Woven Through Time: Unveiling The Rich Tapestry Of European Textiles
Jan 23, 2024 | Divya Salgiya
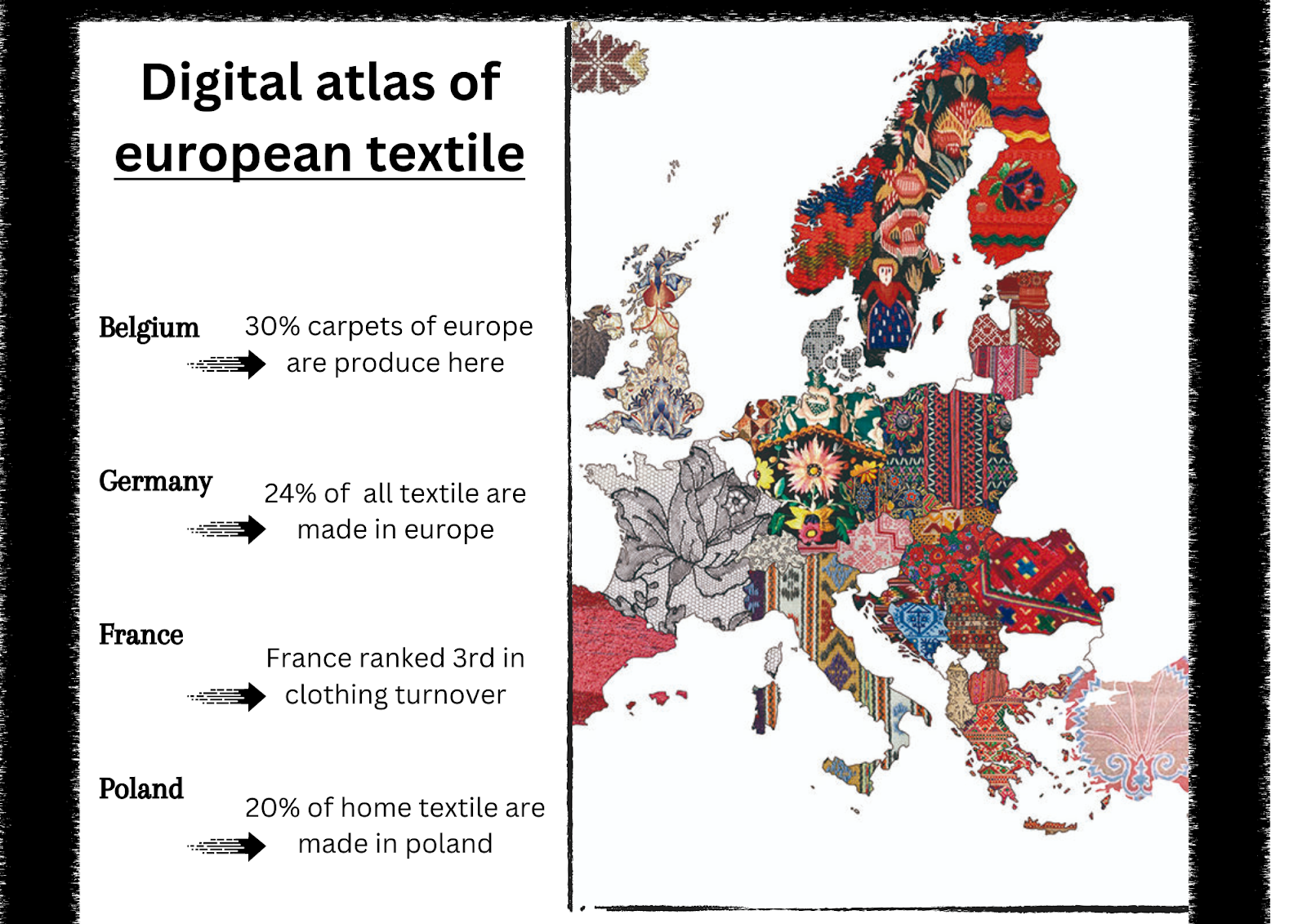
History of Textiles in Europe
The earliest clothing dates back to the Pleistocene prehistoric era, when the earliest hominid, Homo Heidel bergensis, wore the earliest clothing. Scholars believe primitive clothing dates back 100,000 to 50,000 years. Sewing needles date from 50,000 to 60,000 years ago around modern Siberia, South Africa, Slovenia, Russia, China, Spain, and France. Some of the oldest dyed fibers have been found in caves in Georgia dating back 30,000 years. Other textile artifacts, such as net gauges, spindle needles, and weaving sticks, were found in ancient civilizations dating back to the Common Era 5000 years ago.
Cloth and textiles became common in the ancient world. In particular, ancient civilizations in India, Egypt, China, sub-Saharan Africa, Eurasia, South America, and North and East Africa all had some form of textile Production. Until the middle Ages, its two main types were known as the warp-weighted loom and the two-beam loom. These consisted of broad lengths of cloth beams with a cloth woven over them. In two-beam looms the full width of the loom is dropped or tied in place. The Bronze Age saw the rise of clothing production in India and the ancient Near East (around the present-day Middle East). Europeans used the famous Silk Road trade route that spread textile knowledge and materials from China to Egypt and then to Rome. The Iron Age proved to be an effective transitional period in the Middle Ages. Leather belts, woven woolen tunics and skirts, breeches, and robes were common attire. Leather shoes protect feet from the elements.
2024 Is A Turning Point For The European Textiles And Cloting Industry
From June 6 to 9, 2024, Europe will hold crucial elections for the European Parliament, and based on the results, a new European Commission will be formed. In light of this pivotal election, EURATEX publishes a Manifesto, presenting fifteen requests aimed at ensuring the competitiveness of the European textiles and clothing industry.
The textile and apparel industry is making a substantial contribution to European wealth, jobs and growth. Europe counts 192,000 companies employing 1.3 million workers with a turnover of €167 billion and over €67 billion of exports. Entrepreneurship should be recognised as the foundation for a competitive textile industry, offering high quality and sustainable products, based on innovation, creativity and design. European policy makers should recognise such role to textiles and apparel companies and have an open dialogue to create better framework conditions to operate in the internal and global markets.
To realize that vision, the industry and policy makers need to work together on a mix of policy measures and initiatives, which are coherent and offer a transparent and predictable framework for our companies, and make them more resilient and competitive.
These policies should focus around 3 points:
1.Develop and implement a “smart” EU industrial policy
Europe should create policies which enhance competitiveness. The EU textile industry currently employees 1,3 million people, 30% of which is above 50 years old. A critical bottleneck for the textile industry is to attract (young) people and make sure these people have the right set of skills, to operate in a changing textile ecosystem. EURATEX also asks the EU to invest in innovation and digitalisation as they are key to the European competitive advantage. Not only, as the last years have proved, Europe should provide companies with access to sustainable energy at lower prices.
2.No sustainability without competitiveness
The EU Strategy for Sustainable Textiles is pushing our sector towards new business models with a lower environmental footprint. This set of new regulations needs to be coherent, enforceable, feasible and applicable for SMEs, and not push textile companies out of the market. Moreover, some member states are moving forward faster and some legislations will be decided at national level, creating fragmentation of the market. Such scenarios will hamper Europe and its possibilities to grow.
3.Incentivise the Demand for sustainable textiles
To create a demand and help consumers to buy a (genuine) sustainable textile product, there should be standard requirements and fiscal incentives. Public authorities should also implement green public procurements, by increasing the importance of sustainability criteria in their evaluation grids.
Types of Weaving
Weaving has several patterns, which help produce different materials and effects. Sometimes, a singular weave pattern will be used to create a single weave unit, while other weaves require the compilation of several combined techniques to create one unit. Weave patterns range from simple to very intricate.
Plain Weave
A plain weave also called a tabby weave, is the mostasic of all weaving patterns. Like any weaving, you must have a warp wire and a weft wire. The amount of wires and the ratio between wires helps to create intricate patterns. This process is true with all weaves, including the plain weave. The plain weave type only requires two weft yarns in each weave unit, making it simple yet durable.
To create this pattern, two warp yarn pieces are held parallel to one another. The crosswise weft yarn is then run perpendicular, going over and under the warp yarns. This process creates a boxed, square shape of one weaving unit
. To complete this weave, the warp yarn and weft yarn should be of equal size. When different sized threads are used for the warp and the weft wires, you end up with popular fabric options like poplin and taffeta.
One of the most common types of the plain weave style that we see every day is our fabric used for clothing. Another common use of this weave style is used in a tapestry weave. To make a tapestry, artists use a special tapestry loom that creates a plain weave, repeated over and over again.
Twill weave
A twill weave pattern is defined by diagonal lines, compared to the plain weave’s straight lines. The twill weave is made by using one weft yarn and two warp yarns. The weft yarn is crossed over and then under the weft yarn, creating a diagonal pattern. The style of the twill weave can be changed by changing the ratio between warp and weft yarns.
As long as the yarn keeps a 2:1 ratio, such as a 6:3 configuration, the artisan will create a twill weave pattern. Changing the direction of the weave in a twill weave pattern can introduce a herringbone pattern, also desirable for several types of fabrics.
Basket Weave
A basketweave pattern can easily be made with any weaving loom. This is a variation of the plain weave. A basket weave creates a square weaving pattern with an even number of weft thread and warp thread pieces.The two threads will run perpendicular to each other, first crossing over and then under one another. A basket weave differs from a plain weave by allowing for multiple strands of yarn or thread. This differentiator can allow you to create a plain weave with three, four, or more weft and warp yarns to make a thick and sturdy weave structure.
Dutch Weave
A Dutch weave can be used for fabrics or metals and is highly prized for its durability and strength. A Dutch weave requires the pattern to have a limited amount of warp wires, with a maximum amount of weft wires. This structure creates an elongated plain weave pattern. The long stitch makes a very strong and durable fabric that can withstand high pressures and can resist tearing.
Jacquard weave
A jacquard weave is an incredibly intricate weave that is commonly used to produce damask and satin. This weave can be made using a jacquard loom attachment, which is a specialty item. A jacquard weave allows the artisan to include different full-image figures into the pattern of the material.
To do this, the artisan must make individual loom cards, which have the colors and weaving textures necessary to create the desired design or figure. The loom cards require the artisan to stop and reconfigure the loom, making this an incredibly lengthy process. For this reason, the cost of a jacquard weave fabric is usually very high. A jacquard weave usually combines several weave techniques to add to the complexity and difficulty of producing the fabric.
Diverse weaving technique of Europe
Weaving is a process in which two separate sets of threads are woven at right angles to each other to form a fabric. The vertical threads are called the warp and the horizontal threads are the weft. The way in which the warp and weft threads criss-cross is called the weave.
The majority of products woven today are made in one of the three most common weaves: plain weave, satin, or twill.
The woven fabric can be plain (one colour all over), or can be woven with decorative or artistic patterns. The variety of weaves and the possibility of mixing silk yarn with other fibres (e.g. wool or cotton) means that there is no limit to the fabrics that can be created, giving an infinite number of textures, flows, falls, colours and patterns.
In 18th-century Europe, weavers worked on increasingly complex hand looms. In France, the inventions of Basile Bouchon, Jean-Baptiste Falcon and Jacques Vaucanson were important milestones in the improvement of looms. Then, in 1801, weaving underwent a decisive technical revolution with the invention of the Jacquard loom by Joseph Marie Jacquard in Lyon..
The Jacquard loom is made up of two parts: the draw loom, which is used to produce decorated (figured) fabrics, and the Jacquard mechanism, which sits on top of the draw loom.
Basile Bouchon’s needles, an adaptation of the clock mechanism to weaving, used to read a perforated tape (1725);
Jean-Baptiste Falcon’s system of perforated pasteboard cards and an infinite chain of cards, which enabled non-stop control of the loom (1728)
Vaucanson’s loom, which was automated by a hydraulic system and operated by analogue cylinders (1748).
The result was a semi-automatic loom with a square cylinder that controls all the threads – via 600 to 800 hooks – and selects them using a programme written on punched cards, to create varied and complicated patterns.
Its main advantage was that it could be operated by a single person. After a few improvements by the mechanic Jean-Antoine Breton, the Jacquard loom enabled faster and much cheaper production than on previous looms.
Despite initial reluctance on the part of the workers, who saw it as a threat to their jobs, people soon realised the benefits of the Jacquard loom: it made work easier and improved the quality of production.
In 1834, there were 2,885 looms operating on the slopes of the Croix-Rousse in Lyon. By the end of the 19th century, there were almost 20,000 ! The Croix-Rousse silk manufacturers began to specialise in fabrics with complex patterns, including brocade, damask and panne velvet.
Challenges in the European Textile and Clothing Industry:
The European textile and clothing industry is one of the world’s most difficult makets to enter. The EU has very strict legal requirements and it is necessary to meet all the non-legal requirements of European businesses to enter. These non-legal requirements are customer-specific; you can usually read up on them in the suppliers’ manual provided by your buyer. Market entry is getting easier to large numbers of suppliers that are offering more or less the same in terms of speed, price, flexibility and quality, for buyers it is getting easier and cheaper to switch from one supplier to another.
Finding new suppliers fulfilling Corporate Social Responsibility (CSR) requirements and expectations in Europe are getting tougher and are one of the major challenges that buyers are facing nowadays. Some European manufacturers have started to compete with suppliers from developing countries and have built up competitive advantages, such as quality and design, higher flexibility, higher productivity, shorter lead times and innovation. As a result, the production of high-end, ultra-fashionable clothes more and more likely to remain in or near Europe, in countries like Portugal, Spain, Italy and Turkey.
Opportunities in the European Textile and Clothing Industry:
In the European Textile and Clothing Industry technology is changing the techniques of new production, the possibilities of scanning sizes, faster communication. In this fast fashion era, labour-intensive production will likely make way for capital-intensive production, dominated by new technology and robotics. The EU industry will see near sourcing as a major time-saving opportunity. For slow fashion, labour-intensity endures a leading factor: in this segment, most European buyers will prefer far-shore sourcing.
China is slumping down on polluters, pushing many garment factories to shut down; it is a great opportunity for Europe. Due to this many international textile buyers are frequently shifting away from China. With this China’s textiles sector faces escalating costs of inputs such as cotton and wool, costlier environmental rules and massive import taxes for basic manufacturing equipment. Demand is growing faster in the European countries and Europe’s economic rebound is causing new markets to develop.
European famous wall tapestries: a unique choice for home decor
For centuries many different cultures have used tapestries and textiles to decorate their buildings, churches, and homes. Today that trend has continued.
Traditional tapestry wall hangings, particularly those from Medieval times, were produced from wool. This provided a strong fabric for applying many dyes and pigments as well as the added durability and maintenance. Wool tapestries when mixed with synthetic polymers have the distinct advantage of preserving the traditional warmth of standard wool tapestries. The basic use of natural materials has remained a staple with tapestry weaving, even with present day weavers.
Belgian and French Tapestries
The method of weaving Belgian and French tapestries gives them a different perspective of colors from different angles and lighting conditions. Belgian and French tapestries became well know works of art during medieval times. These tapestries are woven using a large variety of fabrics, such as: wool, silk, cotton, linen, and acrylic. The gold, silver and silk threads are what give them a wider range in colors, allowing tapestries to become the finest tapestries in the world. The nobility of the medieval and renaissance periods wanted to have the finest representations of their lives for others to view.
The Lady and the Unicorn
The Cluny Museum in Paris, also known as the National Museum of Medieval Arts, is home to many examples of magnificent medieval tapestries, including the famous Lady and the Unicorn Tapestries a set of six tapestries create in the Middle Ages and known world wide for their beauty. The Cluny Museum is also home to tapestries and weavings from many different countries including Iran, Egypt, Italy, Spain, and Great Britain. There are a variety of different decoration styles as well as production types and while all of the Museums tapestries are beautiful, the Lady and the Unicorn series is by far the most popular.
Recommended
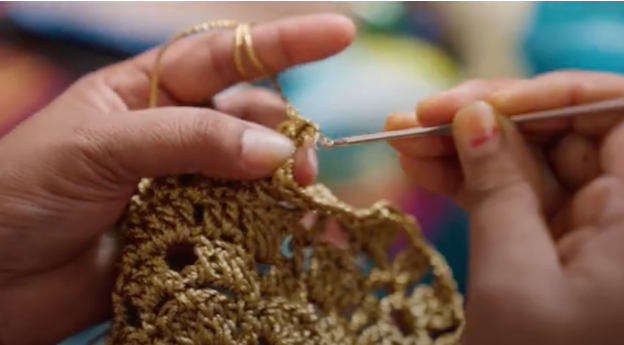
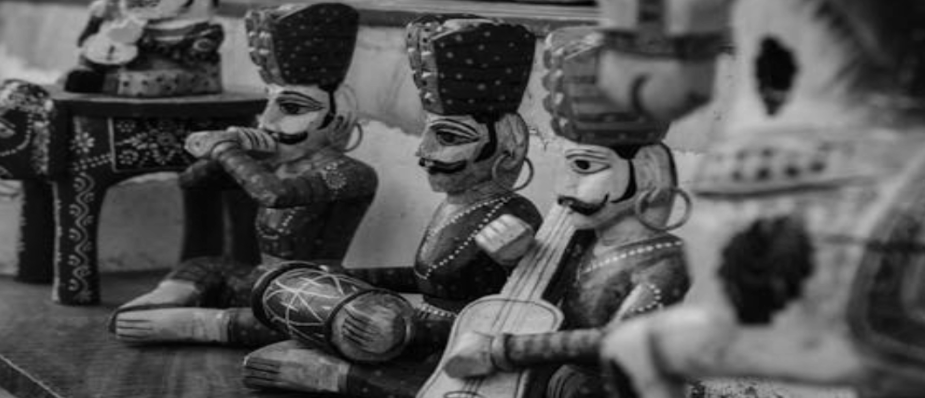
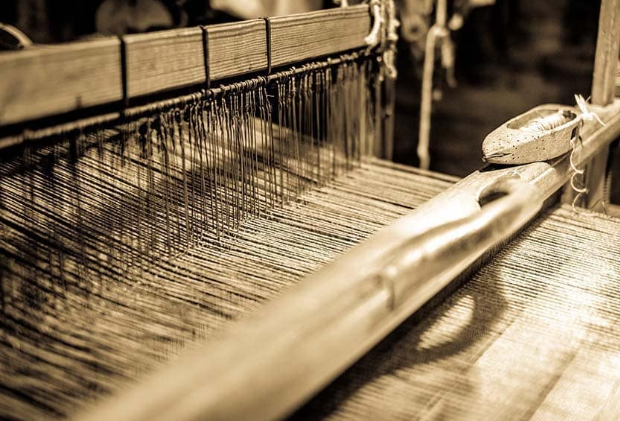