Ada -the Intricate World Of Chikan Embroidery From Lucknow
Aug 31, 2024 | Gracy Gupta
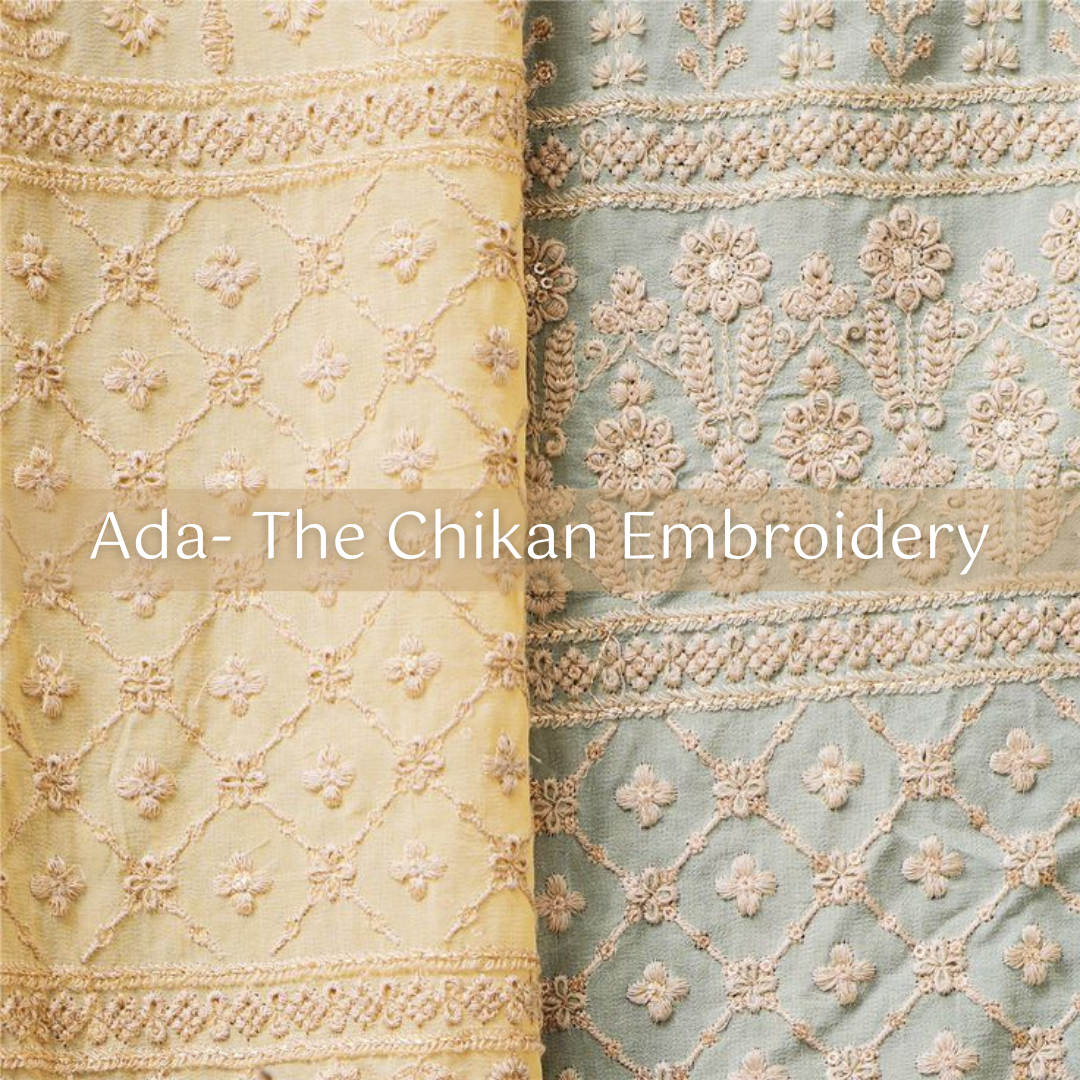
One of the city's most iconic landmarks is the Bara Imambara, an architectural marvel known for its central hall, which is one of the largest arched constructions without support beams. Another notable landmark is the Rumi Darwaza, often referred to as the Turkish Gate, which is a stunning example of Awadhi architecture. The city's vibrant culture is reflected in its language, with Urdu and Hindi being the most widely spoken languages, adding a poetic touch to the daily lives of its inhabitants.
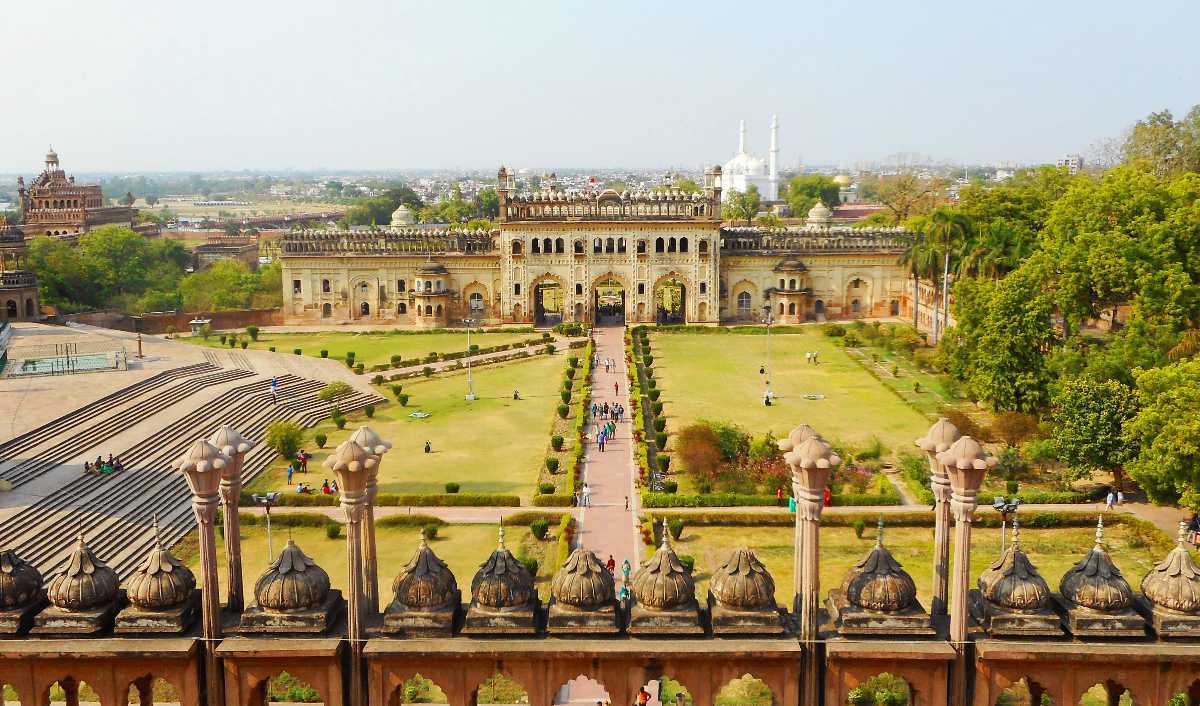
(Image: Bara Imambara in Lucknow)
Lucknow's cuisine is a gastronomic delight, and it is famous for its Nawabi style of cooking, which includes kebabs, biryanis, and kormas. The city is also celebrated for its sweet delicacies like Shahi Tukda and Kheer. Traditional attire includes the elegant Chikankari kurtas, which showcase the intricate embroidery work for which Lucknow is famous. Festivals such as Diwali, Eid, and Holi are celebrated with great enthusiasm, reflecting the city's inclusive and diverse culture.
The city's craftsmanship is showcased through its traditional crafts like Chikankari embroidery, which involves delicate and artistic handwork. Chinhat pottery is another notable craft, characterized by its distinctive blue glaze. Attar (perfume) making, bone craft, kite making, and silverware also hold significant cultural value, each representing a piece of Lucknow's artistic heritage. These crafts not only preserve the city's cultural legacy but also contribute to its economy, making Lucknow a vibrant hub of traditional arts and crafts.
Discover the perfect blend of tradition and modernity with our handcrafted products. Our artisans use time-honored techniques to create beautiful pieces that are perfect for any occasion. From everyday wear to festive attire, our collection has something for everyone. Visit Rural Handmade to explore our wide range of handcrafted items.
Uttar Pradesh Vigyan Manch (UPVM)
Uttar Pradesh Vigyan Manch (UPVM) is a dynamic social organization established in 1994, committed to making a significant difference in the lives of people in Uttar Pradesh. UPVM focuses on women empowerment, income generation, health and family life education, and literacy, aiming to uplift desert communities in the region. The organization emphasizes village-level capacity building, the use of traditional knowledge and appropriate technology, community mobilization, and the holistic development of women.
Over the years, UPVM has made substantial progress in its mission by launching long-term projects at the field and village levels. These initiatives have centered on empowering women and managing resources efficiently. By working closely with women and other marginalized groups, UPVM has gained valuable experience in advocacy, awareness, education, and income-generating activities. This grassroots engagement has earned UPVM recognition as a resource institution in sustainable Chikan embroidery.
The traditional skill development project in Chikankari is implemented by IL&FS Skills, a prominent project-implementing agency for the government and other sectors. Despite India's rapid development, millions still live below the poverty line (BPL), grappling with issues related to health, education, and employment. Providing meaningful employment and livelihood opportunities to the youth is essential for achieving inclusive and sustainable growth. IL&FS Skills has been at the forefront of this effort, offering skills and livelihood training to various social groups, resulting in improved incomes and living standards for individuals, their families, and their communities.
Vision
To enhance the quality of life for oppressed, disadvantaged, and marginalized communities.
Mission
To support, build capacity, and integrate individuals into mainstream society, particularly those traditionally suppressed in personal, social, economic, and political domains.
Objectives of UPVM
To alleviate poverty by improving the economic status of individuals through income-generating activities such as chikankari.
To enhance the skills of artisans through targeted training programs.
To organize women into self-help groups, developing their leadership qualities to empower them to make decisions at personal and social levels.
To identify and develop promising new markets for Chikan products, ensuring sustainable growth and recognition of traditional crafts.
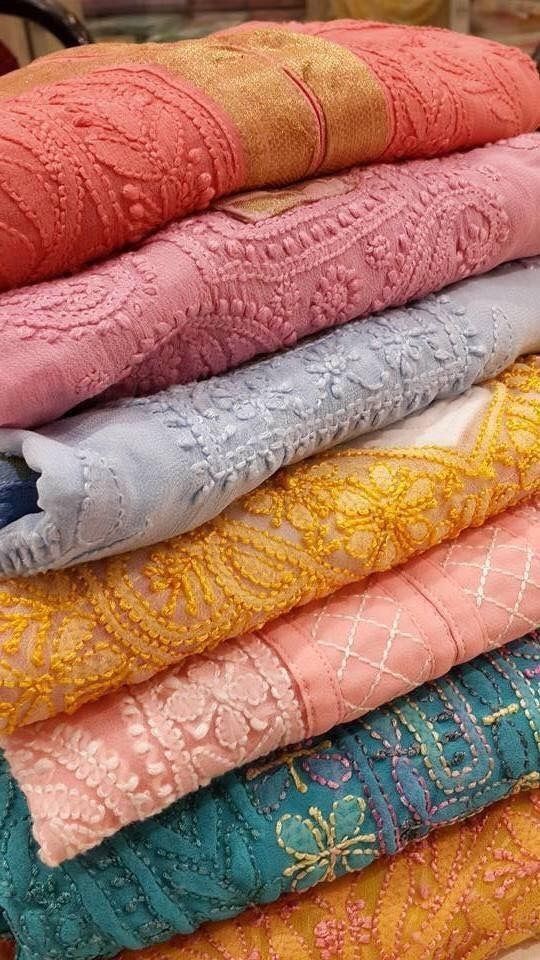
What is the Product Range?
The extensive product range includes elegant ladies wear such as kurtis, tops, suits, shalwars, pajamas/plazos, sarees, suit pieces, dupattas, and skirts while also offering charming children's wear featuring suits, dresses, tops, skirts, as well as stylish men's wear including kurtas and shirts. Additionally, they provide exquisite home furnishing items like tablecloths, runners, table mats, cushion covers, pillow covers, and bed covers.
We pride ourselves on offering unique designs crafted from the finest quality fabrics. Our collection includes elegant ladies' wear, stylish men's wear, and charming children's clothing, all featuring the signature Chikankari embroidery. Whether you're looking for a sophisticated outfit for a special occasion or beautiful home decor items, our products are designed to impress. Discover more at Rural Handmade.
The manufacturing process at UPVM
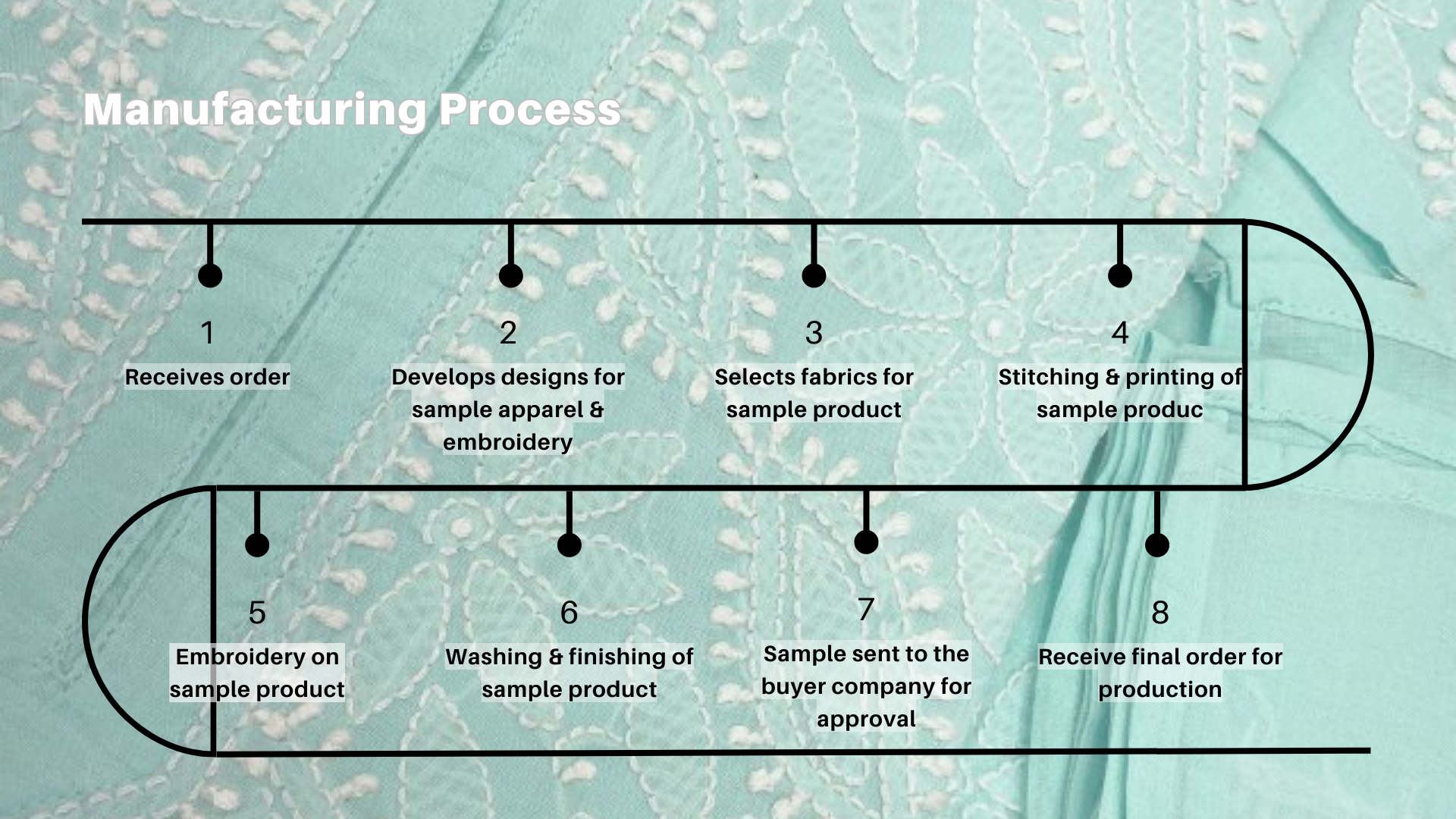
SWOT Analysis of the Chikankari Market
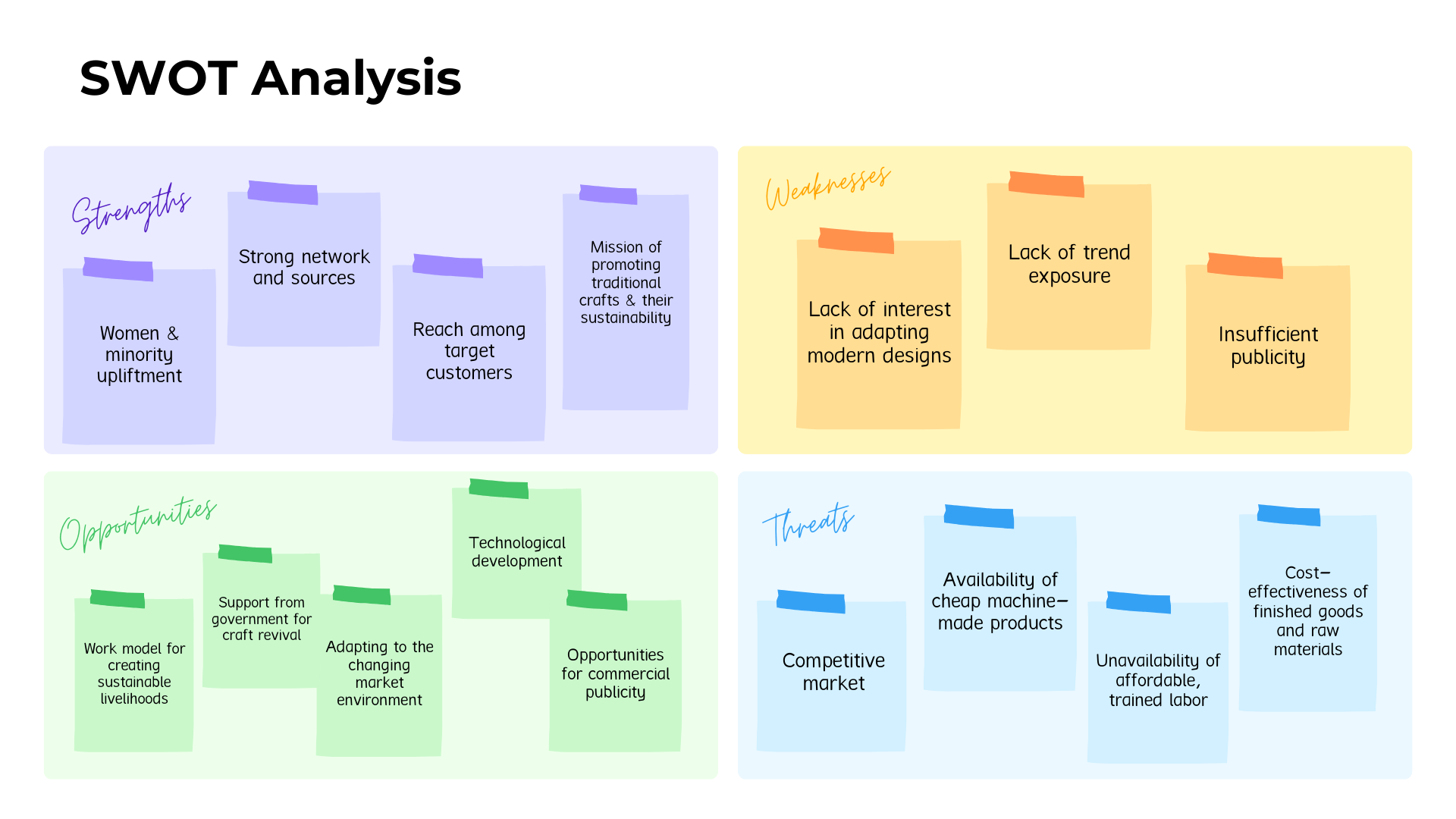
The Timeless Art of Chikankari in Lucknow
Chikankari, a traditional hand embroidery technique, is celebrated for its unique grace and elegance that has transcended generations. Originating from the historical city of Lucknow, this art form embodies a delicate interplay of intricate stitching on fine fabrics such as cotton, muslin, georgette, chiffon, and silk. The hallmark of Chikankari lies in its ability to create a sense of uniformity and consistency across the fabric, achieved through meticulous handwork that involves fine thread knots and elaborate detailing.
The essence of Chikankari embroidery is captured through its motifs and patterns, which are typically inspired by nature and geometric shapes. Floral designs are particularly prevalent, often depicting flowers, leaves, and vines in a variety of arrangements. These motifs are executed with exquisite precision, resulting in embroidery that is both intricate and harmonious. The stitches can be flat or raised, forming delicate mesh patterns that add depth and texture to the fabric. Each stitch in Chikankari, whether it’s the shadow-like Bakhiya, the eyelet-like Hool, or the ornate Jali, contributes to the overall elegance of the piece, making it a true work of art.
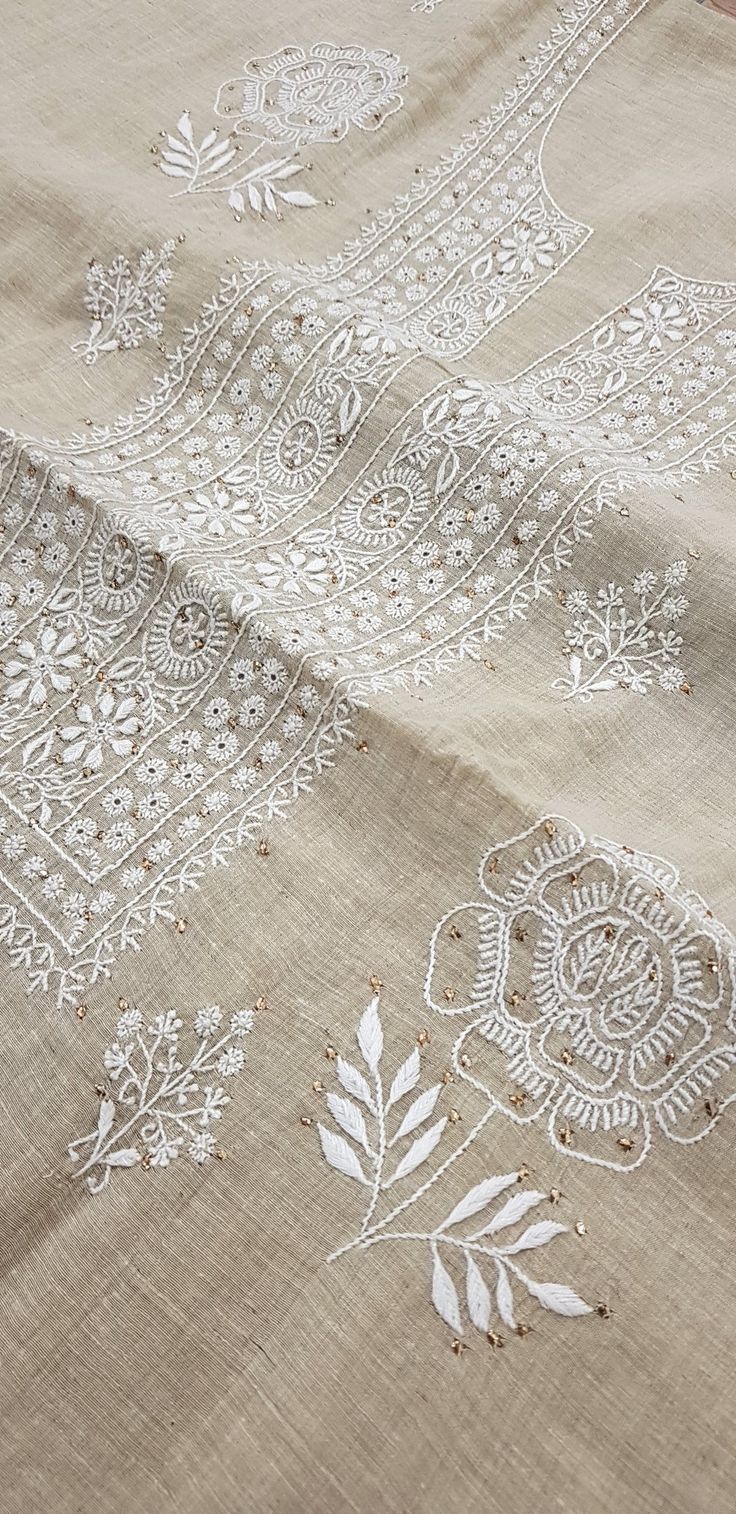
The beauty of Chikankari lies not only in its visual appeal but also in the skill and patience required to create each piece. The process begins with designing the motifs, followed by transferring these designs onto the fabric. Artisans then use various stitches to bring the patterns to life, each stitch contributing to the embroidery's characteristic finesse. The result is a stunning piece of fabric that exudes a timeless charm, making Chikankari a cherished craft that continues to enchant admirers around the world.
(Image: adahbespoke)
History of Chikankari
The origins of Chikankari trace back to the 17th century, credited to Noorjehan, the wife of Mughal Emperor Jehangir, who was inspired by Persian embroidery. She introduced this ethereal, white floral embroidery to the royal courts, earning it patronage and recognition. Historical records also suggest that Chikankari originated in East Bengal, where it was brought to Lucknow by the Nawabs of Awadh. Under their patronage, Chikankari flourished and became renowned. Despite setbacks during British rule, the art form saw a revival post-independence, particularly with the formation of SEWA in 1984, which empowered artisans by eliminating middlemen.
Experience the unparalleled beauty and elegance of our Chikankari products. Each piece is meticulously handcrafted by skilled artisans, preserving the rich heritage and intricate artistry of Lucknow. Explore our stunning collection of Chikankari kurtis, sarees, and home furnishings that blend traditional charm with contemporary styles. Visit Rural Handmade to view our full range of exquisite Chikankari products.
Learning about Chikankari Motifs
According to Mrs. Rani Siddiqui, a national award winner in Chikankari embroidery, the beauty of nature is the primary source of inspiration for many of the designs in Chikankari. This embroidery style, deeply rooted in the cultural and artistic heritage of Lucknow, draws heavily from the Mughal architecture and its intricate details. Noor Jehan, the wife of Mughal emperor Jehangir, played a pivotal role in the evolution of Chikankari motifs. Her fascination with Turkish architectural open-work designs led to the introduction of jaalis (latticework) in Chikan embroidery. These relief and embossed decorative motifs, which adorned Mughal buildings, seamlessly translated into the fabric art, adding an element of elegance and sophistication.
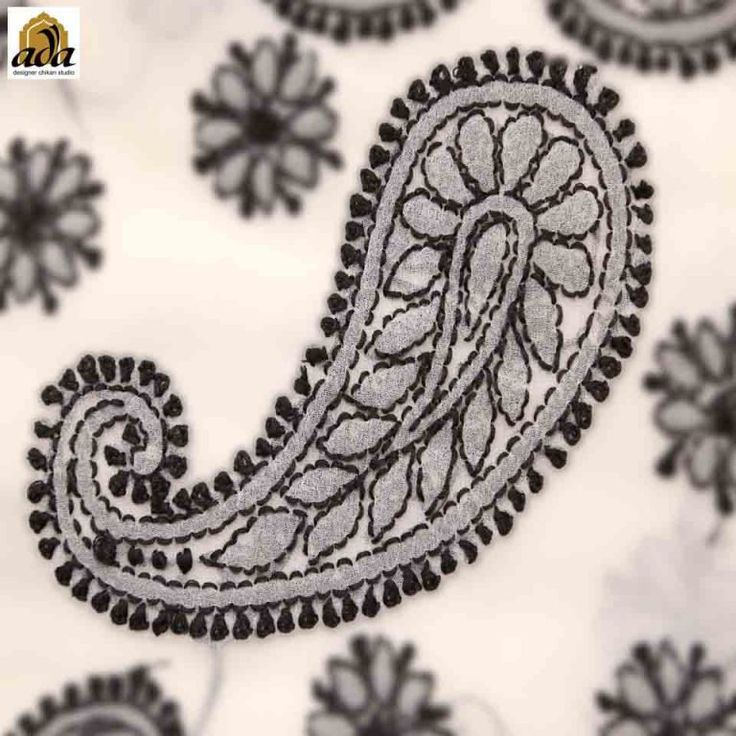
(Image: adachikan)
The Persian influence on Mughal rulers significantly shaped the Chikankari motifs. The rulers' fondness for floral patterns permeated their architecture, paintings, and garments. Consequently, common motifs in Chikankari include paisley, flowers, foliage, creepers, fruits, and various animals like peacocks, parrots, fish, and elephants. The fish motif, in particular, holds historical significance as it was the emblem of the court of Oudh. In contemporary times, designers have introduced new patterns, incorporating horizontal, vertical, and zigzag lines to keep the art form relevant while maintaining traditional designs that remain in high demand.
Chikankari motifs have their own unique vocabulary, with specific terms used to describe the various designs. For instance, 'Buti' refers to stylized floral or geometric forms used in repetitive patterns, while 'Buta' denotes larger versions of these motifs. 'Bel' describes creepers and vines typically used for borders and necklines, and 'Jaal' refers to a floral net pattern covering the fabric's entire surface. The iconic paisley motif, known as 'mangai' or 'kairi' in Indian culture, originates from Persian designs called "boteh jegheh." The creeping vine motif, another Persian import through the Mughals, is favored for filling empty spaces with harmonious and rhythmic designs, often featuring flowers, leaves, buds, and fruits. These motifs not only enhance the visual appeal of Chikankari but also tell a story of cultural fusion and artistic evolution.
What fabrics and threads are used in Chikankari?
Fabrics Used:
Pure Cotton, Muslin, Organdi, Kota, Georgette, Chiffon, Crepe, Silk, Handloom, Dalmia (Synthetic), Chanderi, Terri rubia, Terri voil, Voil, Linen, Net
Thread and Embellishments:
Modern Chikankari also incorporates beads, sequins, and mokaish (white flat silver strip embroidery), with colored threads and silk and cotton threads adding richness to work.
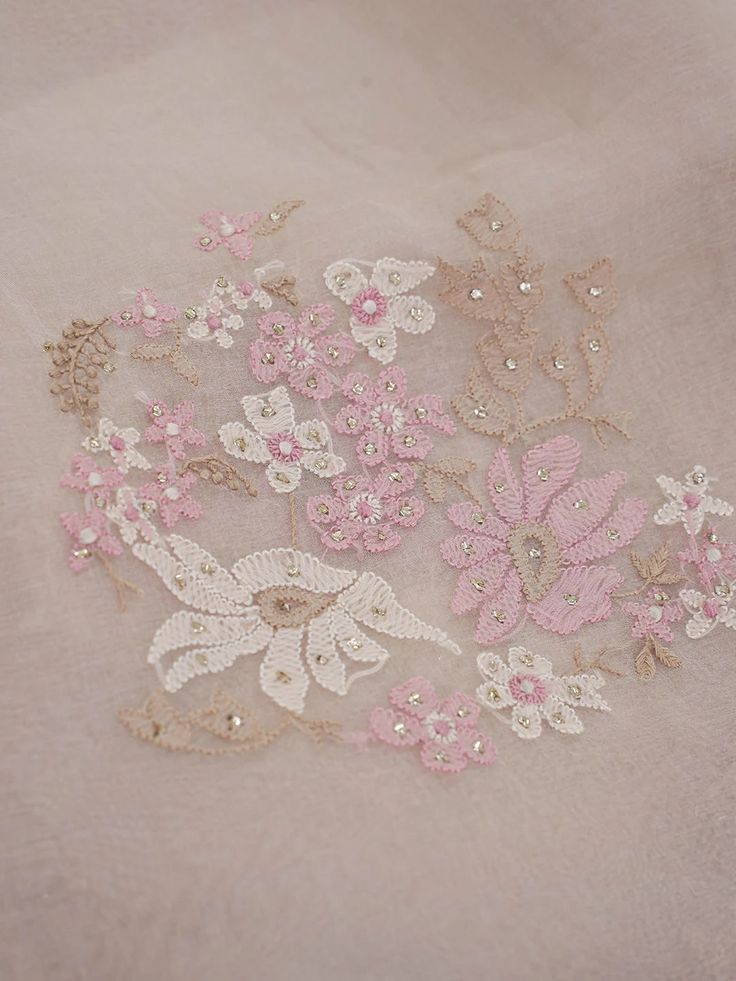
(Image: adachikan)
Stitches in Chikankari
Chikankari embroidery is renowned for its intricate and varied stitches. Here are some of the key stitches used:
Tepchi: A long-running or darning stitch worked with six strands on the right side of the fabric, taking over four threads and picking up one. It forms a line used as a basis for further stitchery or to create simple shapes.
Bakhiya: Also known as double back or shadow stitch, it is done from the wrong side of the fabric with the design rendered in herringbone style. The thread's shadow is visible through the cloth on the right side.
Hool: A fine detached eyelet stitch where a hole is punched in the fabric, and the threads are teased apart and held by small straight stitches. It often forms the center of a flower.
Zanzeera: A small chain stitch worked with one thread on the right side of the fabric. It's used to outline leaf or petal shapes after one or more outlines have been worked.
Rahet: A stem stitch worked with six threads on the wrong side, forming a solid line of back stitch on the right side. Common in the double form of dohra bakhiya as an outlining stitch.
Phanda and Murri: These stitches are used to embroider the center of flowers in chikan work motifs. Phanda is millet-shaped, while Murri is rice-shaped, both similar to French knots.
Banarsi: A unique twisted stitch with no European equivalent, worked with six threads on the right side. It involves small stitches and intricate needlework to create a distinctive pattern.
Khatau: Similar to Bakhiya, but finer and a form of applique. The design is prepared on calico material and stitched onto the final fabric with paisley and floral patterns.
Jali: This stitch involves carefully drawing apart warp and weft threads and inserting minute buttonhole stitches into the cloth, ensuring the back portion of the garment looks as impeccable as the front.
Turpai and Darzdari: Significant stitches in chikan work, with Turpai creating the effect of a thin thread. Darzdari has several varieties, including Kohidarz, Kamal darz, Shankarpara darz, Muchii, and Singbhada darz.
Discover the art of Chikankari by learning a few basic stitches. Click on the image below to get started.
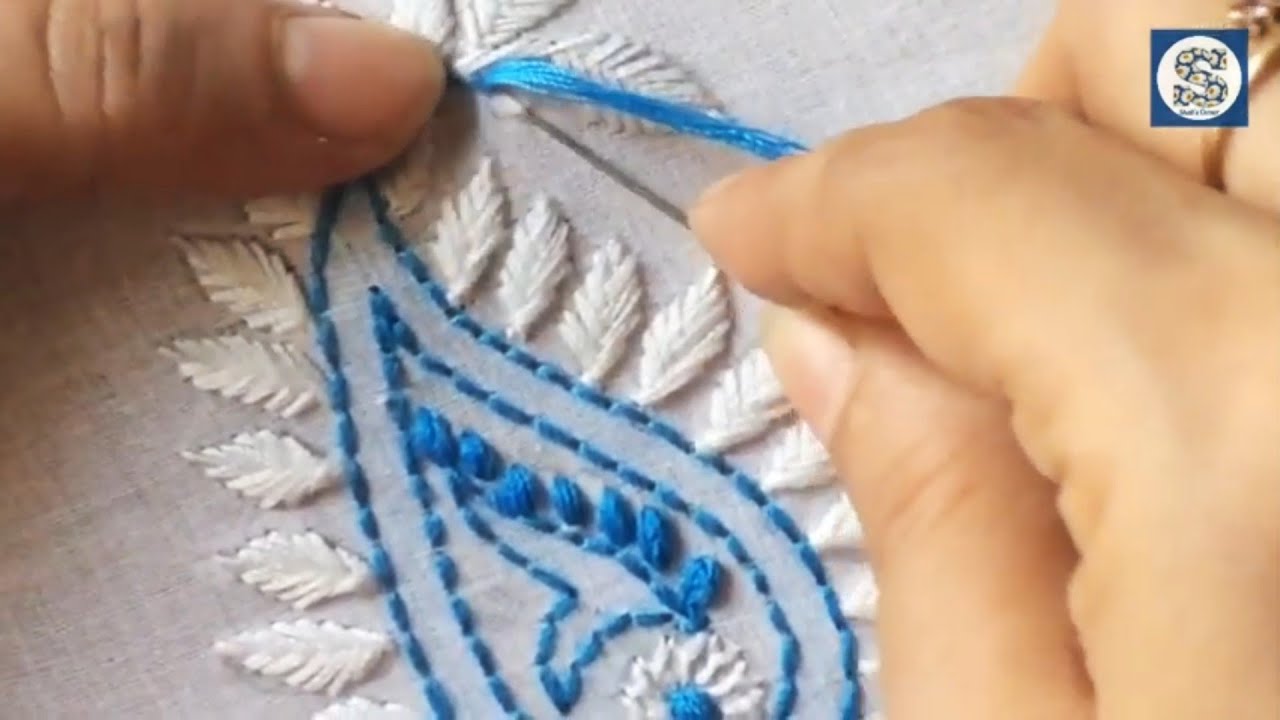
(Video by: Shab Emroideryish)
Other legendary stitches include Pechani, Bijli, Ghaspatti, Makra, Kauri, Hathkadi, Banjkali, Sazi, Karan, Kapkapi, Madrazi, Bulbul-chasm, Taj Mahal, Janjeera, Kangan, Dhania-patti, Rozan, Meharki, Chanapatti, Baalda, Jora, Keel Kangan, Bulbul, Sidhaul, and Ghas ki patti.
What goes into the Chikankari Production Process?
Material Sourcing: The process begins with sourcing raw materials, primarily fabrics and threads. These materials are procured from various markets and vendors and then stored in a central store. The storage is organized by fabric type and color. Inventory management is crucial at this stage, as it tracks materials received and disbursed. The Production Head is responsible for selecting and ordering fabrics, ensuring all necessary threads for rafuu (repair work), turpai (hemming), and stitching are available.
Design: Designing involves either creating new patterns or adapting existing ones using wooden blocks. The design process is critical as it determines the stitches used in the embroidery. Designers draw inspiration from traditional motifs and contemporary trends, ensuring each piece is unique and intricate.
Engraving: Once a design is finalized, it is transferred to wooden blocks. Skilled block makers carve out the wood around the heavier masses first, saving the finer details for last to avoid damage. The finished block resembles flat relief carving, with the design standing out prominently.
Cutting (Shaping): Fabrics are cut and shaped according to the planned products. The cutting pattern determines the number of pieces produced, with intricate cuts requiring more time. An experienced artisan can cut 80-100 pieces per day, working for approximately 7 hours.
Stitching: After cutting, the fabrics are stitched using ‘BUSH’ sewing machines and Vardhaman threads. This step involves fastening or attaching pieces using various stitches. Each product, once cut and shaped, is carefully stitched to ensure durability and aesthetic appeal.
Printing: The next step involves printing the designs onto the fabric using the prepared wooden blocks. The blocks are dipped in dyes such as neel (indigo) and safeda (white), and the printer firmly presses them onto the cloth, striking the back with a wooden mallet. For dark shades, a paste of silver powder, gond (adhesive), and water is used. This process can be done on half-stitched or fully-stitched fabrics, depending on the product requirements.
Embroidery: Embroidery is the heart of Chikankari, where artisans decorate the fabric with needle and thread or yarn. The technique includes various stitches like chain stitch, buttonhole or blanket stitch, running stitch, satin stitch, and cross stitch. Embroidery may also incorporate other materials such as metal strips, pearls, beads, quills, and sequins. Completing an intricate Chikankari saree can take about a month for four artisans working together, while an XL-size Noori kurti can take 20-25 days for all-over embroidery by one artisan.
Washing/Finishing: Post-embroidery, the fabric undergoes thorough washing to remove any residues and to prepare it for finishing touches. This process includes bleaching, acid treatment, stiffening, or starching, and ironing. Quality inspection is conducted in two steps: pre-washing to check for excess thread, over-stitching, and stitching gaps, and post-washing to assess color fading, patches, iron burns, and starch mix proportions. The washed fabrics are then passed to the finished goods section.
Finished Goods: In this final stage, the AGMC (Assistant General Manager of Commerce) oversees the completion of the products. This includes price tagging, individual packing, and bulk packing in cartons. Retail sales are also handled in this section, catering to customers who visit the organization.
This meticulous and labor-intensive process ensures that each Chikankari piece is not only beautiful but also a testament to the skill and dedication of the artisans involved.
Experience the beauty and craftsmanship of traditional handcrafted items with our curated selection. From elegant Chikankari attire to exquisite home decor, each piece is a testament to the skill and dedication of our artisans. Perfect for adding a touch of cultural heritage to your lifestyle, our products are crafted with love and precision. Explore our unique collection at Rural Handmade and bring home a piece of timeless tradition.
Understanding Scalability and Costing in Ada Chikankari
Scalability in the Ada Chikankari industry is a critical factor for artisans, small business owners, and manufacturers aiming to expand their operations. As depicted in the pictograph above, scalability involves increasing the number of artisans or production units to meet rising demand. However, this expansion requires careful planning to maintain the quality and authenticity of the craft while optimizing production processes. By investing in training and infrastructure, businesses can scale up effectively, ensuring that the unique characteristics of Chikankari embroidery are preserved even as production volumes increase. For more on scaling artisan crafts, visit UNESCO's Creative Cities.
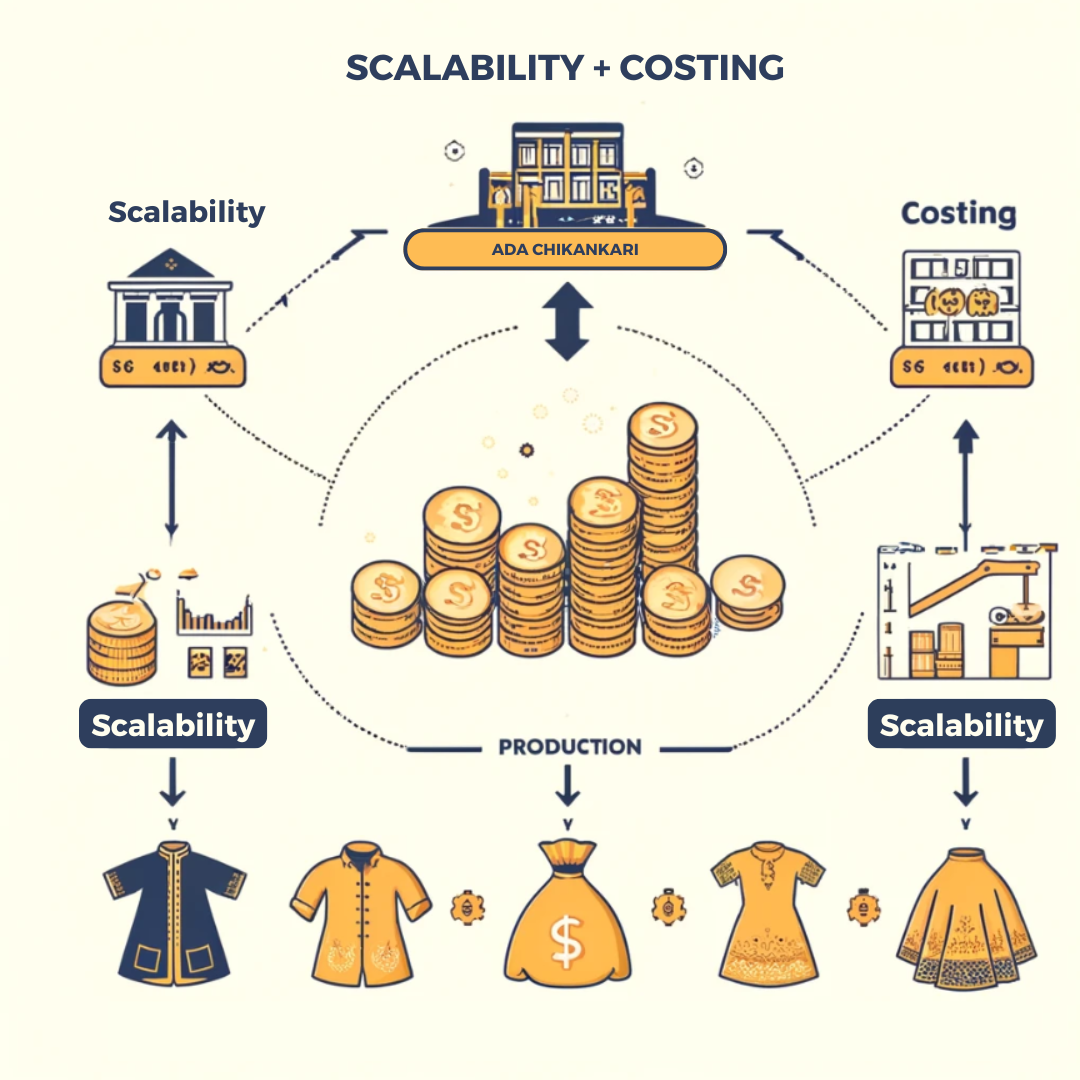
The cost of scaling up production in the Chikankari industry is a major consideration. As shown in the pictograph, the cost is depicted by stacks of coins, representing the investment needed for additional materials, labor, and technology. While initial costs may be high, strategic investment can lead to economies of scale, where the cost per unit decreases as production increases. This balance between scaling and costing is essential for maintaining profitability while expanding operations. For insights on cost management in artisan industries, explore resources from The International Trade Centre.
Finally, the pictograph highlights the relationship between increased production output and associated costs. As the number of finished Chikankari products rises, businesses must ensure that the pricing strategies reflect both the added value of handmade craftsmanship and the need to remain competitive in the market. By carefully managing costs and scaling operations, Ada Chikankari businesses can achieve sustainable growth, ensuring that this traditional art form continues to thrive in the modern marketplace. To learn more about balancing production and cost in the craft industry, refer to Crafts Council UK.
Measure the Impact of Ada Chikankari
Balancing Tradition with Environmental, Social, and Economic Responsibility…
The environmental impact of Ada Chikankari, like many traditional crafts, is shaped by the materials and processes used. Chikankari traditionally relies on natural fibers such as cotton, muslin, and silk, which are more sustainable compared to synthetic alternatives. However, the water-intensive nature of cotton production and the chemical dyes often used can contribute to environmental degradation. Reducing carbon emissions within the Chikankari industry requires a shift towards organic cotton, natural dyes, and water-efficient practices. By embracing eco-friendly methods, artisans and manufacturers can lower their environmental footprint while preserving the authenticity of this centuries-old craft. For more information on sustainable textile practices, visit Textile Exchange.
In addition to environmental concerns, Ada Chikankari has significant social impacts, particularly in empowering rural communities. The craft provides employment opportunities for thousands of artisans, many of whom are women, helping to sustain traditional skills and foster economic independence. By promoting fair trade practices and ensuring that artisans receive fair wages, the Chikankari industry contributes to improving the livelihoods of entire communities. These social benefits are integral to maintaining the cultural heritage of Chikankari while promoting economic development. Learn more about the social impact of traditional crafts at Fair Trade Federation.
Economically, Ada Chikankari plays a crucial role in supporting local economies and preserving cultural heritage. The demand for authentic hand-embroidered garments has created a niche market, allowing small businesses and B2B wholesalers to thrive by catering to discerning customers worldwide. However, scaling up production to meet this demand must be done carefully to avoid diluting the craft's authenticity and value. By balancing economic growth with sustainable practices, the Chikankari industry can continue to expand without compromising the quality that defines this art form. For insights into scaling traditional crafts sustainably, visit Ethical Fashion Forum.
Carbon Footprint: The industry also faces challenges related to carbon emissions, especially in the supply chain and transportation of goods. As global demand for Chikankari products increases, so does the carbon footprint associated with exporting these goods. By investing in greener logistics solutions and encouraging local production where possible, the industry can mitigate its carbon emissions. Collaboration with organizations focused on reducing carbon footprints in the fashion and textile industry can help Ada Chikankari businesses adopt more sustainable practices. For guidance on reducing carbon emissions in fashion, check out Carbon Trust.
Here's a table for the top ten manufacturers/sellers of Ada Chikankari in Lucknow, including their details.
A Seller’s Guide for Ada Chikankari
What are the logistical requirements in Ada Chikankari?
Here’s a detailed explanation of each stage of the logistics involved in the Ada Chikankari supply chain.:
Raw Material Sourcing: The process begins with sourcing high-quality raw materials, primarily cotton or muslin fabrics, which are the base of Chikankari embroidery. The quality of these materials is critical as they determine the durability and the final look of the embroidered product.
Embroidery Craftsmanship: Skilled artisans, often from rural areas, handcraft the intricate Chikankari patterns. This stage requires significant time and effort, as each piece is meticulously embroidered using traditional techniques passed down through generations.
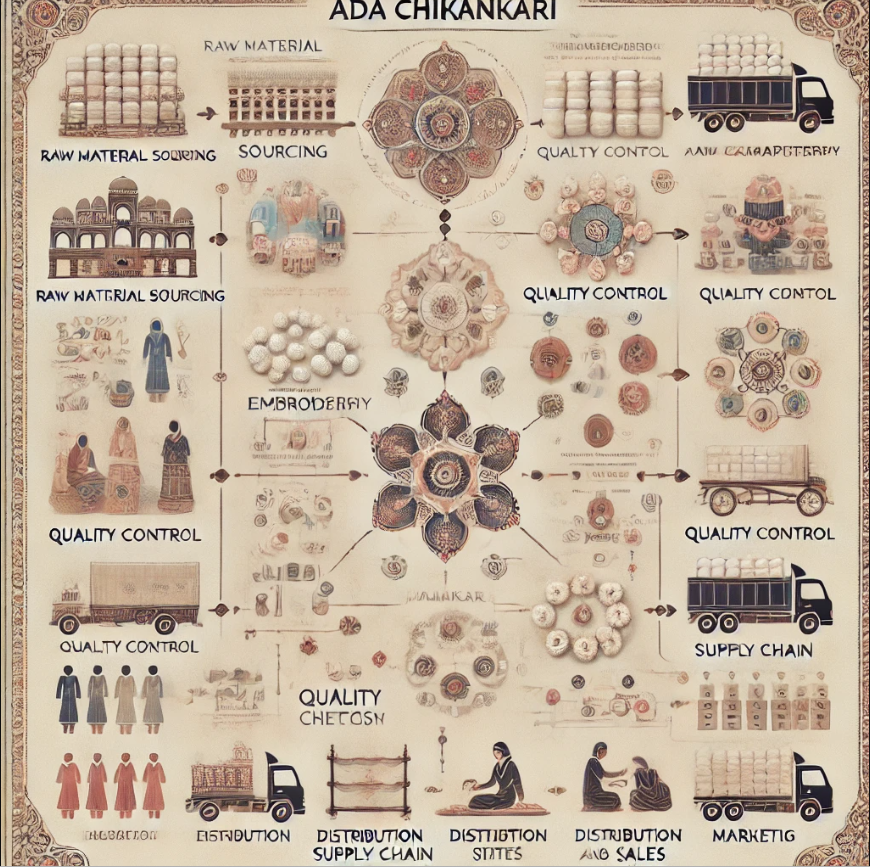
Quality Control: After the embroidery is completed, each piece undergoes strict quality control checks. This ensures that the craftsmanship meets the high standards associated with Ada Chikankari. Any defects or inconsistencies are identified and corrected, maintaining the brand’s reputation for excellence.
Distribution and Supply Chain: Once approved, the products are packaged and transported through a well-coordinated distribution network. This network ensures that the embroidered pieces reach both domestic and international markets efficiently, keeping up with demand.
Marketing and Sales: The final stage involves the marketing and sales of the products. This includes online platforms, brick-and-mortar stores, and partnerships with wholesalers and retailers. Effective marketing strategies help in reaching target audiences, such as artisans, entrepreneurs, and B2B wholesalers, ensuring the continued growth of the Chikankari market.
Each of these stages is interconnected, ensuring that the Ada Chikankari products maintain their cultural integrity while meeting modern market demands.
How to Ensure Quality Control in Ada Chikankari Embroidery?
Quality control is the cornerstone of Ada Chikankari, ensuring that each piece of embroidery reflects the rich heritage and intricate craftsmanship for which this art form is known. In the highly competitive textile market, maintaining consistent quality is vital for artisans, small business owners, and manufacturers alike. The meticulous process begins with selecting the finest fabrics, often muslin, cotton, or silk, which serve as the canvas for the delicate Chikankari stitches. Each fabric undergoes rigorous inspection for defects, ensuring that only the highest quality materials are used. This step is crucial because the quality of the base fabric directly impacts the final product's durability and aesthetic appeal. For more insights on fabric selection and its importance in textile production, visit Textile Exchange.
Once the fabric passes initial inspection, the embroidery process begins, involving multiple layers of quality checks. Skilled artisans, trained in traditional Chikankari techniques, meticulously handcrafted each piece, with supervisors overseeing the process to ensure consistency in the patterns, stitch density, and overall design. This multi-tiered approach to quality control helps prevent common issues such as uneven stitching, loose threads, or color bleeding. Each piece is carefully scrutinized to ensure it meets the stringent quality standards that define Ada Chikankari. To understand more about the importance of quality control in hand-embroidered textiles, explore resources at Craftmark.
The final stage of quality control involves washing, finishing, and packaging the embroidered pieces. Washing is done with care to prevent any shrinkage or damage to the intricate embroidery, followed by ironing and finishing processes that enhance the fabric's luster and texture. Packaging is not just a protective measure but also a presentation aspect that can influence customer perception. Each product is packaged with care, ensuring it arrives in pristine condition. For further details on industry-standard finishing techniques, you can refer to The Woolmark Company.
Cost Management Techniques in Ada Chikankari
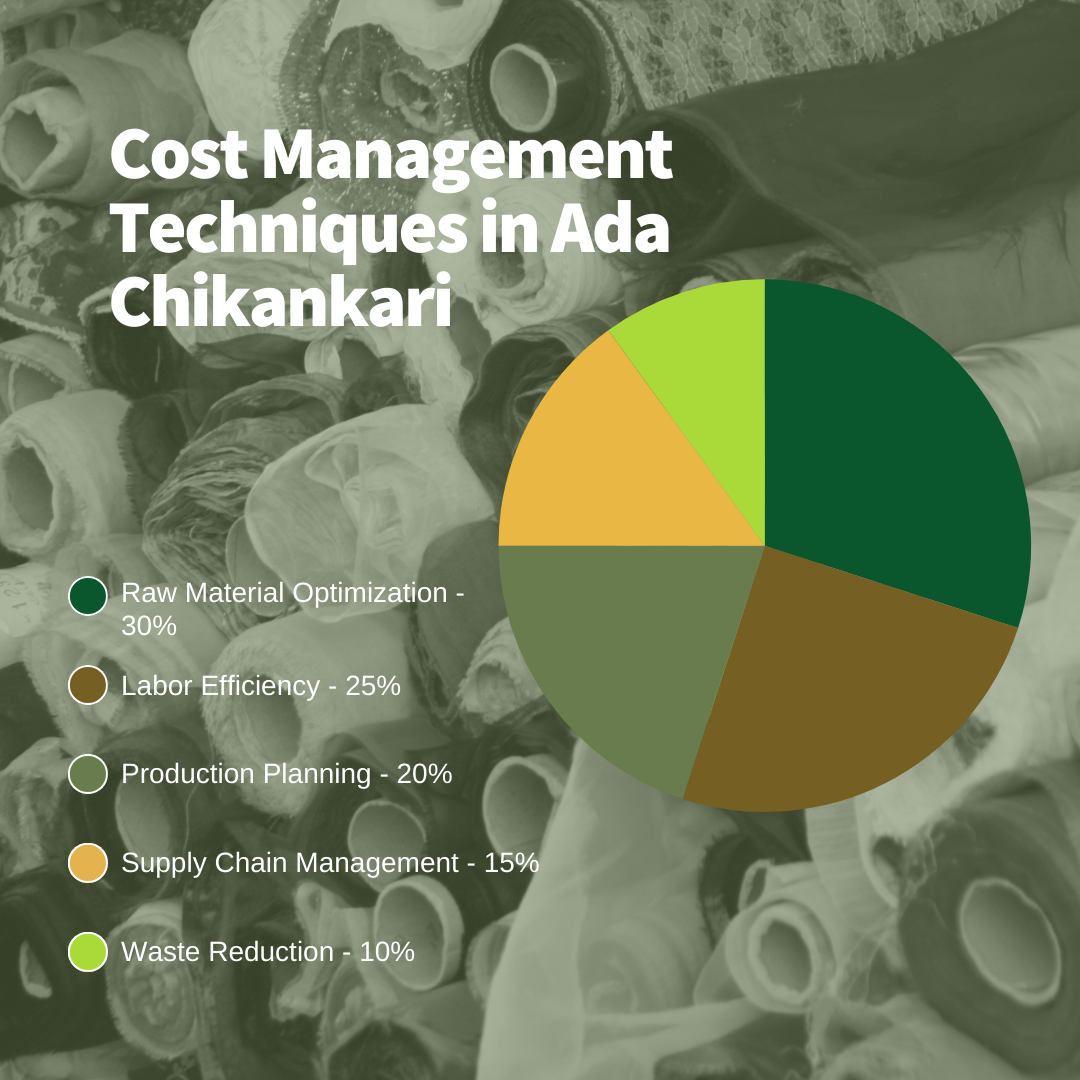
Raw Material Optimization (30%)
Raw materials, including fabrics, threads, and embellishments, make up a significant portion of the costs in Ada Chikankari. Effective cost management starts with optimizing raw material usage. This can involve bulk purchasing to take advantage of discounts, carefully selecting quality materials that minimize wastage, and working closely with suppliers to negotiate better rates. By controlling raw material costs, artisans and manufacturers can significantly lower the overall production expenses while maintaining the quality of the Chikankari work.Labor Efficiency (25%)
Ada Chikankari is a labor-intensive craft that relies heavily on skilled artisans. Managing labor costs without compromising the artisans' livelihood or the quality of the embroidery is crucial. This can be achieved by improving workflow efficiency, providing training to enhance artisan skills, and implementing performance-based incentives. Automation of certain non-essential tasks (like pattern tracing) can also free up artisans to focus on more intricate work, thereby increasing productivity without increasing costs.Production Planning (20%)
Proper production planning can reduce bottlenecks and avoid costly delays. This involves scheduling production runs based on demand forecasts, optimizing batch sizes to reduce setup times, and managing inventory to ensure that materials are available when needed without overstocking. Efficient production planning minimizes idle time and reduces the costs associated with rushed orders or missed deadlines.Supply Chain Management (15%)
Effective supply chain management ensures that materials and finished products move smoothly from suppliers to manufacturers to wholesalers. By developing strong relationships with reliable suppliers, artisans, and business owners can negotiate better terms, such as extended payment periods or lower prices for early payments. Streamlining logistics to reduce transportation costs, and ensuring timely delivery can also prevent costly delays and minimize the need for expensive express shipping.Waste Reduction (10%)
Even small reductions in waste can lead to significant cost savings in Ada Chikankari. This can involve reusing leftover materials, minimizing errors during the production process, and recycling scraps into new products. Implementing quality control measures early in the production process can also reduce the likelihood of producing defective goods, thus saving on rework and material costs.
Why is Customer Service important?
In the world of Ada Chikankari, exceptional customer service is the backbone of business success, particularly for artisans, small business owners, and B2B wholesalers. The intricacy of Chikankari embroidery demands not just a skilled hand but also a deep understanding of customer needs and preferences. By providing top-notch customer service, businesses can foster trust and loyalty among their clients, which is essential in a market that values both tradition and quality. According to a report by Harvard Business Review, companies that prioritize customer experience see revenues increase by 4% to 8% above their market average. For Chikankari sellers, this translates to more repeat customers and stronger word-of-mouth referrals, which are crucial in a niche market like this.
Moreover, excellent customer service in Ada Chikankari helps in addressing any issues or concerns that may arise, whether it's regarding product quality, delivery timelines, or customization requests. By resolving problems swiftly and effectively, businesses can prevent negative experiences from escalating into bad reviews or lost customers. Forbes highlights that 96% of customers who are unhappy with a service won’t complain; they simply won’t return, making proactive customer service even more vital. In a highly competitive industry, where each piece is often handcrafted and made-to-order, maintaining clear communication and ensuring customer satisfaction is not just a best practice but a necessity for sustaining long-term success.
Market Trends in Ada Chikankari
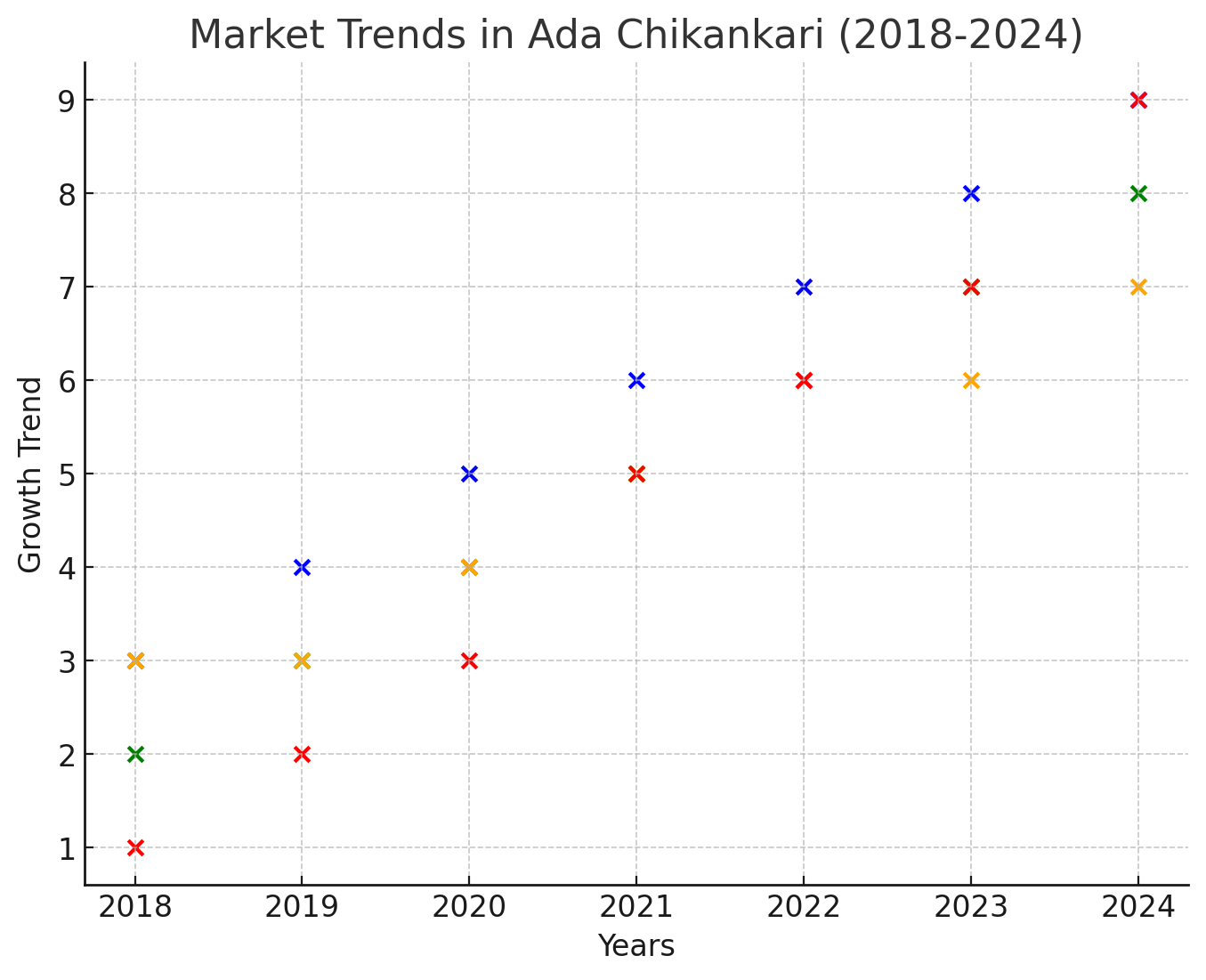
The scatter plot infographic above illustrates the evolving market trends in Ada Chikankari from 2018 to 2024. As observed, the industry has experienced a consistent rise in demand, driven by an increased appreciation for handcrafted and culturally rich textiles. The x-axis marks the timeline, while the y-axis highlights key factors such as market demand, sustainability practices, innovation in designs, and digital presence. Each trend is distinctly marked, showing a clear trajectory of growth across all categories. Notably, the digital presence has seen the most significant spike, indicating the shift towards online platforms for promotion and sales.
Sustainability practices have also gained momentum, reflecting the industry's alignment with global eco-conscious movements. Simultaneously, innovation in designs has kept the Chikankari tradition relevant in modern fashion, appealing to a broader audience. For artisans, small business owners, and wholesalers, these trends present a compelling case for investing in digital strategies and sustainable practices to capitalize on the growing demand. As the market continues to evolve, those who adapt to these trends are likely to find long-term success in the Ada Chikankari industry.
Innovation and Technology in Chikankari
Innovation in Design and Production Techniques
Innovation in Ada Chikankari has transformed this traditional craft, allowing it to adapt to modern market demands while preserving its cultural heritage. Advanced design software and digital embroidery machines have enabled artisans to experiment with intricate patterns and complex designs that were once difficult to achieve by hand. This technological advancement not only speeds up production but also ensures consistency and precision in every piece. According to Textile Today, the integration of digital tools in textile design has increased production efficiency by 20-30%, allowing small businesses and manufacturers to scale up without compromising on quality. Moreover, the use of CAD (Computer-Aided Design) systems allows artisans to visualize and tweak designs before they are physically produced, reducing waste and optimizing resource use.
Technology in E-commerce and Customer Engagement
The adoption of e-commerce platforms and digital marketing tools has also been a game-changer for Ada Chikankari's businesses. By leveraging technology, artisans and small business owners can reach a global audience, expanding their market far beyond local bazaars and craft fairs. Online marketplaces like Etsy and Amazon Handmade provide an accessible platform for Chikankari sellers to showcase their products to a worldwide customer base. Statista reports that global e-commerce sales are projected to reach $6.4 trillion by 2024, underscoring the importance of online presence for small businesses. Additionally, tools like AI-driven customer insights and CRM (Customer Relationship Management) software help businesses personalize their marketing strategies and improve customer retention. For instance, a study by Salesforce revealed that companies using AI in their CRM saw a 20% increase in customer satisfaction, demonstrating the value of technology in enhancing customer engagement for Chikankari sellers.
Optimizing Shipping and Handling in Ada Chikankari
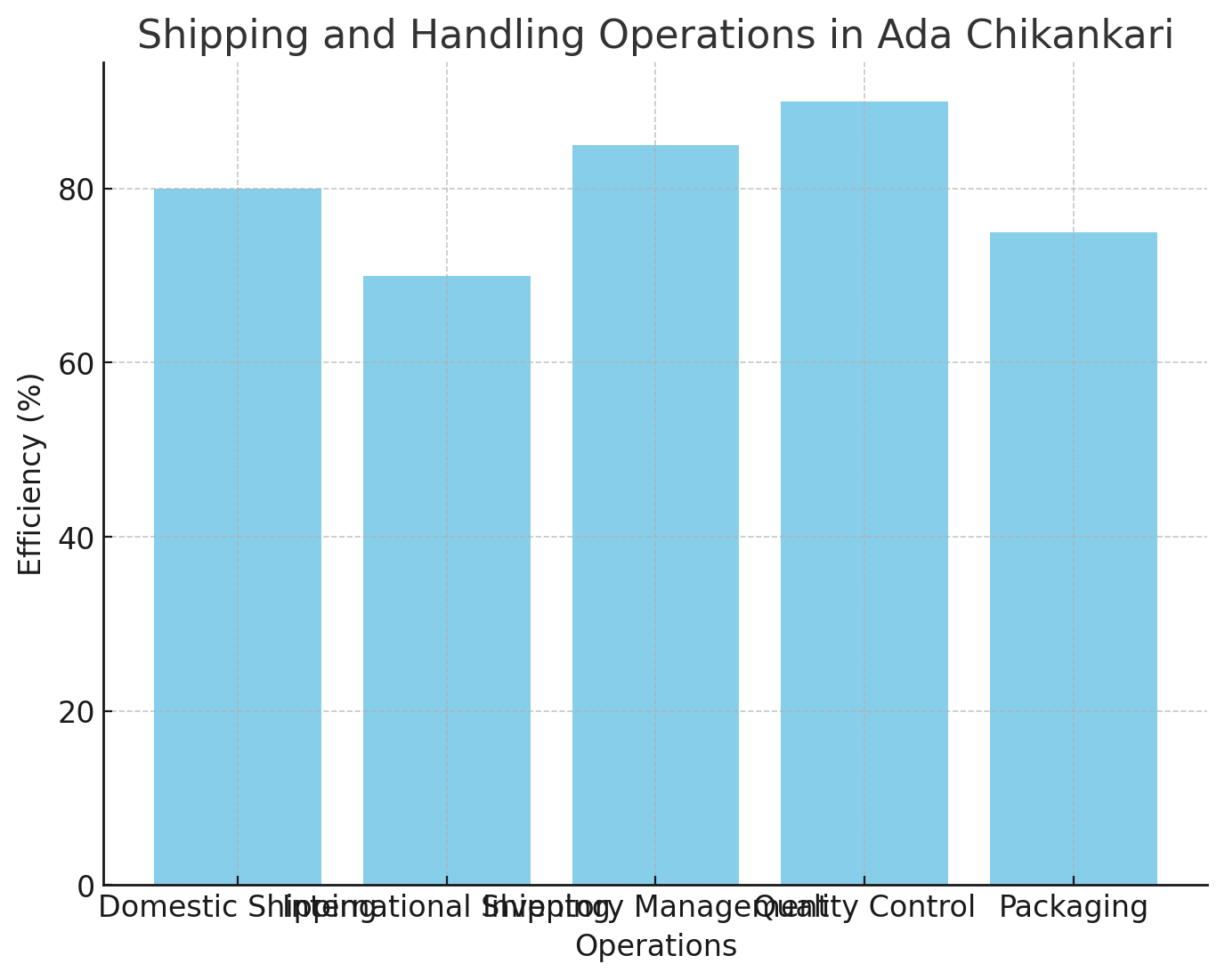
Domestic vs. International Shipping: The bar graph highlights the efficiency of domestic and international shipping operations within the Ada Chikankari industry. Domestic shipping boasts an 80% efficiency rate, showcasing well-established processes. However, international shipping lags slightly at 70%, indicating potential areas for improvement, such as streamlining customs procedures and enhancing global logistics partnerships.
Inventory Management and Quality Control: Inventory management and quality control are critical components of the supply chain, with efficiency rates of 85% and 90%, respectively. The high performance in these areas reflects the industry's commitment to maintaining stock levels and ensuring product quality. This efficiency is vital for meeting customer expectations and sustaining market demand.
Packaging: Packaging, with a 75% efficiency rate, is another crucial operation that influences customer satisfaction and product preservation. While the current performance is strong, focusing on sustainable packaging solutions could further enhance efficiency and appeal to eco-conscious consumers.
How to navigate risks in this craft industry?
Risk Assessment: In the Ada Chikankari industry, risk assessment is essential for identifying potential threats to production, supply chain, and market stability. It involves evaluating factors such as market demand fluctuations, raw material shortages, and workforce challenges. Regular risk assessments help artisans, manufacturers, and business owners anticipate issues before they escalate. For more insights into effective risk assessment practices, visit The Risk Management Association.
Contingency Planning: Once risks are identified, contingency planning is crucial for mitigating these risks. This involves developing backup strategies, such as alternative suppliers for raw materials or flexible production schedules to accommodate unforeseen disruptions. Contingency planning ensures that the business can continue operating smoothly, even in adverse conditions. To learn more about crafting effective contingency plans, refer to The Business Continuity Institute.
Insurance: Insurance plays a pivotal role in protecting against financial losses resulting from risks that cannot be fully mitigated. In the context of Ada Chikankari, insurance can cover various aspects, including property damage, loss of goods in transit, and liability claims. Combining risk assessment and contingency planning with appropriate insurance coverage creates a robust safety net for businesses in this industry. For guidance on selecting the right insurance policies, check out the Insurance Information Institute.
The Venn diagram below illustrates the interconnectedness of risk assessment, contingency planning, and insurance, highlighting how these elements overlap to create a comprehensive risk management strategy in the Ada Chikankari industry.
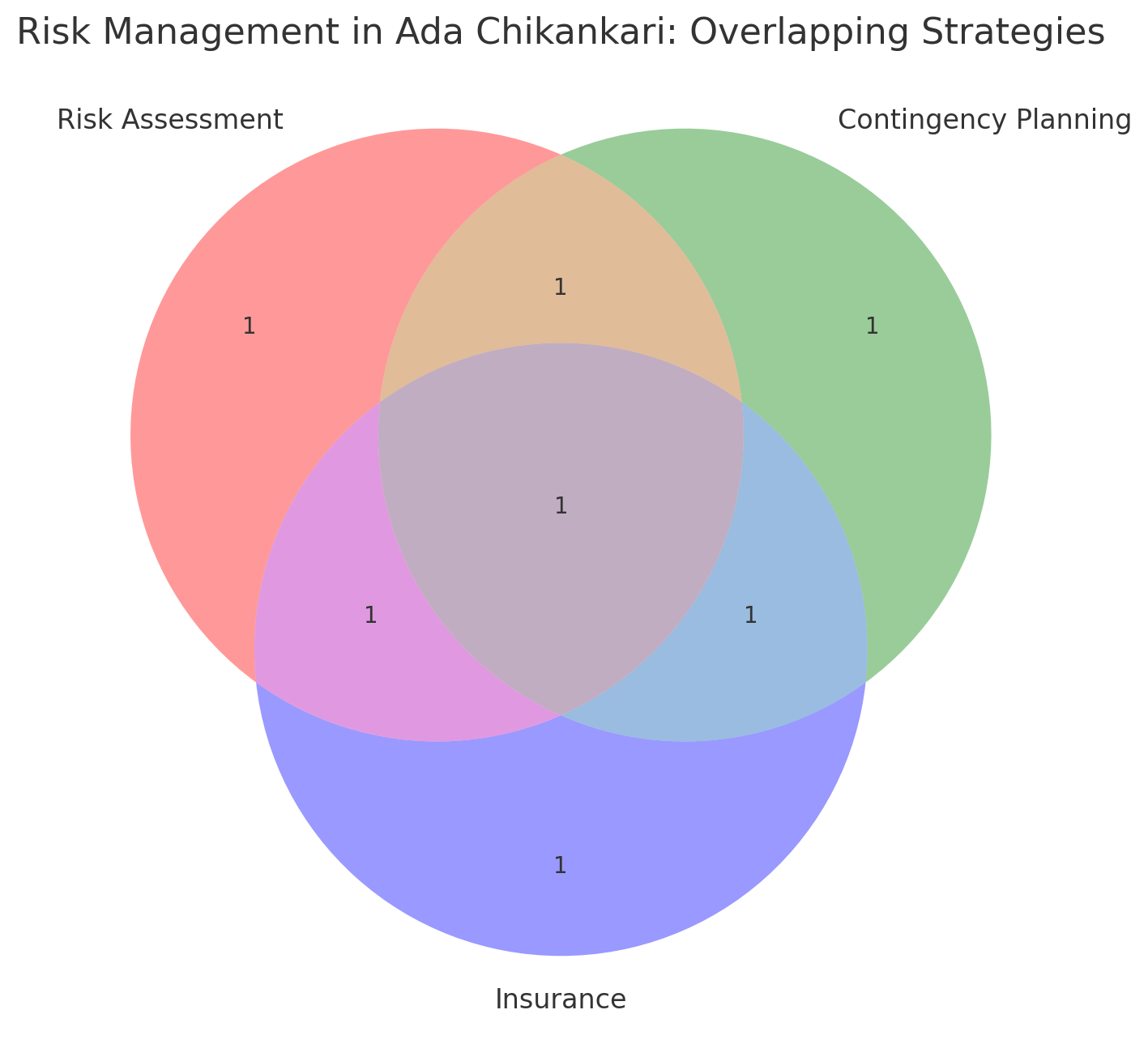
Conclusion: The Timeless Legacy of Chikankari
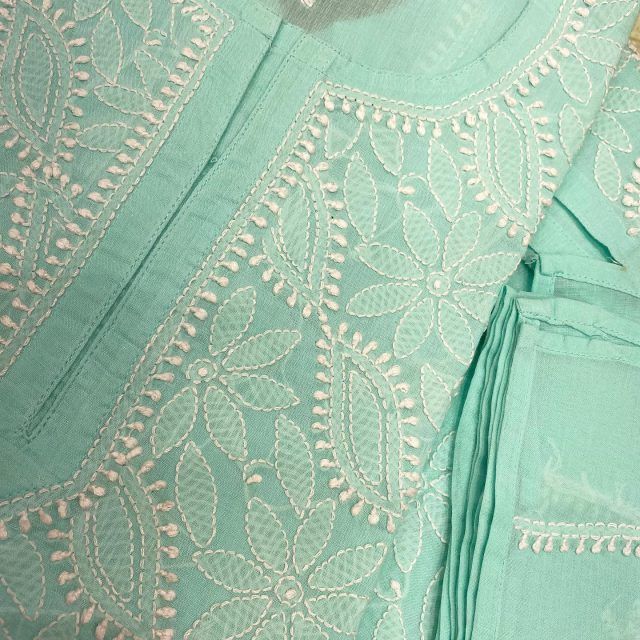
Chikankari is not just an embroidery technique but a living testament to the rich cultural heritage of Lucknow. This intricate art form, with its delicate stitching and exquisite designs, represents centuries of craftsmanship and dedication. From the initial stages of material sourcing and designing to the final touches of embroidery and finishing, each step in the Chikankari production process is a labor of love, requiring skill, precision, and patience.
Lucknow, with its historical grandeur and vibrant culture, provides the perfect backdrop for this timeless craft. The city's commitment to preserving and promoting traditional arts is evident in the meticulous processes followed by artisans to create Chikankari masterpieces. Organizations like Uttar Pradesh Vigyan Manch (UPVM) and IL&FS Skills play a crucial role in empowering artisans and ensuring the sustainability of Chikankari by providing training, advocacy, and market opportunities.
In a world where mass production often overshadows traditional craftsmanship, Chikankari stands out as a symbol of artistic excellence and cultural resilience. Each piece of Chikankari is not merely a garment or fabric; it is a story of heritage, artistry, and the unwavering spirit of the artisans who bring it to life. As we celebrate this exquisite art form, we also acknowledge the importance of supporting and preserving such crafts, ensuring that the legacy of Chikankari continues to enchant future generations.
(Source: By Rupsha Roy Choudhary: Ada- A charisma of chikankari; Uttar Pradesh Vigyan Manch; Indian Textiles & Crafts Repository)
Recommended
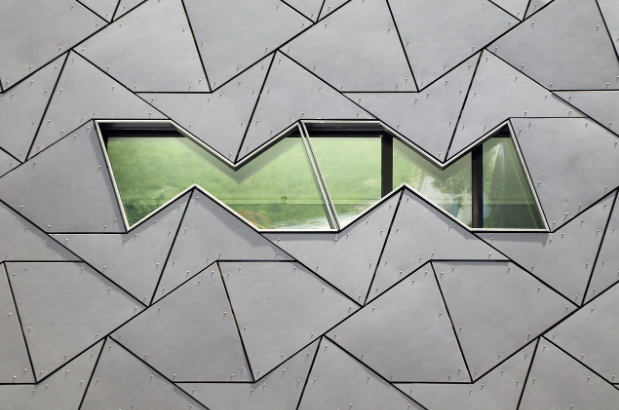

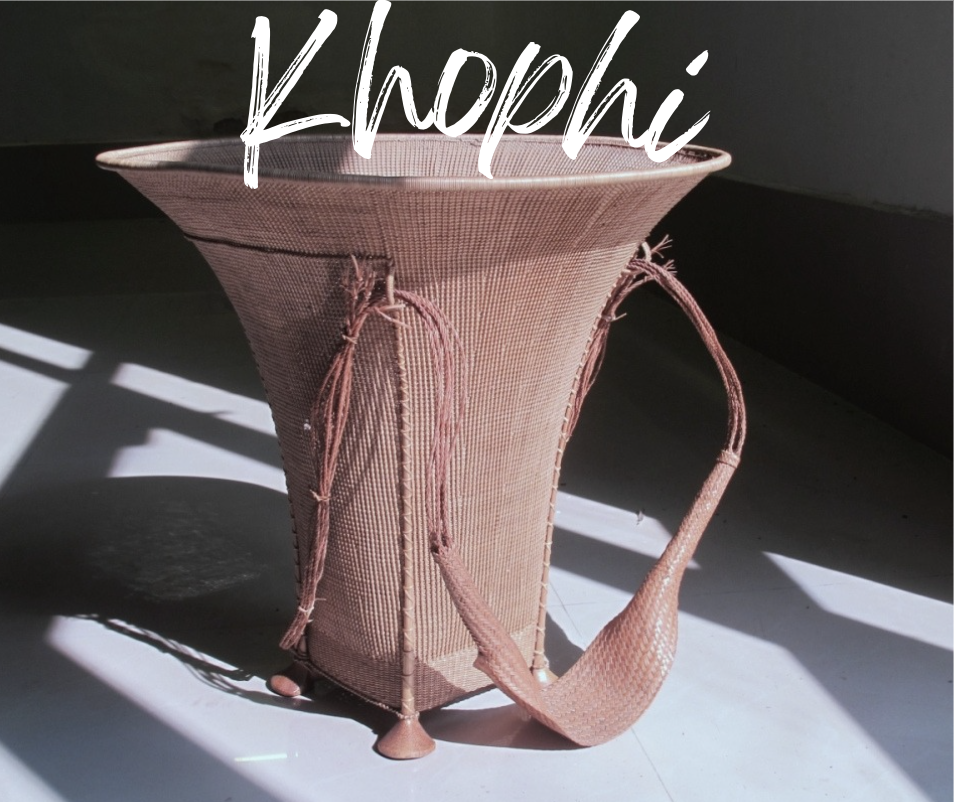