Driving Growth And Innovation In The Indian Handicraft Industry
Jan 25, 2024 | Divya Salgiya
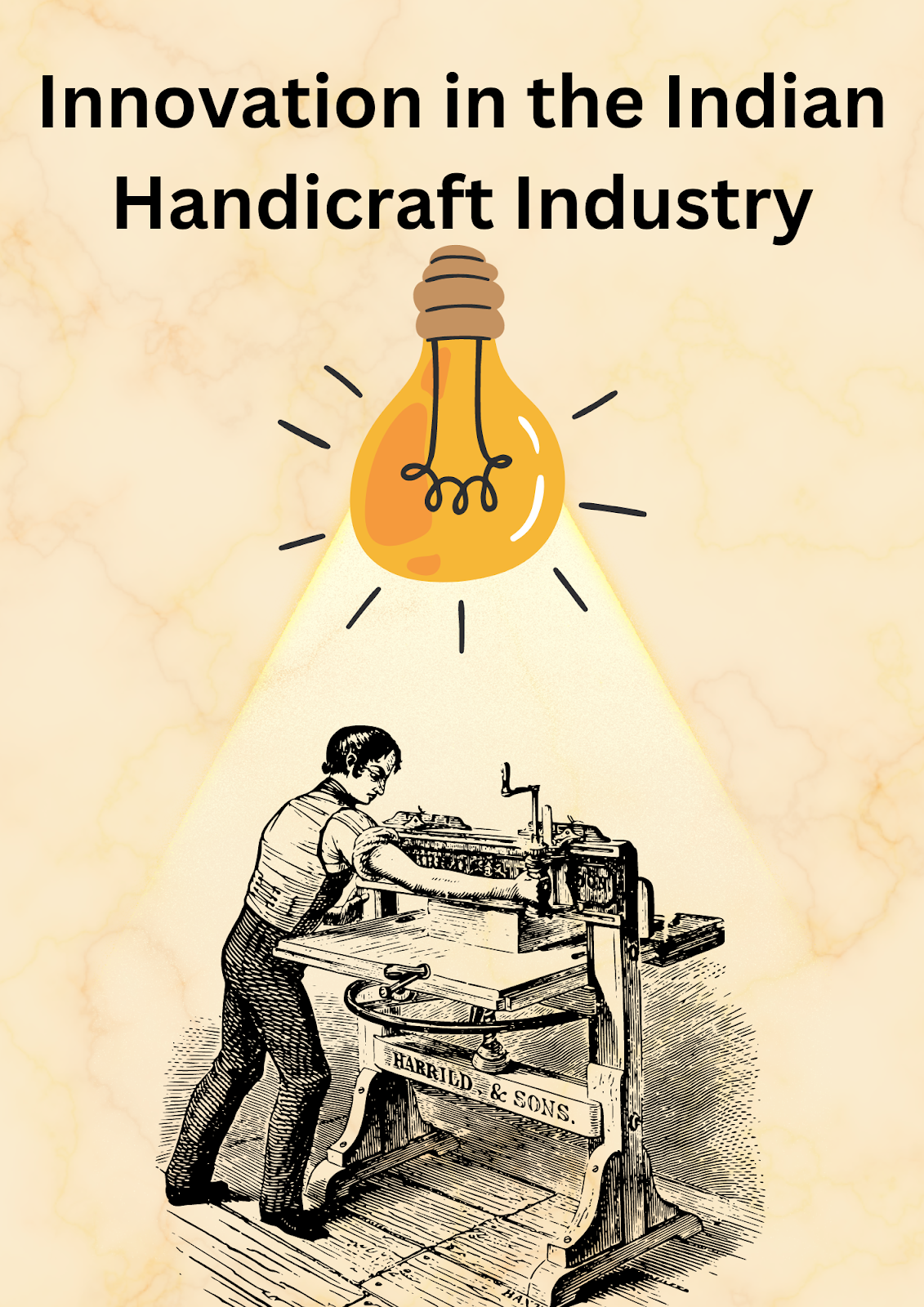
How is craft innovation possible?
In order to achieve craft innovation, it is important that there is collaboration between craftspeople, designers, artists, technologists, entrepreneurs etc who will come together and develop the existent crafts in such a way that they can be contextualized to current needs. Collaboration can also take place with industries, organizations, small and medium enterprises, government associations etc. The craft is no longer seen as something that is ancient and primitive but something that is at par with modern day machine made products.
DICRC always indulges in the process of ‘Co-creation’ by bringing experts from field of Craft, Design, Architecture, Entrepreneurship, Industry, Marketing, and Government in order to promote the field of Craft, for Craft Innovation. The intention of Craft Innovation at DICRC is to develop “Innovation in Craft’ and ‘Innovation through Craft”.
‘Innovation in craft’ refers to bringing about innovation in craft in terms of product, material, system etc. Product intervention can be driven through intervention by designers, material innovation is achieved through material technologists/experts’ intervention while system innovation in craft can be achieved through intervention by social organisations.
‘Innovation through craft’ essentially means using craft as a means to drive innovation. DICRC envisions broadening the scope of craft and developing it to enter into new and varied disciplines. When this happens, craft can act as a catalyst for innovation in other disciplines.
Interdisciplinary collaboration is an established route to innovation*. By working together, it is argued that professionals with different yet complementary backgrounds can create new ways of approaching problems and finding solutions. Increasingly sophisticated yet accessible online platforms have enabled both individuals and organisations to build teams around shared interests and issues, rather than conventional professional disciplines.
Craft should become part of the trend of collaborative practices, where craftspeople will collaborate with professionals from other disciplines. In this way, they can undertake a wide range of projects and roles in sectors including design, architecture, art, media - as well as across the creative industries. Increasingly sophisticated yet accessible online platforms have enabled both individuals and organisations to build collaborative teams around shared interests and issues, rather than conventional professional disciplines. Hence the use digital technologies can upgrade the value and position of craft and craft practices in India.
1. Embracing Technology:
One of the key opportunities lies in embracing technology to modernize production processes, enhance efficiency, and expand market reach. Integrating digital tools such as 3D printing and CAD/CAM can revolutionize design creation, prototyping, and production. Artisans can leverage these technologies to streamline their workflow, improve product quality, and cater to evolving customer demands. Additionally, e-commerce platforms and digital marketplaces provide a global storefront, enabling artisans to access a broader customer base and establish direct connections with buyers from around the world.
2. Collaborations with Designers:
Collaborating with designers can inject fresh perspectives into traditional crafts and bridge the gap between tradition and contemporary aesthetics. By engaging designers, artisans can explore innovative product designs, experiment with fusion styles, and create unique offerings that resonate with modern consumers. These collaborations not only infuse new life into traditional crafts but also open doors to niche markets and upscale segments, thereby increasing the economic value and relevance of Indian handicrafts in the global marketplace.
3. Expanding into Global Markets:
The global market presents vast opportunities for Indian handicrafts. With a growing appreciation for authentic, handmade products, there is an increased demand for Indian crafts worldwide. To tap into this potential, strategic market expansion is crucial. Artisans and businesses can participate in international trade fairs, exhibitions, and craft expos to showcase their creations, build networks, and forge relationships with global buyers. Establishing a strong online presence through e-commerce platforms, social media marketing, and targeted digital campaigns can significantly enhance visibility and attract international customers.
4. Sustainable and Ethical Practices:
In an era marked by heightened environmental consciousness and ethical consumerism, Indian handicrafts hold a unique advantage. The industry’s inherent reliance on natural materials and traditional techniques aligns with sustainable and ethical practices. By emphasizing eco-friendly production processes, reducing waste, and promoting fair trade principles, artisans and businesses can position themselves as champions of sustainability. Such practices not only attract environmentally conscious consumers but also contribute to the preservation of indigenous skills and the socioeconomic well-being of artisans.
5. Skill Development and Training Programs:
Investing in skill development and training programs can empower artisans with new techniques, business knowledge, and marketing skills. Government initiatives, NGOs, and private organizations can collaborate to provide comprehensive training programs that equip artisans with the necessary tools to adapt to changing market dynamics, enhance product quality, and effectively market their creations.
6. Product Diversification:
Expanding the range of handicraft products can attract a broader customer base and cater to evolving consumer preferences. Artisans can explore new product categories, experiment with innovative materials, and introduce modern interpretations of traditional crafts. This diversification not only adds vibrancy to the industry but also ensures its resilience and adaptability in a competitive market.
7. Export Promotion and International Partnerships:
To harness the full potential of the Indian handicraft industry, strategic export promotion efforts and international partnerships are crucial. Government bodies and trade associations can facilitate participation in international trade shows, organize buyer-seller meets, and establish collaborations with global retailers and distributors. These endeavors can pave the way for increased export opportunities and foster sustainable growth in the industry.
8. Digital Marketing and Branding:
In today’s digital era, effective marketing and branding strategies are essential to gain visibility and reach target audiences. Artisans and businesses can leverage social media platforms, content marketing, and storytelling techniques to build a compelling brand narrative and engage with customers. Online marketplaces dedicated to handmade products can also provide a platform for artisans to showcase their unique offerings to a global customer base.
Here are Some Latest technologies Used in the Handicraft industry
These days, the handicraft industry is seeing some remarkable changes. The introduction of technology has taken it to a different level altogether. New techniques and tools are being introduced in the market that assists craftsmen to create better products. These new tools help them to create products that were not possible before. There are many Latest Technologies Used in the Handicraft industry like:
Rapid Prototyping Technology
The traditional craft practices in India are embedded with an inherent empirical knowledge. This knowledge encompasses not only the material understanding and skills of making but also holds a holistic and intuitive understanding of sustainability in the larger context. This understanding needs to be put to use for a purpose that will bring forth various crafts from the remotest corners of our country and make them contextual to the present day. This can be achieved through the process of craft innovation.
The intent is to bring innovation in Space Making Crafts (SMC), Surface Narrative Crafts (SNC) and Crafts related to interior architecture. Our country’s architectural heritage is full of such innovations concerning material usage and its application. The objective of DICRC has been to bring craft innovation in larger interior architectural applications today with collaborative co-creations between various peer groups.Rapid prototyping technology is getting more and more popular in the handicraft industry nowadays. It helps to reduce the cost and time of handicraft production. With rapid prototyping technology, the production of handicrafts has been easier and more efficient.To those who are not familiar with this technology, here is how the process works. Usually, when you go to a company or a store with your order for a particular handicraft item, they will ask you to sketch what you want from them. You can either sketch on paper or create it on any kind of computer software. Depending upon your order and requirements, different materials are used for making these items.
After that, you will be required to upload all the necessary details relating to your order on their website. They may then ask you to make additional changes according to their requirements. The next step would be sending your design file to the company through an online medium such as email so that they can begin work on it immediately!
Laser Technology in Handicrafts;
Laser technology has enhanced its applicability by leaps and bounds and it has a lot of potential that can make it one of the key tools for any business. Industries such as automotive, aerospace, defense, etc. use laser technology to manufacture their products.Laser technology is a new type of manufacturing technology with speed, precision, and high efficiency. The laser cutting machine uses a laser beam to cut material according to the input graphics information. It is suitable for cutting carbon steel, stainless steel, aluminum alloy, copper alloy, galvanized steel plate, and other metal materials.
The Handicraft industry is also using this innovative technology for years now and it has proved to be very beneficial for them too. With the help of laser machines, handicraft manufacturers have been able to deliver accurately designed handicrafts with high precision and efficiency. Some of the applications of lasers in this industry include:
Laser Engraving on Wood
Marking on Glass
Laser Cutting on Metal
Laser Engraving on Leather
Computer-Aided Design (CAD) In the Handicrafts industry
The use of Computer-Aided Design (CAD) in the Handicraft industry has increased rapidly over the past few years. Many companies are using CAD because it provides them with a faster and more efficient way of creating designs and then producing them. It also helps companies reduce their design cost and improve their productivity.Using CAD software like Auto-CAD, craftsmen can convert a drawing into a digital file by using a computer and plotter. In addition, CAD technology offers many benefits
1. Better communication: Better Communication between designers and manufacturers. With CAD, each side of the equation can easily understand what is required. This make it easier to manage expectations and avoid costly mistakes before going into production.
2. Limitless possibilities: CAD lets designers explore more options than ever before. The potential options are limited only by the designer’s imagination — not by the tools available.
3. Flexible working methods: The use of CAD software allows designers to work remotely, on-demand, and at their convenience. As long as they have access to a computer with an internet connection.
CNC Milling Technology in Handicrafts
CNC Milling Technology is a computer-aided manufacturing process that involves cutting away material from a block of material using a rotary cutter. It’s a versatile technique that can be used to create complex shapes with high precision. The CNC milling machine usually consists of two main components: The milling head, which contains all the equipment needed to cut and machine the milling path; and the spindle, which holds the material in place during machining.
CNC milling allows for more precision, flexibility, and efficiency than any other type of handicraft manufacturing. The CNC machines are designed and engineered to produce parts that could be used in a wide range of industries and applications.
Some examples include:
Medical: implants, prosthetic arms, surgical tools, instruments, etc.
Automotive: engines, pistons, turbos, fuel injection systems, etc.
Electronics: circuit boards, adapters, connectors, etc.
Aerospace: fuselages, thrust reverses, wings, landing gear components, etc.
Digital Making and 3D Printing Technologies
3D Printing Technology has been used in various fields and industries to produce intricate and complex designs with the help of the Computer-Aided Design (CAD) software. The CAD software enables the designing, visualization, and analysis of products digitally.Some of the benefits of using Digital Making and 3D Printing Technologies in the Handicrafts industry are as follows:
Improved Quality of Designs produced
Reduced Production Time
Customization and Personalization
Mass Customization & Mass Production
Prototyping
Reduced Cost
THE COOLEST INNOVATIVE FABRICS IN Handloom Sector
Leaf leather
Leaf leather is a plant-based leather alternative made from tree leaves (generally Teak leaves). It is strong and water-resistant, and the leather features the natural design of leaves, making it unique and beautiful. To produce leaf leather, fallen Teak leaves are collected and no trees are harmed to do so. The leaves are soaked in water, dyed and laid flat together to dry.
The drying process bonds them, which leaves us with a large sheet of leaf material that is then mended with cotton fabric. Before it can be sewn into accessories, a thin BOPP film is applied to make the fabric waterproof and more durable.
Vegea
Vegea, also known as wine leather, is a fabric made from leftover grape skins from winemaking, vegetable oils as well as other natural fibers from the agroindustry. It is estimated that for every 10 liters of wine produced, 2.5 liters of waste are created. Thankfully, this waste can be upcycled into one square meter of wine leather!
To produce Vegea, the grape marc, which consists of grape skins, stalks and seeds, has first to be dried. After this step, it is combined with vegetable oil and water-based polyurethane. The mix creates a bio-based material that is coated into a fabric. The production process excludes toxic chemicals, dangerous solvents and heavy metals.
Some great brands that use Vegea are Ganni and Pangaia.
Mushroom leather
Mylo, or mushroom leather, is a vegan leather alternative developed by the company Bolt Threads and designed to have a minimal environmental impact. It is made from mycelium, which is the branching underground root system of mushrooms. Bolt Threads uses mycelium cells and makes them grow on beds of organic matter in a vertical farming facility that is 100% powered by renewable energy. Together, the cells form an interconnected 3D network that is then processed by the company. It is tanned and dyed, transforming it into a leather-like material.
Mylo is soft, supple and durable, which makes it ideal to use in the fashion industry. Sustainable brand Stella McCartney recently launched a bustier top and trousers that are the first-ever garments made from Mylo.
Piñatex
Pineapple leather, or Piñatex, is an innovative natural textile made from pineapple leaf fiber, which is an agricultural waste product. When pineapples are harvested, their leaves are collected and the long fibers are extracted with special machines. After they are washed, the fibers are dried and they go through a purification process to eliminate impurities.
The fluff-like pineapple leaf fiber that is left is mixed with a corn-based polylactic acid and transformed into a non-woven mesh called Piñafelt. Finally, the Piñafelt is colored using GOTS-certified pigments and coated with a resin made from polyurethane to make it even more durable and waterproof. Piñatex has been used by over 1,000 brands, including Svala and No Saints. The company that manufactures Piñatex, Ananas Anam, is a certified B Corporation.
Nettle fiber
Made from nettle plants, nettle fiber was already used by humans during the Bronze Age.
Over the centuries, the use of nettle fibers to make clothes was very popular, but it quickly declined when we started using cotton as an alternative, which was easier and more convenient to grow. However, clothes made from nettle fibers are more sustainable than those made of cotton, because nettles need less water and pesticides to grow. Nettle fibers are extracted from the nettle plant stem and are then carded and spun. This process creates a strong cord that can be used to produce ropes and fishing nets, or when blended with cotton or wool, to create clothing.
Orange fiber
Did you know that each year, 110 to 120 million tons of citrus waste are generated around the world? An Italian company, Orange Fiber, decided to do something about it and created a sustainable fabric made from orange juice by-products. To produce orange fiber, the company uses hundreds of thousands of tons of orange waste. It extracts the cellulose from the peels using its patented process and turns it into a fiber that is spun into yarn. Then, it is woven into a silk-like fabric that is soft and lightweight. It can also be shiny or opaque depending on the final use. Italian luxury brand Salvatore Ferragamo launched in 2017 a capsule collection of women’s wear made from citrus by-products in collaboration with Orange Fiber.
Explore this fabric at our website rural handmade
Eri Silk Fabric: Natural dyed Fabric-
Cactus leather
Cacti are amazing plants! They regenerate the soil naturally, help prevent soil erosion and desertification, and they can absorb carbon dioxide up to 30% of their body mass. But they can also be turned into sustainable fabrics! Developed in Mexico, cactus leather is made from Opuntia Cactus, also called Nopal. Only the mature leaves of cacti are harvested, meaning that no cacti are harmed in the process. Cacti also need very little water to grow, and there is no need for artificial irrigation or pesticides. After the leaves are cut, they are mashed and dried for a few days. They are then mixed with non-toxic chemicals, and finally, attached to a backing.
More and more brands are designing products with cactus leather, including Allégorie, Miomojo and KEVA.
Parblex
Parblex is an innovative bioplastic made using potato waste and developed by the company Chip[s] Board. The company does not disclose much information about its exact production process, but it involves different steps like fermentation, purification, and then polymerization.
Parblex is made from potato peelings, and it is mixed with other agricultural waste, such as wood flour or walnut shells, to strengthen it and give it a certain texture and color.
The material is biodegradable and recyclable, and Chip[s] Board does not use any toxic resins or chemicals derived from oil to produce it. It also reincorporates offcuts back into the production process. The bioplastic has already been used by the eyewear brand Cubitts London, and to make buttons by Isabel Fletcher.
Bio fabricated leather
This bio fabricated leather created by the company Modern Meadow is one of the most intriguing materials on this list! Modern Meadow makes its one-of-a-kind lab-grown material from collagen. More specifically, it grows a strain of yeast that produces collagen, which is a protein we can find in the skin.The collagen is then purified, pressed into sheets and tanned, all without using animal products or toxic chemicals. The final material is very similar to cowhide leather, but it is stronger, thinner, lighter, more versatile and sustainable.
The bio fabricated leather made by Modern Meadow is not accessible yet. But thanks to all its beneficial properties, this unique material deserves recognition and its future looks promising.
Conclusion
The Indian handloom industry, deeply rooted in rich cultural heritage, plays a pivotal role in both the country's economy and cultural identity. For generations, handloom weaving has been a cherished tradition, offering livelihoods to countless artisans, particularly in rural regions. This industry is renowned for its diverse array of exquisitely hand-woven fabrics, showcasing the exceptional artistic skills and craftsmanship of weavers throughout India. In contemporary times, technological innovation emerges as a formidable force propelling economic growth across various sectors, including textiles. Within the Indian handloom industry, these technological advancements offer immense potential. They promise heightened productivity, elevated product
quality, and broader market reach. The integration of modern machinery, digital tools, and automation streamlines production, leading to cost efficiencies and improved overall efficiency. Technology empowers the creation of innovative designs and customizable options, making handloom products more appealing to a wide consumer base.
Recognizing the transformative potential of technology is imperative, and understanding its impact on the economic viability of Indian handloom enterprises is crucial. Policymakers, industry stakeholders, and entrepreneurs must navigate the benefits and challenges associated with these innovations. By doing so, they can harness technology's potential effectively, ensuring the sustainable growth and preservation of the Indian handloom industry. The confluence of tradition and technology offers a promising path forward, safeguarding cultural heritage while enhancing productivity and competitiveness.
Recommended
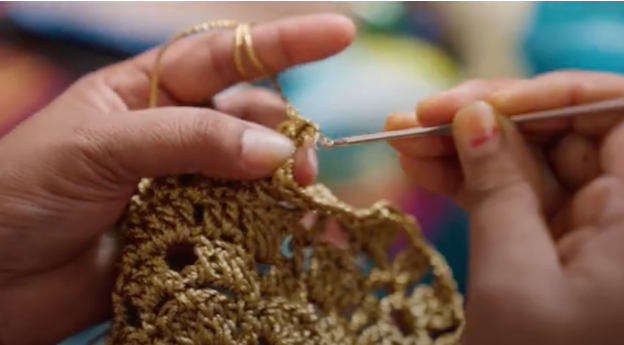
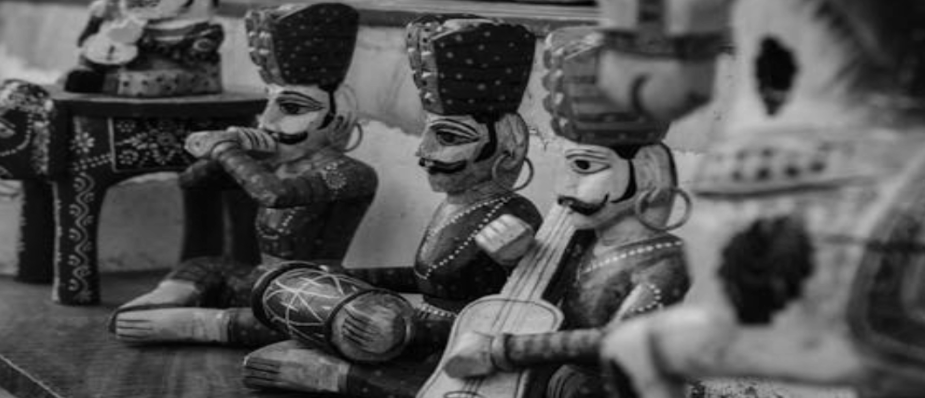
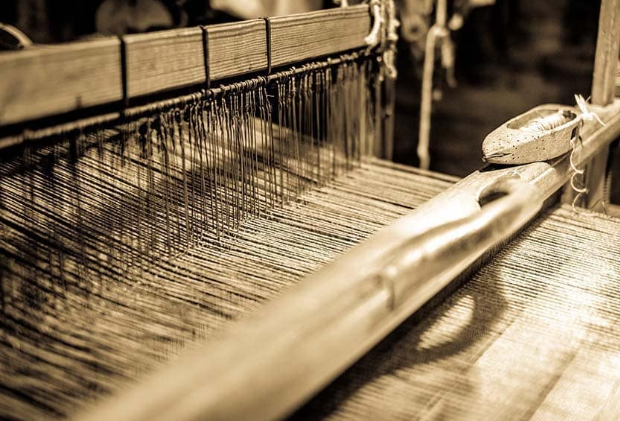