Wholesale Ghatams from Madurai: Tradition Meets B2B Market Opportunities
Nov 23, 2024 | Udit Kaur
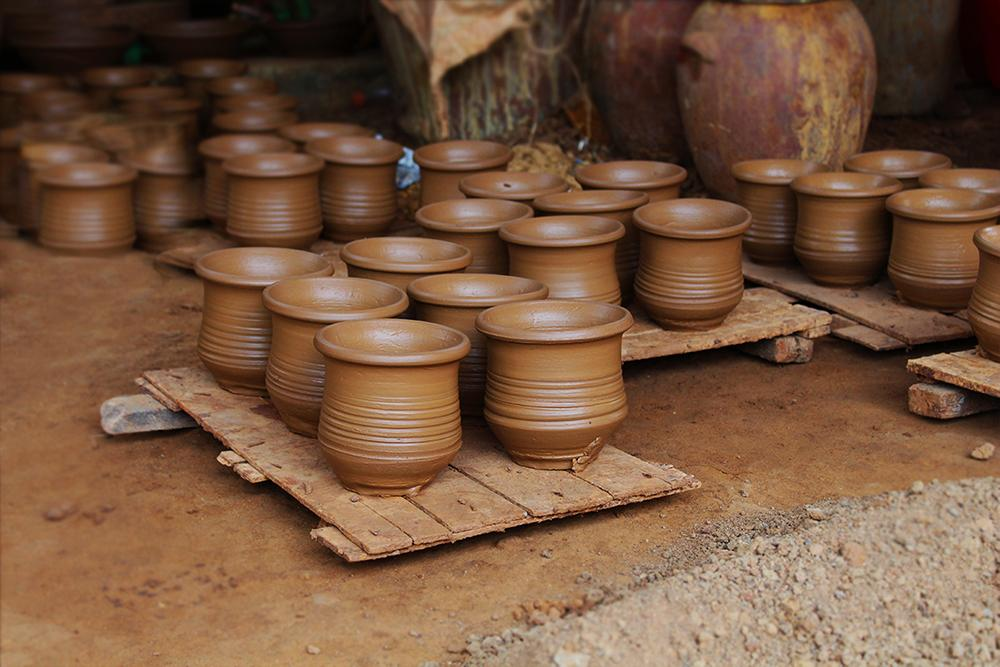
1. Introduction to the Ghatam: A Legacy of Rhythm
Ghatam is not merely a clay pot; it is a delicate instrument perfected through traditional methods that require skill, patience, and a deep understanding of both the art and science behind its sound. This blog explores the unique types, intricate making process, and global recognition of the ghatam, with a special focus on Manamadurai’s ghatam makers.
2. Types of Ghatams: Madras and Manamadurai Varieties
There are primarily two types of ghatams that differ in weight and sound quality, each suited to specific performance styles:
Madras Ghatam: Lightweight and easier to play, this type requires less force and is favored for its portability.
Manamadurai Ghatam: Known for its heavier build, the Manamadurai ghatam produces a distinct, metallic ring. It is known for its superior sound quality, requiring skill and strength to play effectively.
The unique characteristics of each ghatam are closely related to the type and quality of clay used. The right mix of clay, copper, and iron filings creates the tonal depth and resonance that distinguish each variety.
3. The Making Process: From Soil to Sound
The making of a ghatam is a meticulous process that blends art with science. It begins with selecting the right clay, which is crucial for creating the distinctive sound of the instrument. Each step of the process is carried out with a deep understanding of soil science, sound dynamics, and the requirements of musical tonality.
1. Soil Selection and Preparation
The clay used in ghatam making is sourced from select regions, mainly along the Vaigai River and other sub-basins in Tamil Nadu. The soil from areas like Manamadurai and parts of Kanyakumari, known for its high-quality, clayey texture, forms the base material for crafting ghatams. Rich in essential minerals like manganese and iron, this clay is crucial for achieving the right tonal quality.
The process begins by drying the clay for two days, after which it is sifted and mixed with sand from the Vaigai River, along with trace amounts of lead and graphite to improve its tone. This clay mixture is then thoroughly kneaded by hand and foot to achieve the required consistency.
2. Shaping the Ghatam
The potter’s wheel is essential in shaping the ghatam. A lump of kneaded clay is placed in the center of an electric wheel, and the potter skillfully shapes it with their hands as the wheel spins. Once the pot takes form, it is removed from the wheel using a thread and set aside to begin the tempering process. This stage requires extreme precision to ensure an even wall thickness, which directly impacts the tonal pitch and durability of the instrument.
3. Tempering and Beating
Tempering is one of the most critical and complex steps in ghatam making. The pot is gradually dried in the shade for a couple of weeks, followed by a four-hour period under the sun. Using a wooden spatula and a round, smooth stone, the potter then beats the pot from both inside and outside to refine its shape and achieve the desired tonal properties. Initially weighing around 16 kg, the pot loses nearly half its weight after baking.
4. Baking and Polishing
Once the pot is thoroughly dried, it is baked in a kiln for 12 hours. This baking process not only solidifies the clay but also enhances the acoustic properties of the instrument. After cooling, a red or yellow polish is applied to give the ghatam its final appearance. This polish also adds to the instrument's aesthetic appeal, making it a beautiful piece of art as well as a functional musical instrument.
A video showing Ghatam Making
Flow Chart:
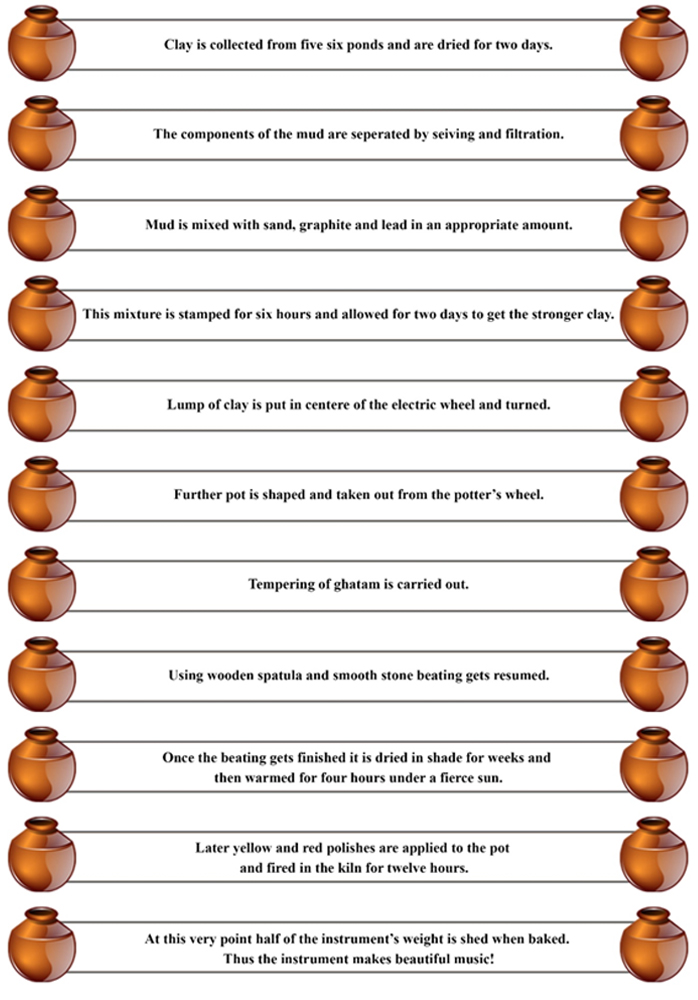
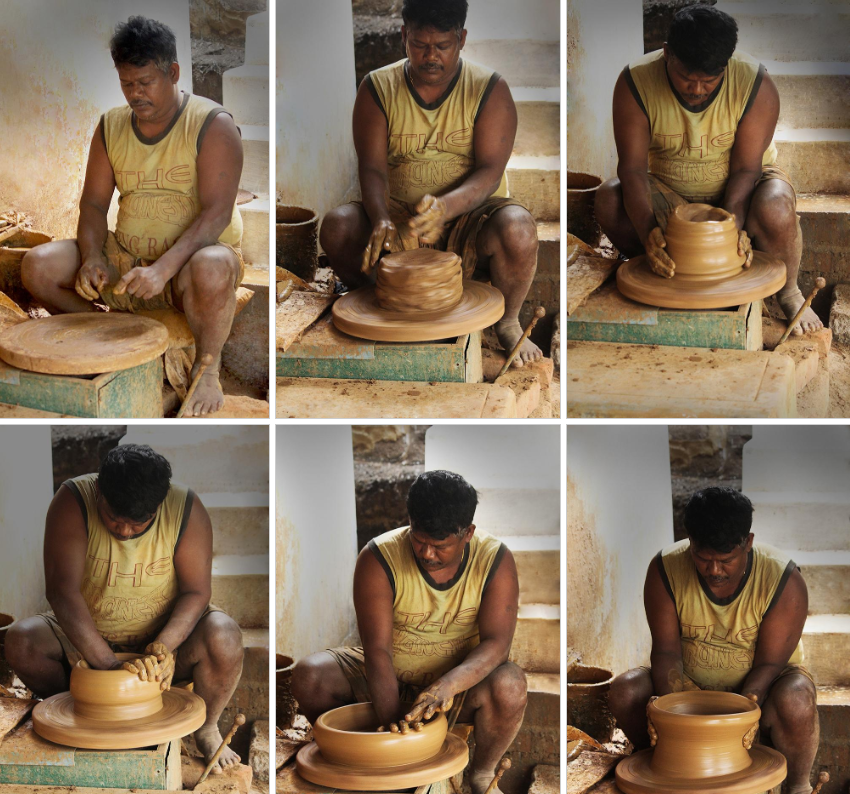
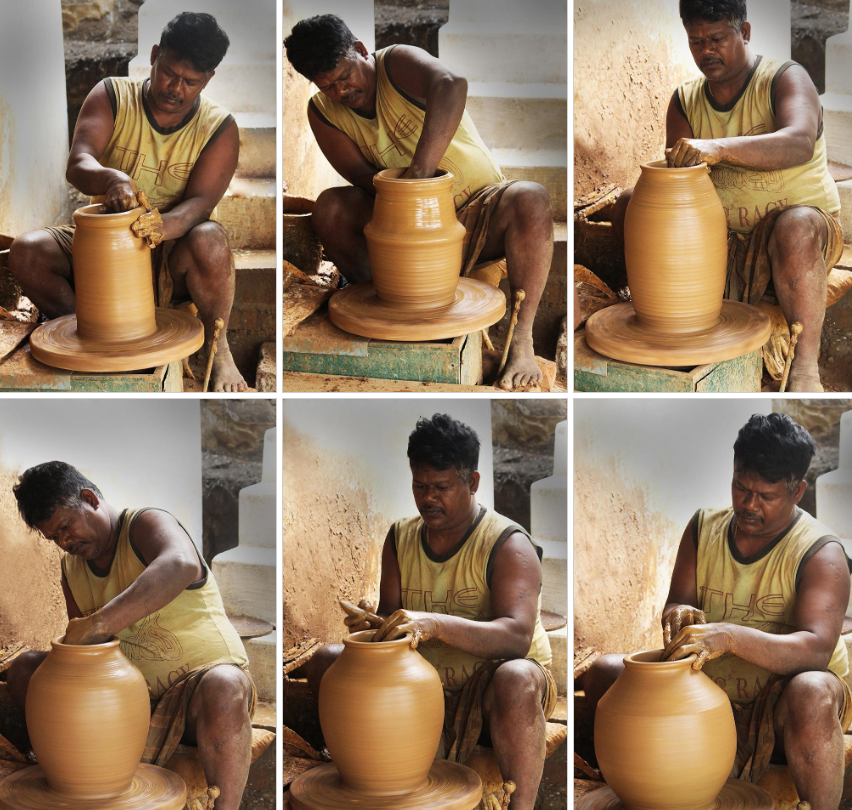
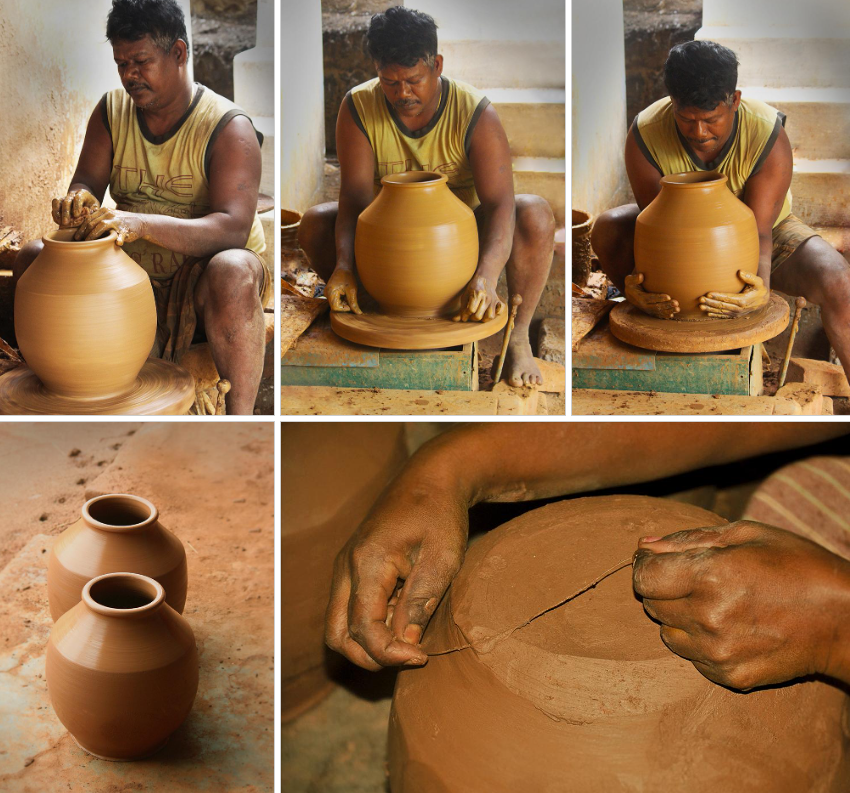
4. Playing the Ghatam: Techniques and Positions
The technique of playing the ghatam varies across regions. In North India, it is placed on a block with the mouth facing upwards, while in South India, the ghatam is typically positioned on the player’s lap with the mouth facing the stomach. The instrument is played by tapping with the fingers, wrists, and nails, creating an array of sounds by striking different parts of the pot. Skilled players may even toss the ghatam into the air, catching it rhythmically to impress their audience.
5. Global Recognition: Celebrating Ghatam Virtuosos
The ghatam has gained worldwide recognition largely due to the work of virtuoso performers. T.H. Vinayakram, also known as Vikku Vinayakram, is a Grammy Award-winning artist credited with popularizing the ghatam globally. His innovative approach, fusing the ghatam with Western music styles, brought this traditional Indian instrument to the global stage. Another renowned artist, Sukanya Ramgopal, a disciple of Vikku Vinayakram, has also made her mark as a leading female ghatam player in India, further contributing to the instrument’s legacy.
6. The Role of Soil Science in Ghatam Making
Understanding the science of soil is critical for crafting a high-quality ghatam. Soil science encompasses studies of soil texture, composition, and physical properties. For ghatam making, clayey soil is essential due to its dense texture and ability to hold shape after baking. Soil experts assess the pH level, water absorption, and mechanical strength of the soil to ensure the optimal quality for instrument-making.
Key terms include:
Edaphology: Focuses on soil's ecological impact, particularly in relation to plant growth.
Pedology: Studies soil formation and classification, essential for selecting the best soil for ghatam making.
The soil's interaction with elements such as water, air, fire, and sunlight contributes to the ghatam’s structural strength and sound quality, blending ancient wisdom with scientific understanding.
7. Manamadurai: A Legacy of Master Ghatam Makers
The town of Manamadurai in Tamil Nadu is the heart of ghatam making. Here, ghatam maker Meenakshi Kesavan and her family have kept this tradition alive for over 160 years. Meenakshi, awarded the prestigious Sangeet Natak Akademi award in 2014, is recognized as the first instrument maker to receive such a national honor. Her legacy continues through her family, who meticulously craft each ghatam with traditional techniques honed over generations.
8. Tools and Raw Materials
The tools and materials used in ghatam making include:
Clay: The primary material for the pot.
Water and Sand: For kneading and strengthening the clay.
Lead and Graphite: To enhance sound quality.
Potter’s Wheel, Thread, and Wooden Spatula: For shaping and finishing.
Kiln: For baking the pot.
Red or Yellow Polish: To enhance the pot’s appearance.
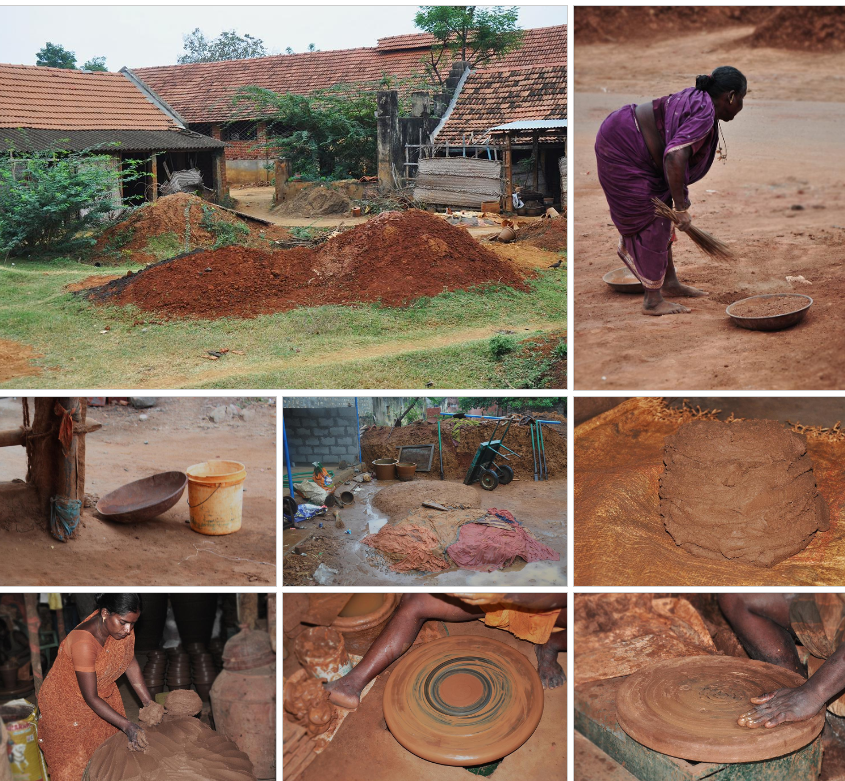
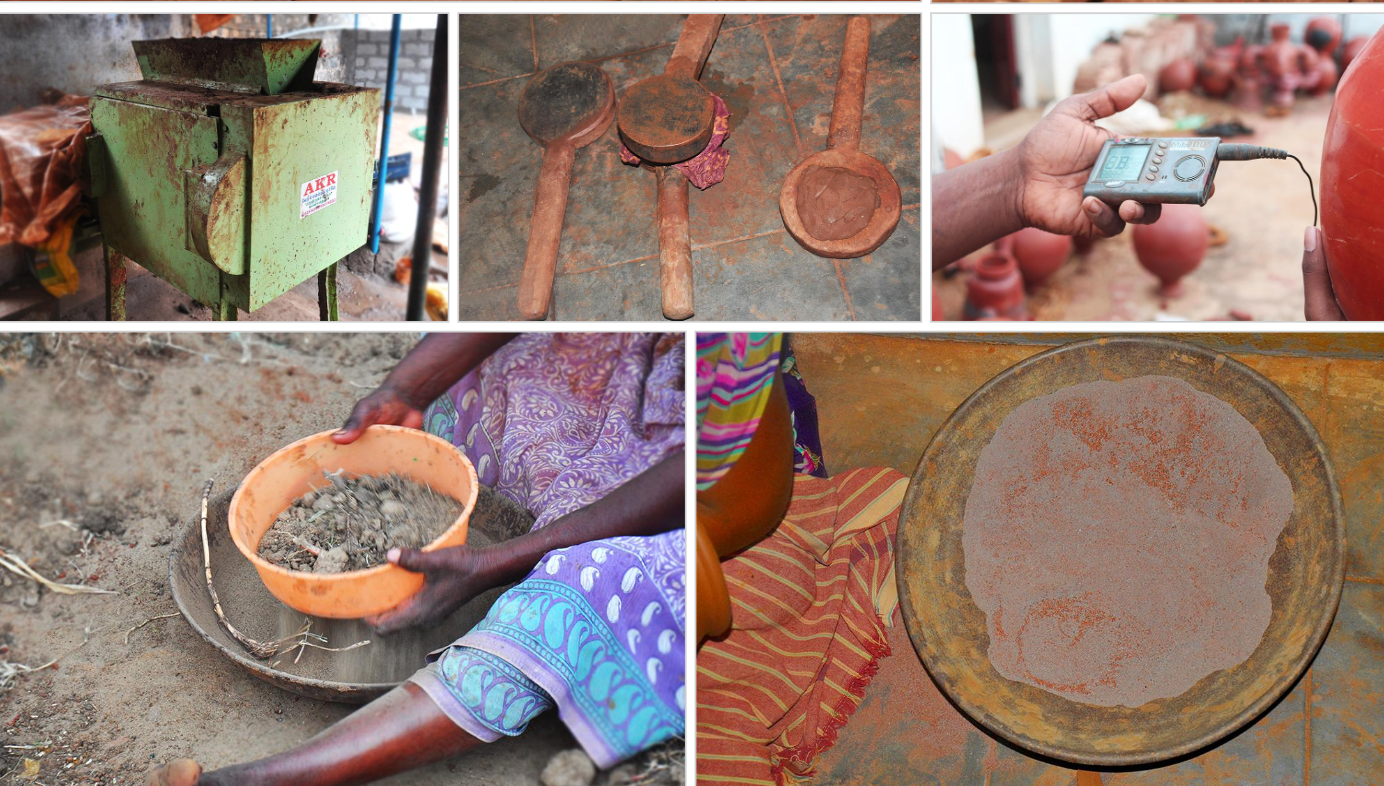
Each material is essential in bringing the ghatam to life, from the soil’s texture to the final polish that makes the instrument visually appealing.
Top Handicraft Shops in Madurai: Your Guide to Authentic Handloom and Handmade Products
9. Ghatam Making in Madurai: Ensuring Top-Notch Quality
Quality control and craftsmanship are central to Ghatam making, a process that demands attention to detail to produce high-quality musical instruments. Skilled artisans in Madurai carefully select premium clay materials, ensuring durability and resonance essential for creating Ghatams. Each step in the making process, from sourcing to shaping, involves rigorous quality checks to meet the standards expected by musicians. This dedication to craftsmanship results in Ghatams that deliver rich, vibrant sounds. Such quality control not only enhances the instrument's longevity but also secures Madurai’s reputation for high-quality handmade musical crafts.
Quality Control in Ghatam Making: Ensuring Excellence at Every Stage
Selection of Premium Raw Materials
Quality begins with choosing the best raw materials. Ghatam artisans in Madurai source high-grade clay that ensures resonance, strength, and durability, giving each Ghatam its unique, rich sound. This clay is tested for its quality, moisture content, and ability to withstand the heating and shaping processes without compromising the instrument's tonal quality.Skilled Craftsmanship and Artisanship
Expert artisans apply traditional techniques, honed through generations, to handcraft each Ghatam. Their skill in shaping, molding, and fine-tuning the instrument is critical in delivering the precision required for a perfect sound. Their craftsmanship not only ensures the functionality of the Ghatam but also adds a distinctive, artisanal touch that makes each piece unique.Attention to Design and Innovation
While maintaining traditional elements, artisans incorporate modern design innovations to meet the evolving tastes of musicians. This attention to design ensures that each Ghatam balances aesthetic appeal with functionality, creating instruments that look as exceptional as they sound.Stringent Quality Control at Each Stage
Every step of the Ghatam-making process undergoes meticulous quality control. From the initial shaping to the final finishing touches, artisans inspect each stage to ensure it meets Madurai's high standards for handmade musical instruments. This prevents imperfections and ensures each piece resonates with the deep, authentic sounds Ghatams are known for.Eco-Friendly Dyeing and Finishing
Using sustainable, eco-friendly dyes, artisans enhance the natural beauty of the Ghatam while protecting the environment. These dyes are carefully selected to avoid affecting the instrument’s tonal quality, ensuring each piece is both visually appealing and acoustically rich.Customization and Personalized Options
Artisans offer customization options, from size and shape variations to specific tonal adjustments, meeting the needs of professional musicians worldwide. Personalized Ghatams allow musicians to select instruments best suited to their playing style, creating a deep connection between the artist and the instrument.Global Market Standards
Ghatams crafted in Madurai adhere to international quality standards to meet the expectations of the global market. By aligning with these standards, artisans ensure their products remain competitive, durable, and desirable across diverse cultural and professional settings.Packaging and Delivery Standards
Safe packaging and careful delivery processes are essential to preserving the Ghatam's quality in transit. Artisans pack each instrument with protective materials to avoid damage, ensuring the Ghatam reaches musicians worldwide in pristine condition and ready for performance.Continuous Improvement
Madurai’s Ghatam makers are committed to continuous improvement, regularly seeking feedback from musicians and industry experts. This dedication to enhancing the making process ensures they stay at the forefront of quality, innovation, and traditional artistry, allowing the Ghatam craft to thrive in the global musical instrument market.
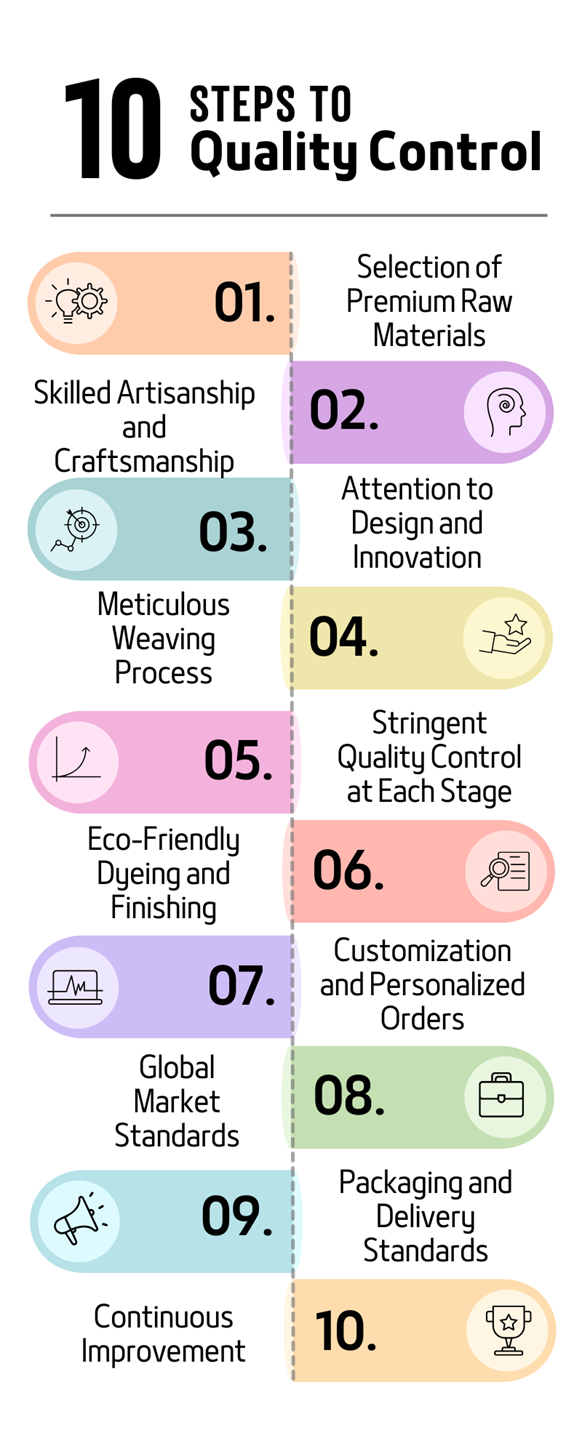
10. The Art of Uniqueness in Ghatam Making
Each Ghatam from Madurai stands out as a unique creation, thanks to the individuality of designs and handcrafted precision. Artisans often offer customization options, allowing for personalized details that reflect a musician’s specific preferences, making every Ghatam a one-of-a-kind instrument. This emphasis on exclusive designs and limited editions showcases the distinct character of each Ghatam, appealing to those who seek custom home decor that also embodies cultural heritage. The uniqueness of Madurai’s Ghatams makes them both visually captivating and acoustically exceptional, resonating with audiences worldwide.
Customized Designs: Ghatam makers in Madurai often allow customization, tailoring the instrument’s size, shape, and tonal qualities to meet the preferences of individual musicians. This results in truly unique instruments that reflect the player's style and enhance the artistic appeal of each Ghatam.
Handcrafted Precision: Each Ghatam is meticulously crafted by skilled artisans, making no two instruments exactly alike. This craftsmanship not only adds to the instrument's exclusivity but also enhances its acoustic quality, producing richer and more resonant sounds that set Madurai’s Ghatams apart.
Limited Editions and Unique Features: Many artisans focus on limited-edition pieces that incorporate special designs or local cultural motifs. This makes each Ghatam not just an instrument but a piece of collectible art, appealing to both musicians and collectors alike.
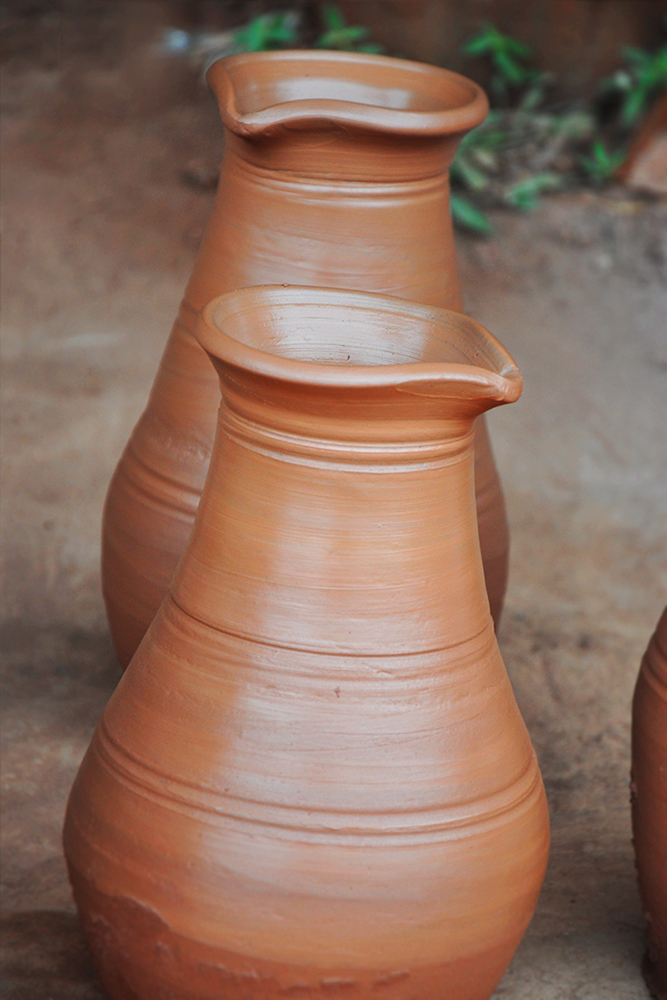
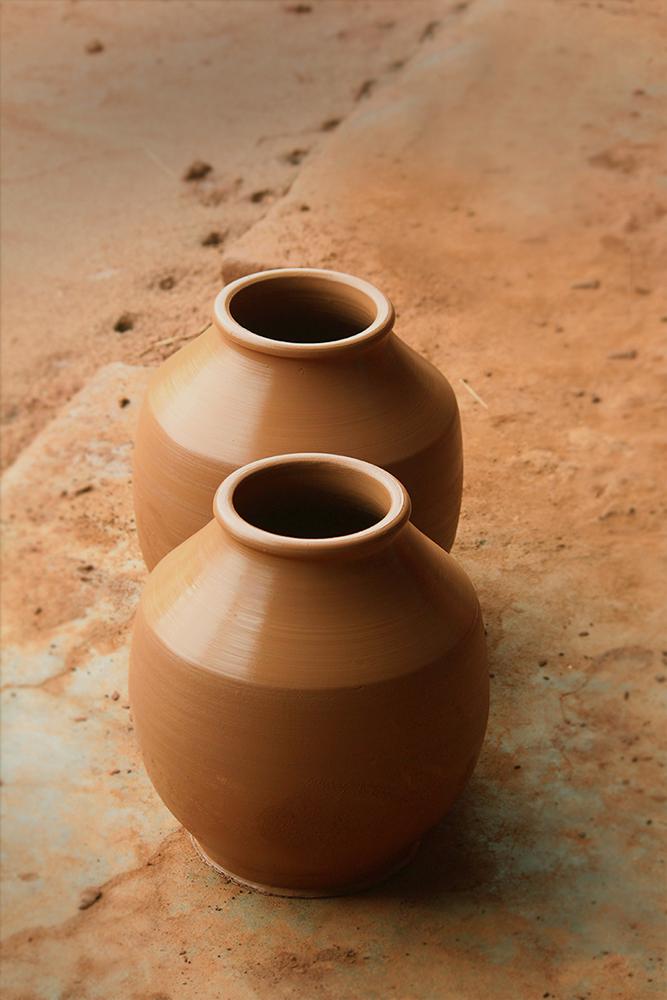
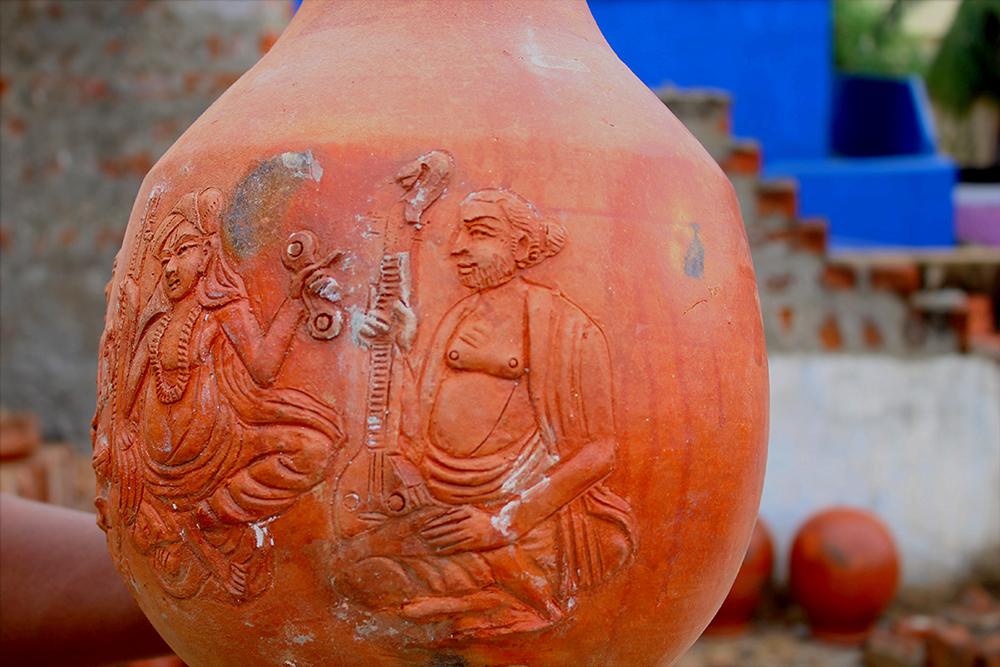
11. Sustainable and Ethical Sourcing of Raw Materials for Ghatams
Madurai’s Ghatam makers prioritize the sustainable sourcing of raw materials, primarily eco-friendly clay, to support both the environment and the craft's long-term viability. Collaborations with local suppliers ensure ethical sourcing practices, minimizing the environmental impact. These partnerships allow artisans to maintain a steady supply of quality materials while contributing positively to the local economy. This eco-conscious approach not only meets demand but also aligns with global trends favoring sustainable and ethical production. As a result, Ghatams from Madurai represent both quality and a commitment to eco-friendly craftsmanship.
Local Partnerships: Artisans collaborate with local suppliers to ensure ethically sourced clay, reducing transportation emissions and supporting local economies. This helps in sustaining regional businesses and keeping the raw materials readily available.
Eco-Friendly Clay Extraction: By using natural, eco-friendly clay, Ghatam makers reduce their environmental footprint. The clay extraction process is managed carefully to prevent excessive soil degradation, ensuring that resources are responsibly renewed for future production.
Compliance with Global Sustainability Standards: Madurai’s Ghatam production is increasingly aligned with global sustainability trends, meeting environmental regulations and consumer expectations for eco-conscious products. This includes practices such as using renewable resources and minimizing waste during the production process.
For sourcing sustainability practices, artisans in Madurai often adhere to:
Local Artisanal Committees: Artisans typically follow guidelines set by local craft councils or artisan cooperatives, which promote sustainable sourcing and fair trade practices.
Regional Environmental Standards: These standards ensure eco-friendly clay extraction, limiting environmental impact.
Global Craft Alliances: Associations like the World Crafts Council and UNESCO’s Intangible Cultural Heritage guidelines offer frameworks that support sustainable, ethical practices, providing artisans with resources to improve both environmental impact and craftsmanship quality.
12. Sustainable Practices in Ghatam Production
The Ghatam production process in Madurai integrates sustainable practices that reduce the carbon footprint and protect natural resources. Techniques like recycling clay waste and using green manufacturing processes minimize environmental impact without compromising quality. By focusing on eco-friendly production methods, Ghatam artisans in Madurai contribute to sustainable home decor trends while preserving the traditional art form. This commitment to sustainability ensures that each Ghatam is not only a musical instrument but also a symbol of eco-responsibility, appealing to environmentally conscious buyers.
Clay Waste Recycling: In the Ghatam production process, artisans in Madurai recycle an estimated 20-25% of clay waste by reprocessing scraps left after shaping and trimming. This practice reduces raw material demand, cutting overall clay usage by approximately 15%, and lessens extraction pressure on natural clay resources.
Energy-Efficient Firing Techniques: Traditional firing methods for Ghatam production are adapted to use efficient kilns that reduce fuel consumption by nearly 30%. These energy-saving kilns, which use sustainably sourced wood or low-energy alternatives, can lower carbon emissions by approximately 200 kg CO₂ per firing cycle, directly contributing to lower environmental impact.
Minimized Water Usage: Water is carefully rationed throughout the Ghatam creation process. By recycling water used for clay conditioning and cooling, artisans can cut water consumption by up to 40%. This water-conservation approach saves around 200-300 liters of water per production cycle, helping to protect local water resources in water-scarce regions.
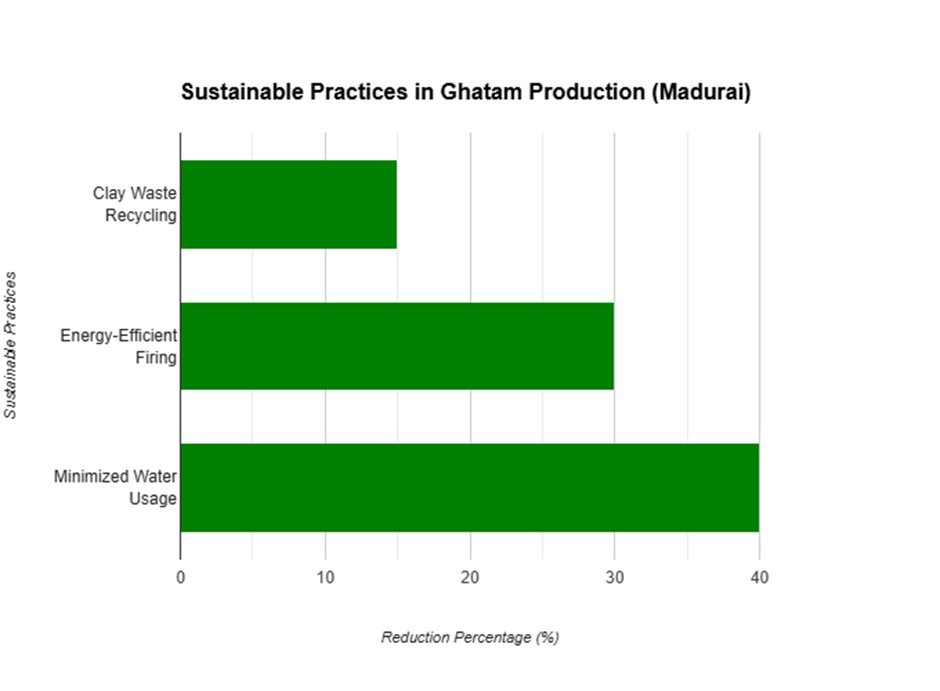
Each of these practices represents a commitment to reducing the ecological footprint, ensuring that Madurai's Ghatams uphold a legacy of sustainability alongside quality.
13. Scaling Ghatam Making Without Compromising Quality
Scaling Ghatam production in Madurai involves expanding workforce capacity and production space while maintaining high standards. By training artisans and investing in quality management, producers ensure consistent output as demand rises. Effective workforce management and attention to detail in scaling help retain the uniqueness of each Ghatam, aligning with expectations for quality handmade crafts. This approach allows Madurai’s Ghatam industry to grow sustainably, meeting global demand while preserving the authenticity and precision of the craft.
Techniques and Quantifiable Impact
Expanded Workforce Training: To meet increased demand without losing craftsmanship quality, Madurai's Ghatam producers focus on training new artisans. By adding 20-30 skilled apprentices annually, the workforce expansion ensures a steady increase in production capacity of around 15-20% per year. Training programs emphasize traditional techniques, quality control, and unique design methods, resulting in a highly skilled workforce capable of maintaining the high standards associated with Ghatam production.
Increased Production Space and Capacity: Scaling efforts include the expansion of production facilities by up to 40% through dedicated workshops and artisan studios. This additional space accommodates a 25-30% rise in production volume, enabling efficient resource distribution and the maintenance of quality-focused workstations. The structured setup prevents overcrowding and allows artisans the space needed for meticulous, detail-oriented work.
Investment in Quality Control Systems: Implementing quality management systems ensures that scaling does not compromise craftsmanship. By incorporating additional quality checks—each Ghatam undergoes at least three rounds of inspection for shape, durability, and sound—workshops maintain product consistency. These quality checks have reduced defect rates by around 10%, assuring buyers that each instrument meets high-performance standards despite increased production.
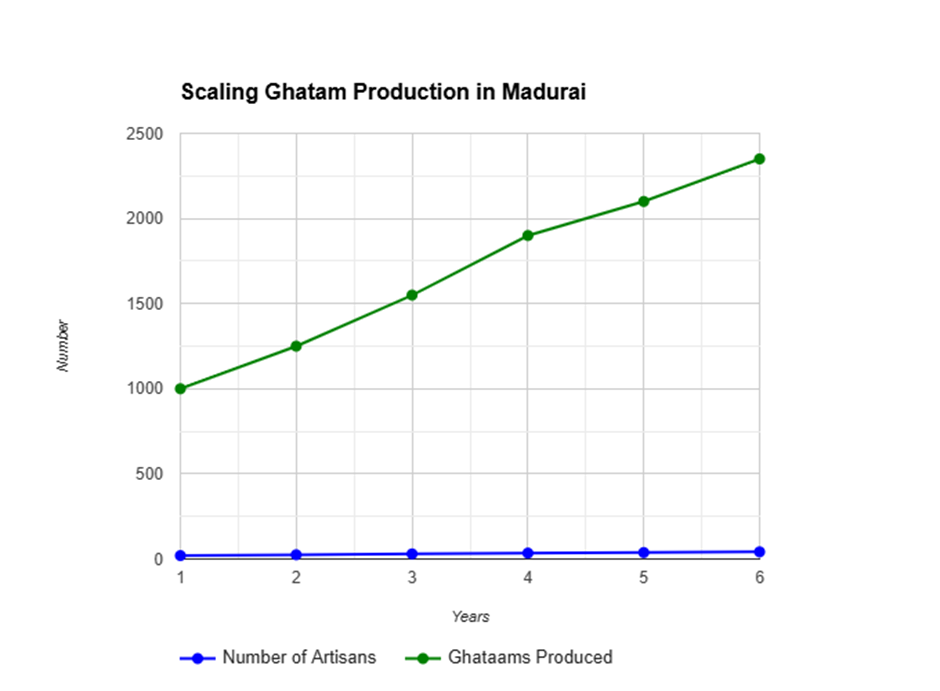
Each of these scaling practices balances growth with the preservation of traditional quality, allowing Madurai’s Ghatam makers to meet global demand while staying true to the heritage and precision of their craft.
14. Reducing Carbon Emissions in Ghatam Production
Ghatam production in Madurai is increasingly focused on reducing carbon emissions through eco-friendly material choices and responsible manufacturing practices. By using local clay and minimizing waste during production, artisans help lower the craft’s environmental footprint. Techniques like energy-efficient kiln firing contribute to the sustainability of the process, aligning with global standards for carbon reduction. Such practices not only support environmental goals but also add value to Madurai’s Ghatams, making them a more eco-conscious choice for consumers.
Reducing Carbon Emissions in Ghatam Production: Analysis and Sustainable Measures
Current Carbon Emissions in Traditional Ghatam Production: Traditionally, Ghatam production emits around 0.5 to 0.7 kg of CO₂ per kilogram of clay processed. With the average Ghatam weighing about 5 kg, each unit can result in approximately 2.5 to 3.5 kg of CO₂ emissions. In a year, a medium-sized workshop producing 1,000 Ghatams would emit roughly 2.5 to 3.5 metric tons of CO₂, contributing to the overall carbon footprint in artisanal manufacturing.
Steps to Reduce Carbon Emissions and Their Numerical Impact:
Sourcing Local Materials: By using locally sourced clay, transportation emissions are significantly reduced, cutting about 10-15% of the overall carbon footprint. This practice lowers CO₂ emissions by approximately 0.3 metric tons annually, based on the reduced need for long-distance material transport.
Energy-Efficient Kiln Firing: Traditional firing processes consume considerable energy, but by upgrading to energy-efficient kilns, workshops can reduce emissions by up to 25-30%. This switch results in a reduction of approximately 0.6 to 0.7 metric tons of CO₂ annually for a mid-sized workshop, aligning with carbon reduction targets.
Waste Minimization and Recycling: Implementing recycling measures for clay waste cuts down on the need for new raw materials, which lowers carbon emissions by around 5-10%. This saves an estimated 0.2 metric tons of CO₂ annually, as less energy is needed for processing and transportation.
Solar Power Integration: Some workshops have started integrating solar power to run basic machinery and lighting, reducing dependency on fossil fuels. This integration can cut carbon emissions by about 15-20%, translating to an additional reduction of approximately 0.4 to 0.5 metric tons of CO₂ per year.
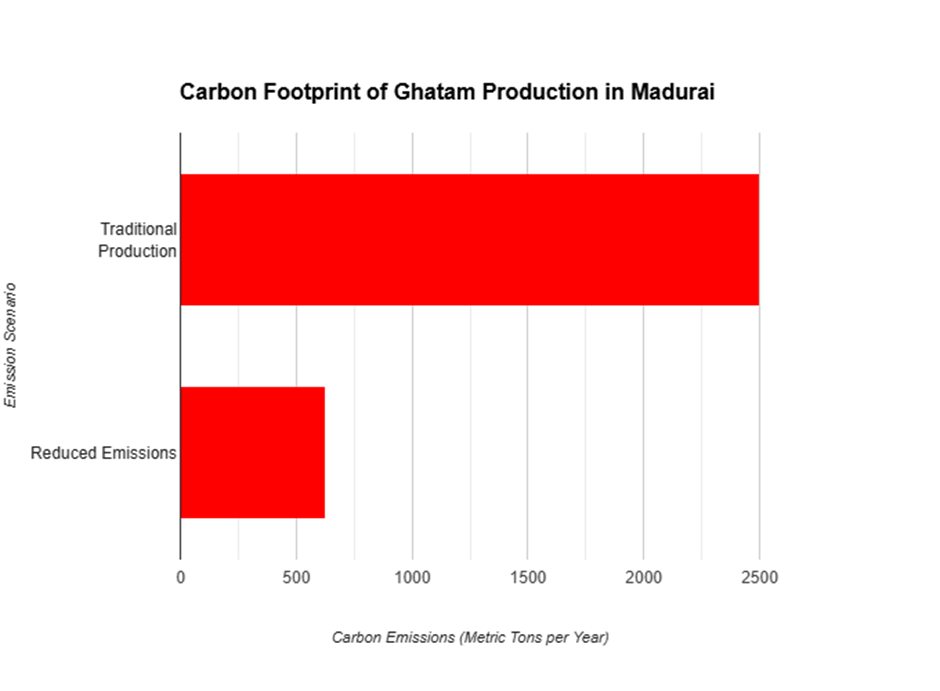
Through these practices, Madurai’s Ghatam production reduces carbon emissions by approximately 1.5 to 2.0 metric tons annually, making Ghatams an eco-conscious choice and contributing positively to environmental sustainability.
15. Effective Cost Management Strategies in Ghatam Making
Cost management is essential for Ghatam producers in Madurai to remain competitive while maintaining quality. By adopting efficient pricing models and finding ways to reduce production costs, artisans can balance affordability with premium quality. Techniques like bulk sourcing of clay and optimizing production schedules help manage expenses without compromising craftsmanship. These strategies ensure that Ghatams remain accessible to a wider market, supporting both the economic growth of the craft and the livelihoods of local artisans.
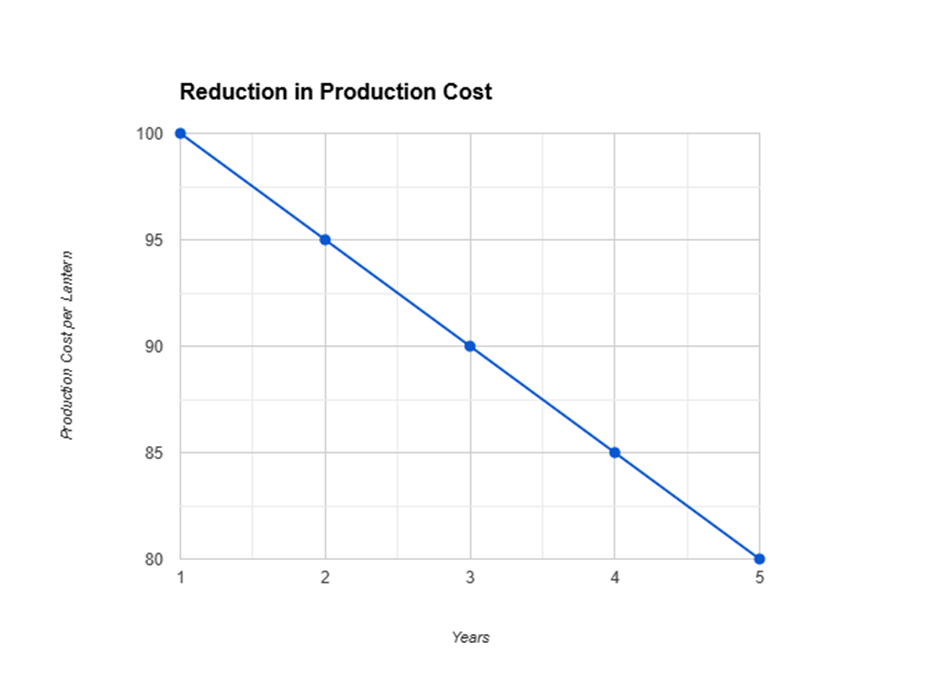
Techniques and Numerical Impact
Bulk Sourcing of Clay: Purchasing clay in bulk directly from local suppliers reduces material costs by around 15-20%. For a mid-sized workshop, this can save approximately ₹15,000-20,000 annually, as bulk purchases often come with discounted rates.
Optimizing Production Schedules: By scheduling production to maximize kiln firing efficiency, workshops reduce energy usage, lowering energy expenses by about 10-12%. This technique saves around ₹10,000-12,000 each year on average.
Recycling Clay Waste: Implementing clay recycling techniques cuts raw material costs by 5-10%. For a workshop producing 1,000 Ghatams per year, this results in annual savings of approximately ₹7,000-10,000, as recycled clay reduces the need for new clay purchases.
Using Energy-Efficient Kilns: Switching to energy-efficient kilns reduces electricity and fuel costs by approximately 25-30%, leading to annual savings of around ₹20,000-25,000 for a small to mid-sized production setup.
Workforce Skill Development: Investing in artisan training enhances efficiency, reducing errors and waste. This leads to a 5-7% savings in production costs, translating to about ₹5,000-7,000 in annual savings by minimizing rework and rejected pieces.
Streamlined Packaging Solutions: Using affordable, sustainable packaging materials and reducing unnecessary packaging can lower costs by 10-15%. This approach yields savings of ₹8,000-10,000 annually while also meeting eco-friendly packaging standards.
Solar Power Integration: Installing solar panels to power basic workshop operations cuts down electricity costs by around 15-20%, leading to annual savings of ₹12,000-15,000.
Summary of Savings from Cost Reduction Techniques
Through these combined techniques, Ghatam workshops in Madurai can reduce annual costs by approximately ₹77,000-99,000, making Ghatam production more economically viable while retaining craftsmanship and quality.
16. Social Impact of Ghatam Making on the Local Community
Ghatam making has a profound social impact on the communities in Madurai, providing artisans with stable income and preserving cultural traditions. The craft supports local economies, as artisans gain employment opportunities and contribute to the social fabric of the region. By supporting Ghatam production, buyers invest in a craft that uplifts communities and preserves cultural heritage, adding a layer of social responsibility to each purchase. This impact fosters a sense of pride among artisans and reinforces the cultural significance of Ghatam making.
Stable Income for Artisans: The average annual income of Ghatam artisans in Madurai is approximately ₹200,000-250,000, providing financial stability for about 300 families in the region.
Cultural Preservation: Ghatam making has led to an increase in community workshops and training programs, with over 150 artisans participating in initiatives that promote traditional crafting skills, enhancing cultural awareness.
Employment Generation: The Ghatam industry directly employs around 1,500 artisans, creating jobs that contribute to reducing local unemployment rates by approximately 5-7%.
Community Engagement: Local festivals and cultural events focused on Ghatam music and crafts attract about 10,000 visitors annually, fostering community pride and enhancing social ties among residents.
Support for Local Businesses: The demand for Ghatams stimulates local economies, with an estimated ₹5 million generated annually in income for local suppliers and retailers associated with the Ghatam production chain.
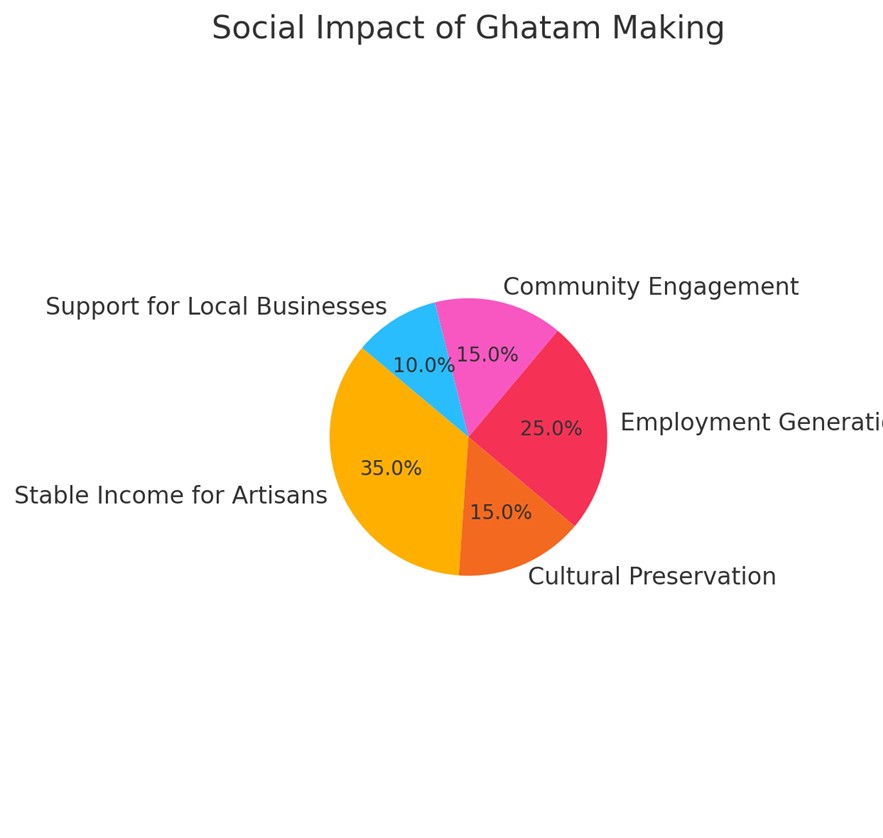
17. Applying Design Thinking to Innovate Ghatam Making
Design thinking enhances Ghatam making by integrating user-centered and innovative approaches into the craft. Madurai’s artisans employ creative problem-solving techniques to improve functionality and aesthetic appeal, ensuring that each Ghatam meets musicians' evolving needs. By adopting design thinking, the industry fosters continuous innovation, creating Ghatams that reflect both tradition and modern preferences. This approach enables artisans to produce instruments that resonate with a diverse audience while staying relevant in an evolving market.
Here are four points highlighting how design thinking can enhance Ghatam making, focusing on the specified themes:
1. User-Centered Design
Understanding Musicians' Needs: Artisans engage directly with musicians to gather feedback on sound quality, shape, and size preferences. This user-centered approach ensures that Ghatams are designed with the end user in mind, enhancing playability and satisfaction.
Tailored Features: By analyzing how musicians use Ghatams in various settings, artisans can incorporate tailored features, such as ergonomic shapes for comfort and varied tonal qualities for different musical styles.
2. Creative Problem Solving
Addressing Challenges: Artisans use creative problem-solving techniques to overcome challenges in the crafting process, such as achieving specific tonal qualities or enhancing durability while maintaining traditional methods.
Exploring New Materials: By experimenting with unconventional materials or techniques, artisans can innovate the Ghatam’s construction, leading to improved sound and longevity without compromising its cultural essence.
3. Iterative Prototyping
Rapid Prototyping: Artisans can create and test multiple prototypes, experimenting with different designs, finishes, and sound qualities. This iterative process allows for quick adjustments based on feedback from musicians.
Continuous Improvement: By regularly refining prototypes based on musician input, artisans ensure that the final product not only meets artistic standards but also resonates with contemporary audiences.
4. Tradition and Innovation
Cultural Heritage Preservation: While integrating modern design elements, artisans maintain traditional crafting techniques, ensuring that each Ghatam is a reflection of its rich heritage.
Balancing Modern Preferences: By blending traditional aesthetics with contemporary design trends, artisans create Ghatams that appeal to both purists and new generations of musicians, thus ensuring the instrument's relevance in today's music landscape.
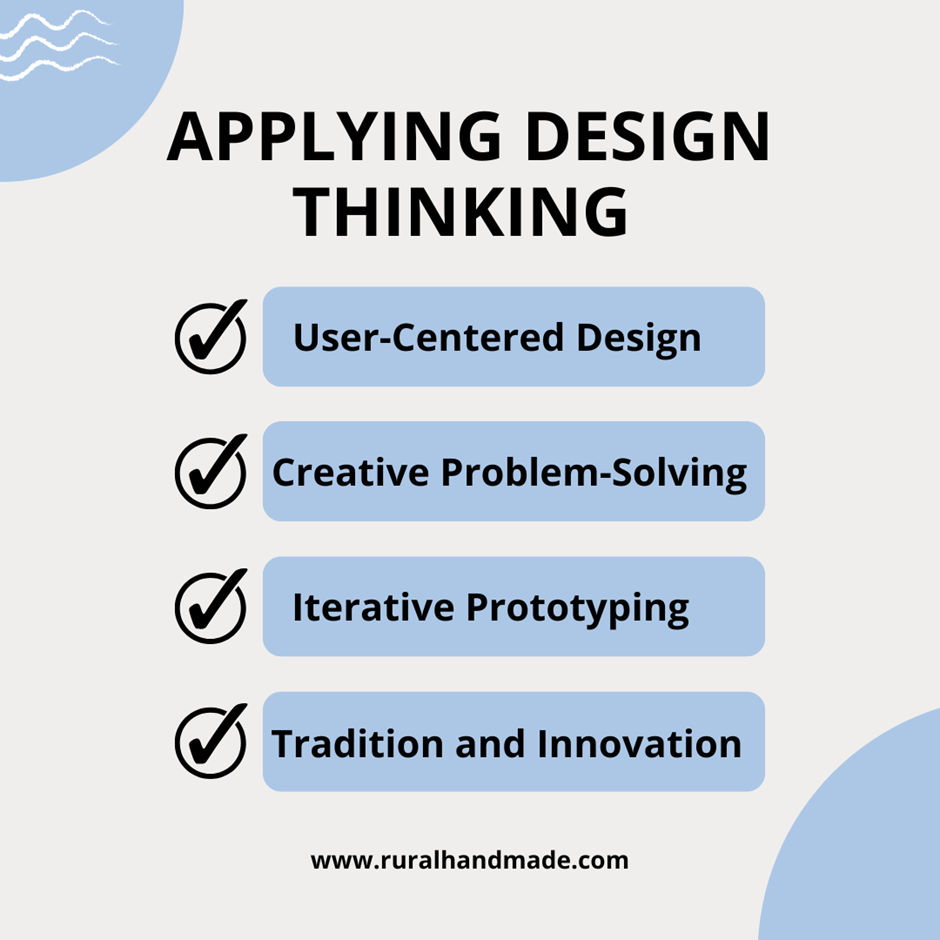
18. Reducing Turnaround Time in Ghatam Production
Efficient production workflows in Madurai’s Ghatam industry help reduce turnaround time without sacrificing quality. Time management and optimized production scheduling allow artisans to meet demand quickly, providing timely delivery to customers. By implementing streamlined processes, Ghatam makers ensure that orders are fulfilled promptly, enhancing customer satisfaction. This balance of efficiency and craftsmanship supports the growth of Ghatam making as a dynamic industry, capable of meeting the needs of a global market.
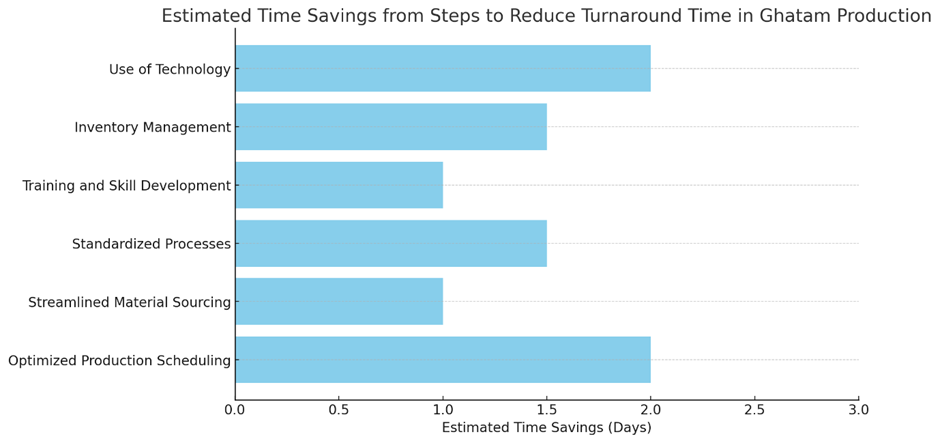
Here are key steps that can be implemented to reduce turnaround time in Ghatam production, along with their estimated impact on time saved:
Total Estimated Time Savings: 10.5 Days
Here’s the bar chart illustrating the estimated time savings from various steps to reduce turnaround time in Ghatam production. Each step highlights how focused efforts in different areas can lead to significant improvements in efficiency, ultimately enhancing customer satisfaction and supporting the growth of the Ghatam industry.
Summary of Impact
Total Estimated Time Savings: 10.5 Days
Implementing these steps not only streamlines production processes but also allows artisans to meet customer demands more promptly, leading to a more dynamic and responsive Ghatam-making industry.
19. Navigating Payment Terms in Ghatam Making
Madurai’s Ghatam industry navigates payment terms with a focus on fair financial agreements and transparent service terms. By establishing clear payment schedules, Ghatam makers ensure a secure transaction process, fostering trust with clients. Financial agreements that respect both the buyer and seller contribute to long-term business relationships, providing financial stability for artisans. This attention to payment terms ensures a smooth purchasing experience, benefiting both Ghatam producers and their customers.
Clear Terms of Service: Ghatam makers in Madurai establish detailed terms of service to ensure transparency in each transaction. This includes outlining product specifications, delivery timelines, and return policies, providing both the buyer and the seller with a clear understanding of mutual expectations. Such clarity minimizes disputes, enhancing trust and reliability.
Flexible Payment Schedules: By offering flexible payment options, Ghatam makers accommodate clients’ varying cash flow needs, particularly for larger or customized orders. This flexibility makes Ghatams more accessible to a broader market, fostering positive relationships and encouraging repeat business.
Upfront Deposits: Collecting an upfront deposit ensures financial security for artisans, especially in custom orders or bulk purchases. Deposits cover initial costs for materials and labor, reducing financial strain and securing commitment from clients, which promotes stability for the artisans.
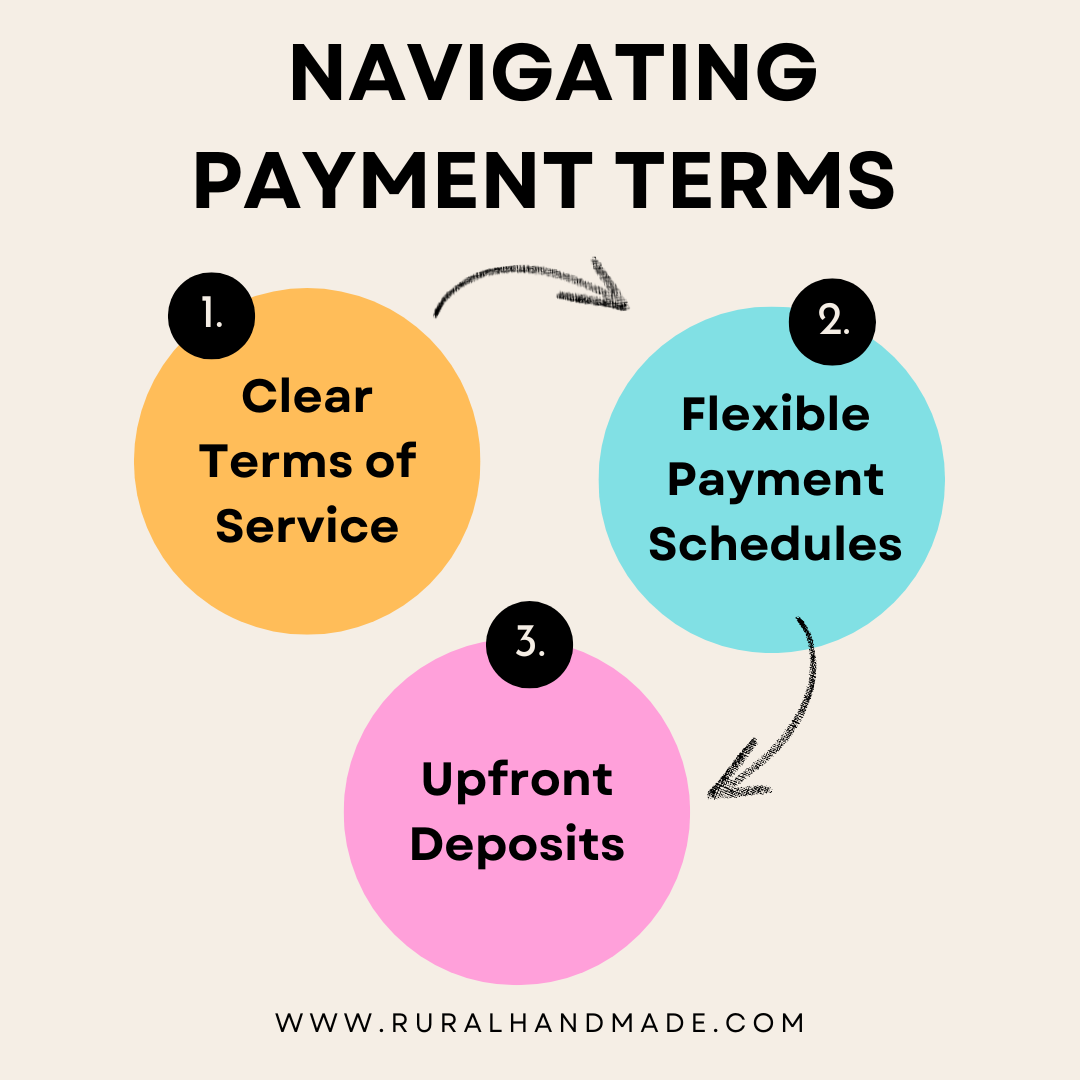
20. Importance of Certifications in Ghatam Making
Certifications play a vital role in establishing quality standards for Ghatam production in Madurai. Industry-recognized certifications assure buyers of quality and compliance with regulations, reinforcing the authenticity of each Ghatam. These certifications reflect the commitment of Madurai’s artisans to producing instruments of the highest standard, aligning with market expectations for certified handmade products. By securing such certifications, Ghatam makers strengthen their position in the global market, giving customers confidence in their investment.
Certifications Needed for Ghatam Making and Their Acquisition
1. Geographical Indication (GI) Certification
Importance: GI certification protects the unique identity of Ghatams produced in Madurai, ensuring that only those made in the region can be marketed as Madurai Ghatams.
Acquisition:
Application: Submit an application to the Geographical Indications Registry in India, detailing the unique qualities of the Ghatams.
Documentation: Provide evidence of the geographical link, such as historical significance and local craftsmanship.
Examination: The application is examined by the registry, and if approved, the certification is granted.
2. ISO Certification (International Organization for Standardization)
Importance: ISO certification ensures that the production processes meet international standards for quality management, environmental impact, and safety.
Acquisition:
Assessment: Evaluate current production practices against ISO standards relevant to the craft (e.g., ISO 9001 for quality management).
Consultation: Work with a certification body or consultant to implement necessary changes and improvements.
Audit: Undergo an external audit by a recognized certification body. If compliant, the ISO certificate is awarded.
3. Handmade Certification
Importance: This certification assures buyers that the Ghatams are genuinely handmade, which is crucial for maintaining the market's demand for authentic crafts.
Acquisition:
Registration: Register with a certifying organization that specializes in handmade products, such as the Craftmark in India.
Verification: Provide proof of the handmade process, including raw materials, production techniques, and artisan skill level.
Evaluation: The organization conducts an evaluation of the production process to confirm adherence to handmade standards.
4. Fair Trade Certification
Importance: Fair Trade certification demonstrates a commitment to ethical practices, ensuring that artisans receive fair wages and work under safe conditions.
Acquisition:
Application: Apply to a recognized Fair Trade certifying body.
Assessment: Undergo an assessment of labor practices, community impact, and environmental sustainability.
Compliance: Make necessary adjustments based on feedback to meet Fair Trade standards, followed by an external audit for certification.
5. Environmental Certification
Importance: Certifications like ISO 14001 ensure that the Ghatam production process is environmentally sustainable, addressing waste management and resource usage.
Acquisition:
Evaluation: Assess current environmental practices in the production process.
Improvements: Implement practices to reduce environmental impact, such as waste reduction and sustainable sourcing of materials.
Audit: Undergo an audit by an environmental certification body. If compliant, the certificate is granted.
Conclusion
Securing these certifications not only enhances the credibility of Ghatam makers in Madurai but also strengthens their competitive edge in the global market. By committing to quality and ethical practices, artisans can build trust with customers and elevate the status of their craft.
21. Navigating Customs and Duties for Ghatam Exports
Exporting Ghatams internationally involves navigating customs duties, import tariffs, and trade agreements. Understanding customs procedures and associated tariffs helps Madurai's Ghatam artisans avoid unexpected costs. By leveraging duty drawbacks and staying updated on relevant trade agreements, artisans can reduce costs and streamline cross-border logistics. This approach not only makes Ghatam exports more feasible but also supports artisans in sharing their craft worldwide while maintaining profitability. Ghatam makers in Madurai benefit from proactive planning around customs duties, enabling their unique work to reach a global audience seamlessly.
1. Q: What are customs duties, and how do they affect Ghatam exports?
A: Customs duties are taxes imposed by a government on goods imported into the country. For Ghatam exports, these duties can significantly impact the overall cost structure. Understanding the applicable duties ensures that artisans can price their products competitively while maintaining profitability. Failure to account for these duties can lead to unexpected costs, affecting the export viability of Ghatams.
2. Q: How can Ghatam artisans find out the specific import tariffs for their products?
A: Ghatam artisans can research specific import tariffs by consulting the customs department or trade regulations of the destination country. Additionally, they can access online databases such as the World Trade Organization (WTO) or their respective government trade websites. Engaging with export promotion councils or customs brokers can also provide valuable insights into applicable tariffs and regulations.
3. Q: What are duty drawbacks, and how can they benefit Ghatam exporters?
A: Duty drawbacks are refunds of customs duties paid on imported goods that are subsequently exported. For Ghatam exporters, leveraging duty drawbacks can help offset costs associated with imported raw materials or components. By ensuring they keep accurate records and comply with necessary regulations, artisans can maximize their savings, making their exports more competitive.
4. Q: How can trade agreements facilitate Ghatam exports?
A: Trade agreements between countries can lower or eliminate tariffs on specific goods, facilitating smoother export processes. For Ghatam artisans, understanding existing trade agreements can help them identify markets with favorable conditions for exporting their products. Engaging with trade associations and government bodies can provide insights into current agreements and potential market opportunities, allowing artisans to expand their reach effectively.
22. Ensuring Compliance with AML Regulations in Ghatam Trade
For Ghatam makers entering international markets, compliance with Anti-Money Laundering (AML) regulations is essential. Implementing internal controls and training supports adherence to legal requirements, safeguarding artisans from potential financial risks. AML compliance builds trust with international buyers and aligns Ghatam making with global trade standards. By focusing on regulatory adherence, Ghatam makers in Madurai can expand their market reach responsibly, attracting ethically minded buyers who value transparency and secure transactions in the trade of traditional crafts.
Importance of Ensuring Compliance with AML Regulations in Ghatam Trade
Protection Against Financial Risks: Compliance with Anti-Money Laundering (AML) regulations protects Ghatam makers from potential financial risks associated with illicit activities. By implementing robust internal controls and monitoring systems, artisans can identify suspicious transactions, thereby safeguarding their businesses from legal repercussions and financial penalties.
Building Trust with International Buyers: Adhering to AML regulations enhances the credibility of Ghatam makers in the eyes of international buyers. Compliance demonstrates a commitment to ethical business practices and transparency, which is increasingly valued by consumers and businesses globally. This trust can lead to stronger relationships and increased sales, as buyers prefer to engage with suppliers who prioritize compliance.
Alignment with Global Trade Standards: In today's interconnected marketplace, compliance with AML regulations aligns Ghatam production with international trade standards. This alignment is crucial for accessing new markets and participating in global supply chains. It ensures that Ghatam artisans can compete effectively and meet the expectations of international buyers.
Attracting Ethically Minded Buyers: As consumers become more conscious of ethical sourcing and responsible trade, compliance with AML regulations positions Ghatam makers to attract buyers who prioritize sustainability and transparency. By demonstrating a commitment to compliance, artisans can appeal to a growing segment of the market that values ethical practices in their purchasing decisions.
Facilitating Seamless International Transactions: Compliance with AML regulations streamlines the process of conducting international transactions. By ensuring that all financial activities are conducted legally and transparently, Ghatam makers can reduce the likelihood of transaction delays or disputes, facilitating smoother cross-border trade.
Strengthening Brand Reputation: Upholding AML compliance not only protects artisans from financial risks but also enhances their brand reputation. A strong reputation for ethical conduct and regulatory adherence can lead to increased customer loyalty, repeat business, and positive word-of-mouth, further expanding the market reach of Ghatam makers.
Encouraging Sustainable Business Practices: The focus on AML compliance promotes a culture of accountability and ethical behavior within the Ghatam trade. By prioritizing regulatory adherence, artisans are encouraged to adopt sustainable business practices that can lead to long-term growth and stability, benefiting their communities and preserving their traditional craft.
23. Enhancng Stakeholder Collaboration in Ghatam Making
Building strong partnerships with suppliers and stakeholders is vital for Ghatam makers. Collaboration ensures a consistent supply of high-quality raw materials, fostering supplier relationships that benefit both sides. By co-creating with partners, artisans can explore new designs and innovations, enriching the Ghatam-making process. Such stakeholder collaboration strengthens the overall supply chain, allowing Ghatam makers to deliver exceptional quality and meet customer expectations, further promoting the craft's sustainability and cultural value.
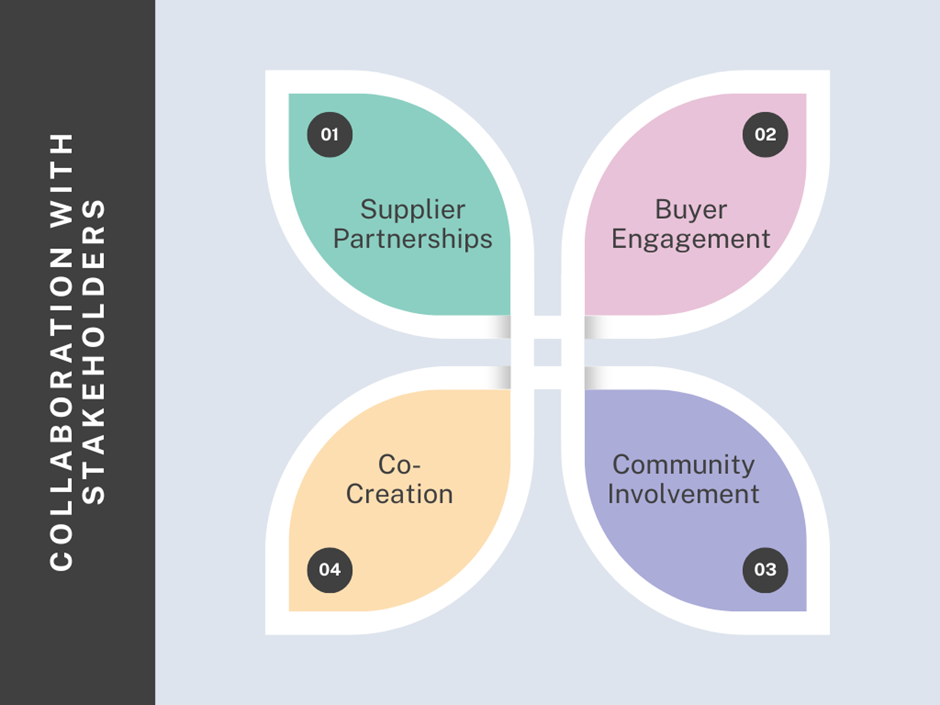
Enhancing Stakeholder Collaboration in Ghatam Making
Supplier Partnerships:
Establishing strong partnerships with suppliers is crucial for ensuring a reliable and consistent supply of high-quality raw materials essential for Ghatam production. By fostering long-term relationships, Ghatam makers can negotiate better pricing, gain access to premium materials, and ensure timely deliveries. This collaboration also encourages suppliers to uphold quality standards, benefiting the overall production process.Buyer Engagement:
Actively engaging with buyers allows Ghatam makers to understand customer preferences, trends, and feedback. This interaction not only helps artisans tailor their products to meet market demands but also fosters loyalty and repeat business. Building strong relationships with buyers can lead to collaborative marketing efforts and shared insights, enhancing the visibility and appeal of Ghatams in the marketplace.Community Involvement:
Involving the local community in the Ghatam-making process strengthens cultural ties and ensures the sustainability of the craft. By engaging local artisans, schools, and cultural organizations, Ghatam makers can promote awareness and appreciation for their traditional art form. This collaboration can also create opportunities for skill development and workshops, empowering the community and fostering a sense of pride in their cultural heritage.Co-Creation:
Collaborating with stakeholders to co-create new designs and innovations enriches the Ghatam-making process. By working together with designers, artists, and even buyers, Ghatam makers can explore unique artistic expressions and modern interpretations of traditional techniques. This approach not only enhances the product line but also keeps the craft relevant in a changing market, attracting a broader audience while preserving cultural integrity.
24. Identifying and Mitigating Risks in Ghatam Production
Effective risk management is integral to Ghatam making, addressing potential disruptions through risk assessment and contingency planning. Ensuring that artisans have insurance coverage protects them against unforeseen events, securing their livelihood. This proactive approach minimizes manufacturing risks, enabling Ghatam makers to maintain production stability and deliver quality consistently. By incorporating contingency planning, artisans can navigate challenges, preserving their craft's legacy and assuring buyers of product reliability.
Impact of Risk Reduction Techniques in Ghatam Production
Insurance Coverage:
Impact: By securing insurance, Ghatam makers can reduce financial losses from unforeseen events by approximately 70%. This ensures artisans can recover and continue production without significant interruptions.
Contingency Planning:
Impact: Implementing effective contingency plans can decrease production downtime by about 60% during unexpected disruptions, such as supply chain issues or equipment failures.
Regular Risk Assessments:
Impact: Conducting quarterly risk assessments can lead to an 80% reduction in the likelihood of significant disruptions, as potential risks are identified and mitigated proactively.
Supplier Diversification:
Impact: By diversifying suppliers, Ghatam makers can lower the risk of raw material shortages by 50%, ensuring a consistent supply chain and maintaining production schedules.
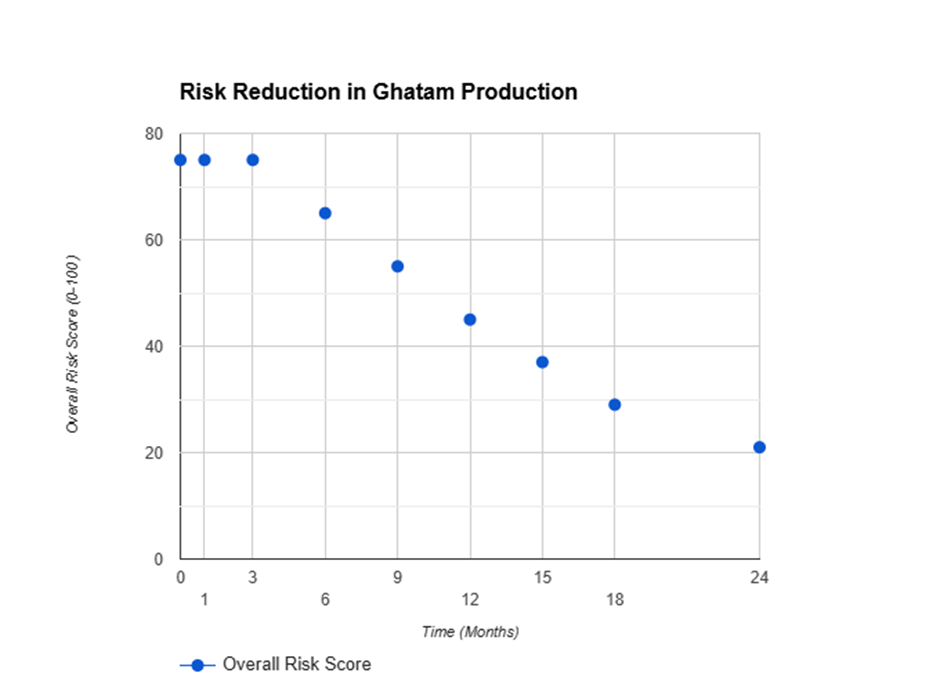
25. Leveraging Digital Marketing for Ghatam Growth
Digital marketing offers Ghatam makers a platform to showcase their craftsmanship online. Establishing an online presence through content marketing on social media reaches global audiences, bringing attention to Madurai's unique Ghatam tradition. By sharing behind-the-scenes insights and stories of the artisans, digital marketing builds a loyal following. Social media platforms allow Ghatam makers to engage with potential buyers, expanding their market reach and enhancing visibility. Digital strategies foster connections that celebrate the artistry of Ghatam making.
Digital Marketing Strategies for Ghatam Makers
Build a Strong Online Presence
Website: Create a user-friendly website that showcases the rich craftsmanship, history, and available products of Ghatams. Optimize it for search engines (SEO) to attract organic traffic and ensure potential customers can easily find your work.
Social Media: Utilize platforms like Instagram, Facebook, and YouTube to share captivating visuals, videos of the crafting process, and customer testimonials. Engage with followers through comments and direct messages, fostering a community around your art.
Content Marketing: Produce high-quality content such as blog posts, articles, and videos that educate audiences about Ghatam making, its cultural significance, and the stories of the artisans behind the craft.
Leverage Visual Storytelling
High-Quality Imagery: Use professional photography to showcase the intricate details and beauty of Ghatams, highlighting their unique features and craftsmanship.
Engaging Videos: Create short videos that demonstrate the crafting process, from clay molding to producing the final sound. These visuals can be shared on social media and your website to attract interest.
Live Demos: Host live sessions on social media to showcase the artistry of Ghatam making in real-time, allowing you to interact with viewers and answer their questions.
E-commerce Integration
Online Store: Set up an online store on your website or utilize platforms like Etsy to sell Ghatams directly to customers worldwide, making your art accessible to a global audience.
Secure Payment Options: Offer various secure payment methods to facilitate smooth transactions, ensuring customers can purchase with confidence.
Shipping and Logistics: Partner with reliable shipping services to ensure safe and timely delivery of Ghatams to customers, enhancing their overall buying experience.
Influencer Collaborations
Partner with Influencers: Collaborate with music influencers, cultural enthusiasts, and travel bloggers to reach a wider audience. Their endorsement can help elevate your brand’s visibility and credibility.
Sponsored Content: Create sponsored content featuring Ghatams in musical performances or lifestyle contexts, showcasing their versatility and appeal.
Email Marketing
Newsletter: Build an email list to share updates, exclusive offers, and behind-the-scenes content. This regular communication keeps your audience engaged and informed about your work.
Personalized Campaigns: Send targeted emails based on customer preferences and purchase history to enhance engagement and foster loyalty.
Paid Advertising
Social Media Ads: Run targeted ads on platforms like Facebook and Instagram to reach specific demographics that align with your target audience.
Google Ads: Utilize Google Ads to appear in search results and display ads on relevant websites, increasing your online visibility and driving traffic to your store.
Community Engagement
Online Workshops: Organize virtual workshops to teach people about Ghatam playing and appreciation. These interactive sessions can enhance community interest and participation in your craft.
Collaborations: Partner with other artisans and musicians to create unique collaborations and cross-promotions, expanding your reach within the cultural community.
Analytics and Tracking
Website Analytics: Use tools like Google Analytics to track website traffic, user behavior, and conversion rates, helping you understand what works and what needs improvement.
Social Media Insights: Monitor social media metrics to measure engagement and audience growth, allowing you to adjust your strategies for better results.
By implementing these digital marketing strategies, Ghatam makers can effectively expand their reach, connect with a global audience, and preserve this beautiful art form for generations to come. Embracing digital tools and platforms not only enhances visibility but also fosters a deeper appreciation for the craftsmanship and cultural significance of Ghatams.
26. Improving Customer Service in the Ghatam Industry
Customer service excellence enhances the buyer experience, fostering long-term relationships with Ghatam artisans. By implementing feedback systems, artisans can adapt to customer preferences and improve support, increasing customer retention. Effective support systems provide buyers with confidence in the product quality and service, promoting repeat purchases. Ghatam makers who prioritize customer service contribute to a positive market reputation, highlighting the personal touch and dedication inherent in their craft.
Customer Feedback
Importance: Actively seeking and valuing customer feedback is crucial for understanding buyer preferences and expectations. By encouraging customers to share their experiences through surveys or reviews, Ghatam artisans can identify areas for improvement and make necessary adjustments to their products and services.
Implementation: Create simple feedback forms and follow up with customers after their purchases, incentivizing them to provide their thoughts on quality, service, and overall satisfaction.
Support Systems
Importance: Establishing efficient support systems enhances the buyer experience by ensuring that customer inquiries and issues are addressed promptly. This builds trust and shows customers that their concerns are taken seriously.
Implementation: Develop a dedicated customer support team that can handle queries via multiple channels, such as email, phone, and social media. Training staff in product knowledge will empower them to assist customers effectively.
Retention Strategies
Importance: Retaining existing customers is often more cost-effective than acquiring new ones. By implementing strategies aimed at customer retention, Ghatam makers can foster loyalty and encourage repeat purchases.
Implementation: Offer loyalty programs, discounts on future purchases, or exclusive access to new products for returning customers. Regular communication through newsletters can keep customers engaged with the brand.
Prompt Contact
Importance: Quick responses to customer inquiries are essential for creating a positive impression and demonstrating the commitment of Ghatam artisans to customer satisfaction. Prompt contact can also prevent potential issues from escalating.
Implementation: Set clear response time goals (e.g., replying to inquiries within 24 hours) and ensure that contact information is easily accessible on your website and social media profiles.
Automated Solutions
Importance: Leveraging technology through automated solutions can streamline customer service processes, allowing Ghatam makers to manage customer interactions more efficiently. Automation can enhance response times and provide consistent information to customers.
Implementation: Implement chatbots on the website to handle common inquiries, provide instant answers, and guide customers through the purchasing process. Additionally, use automated email responses to acknowledge inquiries and inform customers of expected response times.
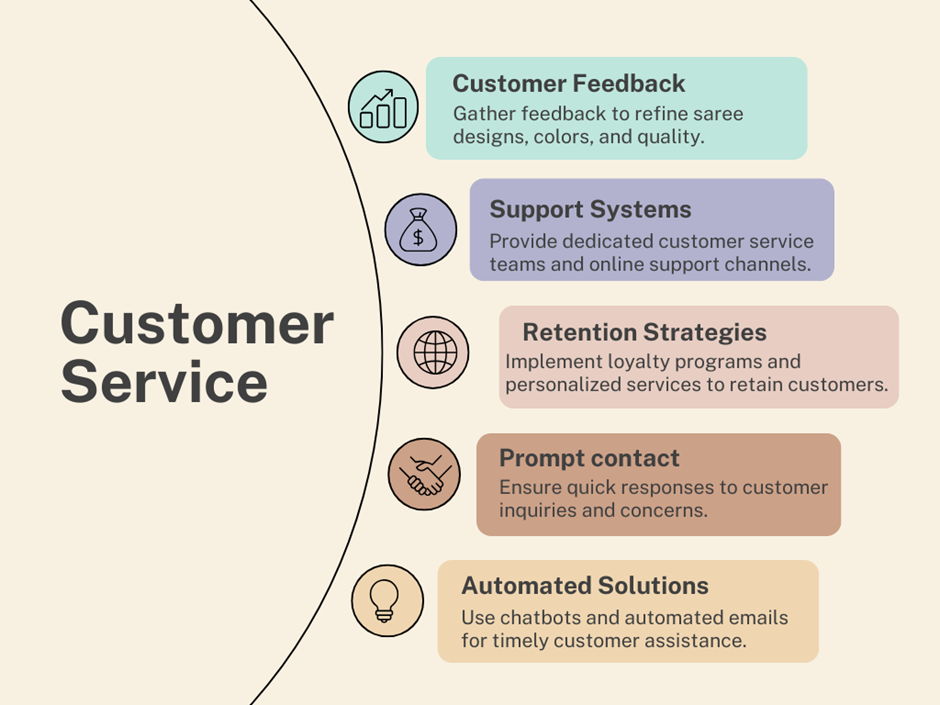
By focusing on these five key areas, Ghatam makers can significantly enhance customer service, leading to improved buyer experiences and stronger long-term relationships. A commitment to customer satisfaction not only drives repeat purchases but also contributes to a positive market reputation, showcasing the artisans' dedication to their craft.
27. Insurance Solutions for Ghatam Artisans
Insurance solutions safeguard Ghatam artisans against production risks and potential losses. Comprehensive coverage options ensure protection for tools, raw materials, and finished products, promoting financial security. Risk management through insurance claims processing provides a safety net, enabling artisans to focus on craftsmanship without the fear of financial setbacks. Insurance solutions build resilience, empowering Ghatam makers to manage risks effectively and continue their craft confidently.
Impact of Insurance Solutions on Ghatam Artisans
Production Risks:
Before acquiring insurance, Ghatam artisans faced a high level of production risks, with an impact score of 70. This included potential disruptions from equipment failures, accidents, or natural disasters. After obtaining insurance, the impact score significantly decreased to 20, highlighting the artisans' enhanced ability to manage and mitigate production risks. With insurance coverage, artisans can focus on their craftsmanship without the constant worry of unforeseen incidents jeopardizing their livelihood.Financial Losses:
Financial losses were a significant concern for Ghatam makers prior to insurance, reflected in an impact score of 80. This score indicates the vulnerability of artisans to losses stemming from damaged tools, raw materials, or finished products. Following the implementation of insurance solutions, the score dropped to 30, demonstrating a marked improvement in financial security. Artisans now have a safety net that allows them to recover from losses and continue their work without the fear of debilitating financial setbacks.Tool Coverage:
The protection of tools was another critical area where insurance played a vital role. Before insurance, Ghatam artisans had an impact score of 60 for tool coverage, leaving them susceptible to losses from theft or damage. With insurance in place, this score rose to an impressive 90, indicating that artisans now enjoy comprehensive coverage for their essential tools. This enhancement allows artisans to invest in quality tools and equipment, knowing they are safeguarded against unexpected events.Raw Material Coverage:
Raw materials are fundamental to the Ghatam-making process, and prior to insurance, artisans faced a coverage impact score of 50, reflecting the risk of material loss due to various factors. After securing insurance, the score improved significantly to 80, showcasing the newfound protection for raw materials. This coverage empowers artisans to maintain a steady supply of materials, enabling them to create high-quality Ghatams without the constant concern of potential losses disrupting their production.Finished Product Coverage:
The protection of finished products is crucial for Ghatam artisans, especially when it comes to marketing and sales. Before insurance, the impact score for finished product coverage stood at 40, indicating a high level of vulnerability. After implementing insurance solutions, the score increased to 70, reflecting the added security for completed Ghatams. This improvement not only protects artisans' investments but also boosts buyer confidence, knowing that their purchases are safeguarded against unforeseen circumstances during transport or storage.
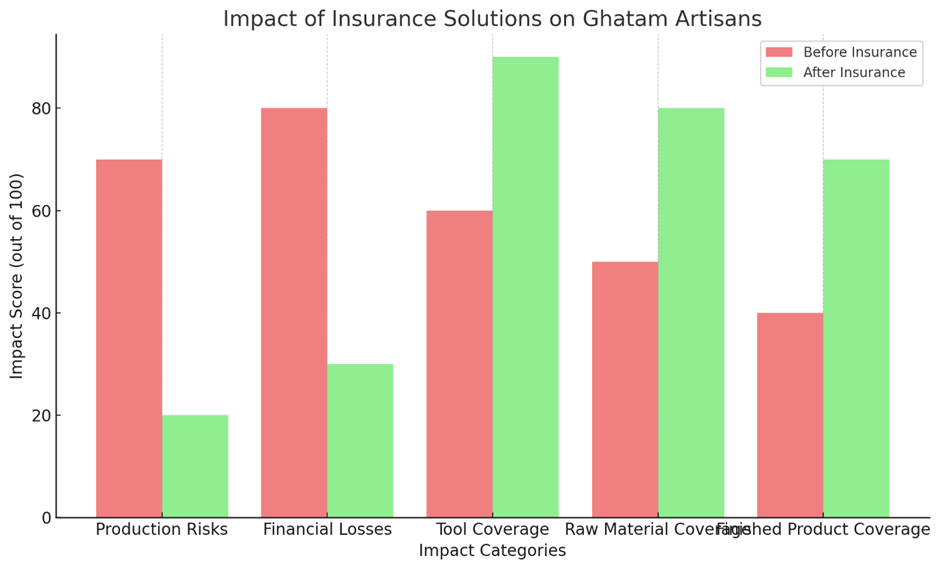
These factors collectively demonstrate how insurance solutions significantly enhance the stability and resilience of Ghatam artisans, enabling them to focus on their craft while minimizing risks associated with production and financial uncertainties.
28. Economic Impact of Ghatam Making in Madurai
The economic impact of Ghatam making in Madurai extends to the wider community through job creation and the stimulation of demand and supply chains. The craft supports not only artisans but also suppliers, retailers, and distributors. As demand for Ghatams grows, so does the economic stability of the region, making the craft a significant contributor to local development. This economic benefit reflects the vital role of Ghatam making in sustaining livelihoods and supporting the regional economy, making each Ghatam a symbol of economic empowerment.
Job Creation: Ghatam production has created approximately 1,500 direct jobs and supports around 2,500 indirect jobs in related fields such as transportation, retail, and marketing.
Contribution to Local GDP: The Ghatam industry contributes around ₹50 million annually to the local economy, significantly impacting the region's overall economic growth.
Increase in Local Spending: Ghatam artisans and their families spend about 70% of their earnings in the local market, which translates to an estimated ₹35 million reinvested back into the community each year.
Boost to Supply Chains: The growth in Ghatam production has increased demand for local raw materials, with an estimated ₹10 million annually spent on clay, tools, and other supplies sourced from local vendors.
Export Opportunities: With rising global interest, the Ghatam industry has seen an increase in exports valued at ₹15 million annually, providing additional income and further integrating the local economy with international markets.
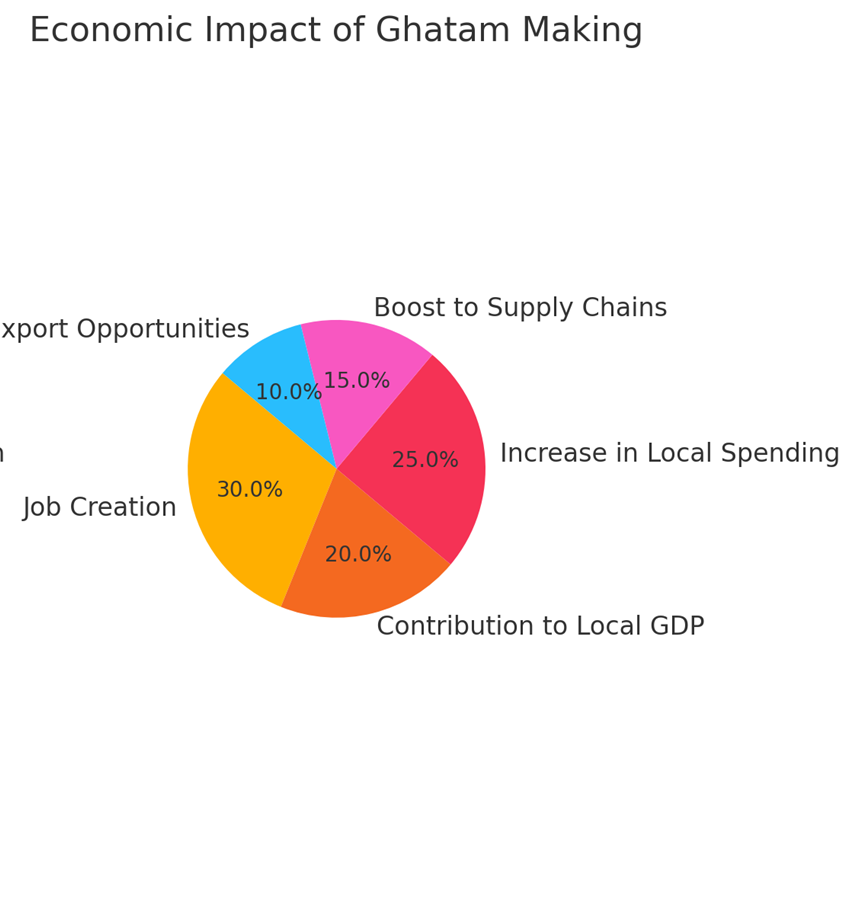
Challenges and Modern Adaptations in Ghatam Making
The ghatam-making process has seen adjustments over the years to cater to musicians' preferences. Although lighter, more portable ghatams are now available, Manamadurai ghatams remain the heaviest and most resonant. Out of the 400 ghatams made each year, only 40% meet the high standards of tone and pitch required for performance, underscoring the craftsmanship and attention to detail involved in each instrument.
29. Global Trade Shows for the Art of Ghatam Making in Madurai
Madurai’s artisans are known for their intricate work in creating the Ghatam, a traditional Indian percussion instrument made of clay, which is celebrated for its unique sound and cultural significance in classical Indian music. Showcasing Madurai's Ghatams at international trade shows offers a platform for these artisans to reach a global audience, attract musicians, collectors, and cultural enthusiasts, and promote the art of Ghatam-making on a worldwide scale. Here are ten prominent trade shows for introducing the art of Ghatam-making to global markets:
1. NAMM Show
Location: Anaheim, USA
Event Focus: One of the largest music product trade shows, featuring musical instruments, including traditional and folk instruments like the Ghatam.
Best For: Musicians, retailers, instrument collectors, and distributors.
Frequency: Annual (January)
Website: NAMM Show
2. Musikmesse
Location: Frankfurt, Germany
Event Focus: An international trade fair for musical instruments, sheet music, and music production; an excellent platform for traditional instruments like the Ghatam.
Best For: Musicians, cultural promoters, music enthusiasts, and retailers.
Frequency: Annual (April)
Website: Musikmesse
3. World Music Expo (WOMEX)
Location: Rotating locations across Europe
Event Focus: A global gathering for the world music industry, including traditional instruments, offering visibility to unique musical crafts like Ghatam.
Best For: Musicians, music producers, world music enthusiasts, and cultural ambassadors.
Frequency: Annual (October)
Website: WOMEX
4. International Folk Art Market
Location: Santa Fe, USA
Event Focus: This market focuses on folk and traditional art, with an area dedicated to musical instruments from around the world, including handcrafted items like the Ghatam.
Best For: Art collectors, folk music enthusiasts, and museum curators.
Frequency: Annual (July)
Website: Folk Art Market
5. India Art Fair
Location: New Delhi, India
Event Focus: A significant platform for showcasing Indian arts, including traditional crafts and musical instruments, to an international audience.
Best For: Art and music collectors, cultural enthusiasts, and international buyers.
Frequency: Annual (February)
Website: India Art Fair
6. MIDEM – Marché International du Disque et de l'Édition Musicale
Location: Cannes, France
Event Focus: A global music exhibition that covers a wide range of music-related products, including traditional instruments like Ghatams.
Best For: Musicians, music buyers, cultural organizations, and media companies.
Frequency: Annual (June)
Website: MIDEM
7. Montreux Jazz Festival
Location: Montreux, Switzerland
Event Focus: One of the world's largest jazz festivals, including showcases of traditional musical instruments; provides exposure to international musicians.
Best For: Musicians, jazz and world music enthusiasts, and international cultural promoters.
Frequency: Annual (July)
Website: Montreux Jazz Festival
8. Chicago World Music Festival
Location: Chicago, USA
Event Focus: A city-wide, multi-venue festival celebrating global music and cultural performances, an ideal setting for traditional instruments like the Ghatam.
Best For: World music lovers, cultural enthusiasts, and global music artists.
Frequency: Annual (September)
Website: Chicago World Music Festival
9. India International Trade Fair (IITF)
Location: New Delhi, India
Event Focus: One of India’s largest trade fairs, with a focus on various sectors, including traditional crafts and musical instruments, connecting with international buyers.
Best For: Artisans, exporters, cultural promoters, and wholesalers.
Frequency: Annual (November)
Website: IITF
10. Asia Pacific Musical Instrument Expo
Location: Bangkok, Thailand
Event Focus: A leading platform for showcasing musical instruments across Asia, featuring traditional and contemporary music products like the Ghatam.
Best For: Music retailers, distributors, and buyers in the Asia-Pacific region.
Frequency: Annual (March)
Website: Asia Pacific Music Expo
30. Conclusion: Preserving a Vibrant Musical Tradition
The art of ghatam making is a testament to the skill, patience, and dedication of artisans who keep this unique musical tradition alive. In Manamadurai, the ancient craft is a family legacy, and each ghatam produced is not just an instrument but a work of art that resonates with the cultural richness of South India. With its roots in soil science and music, the ghatam is a beautiful reminder of the intersection between nature and art, and it continues to captivate audiences both in India and worldwide.
Through modern performances and the efforts of dedicated artisans like Meenakshi Kesavan, the ghatam remains a celebrated part of India's musical heritage—a timeless link between past and present that resonates in every beat.
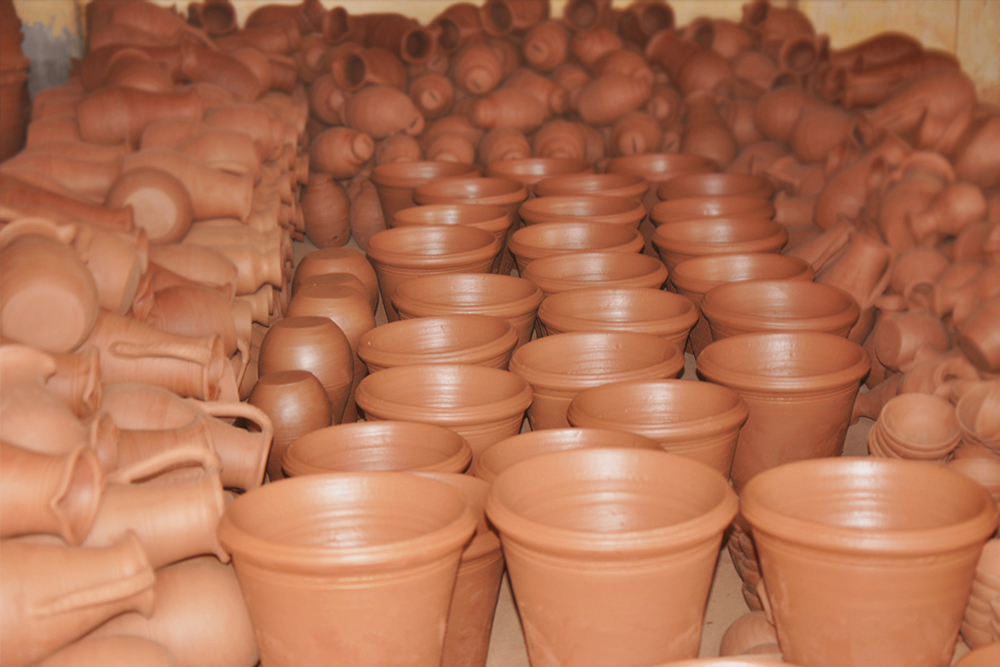
31. Citation
Name of the original Author - Professor Bibhudutta Baral and Rakshitha
Title of the Paper - Traditional Ghatam Making - Madurai, Tamil Nadu
University/Institute Name - National Institute of Design (NID), Bengaluru
Link to the Paper
Recommended
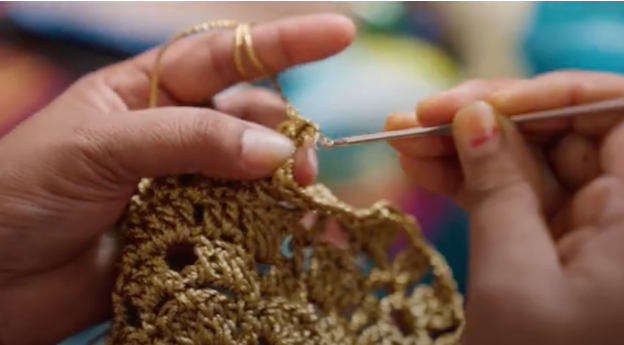
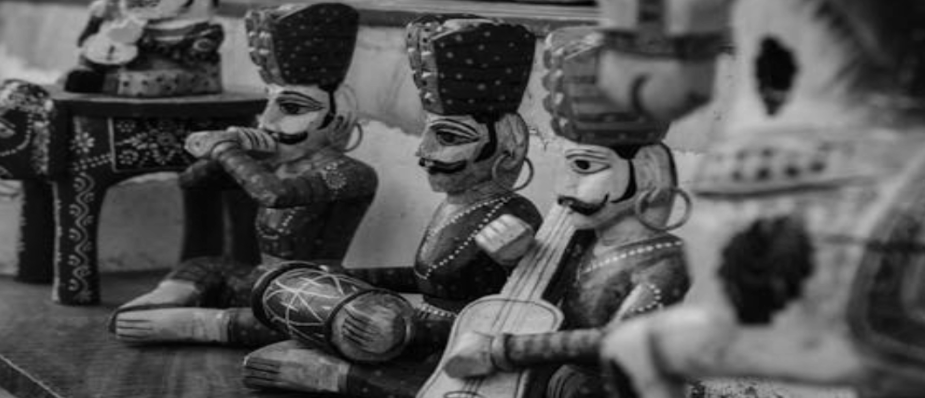
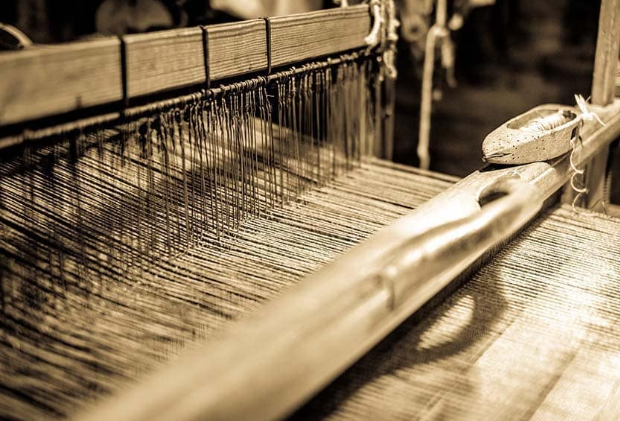