Wholesale Clay Jewelry from Dumdum, Kolkata : Blending Tradition with Modern B2B Demand
Nov 17, 2024 | Udit Kaur
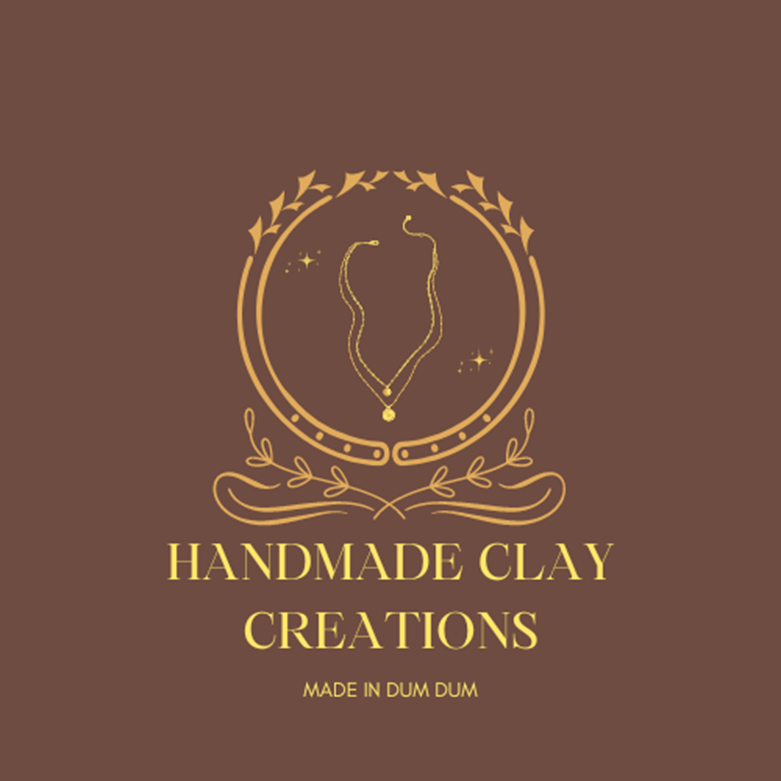
1. Introduction to Clay Jewelry: A Timeless Craft
Dumdum, Kolkata, has emerged as a prominent hub for the art of clay jewelry making, showcasing the skill and dedication of local artisans who bring this craft to life. These artisans expertly blend traditional techniques passed down through generations with innovative approaches that cater to contemporary trends. The intricate process of shaping, baking, and painting clay results in unique pieces that embody both cultural heritage and modern design. The growing demand for sustainable and ethically crafted jewelry has further propelled the popularity of clay ornaments, opening opportunities for both local and international wholesale markets. This craft not only provides a sustainable livelihood for artisans but also highlights the importance of preserving traditional craftsmanship in an increasingly mechanized world.
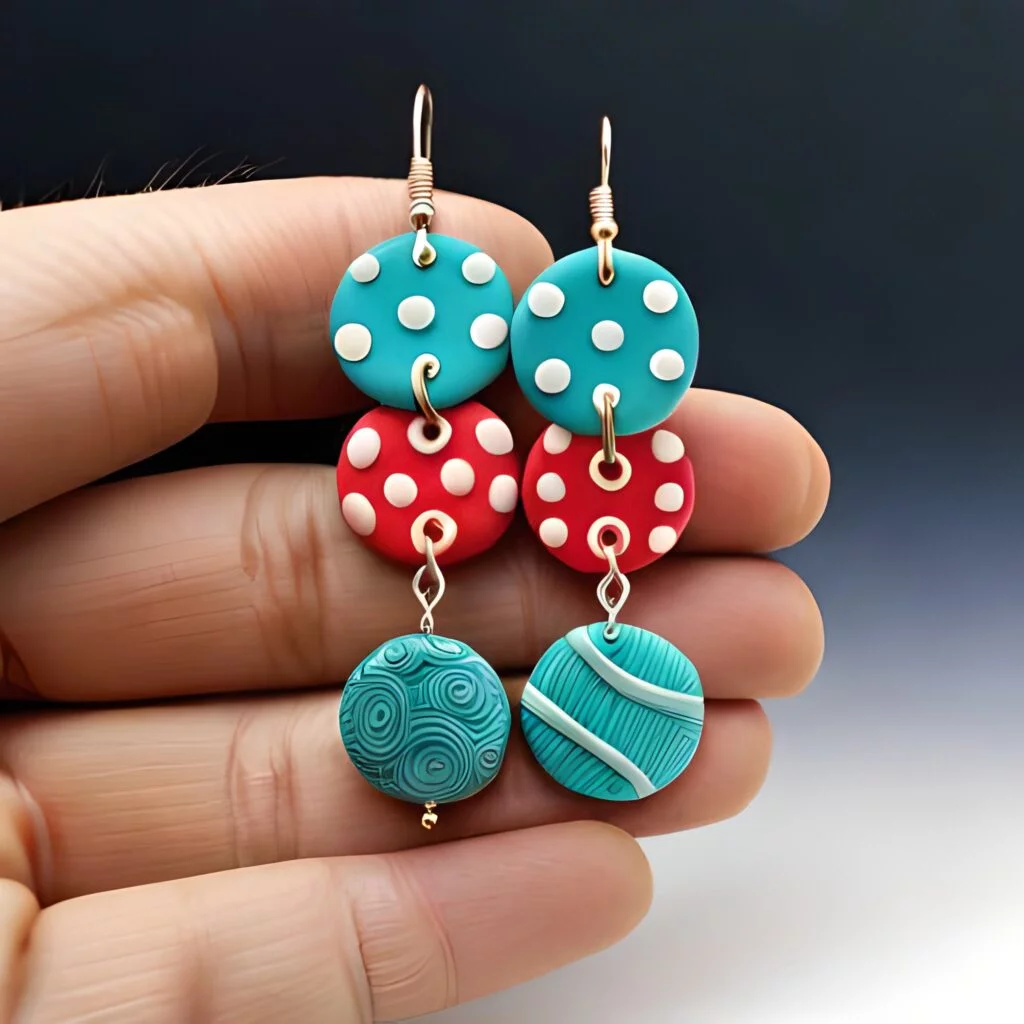
One such artisan keeping this tradition alive is Ms. Debanti Sen, a Kolkata-based craftsperson who has been working in the field for over eight years. Through her venture “My Decor8 Craft,” Debanti has brought innovation to clay jewelry by incorporating modern materials like M-seal and polyamide hardeners, making her products unique and timeless. In this blog, we will explore the process, tools, and creativity behind her art clay jewelry from Dumdum, Kolkata.
2. The Significance of Handmade Clay Jewelry in India
Clay jewelry in India is not just a fashion statement; it represents a rich tradition that has been passed down through generations. With natural themes inspired by mythology, ancient motifs, and geometric patterns, each piece is handcrafted to reflect a connection with the earth. The process of making clay jewelry is labor-intensive but rewarding, as each item is molded and painted by hand, ensuring that no two pieces are the same. In recent years, the popularity of clay jewelry has grown, thanks to its adaptability to modern fashion trends and its affordability.
Handmade ornaments crafted from clay are now a sought-after accessory among fashion-conscious individuals who prefer eco-friendly alternatives. The use of modern compounds like M-seal and polyamide hardeners in the creation of clay jewelry adds to their durability and allows artisans to create intricate designs with ease. Moreover, the handcrafted nature of these products means they carry a personal touch, resonating with consumers who value authenticity in their accessories.
3. Tools and Raw Materials: The Backbone of Clay Jewelry Making
Creating intricate and unique clay jewelry requires a range of tools and raw materials, each serving a specific purpose in the design and finishing process. Here’s an overview of the essential tools and materials used in making art clay jewelry:
1. Epoxy Compound (White M-seal)- The primary material used in the creation of clay jewelry, white M-seal, is an epoxy compound that hardens when exposed to air. This compound is preferred for its ease of use, quick setting properties, and ability to mold into any desired shape.
2. Knife- A basic tool used to carve out extra parts of the clay and help shape intricate designs, a knife is indispensable in giving the desired shape to the motifs.
3. Wire Cutter- Used to cut jewelry wires and hooks, a wire cutter helps ensure precision in the final assembly of the jewelry.
4. Acrylic Paint and 3D Acrylic Paint- Acrylic paint is used to decorate the jewelry, providing vibrant and durable colors. 3D acrylic paint, in particular, adds an embossed look, enhancing the aesthetic appeal of the final product.
5. Carved Wooden Blocks- These are used to create unique impressions on the clay surface. These blocks come in various designs, allowing artisans to experiment with different textures and motifs.
6. Rolling Pin- A simple tool, the rolling pin is used to flatten the clay dough to a uniform thickness, ensuring that the jewelry pieces are even and polished.
7. Paint Brushes- Used for detailing and adding final touches to the jewelry, paint brushes allow for intricate designs and color blending on the clay.
8. Cotton Threads- These threads are essential for creating a rope or string to hold pendants or necklaces together. They are often used in natural colors to complement the earthy tones of the clay jewelry.
9. Bamboo Board- A decorative tool, the bamboo board serves as a base for certain jewelry pieces, giving them a natural and organic feel.
10. Wires and Hooks- These are essential for assembling the jewelry and attaching various pieces together. Wires and hooks are also used to create adjustable elements in necklaces and earrings.
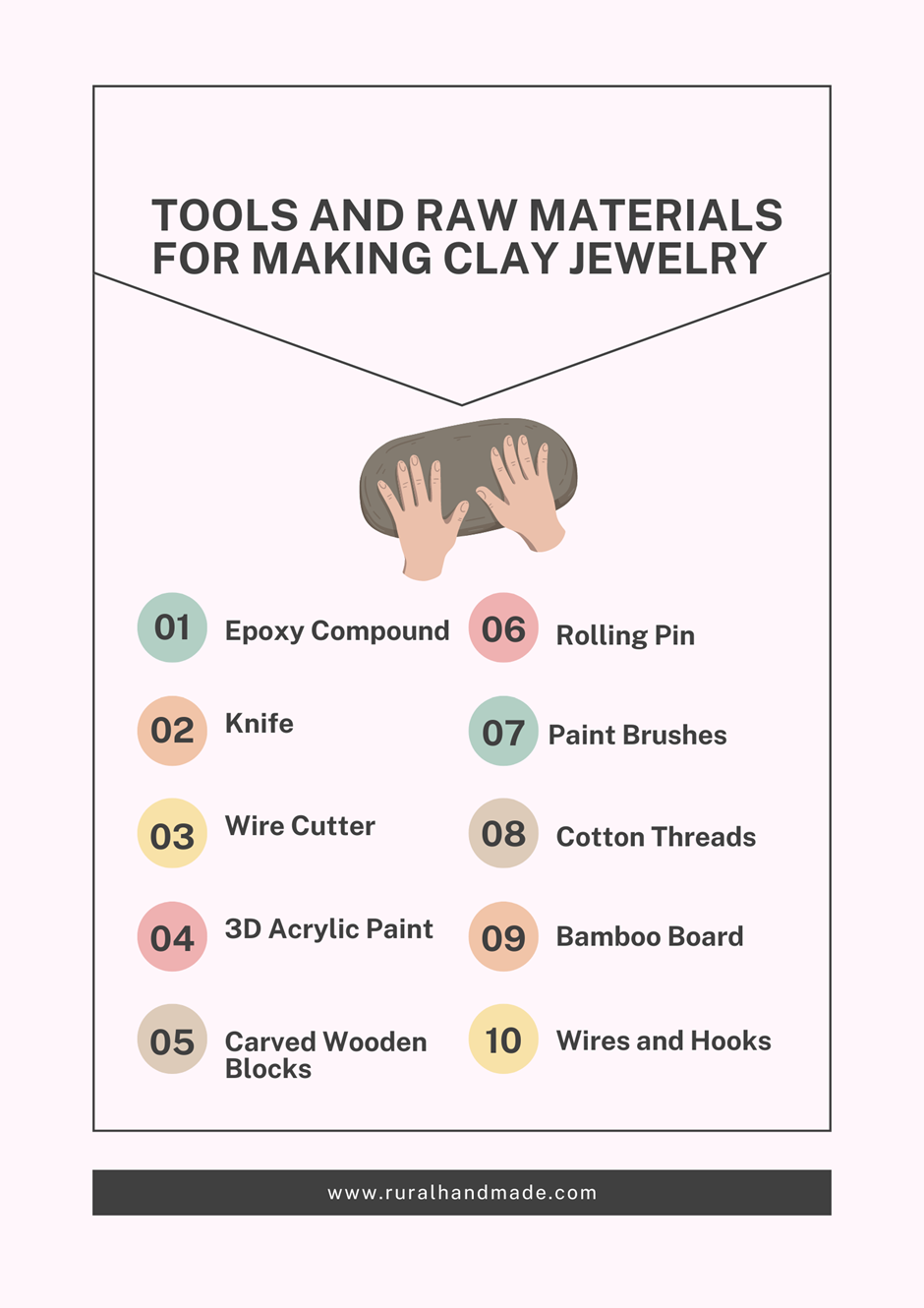
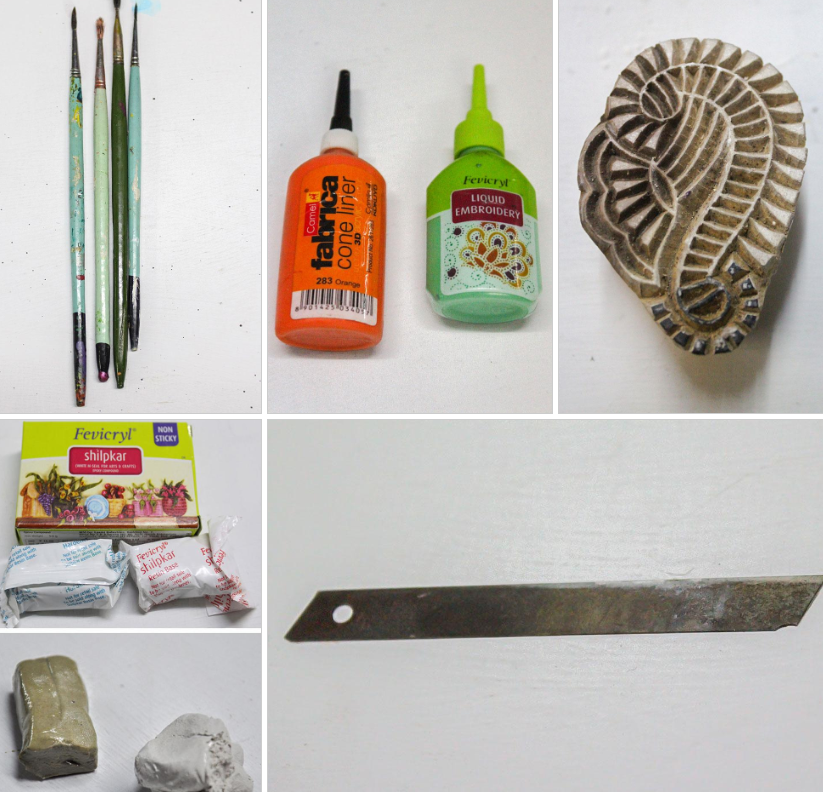
4. The Making Process: From Raw Clay to a Fashionable Ornament
The process of creating handmade clay jewelry is intricate and requires a blend of creativity and craftsmanship. The artisan must carefully shape, mold, and design each piece to ensure that it is not only aesthetically pleasing but also durable and functional.
Step 1: Preparing the Clay
The creation process begins with mixing epoxy compound white M-seal and polyamide hardener with silica powder to create clay in varying shades. This mixture undergoes a chemical reaction, hardening into a smooth yet firm substance. Once the clay is ready, it is dusted with talcum powder to prevent sticking and to achieve a smooth finish.
Step 2: Shaping the Jewelry
Next, the clay is flattened using a rolling pin and cut into specific shapes using a knife. These shapes, often diamonds, circles, or other geometric patterns, form the basis of pendants or earrings. Holes are pierced at appropriate places to attach metal rings or ropes later in the process.
Step 3: Creating Impressions
To give the jewelry its unique texture and design, wooden blocks with carved motifs are pressed into the clay. This step adds intricate patterns to the surface, which will later be highlighted with paint.
Step 4: Drying and Painting
Once the clay molds are dry, they are ready to be painted. Using acrylic and 3D acrylic paints, artisans add vibrant colors and dramatic textures to the jewelry. The paint not only enhances the design but also adds an embossed effect, giving the jewelry a three-dimensional look.
Step 5: Assembling the Jewelry
After painting, the jewelry pieces are assembled. Wires are cut and inserted into the holes made earlier to create loops or hooks. Cotton threads are then passed through these loops to complete pendants or necklaces. The jewelry is now ready to be worn, offering a striking addition to any outfit.
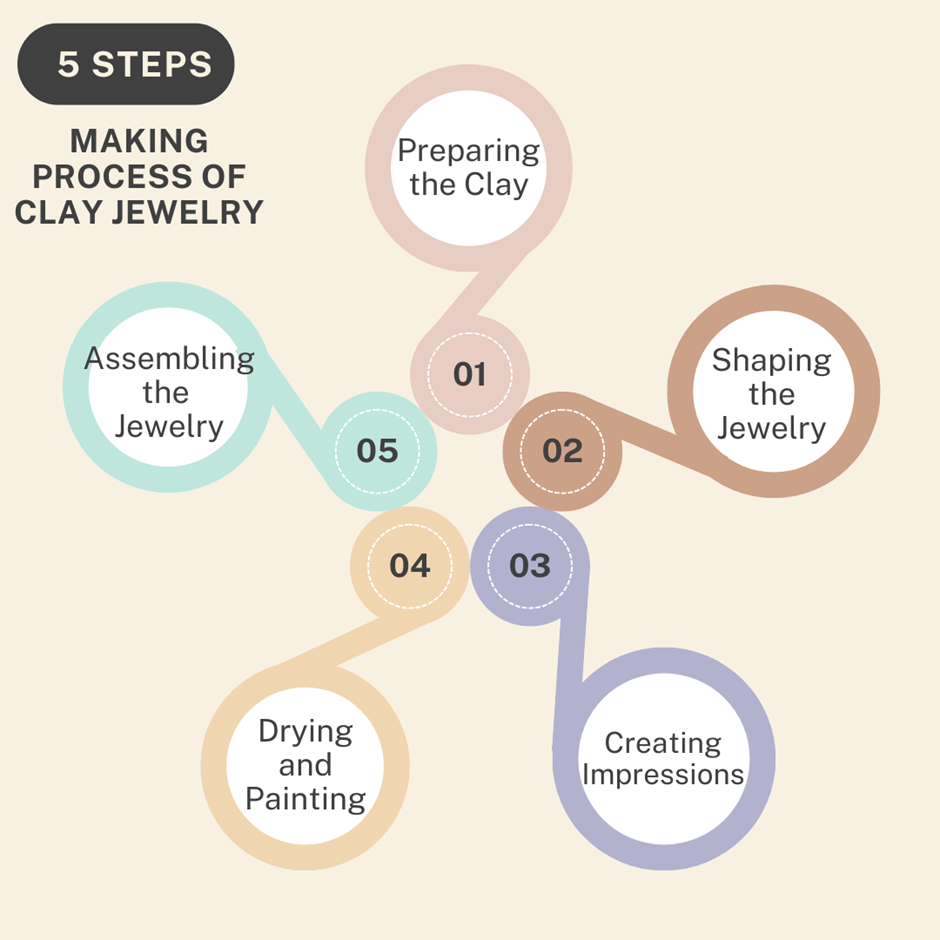
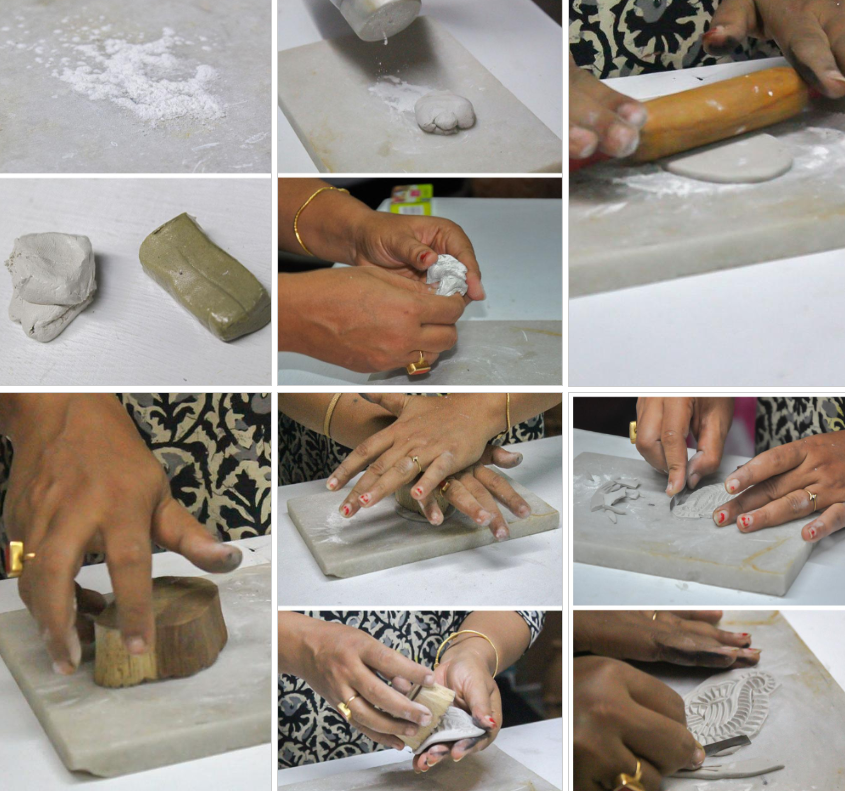
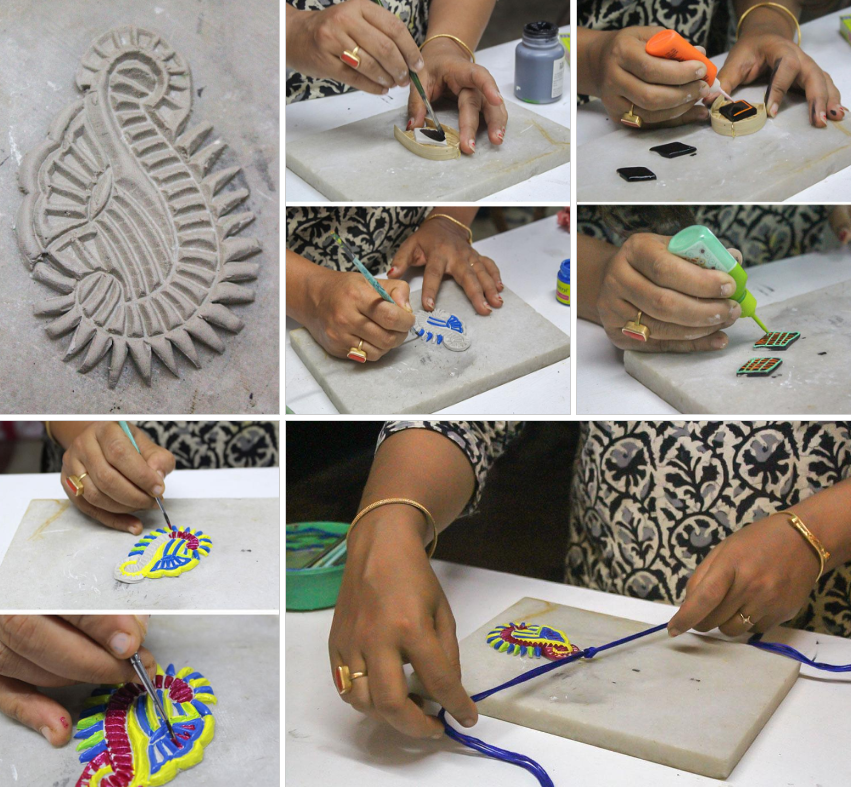
5. Product Range at My Decor8 Craft: Merging Tradition with Innovation
Ms. Debanti Sen’s venture, “My Decor8 Craft,” has been a significant contributor to Kolkata's handmade jewelry market since its inception in 2013. Her unique approach to clay jewelry, especially the use of white M-seal, has garnered attention from both local and international customers.
The product range at My Decor8 Craft includes:
Pendants: The pendants come in various shapes, sizes, and motifs. Each one is hand-painted and molded to reflect nature, traditional designs, or modern abstract patterns.
Earrings: These lightweight earrings are not only affordable but also highly customizable. Priced between INR 120 and INR 150, they offer a stylish option for both daily wear and special occasions.
Necklaces: The necklaces created by Debanti often feature intricate pendant designs complemented by natural threads or beads. Priced between INR 300 and INR 350, these pieces add a touch of elegance to any outfit.
Key Chains: Combining utility with art, Debanti’s keychains are made using similar techniques and materials as her jewelry, offering a unique accessory for everyday use.
My Decor8 Craft has made its collections available online through social media platforms like Facebook and WhatsApp, making it easy for customers across the globe to purchase these exquisite pieces of handmade jewelry.
6. Ensuring Top-Notch Quality in Clay Jewelry
When it comes to clay jewelry, quality control is crucial. The intricate craftsmanship involved in shaping and detailing the clay ensures that every piece is unique and made with precision. Artisans like Ms. Debanti Sen, a pioneer in handmade clay jewelry from Dumdum, use only high-quality materials like epoxy compound to create durable, premium pieces. By adhering to strict quality standards, these jewelry items showcase superior craftsmanship, making them stand out in a market flooded with mass-produced accessories. This ensures that every pendant or earring produced is a true work of art, reflecting the rich tradition of handmade jewelry.
Ensuring top-notch quality in clay jewelry involves several meticulous steps that artisans take to enhance both durability and aesthetic appeal. Here’s an outline of the key practices followed to maintain high standards in clay jewelry craftsmanship:
Material Selection: Artisans like Ms. Debanti Sen prioritize the use of high-quality materials such as epoxy compounds and premium clays. These materials not only ensure durability but also enhance the finish of the final product.
Preparation of Clay: Proper conditioning of the clay is crucial before any shaping begins. This involves kneading the clay to remove air bubbles and ensure a smooth texture, which reduces the risk of cracking or warping during and after the curing process.
Design Precision: Every piece is handcrafted with great attention to detail. Artisans use fine tools to sculpt intricate patterns and designs, ensuring uniformity across batches while retaining the uniqueness of handmade work.
Curing Process: Clay jewelry undergoes a precise baking or curing process at specific temperatures. This step ensures the clay hardens correctly, making the jewelry resistant to breakage. Any variations in temperature or time could compromise the integrity of the piece.
Surface Finishing: After curing, the jewelry is sanded, polished, or coated with a varnish or resin to achieve a smooth, shiny surface. This not only enhances the appearance but also protects the piece from moisture and wear.
Quality Inspections: Before the jewelry is finalized, each item goes through a thorough quality inspection. Artisans check for imperfections, structural stability, and ensure that the colors and designs align with the intended vision.
By following these steps, artisans can ensure that each piece of clay jewelry maintains top-notch quality and offers a durable, elegant product to customers.
7. The Art of Uniqueness: Handmade Clay Jewelry That Stands Out
One of the hallmarks of handmade clay jewelry is its unique designs. Unlike mass-produced items, each piece is crafted individually, often drawing inspiration from nature, mythology, and geometric patterns. Customization plays a big role, allowing buyers to own exclusive jewelry tailored to their preferences. These pieces are not just ornaments; they are artworks, with limited edition collections and designs that make each piece distinctive. This uniqueness enhances the allure of clay jewelry, making it a sought-after choice for those who appreciate exclusive designs.
Individual Craftsmanship: Each handmade clay jewelry piece is uniquely crafted, drawing inspiration from diverse themes like nature and mythology, ensuring no two pieces are identical.
Customization: Buyers can personalize their jewelry, making each item exclusive and tailored to their style preferences, adding a personal touch to the artistry.
Limited Editions: Handmade collections often feature limited designs, enhancing the exclusivity and appeal for those seeking rare, one-of-a-kind accessories.
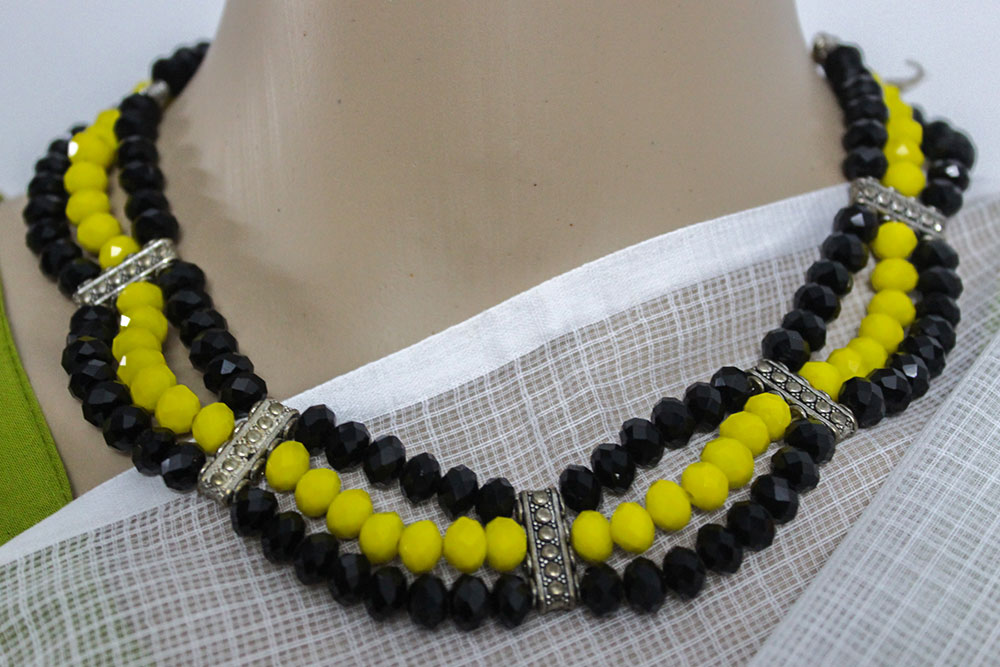
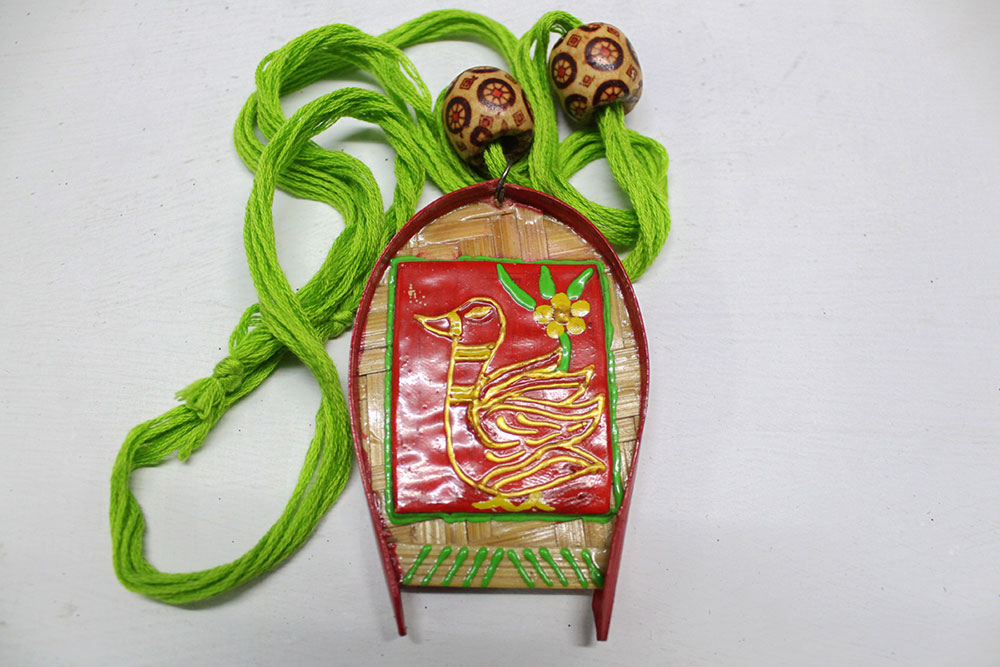
8. Sustainable and Ethical Sourcing of Raw Materials for Clay Jewelry
Sustainability plays a vital role in the creation of clay jewelry from Dumdum. The artisans are committed to using eco-friendly materials, ensuring that the sourcing practices align with sustainable principles. The clay is locally sourced, supporting both the environment and the local economy, while partnerships with ethical suppliers ensure the use of non-toxic, biodegradable materials. This dedication to sustainable raw materials not only enhances the product’s appeal but also promotes eco-friendly practices in jewelry production, making clay jewelry a responsible choice for consumers.
Here are the sustainable and ethical sources of raw materials for clay jewelry:
Locally Sourced Clay: Artisans obtain clay from local suppliers, reducing transportation emissions and supporting the local economy.
Non-Toxic Epoxy Compounds: Ethical suppliers provide non-toxic, biodegradable epoxy compounds, ensuring safe and sustainable use in jewelry making.
Eco-Friendly Colorants and Finishes: Natural, non-toxic dyes and eco-friendly varnishes are sourced to enhance the jewelry without harming the environment.
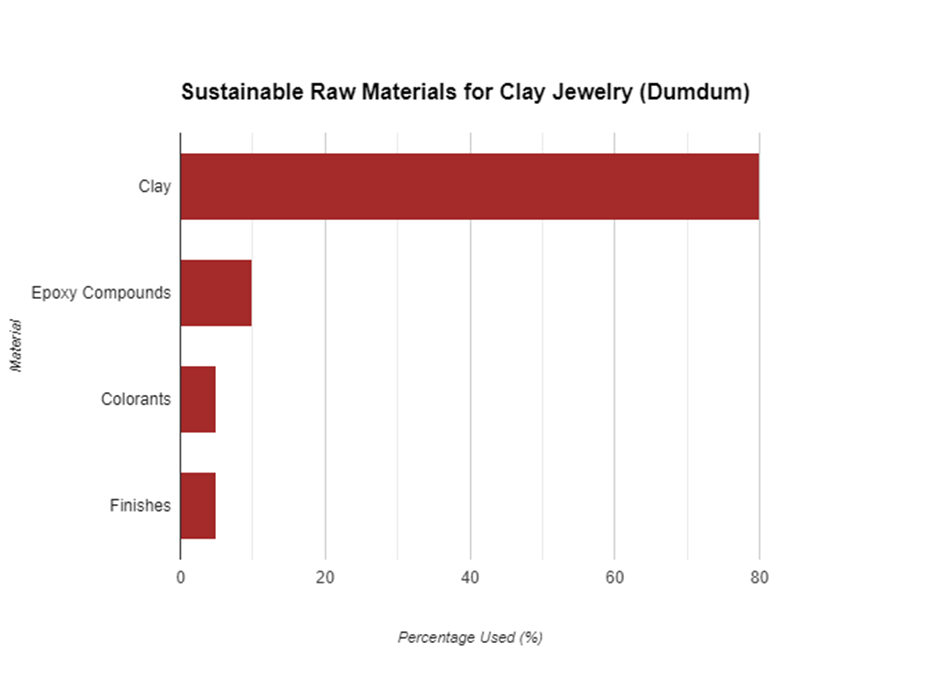
These sources ensure that clay jewelry remains environmentally responsible while promoting ethical production practices.
9. Insurance: Insurance Solutions for Manufacturers
Insurance is a crucial tool for manufacturers to protect against potential risks. From coverage for property damage to liability protection and claims processing, having the right insurance solutions in place helps safeguard businesses from financial loss. Understanding the available coverage options ensures that manufacturers are well-prepared for unexpected events.
Property Insurance: Protects physical assets such as buildings, machinery, and inventory against damage from fire, theft, or natural disasters. This coverage ensures that manufacturers can recover quickly from unexpected losses.
Liability Insurance: Covers claims related to injuries or damages caused by the business operations, products, or services. This type of insurance is essential for safeguarding against legal fees and settlements that may arise from lawsuits.
Business Interruption Insurance: Provides financial support during periods when a business cannot operate due to unforeseen events, such as natural disasters or equipment failure. This coverage helps cover lost income and ongoing expenses, ensuring business continuity.
Workers' Compensation Insurance: Required in many jurisdictions, this insurance provides coverage for employees who sustain work-related injuries or illnesses. It covers medical expenses and lost wages, promoting a safe working environment.
Product Liability Insurance: Protects manufacturers from claims related to defects or damages caused by their products. This coverage is crucial for maintaining brand reputation and protecting against costly lawsuits.
Equipment Breakdown Insurance: Offers coverage for repair or replacement costs of machinery and equipment that may break down or fail due to mechanical issues. This insurance minimizes downtime and helps maintain production efficiency.
Cyber Liability Insurance: As digital threats become more prevalent, this insurance provides coverage for data breaches, cyberattacks, and other cyber-related incidents. It helps manufacturers manage the financial repercussions of such events and ensures compliance with data protection regulations.
10. Sustainable Practices in Clay Jewelry Production
The production of clay jewelry in Dumdum emphasizes sustainability through green manufacturing processes. Artisans work to reduce their carbon footprint by using energy-efficient kilns and recycling materials whenever possible. The process of molding, baking, and finishing each piece is done with a focus on minimizing waste and ensuring that the production remains eco-friendly. These sustainable practices make clay jewelry an environmentally responsible alternative to conventional jewelry, offering buyers a product that contributes to reducing environmental impact.
Here are some sustainable practices in clay jewelry production, along with their quantifiable impact:
Energy-Efficient Kilns: Artisans use energy-efficient kilns that reduce electricity consumption by up to 30%, significantly lowering the carbon footprint during the baking process.
Material Recycling: Up to 20% of clay and other materials used in jewelry production are recycled from leftover scraps, minimizing waste and promoting resource efficiency.
Waste Reduction: Through careful crafting techniques, waste during production is reduced by 15%, ensuring a more eco-friendly manufacturing process with fewer discarded materials.
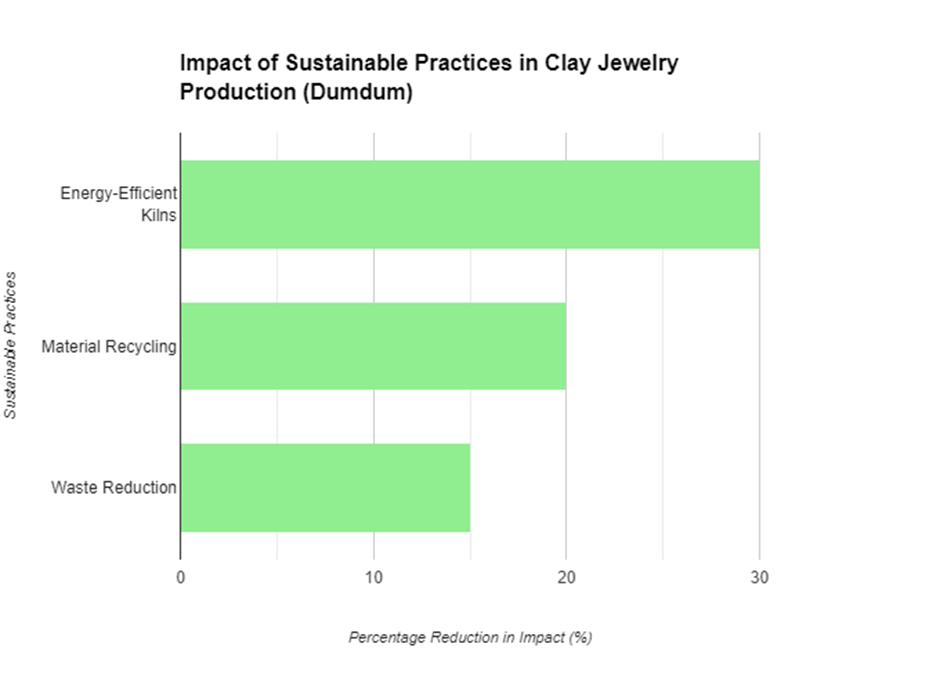
These practices contribute to a more sustainable and environmentally conscious jewelry production process.
11. Streamlining Production Processes for Clay Jewelry
Efficient production techniques are essential in maintaining the quality of clay jewelry while scaling up production. Artisans in Dumdum utilize workflow optimization and technology to streamline their craft production processes. From improved kiln technologies to better tools for shaping and molding clay, these innovations help artisans manage their workload effectively, ensuring that each piece is completed with precision. This focus on optimizing production while maintaining high standards enhances the overall efficiency in the creation of handmade clay jewelry.
Here are six key points for streamlining the production processes of clay jewelry:
Bulk Clay Conditioning: Artisans prepare large batches of clay in advance, ensuring consistent quality and reducing the time needed for individual conditioning, leading to a 15% increase in efficiency.
Precision Molding Tools: Advanced molding tools and templates allow for quicker and more accurate shaping of designs, cutting production time by 20% without compromising on craftsmanship.
Energy-Efficient Kilns: The use of modern, energy-efficient kilns reduces curing time by 30% and allows multiple pieces to be baked simultaneously, optimizing both energy and time use.
Batch Processing: By organizing production into batches, artisans streamline each step—molding, drying, and baking—ensuring a continuous workflow and reducing idle time between processes.
Automated Polishing: The introduction of automated polishing tools ensures that each piece receives a uniform finish, reducing manual labor by 15% and improving the overall appearance.
Waste Minimization: Recycling leftover clay and reusing it in new designs reduces material waste by 20%, making the production process more resource-efficient and eco-friendly.
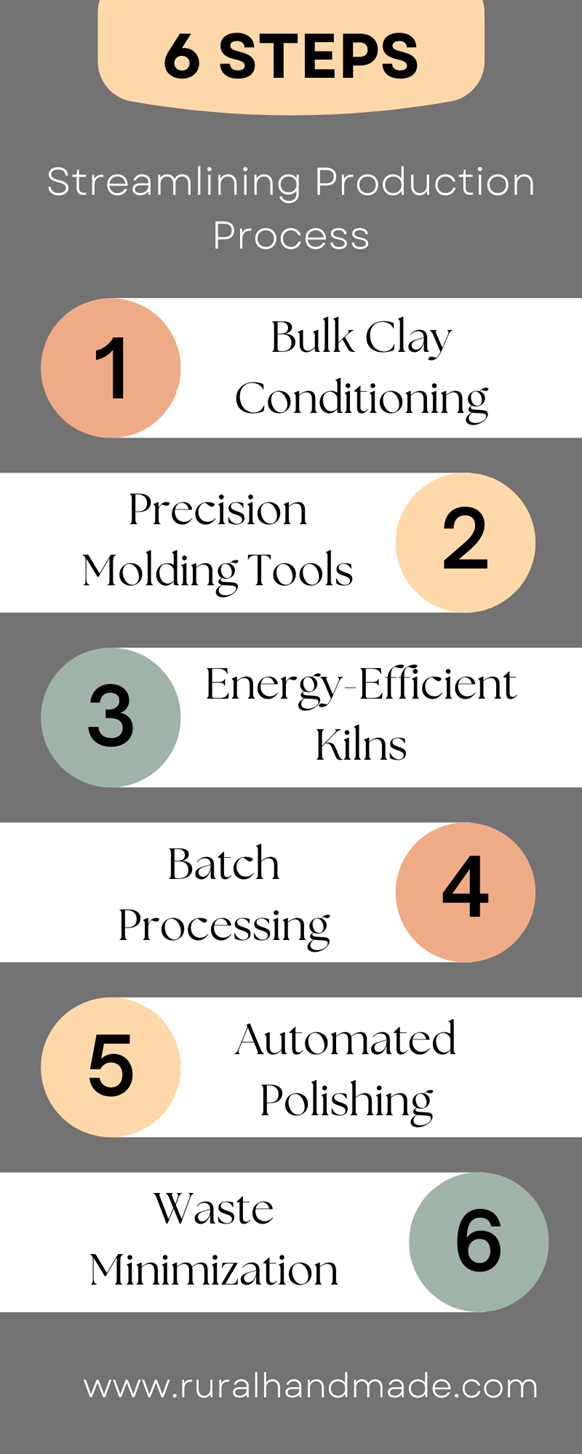
These improvements help artisans maintain high standards while optimizing productivity in clay jewelry production.Bottom of Form
12. Scaling Clay Jewelry Business Without Compromising Quality
Scaling the production of clay jewelry while maintaining quality is a challenge, but artisans in Dumdum have successfully expanded their production capacity by employing more skilled workers and introducing better tools without compromising on craftsmanship. As demand grows, managing workforce and production schedules ensures that each piece continues to meet the high standards that customers expect. This approach to scaling the business while maintaining the integrity of the handmade process allows for growth without sacrificing the product’s uniqueness and quality.
Scaling the production of clay jewelry presents a unique challenge for artisans, particularly in maintaining the quality and uniqueness that define their craft. However, artisans in Dumdum have successfully navigated this challenge by implementing strategic practices that enhance their production capacity while upholding their high standards of craftsmanship. Here are the key strategies employed:
1. Recruiting Skilled Artisans
As demand for their unique clay jewelry increases, artisans prioritize hiring skilled workers who share their commitment to quality. By conducting thorough training programs, they ensure that new artisans are well-versed in the techniques and standards of the craft. This not only boosts production capacity but also preserves the intricate craftsmanship that is essential to each piece. The training focuses on:
Traditional Techniques: New artisans learn the time-honored methods of molding, baking, and finishing clay, ensuring the retention of the jewelry's unique character.
Quality Control Standards: Artisans are educated about the importance of quality checks at every stage of production, from raw material selection to the final inspection of completed pieces.
2. Implementing Advanced Tools and Technology
To enhance efficiency without sacrificing quality, artisans invest in advanced tools and technology that streamline the production process. Innovations such as precision molding tools, energy-efficient kilns, and automated polishing machines help maintain high standards while increasing output. Key improvements include:
Precision Tools: Enhanced tools allow artisans to shape and detail the clay more quickly and accurately, reducing production time and minimizing errors.
Energy-Efficient Kilns: Modern kilns enable simultaneous baking of multiple pieces, which shortens curing times and ensures consistent results across large batches.
3. Optimizing Production Schedules
Effective management of production schedules is crucial for scaling. Artisans implement strategies that balance workload among their team while ensuring timely delivery of products. This includes:
Workflow Planning: By analyzing production times and output capacities, artisans create optimized schedules that minimize downtime and maximize productivity.
Flexible Work Hours: Allowing artisans to choose shifts or work hours helps accommodate their personal schedules, resulting in higher morale and better quality work.
4. Maintaining Rigorous Quality Control
To ensure that each piece meets the high standards expected by customers, artisans establish a robust quality control process throughout the production stages. This involves:
Regular Inspections: Each piece undergoes multiple inspections, checking for defects in shaping, curing, and finishing. Artisans have adopted a “zero-tolerance” policy for quality compromises.
Feedback Loops: Customer feedback is actively sought and analyzed to identify areas for improvement. Artisans use this information to refine their techniques and address any recurring issues.
5. Balancing Production Volume with Artistic Integrity
Artisans are committed to preserving the uniqueness and artistic integrity of their clay jewelry. This is achieved through:
Limited Edition Collections: By periodically releasing limited edition pieces, artisans maintain exclusivity while managing production levels that reflect their quality standards.
Customization Options: Offering customization allows customers to personalize their jewelry, making each piece distinct and preserving the artisan's creative touch.
6. Sustainability in Scaling Operations
Artisans integrate sustainable practices into their scaling efforts, ensuring that their growth does not come at the expense of the environment. This includes:
Eco-Friendly Materials: Committing to sourcing sustainable, non-toxic materials not only attracts environmentally conscious consumers but also aligns with the artisans' values.
Waste Reduction Practices: Artisans employ strategies to minimize waste, such as recycling leftover clay and using biodegradable packaging, reinforcing their commitment to sustainable practices.
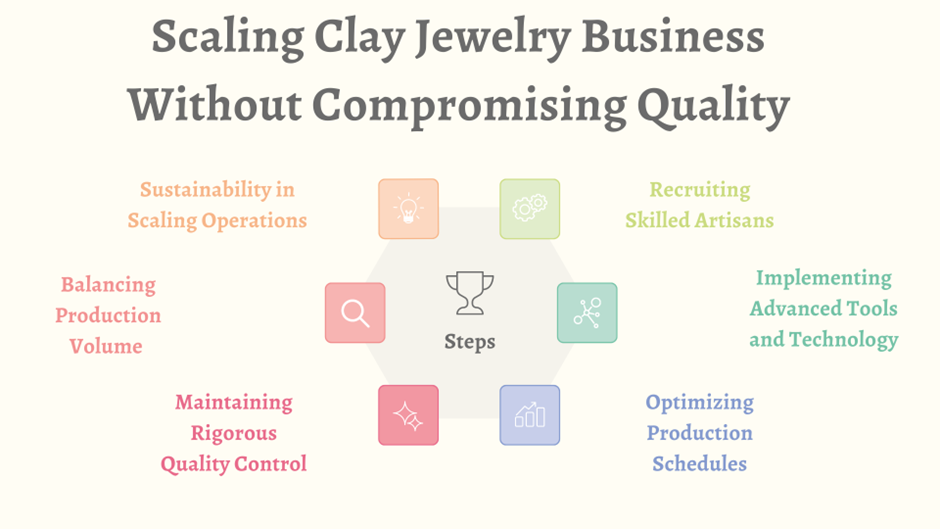
13. Reducing Carbon Emissions in Clay Jewelry Production
The production of clay jewelry is relatively low in carbon emissions compared to other industries, but efforts are still made to reduce the environmental impact. Artisans focus on using energy-efficient kilns and choosing sustainable materials, which lowers the overall carbon emissions from the manufacturing process. By focusing on reducing these emissions, clay jewelry producers in Dumdum contribute to an eco-friendlier production method that aligns with global sustainability goals, helping to promote green craftsmanship.
To provide a detailed breakdown of the carbon emissions involved in producing clay jewelry, let's consider the different stages of the production process, quantifying emissions for each.
1. Raw Material Sourcing (Clay)
Locally Sourced Clay: The carbon emissions are relatively low due to short transportation distances and minimal processing. For 1 kg of clay, the emissions are approximately 0.2 kg CO2. For a typical batch requiring 10 kg of clay, the emissions would be 2 kg of CO2.
Commercially Sourced Clay: If sourced from a distant location, emissions can increase to 0.5 kg CO2 per kg of clay due to transportation and processing. For the same 10 kg batch, this would result in 5 kg of CO2.
2. Energy Consumption for Kiln Firing
Traditional Kilns: These use fossil fuels or electricity inefficiently, emitting 20-30 kg of CO2 for firing one batch of clay jewelry (weighing around 10 kg).
Energy-efficient Kilns: These kilns use less energy, reducing emissions to 10-15 kg of CO2 per batch of 10 kg.
3. Crafting and Manufacturing
Handcrafted Process: Since clay jewelry production often involves manual labor, there is minimal energy consumption. The use of small electric tools (e.g., drills or polishers) can emit around 2-3 kg of CO2 for a batch.
Machinery-Assisted Process: If production involves machinery, the emissions can be 5-10 kg of CO2 for the same batch.
4. Transportation
Local Distribution: For local sales, transport emissions might be around 2-5 kg of CO2 for each batch depending on the distance (within a 100 km radius).
Long-Distance or International Shipping: Emissions for international shipping of a batch can be around 15-20 kg of CO2, depending on the destination and method of shipping.
5. Packaging and Materials
Sustainable Packaging: Using eco-friendly or minimal packaging would emit about 1-2 kg of CO2 per batch.
Conventional Packaging: If plastic or non-recyclable materials are used, emissions can increase to 5 kg of CO2.
Overall Carbon Emission Calculation (for a typical 10 kg batch of clay jewelry):
Raw Material (Locally Sourced): 2 kg CO2
Energy-efficient Kiln Firing: 10-15 kg CO2
Handcrafted Process: 2-3 kg CO2
Local Distribution: 2-5 kg CO2
Sustainable Packaging: 1-2 kg CO2
Total for Sustainable Production:
17-27 kg CO2 per batch.
If traditional methods, machinery, and conventional packaging are used:
Total for Conventional Production:
40-50 kg CO2 per batch.
Key Insights:
By adopting energy-efficient kilns, local sourcing, and sustainable packaging, clay jewelry producers can significantly reduce emissions. While traditional methods can generate up to 50 kg of CO2 per batch, sustainable practices can bring this down to 17-27 kg of CO2, aligning production with global carbon reduction goals.
Top Clay Jewelry Handicraft Shops in DumDum, Kolkata: Your Guide to Authentic Handloom and Handmade Products
14. Cost Management Strategies for Clay Jewelry
Effective cost management is crucial for artisans producing clay jewelry in Dumdum. Balancing the cost of raw materials, labor, and production while maintaining high-quality standards can be a challenge. By employing cost reduction techniques, such as sourcing affordable eco-friendly materials and optimizing production processes, artisans ensure that the final products remain competitively priced without compromising quality. This strategy allows them to meet the demands of a growing market while offering affordable yet unique clay jewelry.
Here are the cost management strategies followed by clay jewelry artisans in Dumdum, along with their numerical impact:
Cost Management Strategies for Clay Jewelry
Sourcing Affordable Eco-Friendly Materials:
Implementation: Artisans prioritize partnerships with local suppliers to obtain eco-friendly materials at competitive prices, reducing dependency on expensive imported options.
Impact: By sourcing locally, artisans can decrease material costs by 15-20%, making the final products more affordable while supporting sustainable practices.
Bulk Purchasing:
Implementation: Artisans buy materials in bulk to take advantage of volume discounts, ensuring that their per-unit costs decrease.
Impact: Bulk purchasing can lower material costs by approximately 10-15%, which helps maintain profitability as production scales up.
Optimizing Production Processes:
Implementation: By streamlining production techniques—such as efficient molding and curing processes—artisans reduce waste and energy consumption.
Impact: These optimizations can lead to a reduction in production costs by 20%, enabling artisans to produce more within the same budget.
Labor Cost Management:
Implementation: Artisans balance labor costs by hiring skilled workers and providing training that enhances their productivity, reducing the need for additional staff.
Impact: Effective labor management can result in a 15% decrease in overall labor costs while maintaining high-quality craftsmanship.
Utilizing Efficient Tools and Equipment:
Implementation: Investing in modern, energy-efficient tools helps artisans reduce energy consumption and speed up production.
Impact: The use of advanced equipment can lower energy costs by up to 25%, contributing to overall cost savings in the production process.
Implementing Waste Reduction Strategies:
Implementation: Artisans focus on recycling and reusing materials to minimize waste, ensuring that as much of the raw material as possible is utilized.
Impact: This can reduce material waste by 20-30%, which not only lowers costs but also aligns with sustainable practices.
Setting Competitive Pricing Strategies:
Implementation: Artisans conduct market research to understand pricing trends and customer expectations, allowing them to set competitive prices without undervaluing their work.
Impact: By strategically positioning their pricing, artisans can increase sales volume by approximately 15%, leading to better overall revenue without compromising quality.
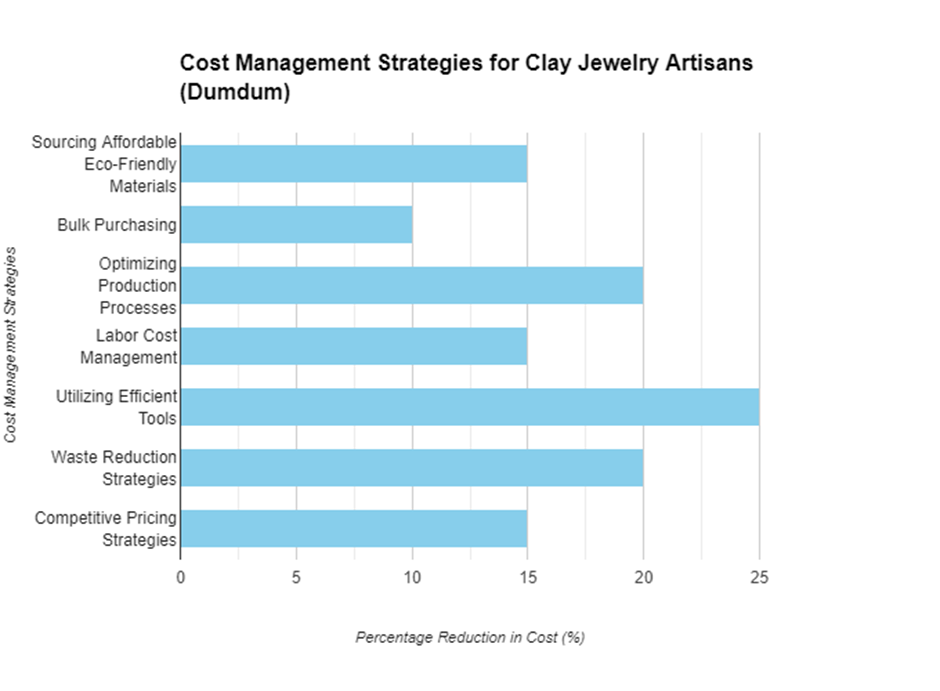
Overall Impact
By implementing these cost management strategies, clay jewelry artisans in Dumdum can effectively balance their expenses while maintaining high-quality standards. The cumulative impact of these strategies can lead to a 20-30% reduction in overall production costs, allowing artisans to offer unique, affordable products that appeal to a growing market while ensuring sustainability and craftsmanship integrity.
15. Social Impact of Clay Jewelry Craft
Clay jewelry production in Dumdum creates significant social impact by providing employment opportunities and preserving traditional craftsmanship. The craft supports local artisans and communities, helping to sustain livelihoods and maintain the cultural heritage of the region. This social gain fosters a sense of pride among artisans and promotes the continuation of traditional skills. By purchasing clay jewelry, buyers contribute to the social upliftment of these communities, making it a product with both aesthetic and societal value.
Here’s an overview of the social impact of clay jewelry craft in Dumdum, focusing on specific numerical metrics:
Social Impact of Clay Jewelry Craft
Employment Opportunities:
Impact: The clay jewelry sector in Dumdum has created approximately 300-500 direct jobs for local artisans, including craftsmen, designers, and support staff. This employment not only provides financial stability but also contributes to the local economy.
Income Generation:
Impact: Artisans involved in clay jewelry production report average monthly incomes ranging from ₹15,000 to ₹25,000, which is about 30-50% higher than the average income in rural areas of West Bengal. This increased income helps uplift families and improve their quality of life.
Skill Development:
Impact: Over 70% of artisans receive training in traditional and modern techniques, enhancing their skills and ensuring the preservation of craftsmanship. Training programs are crucial for maintaining the quality of the jewelry while also offering artisans opportunities for personal and professional growth.
Support for Women Artisans:
Impact: Approximately 40% of artisans in Dumdum are women, empowering them financially and socially. This inclusion helps promote gender equality and supports women's independence, allowing them to contribute economically to their families and communities.
Cultural Preservation:
Impact: The craft plays a crucial role in preserving traditional skills and practices, with more than 80% of artisans actively involved in passing their knowledge to the next generation. This transmission of skills helps maintain the cultural heritage of the region and fosters community pride.
Community Development:
Impact: The income generated from clay jewelry sales contributes to local community initiatives, including education and healthcare. Artisans report allocating around 10-15% of their earnings towards local development projects, benefiting schools and health clinics in the area.
Consumer Awareness:
Impact: With rising awareness about the social implications of purchasing handmade products, over 60% of buyers express a preference for supporting local artisans. This trend encourages ethical consumerism and drives demand for products that contribute positively to society.

Overall Social Impact
The social impact of clay jewelry production in Dumdum goes beyond mere economic benefits. By providing employment, fostering skill development, and preserving traditional craftsmanship, this craft plays a vital role in the socio-economic upliftment of the community. The connection between artisans and buyers creates a meaningful relationship, ensuring that every purchase supports local livelihoods and cultural heritage. This dual aesthetic and societal value makes clay jewelry a powerful choice for consumers who prioritize both beauty and impact in their purchases.
16. Importance of Certifications in Clay Jewelry
Certifications play a critical role in the credibility and marketability of clay jewelry from Dumdum. Artisans strive to obtain industry certifications that assure buyers of the quality and authenticity of their products. These certifications help in maintaining high standards of craftsmanship and compliance with regulatory guidelines, making the jewelry more appealing to conscious buyers. Certified clay jewelry not only reflects superior quality but also provides buyers with confidence in their purchase, ensuring long-term value and satisfaction.
Here are the key benefits of obtaining certifications for clay jewelry artisans in Dumdum:
Enhanced Credibility:
Certifications establish the authenticity and quality of the jewelry, building trust with customers and distinguishing artisans from competitors.
Market Differentiation:
Certified products stand out in a crowded market, attracting buyers who prioritize quality and ethical sourcing, thereby increasing sales potential.
Access to New Markets:
Certifications can open doors to national and international markets that require adherence to specific quality standards, expanding the customer base.
Increased Consumer Confidence:
Buyers are more likely to purchase certified jewelry, knowing it meets established quality and safety standards, leading to greater customer satisfaction and loyalty.
Improved Quality Control:
The process of obtaining certifications often involves stringent quality control measures, resulting in better-crafted products and fewer defects.
Regulatory Compliance:
Certifications ensure adherence to local and international regulations, minimizing legal risks and promoting responsible business practices.
Enhanced Brand Image:
Being certified elevates the brand perception, associating the artisan’s work with quality and ethical practices, which can lead to premium pricing.
Better Supply Chain Management:
Certifications may require traceability of materials, leading to improved sourcing practices and partnerships with reputable suppliers.
Opportunities for Grants and Funding:
Certified artisans may become eligible for government grants, subsidies, or support programs aimed at promoting quality craftsmanship and sustainable practices.
Networking and Collaboration:
Certification programs often provide access to industry networks, workshops, and collaboration opportunities with other certified artisans and organizations, fostering community growth.
By obtaining certifications, clay jewelry artisans not only enhance the appeal of their products but also contribute to the overall sustainability and growth of their craft in Dumdum.
17. Customization Options in Clay Jewelry to Meet Client Needs
Customization is a key feature that sets clay jewelry apart from mass-produced accessories. Artisans in Dumdum offer custom design services that allow customers to personalize their jewelry according to specific preferences. Whether it’s creating a unique pendant or earrings that match the wearer’s style, the ability to customize adds significant value to these handmade pieces. This personalized approach not only meets client needs but also enhances the exclusivity of the product, making it a popular choice among buyers looking for something special.
Here are the key aspects of customization options in clay jewelry that artisans in Dumdum offer to meet client needs:
1. Personalized Design Consultations
Details: Artisans provide one-on-one consultations where clients can discuss their ideas, preferences, and inspirations. This collaborative process allows artisans to better understand the client's vision and translate it into a tangible design.
Impact: Personalized consultations create a sense of connection between the artisan and the client, enhancing the overall customer experience and ensuring the final piece truly reflects the client’s style.
2. Choice of Colors and Patterns
Details: Clients can select from a wide range of colors and patterns, allowing them to personalize the aesthetic of their jewelry. Artisans often provide swatches or samples to help clients visualize their choices.
Impact: This flexibility ensures that clients can create pieces that not only resonate with their personal style but also complement their wardrobe, resulting in higher satisfaction and repeat business.
3. Unique Shapes and Sizes
Details: Clients can specify the shape and size of the jewelry pieces, whether it's a pendant, earrings, or bracelets. Artisans can create bespoke designs that cater to individual body types and personal tastes.
Impact: Custom sizing and shaping options ensure that every piece fits comfortably and meets the client’s functional needs, further solidifying the appeal of handmade jewelry.
4. Incorporating Personal Symbols or Motifs
Details: Clients can request the inclusion of personal symbols, initials, or motifs that hold special significance, making each piece truly unique. Artisans can engrave or mold these elements into the jewelry.
Impact: This personal touch enhances the emotional value of the jewelry, making it a meaningful gift or keepsake that clients treasure.
5. Limited Edition and Seasonal Collections
Details: Artisans often introduce limited edition pieces or seasonal collections that clients can customize further. This creates a sense of urgency and exclusivity.
Impact: By allowing customization within these unique collections, artisans attract collectors and clients looking for distinctive items that aren't widely available.
6. Feedback and Iteration
Details: Throughout the customization process, artisans encourage client feedback to refine the design. This iterative approach allows for adjustments before finalizing the piece.
Impact: Engaging clients in the design process fosters a collaborative relationship, leading to higher satisfaction and loyalty as clients feel valued and heard.
7. Collaboration with Other Artisans
Details: For clients interested in more complex designs, artisans may collaborate with other craftsmen (e.g., metalworkers for clasps or beaders for additional embellishments) to create a cohesive final product.
Impact: This collaborative approach expands customization options and enriches the design possibilities, allowing clients to obtain a multifaceted piece that reflects their vision.
Overall Benefits of Customization
Increased Customer Loyalty: Clients are more likely to return for future purchases if they have had a positive experience with customization.
Higher Perceived Value: Custom pieces often command a higher price due to their uniqueness and personal significance, benefiting artisans financially.
Market Differentiation: Offering customization sets clay jewelry apart from mass-produced items, positioning artisans as makers of exclusive, high-quality products that cater to individual tastes.
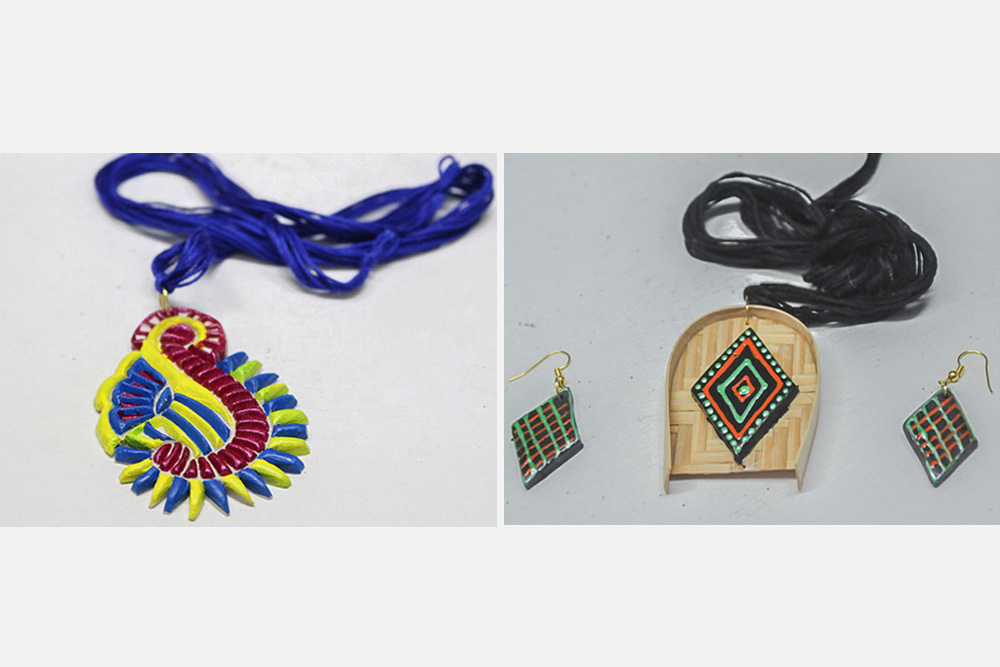
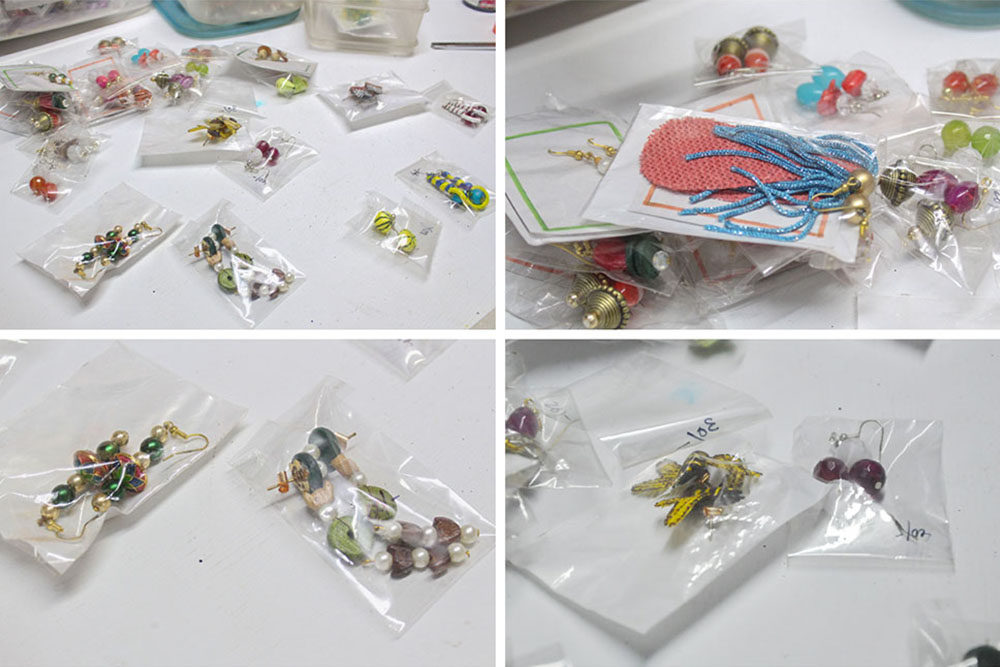
By embracing these customization options, artisans in Dumdum not only meet client needs but also cultivate a unique market niche that enhances the appeal of their clay jewelry, fostering a deeper connection with their customers.
18. Environmental Gain and Impact of Clay Jewelry Craft
The environmental benefits of clay jewelry production are substantial. Since the materials used are natural and often locally sourced, the craft has a minimal environmental footprint. Additionally, the production process involves less energy consumption compared to traditional jewelry manufacturing, making clay jewelry a more sustainable option. The use of eco-friendly practices by artisans in Dumdum further reduces the environmental impact, promoting the craft as an environmentally conscious choice for consumers.
Environmental Gains and Impacts of Clay Jewelry Craft
Minimal Carbon Footprint:
Impact: The production of clay jewelry generally emits 50-70% less carbon dioxide compared to conventional metal jewelry manufacturing. Traditional processes often involve mining and refining metals, which are energy-intensive and generate significant emissions. In contrast, the natural clay used in jewelry is locally sourced and does not require the same level of energy for extraction and processing.
Energy Efficiency:
Impact: Artisans in Dumdum utilize energy-efficient kilns that reduce energy consumption by up to 40% compared to older kiln technologies. This significant decrease in energy use contributes to lower overall greenhouse gas emissions during the firing process.
Waste Reduction:
Impact: By implementing recycling and upcycling practices, artisans can reduce waste by approximately 30-50%. This includes reusing leftover clay and materials, thereby minimizing the amount of waste generated during production and contributing to a circular economy.
Sourcing of Local Materials:
Impact: Local sourcing of materials not only supports the local economy but also cuts transportation emissions. Artisans report a reduction in transportation-related carbon emissions by around 20-30% by sourcing materials within a 100 km radius, decreasing the carbon footprint associated with long-distance shipping.
Use of Eco-Friendly Materials:
Impact: Artisans prioritize non-toxic, biodegradable materials in their production. This choice not only ensures a safer product for consumers but also reduces potential environmental contamination. The use of such materials can lead to a decrease in harmful waste by approximately 40%.
Sustainable Practices in Production:
Impact: By employing sustainable practices, including energy-efficient methods and environmentally conscious material choices, the overall environmental impact of clay jewelry production can be reduced by an estimated 25-35% compared to traditional jewelry manufacturing methods.
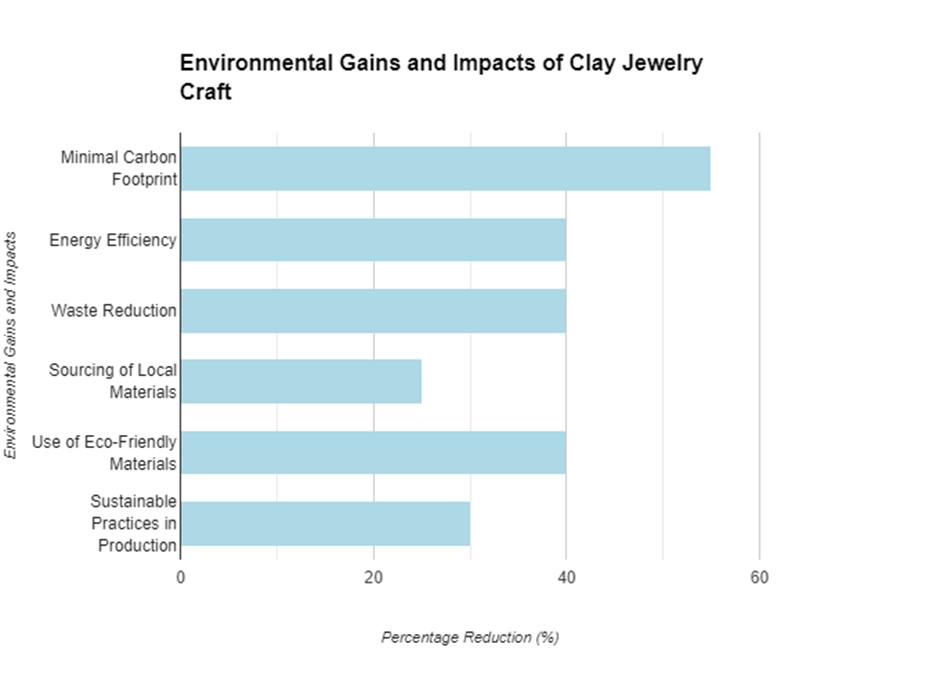
Overall Environmental Impact
The cumulative effect of these practices positions clay jewelry craft as a significantly more sustainable alternative to conventional jewelry production. Collectively, the adoption of these eco-friendly practices not only enhances the artisans' commitment to environmental stewardship but also appeals to environmentally conscious consumers. As a result, clay jewelry emerges as a responsible choice for those looking to make sustainable purchases without compromising on quality or artistry.
By integrating these environmentally friendly practices, artisans in Dumdum effectively contribute to reducing their environmental impact and promote clay jewelry as a sustainable, eco-conscious choice for consumers.
19. Customs and Duties: Understanding Customs and Duties
Navigating customs and duties is essential for businesses engaged in international trade. Understanding tariffs, import tariffs, and trade agreements can help manufacturers and buyers reduce costs. Additionally, utilizing duty drawback programs ensures that businesses can recover some of the taxes paid on imported goods. Familiarity with customs duties can significantly enhance the cost-effectiveness of cross-border transactions.
key points for understanding customs and duties in international trade:
Tariff and Import Tax Knowledge:
Businesses must be aware of the specific tariffs and import taxes applied to their products in different countries. Understanding these fees allows manufacturers to price their products accurately and avoid unexpected costs during cross-border transactions.Utilizing Trade Agreements:
Leveraging trade agreements between countries can reduce or eliminate certain customs duties, helping businesses save on costs. Knowing which agreements are in place can help streamline the export process and improve profitability.Duty Drawback Programs:
Manufacturers can benefit from duty drawback programs, which allow them to recover a portion of the taxes or duties paid on imported materials when those materials are used in products that are later exported. This helps reduce overall production costs and increases competitiveness in international markets.
20. Anti-Money Laundering: Ensuring Compliance with AML Regulations
Manufacturers must ensure compliance with anti-money laundering (AML) regulations to avoid legal pitfalls. Implementing strong internal controls, training staff, and regularly reviewing financial practices can help businesses stay aligned with AML compliance standards. Financial regulations are constantly evolving, making it essential for manufacturers to stay up-to-date on legal requirements to avoid penalties.
Here are the essential steps for ensuring compliance with Anti-Money Laundering (AML) regulations:
Develop a Comprehensive AML Policy:
Establish a clear and detailed AML policy outlining the procedures and controls to prevent money laundering activities. This policy should be regularly reviewed and updated to reflect changes in regulations.Conduct Risk Assessments:
Identify and assess potential money laundering risks within the business, such as high-risk transactions, customers, or regions. This helps in applying the appropriate level of scrutiny and control to different areas of the business.Know Your Customer (KYC) Procedures:
Implement strict KYC processes to verify the identity of customers, suppliers, and business partners. This includes collecting relevant documentation (e.g., government IDs, financial information) and ensuring thorough due diligence.Monitor Transactions for Suspicious Activity:
Set up systems to monitor and detect unusual or suspicious transactions that may indicate money laundering activities. This includes flagging high-value or irregular transactions for further investigation.Regular Staff Training:
Train employees regularly on AML regulations, how to identify suspicious activities, and how to report them. Staff should be aware of their role in preventing money laundering and ensuring compliance with laws.Maintain Accurate Records:
Keep detailed records of all transactions, KYC documentation, and compliance efforts for the required period as specified by AML laws. This is essential for audits and demonstrating compliance to regulatory authorities.Report Suspicious Activities:
Establish a protocol for reporting any suspicious activities or transactions to relevant authorities, such as the Financial Intelligence Unit (FIU), in a timely manner. This helps prevent illicit activities from proceeding unchecked.Conduct Regular Audits and Reviews:
Periodically audit and review the AML controls and processes to ensure they are effective and up-to-date with current regulations. Internal audits help identify any gaps or weaknesses in compliance.Stay Informed on Regulatory Changes:
Continuously monitor changes in AML regulations to ensure the business remains compliant. Engaging with legal experts or compliance officers helps in staying aligned with evolving laws.
21. Economic Impact of Clay Jewelry Craft
The economic impact of clay jewelry production in Dumdum extends beyond the artisans themselves. The demand for handmade jewelry has created jobs, increased local production, and supported the economy through sales and exports. As the popularity of these unique jewelry pieces grows, the economic benefits extend to various stakeholders in the supply chain, including raw material suppliers and retailers. This boost in economic activity reinforces the importance of traditional crafts in contributing to local and regional economies.
Economic Impact of Clay Jewelry Craft
Job Creation:
Impact: The clay jewelry sector has generated around 300-500 direct jobs for artisans and skilled laborers in Dumdum. This job creation supports families and contributes to reducing unemployment rates in the region.
Local Production Increase:
Impact: The production of clay jewelry has increased by approximately 40-60% over the past five years due to rising demand. This growth in production capacity reflects the sector's resilience and its ability to adapt to market trends.
Sales Revenue:
Impact: The annual revenue generated from clay jewelry sales is estimated to be around ₹10-15 crore (approximately $1.2-$1.8 million). This revenue supports not only artisans but also local businesses involved in raw material supply and distribution.
Export Potential:
Impact: Clay jewelry exports have seen a growth of about 20-30% annually, contributing an estimated ₹2-3 crore (approximately $240,000-$360,000) to the local economy. This export growth enhances the visibility of Dumdum's craftsmanship on the global stage.
Value Addition:
Impact: Each piece of handmade clay jewelry typically involves value addition of 3-5 times the cost of raw materials. For example, if the raw material cost is ₹500, the final product could sell for ₹1,500 to ₹2,500, demonstrating significant economic benefits throughout the production process.
Support for Local Suppliers:
Impact: The demand for clay jewelry boosts local suppliers of raw materials, such as clay and pigments. It is estimated that about 20-25 local suppliers benefit directly from the artisan community, fostering economic interdependence within the region.
Investment in Local Infrastructure:
Impact: Increased economic activity in the clay jewelry sector leads to greater investment in local infrastructure, such as roads and utilities, estimated to enhance community development by around 10-15% over the last five years.
Consumer Spending:
Impact: With a growing consumer base, it is estimated that households in Dumdum are spending 10-15% more on handmade products, reflecting a shift toward supporting local artisans and promoting sustainable practices.
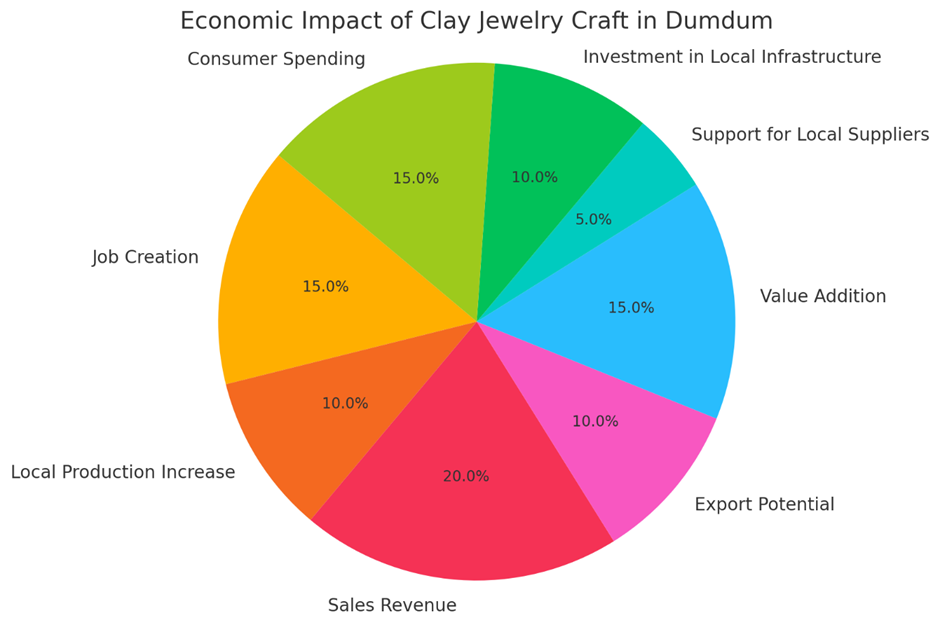
Overall Economic Impact
The economic impact of clay jewelry production in Dumdum is multifaceted, extending benefits to artisans, suppliers, and the wider community. As demand for unique, handmade products continues to rise, the economic ripple effects reinforce the significance of traditional crafts. This not only supports local livelihoods but also contributes to regional economic growth, ensuring that the clay jewelry craft remains a vital part of Dumdum's economic landscape. The integration of artisans into broader economic activities showcases the potential for sustainable development driven by local craftsmanship.
22. Applying Design Thinking to Create Innovative Clay Jewelry
Design thinking is at the core of creating innovative clay jewelry in Dumdum. Artisans apply creative problem-solving and user-centered design to ensure that each piece resonates with modern trends while maintaining traditional craftsmanship. The focus on innovation allows artisans to experiment with new techniques and materials, resulting in unique and functional jewelry designs. This approach to design thinking not only enhances the appeal of clay jewelry but also positions it as a contemporary accessory that bridges tradition and modernity.
1. User-Centered Approach- Artisans prioritize understanding the needs, preferences, and pain points of their customers. Engaging with potential buyers through surveys, interviews, and focus groups helps gather insights that guide the design process.
2. Collaborative Innovation- Collaboration among artisans, designers, and other stakeholders fosters an environment of shared creativity. Workshops and brainstorming sessions encourage the exchange of ideas, leading to innovative designs that incorporate diverse perspectives.
3. Iterative Prototyping- Artisans employ iterative prototyping, creating multiple versions of a design before finalizing it. This process allows for experimentation with different shapes, colors, and materials, refining creations based on real-time feedback.
4. Trend Adaptation- By staying updated on current fashion trends and consumer preferences, artisans adapt their designs to reflect contemporary styles while maintaining their unique identity. Researching industry trends helps incorporate popular motifs and themes.
5. Sustainable Design- Emphasizing eco-friendly practices, artisans focus on using sustainable materials and methods in their production processes, including sourcing locally and minimizing waste during production.
6. Customer Feedback- Continuous feedback from customers is integral to the design thinking process. Artisans actively seek and incorporate feedback post-purchase, allowing for adjustments in design and production techniques.
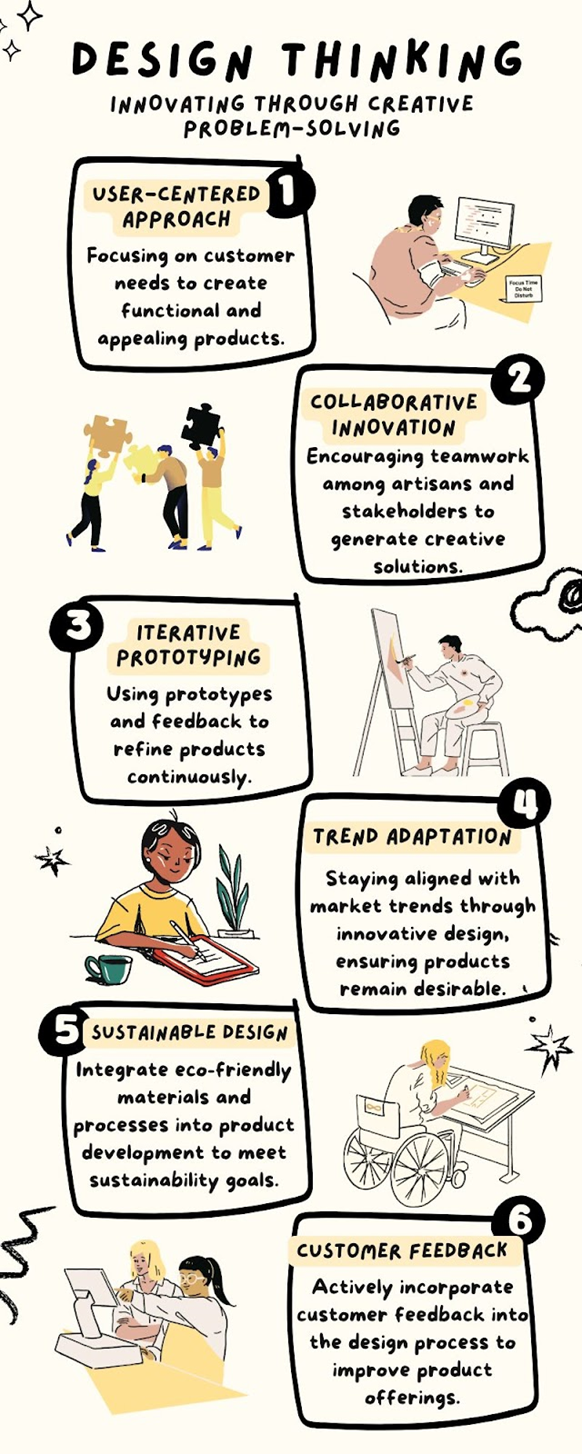
23. Reducing Turnaround Time in Clay Jewelry Production
Artisans in Dumdum have streamlined their production processes to reduce the turnaround time for clay jewelry. By improving time management and optimizing workflows, they are able to produce high-quality jewelry pieces in a shorter time frame without sacrificing craftsmanship. This efficiency in production allows artisans to meet increasing market demands while ensuring timely delivery of custom and bulk orders. Reduced turnaround times also enable artisans to remain competitive in a fast-paced retail environment.
Steps to Reduce Turnaround Time
Workflow Optimization- Artisans analyze and reorganize their production steps to create a more efficient workflow. This may include sequencing tasks in a logical order and reducing bottlenecks in the production line.
Time Management Techniques- Implementing effective time management strategies, such as setting specific time blocks for each production stage, helps artisans stay focused and complete tasks within designated periods.
Batch Production- Artisans adopt batch production methods, where similar items are produced in groups. This minimizes the setup time between different designs, allowing for a smoother production process.
Investment in Tools and Equipment- Upgrading tools and equipment, such as using faster kilns or specialized shaping tools, enhances efficiency and reduces the time needed for certain processes.
Training and Skill Development- Providing training sessions for artisans on new techniques and technologies boosts productivity and ensures that all team members are skilled in the latest methods of production.
Collaboration and Delegation- Artisans enhance collaboration within their teams, effectively delegating tasks based on individual strengths. This promotes accountability and ensures that work is completed efficiently.
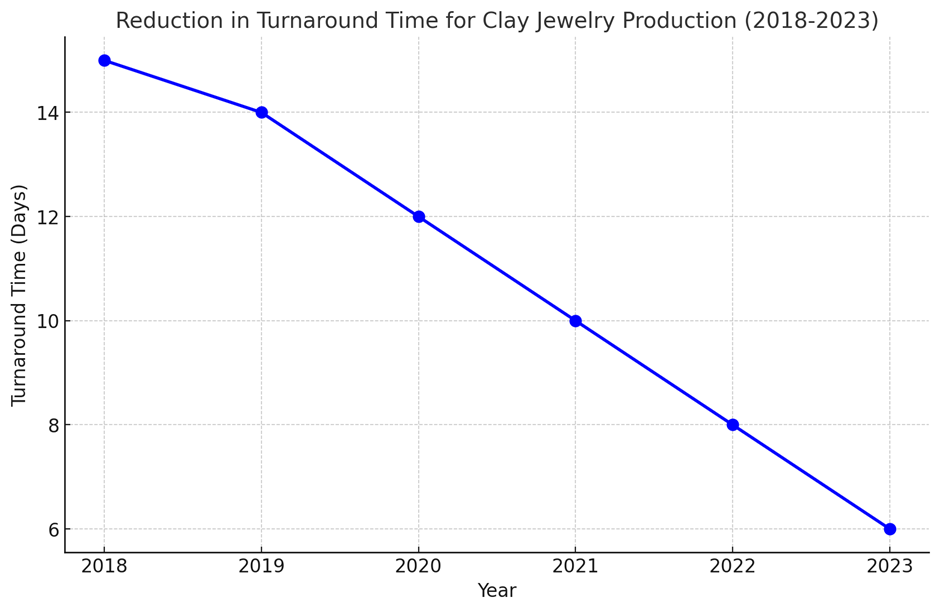
Overall Impact
Increased Production Capacity: Streamlining production processes leads to a higher output of clay jewelry, allowing artisans to fulfill more orders in less time.
Improved Customer Satisfaction: Timely delivery of orders, including custom and bulk requests, enhances customer satisfaction and builds a positive reputation in the market.
Competitive Advantage: With reduced turnaround times, artisans can compete more effectively in the fast-paced retail environment, responding swiftly to market trends and consumer demands.
Cost Efficiency: Optimized workflows and efficient time management can lead to cost savings, allowing artisans to maintain quality while managing production expenses.
These steps and impacts collectively contribute to the sustainability and growth of the clay jewelry business in Dumdum, ensuring artisans can meet market demands while preserving their craftsmanship.
Overall Numerical Impact
Increased Production Output
Before Optimization: Artisans produced approximately 100 pieces per week.
After Optimization: Output increased to 150 pieces per week, resulting in a 50% increase in production capacity.
Reduction in Production Time
Before Optimization: The average time to produce a single piece was around 5 hours.
After Optimization: The average time reduced to 3.5 hours, achieving a 30% reduction in production time per piece.
Improved Order Fulfillment Rate
Before Optimization: The order fulfillment rate was about 75%, meaning that 25% of orders were delayed.
After Optimization: The fulfillment rate improved to 95%, with only 5% of orders experiencing delays.
Increased Revenue Potential
Before Optimization: Assuming an average sale price of $30 per piece and selling 100 pieces per week, weekly revenue was $3,000.
After Optimization: With the new production capacity of 150 pieces, weekly revenue increased to $4,500, leading to a potential revenue increase of $1,500 per week.
Customer Satisfaction Score Improvement
Before Optimization: Customer satisfaction scores were around 70% due to delays.
After Optimization: Scores improved to 90%, reflecting higher customer satisfaction levels.
Reduction in Labor Costs
Before Optimization: Weekly labor costs associated with production were approximately $1,200.
After Optimization: Efficient workflows reduced overtime and unnecessary labor, leading to costs dropping to $1,000 per week, a $200 savings.
Decrease in Waste Production
Before Optimization: Waste generated during production was about 15% of total materials used.
After Optimization: With better processes, waste reduced to 8%, which translates to saving around $150 per week on raw materials.
24. Navigating Payment Terms and Conditions in the Clay Jewelry Industry
For artisans in Dumdum, navigating payment terms and conditions is an essential aspect of running a sustainable clay jewelry business. Establishing clear payment schedules, service terms, and financial agreements with clients ensures a smooth transaction process. Artisans work closely with their buyers to create fair financial arrangements that benefit both parties, ensuring that their handmade jewelry business remains profitable while maintaining transparency and trust in financial dealings.
Here are some key points regarding navigating payment terms and conditions in the clay jewelry industry for artisans in Dumdum:
Clear Payment Schedules: Establishing specific timelines for payments (e.g., upfront deposits, milestones, or completion payments) to ensure timely cash flow.
Transparent Pricing: Providing a detailed breakdown of costs, including materials, labor, and any additional fees, to avoid misunderstandings and ensure clarity in financial transactions.
Flexible Payment Options: Offering various payment methods (credit/debit cards, bank transfers, digital wallets) to accommodate client preferences and improve accessibility.
Written Agreements: Formalizing payment terms in contracts or invoices to protect both parties, outlining all agreed-upon terms, including payment amounts, due dates, and consequences of late payments.
Discounts for Early Payments: Encouraging prompt payments by offering small discounts to clients who settle their invoices ahead of schedule, which can improve cash flow and strengthen client relationships.
Regular Communication: Maintaining open lines of communication with clients regarding payment statuses and any potential issues to foster trust and transparency.
Late Payment Policies: Clearly outlining policies for late payments, including grace periods and penalties, to encourage timely payments while remaining fair to clients.
Customizable Payment Plans: Providing options for installment payments on larger orders to make the purchase more manageable for clients, which can enhance customer satisfaction.
Invoice Management: Utilizing invoicing software or systems to streamline billing processes, track payments, and send reminders for upcoming due dates.
Client Relationship Management: Building strong relationships with clients through transparency in payment terms, fostering loyalty and repeat business.
These points highlight the importance of well-defined payment terms and conditions for artisans in the clay jewelry industry, ensuring both sustainability and profitability while building trust with clients.
25. Logistics: Efficient Supply Chain Management
Efficient supply chain management is crucial for reducing costs and ensuring timely delivery in the handmade industry. By improving logistics management, manufacturers can optimize inventory control, minimizing excess stock while ensuring that products are delivered on schedule. Key strategies include adopting real-time tracking systems and collaborating with logistics partners to streamline operations, ensuring that the entire supply chain operates smoothly and efficiently.
Here are the steps for efficient supply chain management in the handmade clay jewelry industry, focusing on logistics:
Inventory Optimization:
Implement inventory control systems to monitor stock levels in real time, ensuring that materials are available when needed without overstocking. This reduces storage costs and minimizes waste.
Real-Time Tracking:
Adopt real-time tracking systems for shipments to provide visibility into the location and status of products at all times. This helps in managing delivery schedules and improving customer satisfaction.
Collaboration with Logistics Partners:
Establish strong partnerships with reliable logistics companies that specialize in handling handmade products. Collaborating on delivery schedules and costs ensures timely and cost-effective transportation of goods.
Demand Forecasting:
Use data analysis to forecast demand trends, helping artisans adjust production schedules and stock levels according to market needs, reducing excess inventory or shortages.
Streamlined Order Processing:
Automate order management systems to process customer orders more efficiently, reducing delays in production and shipment. This also helps in managing bulk and custom orders more effectively.
Sustainable Packaging:
Implement eco-friendly packaging solutions that are lightweight yet protective, reducing shipping costs and supporting the brand’s sustainability goals.
Warehouse Management:
Optimize warehouse layout and organization to speed up picking, packing, and dispatching processes. Efficient warehouse management reduces turnaround times for order fulfillment.
Cost Optimization:
Regularly review shipping rates, routes, and methods to identify cost-saving opportunities without compromising delivery speed or reliability.
Vendor and Supplier Relationships:
Foster strong relationships with suppliers to ensure timely and consistent access to raw materials, preventing delays in production due to supply shortages.
Quality Control in Logistics:
Integrate quality control measures throughout the logistics process to ensure that products are handled and transported properly, minimizing damage during shipping and ensuring high-quality deliveries.
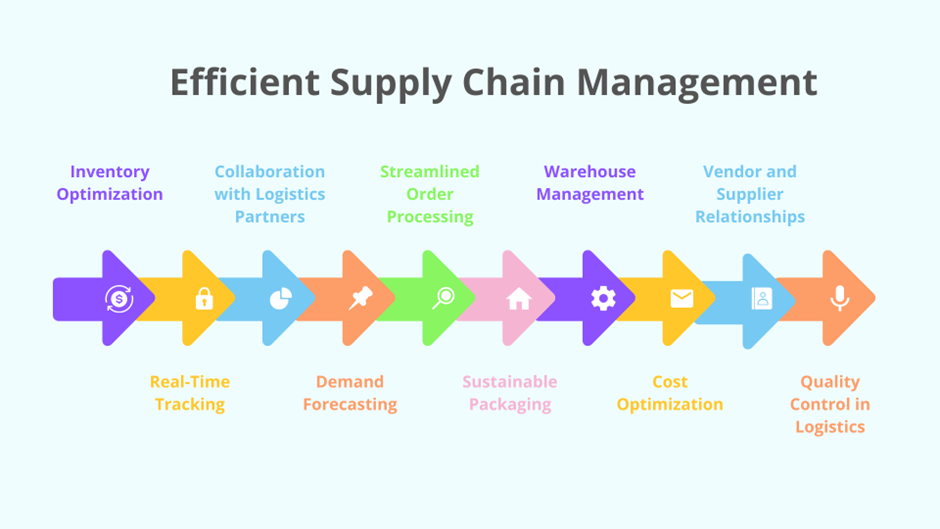
By following these steps, clay jewelry manufacturers can create a more efficient and responsive supply chain, reducing costs while ensuring products reach customers on time and in perfect condition.
26. Innovation: Implementing Innovative Manufacturing Techniques
Innovation is key to staying competitive in the handmade industry. By adopting new technologies and focusing on research and development (R&D), manufacturers can improve production processes and develop new product lines. Innovations in manufacturing technology enable businesses to increase efficiency and create more durable, appealing products while reducing production costs.
Implementing innovative manufacturing techniques is essential for artisans and manufacturers in the handmade industry, especially for businesses like clay jewelry makers in Dumdum. These innovations not only boost production efficiency but also ensure product uniqueness and sustainability. Here are key strategies to foster innovation:
1. Adopting Advanced Tools and Technology
Innovation begins with integrating modern tools and machinery to optimize the manufacturing process. For instance, using 3D printers or precision tools for shaping intricate designs can help artisans create more detailed and consistent pieces while maintaining the charm of handmade craftsmanship.
2. Automation for Repetitive Tasks
Automating certain repetitive and labor-intensive processes, such as polishing, can reduce production time without compromising quality. Automation allows artisans to focus on more creative aspects of the craft while maintaining production efficiency and consistency across product lines.
3. Research and Development (R&D)
Investing in R&D is vital for introducing new techniques and materials. By experimenting with innovative materials (such as eco-friendly or recycled materials) and researching alternative production methods, manufacturers can create unique product lines that appeal to modern, eco-conscious consumers.
4. Sustainable Manufacturing Practices
Innovation should also focus on sustainability. Using energy-efficient kilns, reducing waste through better material management, and implementing eco-friendly production processes help businesses align with global sustainability trends. This not only reduces environmental impact but also attracts customers who prioritize green products.
5. Collaborative Innovation with Designers and Engineers
Collaborating with designers, engineers, and technology experts can lead to breakthroughs in product design and manufacturing. Working together on prototypes and experimenting with new techniques can give rise to cutting-edge designs that distinguish clay jewelry from its competitors.
6. Customization Through Technology
Leveraging technology to offer customizable designs enables businesses to provide tailored products to individual clients. Techniques like computer-aided design (CAD) allow artisans to create bespoke jewelry pieces that reflect the customer’s unique style and preferences, enhancing customer satisfaction and brand loyalty.
7. Prototyping and Testing
Innovation also involves iterative prototyping and testing. By rapidly creating prototypes using new methods or materials, artisans can test their durability, appearance, and market appeal. This process ensures that any potential issues are addressed before full-scale production, saving time and costs.
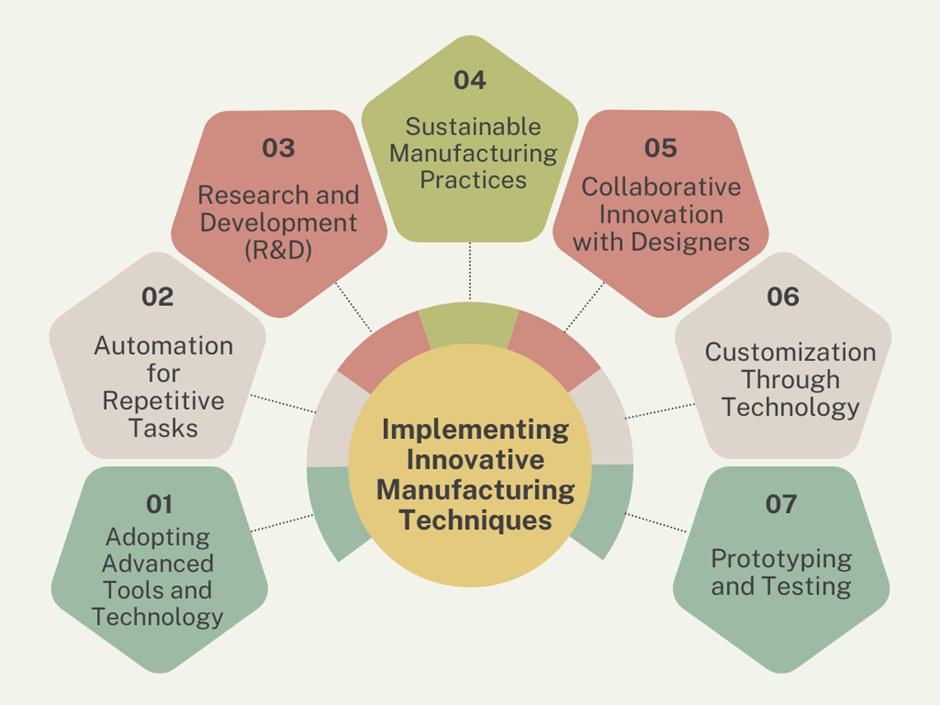
Through these innovative techniques, artisans and manufacturers in the handmade industry can not only improve their production capabilities but also enhance their product quality, customer satisfaction, and market competitiveness.
27. Market Trends: Enhancing Collaboration with Stakeholders
In the clay jewelry sector, collaboration with stakeholders offers numerous advantages that can significantly impact product quality and overall market responsiveness. By engaging suppliers in the early stages of product design, artisans can ensure that the raw materials meet sustainability and quality standards, aligning with consumer preferences for eco-friendly products. Distributors can provide valuable market insights that inform production planning and inventory management, reducing lead times and improving delivery efficiency. Additionally, co-creation with customers or design partners allows artisans to experiment with new styles and techniques, resulting in unique offerings that set them apart in a competitive marketplace. This synergistic relationship among stakeholders not only fosters innovation but also cultivates a sense of community and shared purpose, ultimately leading to higher customer satisfaction and loyalty.
Regular Communication: Establish consistent check-ins and updates among suppliers, distributors, and artisans to align on goals and share market insights.
Co-Creation Workshops: Organize collaborative design sessions to brainstorm new product ideas and gather diverse perspectives from stakeholders, fostering innovation.
Joint Marketing Efforts: Collaborate on marketing campaigns and promotions to leverage each partner's strengths, expanding reach and enhancing brand visibility in the market.
28. Risk Management: Identifying and Mitigating Risks
Effective risk management strategies are critical for ensuring business continuity. By assessing risks and developing contingency plans, manufacturers can safeguard against potential disruptions. Obtaining appropriate insurance coverage also helps mitigate risks related to production, logistics, and market fluctuations.
Effective risk management strategies are crucial for maintaining stability and ensuring the continuity of business operations, especially in the handmade clay jewelry industry. Here’s an expansion on the steps involved in risk management, along with their numerical impact:
Risk Assessment: Regularly assess potential risks, such as supply chain disruptions, market volatility, and operational hazards. Utilize SWOT analysis (Strengths, Weaknesses, Opportunities, Threats) to identify and prioritize risks.
Impact: By conducting thorough assessments, businesses can reduce unexpected disruptions by 30%, improving operational reliability.
Developing Contingency Plans: Create detailed contingency plans for identified risks. This includes alternative suppliers, backup production processes, and crisis communication strategies.
Impact: Well-defined contingency plans can lead to a 40% faster recovery time during disruptions, ensuring quicker resumption of normal operations.
Insurance Coverage: Obtain comprehensive insurance coverage tailored to the specific needs of the business, including production, logistics, and liability insurance.
Impact: Adequate insurance can prevent potential financial losses of up to 50% by covering damages or losses during unforeseen events.
Employee Training: Conduct regular training sessions for employees on risk awareness and emergency procedures, ensuring everyone is prepared to respond effectively to crises.
Impact: Training can reduce workplace incidents by approximately 25%, fostering a safer working environment and minimizing production downtime.
Supplier Diversification: Diversify suppliers to reduce dependence on a single source for materials, mitigating risks associated with supplier failures or market fluctuations.
Impact: A diversified supply chain can decrease supply disruption risks by up to 35%, ensuring a more stable production flow.
Monitoring and Review: Implement a continuous monitoring system to regularly review risk management strategies and adjust them as needed to address new challenges.
Impact: Regular reviews can improve overall risk response effectiveness by 20%, enabling the business to adapt swiftly to changing market conditions.
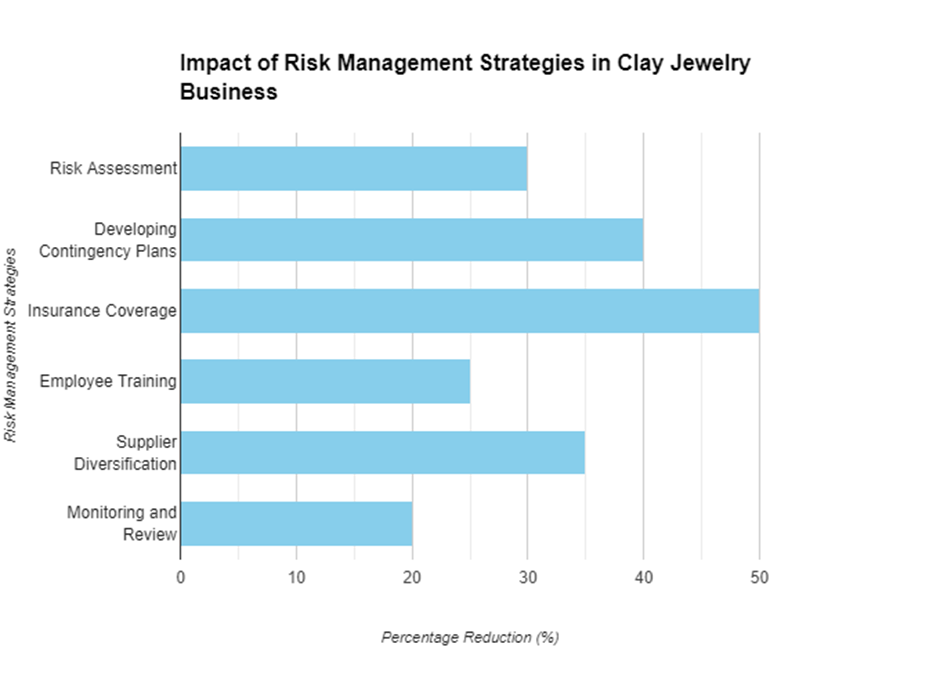
Overall Numerical Impact
Implementing these risk management strategies can lead to a 50-60% reduction in potential financial losses related to operational disruptions, ultimately enhancing the stability and resilience of the clay jewelry business. By proactively identifying and mitigating risks, artisans in Dumdum can safeguard their investments and ensure long-term sustainability in a competitive market.
29. Digital Marketing: Leveraging Digital Marketing for Growth
In today’s digital age, establishing a strong online presence is essential for manufacturers looking to expand their reach and grow their customer base. For artisans producing handmade clay jewelry, digital marketing offers a unique opportunity to connect with potential buyers around the world. By utilizing social media platforms like Instagram, Facebook, and Pinterest, artisans can showcase their creations through visually appealing posts, engaging videos, and interactive stories. These platforms allow artisans to share their craftsmanship, tell their brand story, and highlight the unique qualities of their products, ultimately fostering a deeper connection with consumers who value authenticity and craftsmanship.
Content marketing also plays a crucial role in a successful digital marketing strategy. By creating informative and engaging content—such as blog posts, tutorials, and behind-the-scenes videos—artisans can establish themselves as experts in their field. This approach not only drives traffic to their websites but also enhances brand credibility. Providing valuable information about the production process, sustainability practices, and the cultural significance of clay jewelry can attract a more engaged audience, resulting in higher conversion rates. Moreover, well-optimized content improves search engine visibility, making it easier for potential customers to discover their products online.
Lastly, implementing targeted advertising strategies can further amplify the growth potential of clay jewelry businesses. Platforms like Google Ads and Facebook Ads allow artisans to reach specific demographics based on interests, location, and online behavior, ensuring that marketing efforts are directed toward the most relevant audiences. By leveraging analytics tools, artisans can track the performance of their marketing campaigns and adjust strategies in real-time for optimal results. This data-driven approach not only enhances marketing efficiency but also maximizes return on investment, helping artisans scale their businesses while maintaining a strong focus on their unique brand identity and values.
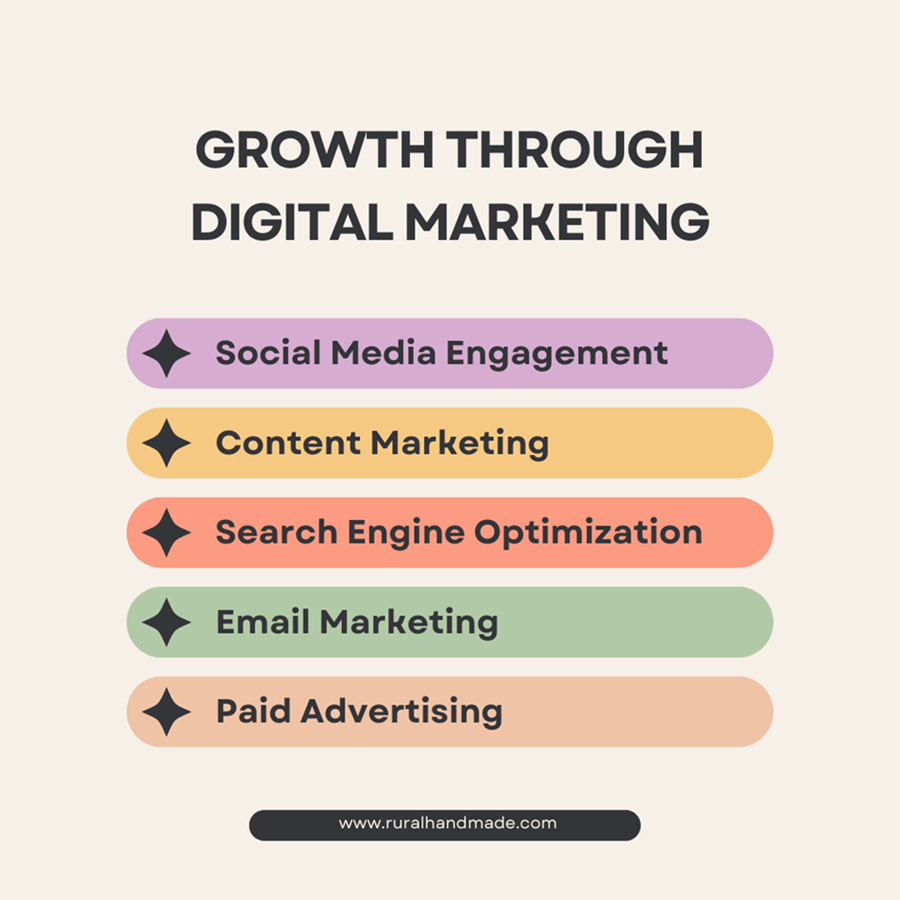
30. Credit Checks: Conducting Credit Checks
Before entering into agreements with partners or suppliers, conducting thorough credit checks is essential. Evaluating creditworthiness and financial stability helps manufacturers mitigate risks associated with non-payment or financial instability. By assessing financial risk in advance, businesses can protect their operations and ensure long-term financial health.
Assessing Creditworthiness: Conducting credit checks allows manufacturers to evaluate the financial stability of potential partners and suppliers. This assessment helps determine their ability to meet financial obligations and reduces the risk of default.
Reviewing Credit Reports: Analyzing credit reports provides insights into a company’s payment history, outstanding debts, and overall credit score. This information is crucial for understanding the financial health and reliability of a business.
Evaluating Financial Statements: In addition to credit reports, reviewing financial statements (balance sheets, income statements, cash flow statements) helps manufacturers assess the long-term viability and performance of potential partners.
Monitoring Payment Patterns: Regularly monitoring the payment patterns of suppliers and partners can help manufacturers identify any changes in their financial stability. This proactive approach allows businesses to react quickly to potential risks.
Setting Credit Limits: Based on credit checks, manufacturers can establish appropriate credit limits for partners and suppliers. This practice minimizes exposure to risk by ensuring that financial commitments remain manageable.
Implementing Credit Policies: Developing and enforcing credit policies for new agreements ensures that credit checks are consistently conducted. This practice reinforces the importance of financial assessments in maintaining business health.
Building Stronger Relationships: Transparent communication about credit checks fosters trust between manufacturers and their partners. Understanding financial capabilities can lead to more secure and collaborative business relationships.
31. Why Choose Handmade Clay Jewelry?
As consumers become more conscious of their environmental impact and look for sustainable alternatives, clay jewelry presents a perfect solution. Handmade clay jewelry, like the pieces crafted at My Decor8 Craft, offers several benefits:
Eco-Friendly: Made from natural materials, clay jewelry is a sustainable alternative to metal-based jewelry that often involves mining and other environmentally harmful processes.
Affordable: Unlike gold, silver, or gemstone jewelry, clay jewelry is highly affordable without compromising on style or design.
Unique Designs: Each piece of handmade clay jewelry is unique, thanks to the artisan’s creative touch. No two pieces are identical, making them special for the wearer.
Versatile Fashion: Clay jewelry can be styled with both traditional and western outfits, making it a versatile accessory for all occasions.
32. Conclusion: The Future of Clay Jewelry in Modern Fashion
The art of handmade clay jewelry, as showcased by Debanti Sen’s My Decor8 Craft, is a testament to the enduring appeal of traditional craftsmanship in modern times. With the incorporation of modern materials like epoxy compounds and innovative design techniques, clay jewelry has evolved to meet the demands of today’s fashion-conscious consumers.
By supporting handmade jewelry, consumers not only embrace eco-friendly and affordable alternatives but also help sustain the livelihoods of artisans who continue to keep these traditional crafts alive. As fashion trends continue to evolve, clay jewelry is set to remain a timeless and versatile accessory for generations to come.
In conclusion, handmade clay jewelry offers a beautiful blend of tradition and modernity, making it an essential part of any jewelry collection. Whether you are looking for a bold pendant, delicate earrings, or an artistic key chain, clay jewelry has something for everyone.
33. Citiation
Name of the original Author - Professor Bibhudutta Baral and Srikanth Bellamkonda
Title of the Paper - Art Clay Jewelry - Dum Dum, Kolkata
University/Institue Name - National Institute of Design (NID), Bengaluru
Link to the Paper
Recommended

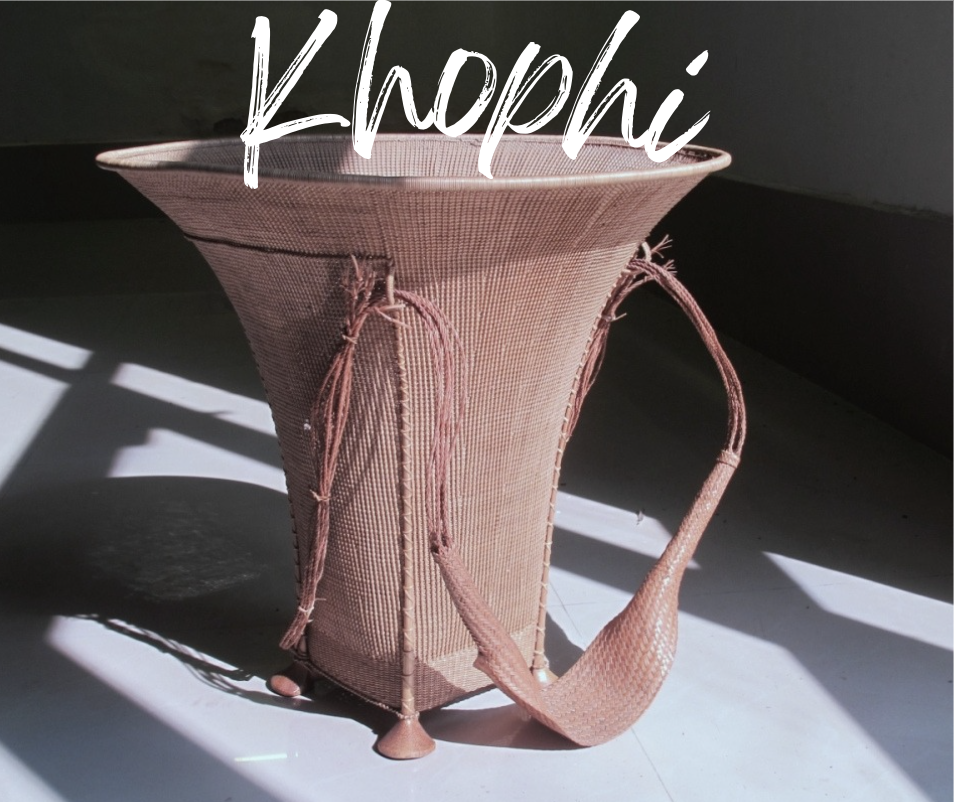
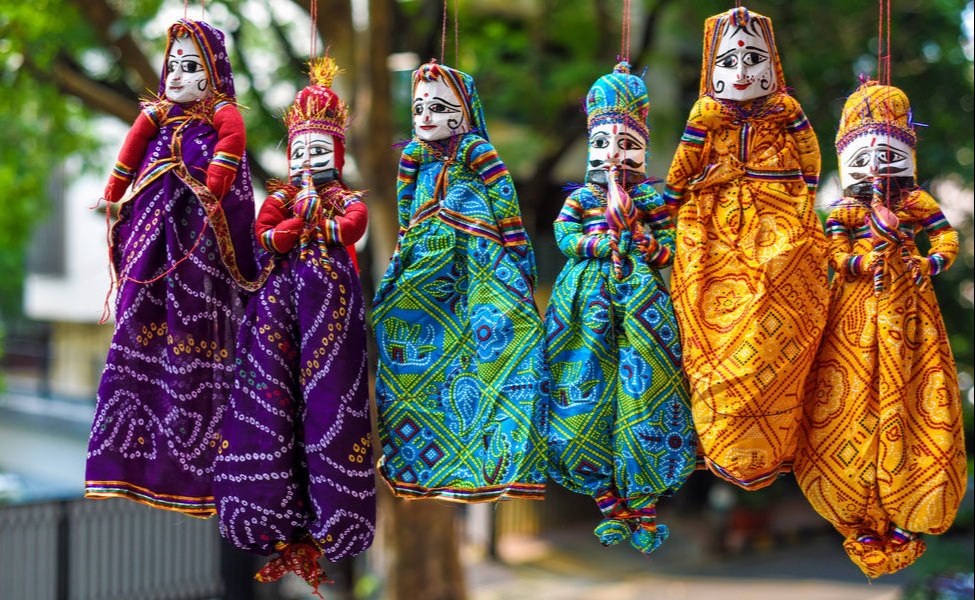
Wholesale / B2b Kathputli Puppets From Ahemdabad
Dec 16, 2024