The Tradition Of Kanghi Making In Himachal's Weaving Culture
Sep 13, 2024 | Udit Kaur
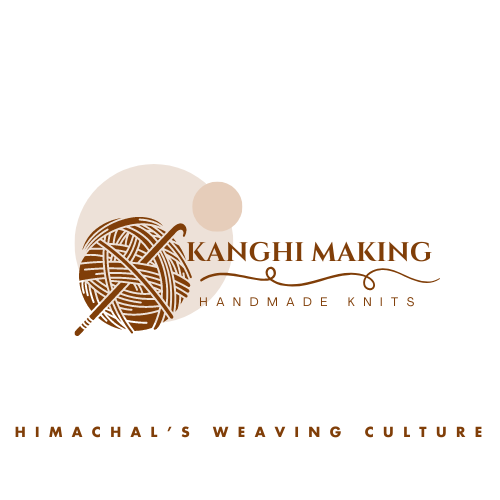
Tourism is a cornerstone of the state's economy, drawing visitors from across the globe who are eager to experience its natural splendor and historical temples. In addition to tourism, agriculture and hydroelectric power also play significant roles in sustaining the region. However, beyond these modern industries lies a world of traditional crafts that have been nurtured for centuries, contributing to both the cultural and economic landscape of Himachal Pradesh.
Among the state's many handicrafts—such as the Kullu shawls, Chamba rumals, and Kangra paintings—one of the most fascinating and lesser-known is the making of the Kanghi. This traditional craft is integral to the weaving process in the region, particularly in the creation of textiles that have become synonymous with Himachal Pradesh.
2. The Loom and its Importance in Kanghi Making
Weaving has long been a part of the Himachali way of life, especially in the colder months when the region's inhabitants retreat indoors. Almost every household owns a pit-loom, a testament to the integral role that weaving plays in daily life. Weaving is not just a means of creating beautiful textiles; it is a craft deeply embedded in the cultural and spiritual fabric of the state. Wool, considered pure, is often used in rituals, and the most famous woven product, the Kullu shawl, is celebrated for its vibrant colors and intricate patterns.
Central to the weaving process is the loom, a device that holds the warp threads under tension, facilitating the interweaving of weft threads to create fabric. The loom, with its various components, is a marvel of simplicity and functionality. One of the critical parts of the loom is the reed, locally known as the "Kanghi." Resembling a comb, the Kanghi serves multiple purposes: it pushes the weft yarn securely into place, separates the warp threads, keeps them untangled, and guides the shuttle as it moves across the loom.
Modern reeds are typically made from flattened strips of wire bound together with tarred string, but traditionally, reeds were crafted from cane. In Kullu, a town renowned for its shawls, the art of making traditional Kanghi is still alive, thanks to artisans like Mr. Bhime Ram, whose family has been involved in this craft for three generations. The making of Kanghi is a meticulous process that requires skill, patience, and a deep understanding of the materials and tools involved.
3. Tools and Raw Materials used in Kanghi Making
The making of Kanghi is a craft that relies on simple yet essential tools and raw materials, each serving a specific purpose in the creation of this vital loom component. The tools and materials used include:
Cane Strips: These are the primary material used in making Kanghi. The cane strips hold the wooden ribs in place, providing the structure necessary for the reed.
Twisted Yarn: Used to tie the ribs together, the twisted yarn not only secures the structure but also creates space between the dents through which the warp threads pass.
Hacksaw: Hacksaw is essential for cutting the cane to the required length, ensuring that it can accommodate the necessary number of reeds.
Sickle: The sickle is used to split the cane into strips. This process requires precision, as the cane needs to be evenly split to maintain uniformity in the reed.
Metal Strip: This is used during the assembly process to tap on the ribs, reducing the space between them and ensuring a tight, secure fit.
Colored Threads: These threads are used not just for decoration but also to add an additional layer of security when tying the ribs together, enhancing both the functionality and aesthetic appeal of the Kanghi.
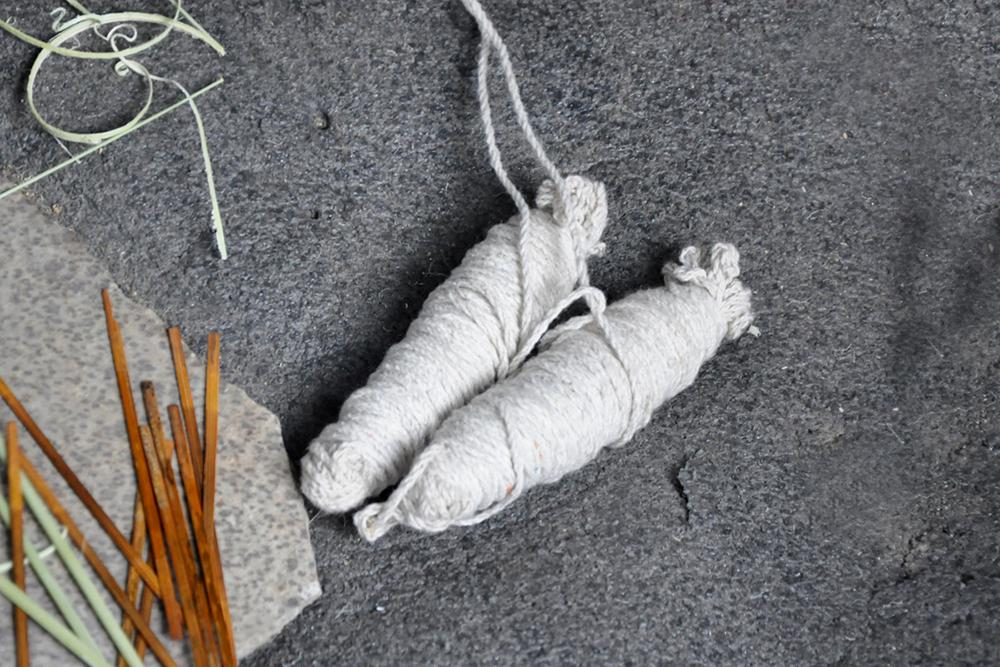
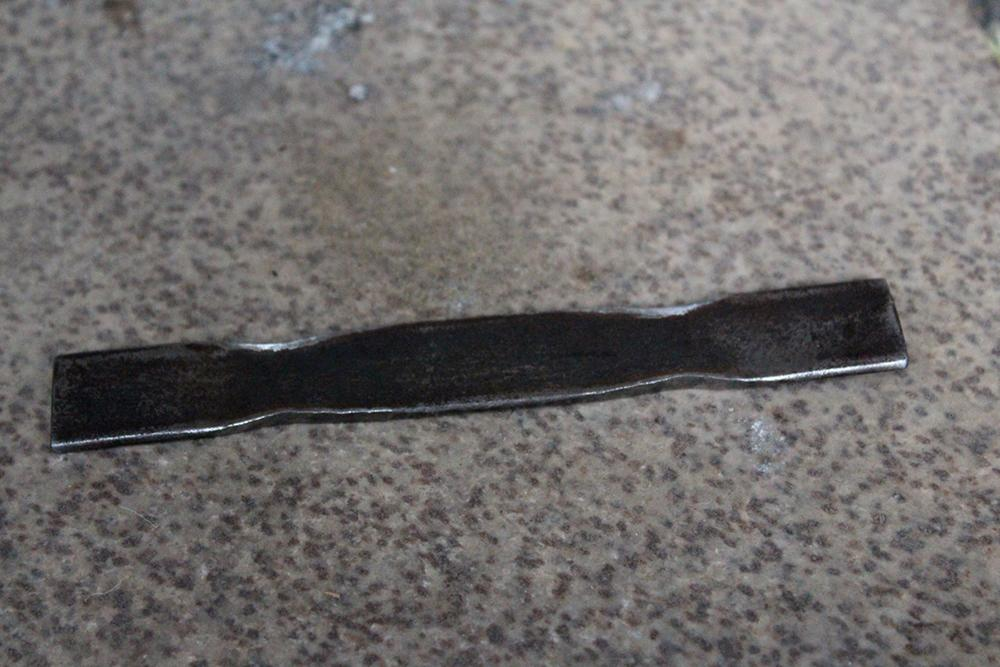
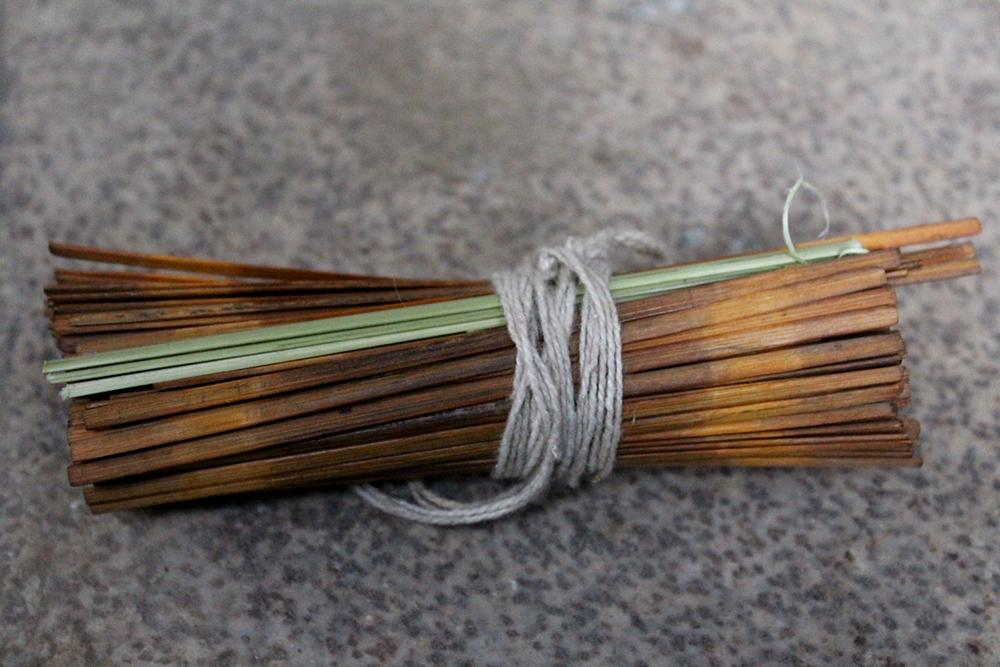
4. The Making Process of Kanghi
The making of Kanghi is a step-by-step process that combines traditional knowledge with careful craftsmanship. The process begins with the preparation of the cane, which is the primary material for the reed.
Cutting the Cane: The first step involves cutting the cane to the required length using a hacksaw. The length is determined by the number of reeds that need to be accommodated, typically around 200 to 250 reeds along the length of the cane.
Splitting the Cane: Once the cane is cut to size, it is split exactly in the center using a hand-held sickle. The artisan must ensure that the split is clean and even, as this will affect the final product's quality. Two pieces of cane of equal length are then split into two, resulting in four pieces.
Preparing the Ribs: The next step involves preparing the ribs that will act as the dents in the reed. These ribs are small strips of wood placed between the split canes, creating space for the warp threads to pass through. The ribs are carefully measured and cut to the required size using a template to ensure uniformity.
Assembling the Reed: The ribs are placed between the split canes, with twisted yarn used to secure them in place. The yarn not only holds the structure together but also acts as a spacer between the dents. The artisan must ensure that the spacing is consistent, as this will directly impact the weaving process.
Tightening the Structure: Once the ribs are in place, the artisan uses a metal strip to tap on the ribs, reducing the gap between them. This step is crucial in ensuring that the reed is tight and secure, with no loose components.
Final Touches: The final step involves tying the split ends of the cane together and securing them in place. Colored threads are often used in this step, adding a decorative element to the reed. The finished Kanghi is a testament to the artisan's skill and dedication, a vital tool that will be used in the weaving process to create beautiful textiles.
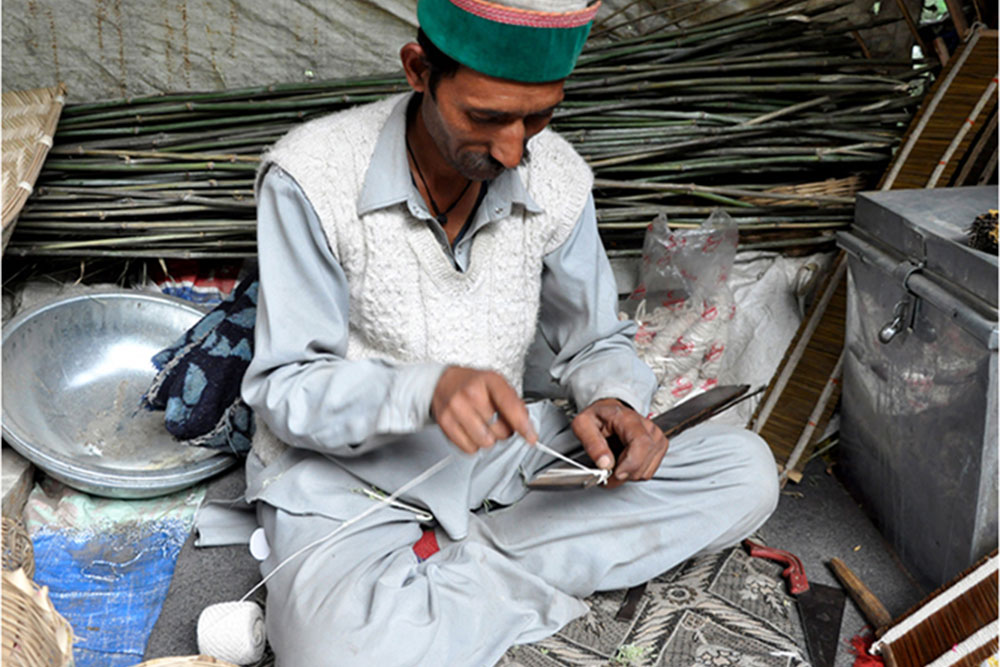
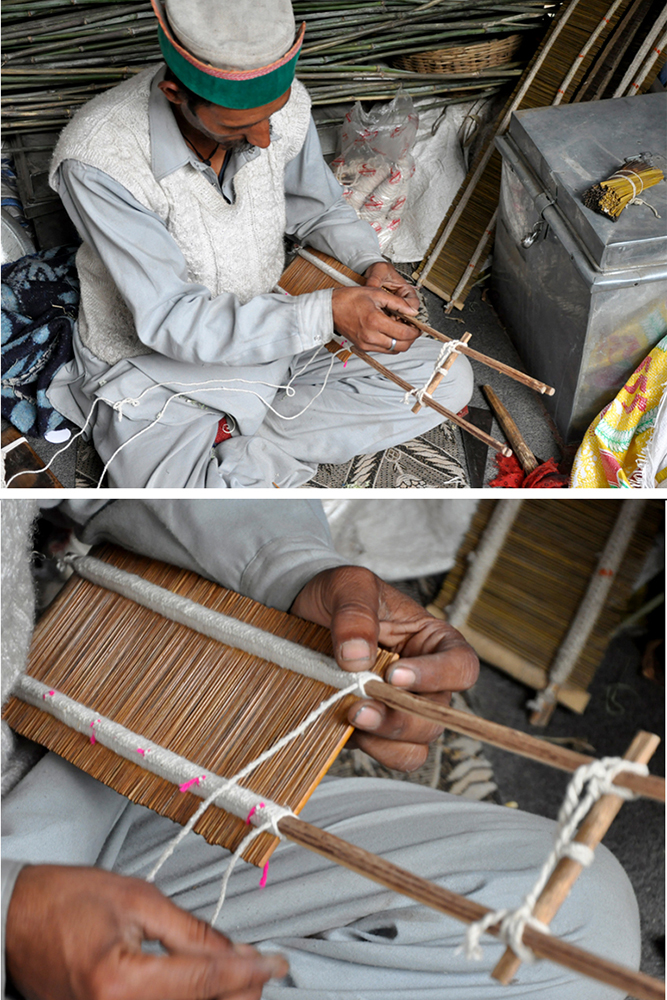
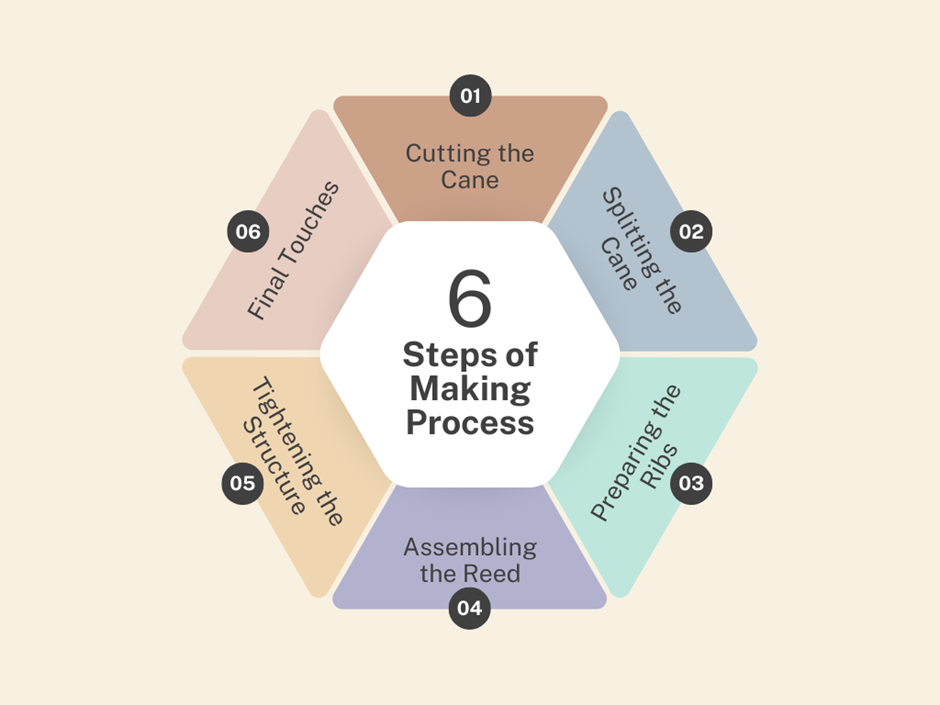
5. Cultural Significance and Contemporary Relevance of Kanghi Making in Himachal Pradesh
The making of Kanghi is not just a craft; it is a tradition that has been passed down through generations. In the cold winters of Himachal Pradesh, when the snow blankets the landscape and life slows down, the loom becomes a center of activity in many households. Weaving is a communal activity, bringing together families and communities, and the Kanghi is an essential tool in this process.
In today's world, where mass-produced goods often overshadow traditional crafts, the making of Kanghi remains a symbol of Himachal Pradesh's rich cultural heritage. Artisans like Mr. Bhime Ram are keepers of this tradition, ensuring that the knowledge and skills required for this craft are not lost. The Kanghi represents more than just a component of the loom; it embodies the history, culture, and resilience of the people of Himachal Pradesh.
With the growing interest in sustainable and handmade products, there is a renewed appreciation for traditional crafts like the making of Kanghi. As consumers seek out products with a story, rooted in tradition and crafted with care, the demand for handmade textiles and the tools used to create them is on the rise. This has provided artisans with new opportunities to showcase their skills and connect with a global audience.
Here you can have a look on the video showing Kanghi making.
6. Ensuring Top-Notch Quality in Making Kanghi
Kanghi making is an artisan craft where quality is paramount. The process begins with the selection of superior raw materials, ensuring that each Kanghi is durable and capable of withstanding the rigors of the weaving process. The artisans' meticulous attention to detail ensures that every piece meets high standards, incorporating traditional craftsmanship techniques that have been passed down through generations. Quality control is rigorously maintained at each stage, from material selection to the final product, ensuring that these handmade products are nothing short of premium.
Material Selection: Only the best raw materials, such as durable woods and strong fibers, are chosen.
Craftsmanship: Artisans employ traditional techniques, ensuring each Kanghi is crafted to perfection.
Quality Control: A rigorous inspection process is in place to maintain premium quality, ensuring that every Kanghi meets the high expectations of customers.
This dedication to quality ensures that Kanghi remains a premium product, synonymous with durability and craftsmanship.
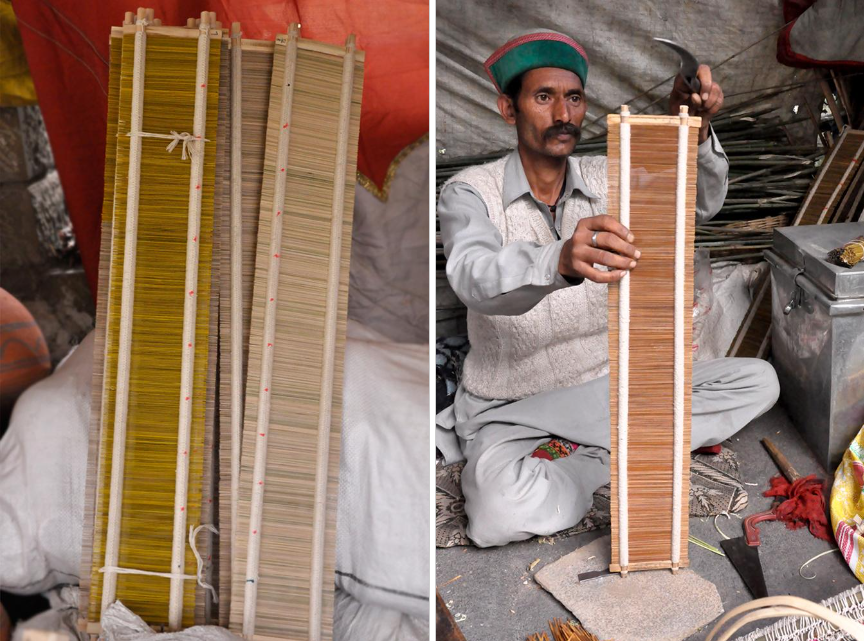
7. The Art of Crafting Uniqueness in Kanghi Crafts That Stand Out
Each Kanghi is a unique piece of art, often created in limited editions. The designs reflect the cultural essence of Himachal Pradesh, with the possibility of customization to meet specific client needs. This uniqueness is not just in design but also in the materials and the personalized touch that each artisan brings to the craft. Customization options allow buyers to request specific designs or features, ensuring that the final product is not only functional but also a reflection of individual style.
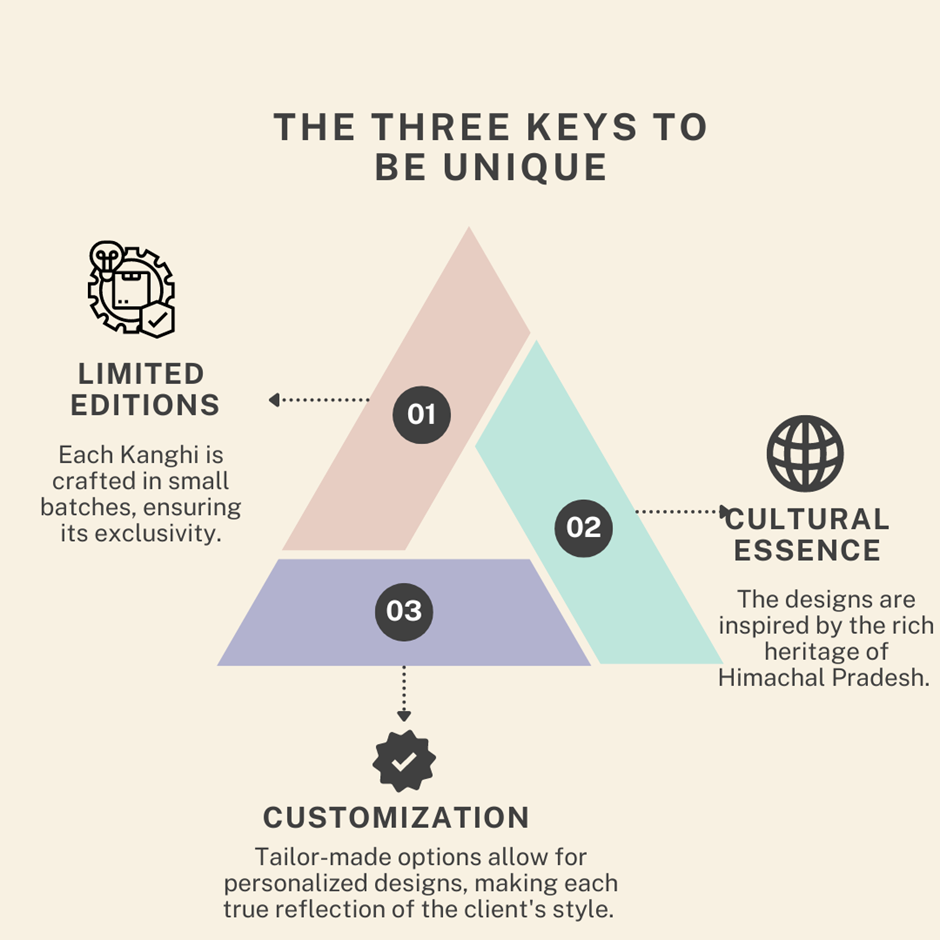
8. Sustainable and Ethical Sourcing of Raw Materials for making Kanghi
Sustainability is a core principle in Kanghi making. The raw materials used are often sourced through eco-friendly practices, ensuring that the environmental impact is minimal. Artisans and suppliers work closely to ensure that materials are ethically sourced, promoting sustainable practices that benefit both the environment and the local economy. This commitment to sustainability extends to every aspect of production, from the materials used to the techniques employed in crafting the Kanghi.
How does this benefit the product- Kanghi?
It results in a Kanghi that is not only high-quality but also aligns with values of sustainability and ethical consumption. This benefit enhances the product in several ways:
Long-Lasting Value: The durability of the Kanghi means that it can be used for years without needing replacement, offering long-term value to the customer. This reduces the frequency of repurchasing, which is particularly important in today's economy where consumers are looking for products that provide lasting quality.
Sustainability: By creating a product that lasts, the Kanghi contributes to sustainability by reducing waste. Consumers are increasingly aware of the environmental impact of disposable goods, and a durable Kanghi aligns with the growing demand for sustainable products. This positions the Kanghi as a responsible choice for eco-conscious buyers.
Ethical Consumption: High-quality, durable products often require careful sourcing of materials and skilled craftsmanship, both of which contribute to ethical consumption. The Kanghi is not mass-produced but is crafted in small batches with attention to detail, supporting fair labor practices and ensuring that the artisans are fairly compensated. This resonates with consumers who prioritize ethics in their purchasing decisions.
Brand Loyalty: Offering a product that meets the dual criteria of durability and ethical production can foster brand loyalty. Customers who value these aspects are more likely to return and recommend the Kanghi to others, increasing brand reputation and market reach.
Cost Efficiency: For businesses, producing a durable product can reduce long-term costs related to returns, repairs, and customer service. It also opens opportunities for marketing strategies for the Kanghi as a premium product, justifying a higher price point due to its quality and ethical production process.
9. Streamlining Production Processes for Handmade Kanghi
Efficiency in production is key to maintaining the high standards of Kanghi making. Artisans use optimized workflows that allow them to produce Kanghi efficiently without compromising on quality. Modern tools and techniques are integrated with traditional methods to streamline the production process, making it possible to meet higher demands while maintaining the artisanal quality that Kanghi is known for.
Process Planning:
Define Objectives: Kanghi artisans start by setting clear goals for production efficiency and quality standards.
Workflow Design: They map out each stage of the production process to ensure that every task is streamlined and efficient.
Tool and Technique Integration:
Select Modern Tools: Artisans carefully choose modern equipment that enhances traditional techniques, improving both precision and speed.
Blend Techniques: Craftspersons skillfully combine contemporary methods with traditional practices, maintaining the artisanal quality for which Kanghi is renowned.
Material Preparation:
Source Quality Materials: Artisans source high-quality, sustainable raw materials to ensure the best possible end product.
Pre-Processing: Materials are prepped and organized efficiently, reducing waste and preparation time during production.
Skill Training:
Train Artisans: Ongoing training is provided to artisans, ensuring they are proficient in both modern and traditional techniques.
Promote Best Practices: Best practices and efficient methods are shared among artisans to ensure consistency and quality.
Production Workflow Optimization:
Streamline Processes: Modular production stages and time-saving techniques are implemented to enhance workflow efficiency.
Minimize Downtime: Regular maintenance of equipment and quick resolution of issues help minimize downtime and keep production smooth.
Quality Control:
Regular Inspections: Quality control teams conduct frequent inspections throughout production to ensure each Kanghi meets high standards.
Feedback Loop: Feedback from quality checks is used to continuously refine processes and address any areas needing improvement.
Batch Production:
Small Batches: Kanghi is produced in small batches, allowing artisans to maintain artisanal quality while meeting higher demands.
Efficient Scheduling: Production runs are scheduled to optimize resource use and manage demand effectively.
Technology Integration:
Automation: Automation is incorporated where appropriate to handle repetitive tasks and streamline production.
Data Tracking: Digital tools help track production data, monitor performance, and pinpoint areas for enhancement.
Continuous Improvement:
Review and Refine: Production processes are regularly reviewed, with artisans seeking ways to improve efficiency and quality.
Adopt Innovations: New tools and techniques are adopted to further elevate the craft.
Customer Feedback:
Collect Input: Feedback from customers is actively sought to understand their needs and preferences.
Adjust Accordingly: Customer insights are used to make necessary adjustments to the production process, ensuring that expectations are consistently met.
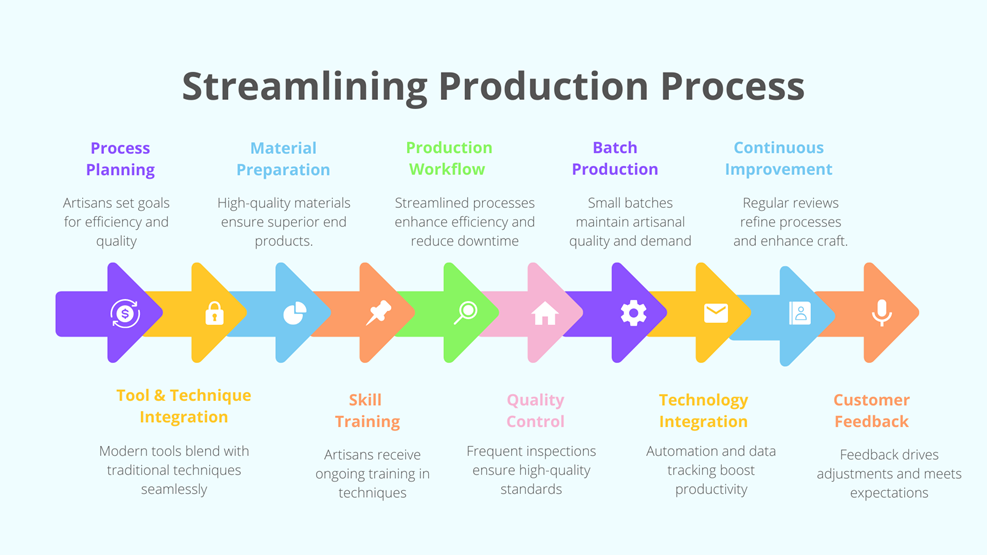
10. Scaling Kanghi Making Businesses without Compromising Quality
As demand for handmade home products like Kanghi grows, there is a need to scale production without losing the essence of quality. In Himachal Pradesh, artisans and business owners focus on expanding production capacity while maintaining the same level of craftsmanship. Workforce management plays a crucial role here, ensuring that artisans are trained to maintain quality even as production scales up. This balance between scalability and quality is what makes Kanghi making a sustainable business model.
Step-by-Step Guide for Kanghi Makers:
Assess Current Capacity:
Kanghi makers evaluate their production capabilities and identify areas for improvement.Implement Standardized Procedures:
They introduce standardized processes to ensure consistent Kanghi quality.Invest in Training:
Artisans receive training to maintain high standards as production scales.Monitor and Adjust:
Kanghi makers continuously monitor quality and make adjustments as needed.
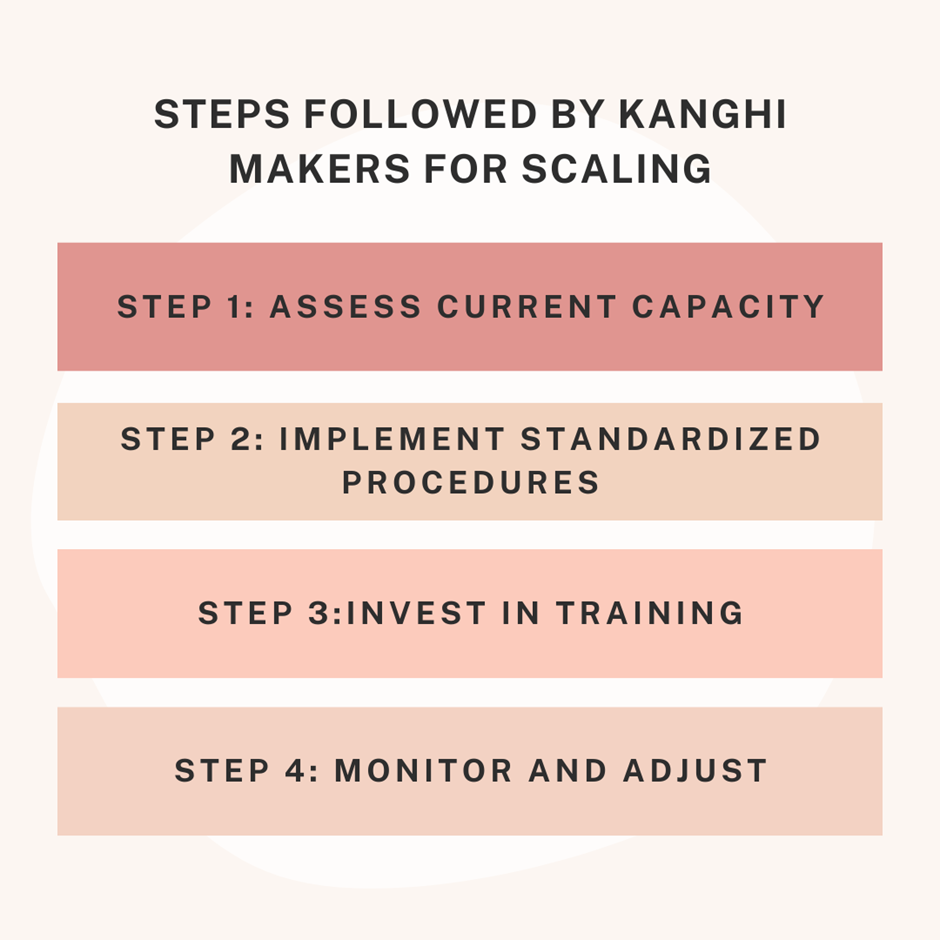
As a Result these steps enable Kanghi makers to expand while preserving exceptional craftsmanship.
11. Reducing Carbon Emissions by Kanghi Weavers
The craft of Kanghi making has a relatively low carbon footprint, especially when compared to industrial production methods. The materials used, the processes employed, and the local sourcing all contribute to reducing carbon emissions. The artisans are committed to further lowering these emissions by adopting more sustainable practices and exploring new ways to make the craft even more eco-friendly.
Steps Taken by Kanghi Makers to Reduce Carbon Emissions
Local Sourcing of Materials:
Kanghi makers source raw materials locally to minimize transportation emissions and support regional suppliers.Use of Natural Dyes:
They employ natural dyes and traditional coloring techniques to reduce reliance on synthetic, environmentally harmful chemicals.Minimizing Waste:
Artisans implement efficient cutting and weaving practices to minimize waste and repurpose any excess materials.Energy-Efficient Tools:
They use energy-efficient tools and equipment to lower energy consumption during production.Sustainable Packaging:
Eco-friendly packaging options are chosen to reduce the environmental impact of shipping and storage.
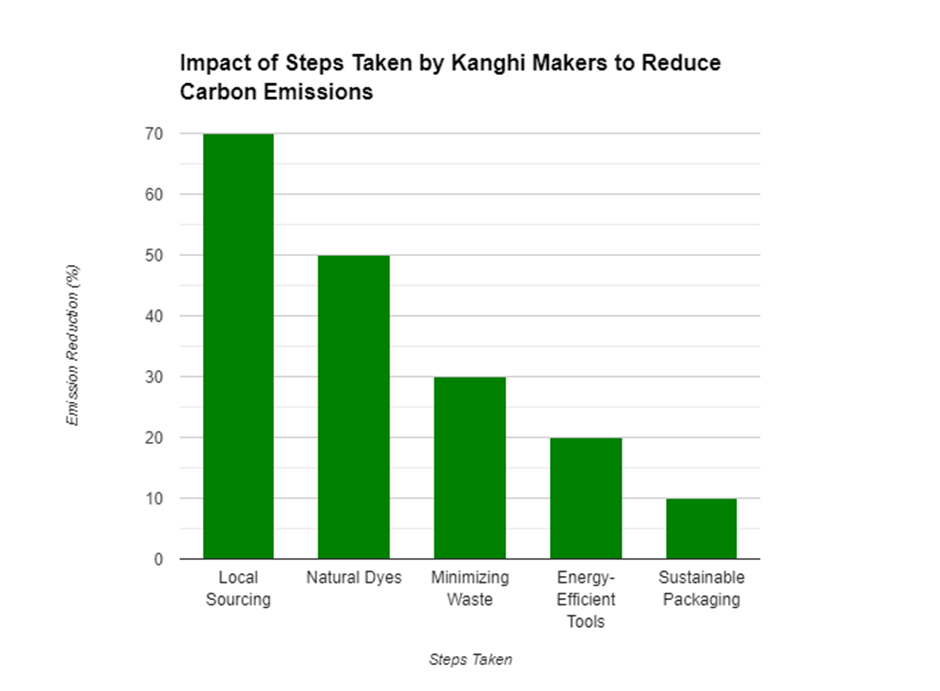
12. Cost Management Strategies followed by Handmade Kanghi Makers
Cost management is an essential aspect of the Kanghi-making business. Artisans carefully balance the cost of materials and labor with the need to produce high-quality products. Pricing models are developed to ensure that the products remain accessible while also providing fair compensation for the artisans. Techniques for reducing production costs without compromising on quality are constantly being explored, ensuring that the business remains viable in the long term.
Cost management is crucial in ensuring the viability of the Kanghi-making business. Artisans and business owners employ several strategies to keep production costs in check while maintaining the high quality that Kanghi is known for.
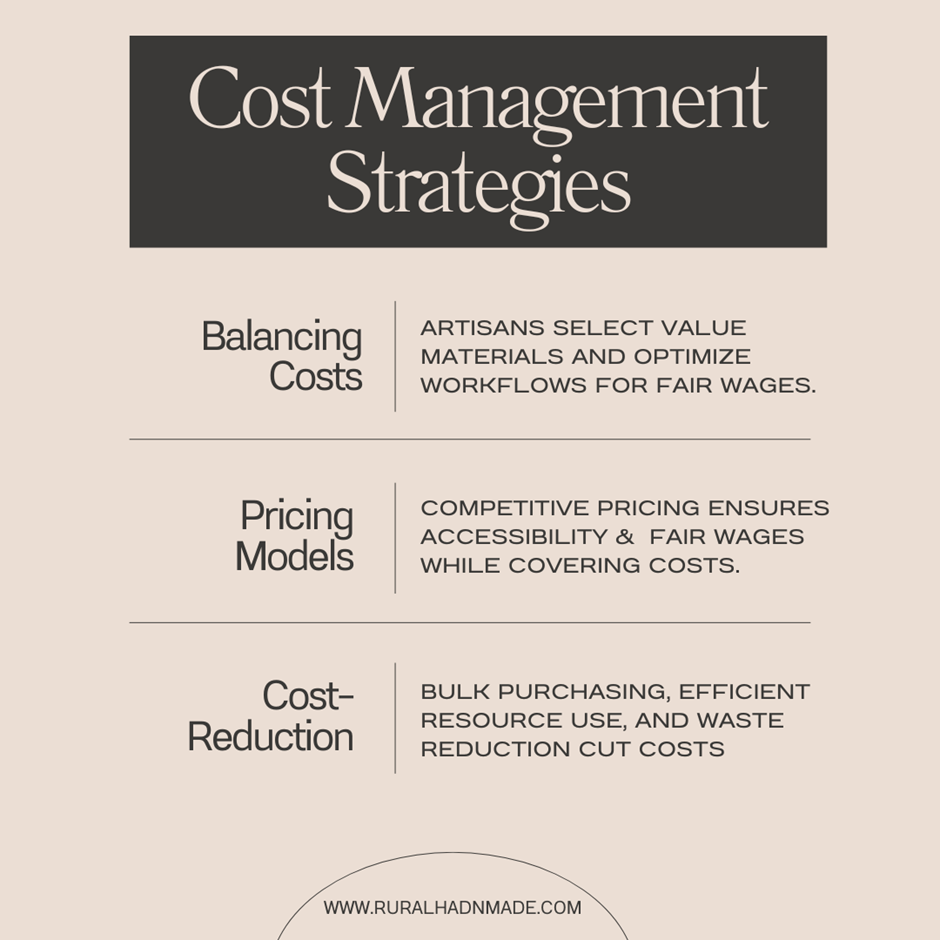
Balancing Material and Labor Costs:
Artisans carefully select materials that offer the best value for money without compromising quality. Labor costs are managed by optimizing workflows and ensuring that artisans are fairly compensated for their work.Pricing Models:
Competitive pricing models are developed to ensure that Kanghi remains accessible to a broad audience while still offering fair wages to artisans. These models take into account the costs of raw materials, labor, and overheads, allowing for sustainable profit margins.Cost-Reduction Techniques:
Techniques such as bulk purchasing of materials, efficient use of resources, and minimizing waste are employed to reduce production costs. Artisans are also exploring new methods and technologies that can streamline production without diminishing the craftsmanship of Kanghi.
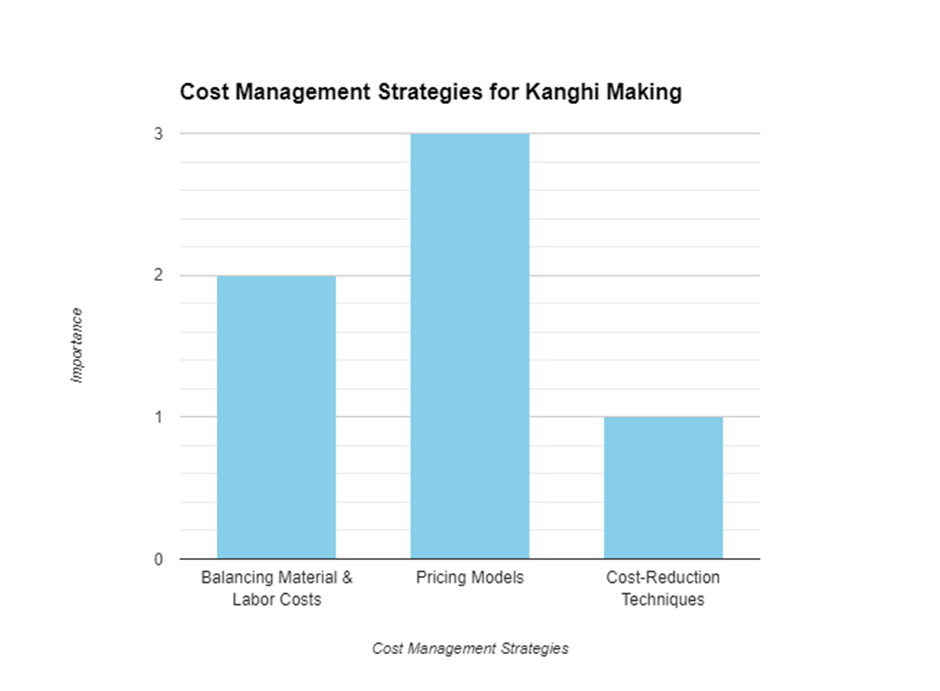
These strategies ensure that Kanghi remains a viable business, capable of sustaining the livelihoods of artisans while delivering high-quality products to customers.
13. Customization Options provided by Kanghi Weavers
One of the key selling points of Kanghi is the ability to customize the product to meet client needs. Whether it's a specific design, material, or size, artisans are capable of creating bespoke Kanghi that perfectly fits the client's requirements. This flexibility in customization ensures that each product is unique and tailored to the buyer’s preferences, adding significant value to the handmade product.
Personalization Beyond the Norm:
Each Kanghi can be customized in various ways, including the choice of materials, design patterns, and even the size of the product. This flexibility allows buyers to own a piece that is not only functional but also a reflection of their personal style.Value Addition Through Bespoke Designs:
Customization adds significant value to Kanghi, as each piece is tailored to the buyer’s specific needs. This bespoke approach ensures that no two Kanghis are exactly alike, enhancing the product's uniqueness and appeal.
The ability to customize Kanghi makes it more than just a tool for weaving; it becomes a personal statement, a one-of-a-kind piece that holds special meaning for its owner.
14. Environmental Impact of making Kanghi Crafts
The environmental impact of Kanghi making is generally positive, with the craft contributing to the conservation of natural resources and promoting sustainable practices. The use of eco-friendly materials and traditional techniques minimizes waste and reduces the overall environmental footprint. By supporting Kanghi making, buyers are also contributing to the preservation of a craft that has a lower environmental impact compared to mass-produced alternatives.
Eco-Friendly Materials:
The materials used in Kanghi making are often natural and biodegradable, reducing the environmental footprint of the craft. These materials are sourced sustainably, ensuring that their extraction does not harm the environment.Traditional Techniques:
Kanghi making employs age-old techniques that are inherently low-impact. These methods minimize waste and energy consumption, making the craft an eco-friendly alternative to mass production.Minimal Waste:
The meticulous crafting process ensures that materials are used efficiently, with little to no waste generated. Any leftover materials are often repurposed, further reducing the environmental impact.Lower Carbon Footprint:
Compared to industrial production methods, Kanghi making has a significantly lower carbon footprint. The local sourcing of materials and the manual crafting process contribute to this reduction.
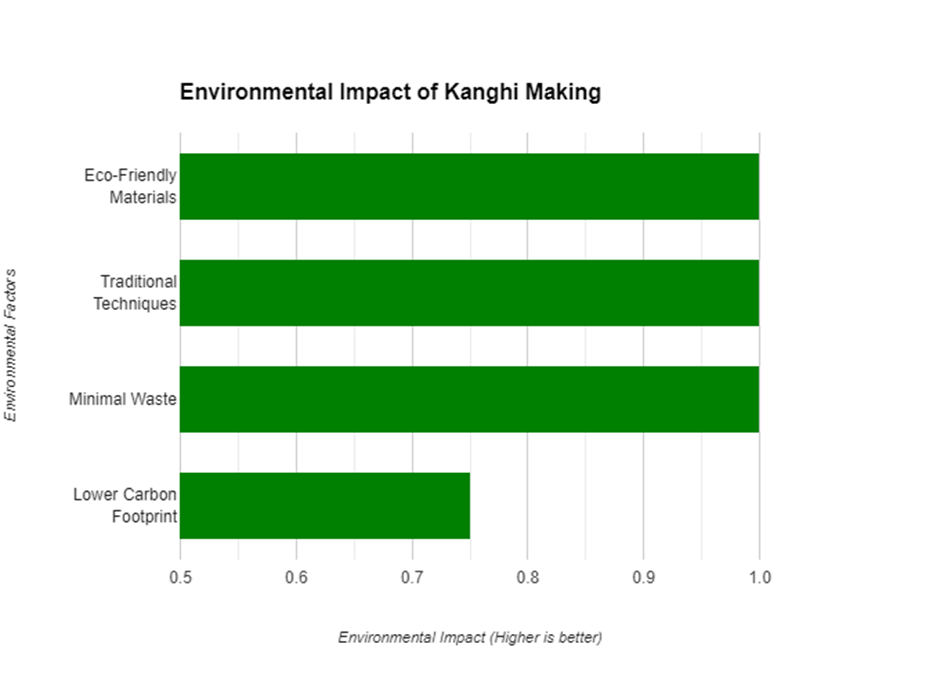
15. Social Impact of Kanghi Crafts
Kanghi making has a profound social impact on the local communities in Himachal Pradesh. The craft provides employment opportunities, supports local economies, and helps preserve cultural heritage. By purchasing Kanghi, buyers are not only acquiring a unique product but also supporting the social and economic well-being of artisan communities. The social gain from this craft extends beyond the artisans to the entire community, creating a ripple effect of positive impact.
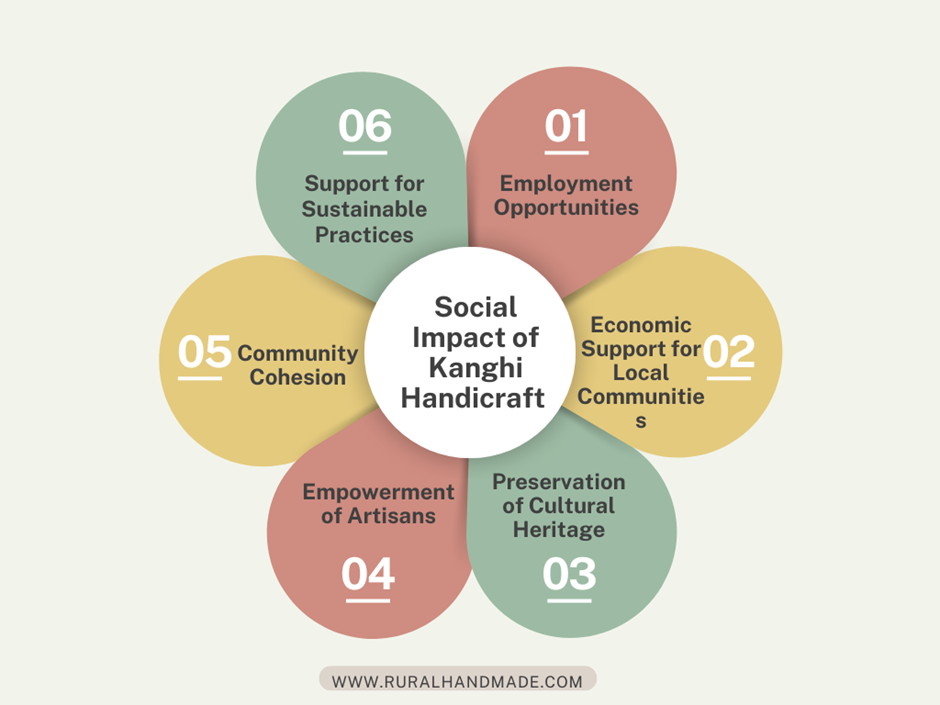
1. Employment Opportunities:
Artisan Jobs: Kanghi making provides jobs to numerous artisans, including weavers and skilled craftsmen, offering a steady source of income and improving their standard of living.
Local Employment: The craft creates additional jobs in ancillary sectors such as material suppliers, dye makers, and tool manufacturers, further boosting local employment.
2. Economic Support for Local Communities:
Economic Development: The income generated from Kanghi sales contributes to the overall economic development of Himachal Pradesh, supporting local businesses and infrastructure.
Income Stability: Regular orders and sales provide financial stability for artisans and their families, reducing poverty levels and supporting community development projects.
3. Preservation of Cultural Heritage:
Traditional Skills: Kanghi making helps preserve traditional weaving techniques and craftsmanship, passing these skills down through generations and maintaining cultural identity.
Cultural Pride: The craft fosters a sense of pride among artisans and the local community, reinforcing cultural traditions and promoting regional heritage.
4. Empowerment of Artisans:
Skill Development: Artisans gain valuable skills and training through their craft, enhancing their capabilities and providing opportunities for personal and professional growth.
Women Empowerment: Many Kanghi artisans are women, and the craft offers them a platform for economic independence and empowerment within their communities.
5. Community Cohesion:
Social Bonds: The process of creating and selling Kanghi fosters strong community bonds, as artisans often work together and support each other in their endeavors.
Cultural Exchange: The craft attracts attention from tourists and buyers, creating opportunities for cultural exchange and increasing the visibility of Himachal Pradesh’s rich traditions.
6. Support for Sustainable Practices:
Eco-Friendly Methods: Kanghi making often involves sustainable practices, such as using natural dyes and locally sourced materials, which supports environmental conservation and promotes eco-friendly living.
Community Initiatives: Revenue from Kanghi sales is sometimes reinvested into community initiatives, such as education programs and health services, further benefiting the local population.
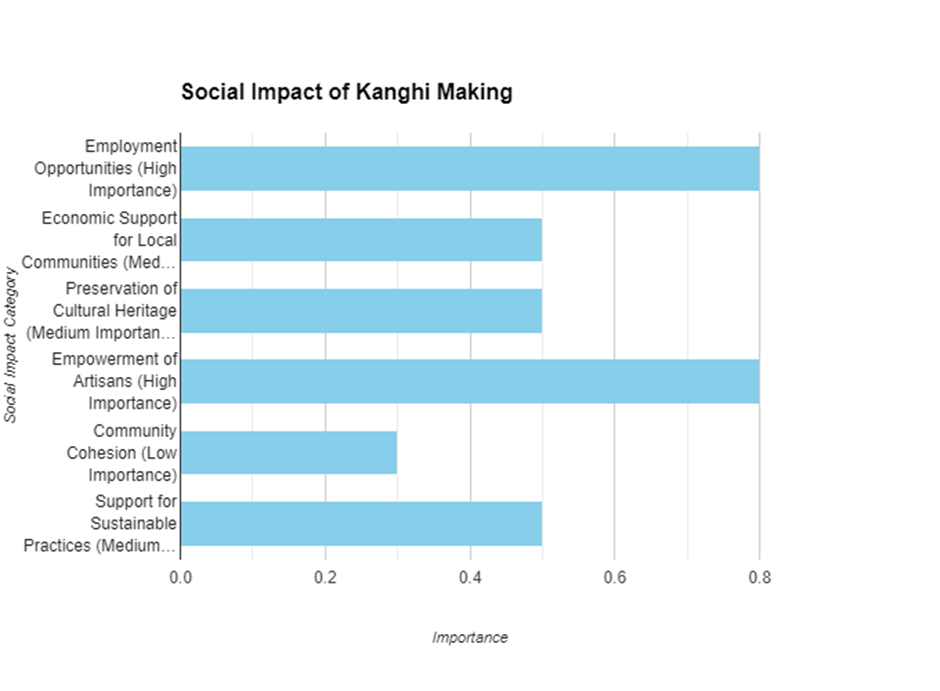
· 16. Economic Impact of Kanghi Crafts
Economically, Kanghi making plays a significant role in the local economy of Himachal Pradesh. It creates jobs, supports local businesses, and contributes to the overall economic development of the region. The demand for handmade Kanghi drives the supply chain, from raw material suppliers to artisans, creating a robust economic ecosystem. The craft’s economic impact is evident in the improved livelihoods of those involved in the production process.
Job Creation:
Artisan Employment: Kanghi making generates employment opportunities for skilled artisans, weavers, and craftsmen, directly impacting their livelihoods.
Ancillary Jobs: Associated roles, such as material suppliers, dye manufacturers, and tool makers, also benefit from the craft’s demand.
Support for Local Businesses:
Supply Chain Boost: The need for raw materials and tools supports local businesses, including suppliers and service providers, contributing to the regional economy.
Local Retailers: Kanghi products are often sold through local markets and stores, boosting sales and revenue for retail businesses.
Economic Development:
Increased Income: Revenue from Kanghi sales enhances the financial stability of artisans and their families, contributing to overall economic growth in Himachal Pradesh.
Infrastructure Improvement: The craft’s economic success can lead to better infrastructure and community services, benefiting the entire region.
Strengthening Economic Ecosystem:
Robust Supply Chain: The demand for Kanghi creates a comprehensive supply chain involving multiple sectors, fostering a resilient economic network.
Market Demand: The growing interest in handmade Kanghi drives production and innovation, supporting economic activity across various levels of the supply chain.
Enhancing Livelihoods:
Income Generation: Artisans and their families experience improved financial conditions due to consistent work and sales from Kanghi production.
Economic Stability: The craft provides a stable source of income, reducing economic uncertainty and supporting long-term financial well-being.
Encouraging Investment:
Attracting Investment: Successful Kanghi production can attract investment in local businesses and infrastructure, further stimulating economic activity.
Entrepreneurial Growth: The craft’s success encourages entrepreneurship and the establishment of new ventures related to Kanghi making and sales.
Regional Economic Integration:
Economic Linkages: Kanghi making strengthens economic connections between different regions, from raw material sourcing to final product distribution through different distribution channels.
Regional Promotion: Increased visibility and demand for Kanghi contribute to regional branding and attract tourists, enhancing economic opportunities for the area.
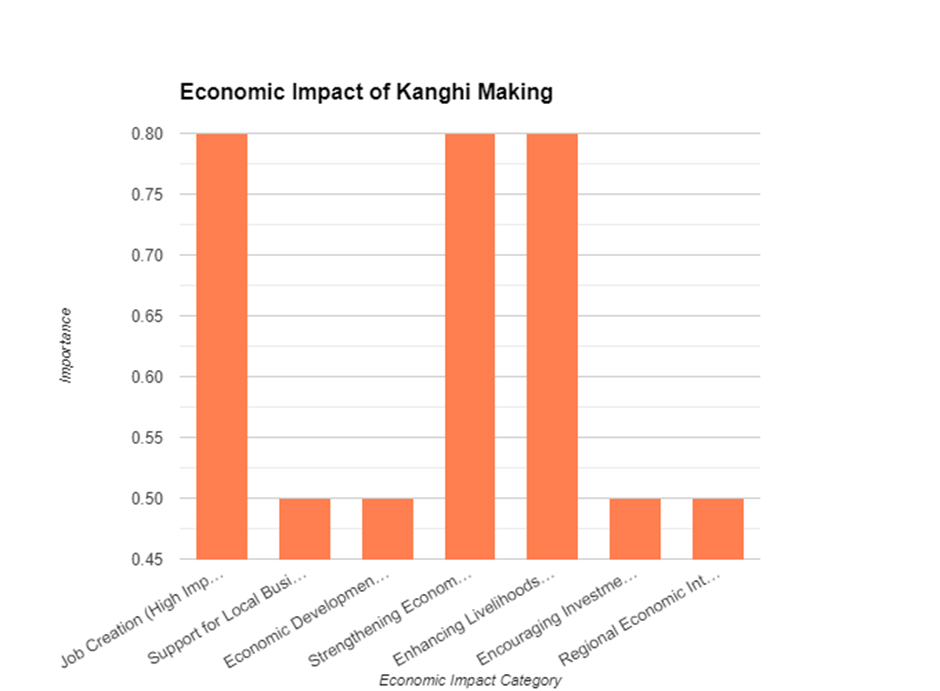
Top Handicraft Shops in Himachal Pradesh: Your Guide to Authentic Handloom and Handmade Products
17. Applying Design Thinking to Create Innovative Handmade Kanghi Products
Innovation in Kanghi making is driven by design thinking, a process that involves creative problem-solving and user-centered design. Artisans continuously explore new ways to improve the functionality and aesthetics of Kanghi, ensuring that the products meet modern demands while retaining their traditional essence. This approach to innovation keeps the craft relevant in a rapidly changing market.
Step-by-Step Guide for Kanghi Makers:
Empathize: Kanghi makers interact with clients to understand their needs and preferences.
Define: They identify challenges and opportunities to enhance Kanghi’s functionality and appeal.
Ideate: Artisans brainstorm creative solutions, blending traditional techniques with modern trends.
Prototype: Prototypes are created to experiment with different materials and designs.
Test: New Kanghi designs are tested with users, gathering feedback for refinement.
By applying design thinking, Kanghi makers innovate while preserving traditional craft, ensuring relevance.
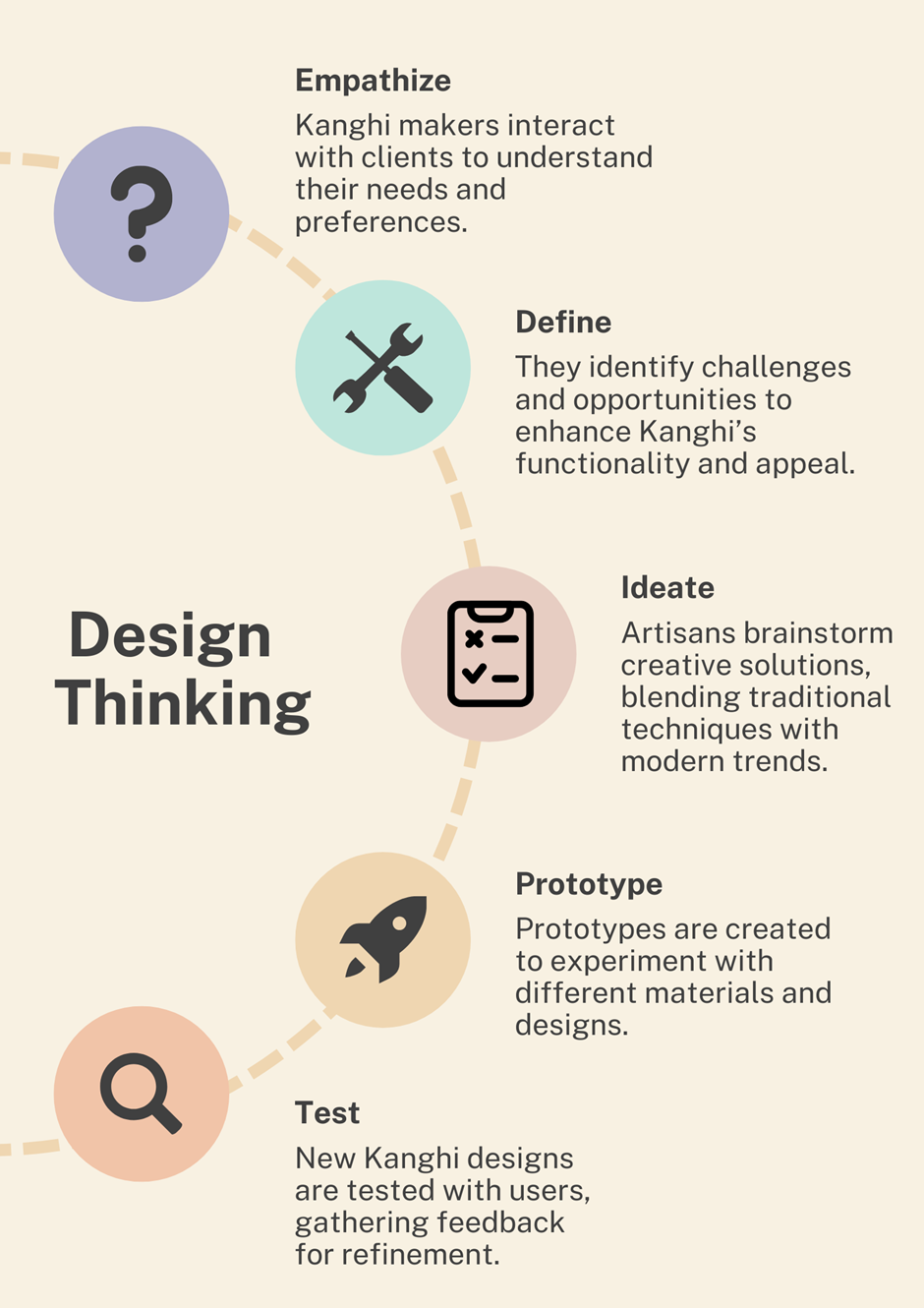
18. Reducing Turnaround Time in the Production of Kanghi
Time management is crucial in the production of Kanghi, especially when dealing with customized orders. Artisans have developed efficient workflows that reduce the turnaround time, ensuring that products are delivered to clients in a timely manner. This efficiency in production not only improves customer satisfaction but also allows artisans to take on more orders, increasing their overall productivity.
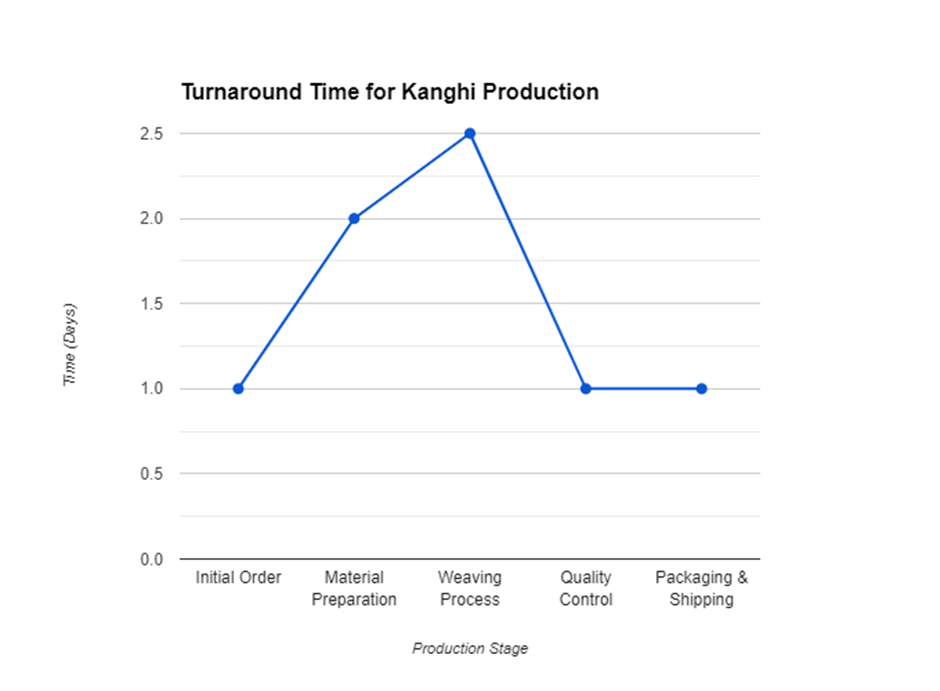
Timeline Format for making Kanghi:
Initial Order:
Upon receiving an order, artisans immediately begin preparing materials and planning the production process. This stage involves selecting the appropriate materials and setting up the loom.Day 1-2: Material Preparation:
The raw materials are prepared, including any necessary cutting, dyeing, or treatment processes. This step is crucial to ensure that the materials are ready for efficient production.Day 3-4: Weaving Process:
The actual weaving process begins. Artisans work diligently, using optimized workflows to ensure that the Kanghi is produced efficiently without compromising on quality.Day 5: Quality Control and Final Touches:
The finished Kanghi undergoes a thorough quality check. Any necessary adjustments or final touches are made to ensure that the product meets the high standards expected by clients.Day 6: Packaging and Shipping:
Once approved, the Kanghi is carefully packaged and prepared for shipment, ensuring it arrives safely at its destination.
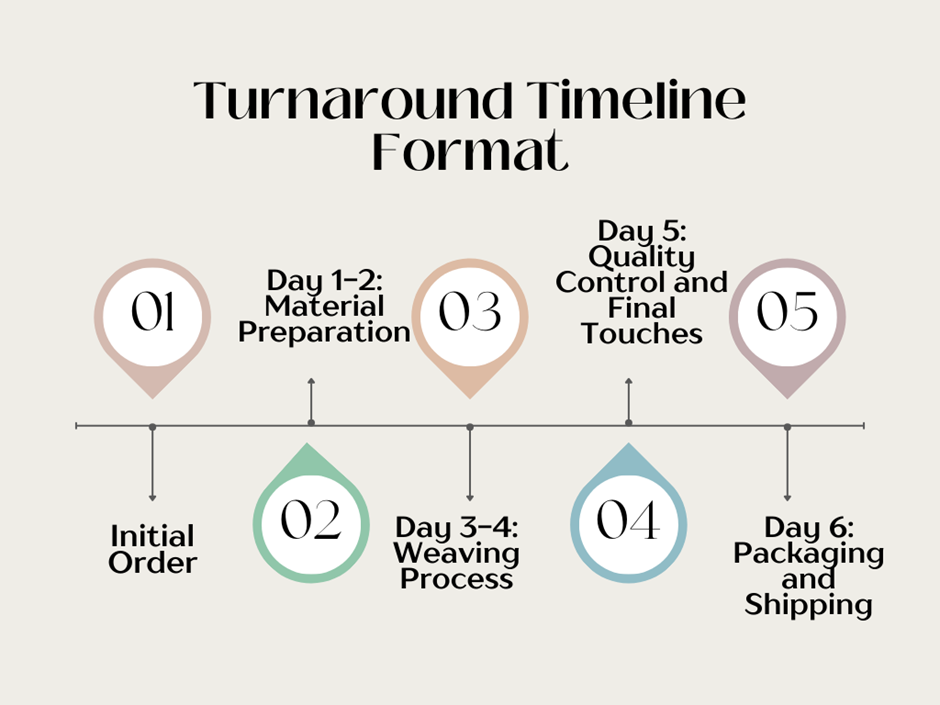
Conclusion:
By adhering to this timeline, artisans are able to reduce turnaround time, improving customer satisfaction and allowing for higher productivity.
19. Navigating Payment Terms and Conditions in the Handmade Kanghi Making Industry
In the handmade home décor industry, clear and fair payment terms are essential for maintaining healthy business relationships. Artisans and business owners in Himachal Pradesh are transparent about their payment schedules and terms of service, ensuring that both parties are in agreement before the production process begins. This clarity in financial agreements helps build trust and ensures smooth transactions.
Clear Payment Schedules:
Ensure that both parties agree on a clear payment schedule before the production begins. This should include deposit requirements, milestones, and final payment terms.Detailed Terms of Service:
Outline all terms of service, including what is covered in the cost (e.g., materials, labor, shipping) and what is not. This clarity helps prevent misunderstandings and disputes.Agreement on Delivery Terms:
Clearly define the delivery timeline and any contingencies. This should include expectations for both the production process and shipping.Fair Compensation:
Ensure that the payment terms provide fair compensation to artisans, reflecting the time and effort required to produce high-quality handmade goods.Transparent Communication:
Maintain open communication throughout the process, updating the client on progress and any potential changes to the agreed-upon terms.
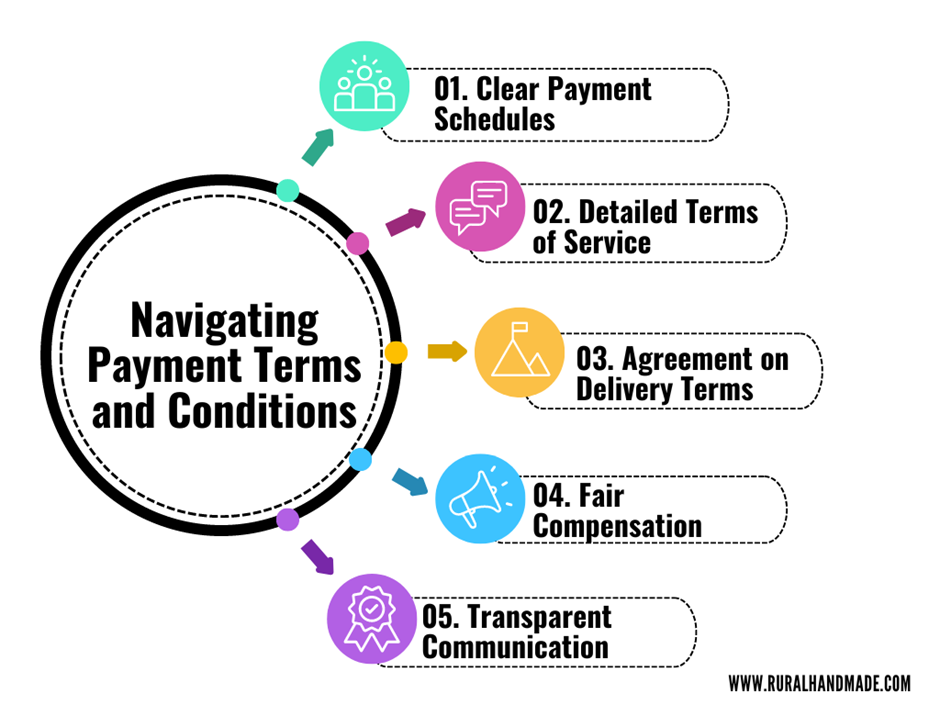
Conclusion:
Navigating payment terms with transparency and clarity ensures smooth transactions, fostering trust and long-term business relationships in the handmade home décor industry.
20. Importance of Certifications in Handmade Kanghi Products
Certifications play a vital role in establishing the credibility of handmade products like Kanghi. Industry certifications not only assure buyers of the product's quality but also demonstrate compliance with regulatory standards. These certifications are a mark of authenticity, ensuring that the products are made according to the highest standards of craftsmanship and ethical practices.
Certifications play a crucial role in the handmade home products industry, particularly for crafts like Kanghi making. They serve as a mark of quality and authenticity, providing buyers with confidence that they are purchasing a product that meets high standards.
Assurance of Quality:
Industry certifications verify that Kanghi has been made using quality materials and craftsmanship. This assurance is especially important in a market where consumers are increasingly concerned about the authenticity of handmade products as per Industry standards.Regulatory Compliance:
Certifications also demonstrate that the product complies with relevant regulations and standards. For example, a certification might indicate that the materials used are safe and sustainable, meeting environmental and safety standards like Green Certification.Ethical Practices:
Certifications can also reflect the ethical practices of the artisans, such as fair labor practices and environmentally sustainable sourcing of materials. This is increasingly important to consumers who want to support ethical businesses.
For the industry, certifications typically include:
ISO 9001: Quality Management Systems
Fair Trade Certification: Ethical labor practices
GOTS (Global Organic Textile Standard): Eco-friendly production
SA8000: Social Accountability in the workplace
OEKO-TEX Standard 100: Textile safety
21. How Efficient Supply Chain Management is in Kanghi Making
Supply chain management is critical in the business of Kanghi making. Artisans and business owners work to optimize the supply chain, ensuring timely delivery of materials and products. Inventory management is also a key focus, with efforts to reduce costs while maintaining a steady supply of raw materials and finished products. Efficient logistics management ensures that products reach customers on time, reducing the risk of delays and enhancing customer satisfaction.
Sourcing Raw Materials:
Secure reliable suppliers for consistent quality and availability, building long-term relationships to ensure steady supply during peak demands while negotiating favorable terms to balance cost and quality effectively.Inventory Management:
Maintain optimal stock levels to balance cost and demand, implementing real-time tracking to avoid shortages or overstocking and regularly reviewing inventory turnover to improve cash flow and reduce storage costs.Logistics Coordination:
Ensure efficient transportation for timely delivery of materials and products, collaborating with logistics partners to streamline the supply chain and reduce delays while utilizing technology to track shipments and manage disruptions proactively.Minimizing Waste:
Optimize material use to reduce waste and enhance efficiency, implementing recycling processes to repurpose excess materials sustainably and continuously evaluating production techniques to further minimize waste.
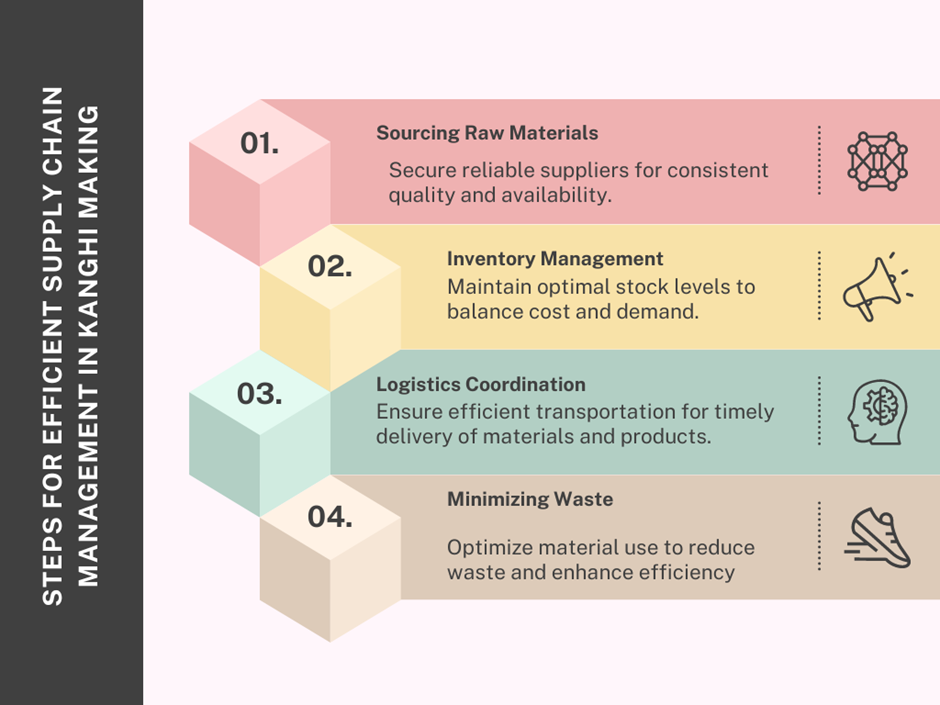
22. Ensuring Compliance with Anti-Money Laundering (AML) Regulations by Kanghi Makers
Compliance with Anti-Money Laundering (AML) regulations is crucial for businesses involved in the international trade of Kanghi. Artisans and business owners must implement internal controls and undergo training to ensure that their operations are compliant with legal requirements. This compliance not only protects the business but also builds trust with international buyers.
Step-by-Step Approach:
Training and Awareness: Implement training programs for artisans and business owners to understand the importance of AML regulations.
Internal Controls: Establish robust internal controls to monitor transactions and prevent money laundering activities.
Regular Audits: Conduct regular audits to ensure compliance with AML laws and regulations.
Documentation: Maintain clear records of all transactions to provide transparency and accountability.
Partnerships: Work with financial institutions and legal experts to ensure that all operations are compliant with AML regulations, building trust with international buyers and safeguarding the business from legal issues.
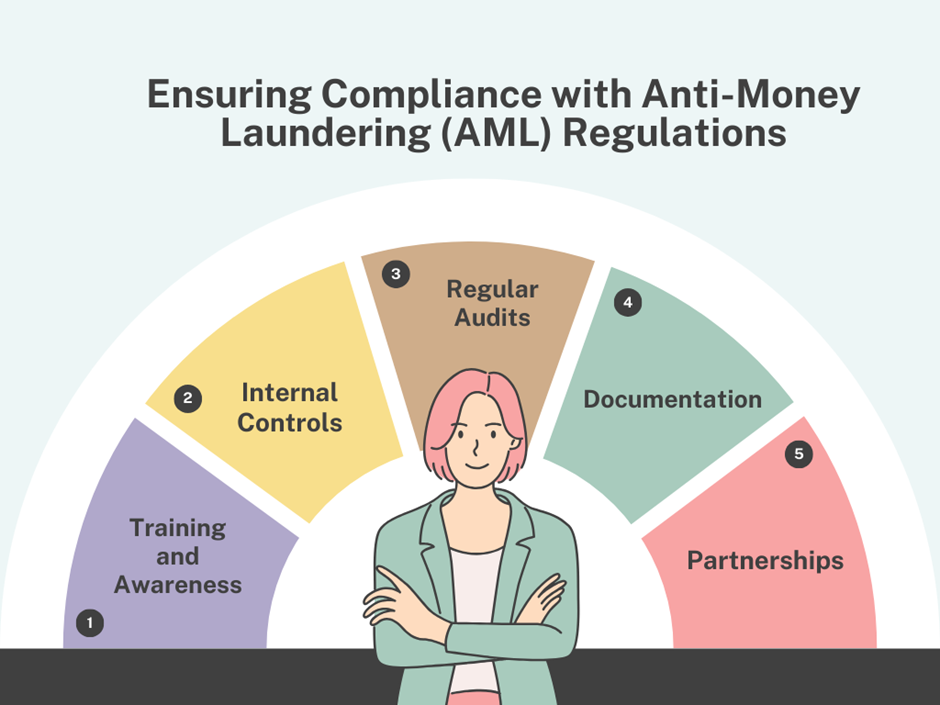
Steps to Follow if You Become a Victim of AML Procedures
Becoming inadvertently involved in money laundering can have serious legal and financial repercussions. If you suspect that you are a victim of Anti-Money Laundering (AML) practices, follow these steps immediately:
1. Stay Calm and Document Everything
Collect All Relevant Information: Gather all documents, emails, bank statements, and communications related to the transaction or activity in question.
Note Down Events: Create a detailed timeline of events that led to your suspicion of being involved in money laundering.
2. Consult a Legal Expert
Seek Professional Advice: Contact a lawyer specializing in financial crimes or AML to understand your rights and the legal implications.
Provide Full Disclosure: Share all the information you’ve collected with your lawyer to help them provide the best advice and defense strategy.
3. Notify Your Bank or Financial Institution
Report the Incident: Inform your bank or financial institution about the suspicious activity. They can guide you on the steps to secure your accounts.
Freeze Transactions: Request your bank to temporarily freeze your accounts to prevent further unauthorized transactions.
4. Contact Relevant Authorities
File a Report: Report the incident to your local law enforcement or financial regulatory authorities, such as the Financial Intelligence Unit (FIU) in your country.
Cooperate Fully: Provide authorities with all requested information and cooperate with any ongoing investigations.
5. Monitor Your Accounts
Keep a Close Watch: Regularly monitor your bank accounts and financial statements for any unauthorized or suspicious activity.
Set Alerts: Use transaction alerts and notifications to stay informed about any changes in your account status.
6. Implement Preventive Measures
Enhance Security: Strengthen your online security measures, including changing passwords, enabling two-factor authentication, and using secure networks for transactions.
Educate Yourself: Learn about common money laundering schemes and red flags to avoid falling victim in the future.
7. Consider Financial Recovery Options
Explore Chargebacks: If possible, initiate a chargeback for unauthorized transactions through your bank or credit card company.
Seek Restitution: In cases where significant financial loss has occurred, your lawyer can advise on legal avenues for restitution.
8. Stay Informed About the Case
Follow Up: Keep in touch with your lawyer and the authorities to stay updated on the status of your case.
Adhere to Legal Advice: Follow any instructions given by your legal counsel to avoid further complications.
23. Understanding Customs and Duties for trading Kanghi in Other Countries
For Kanghi products that are sold internationally, understanding customs and duties is essential. Artisans and exporters must navigate tariffs, trade agreements, and duty drawbacks to ensure that their products reach global markets without unnecessary costs. This knowledge helps in pricing the products competitively while complying with international trade regulations.
Here are a few key points on selling Kanghi internationally with a focus on customs and duties:
Understanding Trade Agreements:
Research relevant trade agreements to leverage tariff reductions and duty exemptions for Kanghi exports.Navigating Tariffs and Duties:
Identify applicable tariffs and duties for target markets, ensuring Kanghi is competitively priced.Staying Updated on Regulations:
Keep informed about changes in international trade regulations to avoid compliance issues.Duty Drawbacks and Refunds:
Explore duty drawback programs to reclaim some costs, improving Kanghi’s profitability.Consulting Trade Experts:
Seek advice from customs and trade experts to navigate complexities and avoid unnecessary costs.Pricing Strategy:
Incorporate customs and duty costs into the pricing strategy to ensure profitability in global markets.Documentation Compliance:
Ensure accurate and complete documentation to facilitate smooth customs clearance and prevent delays.Market Research:
Conduct market research to understand the impact of customs and duties on pricing in different countries.
Below is a table outlining the customs and duties applicable for importing and exporting kanghi products in the top 5 countries where cluster is engaged in trade.
24. Promoting Ethical Manufacturing by Kanghi Makers
Ethical manufacturing is at the heart of Kanghi making. Artisans adhere to fair labor practices, ensuring that workers are paid fairly and work in safe conditions. Transparency in the supply chain is also maintained, with a focus on sustainability and responsible sourcing. By promoting ethical practices, the Kanghi-making community in Himachal Pradesh sets a high standard for handmade home décor products.
25. Implementing Innovative Manufacturing Techniques by Kanghi Makers
Innovation in manufacturing is key to the continued success of Kanghi making. Artisans are open to adopting new technologies and processes that can improve efficiency and product quality. Research and development (R&D) play a role in exploring new materials, techniques, and designs, ensuring that the craft remains relevant and competitive in the global market.
Integration of Modern Tools:
Artisans are incorporating tools like computer-aided design (CAD) software to create intricate patterns with precision.Exploration of New Materials:
R&D efforts focus on finding sustainable materials that complement traditional ones, improving both durability and appeal.Process Optimization:
By blending traditional craftsmanship with automated processes, artisans can scale production without sacrificing quality.
26. Enhancing Collaboration with Stakeholders by Kanghi Makers
Collaboration with stakeholders, including suppliers, buyers, and co-creators, is essential for the growth of the Kanghi-making business. Building strong partnerships helps in securing a reliable supply of materials, gaining access to new markets, and co-creating products that meet customer needs. These collaborations are built on mutual trust and shared goals, ensuring long-term success.
Supplier Partnerships: Building strong relationships with raw material suppliers to ensure consistent quality and availability.
Buyer Engagement: Engaging with buyers to understand their needs and co-create products that meet market demands.
Co-Creation: Collaborating with designers and other artisans to develop new product lines that reflect both traditional and contemporary aesthetics.
Community Involvement: Involving the local community in the decision-making process to ensure that the Kanghi-making business benefits everyone involved.
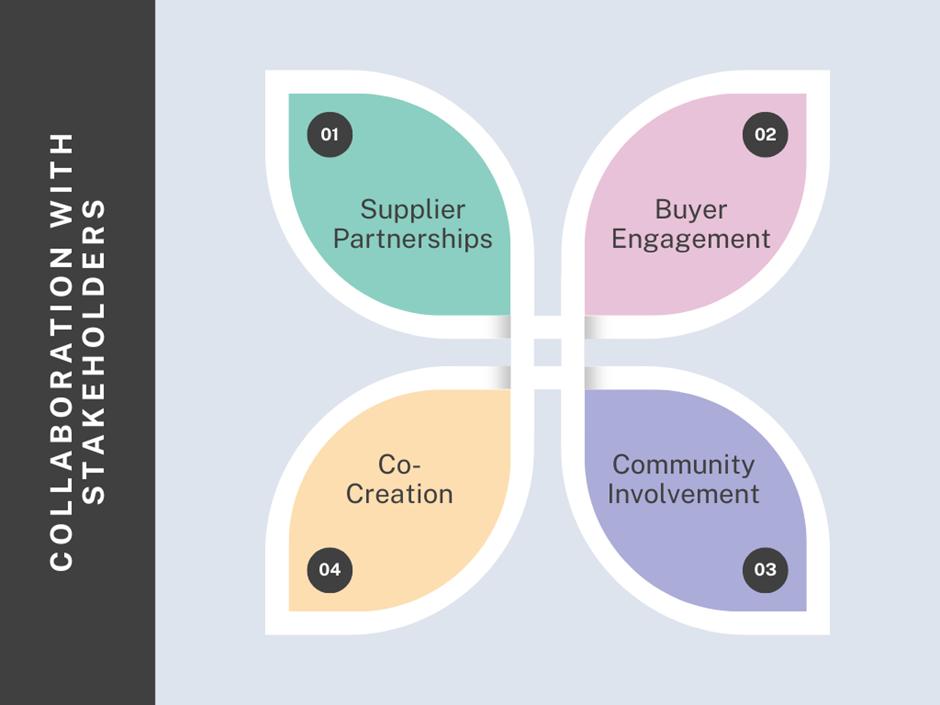
27. Staying Updated on Market Trends by Kanghi Makers
Understanding market trends is crucial for the Kanghi-making business. Artisans and business owners must stay informed about the latest design trends, consumer preferences, and industry developments to stay competitive. This awareness allows them to adapt their products to meet current demands, ensuring that Kanghi remains a sought-after product in the market.
Market Research: Regularly conduct market research to identify emerging trends in home décor and consumer preferences.
Trend Analysis: Analyze trends in materials, colors, and design to adapt Kanghi products accordingly.
Competitor Monitoring: Keep an eye on competitors to understand what they are offering and how Kanghi can differentiate itself.
Customer Feedback: Gather and analyze customer feedback to refine products and meet the evolving demands of the market.
Industry Networking: Attend trade shows, workshops, and conferences to stay connected with industry developments.
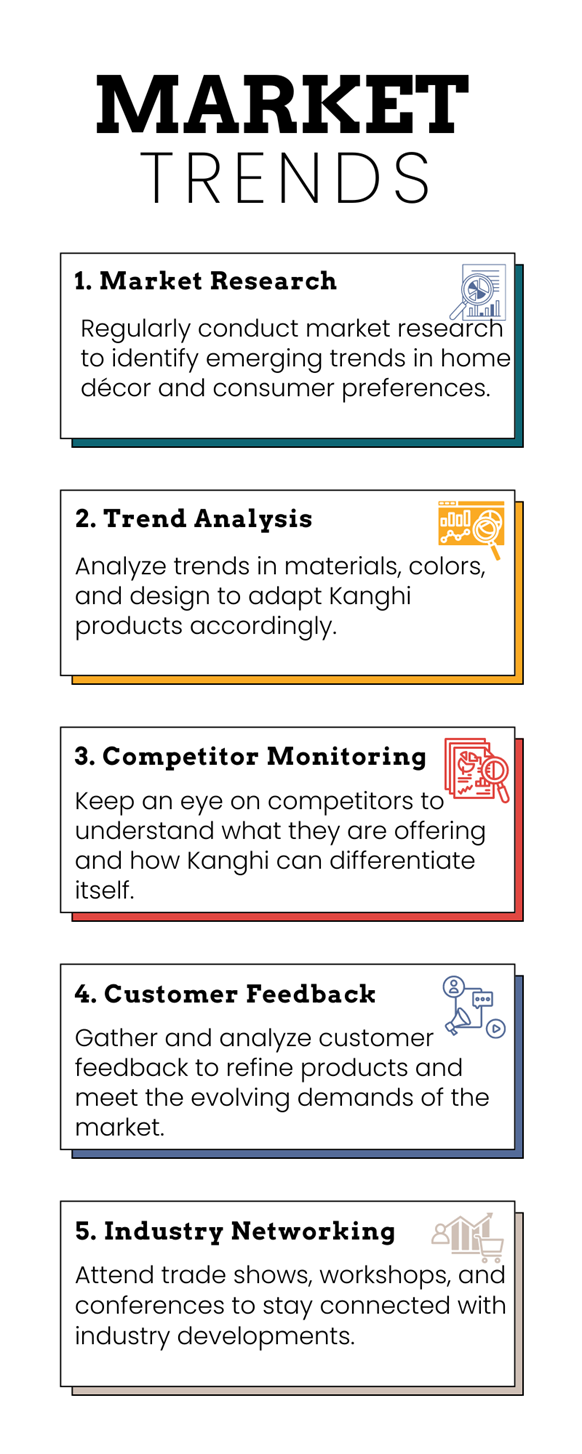
28. Managing Risks in the Handmade Kanghi Business
Risk management is a vital aspect of running a Kanghi-making business. Artisans and business owners must identify potential risks, such as market fluctuations, supply chain disruptions, and regulatory changes,financial risks and develop strategies to mitigate them. Insurance, diversification, and contingency planning are some of the ways to manage these risks, ensuring the sustainability of the business.
Risk Management Framework:
1. Risk Identification: Identify potential risks such as market volatility, supply chain disruptions, and changes in regulations.
2. Risk Assessment: Evaluate the likelihood and impact of each risk, prioritizing them based on their potential effect on the business.
3. Risk Mitigation: Develop strategies to mitigate identified risks. For example, securing insurance to protect against natural disasters or diversifying suppliers to reduce dependency on a single source.
4. Risk Monitoring: Continuously monitor risks and update mitigation strategies as necessary, ensuring the business remains resilient in the face of challenges.
29. Leveraging Digital Marketing to Promote Handmade Kanghi Products
Digital marketing is an essential tool for promoting Kanghi products. Artisans and business owners can use online platforms to showcase their products, reach a wider audience, and engage with customers. Social media, e-commerce websites,SEO and content marketing are some of the strategies used to promote Kanghi, building brand awareness and driving sales.
Social Media Engagement:
Utilizing platforms like Instagram and Facebook to showcase Kanghi designs, share behind-the-scenes craftsmanship, and interact directly with potential buyers.E-commerce and Content Marketing:
Selling Kanghi through online marketplaces and using content marketing to tell the story behind the craft, enhancing brand awareness and driving online sales.
30. Providing Excellent Customer Service in Handmade Kanghi Industry
Customer service is key to building a loyal customer base in the handmade home décor industry. Artisans and business owners prioritize clear communication, timely responses, and addressing customer concerns. Providing a positive customer experience not only leads to repeat business but also generates word-of-mouth referrals, further enhancing the reputation of Kanghi products.
Exceptional customer service is crucial for building loyalty and reputation in the handmade home décor industry. Key practices include:
Clear Communication and Timely Responses:
Artisans and business owners ensure prompt and clear communication, addressing customer inquiries and concerns effectively to build trust.Positive Customer Experience:
Providing a seamless and positive shopping experience, including personalized support and hassle-free returns, encourages repeat business and word-of-mouth referrals.Custom Orders and Personalization:
Offering custom design options and personalized services enhances customer satisfaction and loyalty, catering to individual preferences and needs.After-Sales Support:
Providing ongoing support after purchase, such as maintenance tips or troubleshooting assistance, ensures customers feel valued and supported.Feedback Collection and Improvement:
Actively seeking and incorporating customer feedback helps improve products and services, demonstrating commitment to customer satisfaction and continuous improvement.
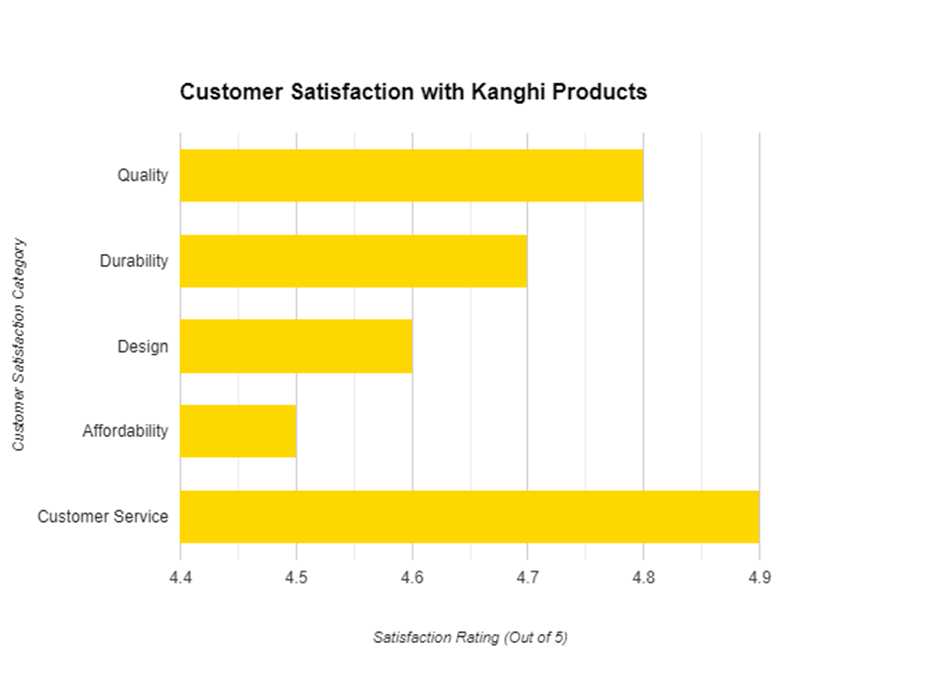
31. Conducting Credit Checks in the Handmade Kanghi Industry
Before entering into business agreements, it is important to conduct credit checks on potential partners and clients. This due diligence helps in assessing the financial reliability of the other party, reducing the risk of non-payment or fraud. By conducting credit assessment checks, artisans and business owners protect their interests and ensure smooth financial transactions.
Q&A
Q: Why are credit checks important in the handmade home décor industry?
A: Credit checks are essential to assess the financial reliability of potential business partners and clients. They help mitigate the risk of non-payment or fraud, ensuring that artisans and business owners are protected in their transactions.
Q: How do you conduct a credit check?
A: Start by requesting financial references or using credit reporting services to obtain a detailed credit history of the other party. Evaluate their payment history, outstanding debts, and overall financial health before entering into any agreements.
Q: What should you do if a credit check reveals red flags?
A: If there are concerns, consider negotiating safer payment terms, such as upfront payments or shorter payment cycles, to minimize risk. In some cases, it may be best to avoid the transaction altogether if the risk is too high.
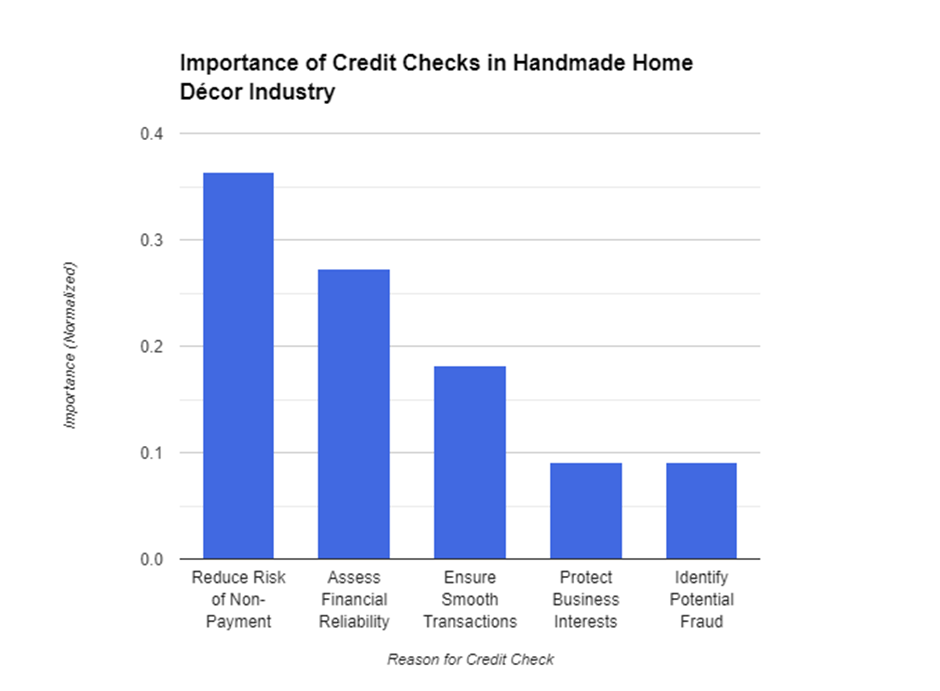
32. Protecting Kanghi Making Business with Insurance
Insurance is essential for protecting the Kanghi-making business from unforeseen risks. Artisans and business owners can obtain various types of insurance, such as liability insurance, property insurance, and business interruption insurance, to safeguard their operations. This protection ensures that the business can recover quickly from any disruptions and continue to thrive.
Insurance is crucial for safeguarding the Kanghi-making business against unforeseen risks and ensuring operational continuity. Key types of insurance and their benefits include:
Liability Insurance: Covers legal costs and damages if the business is sued for injury or damage caused by the products.
Property Insurance: Protects against losses or damage to physical assets, such as tools, materials, and finished products, due to events like fire or theft.
Business Interruption Insurance: Provides financial support for lost income and ongoing expenses if the business is temporarily unable to operate due to covered incidents.
Product Liability Insurance: Covers claims related to defects or issues with the products that may cause harm to customers, offering peace of mind against potential legal claims.
Professional Liability Insurance: Protects against claims of negligence or errors in the professional services provided, including design consultations or custom orders.
Workers’ Compensation Insurance: Covers medical expenses and lost wages for employees who are injured on the job, ensuring their well-being and compliance with legal requirements.
33. Managing Currency Exchange Risks in International Trade by Kanghi Makers
For artisans involved in international trade, managing currency exchange risks is crucial. Fluctuations in exchange rates can impact the profitability of export deals. Strategies such as hedging, forward contracts, and working with financial experts can help mitigate these risks, ensuring that currency fluctuations do not adversely affect the business.
Hedging:
Kanghi makers use hedging strategies to lock in exchange rates for future transactions, minimizing the risk of adverse currency fluctuations.Forward Contracts:
They enter into forward contracts with financial institutions to secure exchange rates for future dates, ensuring pricing certainty.Currency Accounts:
Artisans maintain accounts in multiple currencies to streamline international transactions and reduce the need for frequent conversions.Financial Consultation:
Kanghi makers work with financial experts specializing in currency exchange to develop customized strategies that address their specific business needs.
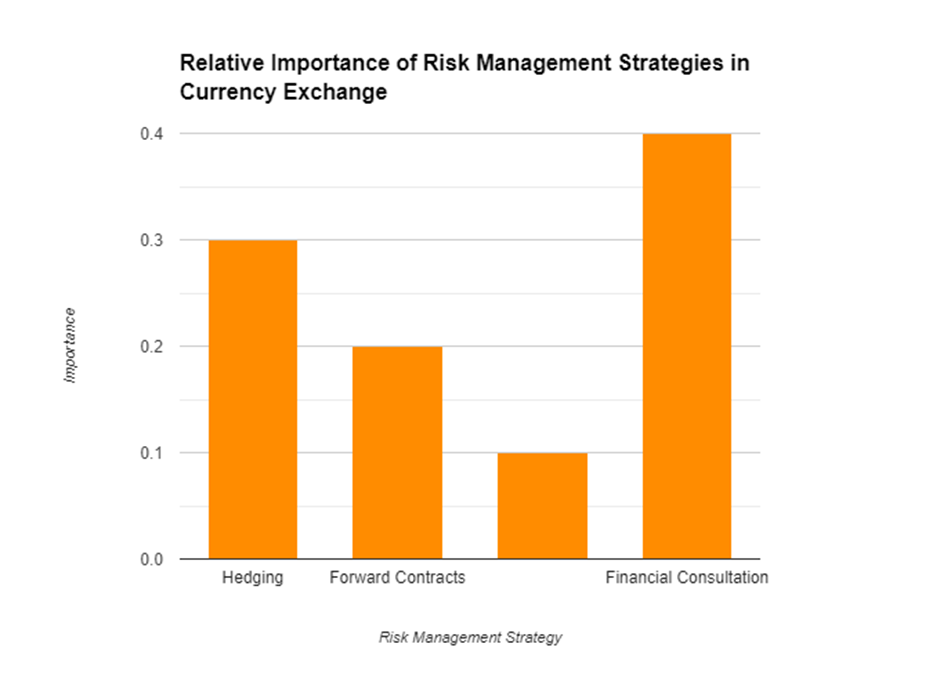
34. Conclusion
The making of Kanghi is a craft that reflects the ingenuity and resourcefulness of the people of Himachal Pradesh. It is a process that combines simple tools and natural materials with the artisan's expertise to create a product that is both functional and beautiful. As the world becomes more aware of the value of traditional crafts and the stories behind them, the Kanghi and the artisans who make it are gaining the recognition they deserve.
This craft is not just about making a tool; it is about preserving a way of life, a connection to the past, and a commitment to the future. The Kanghi is a small but essential part of the weaving process, and in its creation, we see the dedication to quality and tradition that defines the people of Himachal Pradesh. As we celebrate this craft, we also celebrate the resilience and creativity of the artisans who keep this tradition alive, weaving the threads of their heritage into the fabric of the present and the future.
35. Citation
Name of the original Author - Professor Bibhudutta Baral
Title of the Paper - Making of Kanghi - Himachal Pradesh
University/Institue Name - National Institute of Design (NID), Bengaluru
Date of when it was originally published - Not Mentioned in the Paper
Link to the Paper
Recommended
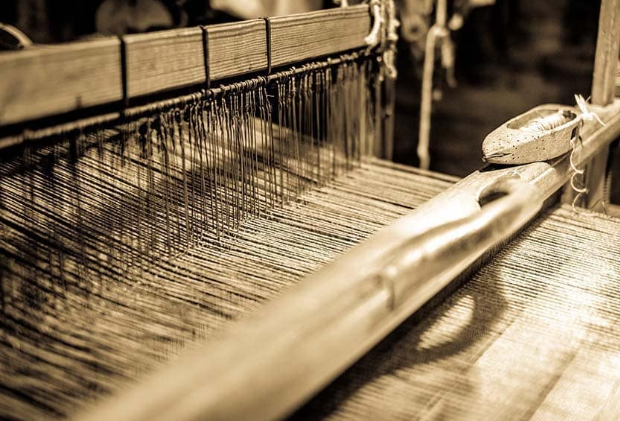
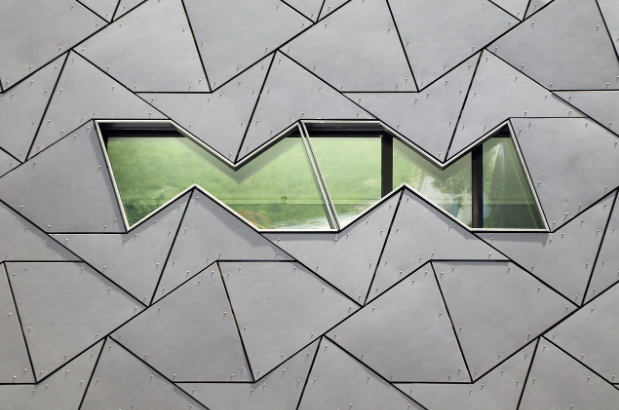
