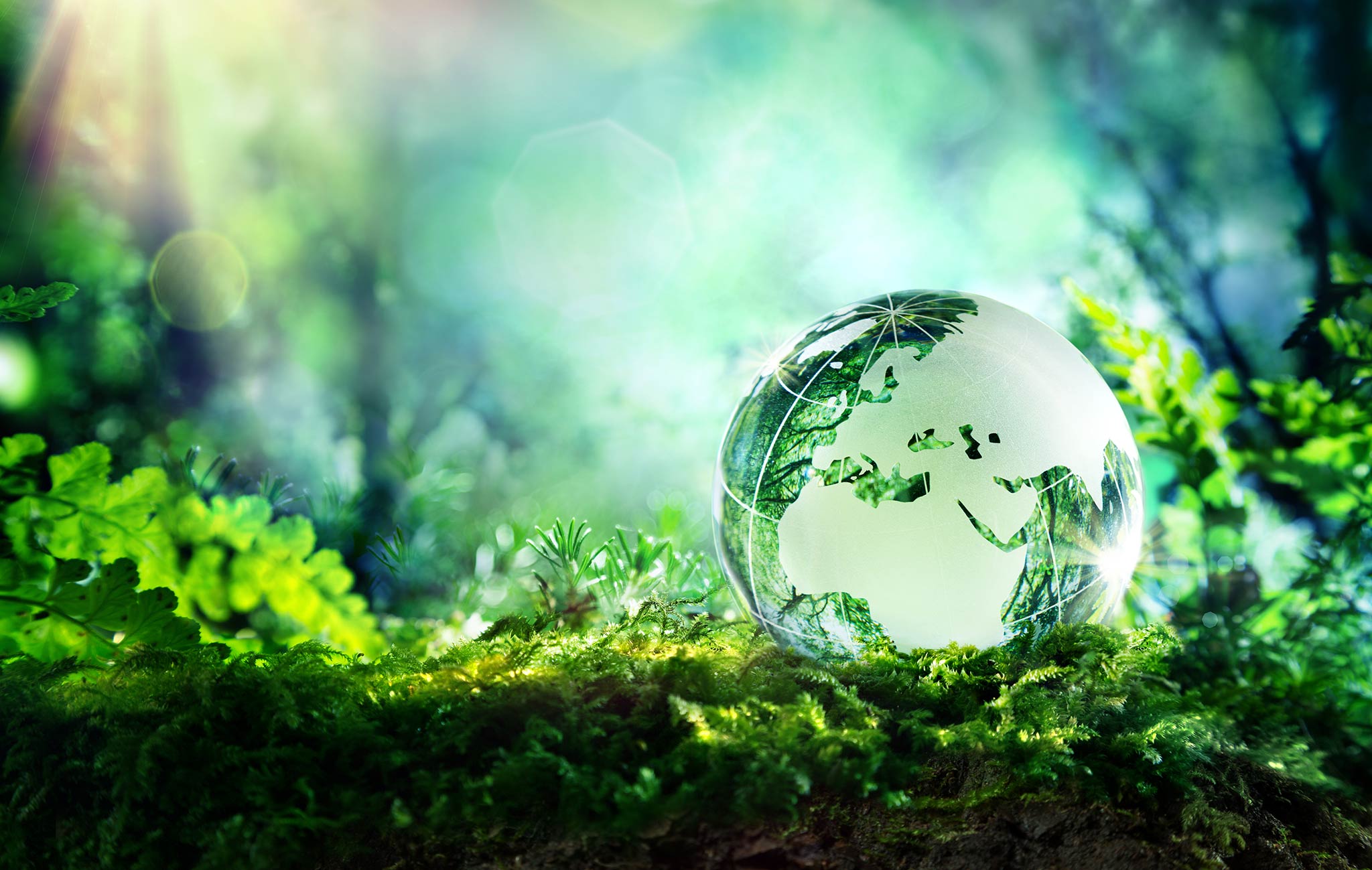
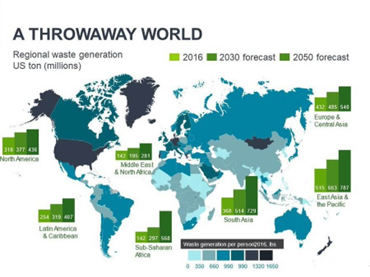
Source: https://miniwiz.medium.com/7-important-recycling-statistics-from-around-the-world-53ac9d3b783c
As shown in the diagram, overall regional waste generation is led by Asian countries. Therefore, the 3R method - reduce, reuse and recycle can be applied to help keep the world less polluted. Sure, it is hard to come up with an idea on how to implement 3R in waste handling, but it is necessary to adapt to the current situation of the world both in economics and ecosystems. For example, a ‘reuse’ method for wooden furniture manufacturing is by benefiting the sawdust and spare wood pieces. This can be done by using the sawdust as planting medium so an alternate business can be done; i.e. selling ornamental plant shoots. In Indonesia, another approach is that the solid waste is used for cultivation of oyster mushrooms and the mushroom is easy to cultivate and the demand of oyster mushrooms in the country is high due to culinary purposes. Additional resources may apply so an intensive calculation and analysis is required so that the best approach is executed.
2. Furniture Features
Aside from reading Rural Handmade’s article on Furniture Manufacturing Style And Techniques In Different Parts Of The World to gain insight on furniture manufacturing designs, it should be acknowledged that office furniture has exquisite commercial value and worldwide marketability with the Southeast Asia region as the best potential manufacturing candidate.
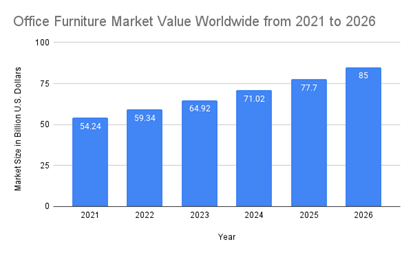
Source: https://www.statista.com/statistics/1062726/office-furniture-market-value-worldwide/
Upon the working-from-home trend due to the pandemic, the office furniture market value has increased and is estimated to keep increasing in the future years as everyone is buying furniture for their own personal working space in their home. Therefore, it is ideal to focus on the features of office furniture to have a better opportunity in the global furniture export market. Although wooden furniture is considered to be highly expandable in the sales, reports said that wooden chairs are not comfortable and wooden products are extremely fire hazardous. So, metal furniture is manufactured instead as metal was seen as safer material and inherits the sturdiness of the wooden furniture. Nowadays, office furniture is often found to be a combination of woods and metals in the form of steel for better strength and anti-rusting. Plastic furniture is also available but plastics are not environmentally-friendly as they are highly non-degradable and release toxic chemicals when incinerated.
Alongside with the material choice, the physical features also play a role in determining a good office furniture product. Such an intention is to instill an ergonomic aspect into the furniture product. This can be done by designing a chair that is suited for a human body. This means that the chair should allow a more natural sitting posture, with less stress to the back, shoulders, legs and arms with adjustability. Therefore, the risk of getting carpal tunnel syndrome is lowered due to incorrectly positioned wrists as this is the most common injury for day-to-day office workers. For desk or table products, they should be able to be raised and lowered either manually or automatically. This will allow office spaces to be created or removed depending on the need of the user. Furthermore, with the installation of technology in this modern era, the desk or table should have holes or tracks for Ethernet wiring and electrical cords. Another optional feature is the ability to easily be disassembled and reassembled at will to meet changing needs.
And lastly, of course the furniture product must have good artistic and stylish value as well. This element is very abstract and every furniture manufacturing company should have their own ‘style’ that can become their company identity so that the design can be iconic and memorable. This will eventually increase the number of sales due to the increased number of interested customers. One great example of this is IKEA which has unique names for every one of their furniture products although they are just regularly fashioned.
3. Index and Indicators
To ensure that the manufacturing process is fully safe to the environment, many different index and indicators are used. This means that the level of environmental impact of an industry can be determined by utilizing the formulas of these index and indicators with the values gained from the industry’s methodological data collection.
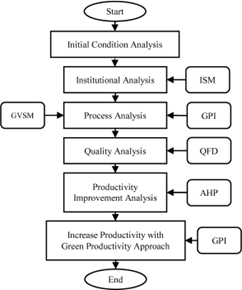
The diagram above shows the flowchart of the Green Productivity Improvement Model proposed by Marimin on their case study at rubber smallholders plantation. The model requires several analytic tools such as Interpretive Structural Modeling (ISM), Green Productivity Index (GPI), Quality Function Deployment (QFD) and Analytical Hierarchy Process (AHP). You can read more on the other tools later but in this section, we’re going to focus on the GPI tool. The GPI tool is that can help measure the environmental impact and economical state of a manufacturing for finding improvement and productivity increase opportunities by using following formula:
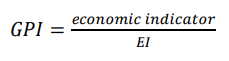
Whereas, the economic indicator formula and Environmental Impact (EI) formula are:

Revenue is the amount of profit or income gained and cost is the amount of expenses needed for a cycle of product manufacturing. A cycle of product manufacturing is the data collected for a set amount of product made.
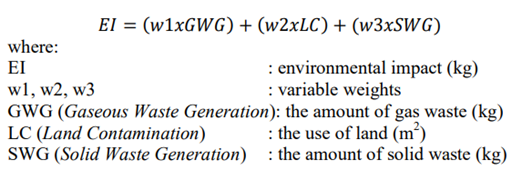
For the EI formula, several variables must be declared first which are the Gaseous Waste Generation (GWG), Land Contamination (LG) and Solid Waste Generation (SWG). GWG, LG, SWG values are variable depending on the number of indicators used by a case study. The weights (w1, w2, w3) are denoted from the Environmental Sustainability Index (ESI).
Example of GPI calculation:
(This case study, Water Consumption, WC is used instead of LC and a cycle is 1kg of liquid metal production)
Firstly, a few indicators is selected from ESI with its weight for the industrial environmental impact measuring:
After that, the values of w in the EI formula can be calculated:
From the case study,
WC = 1.5465kg
SWG = 0.904kg
GWG = 0.087kg
Using the EI formula:
EI = 0.17(0.904) + 0.5(0.087) + 0.33(1.5465) = 0.7075kg
Then, the economic indicator and GPI can be further calculated. There are two analyses of GPI. If the GPI is less than 1, then the environmental impact is greater than the level of the companies’ productivity. Otherwise, the value indicates that the product is poorly eco-friendly.
4. Safety and Health
Working environment plays a vital role in keeping the work up and going all day long. Also often being overlook, the working environment determines the condition of the workers and therefore their productivity output. Accidental deaths and injuries may occur if this aspect is neglected so initial steps must be taken to avoid them. Such ways of avoiding these is by examining the machines and tools used by the workers. First of all, the machines used must have their wastes deposited at a certain spot so it doesn’t scatter. This is so that there is hygienic value upon the working site and allows a more conducive working area. If there is organic water wastes around, it will decay and become a spot for pathogenic bacterial growth which will attract diseases and spread bacterial infections. Next, the workers must also be equipped with the proper attire correlating to the manufactured material for safety. For example, wood wastes create dust so the workers should have masks on when in the working zone or the working area should have a well-accommodated aeration system to keep the dust away.
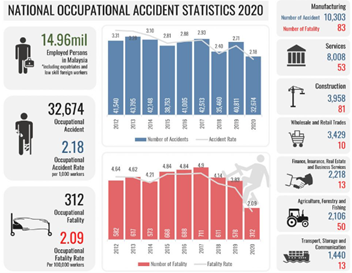
Source: Big Data Analytics: National Occupational Accident Statistics 2020
The statistics show the rate of accidents in Malaysia from 2012 until 2020. So one can assume that they have good safety and health guidelines for working employees as the chart is decreasing over time. Here are some main safety guidelines provided by the Ministry of Human Resources Malaysia in the Department of Occupational Safety and Health:
Identifying the hazardous factors
Identifying steps to reduce hazard impacts on people and surrounding
Providing sufficient information, training and equipments to on-site workers for their safety
Providing and updating emergency plans to handle dire hazards
The document also provides in-depth details on each step and examples for further understanding and utilization. These guidelines are mandatory for employers in Malaysia as stated in the Occupational Safety and Health Act 1994 (Act 514). Although this act is centralized for Malaysians, it is obvious to ensure the workers’ safety and health for every other region nevertheless.
Closure
In conclusion, Southeast Asia is a domain waiting for improvements and innovations. Some company productivity can be increased by connecting small businesses to create a collaborative team of greatness or targeting leading buyer groups which are in the education and health care sectors. Environmentalism is also important because not only does it help save the environment, but customers are also attracted to eco-friendly products as they want to play their own roles too in fighting for nature. Keep follow-up with the successful companies such as Herman Miller, HNI Corporation, Steelcase, Inc. and Knoll, Inc to gain more insights on what steps they did in order to achieve better marketability and sales. Last but not least, the most vital factor is always taking the first step.
Recommended

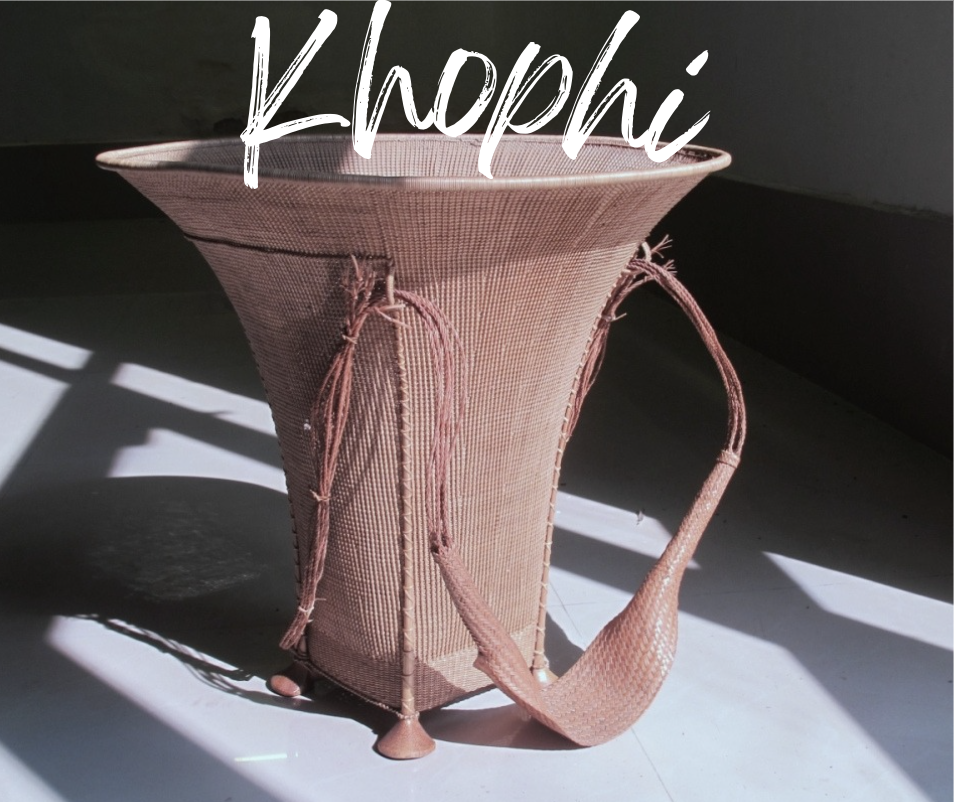
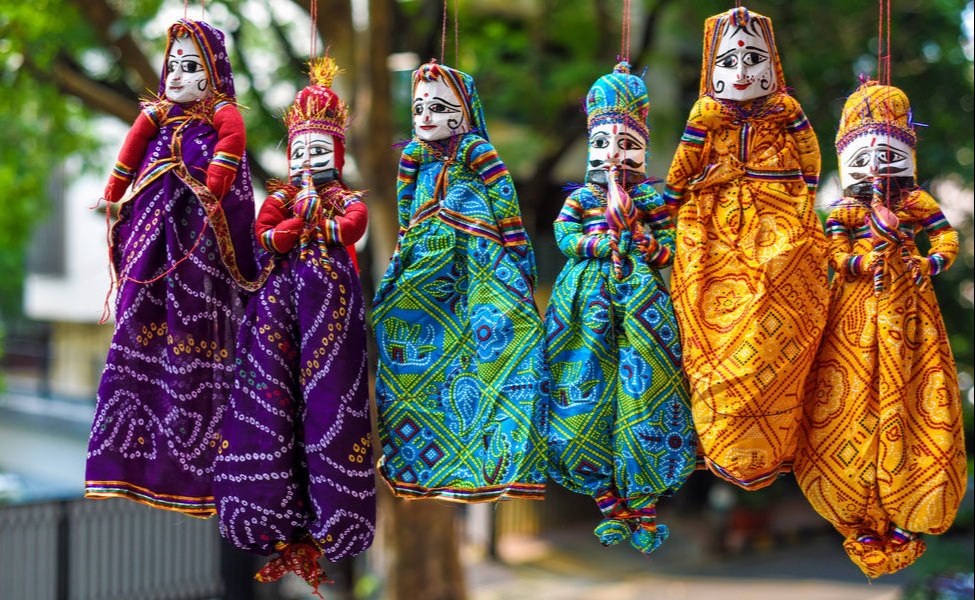
Wholesale / B2b Kathputli Puppets From Ahemdabad
Dec 16, 2024