Veena Craftsmanship for Wholesale Markets: A B2B Guide to Authentic Musical Instruments
Nov 12, 2024 | Shagun Sneha
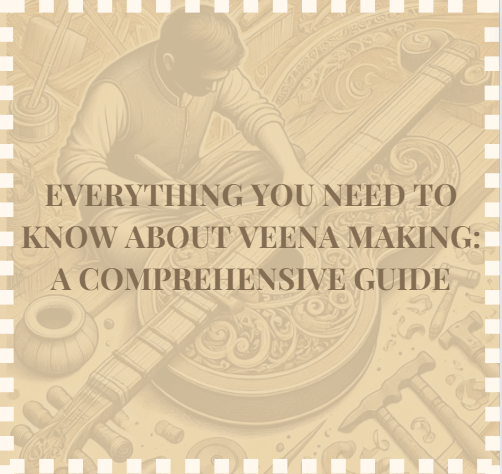
The Veena traces its origins to the Vedic period of India and had an important place in traditional Hinduism music and performing arts. References to music and the Veena are found in such ancient texts as the Markandeya Purana and many other Puranas. The Natya Shastra is the oldest available treatise on classical music and performance arts and represents one of the seminal Sanskrit works by the sage Bharata Muni. It has elaborate sections regarding the Veena, with details of an instrument of seven strings and techniques for playing it. Represented with a Veena, or Kachchapi, and a book, she is the goddess of art and learning, Saraswati, in Hindu iconography. Over time, its design, structure, and tuning evolved, and the instrument took several forms and names, each with a different sound.
The Veena today is a structure about 4 feet in length. Its distinguishing feature is a large resonator carved and hollowed out from a single piece of wood and is known as Ekantha Veena when it is made in one piece. It has a tapering neck topped with 24 brass or bell metal frets set in scalloped black wax on wooden tracks, and a tuning box ending in a downward curve with an ornamental dragon's head. There are typically four main strings and three subsidiary strings. In Yedathore Subbaraya Sharma's Kannada book Sandhyavandaneya Thathvartha Vedaprakaashike, the importance of the Veena is explained.
Playing of Veena is an art that varies from region to region, and it was developed in each region with its own style or Bani. There are basically four main Banis: Thanjavur, Mysore, Travancore, and Vizianagaram—all named after the place from where they originated—characterized by different styles with respect to different approaches and techniques of the musicians. Bani means an individualistic style over a period of time that is evolved by a musician or some group of musicians and passed on through generations.
Even within the different Banis, the style of the Veena differs slightly. For instance, in Vizianagaram, Andhra Pradesh, there exists a Veena-making tradition in the village of Bobbili, from which the Bobbili Veena gets its name. This place was a princely state before and is noted for its patronage of fine arts; the rajas of Bobbili maintained that craft of Veena making. Even to this day, some families in Bobbili still continue this tradition and the Veenas are procured by the Craft Development Centre and sold to enthusiasts. The Bobbili Veena is known for its fine workmanship and the amount of skill involved in its making.
Bobbili Veena: A Tradition of Excellence
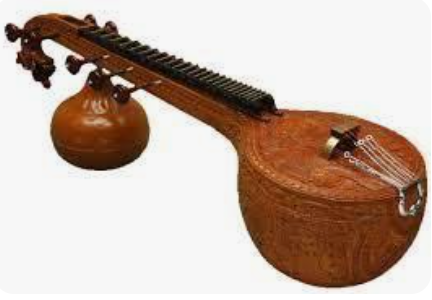
The Bobbili Veena, a distinguished variation of the traditional Veena, hails from the historic town of Bobbili in the Vizianagaram district of Andhra Pradesh. This exquisite instrument is not just a musical tool but a symbol of the rich cultural heritage and craftsmanship that has been preserved for generations.
Historical Significance
Bobbili, once a princely state, was renowned for its deep-rooted cultural and artistic traditions. The rajas of Bobbili were great patrons of the fine arts, and their support played a crucial role in nurturing the craft of Veena making. The town's history is marked by its association with music and the arts, making Bobbili a significant cultural hub in southern India.
The Craftsmanship Behind Bobbili Veena
The making of a Bobbili Veena is a meticulous process that requires exceptional skill and attention to detail. Unlike many modern instruments, the Bobbili Veena is often crafted from a single piece of wood, usually jackwood, which gives it a unique sound quality and durability. This type of Veena is known as Ekantha Veena, reflecting the traditional method of using a single log to carve the entire instrument.
The large resonator, known as the Kudam, is carefully hollowed out, and the body of the Veena is shaped with precision to ensure the correct tonal quality. The neck of the Veena, topped with brass or bell metal frets, is set in scalloped black wax on wooden tracks. The tuning box culminates in an intricately carved dragon's head, a signature feature of the Bobbili Veena, symbolizing the protection of art and culture.
The Bobbili Veena-Making Community
The tradition of Veena making in Bobbili has been passed down through generations, with a few families in the village continuing this age-old craft. These artisans are not just makers of the instrument but custodians of a legacy that dates back centuries. The skills and techniques they use have been honed over time, with each generation adding its nuances to the craft.
These families work tirelessly to produce Veenas that are not only functional musical instruments but also works of art. The Bobbili Veena is known for its superior sound quality and aesthetic appeal, making it a highly sought-after instrument by musicians and collectors alike.
Challenges and Preservation Efforts
Despite its rich history and cultural significance, the tradition of Bobbili Veena making faces several challenges. The shift towards mass-produced musical instruments has led to a decline in demand for handcrafted Veenas, threatening the livelihood of the artisans who have dedicated their lives to this craft.
However, efforts are being made to preserve this tradition. The Craft Development Centre in Bobbili plays a pivotal role in supporting these artisans by procuring their Veenas and promoting them to a wider audience. Additionally, various cultural organizations and music academies are working to raise awareness about the importance of preserving this craft.
The Legacy of Bobbili Veena
The Bobbili Veena is more than just an instrument; it is a symbol of India's rich cultural heritage and the enduring legacy of traditional craftsmanship. By supporting the artisans of Bobbili and appreciating the art of Veena making, we help ensure that this ancient tradition continues to thrive for generations to come. The Bobbili Veena stands as a testament to the timeless beauty of Indian classical music and the dedication of the artisans who keep this tradition alive.
What are the tools and raw materials required for the making of a Veena?
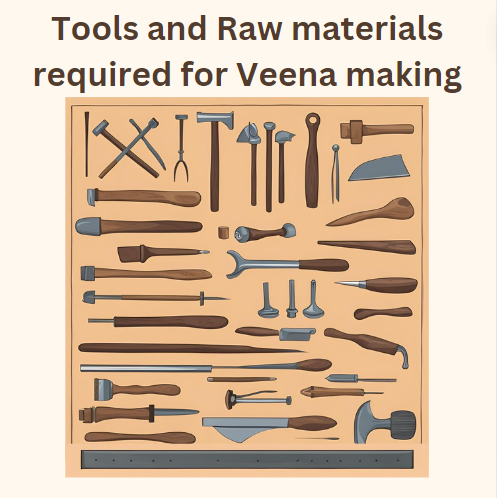
Bench Vice: Holds the wood or any material securely while working on it. (Product link)
Chisels: Used to carve or remove material to create intricate designs. (Product link)
Hammer: Delivers controlled blows to various objects during the crafting process. (Product link)
Cutter: Cuts sheets to the required size. (Product link)
Planning Tool: Evens out surfaces for a smooth finish. (Product link)
Hand Drill: Creates holes in objects as needed. (Product link)
Files: Removes excess material and smoothens surfaces. (Product link)
Emery Paper: Removes roughness from the contours. (Product link)
Brass and Steel String: Strung on the Veena to produce sound when played. (Product link)
Brass Fret: Supports the strings on the Veena. (Product link)
Jackfruit Wood: Used to craft the body of the Veena. (Product link)
Hacksaw: Cuts wood to the required length. (Product link)
White Plastic Sheet: Used to decorate the Veena with inlay work. (Product link)
Lac: Adds color to the carved designs. (Product link)
Heating Rod: Melts lac to fill in the design grooves. (Product link)
Rosewood Bridge: Supports the strings on the Veena. (Product link)
Measuring Tape: Measures the length of various components. (Product link)
Wood Polish/Paint: Treats the surface of the wood for protection and aesthetics. (Product link)
Aluminum Dome: Supports the other end of the Veena when not in use. (Product link)
What is the making process of a Veena?
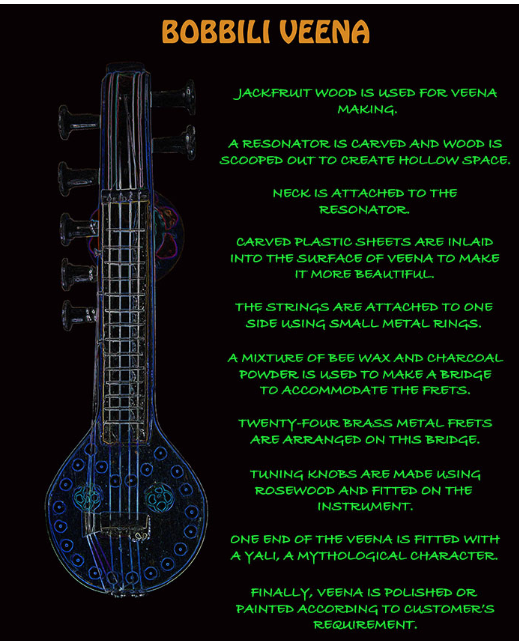
Material Selection:
The Veena is crafted from jackfruit wood, known for its lightweight nature, excellent reverberation, clear grain lines, and great durability.
The wood is seasoned by placing it in shaded areas to enhance its quality.
The correct size of the wooden log is chosen and cut for crafting.
Main Parts of the Veena:
Resonator (Kudam):
A large, hand-carved bowl where the sound is produced.
Crafted using a custom-made handheld scraping tool that removes large chunks of wood.
The quality of the music largely depends on the resonator’s craftsmanship.
A top cover, made from the same wood, is used to seal the resonator.
A small wooden bridge with a convex-shaped brass plate is glued to the resonator cover with resin.
Dandi (Neck):
The Dandi is a U-shaped, hollow wooden piece, approximately 51 inches long and 3.5 inches wide.
It is attached to the resonator and covered with a board on which the fingerboard is fixed using nails.
The fingerboard contains 24 brass frets set in a mixture of scalloped beeswax and charcoal powder.
It ends in a tuning box with a downward curve and an ornamental dragon (Yali) head.
A small box at the end holds the plectrums.
Pegbox:
Located on the sides of the Dandi, the tuning knobs (made from rosewood) tighten the strings.
There are seven strings on the Veena: the first two are steel, and the remaining five are brass.
Strings are tied from the tuning knobs to the tailpiece, a metal shield attached to the main resonator.
The four main strings press against the wooden bridge.
Brass and Bronze Components:
These metal parts are essential for holding the wooden components together, enhancing tonal quality, and adding to the instrument's aesthetic appeal.
Decorative Inlay Work:
The body of the Veena is adorned with intricate inlay carvings, which are now done on a plastic sheet (previously ivory).
The inlay designs are colored using lac, which is heated and filled into the grooves.
Once dried, excess lac is scraped off, leaving only the grooves filled with colors to highlight the design.
Finishing:
Depending on customer preferences, the Veena is either painted or polished.
The final step is tuning the Veena to ensure it produces the correct musical notes.
Time Frame:
It takes approximately 20 days to complete the entire process of making one Veena.
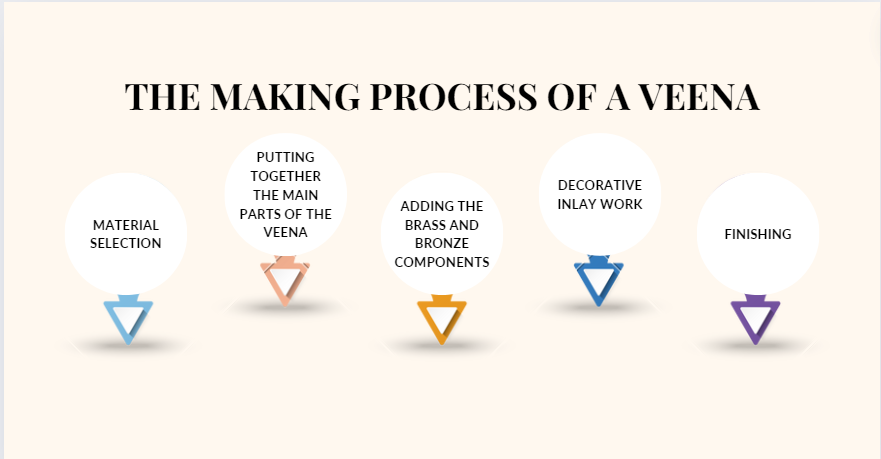
For miniature Veenas:
The Bobbili Veena, known for its rich cultural heritage, is also crafted in smaller sizes as a keepsake or decorative item. These miniature Veenas, which range in size from 9 inches to 23 inches in length and 3-4 inches in width, serve as elegant showpieces rather than functional instruments.
Size and Craftsmanship:
Despite their smaller dimensions, the craftsmanship of these miniatures closely mirrors that of the full-sized Veena. The attention to detail ensures that each miniature captures the essence of the larger instrument.
Depending on the size, the resonator (the main sound-producing body of the Veena) is made either solid or hollow. For smaller Veenas, the entire piece is often carved from a solid block of wood, reflecting the intricate artistry involved. For slightly larger miniatures, the resonator might be hollowed out to reduce weight, making it easier to handle and display.
Crafting Process:
The process of making a miniature Veena is nearly identical to that of a full-sized one. Skilled artisans follow traditional techniques, ensuring that even the smallest details—such as the ornamental dragon (Yali) head, the frets, and the tuning pegs—are meticulously crafted.
Given the reduced size, crafting a miniature Veena is quicker, typically taking between 1 to 4 days to complete, depending on the complexity and size of the piece.
Presentation:
Once completed, these miniature Veenas are often displayed in glass enclosures with a wooden base, enhancing their aesthetic appeal and protecting them from dust and damage. The glass case not only showcases the delicate craftsmanship but also serves as a beautiful addition to any home or office decor.
How to maintain the quality of Veena making?
Maintaining the quality of Veena making is crucial to preserving the instrument’s rich heritage and ensuring that each Veena produced offers the best possible sound and longevity. The following steps can help in maintaining the quality:
Selecting the Right Wood: The quality of wood is paramount in Veena making. Seasoned wood like jackfruit, teak, or rosewood is preferred because of its acoustic properties and durability. The wood must be aged properly to reduce moisture content, which helps in avoiding cracks and warping.
Precision in Craftsmanship: Skilled artisans play a vital role in ensuring the quality of the Veena. The crafting process requires meticulous attention to detail, especially when carving the body, neck, and resonator. Ensuring symmetry and proper alignment during assembly is essential for sound quality and aesthetic appeal.
Proper Tools and Techniques: Using traditional tools and techniques passed down through generations ensures that the craftsmanship remains authentic. However, integrating modern tools where appropriate can also enhance precision without compromising the traditional essence.
Regular Inspections: Throughout the making process, the Veena should undergo regular inspections to identify any defects or imperfections early on. This includes checking for uniform thickness, proper fitting of joints, and smoothness of the finish.
String and Fret Quality: The strings and frets are vital components of the Veena that significantly affect sound quality. Using high-quality strings and ensuring that the frets are properly aligned and polished can enhance the overall performance of the instrument.
Finishing Touches: The final polish and paint should not only enhance the visual appeal but also protect the wood. Using natural varnishes or eco-friendly paints can preserve the wood's quality and contribute to the instrument's longevity.
Ensuring Top-Notch Quality in Handmade Home Products
Handmade home products, whether they are decor items or functional pieces, require a high level of craftsmanship to stand out. Ensuring top-notch quality in these products involves several key practices:
Material Selection: The foundation of any high-quality handmade product is the material used. Opting for premium, sustainable, and durable materials ensures the product not only looks good but also lasts longer. For example, in textiles, organic cotton or linen may be chosen, while for wooden products, responsibly sourced hardwoods are ideal.
Craftsmanship: The skill of the artisan is a defining factor in the quality of handmade products. Ensuring that artisans have the necessary training and tools to perform their work can greatly improve the quality of the final product. Encouraging creativity while maintaining a standard of excellence is important.
Attention to Detail: Handmade products should be meticulously crafted, with careful attention to details like seams, joints, and finishes. Every stitch, cut, or stroke of paint should reflect the care and expertise of the artisan.
Quality Control Measures: Implementing quality control measures at various stages of production helps in identifying and rectifying any defects early. This includes checking the product against design specifications and ensuring that it meets all quality standards before it reaches the customer.
Sustainability Considerations: Today’s consumers are increasingly looking for products that are not only high quality but also environmentally friendly. Using eco-friendly materials and processes can enhance the appeal of handmade home products.
Customer Feedback: Finally, considering customer feedback and making necessary adjustments in future productions can help in maintaining and improving the quality of handmade home products.
Quality Control in Veena Making
Quality control in Veena making is a critical aspect to ensure that each instrument meets the high standards expected by musicians and connoisseurs. Key elements include:
Raw Material Inspection: Before the crafting process begins, the raw materials, particularly the wood, should be inspected for any defects such as knots, cracks, or uneven grain patterns. Only materials that pass this inspection should be used.
Process Monitoring: Throughout the crafting process, each step should be monitored closely. This involves checking the dimensions, symmetry, and alignment of each part of the Veena. Regular measurements and comparisons with standard templates can help maintain consistency.
Sound Testing: Once the Veena is assembled, it should undergo rigorous sound testing. This involves checking the tonal quality, resonance, and sustain of the instrument. Any issues identified should be addressed immediately.
Final Inspection: Before the Veena is considered complete, a final inspection should be carried out. This includes checking the finish, ensuring all components are securely attached, and confirming that the instrument meets all quality criteria.
Documentation: Keeping detailed records of the quality control process helps in tracking any recurring issues and improving the overall quality of future products. This documentation can also serve as a quality guarantee for customers.
Craftsmanship in Veena Making
Craftsmanship is the heart and soul of Veena making, where tradition, skill, and creativity converge to create a masterpiece. The following aspects are crucial:
Mastery of Traditional Techniques: Veena making is steeped in tradition, with techniques passed down through generations. Mastery of these techniques is essential to maintain the authenticity and quality of the instrument. This includes hand-carving the intricate designs, shaping the body, and assembling the parts with precision.
Skillful Carving: The detailed carving on the Veena’s body, especially around the resonator and neck, requires a high level of skill. The designs often have cultural and symbolic significance, which must be accurately represented.
Attention to Aesthetics: In addition to functionality, the aesthetic appeal of the Veena is an important aspect of craftsmanship. The instrument should not only sound good but also look exquisite. This involves careful selection of decorative elements, such as inlays, and ensuring they are applied with precision.
Balancing Tradition with Innovation: While traditional craftsmanship is vital, integrating modern innovations where appropriate can enhance the quality of the Veena. This could include using advanced tools for precision cutting or exploring new materials for certain components.
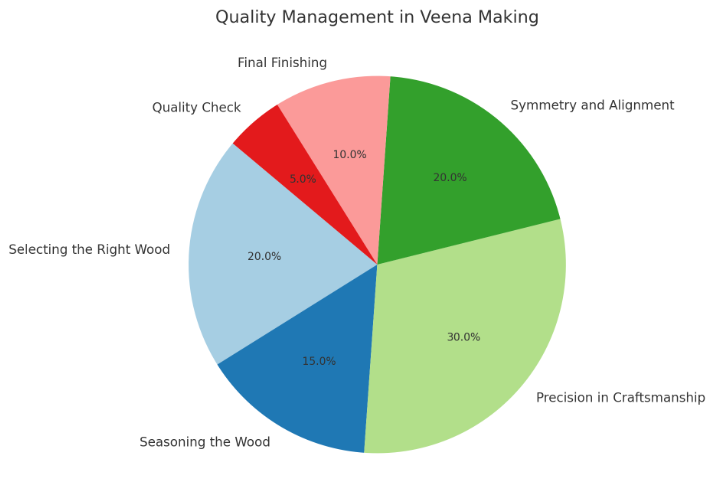
Understanding the Problem
User Needs:
Identify the specific needs and preferences of veena players, considering factors such as comfort, sound quality, and aesthetics.
Conduct interviews, surveys, and observations to gather insights.
Technical Constraints:
Explore limitations in traditional veena making techniques, materials, and manufacturing processes.
Assess opportunities for innovation and improvement.
Market Analysis:
Study the current market for veenas, including trends, competition, and consumer preferences.
Identify potential gaps or underserved niches.
Ideation and Brainstorming
Creative Thinking:
Encourage divergent thinking to generate a wide range of ideas for veena design and functionality.
Use techniques like brainstorming, mind mapping, and SCAMPER (Substitute, Combine, Adapt, Modify, Put to another use, Eliminate, Reverse) to stimulate creativity.
Innovation:
Explore innovative materials, manufacturing techniques, and design elements that can enhance the veena's performance and aesthetics.
Consider incorporating modern technologies or sustainable practices.
Prototyping and Testing
Rapid Prototyping:
Create physical or digital prototypes of potential veena designs to test their feasibility and functionality.
Experiment with different materials, shapes, and features.
User Testing:
Involve veena players in testing the prototypes to gather feedback on comfort, playability, and overall satisfaction.
Make necessary adjustments based on user insights.
Implementation and Iteration
Manufacturing and Production:
Develop a manufacturing process that is efficient, sustainable, and capable of producing high-quality veenas.
Consider factors such as cost, scalability, and ethical sourcing.
Continuous Improvement:
Encourage a culture of innovation and experimentation.
Continuously gather feedback from users and stakeholders to identify areas for improvement.
Iterate on the design and manufacturing process to refine the product.
Key Considerations for Innovative Veena Design
Ergonomics: Ensure the veena is comfortable and easy to play for a wide range of users.
Sound Quality: Experiment with different materials and construction techniques to achieve optimal sound.
Aesthetics: Create visually appealing designs that reflect the cultural significance of the veena.
Sustainability: Use environmentally friendly materials and practices in the manufacturing process.
Accessibility: Consider designing veenas that are accessible to players with disabilities.
Uniqueness of Veena making
Veena making, a traditional Indian craft, offers a unique blend of artistry, tradition, and customization. Each veena is a handcrafted masterpiece, reflecting the skill and creativity of its maker.
Unique Designs:
Traditional Variations: Veenas come in various styles, including the Rudra veena, Saraswati veena, and Vichitra veena, each with distinct characteristics and aesthetics.
Modern Interpretations: Contemporary veena makers are experimenting with new designs, incorporating modern materials and techniques while preserving the essence of traditional craftsmanship.
Custom Designs: Veenas can be customized to meet individual preferences, including the choice of wood, inlays, and ornamentation.
Limited Editions:
Exclusive Pieces: Many veena makers produce limited edition instruments, making them highly sought after by collectors and enthusiasts.
Unique Features: Limited edition veenas often feature special designs, materials, or techniques that set them apart from mass-produced instruments.
Customization:
Personalized Instruments: Veenas can be customized to reflect the personality and preferences of the player.
Tailored Sound: Customization can involve adjusting the dimensions, materials, and construction techniques to achieve a specific sound profile.
Sentimental Value: Customized veenas often hold sentimental value for their owners, as they are uniquely crafted to their specifications.
Unique Handmade Crafts:
Individuality: Each veena is a unique creation, reflecting the maker's skill and artistic vision.
Quality: Handmade veenas are often made with high-quality materials and meticulous attention to detail.
Cultural Significance: Veena making is a cultural heritage, preserving traditional techniques and designs.
Custom Home Decor:
Statement Pieces: Veenas can serve as stunning pieces of home decor, adding a touch of elegance and cultural significance.
Personalized Touches: Customized veenas can be displayed in living rooms, bedrooms, or music studios to create a personalized atmosphere.
Exclusive Designs:
Limited Availability: Unique and customized veenas are often limited in availability, making them exclusive and desirable.
Investment Value: Well-crafted veenas can appreciate in value over time, making them not only beautiful but also valuable investments.
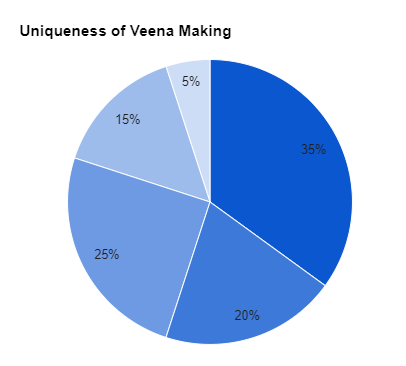
What is the importance of raw materials in Veena making?
Raw materials are the foundation of veena making, influencing the instrument's sound, durability, and aesthetic appeal. The choice of materials plays a crucial role in determining the overall quality and character of a veena.
Key Raw Materials Used in Veena Making:
Wood:
Tonewood: The most important material, tonewood determines the veena's sound characteristics. Common choices include rosewood, teak, sandalwood, and mango wood.
Density and Grain: The density and grain pattern of the wood influence the veena's resonance, sustain, and projection.
Seasoning: Properly seasoned wood is essential for preventing warping, cracking, and other defects.
Metal:
Frets: Brass or nickel silver are commonly used for frets, affecting the intonation and playability of the veena.
Tuning Pegs: Metal pegs are used to adjust the tension of the strings.
Inlays: Metal inlays can be used for decorative purposes or to strengthen the veena's structure.
Strings:
Material: Traditional veena strings are made from gut or synthetic materials.
Gauge: The thickness of the strings affects the tension and playability of the veena.
Other Materials:
Ivory or Bone: These materials are often used for the bridge, nut, and tuning pegs, providing a smooth surface for the strings.
Lacquer: Lacquer is used to finish the veena, protecting the wood and enhancing its appearance.
The Impact of Raw Materials on Veena Quality:
Sound: The choice of wood, especially tonewood, has a significant impact on the veena's sound quality, including its resonance, sustain, and tone.
Durability: High-quality materials, such as properly seasoned wood and durable metals, contribute to the veena's longevity.
Aesthetics: The appearance of a veena is influenced by the choice of wood, inlays, and finishes.
Playability: The materials used for the frets, tuning pegs, and strings affect the veena's playability and tuning stability.
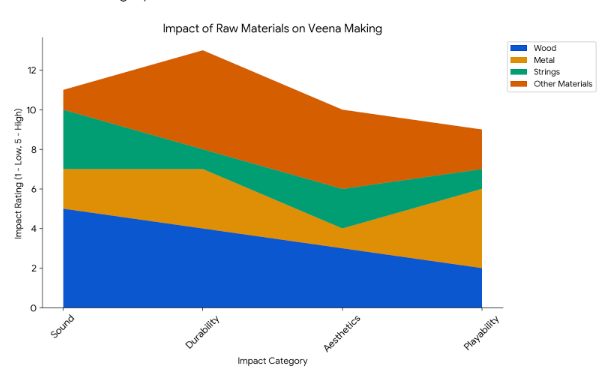
What are the sustainability measures of Veena making?
Sustainability is becoming increasingly important in various industries, including the arts and crafts sector. Veena making, a traditional Indian craft, can also incorporate sustainable practices to minimize its environmental impact.
Sustainable Materials:
Ethical Sourcing: Ensure that the wood used for veenas is sourced from sustainably managed forests.
Recycled Materials: Explore the use of recycled materials, such as recycled metal for frets or tuning pegs, to reduce waste.
Alternative Materials: Consider alternative materials with lower environmental impact, such as bamboo or certain synthetic materials.
Energy Efficiency:
Renewable Energy: Use renewable energy sources, such as solar or wind power, to power workshops and tools.
Energy-Efficient Equipment: Invest in energy-efficient tools and machinery to reduce energy consumption.
LED Lighting: Use LED lighting in workshops to reduce energy consumption and improve lighting quality.
Waste Reduction:
Reduce, Reuse, Recycle: Implement waste reduction practices, such as recycling wood scraps, metal shavings, and packaging materials.
Composting: Compost organic waste generated during the manufacturing process.
Minimalist Packaging: Use minimal and recyclable packaging for veenas to reduce waste.
Water Conservation:
Efficient Water Use: Implement water-saving measures in workshops, such as using low-flow fixtures and collecting rainwater for non-potable use.
Wastewater Treatment: Treat wastewater before discharging it into the environment.
Social Responsibility:
Fair Labor Practices: Ensure fair wages, working conditions, and benefits for workers.
Community Engagement: Support local communities and initiatives related to sustainability and environmental protection.
Preservation of Traditional Skills: Promote the preservation of traditional veena making techniques to ensure the continuity of this cultural heritage.
Certification and Labeling:
Sustainable Certifications: Seek certifications, such as FSC (Forest Stewardship Council) for wood or Fair Trade for materials, to demonstrate commitment to sustainability.
Eco-Labels: Use eco-labels to highlight the sustainable practices incorporated in veena making.
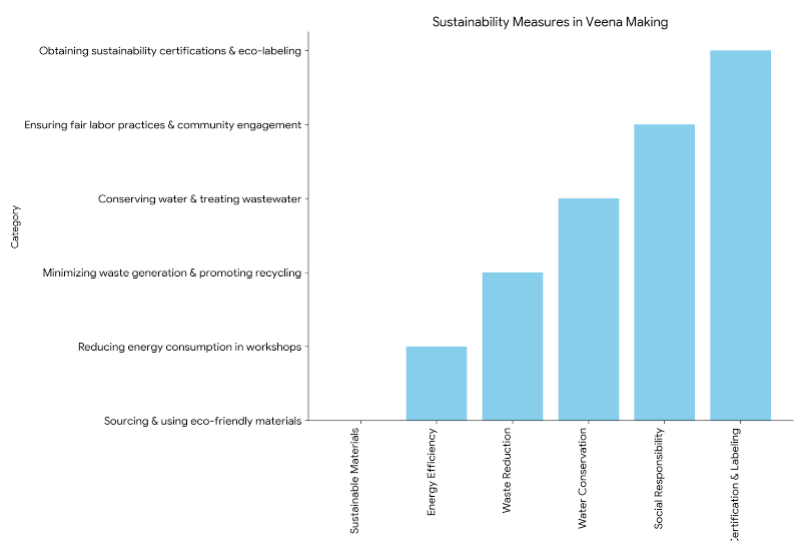
What are the production steps of Veena making?
Veena making is a complex process that involves several steps, each requiring skill and precision. Here's a breakdown of the typical production steps:
1. Material Selection:
Wood: Choosing the right type of wood is crucial for the veena's sound quality and durability. Common tonewoods include rosewood, teak, sandalwood, and mango wood.
Metal: Brass or nickel silver are used for frets, tuning pegs, and inlays.
Strings: Gut or synthetic materials are used for veena strings.
2. Design and Planning:
Dimensions: Determining the exact dimensions of the veena based on traditional measurements and the desired sound characteristics.
Inlays and Ornamentation: Planning the design and placement of inlays, carvings, or other decorative elements.
3. Wood Preparation:
Seasoning: Ensuring the wood is properly seasoned to prevent warping and cracking.
Cutting and Shaping: Cutting the wood into the desired shapes using traditional tools or modern machinery.
4. Body Construction:
Joining: Assembling the various parts of the veena body, such as the neck, soundboard, and resonator.
Inlays and Carving: Adding inlays, carvings, or other decorative elements as planned.
5. Fretting:
Fret Placement: Carefully placing the frets on the neck according to the desired scale and intonation.
Fretting Techniques: Using traditional fretting techniques to ensure the frets are secure and level.
6. Soundboard Preparation:
Soundhole: Cutting the soundhole in the soundboard, which affects the veena's tone and volume.
Bridge Installation: Installing the bridge, which supports the strings and transmits vibrations to the soundboard.
7. Tuning Pegs and Strings:
Tuning Peg Installation: Attaching the tuning pegs to the headstock.
Stringing: Installing the strings on the veena, ensuring proper tension and alignment.
8. Finishing:
Sanding and Polishing: Smoothing the surface of the veena and applying a finish (e.g., lacquer) to protect the wood and enhance its appearance.
9. Quality Control:
Inspection: Thoroughly inspecting the veena for any defects or imperfections.
Testing: Testing the veena's playability, sound quality, and intonation.
10. Final Touches:
Decorations: Adding any final decorations or embellishments.
Packaging: Preparing the veena for shipping or sale.
What is the scope of scalability of Veena making?
Veena making, a traditional Indian craft, has seen limited scalability due to several factors:
1. Labor-Intensive Process:
Skill Requirement: Veena making is a highly skilled craft that requires years of training and experience.
Manual Processes: Many of the production steps, such as carving, inlaying, and finishing, are still performed manually.
Limited Labor Availability: Skilled artisans may be limited in number, hindering the ability to scale up production.
2. Material Constraints:
Supply Limitations: High-quality tonewoods and other materials may be limited in supply, restricting production volume.
Sustainability Concerns: The sourcing of sustainable materials can be challenging, especially for certain types of wood.
3. Market Demand:
Niche Market: The market for veenas is relatively niche compared to mass-produced musical instruments.
Limited Export Markets: While there is a global market for Indian classical instruments, the demand for veenas may be limited outside of India and a few other countries.
4. Preservation of Traditional Techniques:
Focus on Quality: Many veena makers prioritize preserving traditional techniques and maintaining high quality standards, which can limit production speed and scale.
Resistance to Automation: There may be resistance to automating certain aspects of veena making, as it could compromise the craftsmanship and uniqueness of the instruments.
Despite these challenges, there is potential for limited scalability in veena making:
Specialized Workshops: Establishing specialized workshops with trained artisans can increase production capacity.
Modernization of Techniques: Incorporating modern tools and techniques, while preserving traditional craftsmanship, can improve efficiency.
Product Diversification: Expanding the product range to include veena accessories or related products can broaden the market.
Online Sales: Utilizing online platforms to reach a wider audience and facilitate sales can contribute to growth.
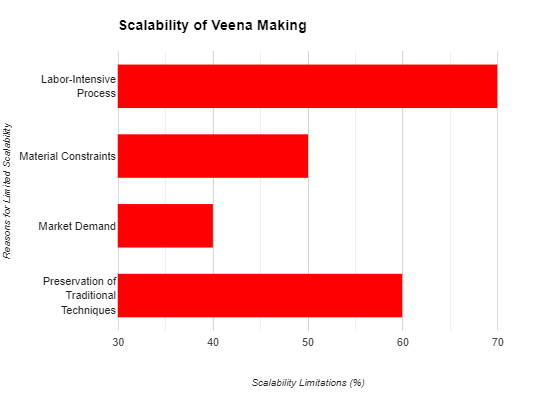
How to do carbon emission management of Veena making?
Veena making, a traditional craft, can also contribute to environmental sustainability by implementing carbon emission management strategies. Here are some key areas to focus on:
1. Sustainable Materials:
Ethical Sourcing: Ensure that the wood used for veenas is sourced from sustainably managed forests, reducing deforestation and carbon emissions.
Recycled Materials: Explore the use of recycled materials, such as recycled metal for frets or tuning pegs, to minimize the need for new resources.
Alternative Materials: Consider alternative materials with a lower carbon footprint, such as bamboo or certain synthetic materials.
2. Energy Efficiency:
Renewable Energy: Use renewable energy sources, such as solar or wind power, to power workshops and tools.
Energy-Efficient Equipment: Invest in energy-efficient machinery and tools to reduce energy consumption.
LED Lighting: Use LED lighting in workshops to reduce energy consumption and improve lighting quality.
3. Waste Reduction:
Reduce, Reuse, Recycle: Implement waste reduction practices, such as recycling wood scraps, metal shavings, and packaging materials.
Composting: Compost organic waste generated during the manufacturing process.
Minimalist Packaging: Use minimal and recyclable packaging for veenas to reduce waste.
4. Transportation:
Local Sourcing: Source materials and components locally to reduce transportation-related emissions.
Efficient Transportation: Use fuel-efficient vehicles or public transportation for transportation needs.
Online Sales: Encourage online sales to reduce the need for physical transportation of veenas.
5. Carbon Offset:
Carbon Credits: Purchase carbon credits to offset the carbon emissions associated with veena making.
Reforestation: Support reforestation projects to absorb carbon dioxide from the atmosphere.
6. Awareness and Education:
Public Awareness: Raise awareness about the environmental impact of veena making and encourage sustainable practices.
Education and Training: Provide training and education to veena makers and artisans on sustainable practices.
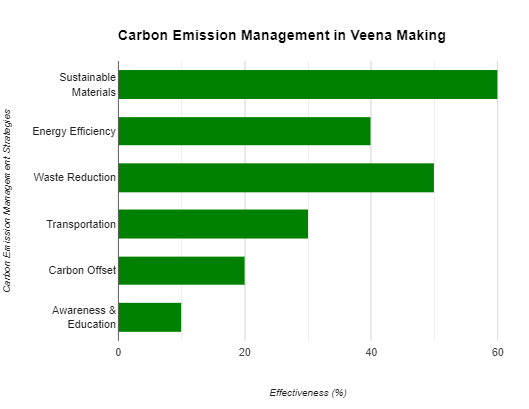
What is the cost of Veena making?
The cost of a veena can vary significantly depending on several factors:
Material Costs:
Wood: The primary material for a Veena is wood, usually from jackfruit, rosewood, or teak trees. The cost depends on the type and quality of wood used. High-quality, seasoned wood can be expensive.
Estimated Cost: ₹10,000 - ₹30,000 ($120 - $360)
Metal Components: The metal frets, strings, and other fittings are crucial for the instrument’s functionality. These are usually made from brass, copper, or steel.
Estimated Cost: ₹2,000 - ₹5,000 ($24 - $60)
Inlay Work: If the Veena includes intricate inlay work, such as mother-of-pearl or ivory, this adds to the cost.
Estimated Cost: ₹3,000 - ₹7,000 ($36 - $84)
Finishing Materials: Polishes, varnishes, and paints are used to finish the instrument, giving it a smooth and shiny appearance.
Estimated Cost: ₹1,000 - ₹2,000 ($12 - $24)
Labor Costs:
Craftsmanship: Skilled artisans spend weeks or even months carving, assembling, and fine-tuning each Veena. The labor cost reflects the time and expertise involved.
Estimated Cost: ₹20,000 - ₹50,000 ($240 - $600)
Inlay and Decoration: If the Veena has detailed inlay work or decorative elements, this requires additional labor and increases the cost.
Estimated Cost: ₹5,000 - ₹10,000 ($60 - $120)
Overhead Costs:
Workshop Maintenance: Running a workshop where the Veena is made incurs costs such as rent, utilities, and equipment maintenance.
Estimated Cost: ₹5,000 - ₹10,000 ($60 - $120)
Transport and Shipping: The cost of transporting materials to the workshop and shipping the final product to customers.
Estimated Cost: ₹1,000 - ₹3,000 ($12 - $36)
Total Estimated Cost:
The total cost of making a Veena can vary widely depending on the materials used, the complexity of the design, and the location of the workshop.
Estimated Total Cost: ₹47,000 - ₹117,000 ($564 - $1,404)
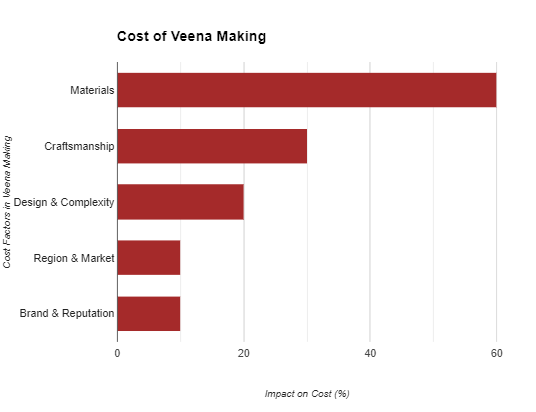
What is the scope of customization of Veena making?
Customization is a popular trend in the world of handmade instruments, and the veena is no exception. Veena makers offer a wide range of customization options to cater to individual preferences and tastes.
Common Customization Options:
Wood Selection:
Choose from a variety of tonewoods, such as rosewood, teak, sandalwood, or mango wood, to achieve different sound characteristics.
Inlays and Ornamentation:
Select intricate inlays and carvings made from materials like ivory, bone, metal, or gemstones.
Customize the design and placement of inlays to create a unique look.
Size and Shape:
Adjust the dimensions and shape of the veena to suit your comfort and playing style.
Fretboard:
Choose different fretboard materials, such as rosewood or ebony, and customize the fret spacing to suit your playing style.
Tuning Pegs:
Select different types of tuning pegs, such as ebony or metal, and customize their appearance.
Finish:
Choose from a variety of finishes, including lacquer, varnish, or wax, to achieve different aesthetics and levels of protection.
Sound:
Work with the veena maker to achieve a specific sound profile by adjusting the dimensions, materials, and construction techniques.
Benefits of Customization:
Personalized Instrument: A customized veena is tailored to your individual needs and preferences, providing a more satisfying playing experience.
Unique Aesthetic: A custom veena can be a beautiful and unique piece of art that reflects your personal style.
Investment Value: Customized veenas may appreciate in value over time, especially if they are made by renowned craftsmen.
What is the environmental impact of Veena making?
Veena making, while a traditional craft, can have certain environmental impacts. Here are some key areas to consider:
1. Deforestation:
Wood Sourcing: The sourcing of tonewoods, such as rosewood and teak, can contribute to deforestation if not done sustainably.
Habitat Destruction: Deforestation can lead to habitat destruction for various species and contribute to climate change.
2. Chemical Use:
Finishes: The use of certain finishes, such as lacquers or varnishes, can involve the use of chemicals that may have harmful environmental effects.
Wastewater: The disposal of wastewater from the manufacturing process can pollute water bodies if not treated properly.
3. Energy Consumption:
Workshop Operations: The energy used to power tools, machinery, and lighting in workshops can contribute to greenhouse gas emissions.
4. Transportation:
Material Sourcing: The transportation of materials, such as wood and metal, to and from workshops can generate carbon emissions.
Product Distribution: The transportation of finished veenas to markets or customers can also contribute to emissions.
5. Waste Generation:
Material Waste: The production process can generate waste, such as wood scraps, metal shavings, and packaging materials.
To mitigate these environmental impacts, veena makers can adopt sustainable practices, such as:
Ethical Sourcing: Ensuring that wood is sourced from sustainably managed forests.
Reducing Chemical Use: Using eco-friendly finishes or minimizing the use of chemicals.
Energy Efficiency: Using energy-efficient equipment and renewable energy sources.
Waste Reduction and Recycling: Implementing waste reduction and recycling practices.
Supporting Reforestation: Supporting reforestation efforts to offset carbon emissions.
What is the social impact of Veena making?
Veena making has a significant social impact, contributing to cultural preservation, economic development, and community engagement.
1. Cultural Preservation:
Preserving Tradition:
Veena making is a traditional craft that preserves Indian musical heritage.Promoting Cultural Identity: The creation and performance of veenas contribute to a sense of cultural identity and pride.
Education and Training: The teaching of veena playing helps to pass down traditional knowledge and skills to future generations.
2. Economic Development:
Job Creation: Veena making provides employment opportunities for artisans, craftsmen, and musicians.
Local Economy: The industry can contribute to the local economy by generating income and supporting related businesses.
Export Potential: Veenas can be exported to international markets, expanding economic opportunities.
3. Community Engagement:
Social Interaction: Veena making and playing can foster social interaction and community engagement.
Cultural Events: Veena performances and workshops can bring communities together and promote cultural exchange.
Educational Programs: Veena making programs can provide educational opportunities for young people and contribute to their development.
4. Therapeutic Benefits:
Stress Relief: Learning and playing the veena can have therapeutic benefits, reducing stress and promoting mental well-being.
Emotional Expression: Music can be a powerful tool for emotional expression and self-discovery.
5. Social Impact Initiatives:
Supporting Local Artisans: Veena makers can support local artisans and communities by providing fair wages and promoting their work.
Philanthropic Activities: Veena makers can contribute to philanthropic initiatives, such as supporting music education programs or charitable causes.
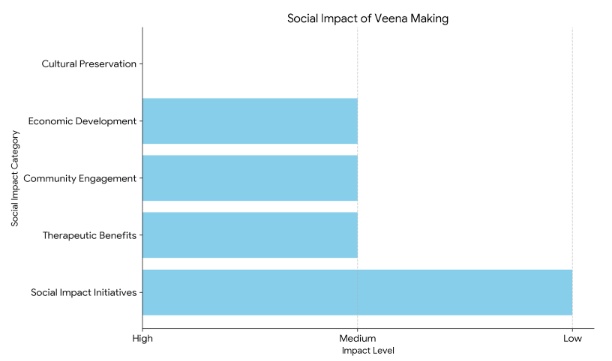
What is the economic impact of Veena making?
Veena making, a traditional Indian craft, has a significant economic impact, contributing to local economies and supporting livelihoods. Here are some key areas:
1. Job Creation:
Artisans and Craftsmen: Veena making provides employment opportunities for skilled artisans and craftsmen involved in various stages of the production process.
Musicians and Teachers: The demand for veenas also creates jobs for musicians and teachers who specialize in veena playing and instruction.
2. Local Economies:
Supporting Businesses: Veena making can support a range of local businesses, such as suppliers of raw materials, tools, and accessories.
Tourism and Cultural Events: Veena performances and related cultural events can attract tourists and generate revenue for local businesses.
3. Export Potential:
Global Market: Veenas can be exported to international markets, expanding the economic reach of the craft.
Cultural Exchange: Exporting veenas can promote cultural exchange and understanding.
4. Preservation of Traditional Skills:
Skill Development: The practice of veena making helps to preserve traditional skills and knowledge.
Economic Viability: By maintaining traditional craftsmanship, veena making can remain economically viable and support livelihoods.
5. Social Impact:
Community Development: Veena making can contribute to community development by providing economic opportunities and fostering social interaction.
Cultural Preservation: The preservation of veena making helps to maintain India's rich cultural heritage.
What is the turnaround time of Veena making?
The turnaround time for crafting a Veena can vary significantly depending on several factors, such as the complexity of the design, the materials used, and the availability of skilled artisans. Here's a general overview:
Simple Veena Design:
Estimated Time: 2 to 4 weeks
This timeline applies to Veenas with minimal decorative elements and standard materials. The focus is on producing a functional instrument with good acoustic qualities without extensive ornamentation.
Custom or Intricate Design:
Estimated Time: 6 to 12 weeks
For Veenas that include custom designs, intricate inlay work, or rare materials, the crafting process takes longer. The additional time is needed for detailed work, such as carving, inlaying, and fine-tuning the instrument.
Premium or Collector's Veena:
Estimated Time: 3 to 6 months
These Veenas are often made to order, with the highest quality materials and the most skilled craftsmanship. The extended time frame is due to the careful selection of materials, intricate design work, and multiple stages of quality checks.
Factors Influencing Turnaround Time:
Availability of Materials: Delays in sourcing high-quality wood or decorative materials can extend the timeline.
Artisan Skill and Experience: More experienced artisans may work faster, but the complexity of the design often dictates the overall time required.
Weather and Environmental Conditions: The drying and seasoning of wood can be affected by humidity and temperature, which might slow down the process.
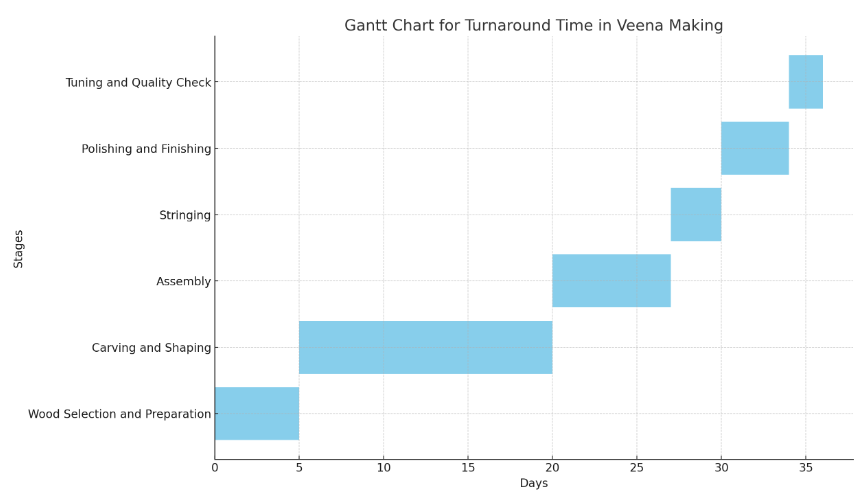
What are the payment terms of Veena making?
Payment terms for veena making can vary depending on the veena maker, the complexity of the project, and the customer's preferences. Here are some common payment terms:
1. Upfront Payment:
Full Payment: Some veena makers require full payment upfront before starting work on the veena.
Pros: This ensures that the maker has the necessary funds to complete the project and can help to secure their time and resources.
Cons: This may be a barrier for customers with limited upfront funds.
2. Deposit and Balance:
Partial Payment: A deposit is typically required upfront, followed by the balance upon completion of the veena.
Pros: This provides the maker with some financial security while allowing customers to spread out the payments.
Cons: There is a risk of the customer not paying the balance upon completion.
3. Milestone Payments:
Progress-Based Payments: Payments are made at specific milestones throughout the veena making process, such as when the body is completed, the fretboard is installed, or the veena is finished.
Pros: This offers flexibility for both the maker and the customer, as payments are tied to the progress of the project.
Cons: It may require more administrative work to track and manage payments.
4. Financing Options:
Payment Plans: Some veena makers may offer payment plans that allow customers to spread out the cost over a period of time.
Financing Partners: Some makers may partner with financing companies to offer customers financing options.
When choosing payment terms, it's important to consider:
Your Budget: Determine how much you can afford to pay upfront and whether you need financing options.
The Maker's Terms: Understand the maker's preferred payment terms and any associated fees or conditions.
Level of Trust: If you have a high level of trust in the maker, you may be more comfortable with upfront payments or milestone payments.
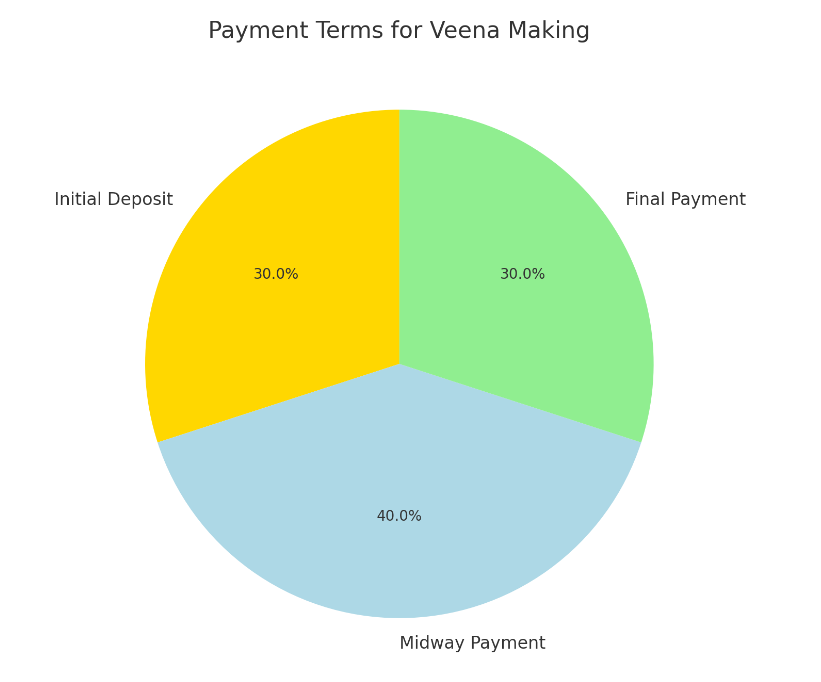
What are the key certifications of Veena making?
While Veena making is a traditional craft that has been passed down through generations, formal certifications specifically for Veena making are rare. However, there are several ways artisans and craftsmen can gain recognition and validate their skills:
Traditional Apprenticeship Certifications:
Guru-Shishya Parampara: In many cases, Veena makers are trained under the traditional guru-shishya (master-disciple) system. Upon completing their apprenticeship, some masters provide a certification or letter of recommendation attesting to the skill level and training of the apprentice.
Family Lineage: Veena making is often a family tradition, and the reputation of the family or lineage itself can serve as an informal certification of quality and authenticity.
Government and Handicraft Organizations:
Geographical Indication (GI) Tags: Certain regions in India are famous for Veena making, such as Thanjavur in Tamil Nadu. Instruments from these regions might carry a GI tag, which certifies that they are made in a traditional manner specific to that region.
Government-Recognized Artisans: Artisans can apply for recognition from government bodies like the Ministry of Textiles in India, which sometimes provides certifications or awards to master craftsmen in traditional arts, including Veena making.
National and State Awards: In India, artisans may receive awards such as the National Award for Master Craftspersons, which acts as a form of certification and recognition for their expertise in Veena making.
Institutional Certifications:
Crafts Schools and Colleges: Some institutions, such as art and craft colleges, offer courses or diplomas in traditional musical instrument making, which might include Veena making as part of their curriculum.
Vocational Training Centers: In certain regions, vocational training centers offer courses on musical instrument crafting, and successful completion of these courses often results in a certificate.
Quality Assurance Certifications:
ISO Certification: While not specific to Veena making, some high-end instrument makers might obtain ISO certification for quality management systems. This certification ensures that the instruments are made to a high standard, though it is more common in larger workshops or companies.
Handicraft Mark: In India, products that meet certain quality criteria might be eligible for a handicraft mark, which can serve as an assurance of authenticity and quality.
Cultural and Heritage Certifications:
UNESCO Intangible Cultural Heritage: If Veena making is part of a recognized UNESCO Intangible Cultural Heritage, this status can serve as a broader certification of the cultural significance and authenticity of the craft.
State Cultural Boards: Some state governments in India have cultural boards that certify and promote traditional arts and crafts, including Veena making.
Importance of Certification
While formal certifications are not always required or available, they can help Veena makers:
Build Trust: Certifications can assure customers of the quality and authenticity of the Veena.
Enhance Marketability: Certified products may command higher prices and attract a wider audience.
Preserve Tradition: Recognizing skilled artisans helps preserve the craft and pass it on to future generations.
What are the logistics of Veena making?
Material Sourcing:
Wood:
Quantity: Approximately 50-100 kg of seasoned wood per Veena.
Lead Time: 6 to 12 months for seasoning wood.
Transportation Distance: Often sourced from regional forests or suppliers within 200-500 km.
Metal Components:
Quantity: About 1-2 kg of brass, copper, or steel for strings and frets.
Lead Time: 2 to 4 weeks for custom parts.
Transportation Distance: Typically within 100-300 km from metal workshops.
Labor:
Craftsmen:
Number of Artisans: 1 master craftsman with 2-3 assistants per Veena.
Man-Hours: 150 to 300 hours per Veena.
Quality Checks:
Number of Inspections: 3 to 5 quality inspections during different stages.
Inspection Time: 1-2 hours per inspection.
Manufacturing Time Frame:
Basic Veena:
Time: 2 to 4 weeks.
Customized Veena:
Time: 6 to 12 weeks.
High-End/Collector’s Veena:
Time: 3 to 6 months.
Storage:
Finished Veenas:
Storage Space: 1 to 2 cubic meters per Veena.
Temperature and Humidity Control: Ideal conditions are 20-25°C and 50-60% humidity.
Inventory Turnover: Typically, Veenas are sold within 1 to 6 months after production.
Domestic Shipping:
Average Distance: 500-1,500 km within India.
Cost: ₹1,000 - ₹3,000 ($12 - $36) per Veena, depending on distance and service.
Time: 3 to 7 days.
International Shipping:
Average Distance: 5,000-10,000 km.
Cost: ₹10,000 - ₹20,000 ($120 - $240) per Veena, depending on destination.
Time: 1 to 3 weeks.
Materials:
Quantity: Approximately 5-10 kg of packaging materials, including wooden crates, bubble wrap, and cushioning.
Cost: ₹2,000 - ₹5,000 ($24 - $60) per Veena.
Durability: Packaging is designed to withstand shocks, with drop tests conducted from 1-2 meters.
Sales and Distribution:
Retailers/Dealers:
Number of Outlets: Typically 10-20 authorized dealers in major cities.
Online Sales:
Percentage of Sales: 20-30% of Veenas are sold through online platforms.
Lead Time for Delivery:
Domestic: 5-10 days.
International: 2-4 weeks.
Summary
What are the customs and duties of Veena making?
When it comes to the export and import of Veenas, several customs and duties may apply depending on the country of origin and destination. These costs and regulations can significantly affect the overall price and logistics of Veena making and selling.
1. Export Customs Duties (India):
HS Code: Musical instruments like Veenas are typically classified under the Harmonized System (HS) code 9202.90 (other string instruments).
Export Duty: India generally has zero export duty on musical instruments, including Veenas. However, if the Veena contains materials like ivory or rare woods, additional clearances may be required under the Convention on International Trade in Endangered Species (CITES).
Documentation: Exporters must prepare an invoice, packing list, and a shipping bill. A certificate of origin may be needed to avail preferential duty rates in the destination country.
Inspection: The instrument may be subject to inspection by customs officials to ensure compliance with export regulations, particularly concerning restricted materials.
2. Import Customs Duties (Destination Country):
Import Duty Rates: The import duty on Veenas varies by country. For example:
United States: Typically, 3-5% import duty on musical instruments.
European Union: Around 2-4% import duty, though this may vary by member state.
Canada: Generally, a 6% import duty.
VAT/GST: Many countries also impose a Value Added Tax (VAT) or Goods and Services Tax (GST) on imported goods, which can range from 5% to 25% of the value of the Veena, including shipping costs.
Customs Clearance: Importers must submit a customs declaration, including the invoice, bill of lading, and any relevant certificates (e.g., CITES for restricted materials).
Harmonized Tariff Schedule (HTS): The specific tariff code used by the destination country will determine the exact duty rate applied to the Veena.
3. Special Considerations:
CITES Compliance: If the Veena contains materials from endangered species (like ivory or certain rare woods), both the exporter and importer must ensure compliance with CITES regulations. This often requires special permits and can delay shipping.
Cultural Goods Regulations: Some countries have specific regulations for the import of cultural goods, which may apply to traditional musical instruments like the Veena. These regulations can include additional documentation or import restrictions.
Antique Veenas: If the Veena is an antique (over 100 years old), it may be subject to different customs duties and regulations, often requiring certification as an antique.
4. Customs Duties Impact on Pricing:
Price Markup: The combined cost of import duties, VAT/GST, and customs clearance fees can increase the price of a Veena by 10-30% in the destination country.
Shipping and Insurance: Customs duties are often calculated on the CIF (Cost, Insurance, and Freight) value, meaning that the duty applies to the total cost of the Veena, including shipping and insurance.
Anti-money laundering of Veena making
Veena making is primarily a traditional and cultural craft. There are some potential areas where Anti-Money Laundering (AML) measures could be relevant, especially for high-value transactions and international trade. Here's how AML considerations might apply to the Veena making and selling industry:
1. High-Value Transactions:
Risk of Money Laundering: Like other luxury and high-value items, Veenas—particularly antique or custom-made ones—could be used in money laundering schemes. High-value transactions in cash or with unclear sources of funds might raise red flags.
Due Diligence: Artisans, dealers, and exporters should perform due diligence on buyers, especially for transactions exceeding a certain threshold (e.g., ₹10 lakh or $12,000). This includes verifying the identity of the buyer, the source of funds, and the purpose of the purchase.
2. International Trade and Cross-Border Transactions:
Cross-Border AML Regulations: When exporting Veenas internationally, especially to countries with strict AML regulations, compliance with local and international AML laws is crucial. This may involve reporting large transactions, especially if they are made in cash or involve complex financial arrangements.
Suspicious Transaction Reporting: If a Veena maker or dealer notices unusual patterns in cross-border payments—such as multiple small payments from different accounts or payment from high-risk jurisdictions—they may need to report this as a suspicious transaction to the relevant authorities.
3. Use of Shell Companies or Fronts:
AML Red Flags: The use of shell companies or intermediaries without a clear business purpose in Veena transactions might be a red flag for money laundering. Sellers should be cautious of buyers who use complex or opaque ownership structures to purchase Veenas.
Transparency and Record-Keeping: Maintaining clear records of all transactions, including the identities of buyers and the payment methods used, is essential for AML compliance. Transparency in the ownership and sale process helps mitigate risks.
4. Regulatory Compliance:
Know Your Customer (KYC): Implementing KYC procedures can help Veena makers and dealers verify the identity of their customers and ensure they are not dealing with illicit funds. This includes collecting information such as the buyer’s name, address, and identification documents.
AML Training: For larger businesses or those involved in frequent high-value transactions, training staff on AML regulations and how to spot potential money laundering activities is crucial.
5. Reporting Obligations:
Thresholds for Reporting: In many jurisdictions, there are specific thresholds for mandatory reporting of cash transactions. For instance, transactions exceeding ₹10 lakh in India must be reported to the Financial Intelligence Unit (FIU).
Currency Transaction Reports (CTRs): If a business regularly handles large cash transactions, it may need to file Currency Transaction Reports (CTRs) with relevant authorities, detailing the nature and amount of the transaction.
6. Enhanced Due Diligence (EDD):
High-Risk Customers: For buyers or transactions deemed high-risk (e.g., politically exposed persons, transactions involving tax havens), enhanced due diligence measures should be taken. This might include additional verification steps, monitoring of the transaction, and more thorough documentation.
What are the ethical practices of Veena making?
Veena making, like other traditional crafts, is not just about creating a musical instrument but also about preserving a cultural heritage. Ethical practices in Veena making encompass various aspects, including the sourcing of materials, fair labor practices, environmental sustainability, and cultural respect. Here’s how ethical considerations can be integrated into the Veena making process:
1. Sustainable Sourcing of Materials:
Wood Sourcing:
Sustainable Forestry: Using wood from sustainably managed forests is crucial. This means sourcing wood that is harvested in a way that maintains the health of the forest and ensures its long-term viability.
Certification: Ensuring that the wood used in Veena making comes from sources certified by organizations such as the Forest Stewardship Council (FSC) can help guarantee that it is harvested responsibly.
Avoiding Endangered Species: Certain woods, like rosewood or sandalwood, are endangered. Ethical Veena makers avoid using these materials or ensure they are sourced in compliance with international regulations like CITES (Convention on International Trade in Endangered Species).
Metal and Decorative Materials:
Ethical Sourcing of Metals: Metals used in frets and other components should be sourced from suppliers who adhere to ethical mining practices, ensuring fair labor and minimal environmental impact.
Inlay Materials: The use of materials like ivory or bone, which involve harm to animals, should be avoided. Alternatives like synthetic or plant-based materials can be used for inlays and decorations.
2. Fair Labor Practices:
Artisan Welfare:
Fair Wages: Artisans involved in Veena making should be paid fairly for their work, reflecting their skill, experience, and the time they invest in each instrument.
Safe Working Conditions: Ensuring a safe and healthy working environment is vital. This includes providing adequate tools, proper ventilation, and safe handling of materials.
Respect for Traditional Knowledge: Veena making often involves traditional knowledge passed down through generations. Respecting and preserving this knowledge is an ethical responsibility.
No Child Labor:
Prohibition of Child Labor: Ethical Veena making must adhere to international and local laws prohibiting child labor. Ensuring that no child is involved in the production process is a critical ethical practice.
3. Environmental Sustainability:
Waste Management:
Minimizing Waste: Implementing practices to minimize waste during the crafting process, such as using wood offcuts for smaller parts or other crafts, contributes to sustainability.
Safe Disposal: Proper disposal of any waste materials, particularly those that could harm the environment, like varnishes or metal shavings, should be a priority.
Energy Efficiency:
Eco-Friendly Tools and Equipment: Using energy-efficient tools and reducing energy consumption in workshops can help lessen the environmental footprint of Veena making.
Renewable Energy: Where possible, using renewable energy sources such as solar power for workshop operations adds to the sustainability of the craft.
4. Cultural Respect and Preservation:
Cultural Authenticity:
Respecting Tradition: While innovation in design and technique is valuable, it is important to respect the cultural and spiritual significance of traditional Veena making practices.
Passing on Knowledge: Ethical practice includes ensuring that traditional knowledge is passed on to the next generation, either through formal apprenticeships or community-based learning.
Avoiding Cultural Appropriation:
Respectful Marketing: Veenas should be marketed and sold in a way that respects their cultural heritage. Avoiding the commercialization of cultural symbols or the use of culturally insensitive marketing is essential.
5. Transparent Business Practices:
Honesty in Advertising:
Accurate Representation: Veenas should be accurately represented in terms of the materials used, the craftsmanship involved, and the origins of the instrument.
Clear Communication: Providing clear information about the sourcing of materials, the crafting process, and the artisans involved helps build trust with customers.
Ethical Pricing:
Fair Pricing: Prices should reflect the true value of the Veena, considering the materials, labor, and craftsmanship involved, while also being accessible to those who value the instrument’s cultural significance.
What are the innovative aspects of Veena making?
Veena making, a traditional Indian craft, has seen a resurgence of interest in recent years, with innovative approaches emerging to modernize the instrument while preserving its cultural heritage. Here are some key innovative aspects:
1. Material Innovations:
Modern Materials: Experimenting with alternative materials, such as carbon fiber or synthetic materials, to enhance the veena's sound, durability, and playability.
Sustainable Sourcing: Prioritizing sustainable sourcing of materials, especially wood, to reduce the environmental impact.
2. Design Innovations:
Ergonomic Designs: Incorporating ergonomic principles to improve the comfort and playability of the veena, especially for beginners or those with physical limitations.
Hybrid Designs: Combining traditional veena designs with elements from other instruments to create unique and versatile instruments.
3. Manufacturing Innovations:
Computer-Aided Design (CAD): Utilizing CAD software for precise design and prototyping, improving efficiency and accuracy.
Modern Tools and Techniques: Employing modern tools and techniques to streamline the manufacturing process while maintaining traditional craftsmanship.
4. Sound Innovations:
Amplification: Developing amplification systems specifically designed for veenas to enhance their sound projection and versatility in different performance settings.
Electronic Modifications: Experimenting with electronic modifications, such as pickups or MIDI interfaces, to expand the veena's sonic capabilities and integrate it with modern music technology.
5. Cultural Fusion:
Fusion Styles: Exploring fusion styles that combine traditional veena techniques with elements from other musical genres, such as jazz, rock, or classical Western music.
Collaborative Projects: Collaborating with musicians from different cultures to create innovative and cross-cultural musical compositions.
6. Educational Innovations:
Online Learning: Developing online resources and tutorials to make veena learning accessible to a wider audience.
Interactive Learning Tools: Creating interactive learning tools, such as virtual veenas or augmented reality applications, to enhance the learning experience.
These innovative aspects are helping to revitalize veena making and expand its reach beyond traditional boundaries. By embracing innovation while preserving the core values of the craft, veena makers are ensuring the continued relevance and evolution of this timeless instrument.
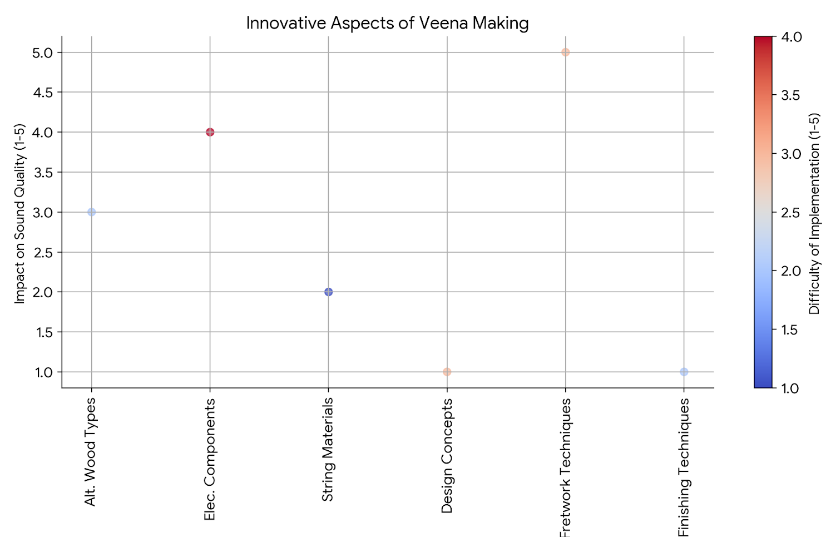
What are the market trends of Veena making?
The market trends for veena making, particularly in India, are influenced by several factors, including cultural demand, craftsmanship, and technological advancements.
1. Cultural and Religious Significance
The veena holds a significant place in Indian classical music, particularly in Carnatic music, and is also associated with Hindu mythology, particularly the goddess Saraswati. This cultural and religious significance ensures a steady demand for veenas, especially during festivals, religious ceremonies, and cultural events.
2. Artisanal Craftsmanship
Veena making is a highly skilled craft, often passed down through generations of artisans. There is a growing appreciation for handcrafted, traditional musical instruments, which has led to a niche but steady market for veenas. Buyers often seek instruments that are not only playable but also aesthetically pleasing and culturally authentic.
3. Customization and Personalization
Increasingly, customers are looking for personalized and customized veenas, tailored to their specific needs regarding size, wood type, and decoration. This trend has led to artisans offering bespoke services, which often command higher prices.
4. Market Segmentation
The veena market is segmented into professional musicians, students, collectors, and cultural institutions. Each segment has different price points and quality expectations. Professional musicians tend to invest in higher-end, custom-made veenas, while students and hobbyists might opt for more affordable, mass-produced versions.
5. Impact of Technology
While traditional veena making remains largely manual, there has been a gradual incorporation of technology in certain aspects, such as the use of machines for precision cutting and shaping. However, the market for fully handcrafted veenas remains strong, driven by the demand for authenticity and quality.
6. Challenges and Opportunities
Challenges: The veena-making industry faces challenges like the scarcity of high-quality wood, competition from cheaper, mass-produced instruments, and a declining number of skilled artisans.
Opportunities: There is potential for growth in international markets, especially among Indian diaspora communities and world music enthusiasts. Additionally, the growing interest in sustainable practices could drive demand for veenas made from eco-friendly materials.
7. Government Support and Initiatives
In India, government initiatives promoting traditional crafts and musical instruments have provided some support to veena makers. This includes financial aid, training programs, and marketing support to help artisans sustain their craft.
8. Global Interest
There is a rising global interest in traditional Indian instruments, including the veena, particularly in the context of world music. This has opened up export opportunities, especially to countries with significant Indian populations or where Indian music is gaining popularity.
9. Online Sales and Marketing
The digital transformation has also impacted the veena market. Artisans and sellers are increasingly using online platforms to reach a broader audience, both within India and internationally. Social media, e-commerce platforms, and virtual exhibitions have become key tools in promoting and selling veenas.
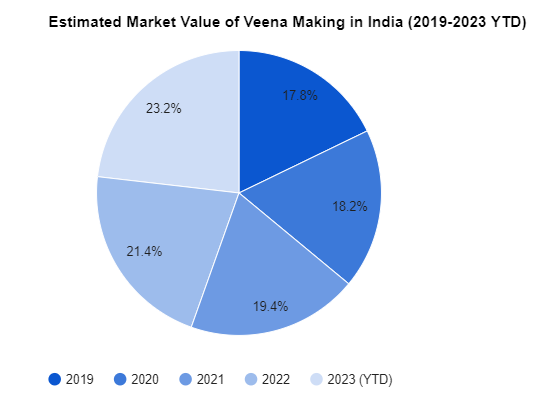
Risk Management of Veena making
Veena making, like any craft, faces various risks that can impact its profitability and sustainability. Effective risk management strategies are essential to mitigate these risks and ensure the long-term success of the business.
Key Risks in Veena Making:
Market Risk:
Fluctuations in demand for veenas due to economic conditions, cultural trends, or competition.
Changes in consumer preferences or tastes.
Emergence of substitute products or technologies.
Operational Risk:
Supply chain disruptions, such as delays in material delivery or quality issues.
Damage to equipment or facilities.
Labor shortages or turnover.
Production bottlenecks or inefficiencies.
Financial Risk:
Currency fluctuations.
Changes in interest rates.
Credit risk from customers or suppliers.
Cost overruns due to unexpected expenses.
Regulatory Risk:
Changes in government regulations or policies related to environmental protection, labor standards, or trade.
Compliance challenges with import/export regulations.
Risk Management Strategies:
Market Research and Analysis:
Conduct regular market research to identify trends, preferences, and potential risks.
Monitor competitors and industry developments.
Develop a marketing strategy to address changing market conditions.
Diversification:
Offer a variety of veena models or styles to cater to different customer preferences.
Explore new markets or export opportunities to reduce reliance on a single market.
Supply Chain Management:
Establish strong relationships with reliable suppliers.
Diversify suppliers to reduce dependence on a single source.
Implement inventory management systems to optimize stock levels.
Risk Assessment and Mitigation:
Conduct regular risk assessments to identify potential threats and vulnerabilities.
Develop mitigation strategies to address identified risks.
Implement contingency plans for unexpected events.
Financial Planning:
Develop a robust financial plan to manage cash flow, budgeting, and investments.
Consider hedging strategies to mitigate currency and interest rate risks.
Maintain adequate insurance coverage to protect against financial losses.
Compliance and Regulatory Monitoring:
Stay updated on relevant regulations and ensure compliance.
Appoint a compliance officer to monitor regulatory changes and ensure adherence to standards.
Business Continuity Planning:
Develop a business continuity plan to address potential disruptions, such as natural disasters or supply chain disruptions.
Test the plan regularly to ensure its effectiveness.
What are the digital marketing measures of Veena making?
Digital marketing can be a powerful tool for promoting veena making and reaching a wider audience.
1. Website and Online Store:
Create a Professional Website: Design a visually appealing and informative website that showcases your veenas, provides details about your craftsmanship, and offers online purchasing options.
Optimize for Search Engines (SEO): Use relevant keywords and SEO best practices to improve your website's visibility in search engine results.
Online Store Integration: Set up an online store to allow customers to purchase veenas directly from your website.
2. Social Media Marketing:
Engage with Your Audience: Create engaging content, such as videos, photos, and behind-the-scenes glimpses of your workshop, to connect with your audience on social media platforms like Instagram, Facebook, and YouTube.
Use Relevant Hashtags: Use relevant hashtags to increase your content's visibility and reach a wider audience.
Run Contests and Giveaways: Organize contests or giveaways to attract new followers and encourage engagement.
3. Content Marketing:
Blog: Create a blog on your website to share insights into veena making, cultural traditions, and playing techniques.
Guest Blogging: Contribute guest posts to relevant blogs or websites to reach a wider audience.
Video Tutorials: Produce educational videos on veena playing techniques, care, and maintenance.
4. Email Marketing:
Build an Email List: Collect email addresses from visitors to your website and social media channels.
Send Newsletters: Regularly send newsletters with updates, promotions, and exclusive content to your subscribers.
5. Online Advertising:
Pay-Per-Click (PPC) Advertising: Use platforms like Google Ads to target potential customers with relevant ads.
Social Media Advertising: Promote your veenas and content on social media platforms through targeted ads.
6. Influencer Marketing:
Collaborate with Influencers: Partner with influencers in the music or cultural industry to promote your veenas to their followers.
7. Online Music Platforms:
Sell Veenas Online: List your veenas for sale on online music marketplaces or platforms like Etsy.
Promote Music: Encourage musicians to use your veenas and share their performances on online music platforms.
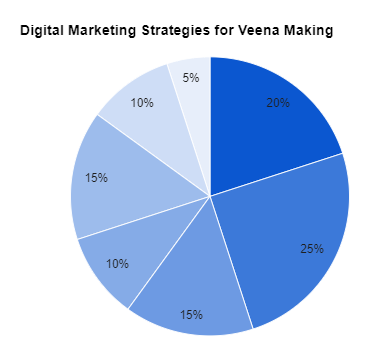
What are the customer service aspects of Veena making?
Excellent customer service is crucial for the success of a veena making business. Here are some key aspects to consider:
1. Personalized Attention:
Individualized Approach: Treat each customer as an individual with unique needs and preferences.
Personalized Recommendations: Offer personalized advice on veena selection, maintenance, and playing techniques.
2. Clear Communication:
Open and Honest Communication: Maintain open and honest communication with customers throughout the entire process.
Regular Updates: Keep customers informed about the progress of their orders and address any concerns promptly.
3. After-Sales Support:
Warranty: Offer a warranty or guarantee on your veenas to provide customers with peace of mind.
Maintenance and Repairs: Provide after-sales services such as maintenance, repairs, and string replacement.
Customer Support: Offer ongoing customer support through various channels, such as email, phone, or social media.
4. Customer Feedback:
Gather Feedback: Actively seek feedback from customers to identify areas for improvement.
Address Complaints: Respond to customer complaints promptly and effectively to resolve issues and maintain customer satisfaction.
5. Customer Loyalty Programs:
Rewards and Incentives: Offer loyalty programs or rewards to encourage repeat business and customer referrals.
6. Cultural Sensitivity:
Respect for Traditions: Demonstrate respect for the cultural significance of the veena and its traditions.
Cultural Understanding: Show understanding of different cultural perspectives and preferences.
7. Accessibility:
Inclusive Practices: Ensure that your business is accessible to all customers, including those with disabilities.
Language Options: Consider offering customer support in multiple languages to cater to a diverse customer base.
By prioritizing excellent customer service, veena makers can build strong relationships with their customers, foster loyalty, and contribute to the long-term success of their business.
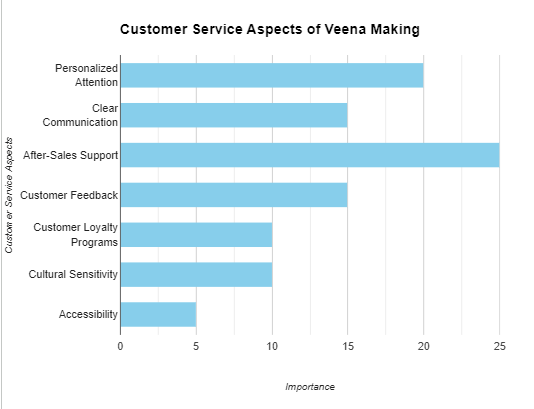
How to do quality control of Veena making?
Quality control is essential in veena making to ensure that the finished instruments meet high standards of craftsmanship, sound quality, and playability.
1. Material Quality:
Wood Selection: Ensure that the wood used is of high quality, with proper seasoning and grain orientation.
Metal Components: Verify the quality of metal components, such as frets, tuning pegs, and inlays.
String Quality: Use high-quality strings that meet the specific requirements of the veena.
2. Manufacturing Process:
Adherence to Standards: Ensure that the manufacturing process adheres to established standards and techniques.
Dimensional Accuracy: Check for accuracy in dimensions and measurements.
Joint Strength: Verify the strength and stability of joints and connections.
3. Sound Quality:
Tone and Resonance: Assess the veena's sound quality, including its tone, resonance, and sustain.
Intonation: Check for accurate intonation across the frets.
4. Playability:
Comfort: Ensure that the veena is comfortable to play, with proper ergonomics and string tension.
Ease of Playing: Assess the ease of playing the veena, including finger placement and fretboard feel.
5. Visual Inspection:
Appearance: Check for any defects, blemishes, or scratches in the finish or appearance.
Inlays and Ornamentation: Verify the quality and precision of inlays and other decorative elements.
6. Functional Testing:
Tuning Stability: Test the veena's ability to hold tuning over time.
String Buzzing: Check for any string buzzing or other unwanted noises.
7. Documentation:
Inspection Reports: Maintain detailed inspection reports for each veena.
Quality Records: Keep records of quality control measures and any corrective actions taken.
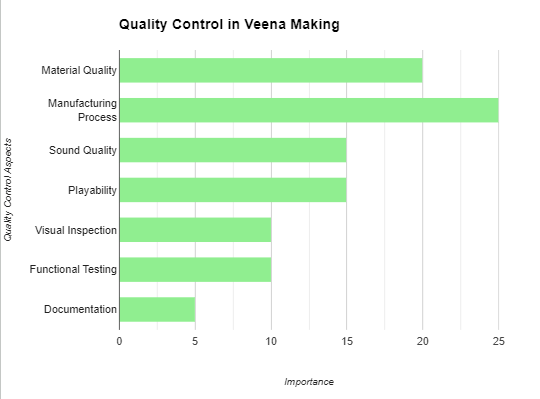
How to do cost management of Veena making?
Budgeting for Veena Makers
Raw Materials: Budgeting for the purchase of high-quality wood, strings, and other materials is critical. Ensure to account for fluctuations in material costs due to market changes or availability.
Labor Costs: Budget for skilled artisans, including wages, training, and benefits. Consider the costs of hiring apprentices to ensure the continuity of the craft.
Overheads: Allocate a budget for utilities, rent, equipment maintenance, and other operational costs.
Marketing and Sales: Include costs for marketing, such as online promotions, participation in exhibitions, and e-commerce platform fees.
Contingency Fund: Set aside a portion of the budget for unforeseen expenses, such as equipment repairs or sudden price increases in materials.
Cost Reduction Strategies
Bulk Purchasing: Purchase materials in bulk to take advantage of discounts and reduce per-unit costs.
Process Optimization: Streamline the production process to minimize waste and inefficiencies. Invest in tools or minor technology that can help improve precision and reduce errors.
Outsourcing Non-Core Activities: Consider outsourcing non-core activities such as marketing, accounting, or logistics to specialized agencies, allowing artisans to focus on craftsmanship.
Energy Efficiency: Implement energy-saving practices, such as using energy-efficient lighting and machinery, to reduce utility costs.
Waste Management: Recycle or repurpose wood scraps and other by-products to minimize waste and create additional revenue streams (e.g., small handcrafted items).
Estimated Pricing of the Product
Cost-Based Pricing: Calculate the total cost of producing a veena, including materials, labor, overheads, and mark-up to determine the selling price. This ensures that all costs are covered and a profit margin is maintained.
Value-Based Pricing: Consider the perceived value of the veena to the customer. Factors like craftsmanship, customization, cultural significance, and brand reputation can allow for higher pricing.
Competitive Pricing: Research the prices of similar products in the market. Position your product competitively while ensuring it reflects the quality and uniqueness of your veenas.
Tiered Pricing: Offer different price points based on product variations, such as basic, mid-range, and premium models. This caters to different customer segments.
Financial Planning
Cash Flow Management: Monitor cash flow regularly to ensure sufficient liquidity for day-to-day operations. Implement strategies like offering early payment discounts to customers to improve cash flow.
Investment in Technology: Plan for investments in tools or technology that can enhance productivity without compromising craftsmanship. Consider long-term returns on such investments.
Diversification of Revenue Streams: Explore additional revenue opportunities such as workshops, repair services, or selling related products (e.g., veena accessories).
Debt Management: If taking loans for expansion or equipment, ensure that the repayment terms are manageable. Evaluate the return on investment (ROI) before incurring any debt.
Savings and Emergency Funds: Allocate a portion of profits to savings and create an emergency fund to safeguard against market downturns or unexpected expenses.
Cost Management Strategies
Regular Financial Reviews: Conduct monthly or quarterly reviews of costs versus budget. Adjust plans and strategies based on the financial performance to stay within budget.
Supplier Negotiations: Regularly negotiate with suppliers for better rates, especially if you have established a long-term relationship. Consider alternative suppliers to reduce costs.
Inventory Management: Maintain an optimal level of inventory to avoid overstocking or stockouts. This helps in reducing storage costs and minimizing capital tied up in inventory.
Lean Manufacturing: Apply lean manufacturing principles to minimize waste, improve efficiency, and reduce costs throughout the production process.
Cost Tracking and Analysis: Implement a cost tracking system to monitor expenditures in real-time. Analyze costs to identify trends or areas where savings can be made.
Budgeting for Manufacturers
Annual Budget Planning: Develop an annual budget that aligns with your business goals and expected demand. Review this budget periodically to ensure it reflects current market conditions.
Capital Expenditures (CapEx): Plan for capital expenditures, such as new machinery or workshop upgrades, within the budget. Ensure these investments align with long-term business objectives.
Operational Expenditures (OpEx): Clearly define operational expenditures, including materials, labor, and utilities. Monitor these closely to stay within budget and avoid overspending.
Profit Margins: Set target profit margins and ensure that all pricing and budgeting strategies support these margins.
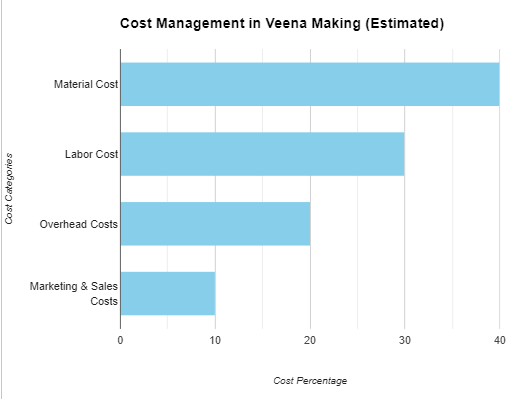
Business Authenticity of Veena making
Business authenticity in veena making refers to the genuine nature and integrity of the craft and its practitioners. It encompasses several key aspects:
1. Traditional Craftsmanship:
Preservation of Techniques: Adhering to traditional veena making techniques, ensuring the continuity of the craft's heritage.
Skill and Expertise: Demonstrating the requisite skills and expertise to create high-quality veenas.
2. Ethical Sourcing:
Sustainable Materials: Sourcing materials ethically and sustainably, particularly wood, to minimize environmental impact.
Fair Trade Practices: Ensuring fair trade practices in the sourcing of materials and components.
3. Transparency and Honesty:
Open Communication: Maintaining open and honest communication with customers about the veena making process, materials used, and pricing.
Transparency in Production: Providing transparency into the production process, allowing customers to see the craftsmanship firsthand.
4. Cultural Respect:
Preservation of Cultural Significance: Understanding and respecting the cultural significance of the veena and its traditions.
Authentic Designs: Creating veenas that reflect traditional designs and styles, while incorporating modern elements where appropriate.
5. Customer Satisfaction:
Prioritizing Customer Needs: Putting the customer's needs and satisfaction at the forefront of the business.
Quality Assurance: Ensuring that veenas meet high standards of quality and craftsmanship.
Excellent Customer Service: Providing exceptional customer service, including after-sales support and maintenance.
6. Community Engagement:
Supporting Local Artisans: Supporting local artisans and communities involved in the veena making process.
Contributing to Cultural Preservation: Actively participating in initiatives to preserve and promote the cultural heritage of veena making.
What are the credit checks of Veena making?
Credit checks play an essential role in managing financial risks and ensuring smooth transactions in the veena-making business, particularly when dealing with customers, suppliers, or financial institutions. Credit checks are a valuable tool in managing financial risk in veena making, helping to ensure that both customer transactions and supplier relationships are conducted smoothly and securely.
Importance of Credit Checks
Assessing Customer Creditworthiness: If veena makers offer credit terms to customers (such as payment plans or deferred payments), credit checks help assess the likelihood of the customer repaying on time. This minimizes the risk of bad debts.
Supplier Reliability: Credit checks on suppliers can provide insights into their financial stability, ensuring they are reliable and won’t default on delivering materials. This is crucial when entering into long-term contracts or bulk purchasing agreements.
Securing Loans or Financing: When seeking loans or other forms of financing, veena makers may undergo credit checks by financial institutions. A strong credit history can improve the chances of securing favorable loan terms.
Conducting Credit Checks
For Customers:
Obtain Basic Information: Collect basic information from the customer, such as their full name, address, and financial details.
Credit Agencies: Use credit reporting agencies to check the customer’s credit score and payment history.
Internal Records: Review the customer’s previous transactions with your business, if applicable, to assess their payment behavior.
References: Request trade references or bank references, particularly for larger orders or business customers.
For Suppliers:
Credit Reports: Obtain credit reports from credit agencies that provide business credit scores.
Financial Statements: Review the supplier’s financial statements, if available, to assess their financial health.
Industry Reputation: Gather feedback from other businesses in the industry regarding the supplier’s reliability and payment history.
For Your Business:
Maintain Good Credit: Ensure timely payment of all debts, loans, and bills to maintain a good credit score for your own business. This will help in securing favorable terms with suppliers and financial institutions.
Regular Monitoring: Regularly monitor your business credit score and address any discrepancies or issues that may arise.
Managing Credit Risk
Setting Credit Limits: Based on the results of the credit check, set appropriate credit limits for customers or suppliers. For high-risk customers, consider requiring upfront payments or a larger deposit.
Payment Terms: Offer flexible payment terms based on creditworthiness. For instance, offer longer payment terms to customers with strong credit and shorter terms to those with weaker credit.
Credit Insurance: Consider obtaining credit insurance to protect against the risk of non-payment, especially when dealing with large orders or international customers.
Monitor Accounts Receivable: Keep a close eye on accounts receivable and follow up promptly on overdue payments. Implementing an automated system for reminders and collections can improve efficiency.
Legal and Ethical Considerations
Consent and Privacy: Ensure you have the customer’s or supplier’s consent before conducting a credit check. Be transparent about why the credit check is necessary.
Accuracy of Information: Ensure that the information used for credit checks is accurate and up-to-date. Disputing inaccurate information promptly can help maintain relationships.
Compliance: Comply with local laws and regulations regarding credit reporting and data protection to avoid legal issues.
Benefits of Effective Credit Checks
Reduced Financial Risk: By assessing creditworthiness, veena makers can minimize the risk of non-payment and bad debts.
Improved Cash Flow: Ensuring that customers are likely to pay on time helps maintain steady cash flow, which is crucial for the operational stability of the business.
Better Supplier Relationships: Conducting credit checks on suppliers can lead to more reliable partnerships and better negotiation power in terms of payment terms and discounts.
Challenges and Considerations
Cost of Credit Checks: Credit checks may involve costs, particularly when using third-party credit reporting agencies. Balancing the cost with the potential risk is essential.
Impact on Customer Relationships: Some customers may perceive credit checks as intrusive. Clear communication and transparency can help mitigate any negative impact.
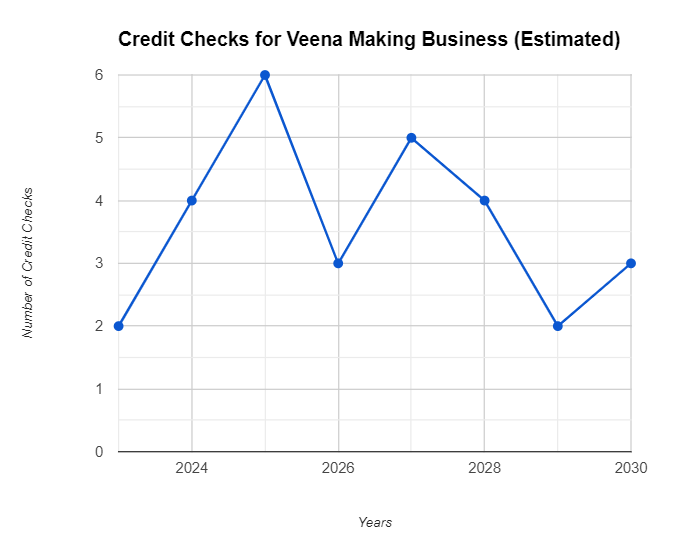
What is the importance of insurance for Veena making?
Insurance is crucial for veena makers to protect their business from potential financial losses. By obtaining appropriate insurance coverage, veena makers can protect their business from financial risks and ensure its long-term sustainability. It is recommended to consult with an insurance professional to determine the specific types and coverage levels that are best suited for your business needs.
1. Property Insurance:
Workshop and Equipment: Protects against damage to your workshop, equipment, and tools due to fire, theft, natural disasters, or accidents.
Inventory: Covers the cost of replacing lost or damaged veenas, materials, and components.
2. Liability Insurance:
Product Liability: Protects against claims of product liability if a customer is injured or damaged due to a defective veena.
Professional Liability: Covers claims of negligence or professional misconduct.
3. Business Interruption Insurance:
Loss of Income: Provides coverage for lost income if your business is unable to operate due to a covered event, such as a natural disaster or equipment damage.
4. Workers' Compensation Insurance:
Employee Injuries: Covers medical expenses and lost wages for employees who are injured on the job.
5. Cyber Liability Insurance:
Data Breaches: Protects against financial losses and legal liabilities arising from data breaches or cyberattacks.
6. Transportation Insurance:
Damage in Transit: Covers damage to veenas during transportation, whether they are being shipped to customers or suppliers.
Currency exchange of Veena making
Managing currency exchange is crucial for veena makers, especially those involved in international trade. Exchange rates can significantly impact the cost of materials, pricing of products, and overall profitability. Managing currency exchange in veena making involves a combination of monitoring exchange rates, implementing hedging strategies, and incorporating forex management into overall financial planning. By taking a proactive approach, veena makers can mitigate forex risks and optimize their profitability in international markets.
Understanding Currency Exchange in Veena Making
Exchange Rates: The value of one currency relative to another can fluctuate due to various economic factors. These fluctuations can affect the cost of importing raw materials or the revenue from exporting veenas.
Forex Risk: The risk associated with changes in exchange rates is known as foreign exchange (forex) risk. This risk can lead to increased costs or reduced revenues if not managed properly.
Managing Currency Exchange
Currency Exchange Monitoring: Regularly monitor exchange rates to understand trends and anticipate potential impacts on your business. Staying informed about global economic conditions can help in making better financial decisions.
Negotiating Contracts in Stable Currencies: When entering contracts with international suppliers or customers, consider using a stable currency, such as the US Dollar or Euro, to reduce exposure to volatile currencies.
Hedging Strategies
Forward Contracts: Enter into forward contracts with financial institutions to lock in a specific exchange rate for a future date. This can protect against unfavorable movements in exchange rates.
Options Contracts: Purchase currency options, which give you the right, but not the obligation, to exchange currency at a predetermined rate. This provides flexibility and protection against adverse rate movements.
Natural Hedging: Match the currency of your costs with the currency of your revenues. For example, if you are selling veenas to the US market and also sourcing materials from the US, conducting both transactions in USD reduces forex risk.
Currency Swaps: Engage in currency swaps to exchange principal and interest payments in one currency for those in another. This can help manage forex risk, particularly in long-term contracts.
Forex Management in Veena Making
Multicurrency Accounts: Consider opening multicurrency bank accounts to hold and manage different currencies. This can reduce the need for frequent conversions and minimize transaction costs.
Dynamic Pricing: Implement dynamic pricing strategies where the price of veenas is adjusted based on current exchange rates. This ensures that your pricing remains competitive while protecting your profit margins.
Invoice in Local Currency: If feasible, invoice customers in your local currency to transfer the exchange rate risk to the buyer. This can be advantageous, especially in markets where your currency is stable.
Financial Planning and Forex Management
Budgeting for Forex Fluctuations: Include a buffer in your budget to account for potential fluctuations in exchange rates. This can help avoid unexpected financial shortfalls.
Risk Assessment: Regularly assess the forex risk associated with your international transactions. This includes evaluating the potential impact on profitability and cash flow.
Consulting with Forex Experts: Work with forex consultants or financial advisors to develop and implement effective forex management strategies tailored to your business needs.
Cost Management and Pricing
Incorporating Exchange Rate Margins: When pricing veenas for international markets, consider incorporating a margin to cover potential forex losses. This can help maintain profitability even when exchange rates fluctuate.
Revisiting Pricing Strategies: Regularly revisit your pricing strategies to ensure they align with current exchange rates. Adjust prices as necessary to reflect changes in costs due to currency movements.
Challenges and Considerations
Volatility in Emerging Markets: If you are dealing with currencies from emerging markets, be aware that these can be particularly volatile. Managing forex risk in these markets may require more aggressive hedging strategies.
Transaction Costs: Currency exchange often involves transaction costs, including fees and spreads. Minimizing these costs through strategic planning can improve profitability.
Benefits of Effective Forex Management
Stability in Profit Margins: By managing currency exchange effectively, veena makers can protect their profit margins from the impact of adverse exchange rate movements.
Improved Financial Predictability: Hedging strategies and proactive forex management can provide greater financial predictability, allowing for better planning and decision-making.
Enhanced Competitiveness: Effective currency exchange management can help veena makers remain competitive in international markets by offering stable and attractive pricing to customers.
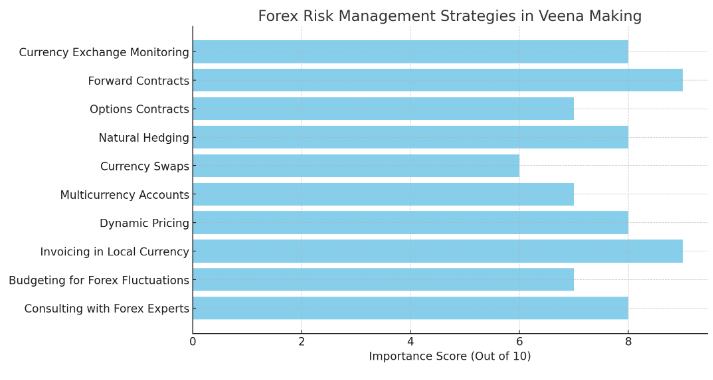
What are the sustainability measures of Veena making?
Sustainability is becoming increasingly important in various industries, and the traditional craft of veena making is no exception. By adopting sustainable practices, veena makers can contribute to environmental protection, promote social responsibility, and ensure the long-term viability of their craft.
Key Areas of Sustainability in Veena Making:
Ethical Sourcing: Ensure that the wood used for veenas is sourced from sustainably managed forests.
Recycled Materials: Incorporate recycled materials, such as recycled metal for frets or tuning pegs, whenever possible.
Alternative Materials: Explore the use of alternative materials with a lower environmental impact, such as bamboo or certain synthetic materials.
Energy Efficiency:
Renewable Energy: Use renewable energy sources, like solar or wind power, to operate workshops and tools.
Energy-Efficient Equipment: Invest in energy-efficient machinery and equipment to reduce energy consumption.
LED Lighting: Use LED lighting in workshops to minimize energy consumption and improve lighting quality.
Waste Reduction:
Reduce, Reuse, Recycle: Implement waste reduction practices, such as recycling wood scraps, metal shavings, and packaging materials.
Composting: Compost organic waste generated during the manufacturing process.
Minimalist Packaging: Use minimal and recyclable packaging for veenas to reduce waste.
Water Conservation:
Efficient Water Use: Implement water-saving measures in workshops, such as using low-flow fixtures and collecting rainwater for non-potable use.
Wastewater Treatment: Treat wastewater before discharging it into the environment.
Social Responsibility:
Fair Labor Practices: Ensure fair wages, working conditions, and benefits for workers.
Community Engagement: Support local communities and initiatives related to sustainability and environmental protection.
Preservation of Traditional Skills: Promote the preservation of traditional veena making techniques to ensure the continuity of the craft.
Benefits of Sustainable Veena Making:
Reduced Environmental Impact: Contributes to mitigating climate change and protecting biodiversity.
Enhanced Reputation: Builds a positive brand image and attracts environmentally conscious customers.
Cost Savings: Can lead to cost savings through efficient resource use and waste reduction.
Community Development: Promotes social responsibility and supports local communities.
Long-Term Viability: Ensures the sustainability of the veena making industry for future generations.
How to do shipping and handling of Veena making?
Shipping and handling are essential aspects of veena making, ensuring the safe and timely delivery of instruments to customers.
1. Packaging:
Protective Materials: Use high-quality packaging materials, such as wooden crates, bubble wrap, and cushioning, to protect the veena during transit.
Custom Packaging: Offer custom packaging options to meet specific customer requirements or for high-value instruments.
Drop Tests: Conduct drop tests to ensure the packaging can withstand shocks and vibrations.
2. Shipping Methods:
Domestic Shipping: Choose a reliable shipping carrier with experience in handling delicate instruments.
International Shipping: Consider factors such as customs regulations, shipping times, and costs when shipping veenas internationally.
Insurance: Obtain insurance coverage to protect the veena against damage or loss during transit.
3. Shipping Costs:
Factors Affecting Cost: Shipping costs are influenced by factors such as weight, dimensions, destination, and shipping method.
Cost Estimates: Provide customers with accurate shipping cost estimates upfront.
4. Tracking and Notifications:
Shipping Tracking: Use tracking systems to monitor the shipment's progress and provide customers with updates.
Notifications: Notify customers of shipment status, including estimated delivery dates and tracking information.
5. Delivery Options:
Standard Shipping: Offer standard shipping options with reasonable delivery times and costs.
Expedited Shipping: Provide expedited shipping options for customers who require faster delivery.
Local Pickup: Allow customers to pick up their veenas from your workshop for convenience.
6. Return Policy:
Clear Policy: Have a clear and transparent return policy in place, outlining the conditions under which customers can return a veena.
Handling Returns: Ensure efficient handling of returns, including inspections and refunds.
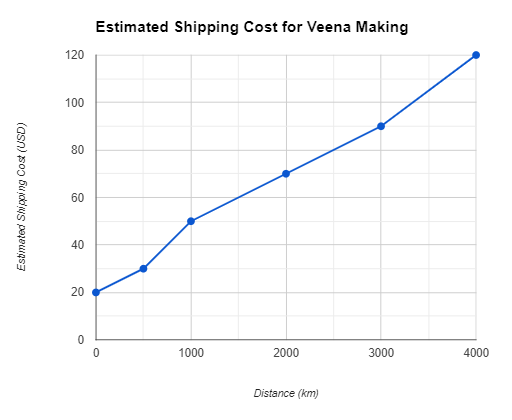
An insight about the products:
Physical Characteristics:
The full-sized Bobbili Veena is approximately 53 inches in length, with a width diameter of about 15 inches.
The height of the Veena is around 12 inches, and it weighs approximately 10 kilograms.
Cost:
A full-sized Bobbili Veena is typically sold for approximately INR 20,000 in the market.
Miniature Veenas:
In addition to the full-sized instrument, artisans also craft miniature versions of the Bobbili Veena as decorative items or showpieces.
The miniature Veenas range in size from as small as 9 inches to 23 inches in length, with a width of 3-4 inches.
These miniatures maintain the intricate details of the full-sized Veena, though they are not functional for playing music.
Cost of Miniature Veenas:
The price of a miniature Bobbili Veena starts from approximately INR 800 and can vary based on size and craftsmanship.
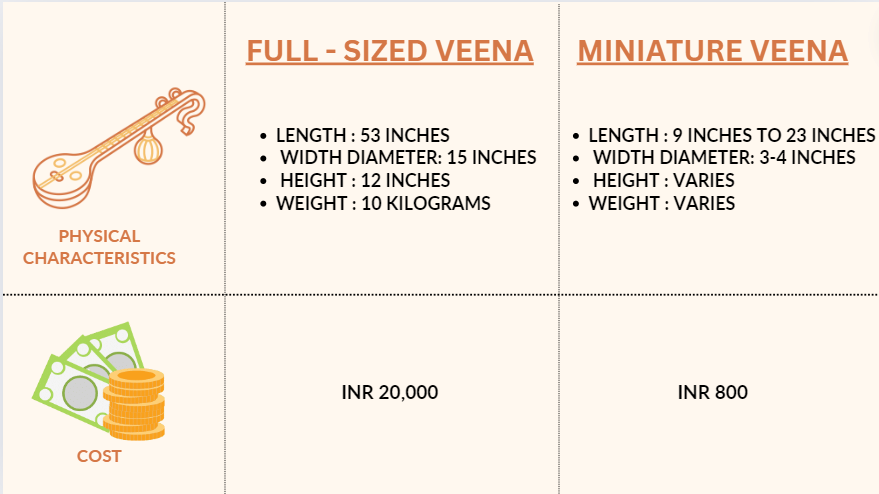
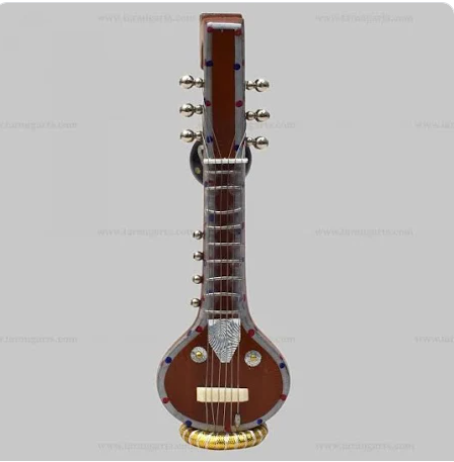
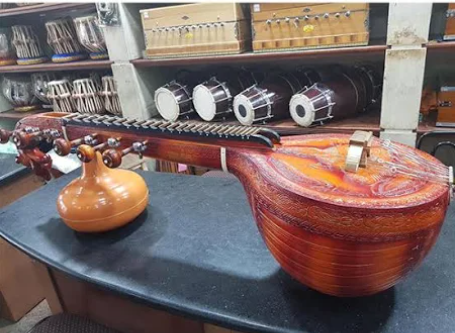
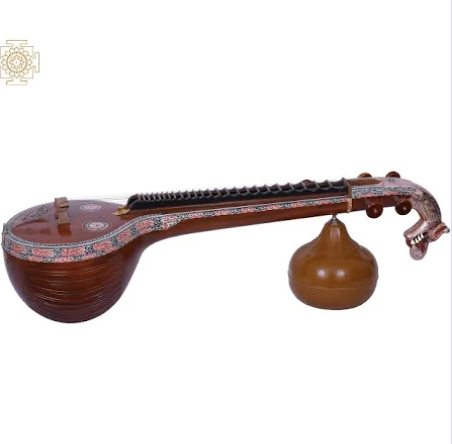
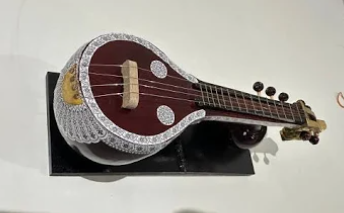

MANUFACTURERS OF VEENA:
Details of the source paper:
Professor Bibhudutta Baral and Parvathi Pooja - Veena Making - Bobbili, Andhra Pradesh - NID, Bengaluru - D’source - Paper link
Recommended
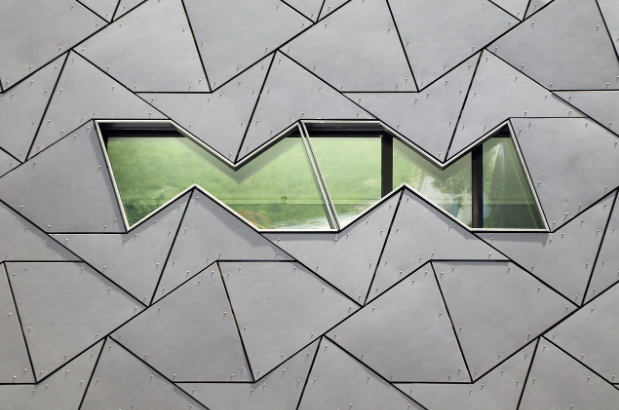

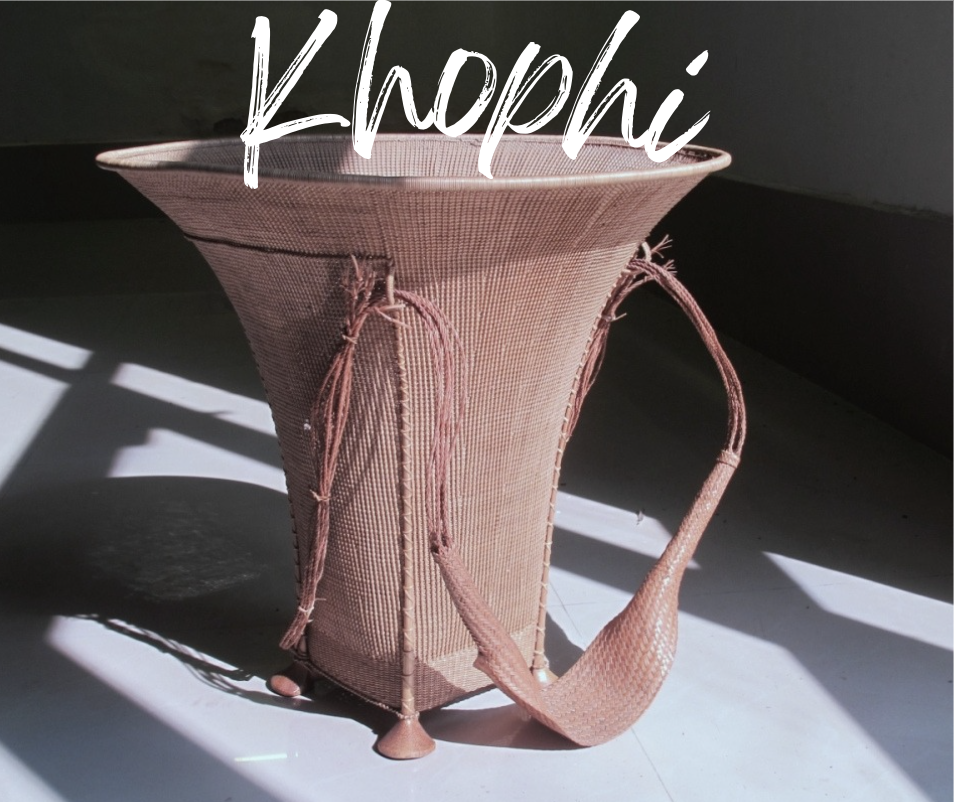