The Sustainability Accounting Standard & Apparel, Accessories & Footwear
Jan 13, 2023 | Medini Perera
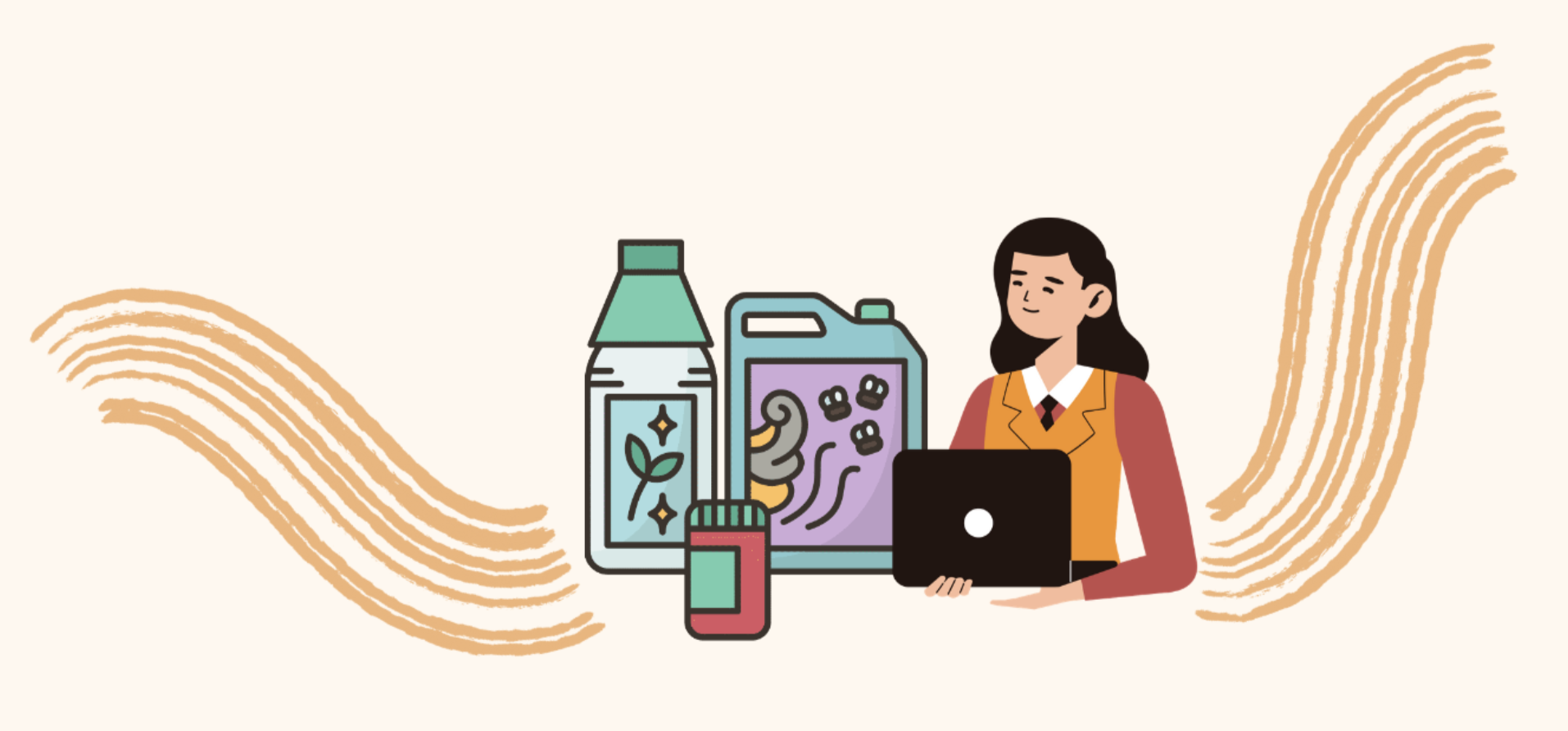
What is the use of SASB standards ?
The SASB guidelines are designed to be used when communicating with investors about sustainability-related issues that could affect a company's potential to generate value over the long term. A corporation chooses the standard(s) that apply to it, the disclosure issues that are financially significant to its operations, and the corresponding metrics that should be reported. The SASB criteria may not always cover all financially significant sustainability risks or opportunities that are particular to a company's business strategy.
There are 4 main topics of concern,
Management of Chemicals in Products
Environmental Impacts in the Supply Chain
Labour Conditions in the Supply Chain
Raw Materials Sourcing
Management of Chemicals in Products
A growing regulatory and stakeholder concern is shown in the introduction of the Consumer Product Safety Improvement Act in the U.S. and the Registration, Evaluation, Authorization, and Restriction of Chemicals legislation in the EU. There have been discoveries of banned or restricted compounds in finished garment and footwear goods. Failure to address this problem could lead to increased regulatory scrutiny and affect a company's social licence to operate.
Accounting metrics,
The entity must explain how it uses input stream management, restricted substance lists (RSL), material supplier agreements, finished product and product input laboratory testing, and input verification. RSLs are a list of compounds that the organisation prohibits from being used in raw materials, component parts, and finished goods. The organisation must also go over the testing and verification procedures it uses to ensure that its materials remain compliant with laws governing prohibited chemicals. Use an RSL that reflects the lowest permissible concentration of the regulated chemical that can be found in any regulation in all jurisdictions where the chemical is regulated worldwide. (AAFA RSL, February 2018 | Release 19, for instance).
Use one or more RSLs to add voluntary limits or chemical bans that go beyond the scope of the strictest international rules. The entity must make public the location of and if the restricted substances (RSL) it uses are accessible to the general public. The organisation must additionally make public the supplier tiers whose compliance with RSL requirements it has confirmed. Disclosures often match the Higg Brand & Retail Module of the Sustainable Apparel Coalition (SAC).
Information about the procedures used by businesses and operations to identify and manage potential risks and hazards related to materials, chemicals, and substances (hereafter "chemicals"). The management of chemicals used in manufacturing and production processes, or those linked to raw materials or parts of its products, is not included in the scope of disclosure. The entity must explain how it manages chemicals at each stage of the lifecycle of its products, including product planning and design, materials and chemical sourcing, manufacturing, completed goods testing, product labelling, and marketing. Additionally, it must explain how it works to incorporate alternative chemicals into product formulation and design as well as how it prioritises certain chemicals for reduction and/or elimination from its goods.
A product is deemed green if one or more green chemistry principles are applied during the product's design, material selection, manufacturing processes, use phase, and/or disposal at the end of its useful life. The company is allowed to say whether it looks into third-party certifications to confirm the chemical composition of its completed goods.
How to manage chemicals in products sustainably according to SASB standards?
The Sustainability Accounting Standards Board (SASB) provides industry-specific standards for companies to report on their sustainability performance, including on the sustainable management of chemicals in products. To align with SASB standards, companies can consider the following actions:
Identify and prioritize chemicals of concern: Identify the chemicals used in your products and assess their potential impacts on human health and the environment. Consider prioritizing the phase-out or substitution of chemicals that are of particular concern.
Evaluate and select safer alternatives: Consider alternative chemicals or materials that may be less hazardous and have a lower environmental impact. Use tools such as the GreenScreen for Safer Chemicals or the European Union's REACH regulation to help identify safer alternatives.
Minimize the use of hazardous chemicals: Look for opportunities to reduce the overall amount of hazardous chemicals used in your products. This might involve using smaller amounts of chemicals, designing products to be more durable or longer-lasting, or using multi-functional chemicals that can perform multiple tasks.
Properly label and communicate about chemicals: Clearly label products that contain hazardous chemicals and provide information about the potential risks and how to safely use and dispose of the products.
Safely manage and dispose of chemicals: Properly store, handle, and dispose of chemicals to minimize the risk of accidents or releases. Follow local regulations and best practices for chemical management and disposal.
Monitor and report on performance: Regularly monitor and report on the environmental performance of your products, including on the sustainable management of chemicals, to track progress and identify areas for further improvement. This can help to demonstrate to stakeholders that you are meeting SASB standards and addressing sustainability risks and opportunities in this area.
Environmental Impacts on the Supply Chain
Through water use and pollution, the apparel, accessories, and footwear sector strongly impacts environmental externalities. These effects could harm a company's reputation and eventually have an effect on cost structures. Companies across the industry are collaborating with suppliers to lessen their environmental effect as a result of increased scrutiny from stakeholders and customers.
Accounting metrics,
Tier 1 suppliers are those who conduct business directly with an entity, like producers of completed goods (e.g., cut and sew facilities). If a supplier complies with the limits defined by regional legal or regulatory requirements for each chemical, it is deemed to be in accordance with the relevant permits and/or contractual agreements. Disclosure of supply chain hazards including water from supplier facilities and an explanation of how these risks are managed. The range of disclosure includes, but is not limited to, stakeholder perceptions, increased liability and/or reputational risks, operational and financial limits, restrictions on discharges, increased operating costs as a result of regulation. The entity must briefly describe the wastewater treatment processes employed at supplier facilities before wastewater is discharged.
Reverse osmosis/ultrafiltration, biological decomposition, and screening and settling are among treatment techniques. The percentage of water treated and released into the environment by each treatment process may be disclosed by the entity (by volume).
The entity must disclose (1) the proportion of Tier 1 supplier facilities that have finished the Sustainable Apparel Coalition's Higg Facility Environmental Module (Higg FEM) assessment, and (2) the proportion of Tier 2 supplier facilities that have finished an equivalent environmental data assessment. Tier 1 suppliers are those who do business directly with the firm, such as makers of completed goods (e.g., cut and sew facilities).
How to minimise environmental impacts in the supply chain ?
There are a number of steps that companies can take to minimize environmental impacts in the supply chain:
Identify and prioritize environmental impacts: Conduct an environmental impact assessment to identify the key areas of impact in your supply chain, and prioritize those that are most significant or can be most easily addressed.
Engage with suppliers: Work with suppliers to understand their environmental practices and identify opportunities for improvement. Consider setting environmental performance targets for suppliers and providing support to help them meet these targets.
Use sustainable sourcing practices: Consider sourcing materials and products from suppliers who have demonstrated a commitment to sustainability and can provide evidence of their environmental performance.
Reduce energy and resource use: Look for opportunities to reduce energy and resource use throughout the supply chain. This might involve optimizing transportation routes, using more efficient equipment and processes, or finding alternatives to resource-intensive materials.
Promote waste reduction and recycling: Encourage waste reduction and recycling within your supply chain to reduce the environmental impact of waste.
Monitor and report on performance: Regularly monitor and report on the environmental performance of your supply chain to track progress and identify areas for further improvement.
Labour Conditions in the Supply Chain
Concern is developing over how employees are treated in the apparel, accessory, and footwear industry's supply chain. Fair compensation, child labor, forced labor, and employee health and safety are important facets of this topic. This dynamic may increase a company's vulnerability to hazards to its reputation and have an effect on both short- and long-term expenses and sales.
Accounting metrics,
A labor code of conduct is a company policy, regulation, or contract that specifies standards for suppliers and contractors regarding working conditions, labor practices, and environmental health and safety. Tier 1 suppliers are those that conduct business directly with the firm, such as producers of completed goods (cut and sew facilities). Manufacturers, processing facilities, and companies that extract raw materials are all considered Tier 2 suppliers. The range of audits carried out by the entity includes those carried out by a third-party auditor or an internal corporate representative. The organization may discuss how it evaluates and ranks its supply chain partners, including subcontractors, in order to establish the degree of risk each poses in terms of working conditions.
The entity is required to reveal the frequency of non-conformances by its suppliers with external labor code of conduct audit criteria as well as the frequency with which such cases have resulted in corrective action. Facilities that have been audited by the entity, by other brands, or by external third parties in lieu of audits undertaken exclusively for entity purposes are included in the scope of disclosures. The entity may give a breakdown by geographical area or by the supply chain levels (Tier 1, Tier 2, or other) where non-conformances occurred. It can highlight the top three risks to the entity's supply chain in terms of both environmental health and safety and labor conditions.
In relation to the standards outlined in the entity's labor code of conduct or audit criteria, labor conditions risks include the following: excessive working hours, infractions of the minimum age requirements, unfair compensation practices, a lack of freedom of association rights, and other risks related to labor conditions. Concerns to environmental health and safety can include unsafe levels of air and water pollution, incorrect handling of hazardous materials, violations in the disposal of solid waste and wastewater, or other risks that the institution has discovered.
How to improve labour conditions in the supply chains ?
There are several steps that companies can take to improve labor conditions in their supply chain:
Establish a clear code of conduct: Develop a code of conduct that outlines the company's expectations for labor practices in the supply chain. This should include standards for fair wages, working hours, and treatment of workers.
Engage with suppliers: Work with suppliers to understand their labour practices and identify opportunities for improvement. Consider setting labour performance targets for suppliers and providing support to help them meet these targets.
Monitor and assess supplier performance: Regularly monitor and assess the labour practices of your suppliers to ensure that they are meeting the company's standards. This might involve conducting audits, reviewing supplier self-assessments, or using third-party assessment organisations.
Provide training and support: Offer training and support to suppliers to help them improve their labour practices. This might include training on topics such as fair wages and safe working conditions.
Communicate with stakeholders: Communicate with stakeholders, including customers, employees, and investors, about the company's efforts to improve labour conditions in the supply chain. This can help to build trust and confidence in the company's practices.
Take corrective action: If labour violations are identified, work with suppliers to develop and implement a plan to address the issues and prevent future violations. Consider using remediation programs or other resources to help suppliers improve their labour practices.
Raw Materials Sourcing
The industry's capacity to consistently acquire materials is being shaped by factors such as climate change, land use, resource scarcity, and regional conflict. These variables can then have an effect on company risks like reputational hazards, supply interruptions, and material shortages. By interacting with suppliers, improving supply chain visibility, and utilizing certification standards, businesses may control these risks.
Accounting metrics,
The Textile Exchange's Materials Terminology Guide's concept of "priority materials" shall be used by the entity to identify priority raw materials. Synthetic, natural, produced cellulosic, animal-derived, and raw materials utilized directly in the production of clothing, accessories, or footwear are examples of priority raw materials. The entity shall provide its management strategy for handling business risks and opportunities related to environmental and/or social variables that are most likely to jeopardise its capacity to obtain priority raw materials. Relevant initiatives include improving traceability to raw material sources and supply chain visibility through due diligence procedures and research into traceability systems. The organisation may also go into detail on how vulnerable it is to cotton-growing areas that are experiencing water stress and how it mitigates the risk of price volatility from these areas.
The entity may use the following table format to organize disclosure.
Priority raw materials could include things like cotton, rayon, viscose, polyester, acrylic, spandex, rubber, foam, leather, wool, cashmere, mohair, flax, silk, hemp, and down that are used directly to manufacture clothing, accessories, or footwear products. Priority raw materials contained in completed items are included in the scope of disclosure, while raw materials utilised in manufacturing and packaging are not. Materials may come from a method that has received environmental and/or social certification from a third party. Materials may include, but are not limited to, recycled wool and cotton, nylon, lyocell, and polyester that has been chemically or mechanically recycled. The entity must state how many metric tons of each priority raw material were bought with certification for meeting environmental or social standards, broken down by standard.
For each priority raw material, the entity shall disclose the amount, in metric tons, purchased that is certified to a third-party environmental and/or social standard, by standard. Materials may include, but are not limited to, recycled wool and cotton, nylon, lyocell, and polyester that has been chemically or mechanically recycled.
the following table format can be used to organise disclosure.
How to sustainably source raw materials according to SASB standards?
Identify and prioritise materials: Conduct a materials assessment to identify the key raw materials used in your products or operations, and prioritise those that have the greatest environmental impact or are at risk of supply chain disruption.
Engage with suppliers: Work with suppliers to understand their environmental and social practices, and identify opportunities for improvement. Consider setting sustainability performance targets for suppliers and providing support to help them meet these targets.
Use sustainable sourcing practices: Consider sourcing materials from suppliers who have demonstrated a commitment to sustainability and can provide evidence of their environmental and social performance. Look for materials that have been produced sustainably, with minimal environmental impact, and that are sourced from responsible sources.
Consider recycled or recovered materials: Using recycled or recovered materials as raw materials can help to reduce the overall environmental impact of the materials used in your products or operations, and can also support the development of circular economy practices.
Engage with stakeholders: Engage with stakeholders, including customers, employees, and investors, to understand their sustainability priorities and how they might influence your sourcing decisions. This can help to ensure that your efforts to source sustainable raw materials align with the expectations of those who are important to your business.
Recommended
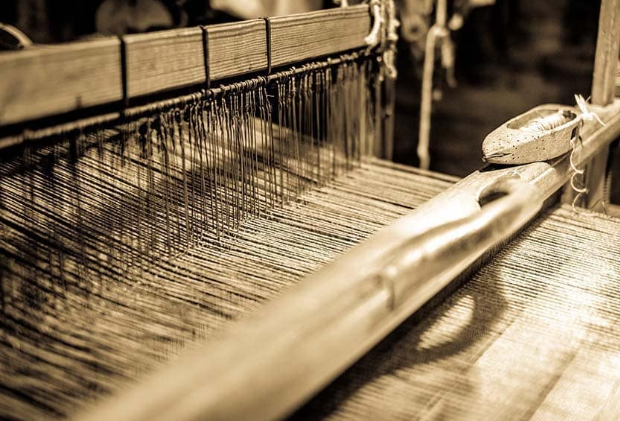
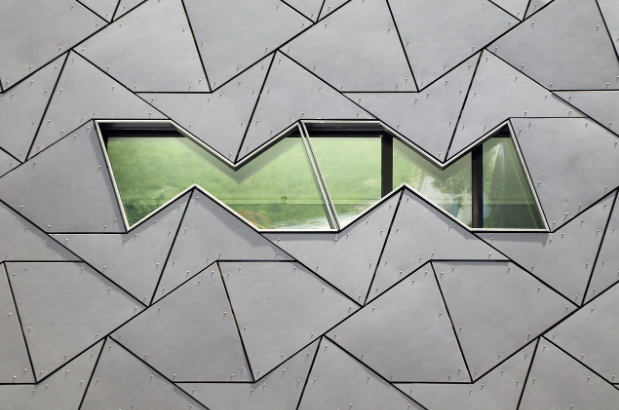
