A Palette Woven On Threads: Unveiling The Art And Science Of Textile Dyeing
Jan 23, 2024 | Divya Salgiya
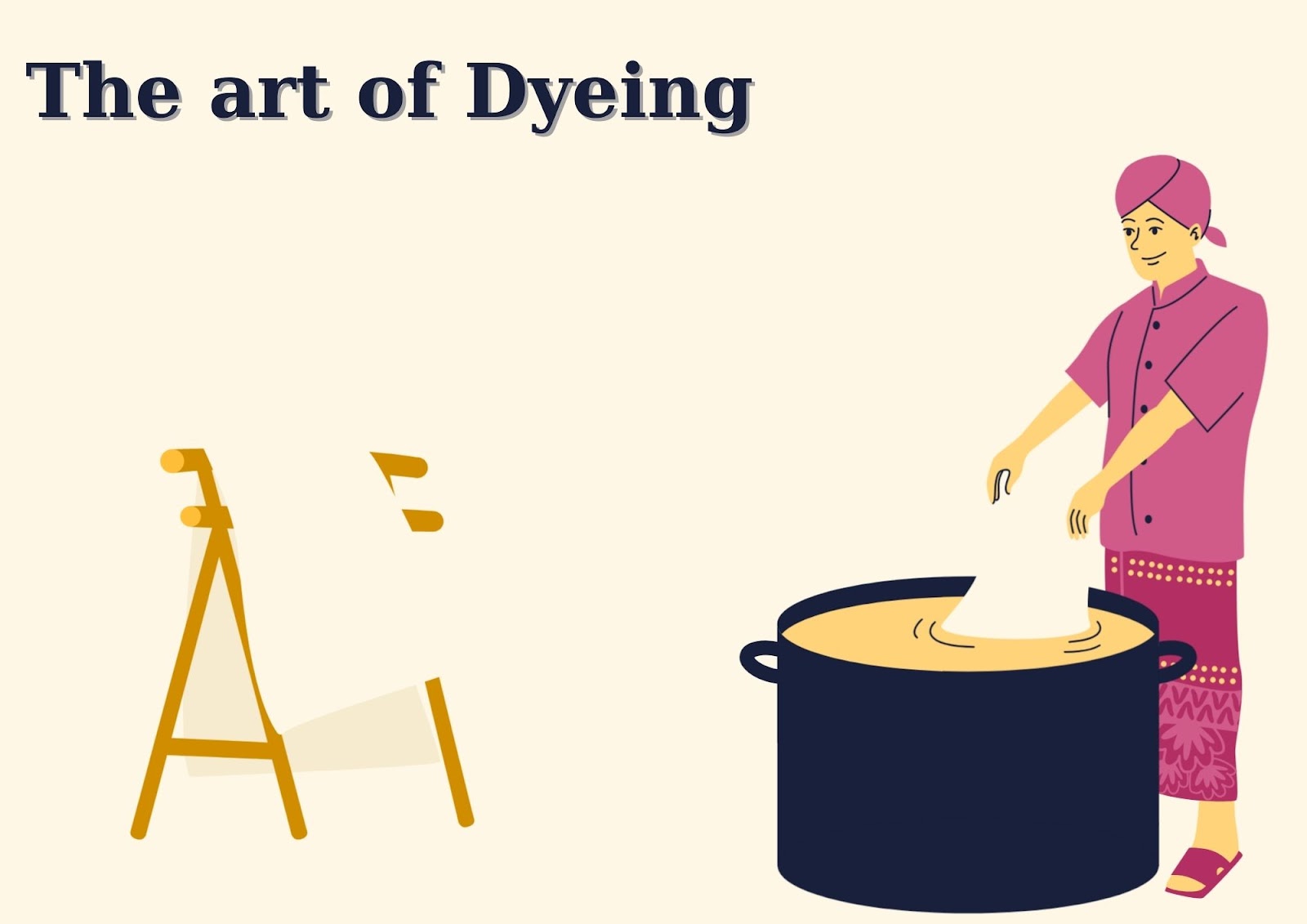
To Dye textiles in patterns we need four colors to start with
Blue
red
yellow
Brown
Blue is given us by indigo and woad, which do not differ in colour in the least, their chemical product being the same. Woad may be called northern indigo; and indigo tropical or sub-tropical woad.
Red is yielded by the insect dyes kermes, lac-dye, and cochineal, and by the vegetable dye madder. Of these, kermes is the king; brighter than madder and at once more permanent and more beautiful than cochineal.
Yellow dyes are chiefly given us by weld (sometimes called wild mignonette), quercitron bark (above mentioned), and old fustic, an American dye-wood. Of these weld is much the prettiest, and is the yellow silk dye par excellence, though it dyes wool well enough.
Brown is best got from the roots of the walnut tree, or in their default from the green husks of the nuts. This material is especially best for `saddening,' as the old dyers used to call it.
The Evolution of textile dye
Dyes have been in use for thousands of Years, the earliest documented use of dyes was as early as 15,000 BC when cave paintings using pigments such as black, white, yellow, and reddish pigments were used for cave paintings.
Archaeologists have discovered evidence of dyed textiles which date back to the New Stone Age, or Neolithic Period, which took place around 10200 BC. During an excavation in the Timna Valley in Isreal which took place throughout 2013-14, fragments of dyed wool were recovered. And linens found in the tombs of Ancient Egypt have also shown evidence of textile dyeing.
It is thought that textile dyeing become more prominent when the first true civilisations emerged and indeed flourished in the Middle East, Asia and Egypt. As civilisations grew, so did populations, and the desire to distinguish between gender and class, became more pronounced, natural dyes became widely used.
All textile dyeing done in ancient times, and right up until around the 1850s, was done with natural dyes, meaning they are derived from natural sources, such as insects or animals, plants or vegetables and minerals.
Animal Dyes – Animal dyes generally come from insects or shellfish, but lichens, a truly bizarre and complex organism, which is an organism made up of two separate organisms, a fungus and an algae which have a symbiotic relationship, can also be classified in this category,
Mineral Dyes – The earth holds a wide variety of minerals, sometimes found on the surface of the earth, and at other times found deep underground in mines. By scratching at the surface of any mineral-laden rock, and then mixing the resulting powder with oil or water, a dye is created.
Plant Dyes – The easiest to find and develop of all the natural dyes are those derived from plants and trees, with leaves, roots, and bark being used.
A Dye to Die For
Royal or Imperial purple was previously known as Tyrian purple, as it was derived from the sea snails in the Eastern Mediterranean, and it was the ancient city of Tyre that became synonymous with its manufacturing.
Producing a vivid, bright, and colourfast shade of purple, it quickly became the most expensive dye of the ancient world. Such was its demand, that Byzantine emperor Theodosius I declared that it was only to be used by the noble classes, anyone from the lower classes caught wearing purple ran the risk of being executed.
Dyes were widely used as a display of wealth and status, the rich and powerful could afford the bright hues and vivid colours, while the “working class” would generally be wearing greens, blacks or browns, the cheaper, more readily available shades.
Synthetic Dyes
Right up until the mid 19th century, when the first synthetic dyes were discovered, this shade of purple, and indeed almost all other bright hues remained highly sought after, and highly priced.
While picric acid, which produces a bright yellow when dyed with silk, was the first official synthetic dye, the man regarded by the industry to be responsible for the rise of synthetic dyes was William Henry Perkin.
While studying chemistry, in his quest to synthesis an anti-malarial drug, he accidentally created “Mauve” which quickly became a fashion phenomenon. The black residue left behind by his experiments on coal tar, when dissolved in methylated spirit created a purple solution, which could be used to dye textiles.
Suddenly, there was a demand for low cost, readily available and easy to apply dyes, which led to the creation of synthetic dyes as we know them today. There is no almost no colour that cannot be achieved with synthetic dyes, and this resulted in regular folk now having access to the colours that were previously beyond their reach.
Where there is a demand, there is almost always a supply. And commission dyers working out of dyehouses around the world filled that demand.
Through the years, as more and more research and investment went into the development of synthetic dyes, they became more sustainable and lessened the detrimental impacts on the environment.
Famous Traditional Dyes from Around the World
People have been wearing colours proudly for thousands of years. From social status to artistic statements, clothing colour has had a depth of meaning we probably don’t think about when we shift through the bursting racks of fast fashion chain stores. The synthetic dyes used to make most of our fabrics colourful now are poisoning waterways and causing serious health problems for workers around the world.
Before the invention of synthetic colours, clothing dyes were sourced from nature and applied through slowly cultivated traditional techniques – gentler on the environment, the makers and the wearers. So maybe it’s time we take a look around the world at some of the kinder ways to give our clothing that pop of colour we love.
Mali – Bogolan Mud Dyeing
‘Bogolan’ means ‘made from mud’ in Mali’s main language, Bambara. The base cloth is usually dyed deep reds or yellows by boiling bark and leaves. Then, using mud which has undergone a special fermentation process, distinct patterns are painted onto the fabric using sticks, brushes or reeds. The cloth then is soaked in natural solutions which bind the colour left behind by the mud to the fabric. Once dried, each piece of fabric becomes a totally unique work of art, in hues of red, brown, yellow, black and white, and patterns with a distinct regional aesthetic.
Japan – Shibori Dyeing
Indigo, the mesmerising deep blue that comes from the Indigofera tinctoria plant, has been called ‘the colour that changed the world’, and Japan is one place where the dye continues to hold a cherished place in the culture. The Shibori dyeing process was developed during a time when the Japanese lower classes were forbidden from wearing silk and brightly coloured clothing. The dark indigo colour, however, was allowed.
India – Ayurvedic Dyes (Ayurvastra)
The world has always admired the vivid colours of the Indian subcontinent. From art to architecture, to celebrations, and clothing, colour and design are central to the country’s fascinating culture and history. The ancient Indian practice of Ayurvedic medicine not only uses plants to aid health and cure illness, it can also be drawn upon to create clothing dyes that are good for both the wearers and the planet. The traditional methods of Ayurvastra (Ayur meaning health, vastra meaning clothing – literally ‘healthy clothing’) allow the colours from these plants to be applied to cloth 100% naturally, without the use of any toxic chemicals and causing no harm to animals or people.
The Monsoon Blooms’ dye house, set in the quiet forests of Kerala in Southern India have been dyeing fabric for tens of thousands of years, using techniques passed down through the generations. There are over 1200 medicinal plants grown at the dye house, and those used to dye and bleach Monsoon Blooms’ underwear include turmeric, aloe vera, and the treasured neem plant.
Scotland – Harris Tweeds
Scotland’s Harris tweed (think Grandma’s favourite checked tweed jacket), worn for its hardy warmth, is traditionally dyed using natural colours and ecologically friendly dye processes. The deep reds, purples and yellow checks of the Scottish kilt are created from lichens, a type of fungus, and the plant woad (another source of indigo) to create the blues. The colours themselves are intended to evoke the rich hues of the Scottish landscape.
Dyeing Process in Textile
Dyeing the fabric means transferring the color to the textile material (yarn or final fabric.) Scholars have found mention of the dyeing process of textiles as far back as 2600 BCE. Yes, fabric dye is such an old process. Primarily, the source of dye was nature. The dyes/colors were extracted from animals or plants. Since the mid-19th century, humans have started producing artificial dyes to get a broader range of colors and also to have more long-lasting ones.
Dyeing- The Imparting color
Dyeing is a process of imparting color to textile materials like fabrics, yarns, and fibers. It is an ancient art and has been used by humans for thousands of years. Dyes come in four forms- powders, pastes, crystals, and liquid dispersions. They all get completely dissolved in an aqueous solution like water. When the textile material is dipped into it, the dye molecules get fixed on the fibers. The dyeing process is all about absorption and diffusion. Absorption is the transferring of dyes from the aqueous solution onto the fabric surface and diffusion is the dyes getting diffused into the fibers. Of course, the temperature and other controlling factors play a major role. This dyeing can be either done by hand or machine. Also, different kinds of dyes are used for different types of fabrics.
For example, acid dyes are used to dye wool and silk, the basic dye is used for acrylic fabric, disperse dyes for polyester yarn, mulmul and cotton can be dyed with a variety of dyes like vat dyes, direct dyes, and modern synthetic reactive.
Nowadays tie and die has become the most popular trend among people. They love wearing tie and dye Indian ethnic wear, shirts, and dresses that look stunning and beautiful during the summer season.
Textile Pre-Treatment Process
Textile pre-treatment is an essential process that ensures the quality of the final textile product. The fabric dyeing process step by step that is done to prepare the raw material for further processing. This process of dyeing involves several steps, including singeing, de-sizing, sourcing, bleaching, mercerizing, and dyeing. Each of these steps plays a crucial role in the overall quality of the textile product.
Singeing and Desizing:
They are the first two steps of pre-treatment respectively. Singeing is done to remove the loose, hairy, and projecting fibers from the surface of the fabric. These fibers are often present in natural fibers, such as cotton and wool. They can make the fabric look uneven and reduce the quality of the final product. Desizing is done to remove the gummy materials over the fiber. These materials are often present in the form of starch or sizing agents used in the weaving process. This process makes the fabric softer, more pliable, and easier to work with.
Sourcing:
This is done to remove the impurities over the textile material. Sourcing is done to eliminate the impurities present in the raw material. These impurities can include dust, dirt, oil, or any other foreign particles that methods of dyeing may be present on the fabric. Sourcing is done by washing the fabric in hot water and soap or with the help of chemicals.
Bleaching:
In this step, the natural color of the raw materials is reduced. This step is done to prepare the fabric for dyeing or to achieve a specific shade of color. Bleaching is done with the help of chemicals or by exposure to sunlight. This process makes the fabric whiter and brighter, making it easier to dye and giving it a more appealing appearance.
Mercerizing:
It is an additional step and it is done to increase the strength and luster of the material. This process is done by treating the fabric with sodium hydroxide under tension. This process causes the fiber to swell and makes it stronger and more lustrous. It also improves the dye uptake of the fabric, making it easier to dye and giving it a more vibrant color.
Dyeing:
Here the material is dyed into another color. It is the last process of pre-treatment textile that sees the refined appearance of the fabric that has to be manufactured. Dyeing can be done with natural or synthetic dyes, depending on the desired outcome. It is a crucial step in the pre-treatment process, as it determines the final appearance and quality of the textile product.
Importance of natural dye over synthetic dye:
Natural dyes are biodegradable, non-toxic and non-allergenic. Provided they are processed in a way that avoids the use of harmful chemicals during the dyeing and finishing process, they have a much lower environmental impact than synthetic dyes.
Non-Toxic
The textile dyeing industry is one of the most chemically intensive on the planet and a major polluter of water. The majority of textile dyeing takes place in countries with minimal regulations and few safeguards over the amount of exposure workers have to toxic chemicals and how the waste from the dyeing process is disposed of. It’s estimated that 17-20% of industrial water pollution comes from textile dyeing with toxic runoff entering rivers before making its way to oceans and causing harm to marine life. Documentaries like RiverBlue have raised public awareness of the issues, showing us how, as rivers become polluted, the health of the people who use them is negatively affected and wildlife is endangered.
Synthetic dyes can also pose a direct risk to consumers. Certain dyes remain on the fabric, evaporating into the air we breathe or being absorbed by the skin. Contact with some chemicals can trigger allergic actions, cause skin irritation and rashes and there are also concerns regarding the carcinogenic properties of some dyes, although the most toxic ones, such as azo dyes, are now banned in the UK.
2. Therapeutic
As well as being kinder and safer for our skin and for our homes, natural dyes can help to create a relaxing and restorative environment. Colours created by natural dyes have an aesthetic that synthetic dyes simply can’t compete with. They are rich and complex. Many natural dye plants contain more than one type of dye compound, the proportions of which vary with the soil type and climate where they are grown. This provides a wealth of colour variation compared to synthetic dyes that are more uniform and flat. This subtle complexity is soothing to look at and has a calming effect on the viewer.
Natural colours are alive. They speak to their origins in the natural world with their depth and variation, the soft play of light and shadow and the organic patina that develops with older textiles over time as they are used and exposed to sunlight. Colours shift from dye bath to dye bath and from season to season with inconsistency and variations in colour forming part of their intrinsic beauty. Their subtle, aromatic scent helps to create a multi-sensory experience, an important facet of the biophilic design approach that aims to bring nature indoors and enhance our well-being through reconnection to the natural world. Humans have evolved in an environment saturated with natural colours, so we feel relaxed and at home with them.
3. Regenerative
Natural dyes have the potential to restore the environment and support sustainable rural industries. Dye crops can be grown regeneratively with by-products, such as organic compost and biofuel, increasing the range of useful outputs and providing environmentally sound alternatives to other products. Using natural dyes from trees such as myrobalan Terminalia cheruba, can help to preserve the biodiversity of native trees and increase the amount of permanent forest cover.
One of our favourite natural dyes is indigo, a blue dye that is extracted from the leaves of the Indigofera tinctoria plant. Indigofera’s sustainability credentials are second to none. It’s a very hardy crop and grows easily in various types of soil without the help of chemical inputs. As a legume, it’s a natural fertiliser, fixing nitrogen into the soil and is often used in crop rotations to revitalise soil fertility. In India and Bangladesh, where the indigo in our collections is produced, the stems of the plant are used as a biofuel after the dye material has been harvested.
Moving Towards Sustainable Techniques of Dyeing
The world population will be increased around 35 percent by 2050. As a result, the consumption of textiles will be increased. The increase in textile consumption will increase the use of water and energy, as well as the chemicals and total discharged wastes in the textile industry.
As we know the textile industry is one of the largest contributors to environmental threats globally. Cause its producing 60 billion kilograms of fabric annually and using up to 9 trillion gallons of water in textile dying and printing process. Evaluate the sustainable dyeing and finishing methods like: plasma, ultrasonic, laser, and supercritical carbon dioxide dyeing, which can enrich specific properties of fabrics without causing adverse effects on the environment.
Do you know that several aids have been provided by the sustainable textile dyeing and finishing process towards the consumption of natural resources and waste generation? Mainly, sustainable development focuses on the technological, cultural, social, and environmental aspects of the production of textiles.
It can be said that the textile industry faces numerous challenges during the process of dyeing and finishing. The sector comprises processes such as coloration and processing of units within the textile industry which is high in cost and demands harmful chemicals.
Basically, sustainability is a main element that stays as a prescription for several challenges faced by the industry during managing the usage of water, chemicals, and energy.
Conclusion
Dyeing can be complex and even cumbersome. Dyeing quality and performance are directly controlled by time, temperature, pH, and chemical auxiliaries. Dyes are fiber specific and have their individual advantages and disadvantages. They must be processed under careful control. What may be thought of as an insignificant variable can have a major impact on dyeing performance and dyed product quality. Dyeing equipment is designed for specific types of textile substrates and, in certain cases, specific dyeing conditions.
The goal of dyeing is to produce the highest quality on-shade product which meets all of the customer's specification for colorfastness and color durability. This dyed product should be produced in the shortest amount of time, using the least amount of energy, generating minimum water waste. This produces the most profit for the manufacturer and the highest quality product for the customer.
Recommended
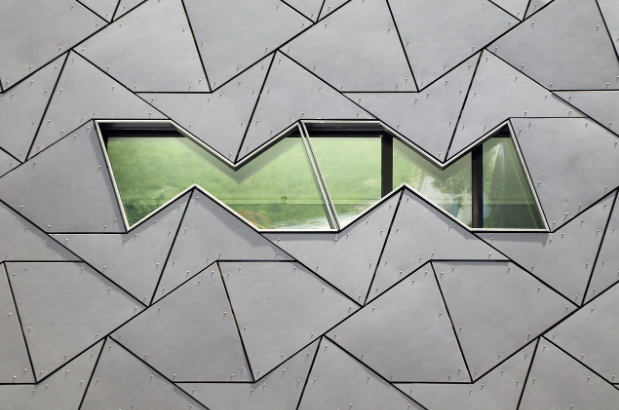

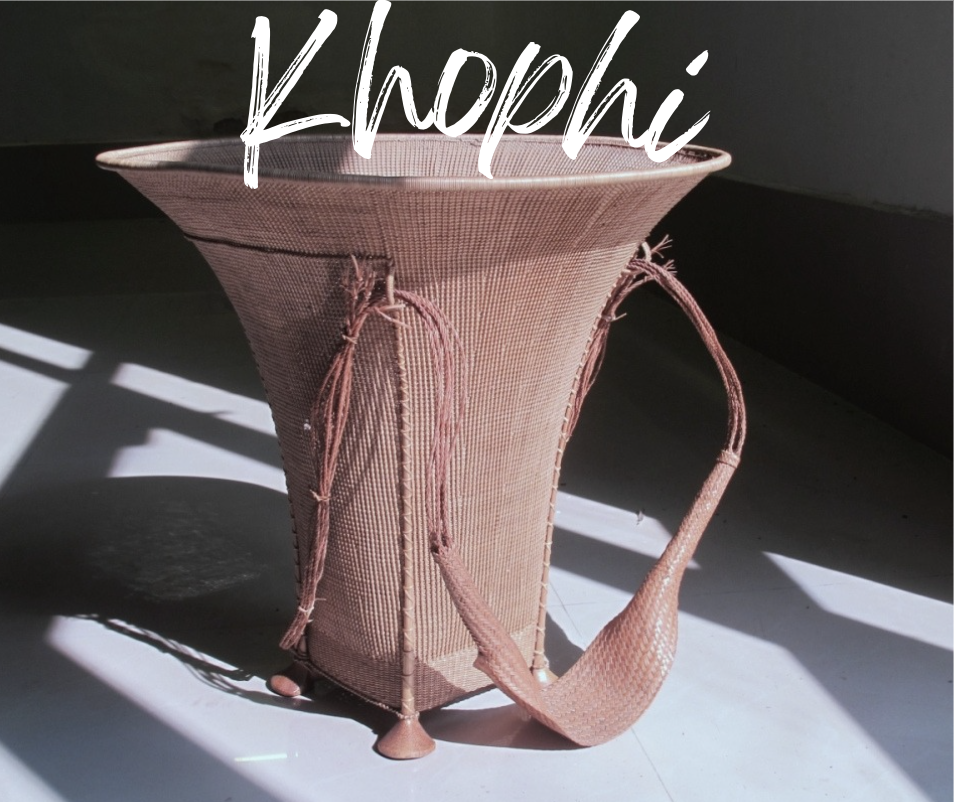